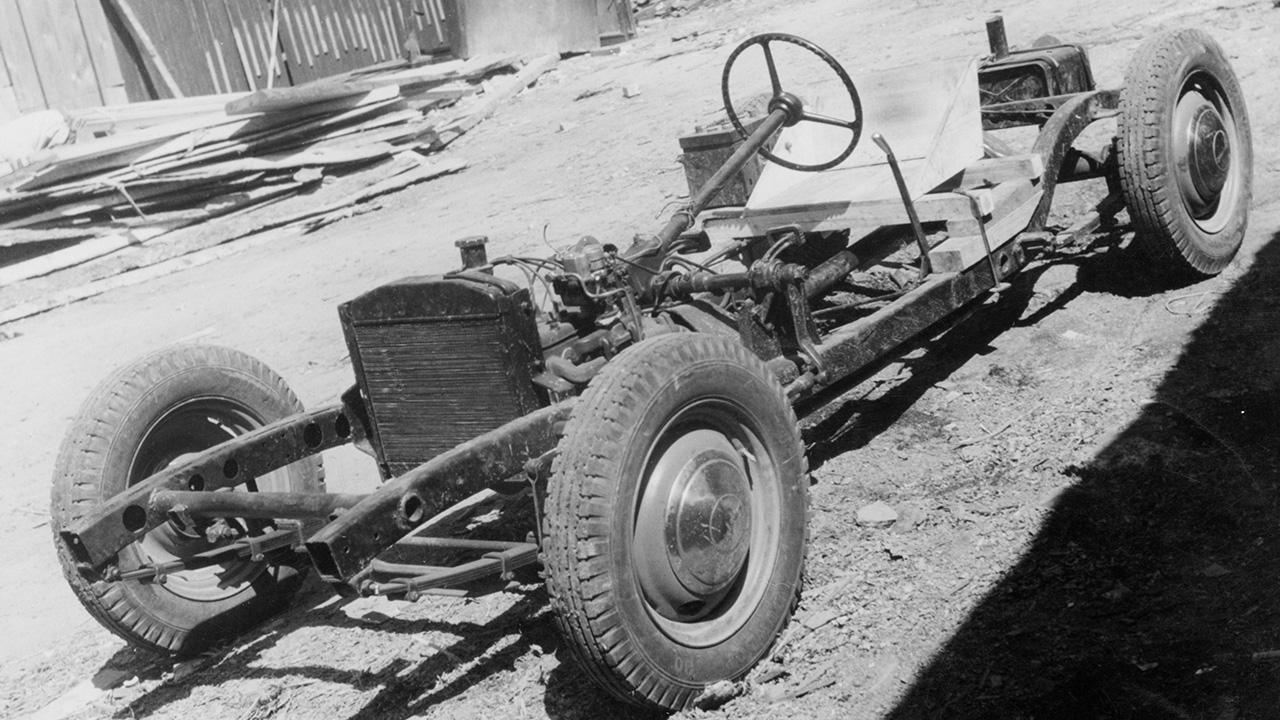
幻のレーシングカーの復元プロジェクトを追う。第5回前編はラダーフレーム製作の奮闘を紹介。
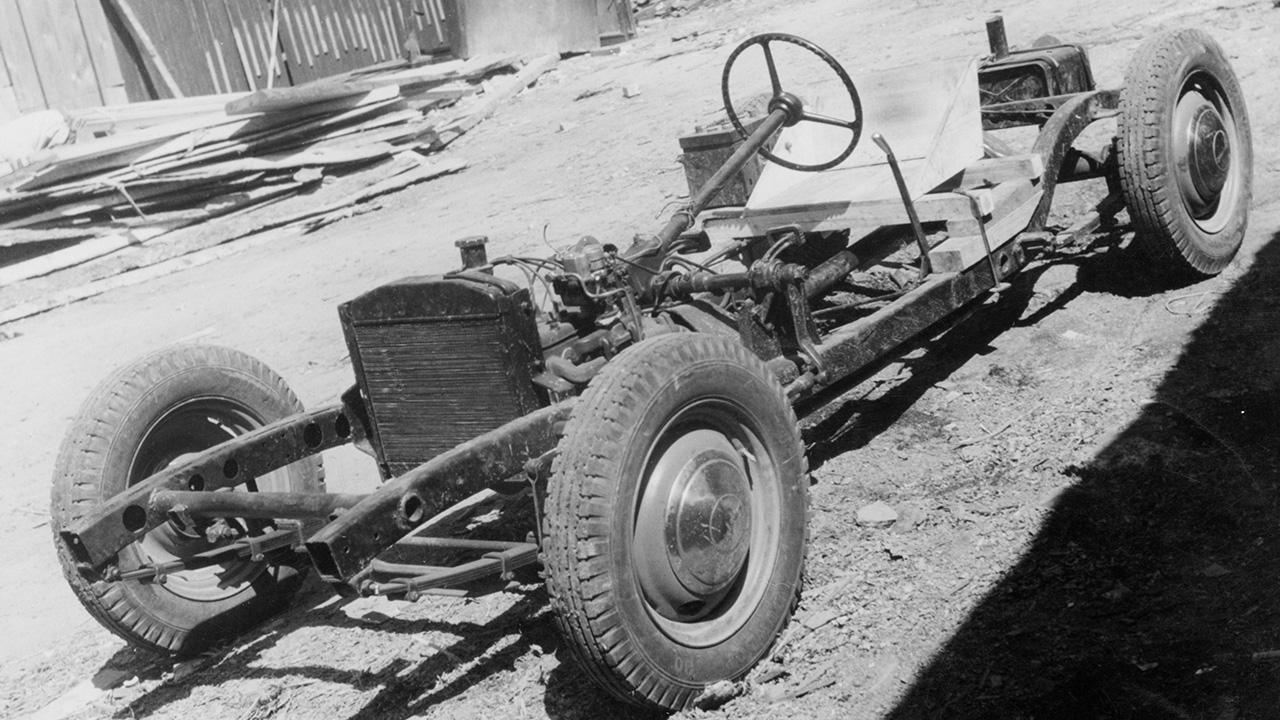
トヨタ社内で復元された幻のレーシングカーが、富士スピードウェイにオープンした「富士モータースポーツミュージアム」に展示されている。それは誰がどんな想いで、どんな目的で開発した、どんなマシンだったのか。その歴史と意味、そして復元の現場をリポートする特集企画。
第5回は車両の骨格であるラダーフレームとボディの製作を担当したチームの奮闘をお届けする。今回はその前編としてラダーフレームの設計から製作、完成までをリポート。
マシンのすべての基礎になるラダーフレーム
トヨペット・レーサーは、今から70年以上前の1951年に2台だけ製作されたレーシングカー。車両は現存していないため、復元プロジェクトのメンバーは当時の写真やベース車両の図面を頼りに、多くの主要部品をゼロから製作することになった。
