
トヨタ生産方式(TPS)の原点は、夜なべする母親を想う少年の気持ち!?社員に向けて語られたTPSの"本当の目的"とは?

5月の決算説明会で豊田社長は「この数年間は“トヨタらしさを取り戻す闘い”と“未来に向けたトヨタのフルモデルチェンジ”の両方にガムシャラに取り組んだ」と話していた。ここでいう“トヨタらしさ”とはなんだったのか?さらに豊田社長の発言を遡ると2年前の決算説明では、こう語っている。
先日、トヨタの社内で「トヨタ生産方式」を改めて学ぶ研修が始まった。そのキックオフの会合で講師として現れたのは豊田社長だった。
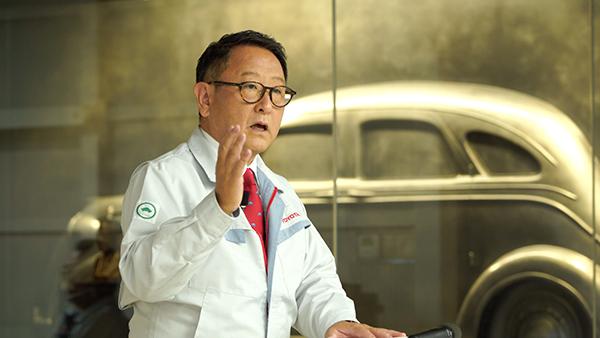
“トヨタ生産方式”。本屋にも関連書籍が並び、今はもう社内用語ではなくなっているかもしれない。だが、豊田社長の切り口は、それらの本で読んだ内容とは少し異なっていたように思える。
「私の解釈ですけど」と繰り返しながら語った“豊田章男流解釈のトヨタ生産方式”について、今回のトヨタイムズではお伝えしていきたい。
1.母さんが夜なべして…
今回始まった研修は“普段は生産現場にいない社員”もトヨタ生産方式(TPS)を学び、“トヨタらしさを取り戻す闘い”と“未来に向けたトヨタのフルモデルチェンジ”を進めていこうという目的のものだった。
受講者が事前に提出したレポートの束を片手に、豊田社長はこう切り出した。
非常に人事っぽく、こういうのをまとめさせられているんですよ(笑)
受講者は笑い出し、さらにレポートの話を続ける。
豊田社長
さすがに皆さんトヨタのキーワードをしっかり使ってくるな…ということなんですが、この中で、僕がちょっと気になったのは「今回のこのTPS研修で、なんとかトヨタを変えていきたい」という意気込み。
「変えていきたい」ということはいいんです。だけど、なんでもかんでも思想なく変えてしまっては、会社がメチャクチャになります。
トヨタ自動車にはやはり創立以来…、いや、トヨタ自動車ができる前からの“2つの考え方のポイント”があります。なんだか分かりますか?
受講者A
TPSと原価低減です…。
豊田社長
TPSと原価低減…。隣の人、どう?分かる?
受講者B
はい…。「ジャスト・イン・タイム」と「ニンベンのついた自働化」…。
豊田社長
そうそうそうそう!これが言ってほしかったの!(一同笑)
ジャスト・イン・タイムとニンベンのついた自働化っていうのを、入社以来ずっとその2つが2本の柱とされて、ずっと分かったような気になってると思います。
たぶん分かってる人もいるでしょう。分かった気になった人もいると思います。
だから、今回このTPSの研修にあたり、この基本中の基本である「自働化」とそして「ジャスト・イン・タイム」という2つの言葉の意味を、皆さんと我々でギャップを、ちょっと縮めておきたいなということで、そこだけは私にやらせてもらうということになりました。
こういって豊田社長の話は本編に入っていった。
まず自働化なんですけど、これは私がごちゃごちゃ言う前に、豊田佐吉翁がつくった自動織機というのが、そこにあります。ですから、それを見ながら説明をしたほうがいいので…
そういうと豊田社長は教壇から研修室の後方にある織機の方に全員を引き連れて移動した。
佐吉というのは大工の息子でした。何をしたら、この世の中のためになるんだろうかと、日々いろんな本を読んで勉強していたそうです。
そういう中で佐吉少年が気付いたのは、毎晩、夜なべをしてお母さんが機織り仕事をしていた…、その仕事を楽にできないのかなということ。それが佐吉少年の着眼点だったんです。
