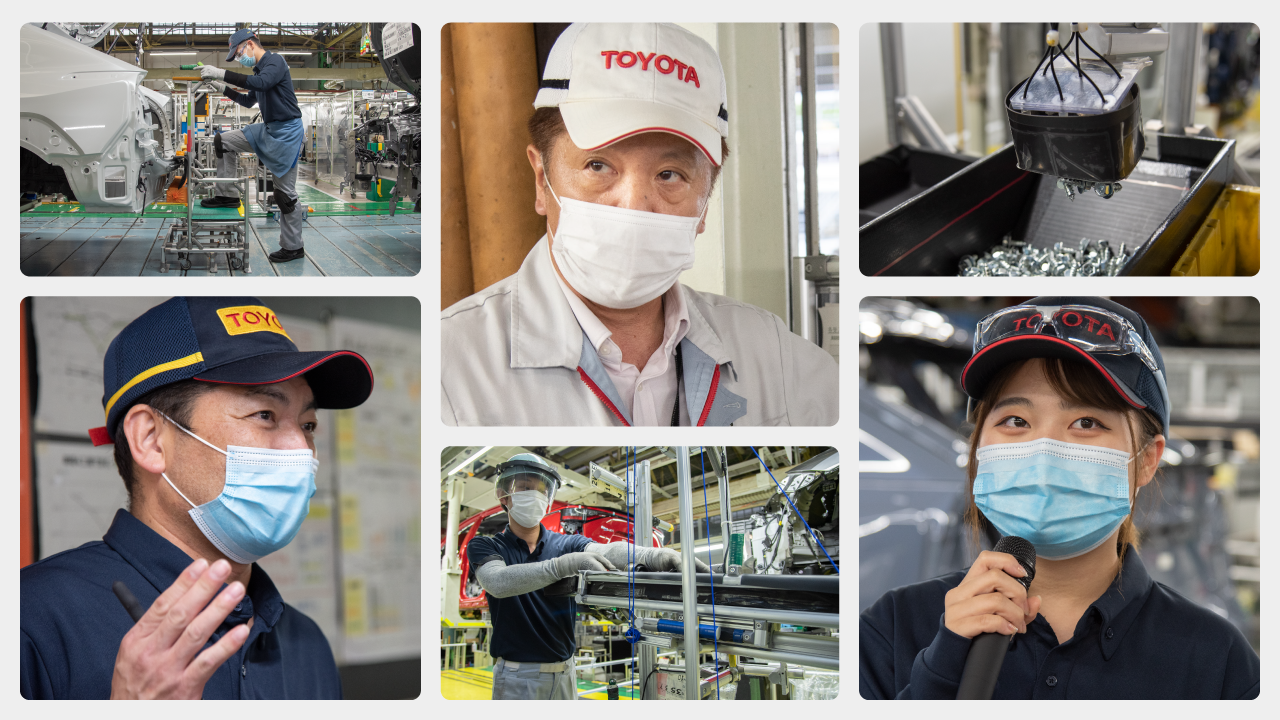
色だけじゃない。大きさも、動力もバラバラのクルマが同じラインを流れていく。不可能を可能にした知恵と工夫の現場を取材した。
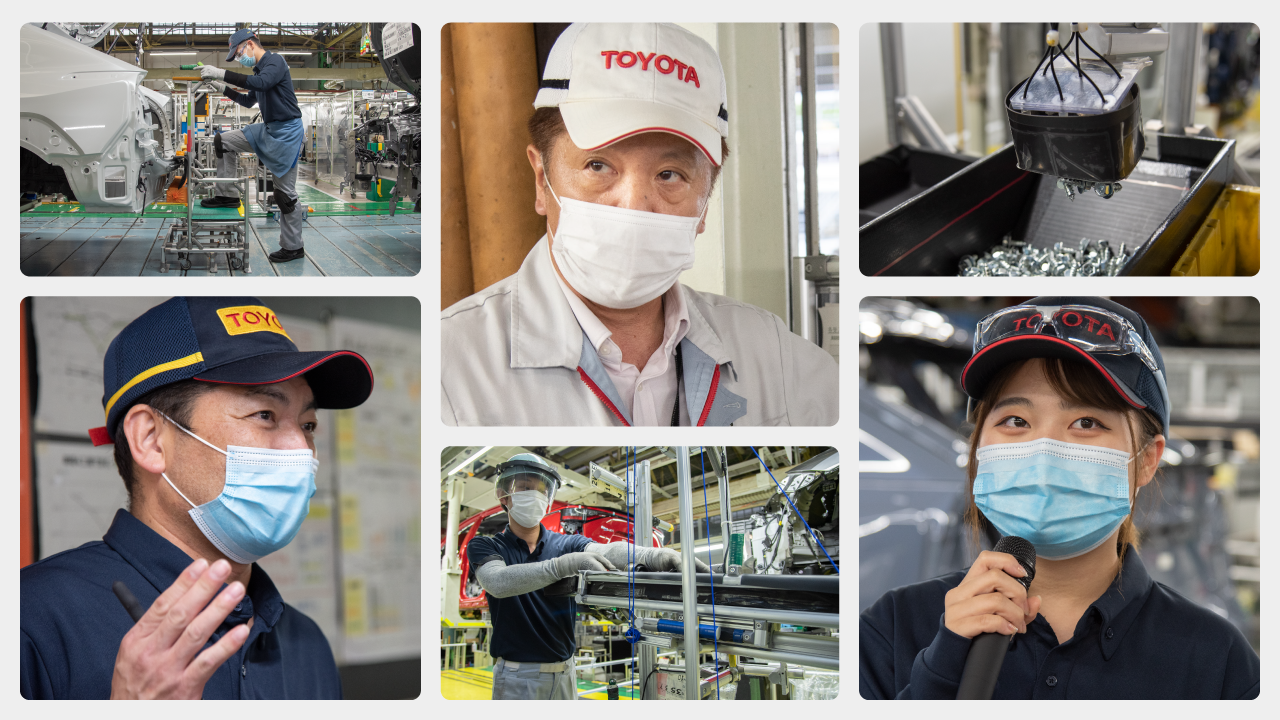
6月、岸田文雄 内閣総理大臣がトヨタの元町工場(愛知県豊田市)を訪問した。総理は現場を視察した後の記者団の取材で、開口一番、次のように答えている。
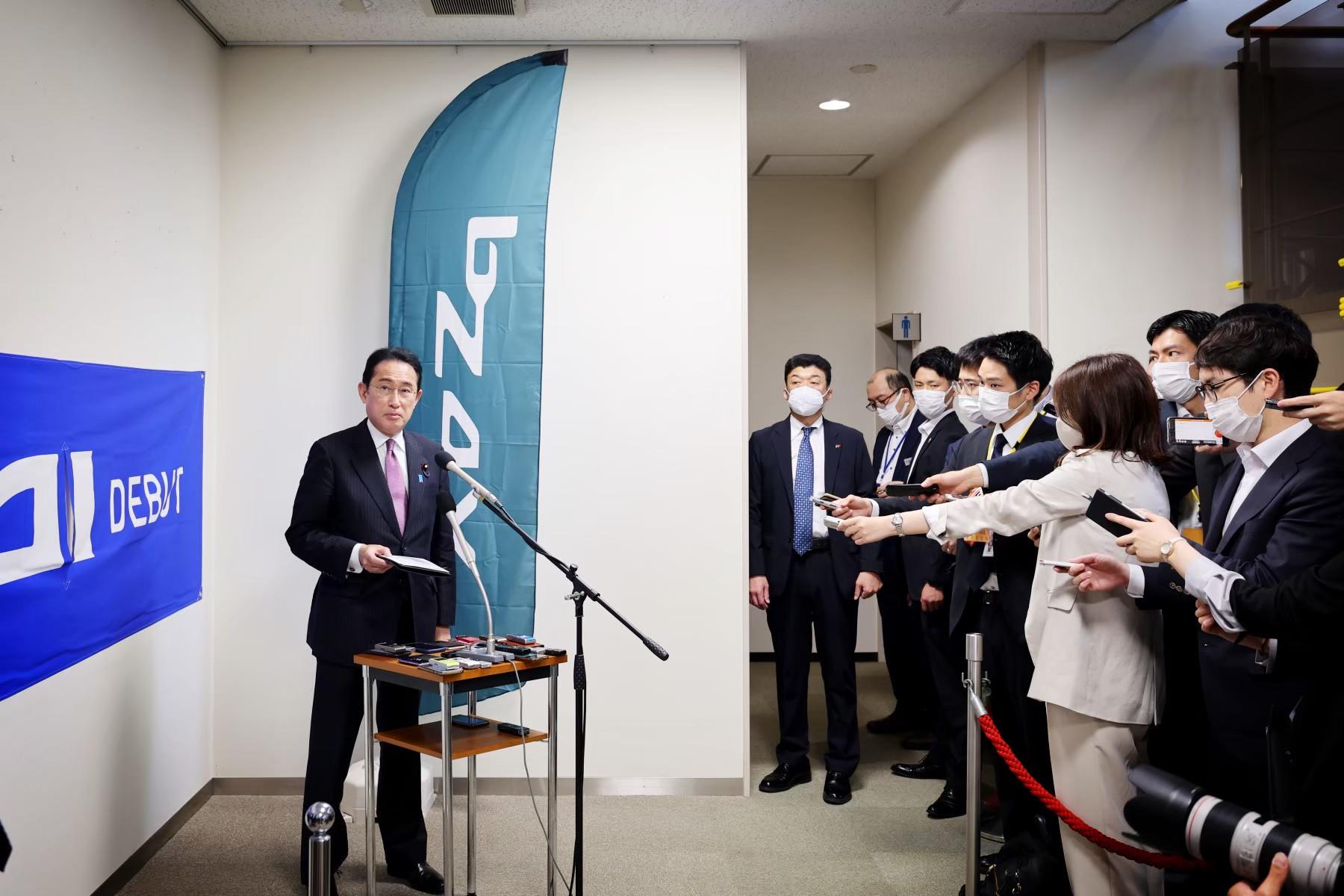
「電気自動車をはじめ、異なる種類のクルマを一つのラインで一緒に生産し、カーボンニュートラルに向けた多様な選択肢を追求する現場を拝見しました」
「製造工程に手づくりのさまざまな工夫を凝らす“カイゼン”という言葉が世界中で使われていますが、まさにその現場を見させていただいたと感じ、感銘を受けました」
流れるクルマの形は、セダン、SUV、ミニバン。クルマの種類は、ガソリン車、ハイブリッド車(HEV)、電気自動車(BEV)、燃料電池車(FCEV)と何もかも違うはずのクルマが目の前を通り過ぎていく。
この“混流生産”もさることながら、今年の元町工場は、これまでに経験したことのない大きな挑戦に取り組んでいる真っただ中だという。先の見えない非稼働が続く工場で、改善を続ける現場の知恵と工夫をレポートする。
混流に向き合ってきた元町工場
クラウンの故郷として知られる元町工場の操業開始は1959年。それまでトヨタの主力車種はトラックだったが、国産乗用車をつくるという創業者・豊田喜一郎の悲願を形にする乗用車専用工場として立ち上がった。
