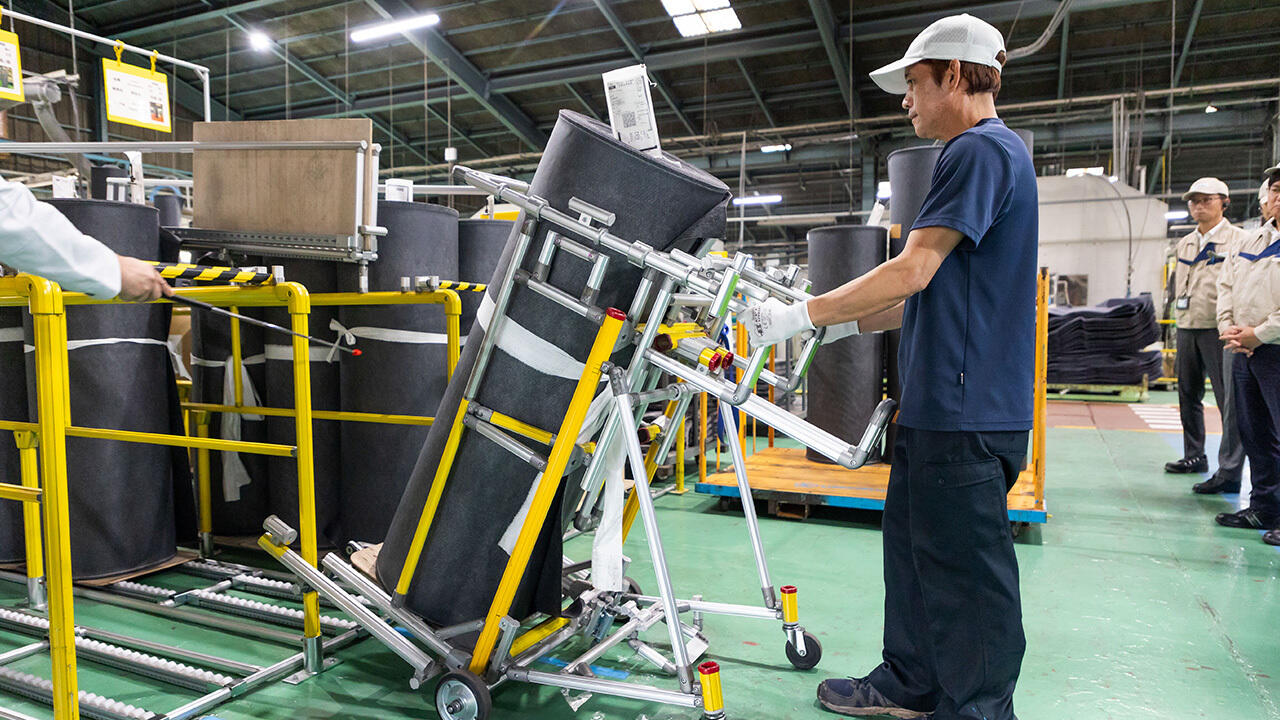
「トヨタさんが来る...」。トヨタ生産方式の積極的な取り入れに不安があった仕入先。だが一緒に改善に取り組む中で意識は徐々に変わっていき...。
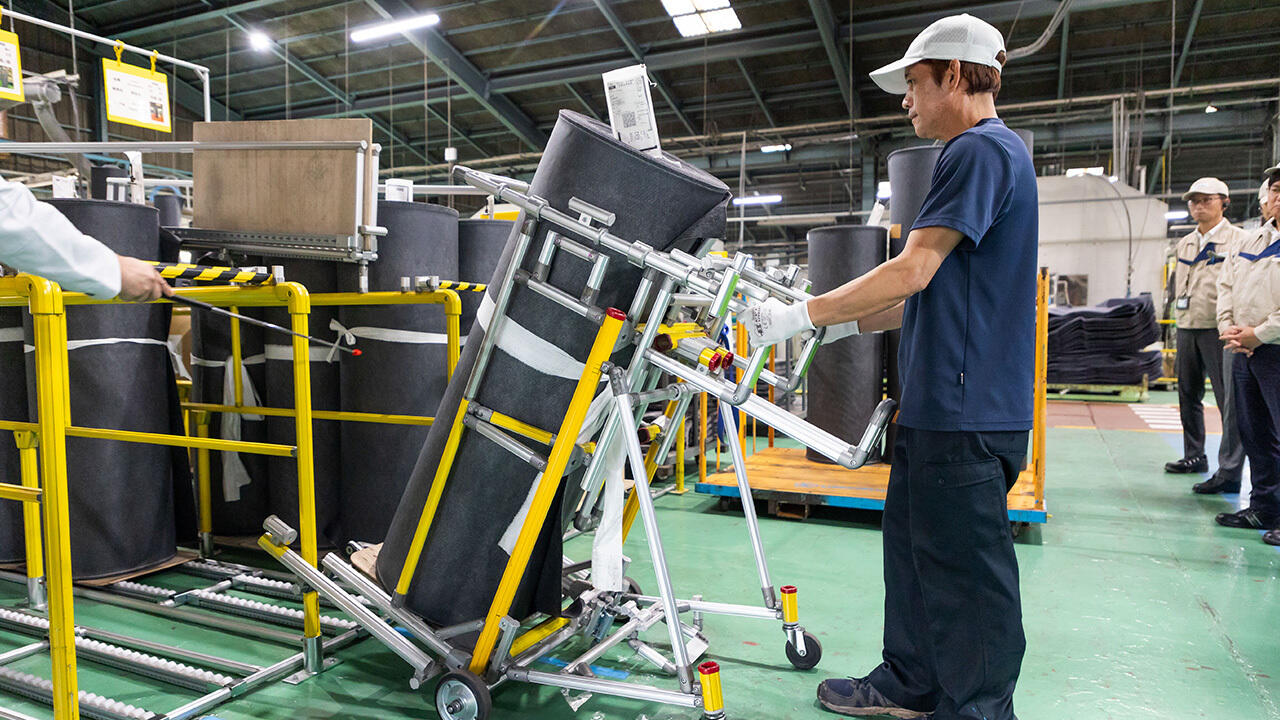
トヨタと仕入先との関係を探る連載。前回は、トヨタの調達部門が掲げるミッションやルールを紹介したほか、熊倉和生 調達本部長、加藤貴己 調達副本部長のインタビューを掲載した。
今回はトヨタが1次仕入先(Tier1)、Tier2とともに、Tier2現場の改善に取り組んできた活動を紹介する。
トヨタ生産方式(TPS)導入は生産性向上だけでなく、現場の意識にも変化を与えたようだった。
グループ連携活動
事例の紹介に入る前に、「グループ連携活動(グル連活動)」について触れておきたい。
グル連活動は、Tier2の困りごとに対しトヨタとTier1が一緒に解決に取り組む活動。もともとは、2015年にトヨタとグループのTier1間で情報や想いを共有する連絡会が発足したことに端を発する。