織機がトヨタのルーツであるということは有名かもしれない。しかし「なぜ佐吉が織機を発明するに至ったのか」という背景までは、そこまで知られていない。
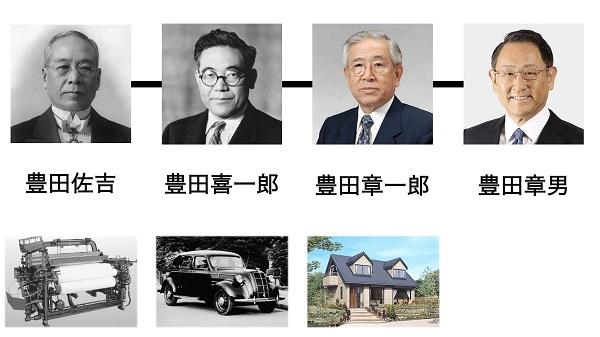
佐吉が母を想い、はじめにつくった織機は、片手で操作ができるものだった。織機は、たて糸・よこ糸それぞれ両手を使って作業することが常識だった時代、その発明は作業性を画期的に向上させた。
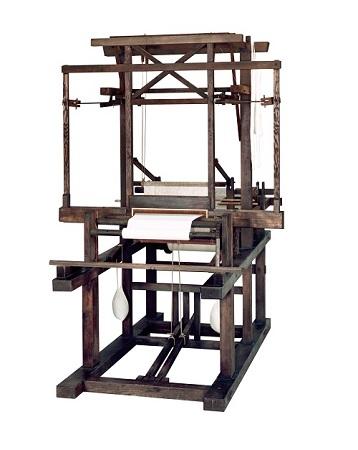
そう語りながら、豊田社長は次の機械のもとへ向かう。辿り着いたのはG型自動織機と呼ばれるものだ。
2.生産性向上は目的ではない
これが“G型織機”。トヨタが大きく、事業構造をモデルチェンジしたきっかけになった機械です。
時の自動織機というのは、必ず “ワンマン、ワンマシン”っていう、1人のオペレーターが、マシンに対して、いつもくっついて監視をしていたわけです。“人は機械の番人”といわれるような形で…。
それはなぜだと思います?
“異常”が、いつ起きるか分からないからです。

この織機は、トヨタが織機屋から自動車屋へ事業をモデルチェンジするための資金を生み出した機械である。当時世界のトップメーカーだったイギリスの会社が、この織機の技術を供与して欲しいとトヨタに申し出たのである。
その技術とは“異常を検知するシステム”であった。
一体どんな技術だったのか?なぜその発明に至ったのか?発明者の“ひ孫”である豊田社長がそれを説明した。
織物を織るということに対して“異常”ってどういうことでしょう?「糸がなくなる」「糸が切れる」これらが織機の“異常”で一番大きいものでした。
その2つの“異常”を、センサーがない時代に検知できているのがこのマシンです。
G型織機はたて糸・よこ糸それぞれにバネでピンを押し当てている。糸がなくなればバネの力でピンの位置がズレる。それによって異常を検知し、自動的に新しい糸へと入れ替える。
センサーどころか、モーターなどの動力も使わずに異常検知を実現しているのには素直に驚かされるが、この部分は、豊田社長が機械を前にして説明したように、やはり実物を見て頂くのが一番分かりやすい。愛知県のトヨタ産業技術記念館で糸を入れ替える実演が見られるので、ぜひ足を運んでいただきたい。
豊田社長は異常を検知した後、糸を入れ替えるための工夫へと説明を続けた。
(機械から“よこ糸を通すための木管”を取り出し…)糸がなくなると、この機械は自動的に木管ごと替えるわけです。
実は、木管からはこうやって糸口が出ていなきゃいけない。それを以前はどうやっていたかというと、口で吸って糸を出していた。
ところが、現場は綿ボコリが出ているので、現場の作業者たちはそれを吸って肺を患ってしまう。
糸を切るだけで木管の必要なところに糸が勝手に出てくるというのが、佐吉たちの発明だった。これにより作業者たちは糸を口で吸い出す必要がなくなった。
これも佐吉たちの発明のひとつです。
“発明”と聞くと、すごく先進的なもののように感じるかもしれませんが、この発明は、現場で肺を痛めていた作業者をなんとかしてあげたいというのが原点でした。現場に立っている人じゃなかったら、それは分からなかったかもしれません。
センサーがない時代に、“異常管理の仕組み”を入れたのが、このG型自動織機です。これによって生産性はものすごく伸びました。ただ、それはあくまでも結果です。
作業者が肺で苦労していた…、設備がしょっちゅう止まり、糸も切れて作業者が設備に張り付いていた…。