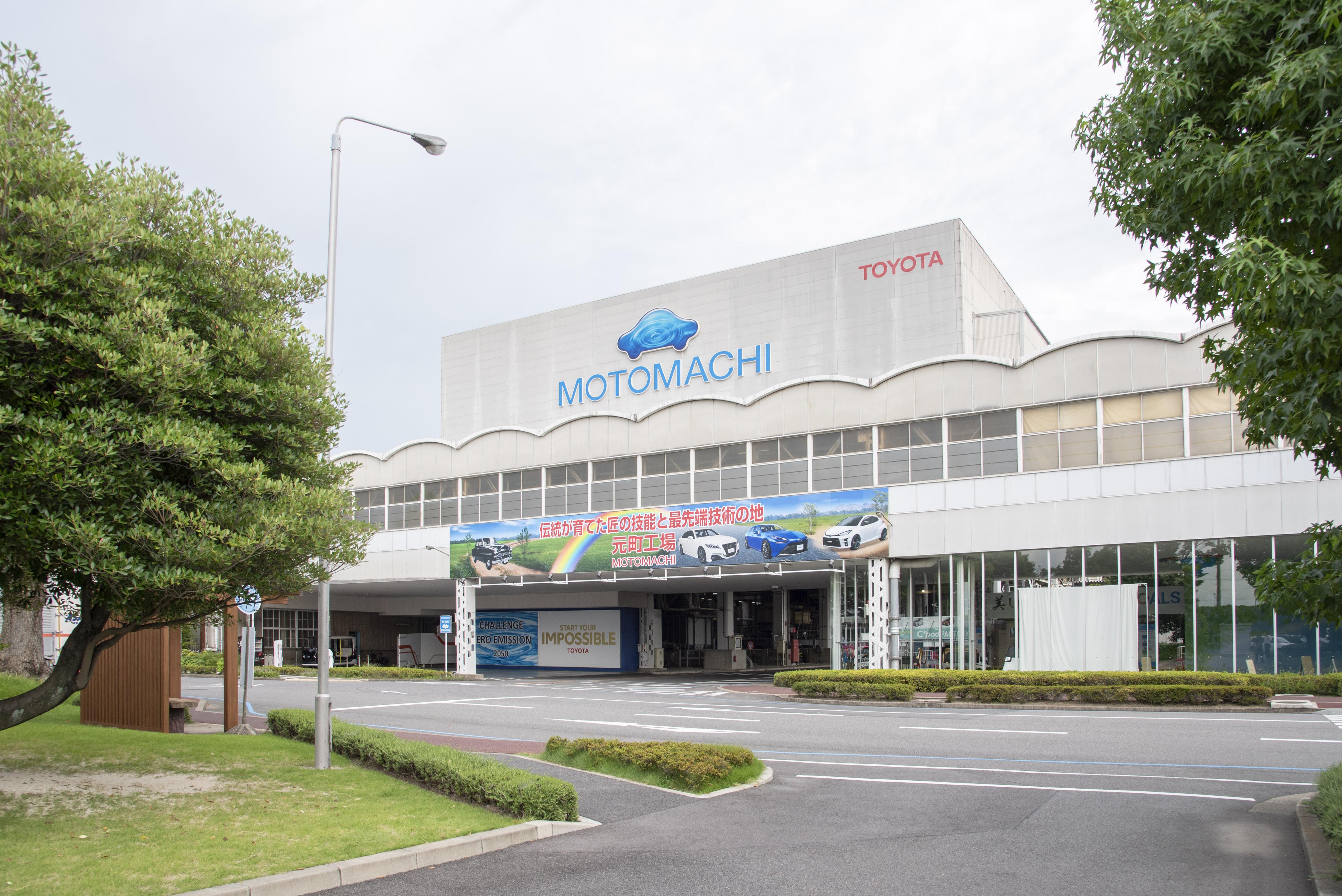
同工場の生産のピークは、日本がバブルに沸いた1990年。マークIIとクラウンで、44.5万台を送り出した。
しかし、翌年以降、台数は減少をたどり、ここ20年は1直、2直稼働を繰り返している。
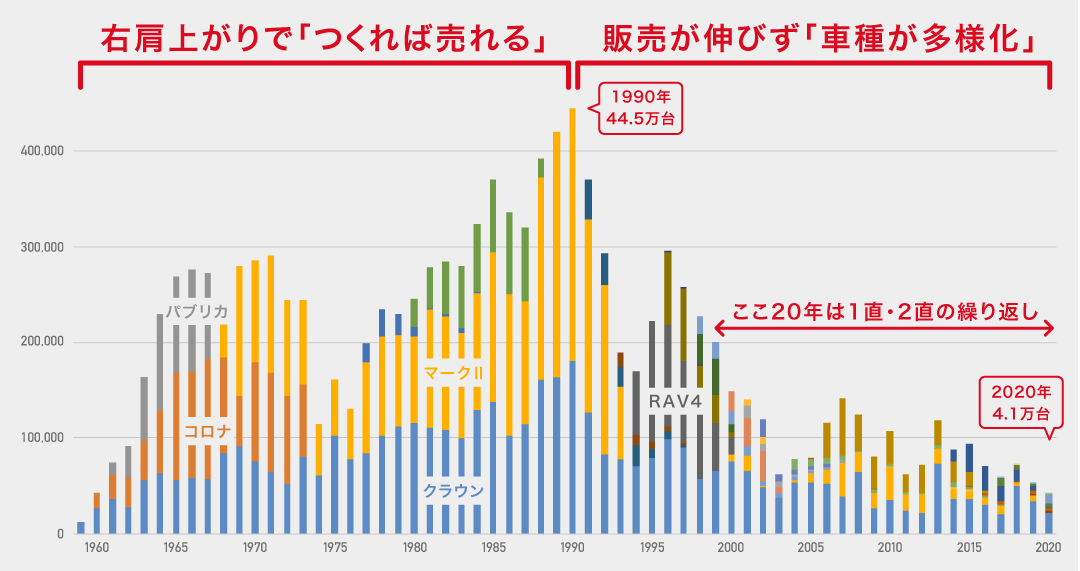
また、この年を境に手がける車種の数も変化。それまで生産していたのはせいぜい3車種で、つくれば売れる時代。
以降は5~6車種をつくるのが当たり前になり、新型車が立ち上がっても、数カ月で販売が伸び悩む時代に入る。
他の車両工場が短いタクトタイム(工程作業時間)で2直稼働を続けるのとは対照的に、元町工場は2直になっても、数カ月後には1直に戻るという歴史を繰り返してきた。そんな時期をへて、今年はこれまでに10車種を生産している。
従来から複数の車種を同じラインでつくってきたが、今回は、クルマのボディタイプも、パワートレーンも異なり、混流のレベルは1段も2段も上がっている。
同工場の現場のおやじであり、入社以来ほとんどの時間を元町で過ごしている明里雄二次長(元町工場総組立部)は「どんなクルマが来ても、つくれる工場にする」と意気込む。
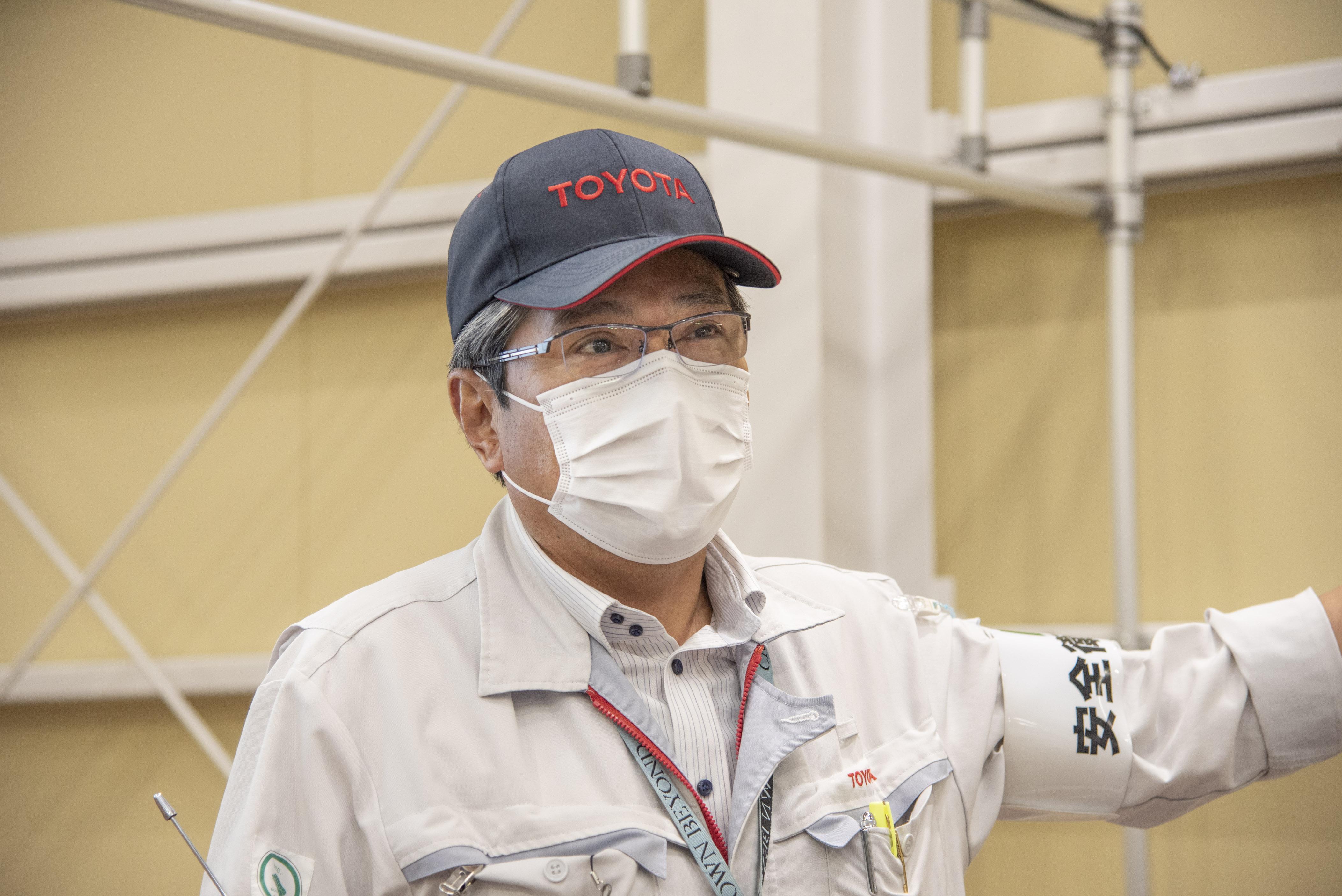
さらに今年は元町工場にとって約1年で4つの車種を立ち上げる異例の年でもある。
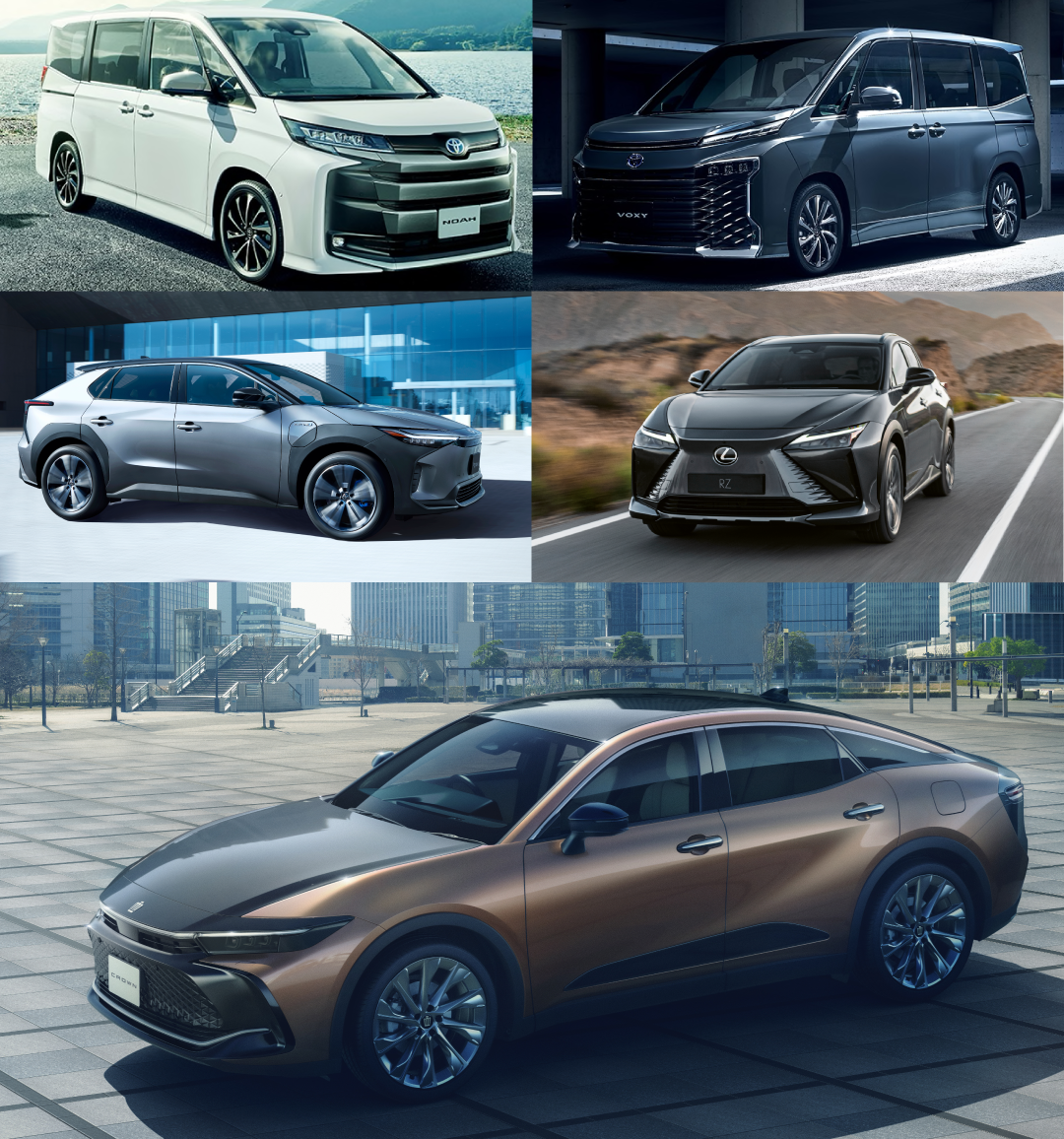