当初はトヨタからの情報発信がメインの活動だったが、自動車産業の環境変化に対応するため、18年からは相互研鑽/調達力強化も推進。その一つとしてTier2の体質強化活動が始まった。
前回紹介した「SSA(Smart Standard Activity)」が品質・性能基準の適正化により原価低減につなげていくものだとするならば、こちらはTier2の生産性向上・働く環境面での改善活動だ。
活動では、まずTier2の困りごとを共有。現場でTPSを積極的に活用していくだけでなく、必要に応じてトヨタのグローバル生産推進センター(GPC)など調達以外の部門にも協力してもらいながら改善を進めていく。
2019年からスタートし、24年10月時点でTier2の21社が参加している。今回紹介する梅村工業もその一つだ。
からくり台車で安全運搬
梅村工業(本社・愛知県豊田市)は、クルマの内装部品のシステムサプライヤー(クルマの内装トリム*を一括で開発し、Tier2から届く製品を取りまとめる役割)である林テレンプの仕入先で、トヨタにとってはTier2にあたる。クルマのフロアカーペットを主力製品にしており、国内に3工場を持つ。今回グル連活動に取り組んだのは、その中の藤岡工場(愛知県豊田市)。
*自動車の室内に使用されている内張りの総称。
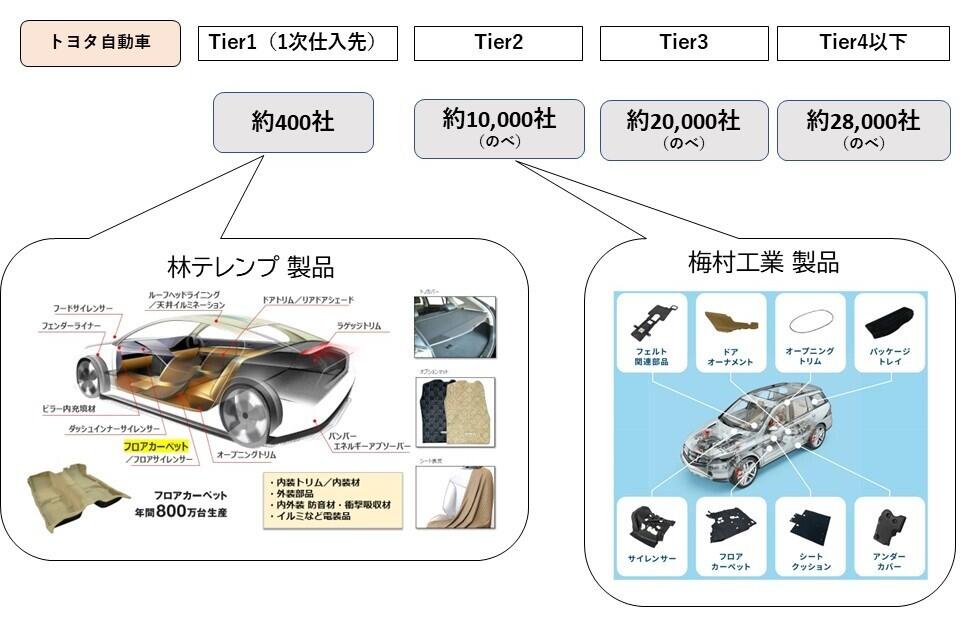
藤岡工場のフロアカーペット製造工程は次の通り。
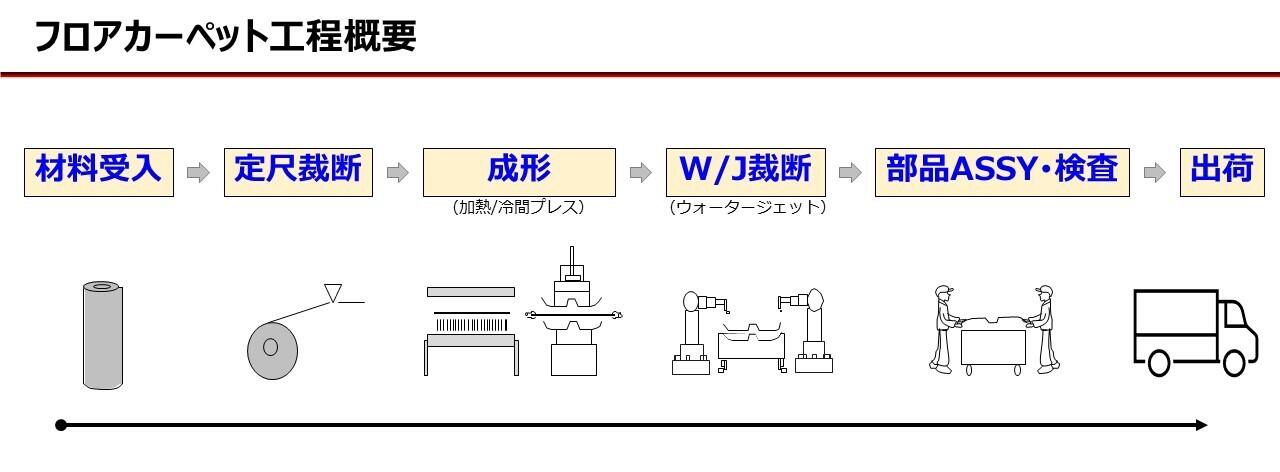
クルマごとに形状が異なるフロアカーペットだが、材料受入の段階ではロール状態でやって来る(この状態の材料は原反(げんたん)と呼ばれる)。
原反は車種によって異なるが、重いものだと90キロほど。グル連活動前は、トラックからパレットへ原反を寝かせて積んで工場内に移送。工場内で再度起こしてから台車に載せ替え、種類ごとにレーン分けされた保管場所へ運んでいた。
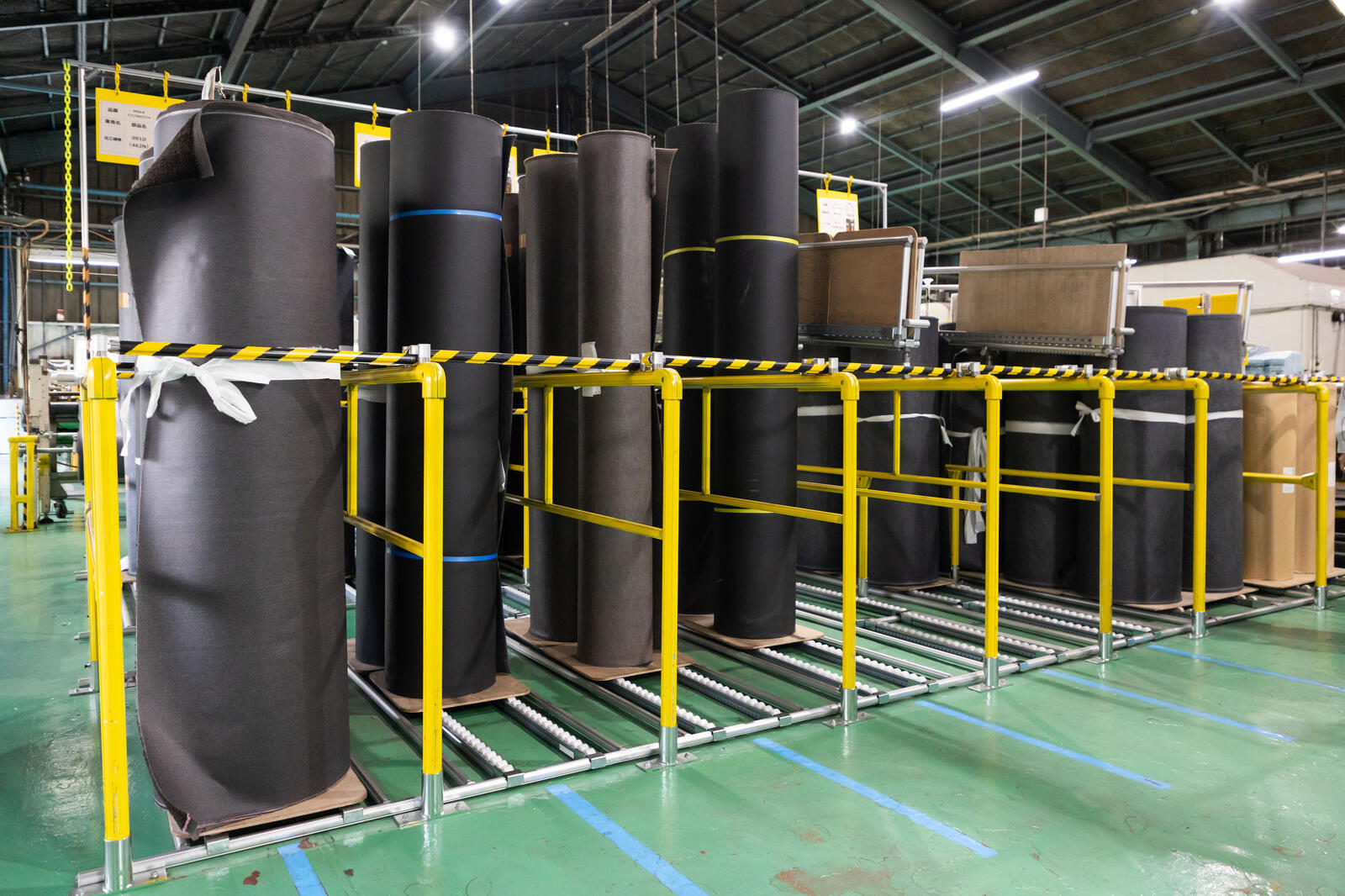
原反を起こす作業は従業員の体にも負荷が大きく、山積みの原反に登って行っているため、足元も不安定となり危険を伴う。