だから、異常がなにか?を決めて、そして、異常を止めることによって、異常管理ができるシステムをつくったことによって生産性が上がったということです。
生産性を上げるためにそうしたっていうことじゃないんです。
佐吉の発明は、どれも「現場発」であり、原点は「誰かの仕事を楽にする」というものであった。その“誰かのために”の想いが、結果として生産性向上に繋がったのだということを豊田社長は強調した。
3.豊田章男の解釈「自働化」
自働化について、もう一回復習しますと、要はトヨタのニンベンのついた「自働化」というのは…
私の解釈ですよ…、私の解釈は“やっぱりヒト中心”にしてくれってことなんです。
そこで働いているヒトの気持ちに成り代わって(考える)。自分は安全地帯で、「効率を上げろ」「人を抜く(減らす)」と言うことだけで考えてはダメ。
1人工の追求というのがトヨタにはあります…
豊田社長は、こう言って、改めて、ヒトの大切さを語った。そして“1人工”(いちにんく)という考え方を持ち出す。
“1人工”とは、1人の作業者が1日にこなすことのできる仕事量を指している。それを“追求”するとはどういう意味なのか…説明は続いた。
なぜ1人工を追求するかというと…
やっぱり皆さん1日24時間。それは皆さんも、私も、1日24時間しかないんです。「私は忙しいから1日48時間もらいます」って訳にいかないんです。
そうすると、1日24時間というのは、誰に対してもイコールに与えられた条件です。その中を、皆さんにも家庭があります。そして、プライベートもあるでしょう。ところが、会社というものに対しても本当に多くの時間を費やしてくれています。
そうだったら、意味のある仕事をさせるのが上司の仕事じゃないですか。そういうのを徹底的に追求しているのがトヨタの生産現場です。
「付加価値をつける仕事をどんどん増やしていこう」、「単に“手待ち”とか、単に“やり直す”とか、そういうような仕事はどんどんやめさせてあげよう」ということです。
だから「ヒト中心ですよ」ということだけは、私の解釈ですけど…、ぜひ皆さんに考えていって欲しいなというふうに思います。
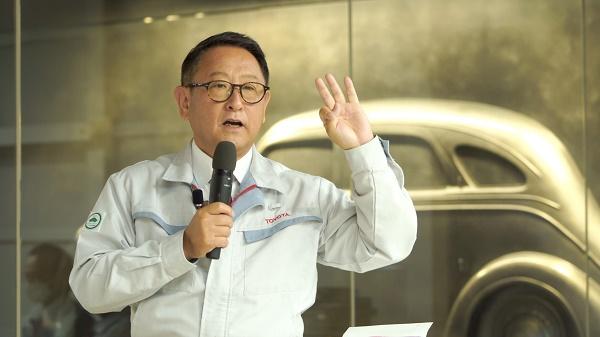
トヨタ生産方式は、労働強化と誤って受け取られることがある。先日の第1四半期決算の結果も、一部では「下請け叩き」と伝えられていた。
「ムダ・ムリ・ムラ」を極限まで突き詰めるというのがトヨタ生産方式の中の1つの考え方である。しかし、これが“休むことのない過酷な労働”をイメージさせているのかもしれない。
だが、佐吉の「母親を楽にするために」という想いがトヨタ生産方式の原点だと知ると印象は変わる。作業者の無駄な仕事を無くし、残業を減らして自由な時間を生み出す。1人工の追求とは、その人の時間を大切にすることなのだ。
4.豊田章男の解釈「ジャスト・イン・タイム」
続けて、豊田社長は2本柱のもう1つ「ジャスト・イン・タイム」について説明した。
これは、佐吉の息子であり、トヨタ自動車の創業者、豊田喜一郎が導入した考え方だ。ジャスト・イン・タイムの説明には「必要なものを、必要な時に、必要なだけ」というフレーズがよく使われる。
しかし、このフレーズを巡って、豊田社長はやはり独特の説明をしはじめる。キーワードは「リードタイム」である。リードタイムとは「受注からモノ・サービスの提供までに掛かる時間」を意味する言葉だ。
説明にはいる前のやり取りから紹介したい。
豊田社長
ジャスト・イン・タイムと聞くと何を考えます?