この前代未聞のプロジェクトに備え、第1組立ラインでは、昨年4月から年末にかけて、要員を募集。他工場から多くの社員に異動してもらい、期間従業員や派遣社員も採用。
多いときは週20人のペースで人が増え、今では、物流担当も含めて1000人。うち、6割以上が新しい顔ぶれとなった。
教育や訓練を重ねて、4月には連続2交代を立ち上げ、今月に入って3車種目となるクラウンをラインオフ。前例のないチャレンジは今なお進行中だ。
混流に対応した移動式踏み台
流れてくるクルマの形が違えば、働く人の作業姿勢も変わる。特にSUVのbZ4Xのバックドアは大きく、クルマの後端から身を乗り出してワイヤーハーネスを通そうとしても、なかなか手が届かない。
組立では、両手で行う作業は奥行き700mmまでを基準としているが、bZ4Xはそれをはるかにオーバーする1000mm。立ち上がりへ、改善が急務となっていた。
そこで、山中皇士さん(総組立部第1組立課)が考えたのが、部品や工具を載せるワゴン台車と一体化した移動式の踏み台だ。
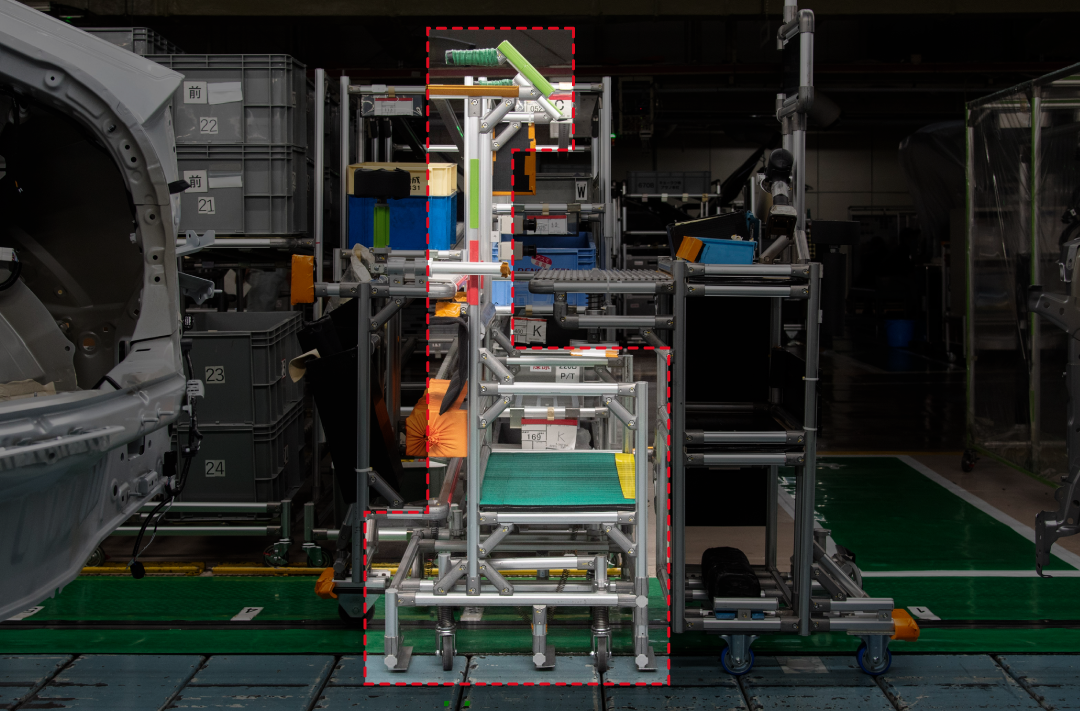
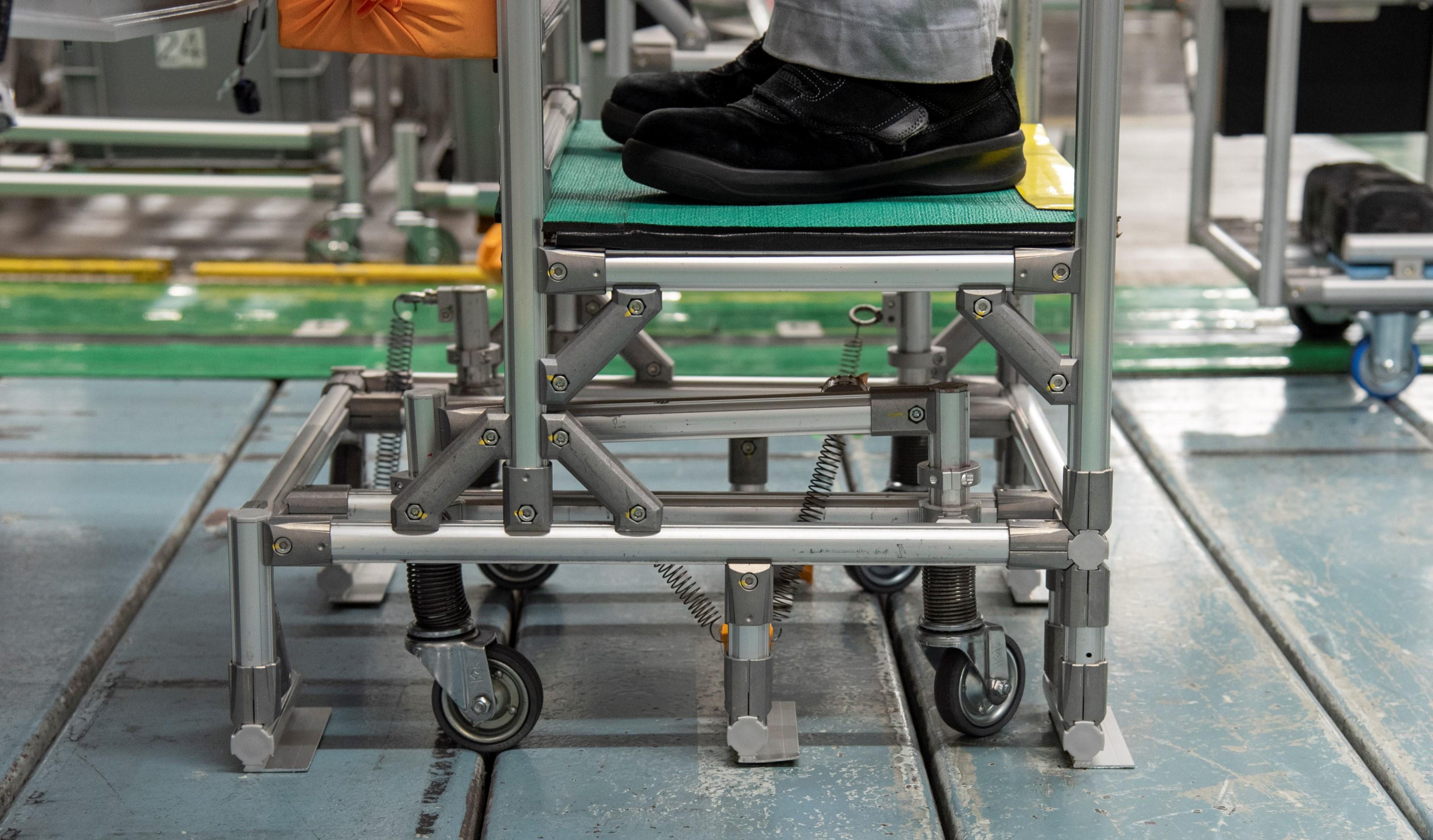
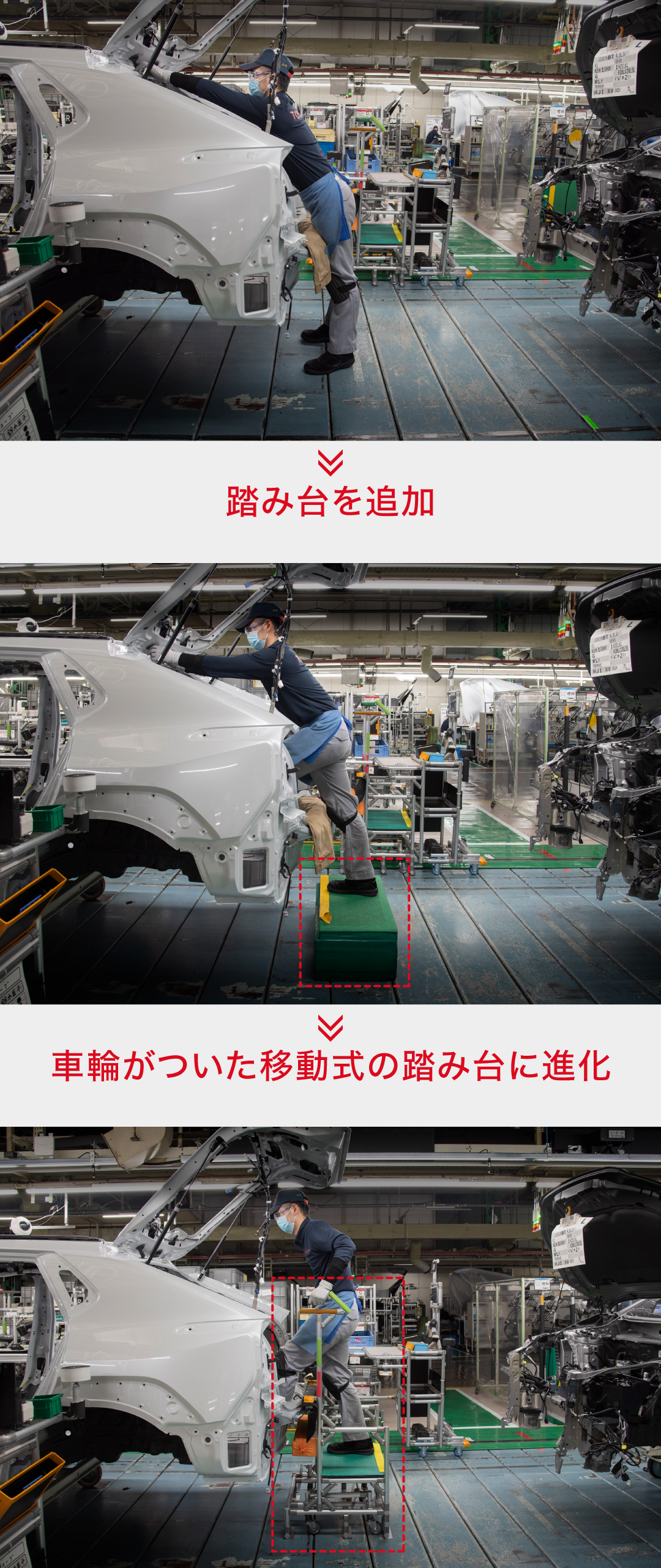
踏み台の導入で、姿勢が改善されると、体への負荷が減ってラクになっただけでなく、目視でしっかり作業ポイントが確認できるように。
山中さんは「作業品質の向上にも貢献できたと思う」と改善の効果を語った。
混流で踏み切った物流改革
車種が増えると、部品点数が増える。第1組立ラインの部品の受入場は2700m 2 の広さだが、4プロジェクトが立ち上がると、スペースが不足する。