そこで梅村工業は活動を契機に、受け入れ時の原反を寝かせる工程を排除。トラックからパレットまで立てたまま納入するように変更した。以前は立てたまま運べるパレットがなかったこともあり、そういった運搬の発想もなかったが、トヨタや林テレンプが入ることで、今回の改善につながった。
こうした外からの視点で気づきを得られるのもグル連活動の利点だ。
下の動画は改善前後の作業の様子。改善前の作業者の大変さが分かってもらえるだろう。
この動画の改善後に映っている台車(原反運搬台車)は、GPCの職人と一緒につくり上げたもの。センサーや制御機器はなく、ギアやシャフトを組み合わせた“からくり*”が用いられている。
*電気や高出力モーターなどを使わず、重力やテコなどを利用して効率を上げたり作業を楽にする道具や仕組み。例えば「足で開くごみ箱」や「自動開閉の傘」など、身近な道具にも応用されている。コストを抑えられるとともに、省エネにもつながっている。
従来の台車にはなかった、原反が前方に転倒するのを防ぐバーが取り付けられているため、安全に保管レーンまで運ぶことが可能だ。
また、原反を保管レーンに移す際にもからくりが活躍する。これまでは、「レーンに原反の受け板をセット→台車ごと原反を受け板に載せる→台車を引き抜く」という手順で、台車を引き抜くときに、原反が倒れないように手で支えていなければならなかった。