中でも最も大きな主要部品が、“車両の背骨”となるラダーフレーム。左右2本の縦長のフレーム(サイドメンバー)を、ハシゴのように数本のクロスメンバーでつないだ構造。見た目がラダー(ハシゴ)の形をしているのでこう呼ばれる。
エンジンもトランスミッションもボディも、すべてこの上に搭載される。つまりマシンの“土台”になるものだから、強度でも精度でも妥協は許されず、そして真っ先に完成させなければならない。
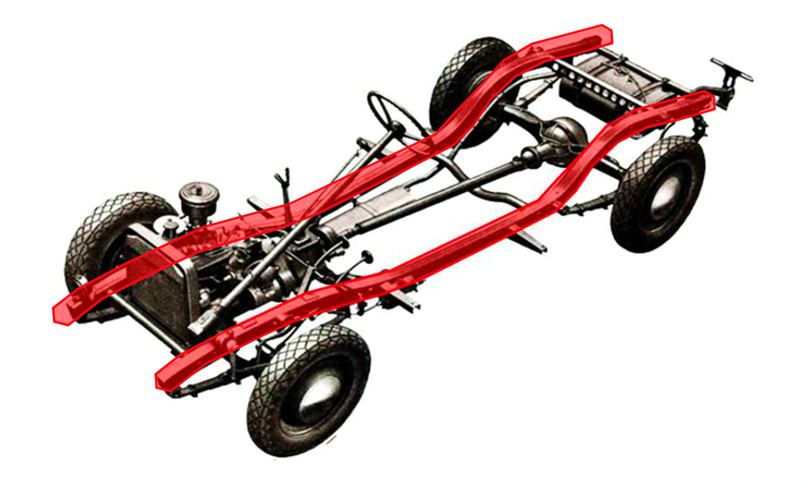
トヨペット・レーサーの復元プロジェクトでこのラダーフレームの設計と製作に挑んだのが、渡部真史、恒川国大の2人だ。
渡部は入社7年目、普段はボデー開発部でボディ設計を担当。復元プロジェクトでは通常の仕事と同じボディ設計に関わることになった。
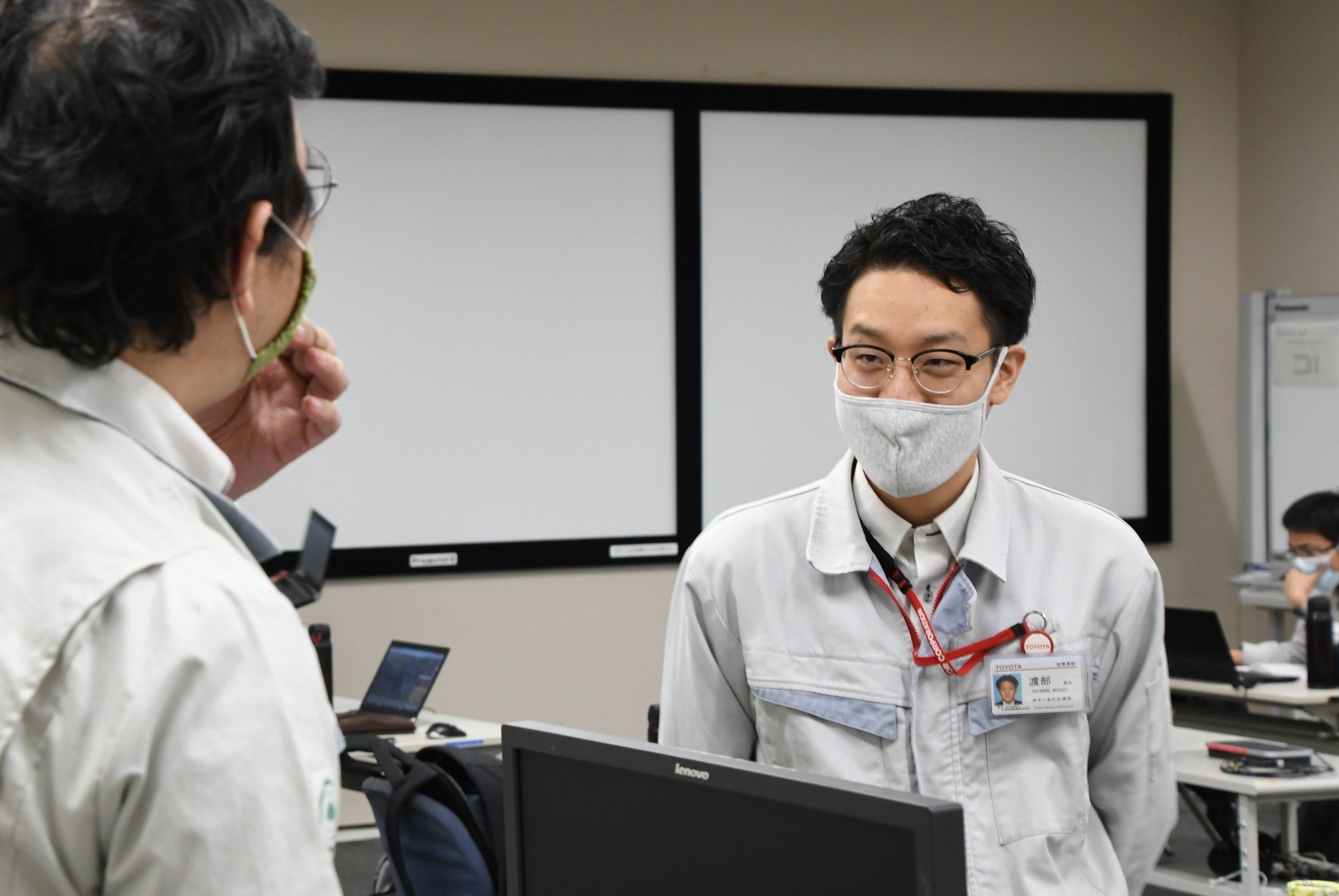
渡部
上司から「君は学生フォーミュラをやっていたし、こういうプロジェクトは好きだろう。だから推薦しておいた」と言われたのが、参加したきっかけです。