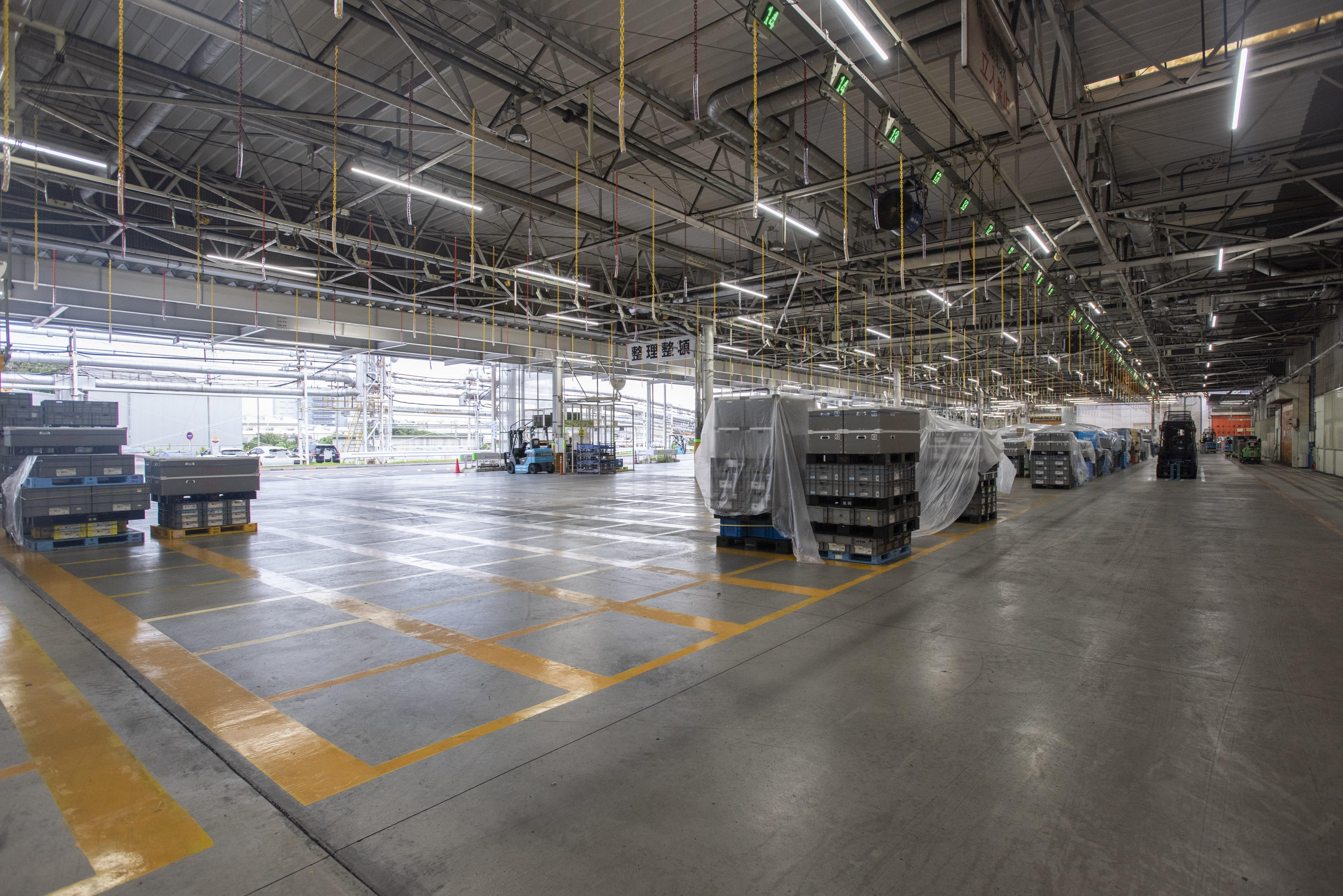
そこで、3月末、ラインから離れた別の建屋に部品の受入場を立ち上げた。もちろん、それだけでは非効率なので、工場が抱える課題を解決できるよう知恵を絞った。
元町工場の組立建屋は東西に細長く300mある。従来、受入場は東の端に1カ所しかなく、そこから建屋をぐるっと回って部品を届けていた。
そこで、新しい受入場に届いた部品は、大型トラックで工場建屋の西側まで運び、直接ラインに供給。従来の受入場と東西で半分ずつ、部品供給を分担するようにした。
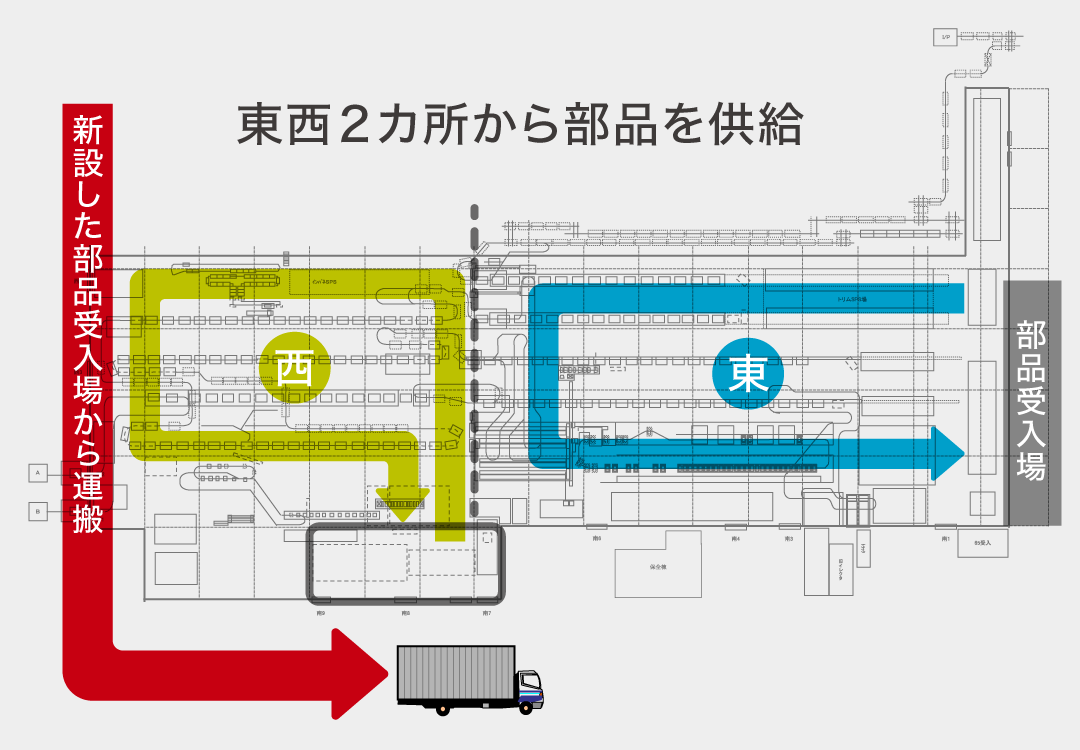
このプロジェクトを担当する小谷一博工長(総組立部物流課)は「物流車両一台当たりの走行距離を抑えることができ、工場内で発生していた渋滞も緩和することができた」とその効果を語る。
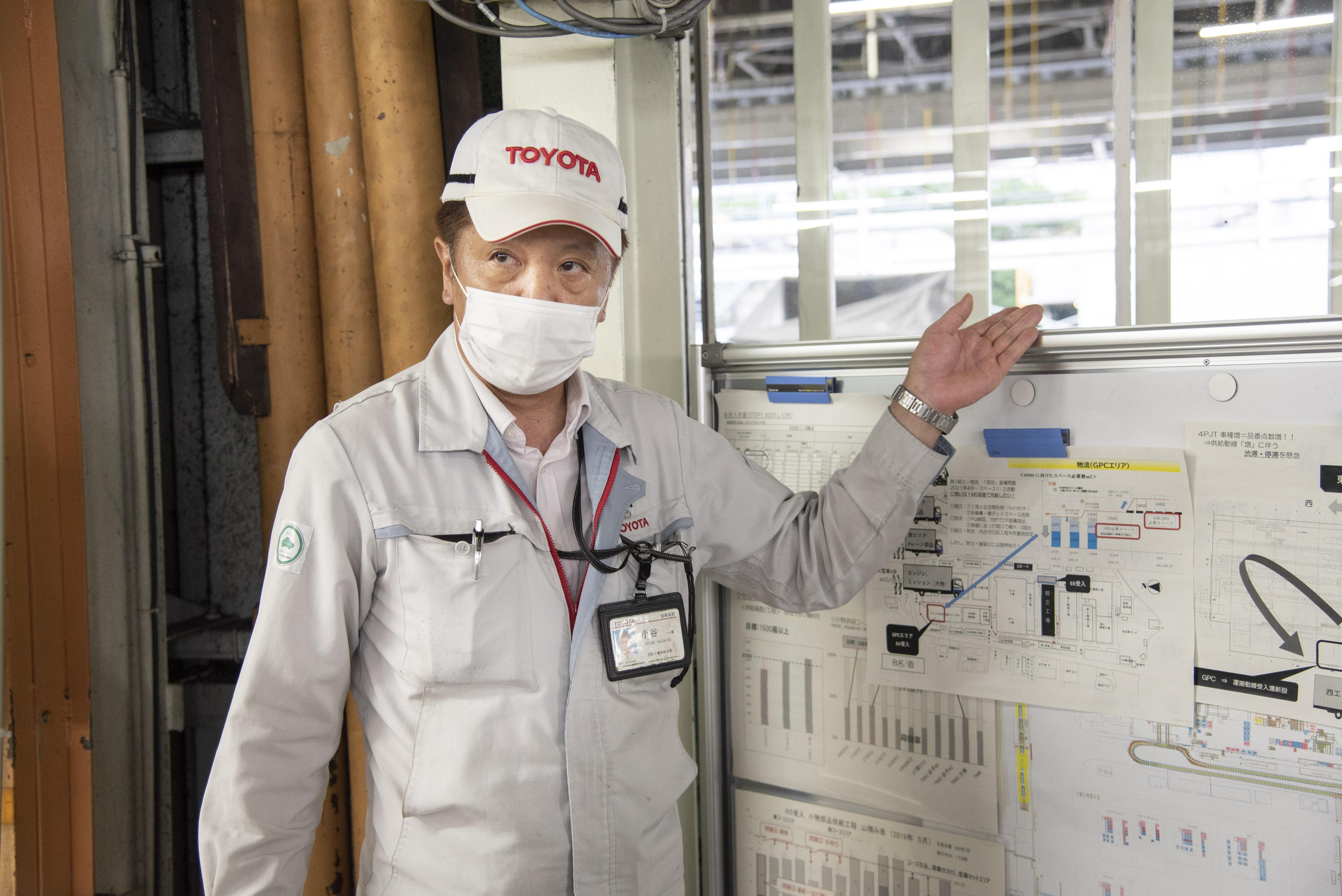
あわせて、受入場の新設に伴う大型トラックやフォークリフト作業に対応するため、訓練プログラムも立ち上げ、従業員の新たなスキルの習得を進めている。
一石二鳥の床色改善
クルマのプラットフォームの組立を行うシャシー2ラインはほかとの違いが一目でわかる。床が黄色と緑で塗り分けられているのだ。
車両を吊り下げるハンガーにぶつかり、仲間にケガをさせないよう、危険が視覚的にわかる黄色を取り入れたが、他の場所と比べて、70ルクス明るくなるというおまけの効果もあった。