受講者C
必要なときに、必要なだけ、必要なものを提供すること。
豊田社長
そうなんだけど…、それはじゃあ具体的にどういうこと?
受講者C
…。
豊田社長
じゃあ、必要なものを、必要なときに…っていった時に、(すぐにお客様のニーズに応えるためには)めちゃくちゃ在庫がたまるじゃん。
受講者C
はい…。
豊田社長
自動車の場合、3万点も部品があるんだよ。
受講者C
うーん…。
豊田社長
そうした時に、どの車種が来ても、どのスペックが来ても、なんでもOKの生産ラインとしたら、とんでもない在庫になる。
受講者C
お客様が必要なものを知れば…。
豊田社長
お客様って誰?
受講者C
後工程…。
豊田社長
え?
受講者C
エンドユーザーのお客様…。
豊田社長
だけど、年間で1000万台近く売れているわけ…。ということは1000万人のお客様がいる。それをどうやって把握するの?できないでしょう。
だから、どうするかというと、異常がすぐ分かる、異常が分かったら止まってもらって、それで、すぐ改善ができるような構造にしておかなきゃいけないっていうことなんです。
だから、ジャスト・イン・タイム。
これも私流の解釈ですよ…。
これを一番分かりやすくする“道具”というか、“考え方”が、僕は「リードタイム」だと思います。
トヨタでは次の工程のことを後工程(あとこうてい)という。そして、その“後工程” のことを“お客様”と考える。
だから後工程に“絶対に不良品を流さない”。これが続いていけば、その先にいる“本当のお客様”に不良品が届くことはない…という考えだ。
さらには「どうすれば次の工程がもっと楽に作業できるか」を考える。前後の工程がコミュニケーションし、一緒に改善を重ねていく。そうして生産性を追求していく。
普段、我々(トヨタの社員)が「ジャスト・イン・タイム」と聞くと連想するのは「後工程に対して“ジャスト・イン・タイム”で供給できているか?」ということだが、ここで豊田社長が言った“ジャスト・イン・タイム”はスケールが大きかった。
「クルマを買ってくださるお客様に“ジャスト・イン・タイム”でクルマをお届けする」という、トヨタ全体を見渡しての“ジャスト・イン・タイム”である。
ひとつの車種にも“仕様”は何通りもある。
グレード×外板色数×内装色×オーディオ種類…、例えばプリウスで言えば、この掛け算の結果(仕様数)は1万4000通りにもなる。すごい数だが、これは種類を削減する努力をした結果だと言う。先日の改良モデル発売までは4万8000通りもあった。これは日本出荷分だけの話。海外向けも同じ工場でつくっていれば、掛け算はさらに増えていく。
全ての種類の在庫を持てば、お客様にジャスト・イン・タイムで車をお届けできる。しかし、それは現実的ではない。しかし、「だから、そこは諦めていいよ」と豊田社長も言っているわけではない。むしろ「リードタイム」を追求して、ジャスト・イン・タイムに拘り続けようと訴えた。
5.お寿司のリードタイムを目指せ
豊田社長は、寿司屋を例えにして、リードタイムの説明をしはじめた。
例えば、お寿司の世界ね。
スーパーへ行くと完成品(在庫)が並んでいますよね。ところが、ちゃんと目の前で握ってくれるお寿司屋に行くと、握る人のところに在庫って置いてある?