クルマは大好きだし、モノづくり自体が好きで、学生フォーミュラでもボディ設計を担当していましたので、「何か面白そうなクルマをつくれそうだ」と乗り気でした。自分たちの権限でモノづくりができるのは魅力的ですし。ちなみに、トヨペット・レーサーのことは参加して初めて知りました。
ただ、私たちが担当するラダーフレームは真っ先に仕上げなければならないパーツですし、つくらなければならない関連部品も多いほうでした。復元プロジェクトは、パートごとに人員を割り当てたチーム編成なので「これを2人では荷が重すぎるのでは?」とも思いました。
一方の恒川は入社18年目。入社後11年間プレス生技部に籍を置き、復元プロジェクト時は開発試作部。現在は電池製造技術部でEV電池製造技術に携わっている。
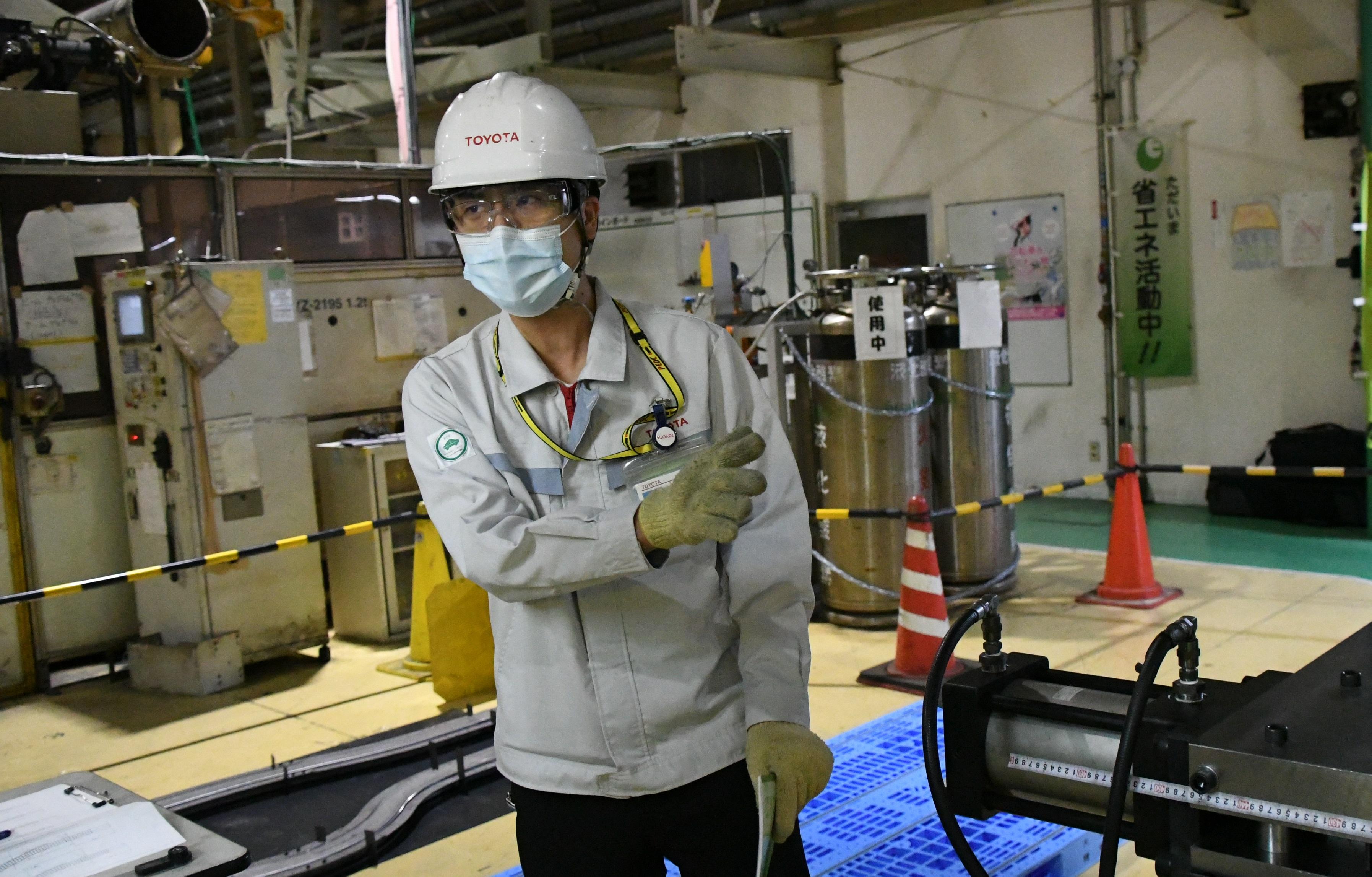
恒川