このラインでは、クルマの床下を見上げるようにして作業する。黒などのダークカラーのクルマでは、ボルトやゴムをつける際、穴の位置がよく見えないという課題があった。
この対応として、過去には蛍光灯を床に付けたり、ヘルメットにライトつけて作業をしていたが、作業者からは「光が強すぎて、かえって見づらい」と言われていた。
それが、床色を変えたことで、「蛍光灯をつけるほど眩しくなく、ちょうどいい明るさ」(明里次長)に。働く人の安全のための改善が作業性の向上につながった。
Executive Fellowの河合満おやじが現場を訪れた際には、こんな言葉も残していったという。
「このラインでは、エアーやモーターなどの動力を使わないだけでなく、明るくするのに電気も使っていない。これが本当のカーボンニュートラルの組付ラインだ」
新しい仲間と受け継ぐ現場の精神
先に紹介したように、第1組立ラインの6割を超える人が新しいメンバーだ。平時よりコミュニケーションが求められる状況だったが、そこに厳しさを増すコロナ禍。
休憩時間の会話も減り、工場の非稼働で休みの人も多く、職場の仲間と談笑できる時間は限られていた。しかし、その間に取り組んだ改善活動を通じて、それぞれが少しずつ打ち解けていったという。
新入社員の山崎瑠菜さん(総組立部第1組立課)は配属当初、先輩から「やりにくい作業はないか」と聞かれたが、初めて取り組む作業に「何がやりにくいのかさえ分からず不安だった」という。
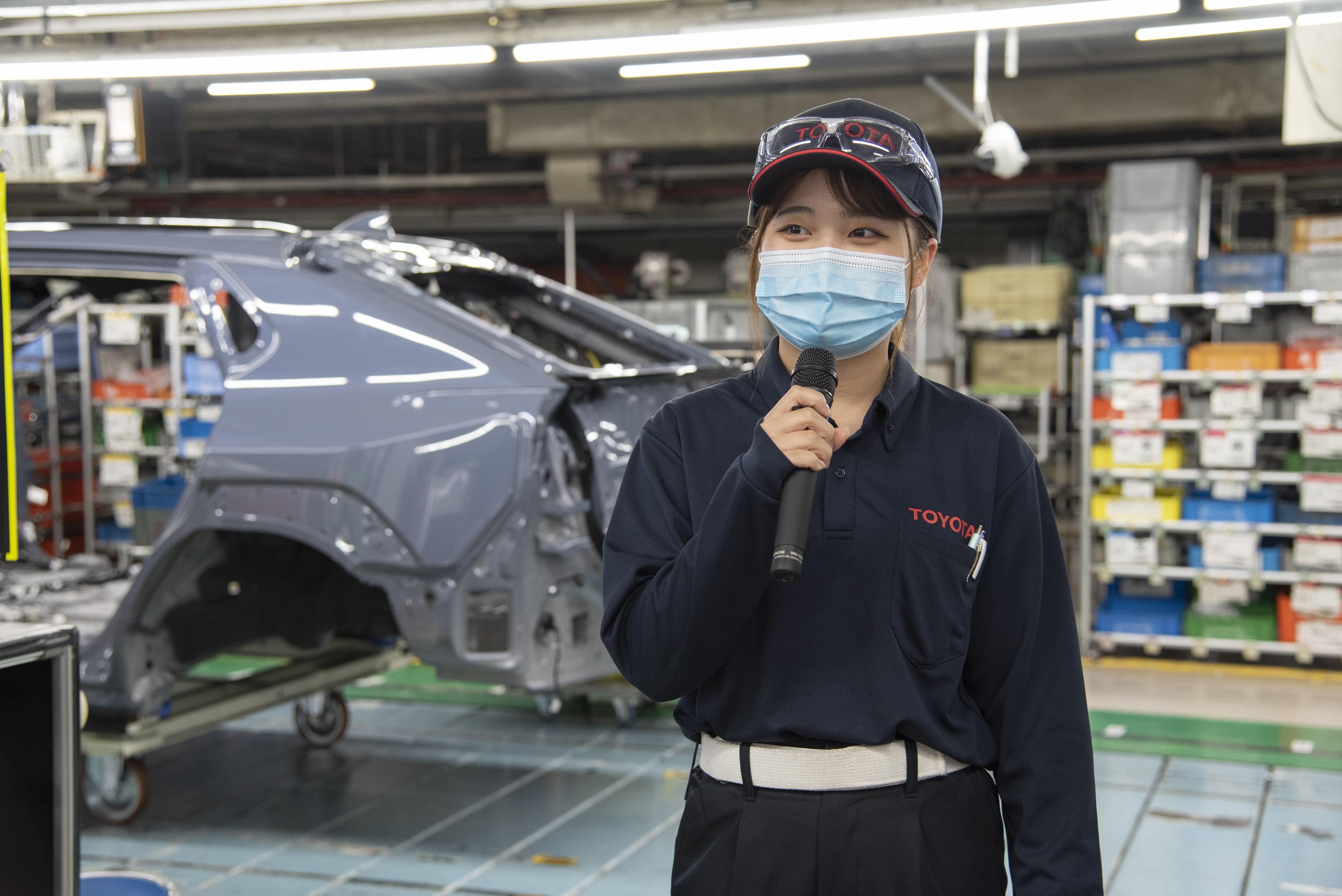
そんな山崎さんの作業を見た上司や先輩がやりにくそうなしぐさを見つけて、アドバイスをくれた。そのうちの一つが持ち運びを行う部品箱、通称「弁当箱」の改善だ。