新しい台車は、パレットから原反を載せ替える時点で台車に受け板をセットしているので、引き抜く必要がない。レーンへ移すときも、押し込みバーを使って滑らせるように移動できるようになっている。実際の様子をご覧いただきたい。
作業者からは、「『倒れないように』とか『転ばないように』という気遣いがなくなって、やりやすくなった」という声が上がっているという。
こうしたからくりを使った改善は、原反納入後の定尺裁断工程にも見られる。
費用をかけずに知恵を出し合う
原反を必要なサイズ分引き出し、シート状に切り分ける定尺裁断。以前は一度切り始めると、ロール状の原反すべてを裁断しきっていた。
これは原反を余らせると保管場所に戻さなければならず、この時に発生する再び立てる作業が負担になるため。結果、切り分けたシートの過剰な在庫が生まれ、広い保管場所も必要だった。
そこでグル連活動を通じて、必要数だけ裁断するように変更。保管場所が36%ほど削減されたほか、原反1本を裁断しきるために生まれていた残業も減り、急な変動にも強くなった。
この変更によって追加された、裁断後に余った原反を起こす作業。これを解決するためにつくったのが、原反起立台車。てこの原理を応用することで、床に置いた原反を力任せに起こすよりも、約4分の1の力で起こすことができるという。
梅村工業・藤岡工場 近藤貴彦 工場長
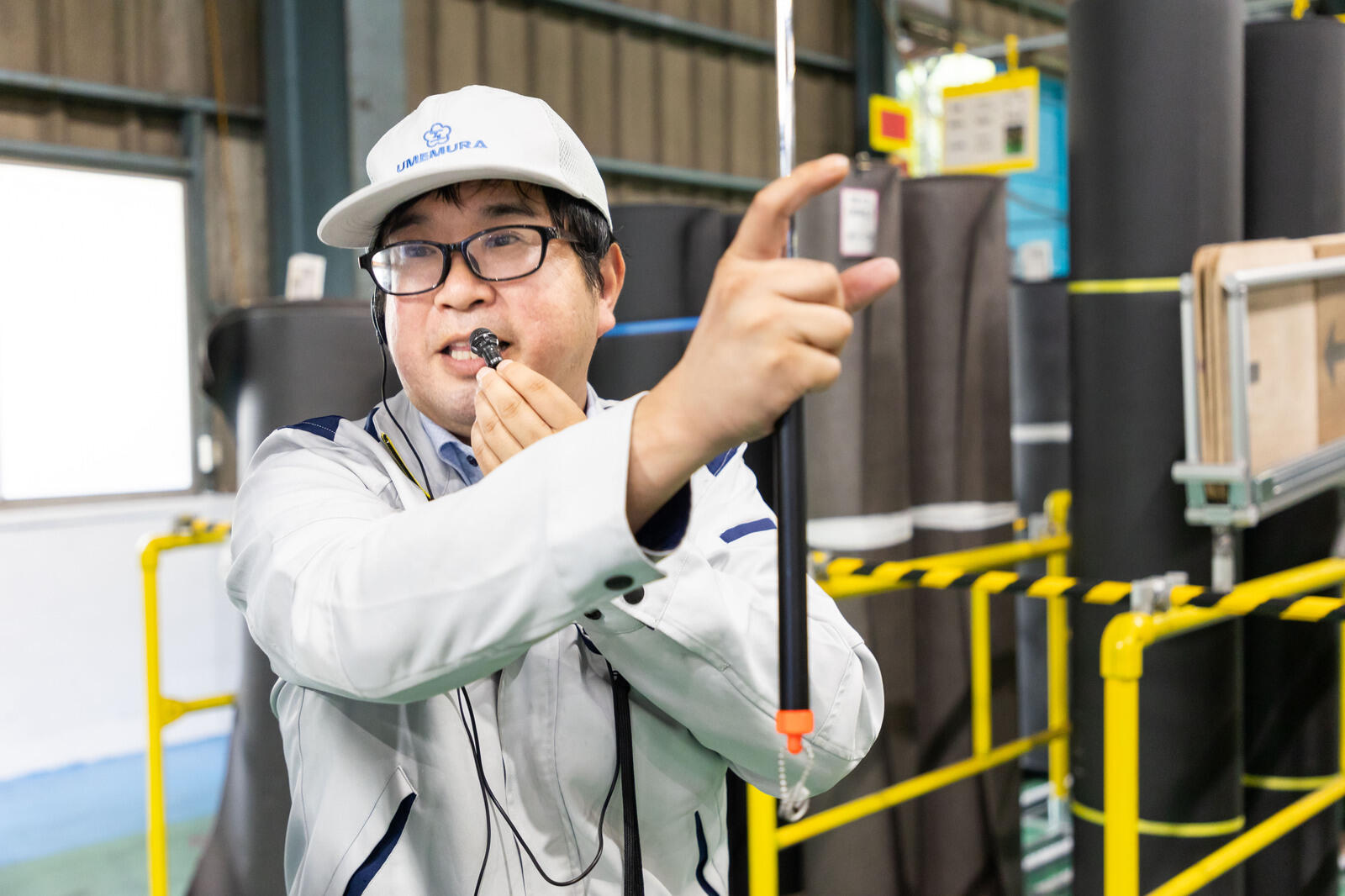
この原反を起こす作業というのは、以前はほとんどありませんでした。
今回、生産に必要な分だけ原反を切ろうと仕組みを導入しましたが、その結果原反の残りができます。当初は(起こす作業が)危ないなと困っていました。
今は、その仕組みを導入しつつ、からくり台車があることで作業者からも「簡単に起こせる」、「安全だ」という声をもらっています。
原反運搬台車や起立台車は、梅村工業で試作し、GPCと一緒に改良点を検討、さらに試作というサイクルを繰り返して生まれたもの。費用をかけずに知恵を出し合う、トヨタの改善マインドが形になったものだ。
現場からは「作業者が変わっても使えるような治具をつくっていこうと思っています」という声もあり、グル連活動が終わった後も改善は続いている。