上司から「プレス、板金関係のメンバーが必要だというので推薦しておいた」と言われてこのプロジェクトを知りました。これまで、プレスという限られた範囲で仕事をしてきたので、これは「車両全体を見る」いい機会になると思いました。
トヨタのモータースポーツ活動の礎となった初代クラウンのオーストラリア一周ラリーのことは知っていましたが、トヨペット・レーサーの存在は知りませんでした。
問題はフレームの「つくり方」
ラダーフレームは頑丈なので現在もトラックやバス、そしてランドクルーザーなど苛酷な環境での使用を想定して開発された一部のSUVにも採用されている。しかしトヨペット・レーサーがつくられた当時は、一般的な乗用車にもラダーフレームが用いられていた。
トヨペット・レーサーのベース車両となった乗用車「トヨペットSD型」も、そのベースになった「トヨタSB型トラック」もラダーフレームを採用。その設計図は社内に残ってはいたが、当時の手書きの図面を3D-CAD*を用いて3次元データ化するのは困難な作業だった。
*コンピューター上で3次元データの作成を行うシステム
そして今回、このチームが直面した最大の課題は「ラダーフレームをどうつくるか」だった。このラダーフレームづくりを中心的に取り組んだのが恒川である。
ラダーフレームは、金型を使って製作するのが常識だ。だが、たった1台だけしかつくらない(復元しない)トヨペット・レーサーのために金型をつくることは、安く早くつくるというプロジェクトの方針もあり、コスト的に難しい。
そこで恒川は渡部と相談しながら「型レス」、つまり金型を使わずに製作できないか、さまざまな方法を模索した。多品種少量生産のためのソリューション開発は、電動化など“これからのクルマづくり”に取り組むトヨタ自動車にとって、解決しなければならない課題でもある。
前述したように、ラダーフレームは真っ先に完成させなければならない。他のチームがまだ検討段階にあった2020年の年末に、恒川らはどうつくるかを必死で検討した。
検討を重ねる中で恒川は、2人乗りの超小型EV「C+pod(シーポッド)」のフレームが、協力企業の大豊精機の「押し通し曲げ」という技術を使って生産されていることを知る。