山崎さんの工程では、インパクトというボルトの締め付けをする工具を2種類使用する。
従来は片方のインパクトで作業を終えると、一度、部品や工具を置く台車に戻り、もう一方のインパクトと交換して再び作業。一つのクルマをつくるのに、台車との間を2往復していた。
しかし、「弁当箱」に穴をあけ、フックをつけることで、部品と2つのインパクトを一度に運び、作業中はクルマに固定できるようになった。
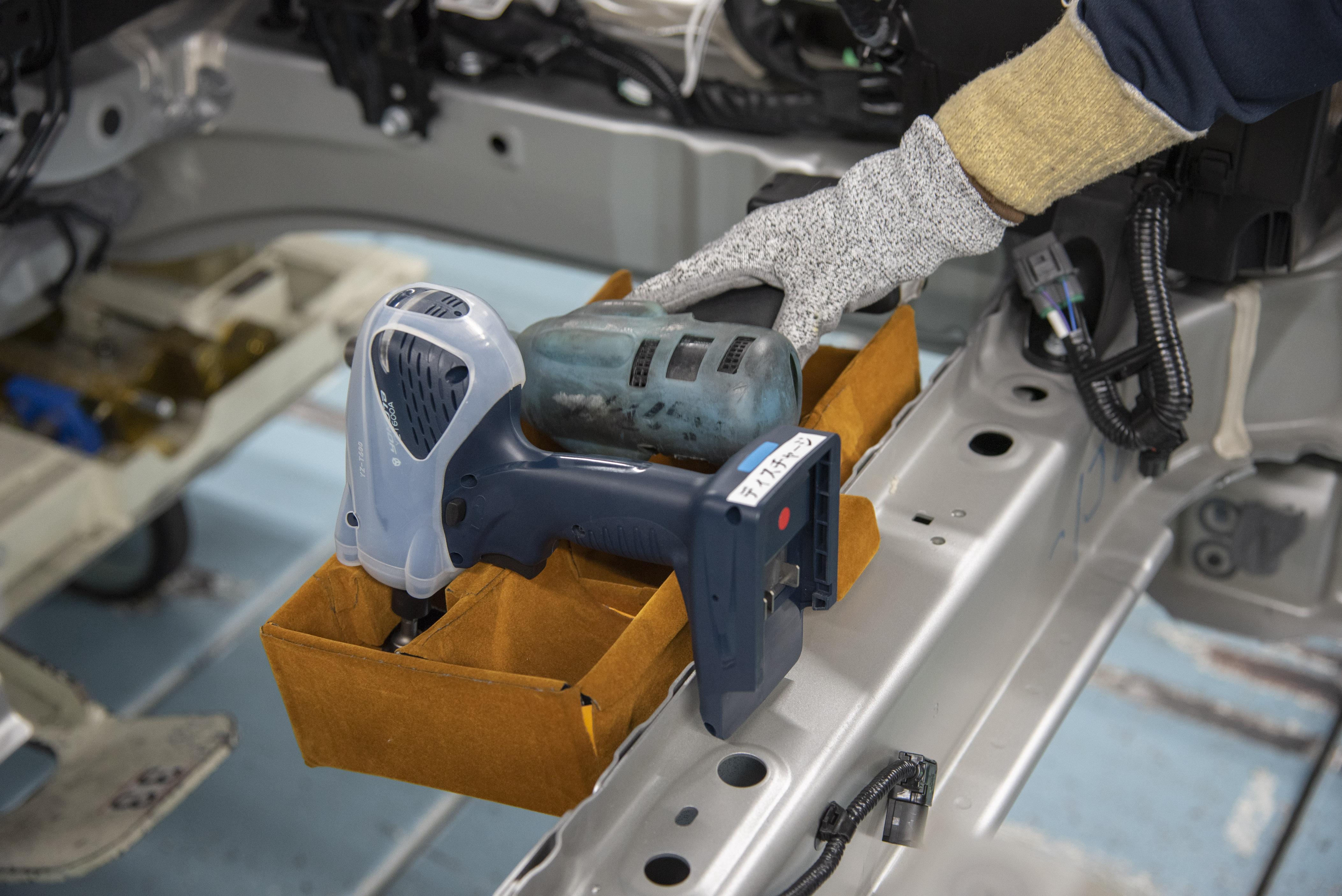
インパクトが安定するよう、穴の大きさや支点の形状も工夫。「改善を通じて先輩たちと仲良くなれたし、改善のやり方についての知識も身に付いた」と笑顔で語った。
ドアラインのチームリーダーを務める堅田守班長(総組立部第1組立課)は去年6月、エンジンを生産する下山工場の加工職場から異動してきた。
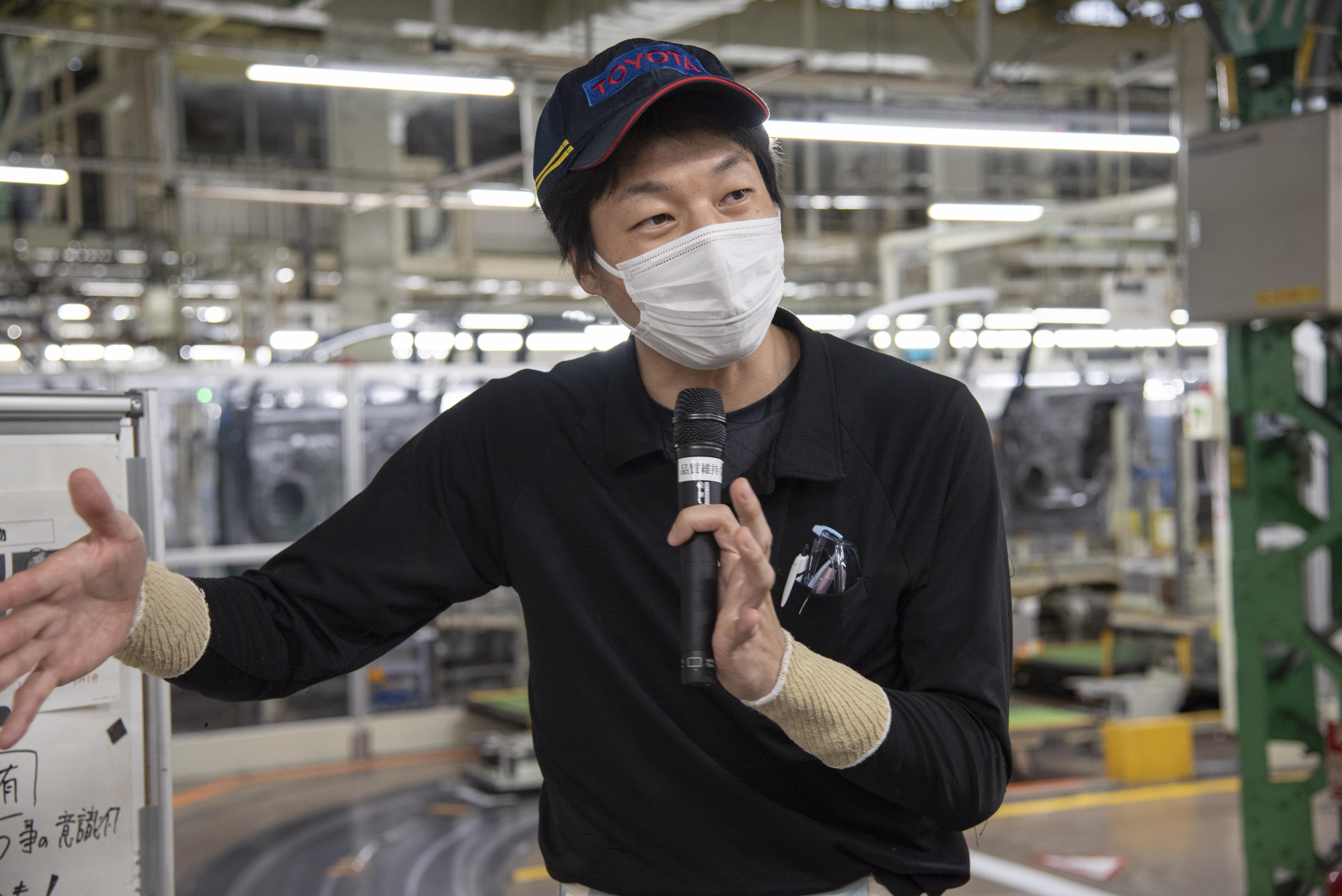
加工と組立では、仕事がまったく違う。不安を抱えながらも、新しい職場でリーダーとして仕事を覚え、同じように、初めて組立に関わるメンバーをまとめる立場を任された。
大きな環境変化を迎えるときには、基本がおろそかになりがちだ。そこで、落下物の対応について、メンバーの意識付けと改善に取り組んだ。
動いているラインで、落とした部品を焦って拾おうとすると、ケガの原因にもなるので、「落としたら上司を呼ぶ」というルールを改めて徹底。さらに部品を落とさないようにする工夫にも取り組んだ。
そのうちの一つが磁石の力で必要な数のボルトを取り出してくれる「カメレオン」というからくり。