置いてないでしょう。
それで、ネタは切ってある?切ってもいないね。
注文が入ってから「はいよ」と言って、その材料を取り出して、切って、段取りして、握って、出す。何が言いたいかというと、リードタイムさえ短くしておけば、それは可能なわけでしょう。
ところが、前もってつくっておきましょうなんていって、1000万台のお客さん相手に、どういうスペックか?なんてできないでしょ…と。
できないことは、できない。じゃあ、それで何をするか?というと「リードタイムを短くしておこう」ということが大切になる。
クルマもお寿司と同じように“お客様のオーダーを受けて”、“部品を用意して”、“組み立てて”、“すぐ出荷”できれば理想である。しかし、現実には難しい。
だからこそ、それぞれの工程が「リードタイムを短くする」を積み重ねておかないといけないということである。
6.“副社長”より“担当者”
豊田社長がひと通りの話を終えた後、ひとりの受講者が手を挙げた。
本日はありがとうございました。入社して私は20年なんですけど、この距離感でお言葉をいただけるのが初めてなので大変興奮してます。
入社した時に当時の部長から「働くって意味は分かるか?」と言われて、“ハタラク”というのは、「周り」つまり「端(ハタ)」を「楽(ラク)」にすることだと言われて、その言葉が、先ほど社長がおっしゃった「ニンベンのついた自働化」の“周りを楽にする”、“誰かのために”というところで、スコーンッと自分の中でつながりました。20年も経って初めて気付きました。
今日、社長からだいぶ熱量をいただいたんですけれども、自分の部署やセンター全部に対して、社長の熱量を今一度伝えたいなと思ってます。
これに対し、豊田社長は自身が課長時代に、販売店の生産性向上に取り組んだ時のエピソードを語った。
販売店と一緒に改善活動をしていた時、よく現場のトラブルに遭遇しました。
トラブルが発生した時に一番困っているのは、現場のメカニックとか営業スタッフ。つまり、最前線の担当でした。
彼らは日報でそれを報告しているが、上位者には伝わっていないんです。
当時(メーカーから行った)私たちが「何故それをもうちょっと早く営業所長に言わなかったんですか?」と聞くと、その営業所長は「さすがトヨタの人!自分が営業所長会議で言っていることを言ってくれた!」という。
「だけど営業所長会議は週に1回でしょ?」と切り返すと、それを聞いていた、さらに上役の営業本部長が「さすがトヨタの人!俺がいつも役員会で言っていることを言ってくれた!」。
でも、その役員会は月に1回なんですよ…。
なんで私が肩書を廃止したか?
ジャストインタイム(にしていくための改善で)で一番必要なのは“その担当者”なんですよ。日々の日報が大切なんです。
ところが、肩書が上がれば上がるほど、それが(その報告を受けて判断するのが)週単位、月単位、年単位になっちゃう…。
肩書がある人が“判断をする人”だとは言うけれど、改善のスピードは、そこで落ちているんです。
だけど、我々は365日、休みを除いてほとんどの時間を会社で過ごしている。だから、その毎日を変な肩書社会じゃなくて、その毎日の(目の前で起きてる)現象をどう変えていけるか?これが大切だと思いますよ。
だから、20年掛けてそれを分かっているようじゃダメ(笑)。20年を日単位にしてください。そうすると365×20だよ。
それだけの日にちを普通に生きちゃってるでしょう。なんか損したような気になるでしょう。
だからこそ、やっぱり日々思ってることを、日々改善できるような…、日々リードタイムを短くするようなことを考えてくれるとありがたいですね。
先日からトヨタ自動車では副社長という役職はなくなった。これも改善のスピードを上げるためだと、豊田社長は話している。
お客様のためにリードタイムを短くする…。働く仲間のために作業を楽にする…。働く本人やその家族のために、もっと時間を有効に使えるようにする…。
その改善を生み出すのは肩書ではなく、豊田佐吉翁がそうしていたように、現場に立つ日々から生まれていくということを、トヨタ生産方式研修のキックオフで豊田社長は従業員に伝えていた。
7.編集後記:他の誰かのために
トヨタイムズでは医療用防護ガウンを生産する雨ガッパ屋「船橋(株)」の“改善”にはいったトヨタ従業員の姿をお伝えしてきた。
船橋をはじめて取材した時、我々が一番戸惑ったのは、船橋社員とトヨタ社員の見分けがつかなかったことだった。
トヨタの社員たちは“トヨタロゴの入った作業着”と“会社の肩書”を脱ぎ捨て、船橋の社員たちと和気あいあいと仕事をしていた。話を聞くと、これには狙いがあった。会話をしながら一緒に作業をすると、改善のタネが自ずと見えてくるということである。
隣で作業している人が「腰が痛い」と言っていたら、「どうしたら解決できるかな?」と話しかけ、作業台の高さを変える改善を導いた。目の前の作業者が、ハサミを探そうとキョロキョロしていたら、そこを“ムダ”と見抜いて、ハサミの置き場を決めましょうと提案した。
母親が苦労して機織りをしている時も、G型自動織機がつくられた時も、同じように「現場に立つ佐吉の姿」があったのだと思う。
トヨタ生産方式の土台には、佐吉の時代から脈々と流れ、実践されている「他の誰かのために」という想いがある。