同社は、トヨタ車のシャシーや足回りの部品の試作から生産まで一貫して行う豊田市にあるモノづくり企業だ。そこで恒川は同じ技術が使えるのでは?と考え、大豊精機にトヨペット・レーサーのラダーフレームを型レスでつくれないか、と打診した。
サイズが大きすぎて“つくれない”
打診を受けた大豊精機の担当者は「お話を伺うと、素材の板厚が厚く長くて成形時の荷重もそれなりに必要。しかも『型レス』と聞いて、これは大丈夫かなと思いましたが、ダメ元で社内に相談すると、金属の丸いパイプを連続的に曲げて3Dで成形する設備が当社にあるので、この設備でつくれないかということになりました。」
以前から曲げ加工の実験をトヨタ自動車 開発試作部と行ってきたが、こんなに大きなサイズは初めてだった。設備改造でつくることも考えたが、それでもコスト的に難しいということが分かった。考えに考え新たに専用の簡易的な設備を使ってつくることにした。
「金型レス」の画期的な金属成形技術
最終的にたどり着いたラダーフレームの「金型レス」でのつくり方。それが後にトヨタ自動車と大豊精機が共同で特許を出願することになる「逐次ずらし曲げ成形」と呼ばれる加工法だった。
これは新たに開発した曲げ加工機を用い、パイプ状の金属を弱い力で少しずつ曲げ、さらに加工点をずらしながら成形していく加工法。
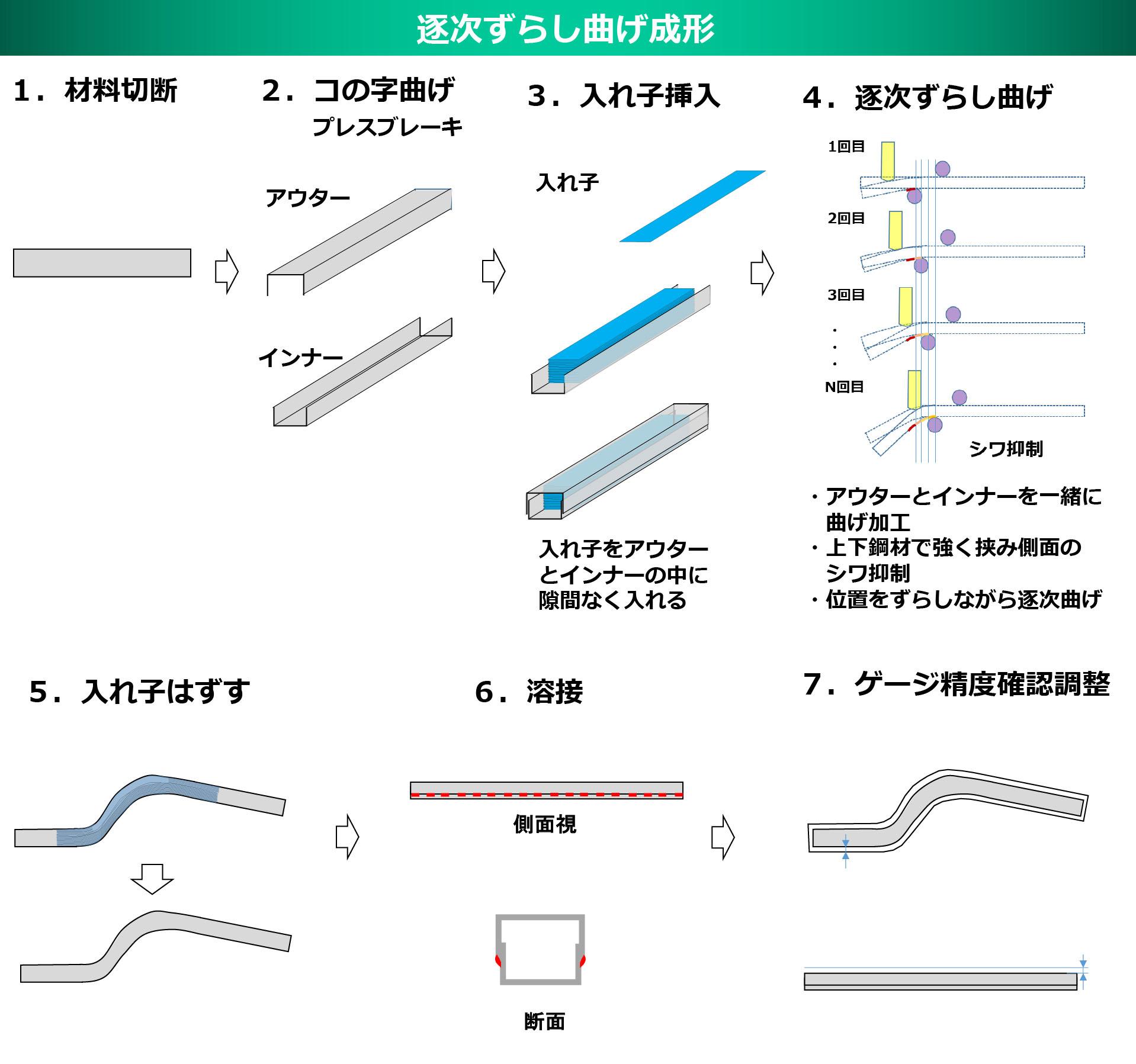
金属の曲げ加工ではどうしてもシワやゆがみの発生は避けられない。だがこの加工法では、アウターとインナーの間に入れ子*を隙間なく詰め、それを上下から強く挟むことで金属素材のゆがみやシワを最小限に抑えることができる。
*成形不良を防止するための部材
そして、狙い通りの形状に加工できたら、中の入れ子を外してアウターとインナーの側面を溶接する。
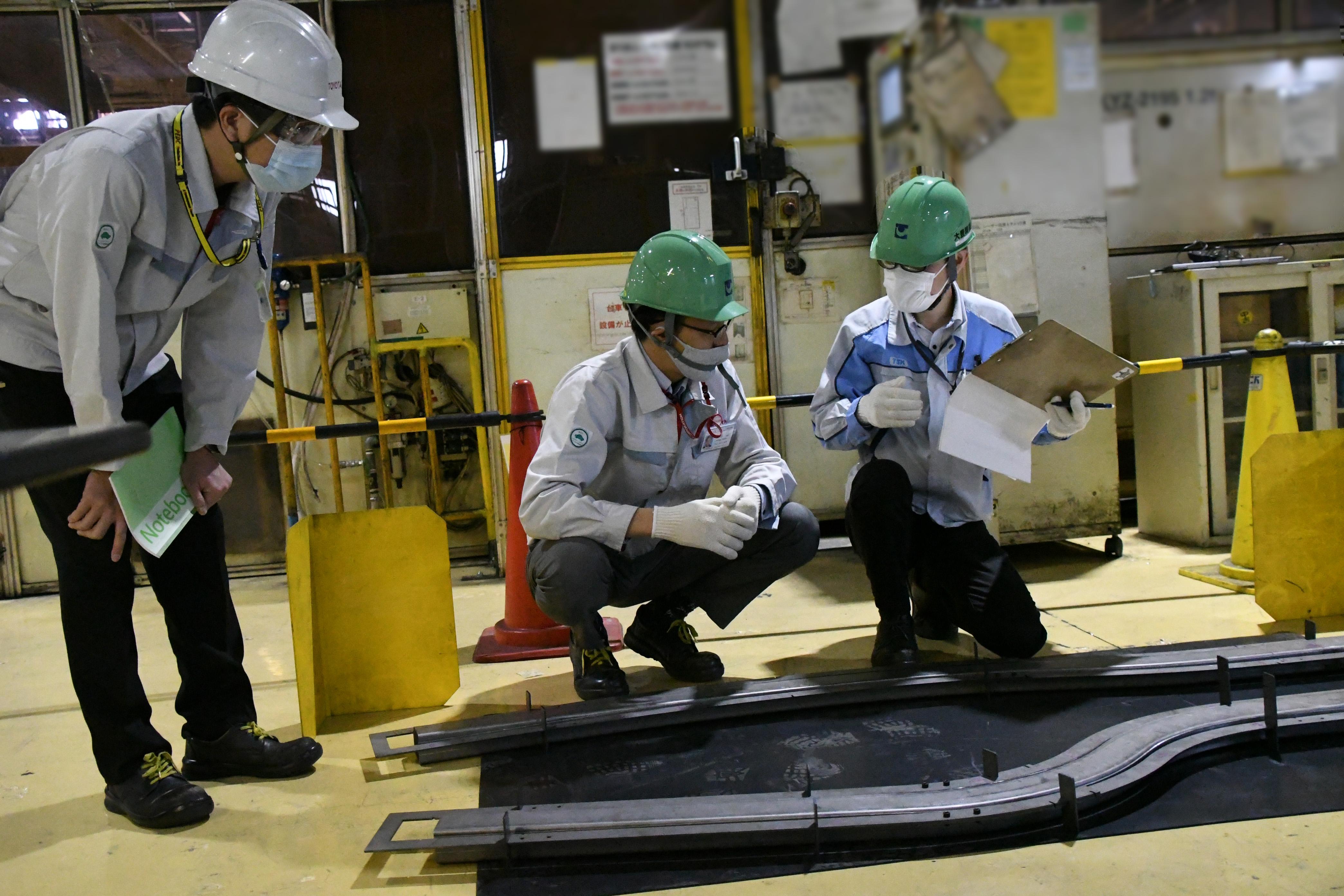
この方法に大豊精機の担当者も「これは、小さな角パイプ(サイドレール)の曲げ加工のアイデアを応用したもの。従来の方法では提示された予算での製作は絶対に無理でした。そしてこの制約があったから、新しい方法が考案できました。