インパクトを手に取ると、ひもで釣られた磁石が部品箱へと下り、ボルトを吸着。インパクトを元の位置に戻すと、とりやすい位置に釣り上げてくれる仕組みだ。
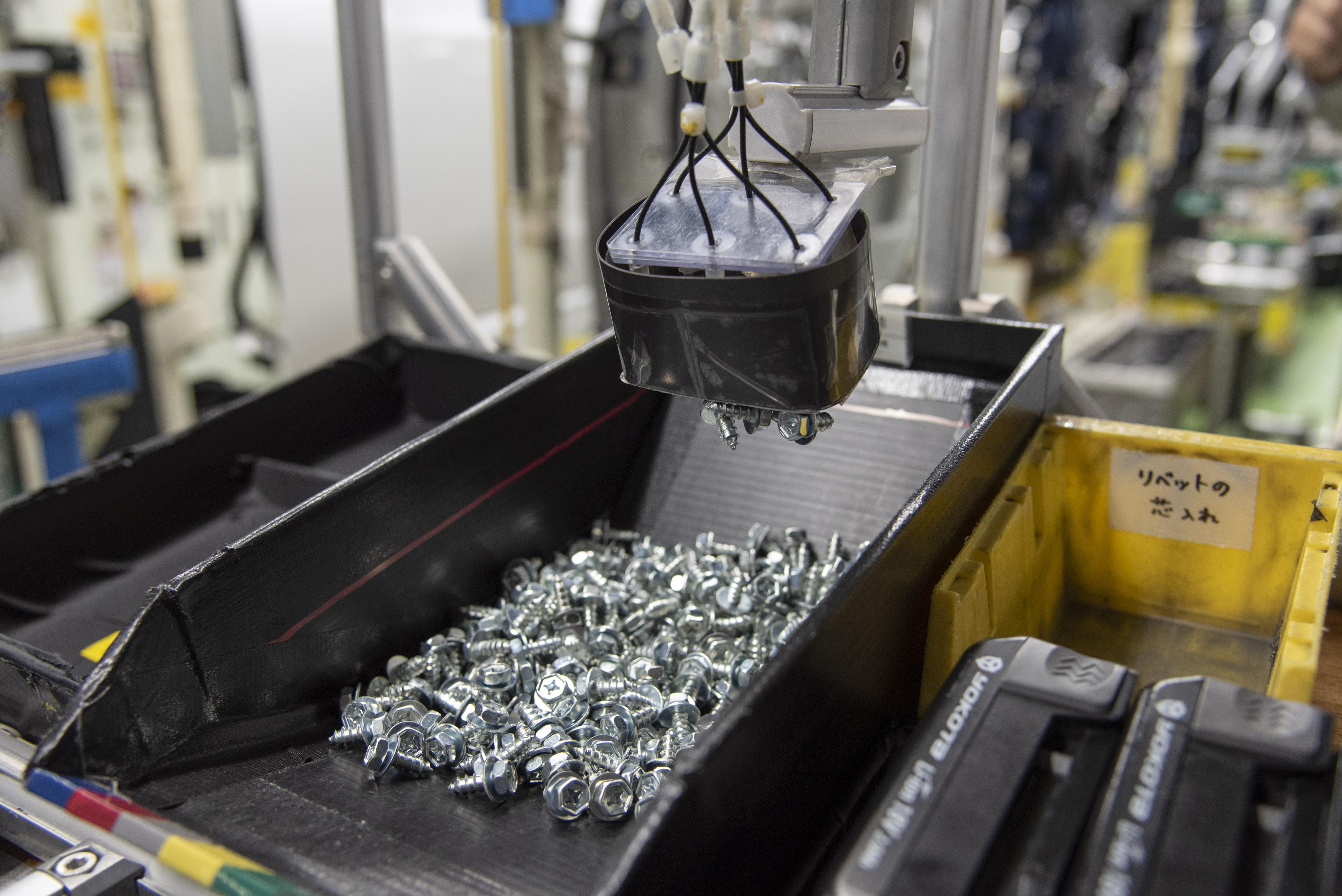
同じく、昨年6月にエンジンをつくる上郷工場から転籍してきたシャシー2ラインの大竹雄也さん(総組立部第1組立課)は、ステアリングの動きを車輪に伝えるインターミディエイトシャフトの一次置き場の改善に取り組んだ。
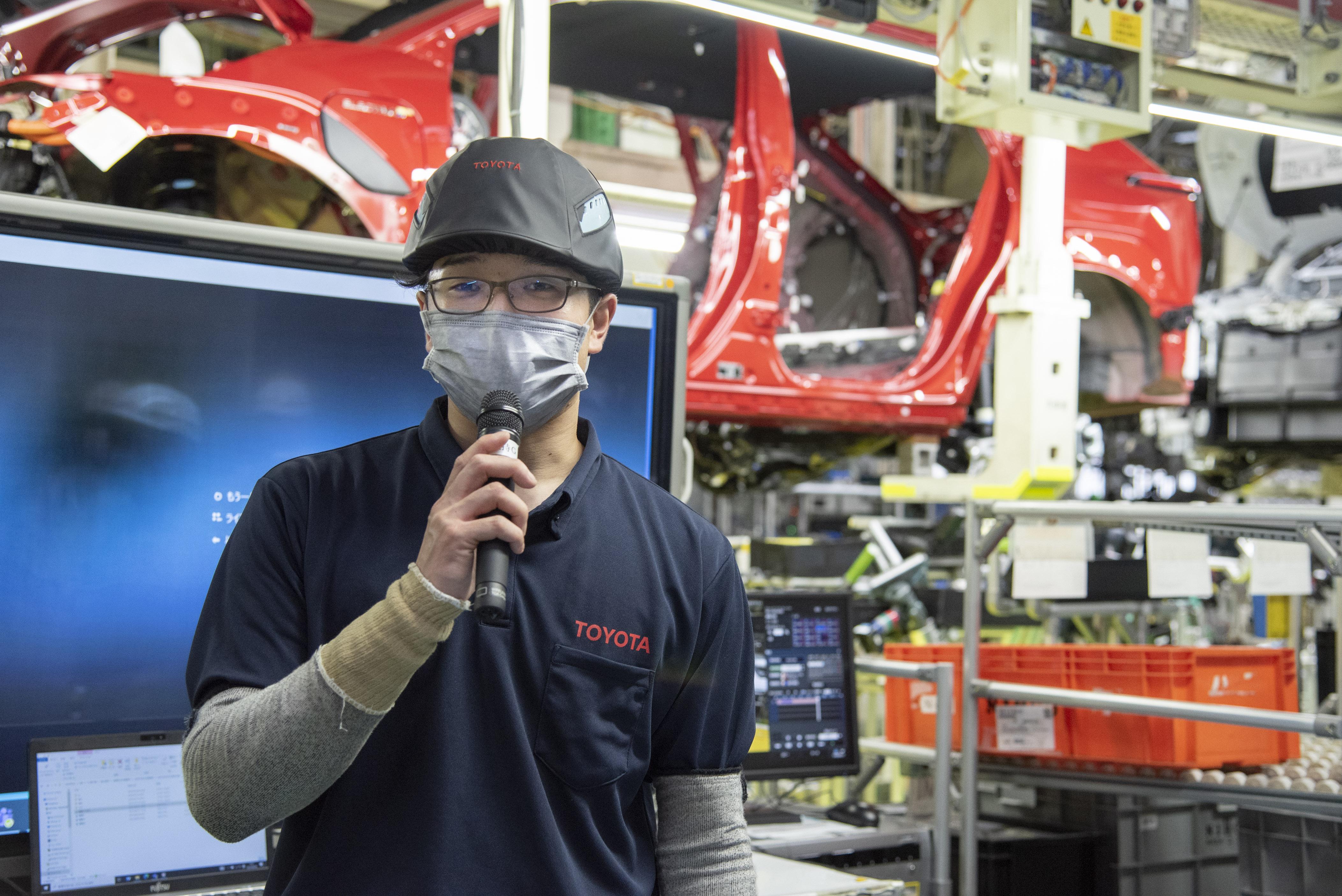
これまでは、一時置き場が固定されていたことで、大きく重たい部品を持った移動の距離が長かった。
しかし、両手がふさがって、転倒してけがをしたり、部品に傷をつけたりするおそれがあった。また、隣の工程のメンバーの作業に干渉することも少なくなかった。
この状況を解決するため、部品を載せたら自重でスライドし、作業位置まで運ぶからくりを取り入れた。
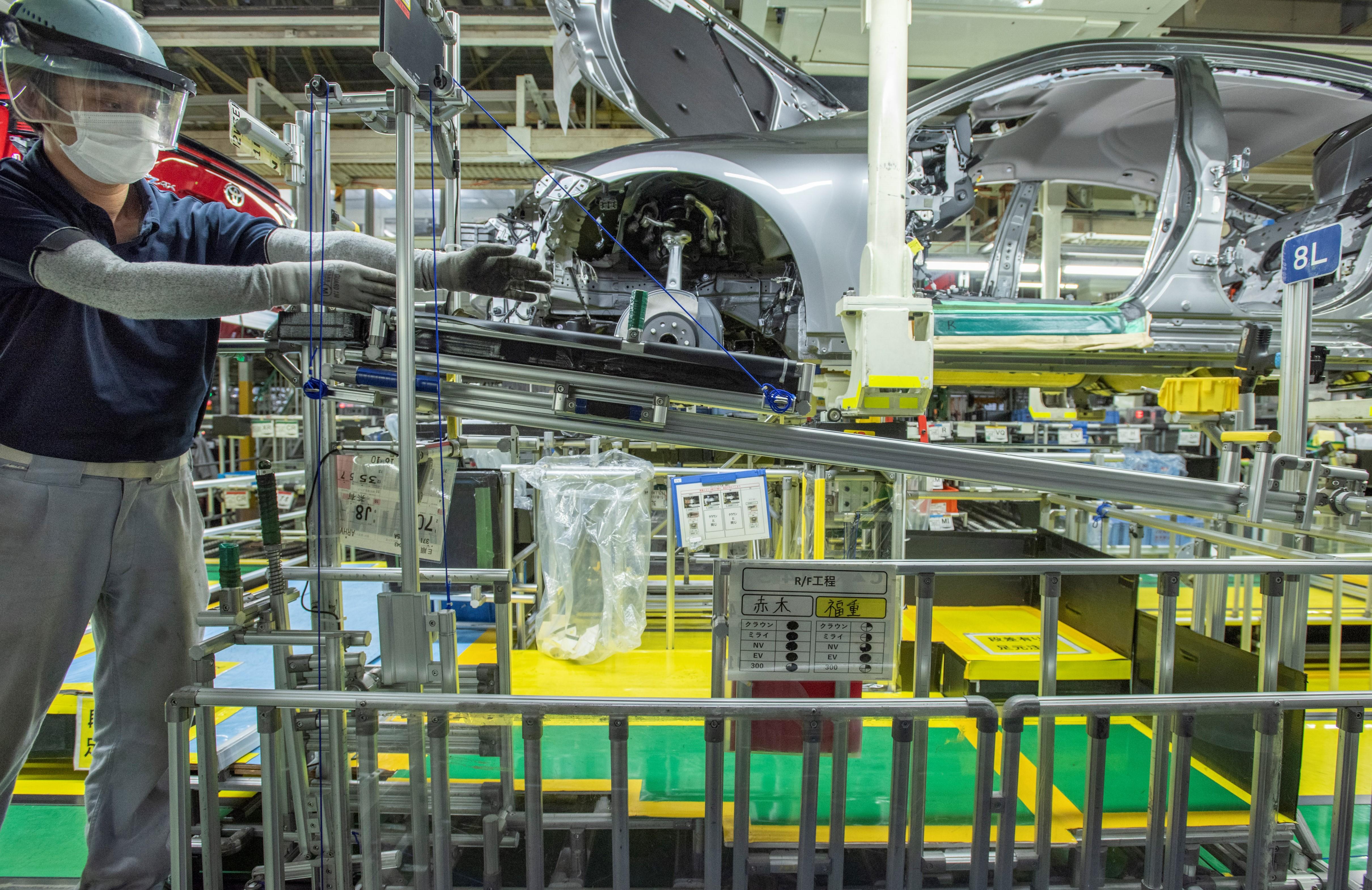
「いろいろな人が豊富なアイデアを持っている。自分もいろんなアイデアを出して困りごとを改善していけるようになりたい」と今後のさらなる改善に意欲を見せた。
インパネラインの長野賢二組長(総組立部第1組立課)は今年1月、部内の別の職場から異動してきた。
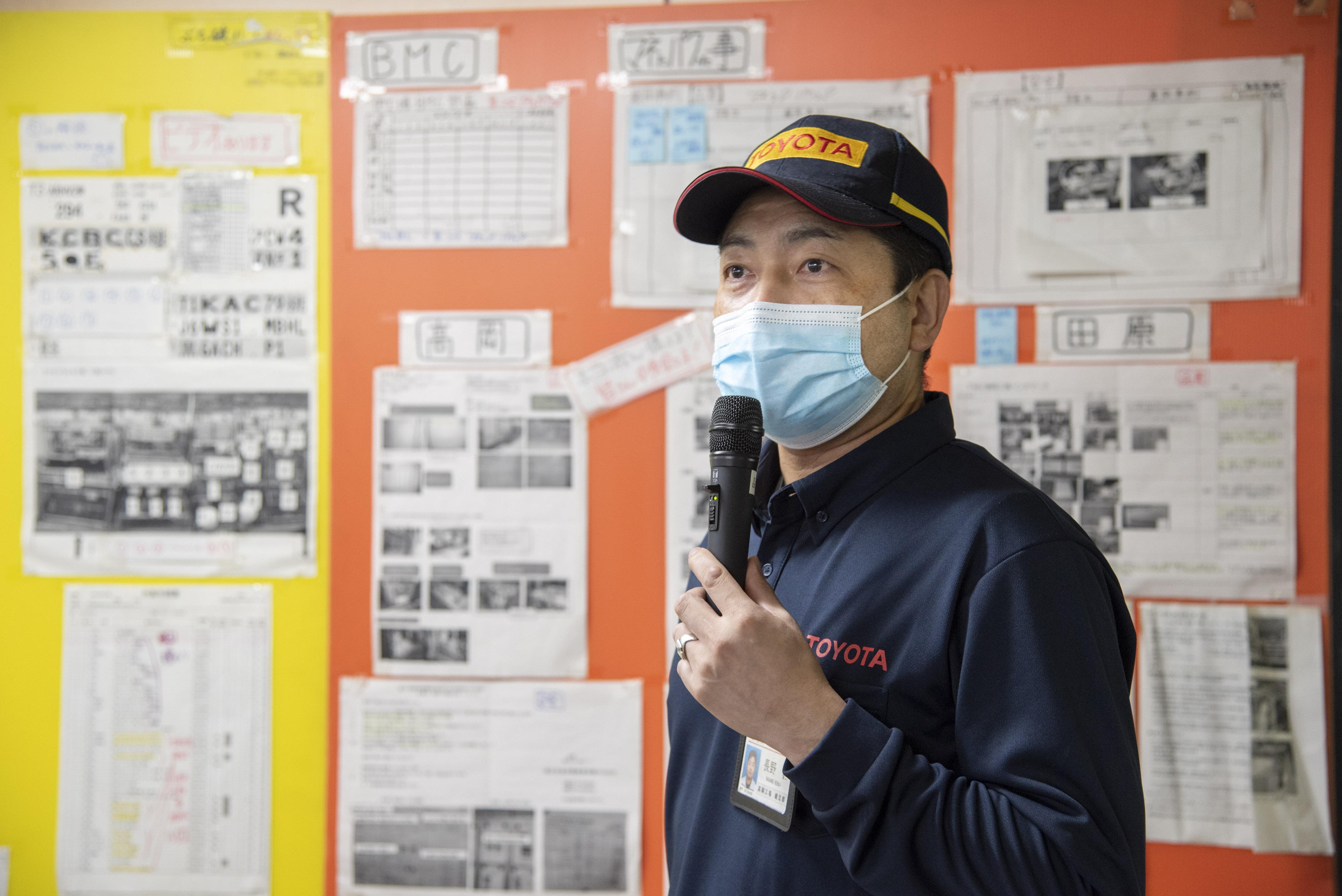
「目的を理解したうえで活動できる人材をつくらずに、品質の良いクルマはつくれない」