ラダーフレームの製作は、プレスなら1000t以上の大型になります。金型も大規模になってしまう。この方法なら、10t程度の力で成形でき、専用金型も必要としません。これは画期的です。」と語った。
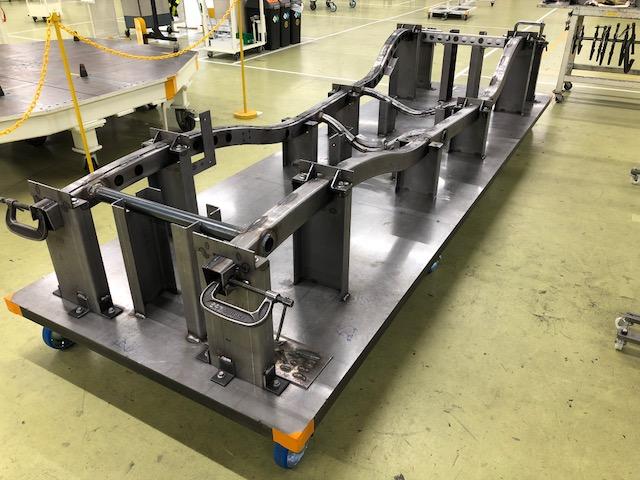
恒川
最終的には高い精度でフレームを仕上げ、しかもコストが金型を使った従来の方法の約半分に抑えることができました。今後社内外で、さまざまな用途に活用できると考えています。
トヨペット・レーサーと同様、もはや金型が残されていないクラシックカーなどをレストアする際にも、この「逐次ずらし曲げ成形」は大いに役立つはず。もちろんクルマ以外の少量生産のモノづくりにもさまざまな活用ができそうだ。
トヨペット・レーサーは70年の時を超えて、現役の技術者、技能者たちを刺激し、新しい技術のブレークスルーをもたらしたのだ。
後編ではラダーフレームの上、葉巻型のボディを構成するアッパーフレームと外板の製作についてリポートする。
(文・渋谷康人)