ただ決められた作業を行うだけでは、高い品質を維持できないという上司の教えを受けて、まずは、自分自身が腹落ちできるまで、職場の品質の取り組みと目標設定の背景を叩き込んだ。
学んだことは、部下にも伝えていった。自身の理解が深まると、ミーティングでの部下の反応も変わってきた。
最初はただ聞いているだけだったのが、2度目にはメモを取る人が出だし、さらに回を重ねると、手を挙げて答えるメンバーも現れたという。
「ラインが回れば、結果は出ると思う。万一、新たな問題が見つかれば、しっかり原点に立ち戻って、教え込み、これからのプロジェクトも成功させていきたい」。長野組長は頼もしく今後の展望を語った。
大きなプロジェクトを支える地道な活動
約1年で4プロジェクトを立ち上げ、複数の車種を同じラインで流す前例のないプロジェクトに、多様な人材で臨む元町工場。
一見、先進的な取り組みを支えるのは、最新鋭の設備ではなく、現場の従業員一人ひとりが続けてきた地道な改善だ。
明里次長はこう語る。
「僕らは何回も工程変更をして『今月は生産台数が日当たり100台、来月は150台増える(減る)』ということを年に6~7回もやってきた。そのたびに設備を動かさないといけない。タクトタイムや工程が変わらないところはいいかもしれないが、うちの職場のやり方じゃない」
稼働が止まったラインでうまくいったことが、再開時にすべて順調にいくかどうかはわからない。
それでも、元町工場は生産変動や車種の変更といった環境の変化を人の知恵と工夫で乗り越えてきた。
工場で働く仲間のため、部品を納めてくれる仕入先のため、そして何より、クルマを心待ちにするお客様のため。改善を重ねていく姿勢に迷いはない。