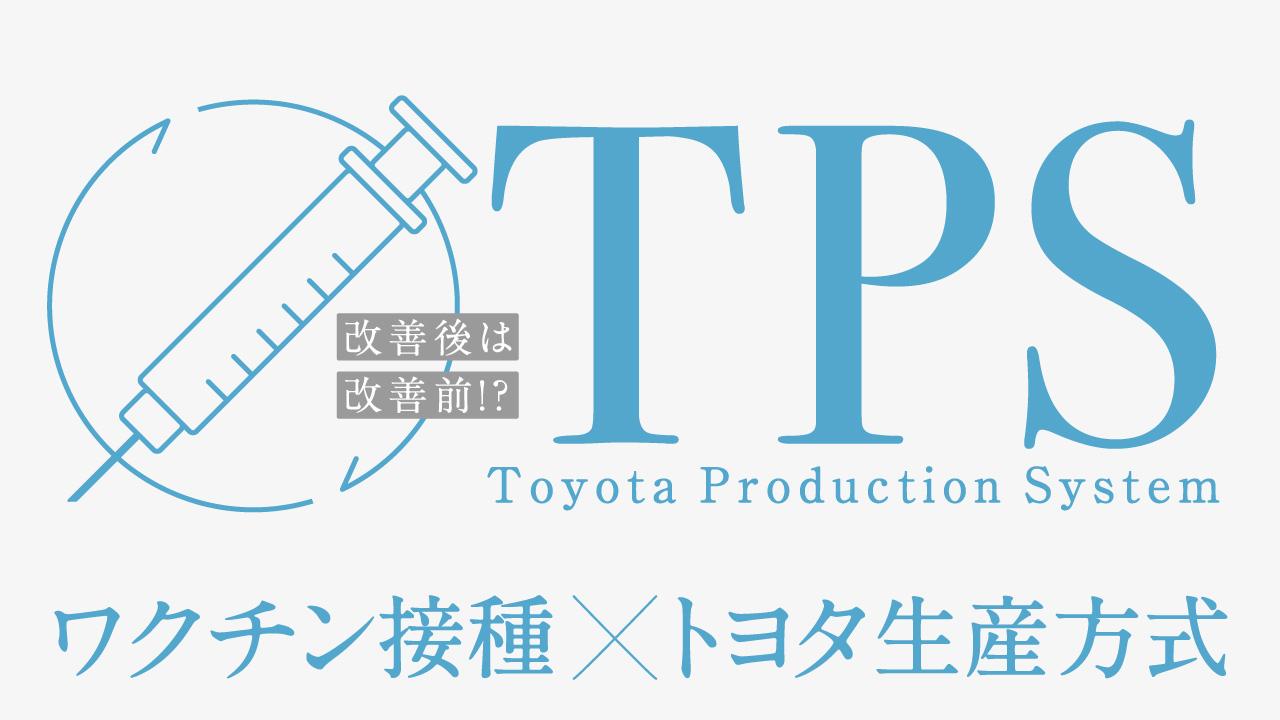
ワクチン接種にTPSはどう活きるのか。"医官民"が総力を挙げて取り組む「豊田市モデル」を取材した。
医療従事者が医療行為に集中できるように
安全・安心なワクチン接種には、ワクチンを「超低温」で運ぶヤマトの流通オペレーションも欠かせない。
豊田市で使用するワクチンは、-90℃~-60℃という温度帯での保管が推奨されている。そのため、一般的な流通においてはドライアイスを大量に使用してこの温度帯を保っているが、ドライアイスは取り扱いにさまざまな注意が必要な物質でもある。
対してヤマトが輸送に用いるのは、超低温の「氷」と専用の保冷ボックスだ。この組み合わせにより、推奨温度を最大30時間まで保持することができる。
接種会場までの配送と保管を一貫して保冷ボックス内で行うことで、広大な豊田市における140カ所の接種所(個別会場も含む)への配送と、冷蔵設備が備わっていない集団接種会場での保管を可能に。未使用のワクチンも持ち帰ることができ、社会課題となっている廃棄のリスクもなくなる。
この輸送スキームを進めるヤマト運輸 グローバルSCM事業本部の林昌弘営業企画部長は、取り組みにかける想いを以下のように語る。
林営業企画部長
政府から自治体に供給された後のワクチン配送運営は自治体に委ねられていますが、どの医療機関に、いつワクチンを供給するのか、自治体だけでコントロールするのも無理があります。
また、すでにこれほど医療現場が逼迫しているなか、受け取る病院関係者にまで、オペレーションを担わせるわけにはいきません。ワクチン接種に注力していただくためにも、そこは、これまで医薬品流通に関する経験や実績を積んできた私たちが担うべきと考えています。
ワクチンそのものに加え、接種に必要な希釈用の生理食塩水や注射針といった備品も、受け取り側の負担が最小限となるように配送拠点でセットしてから送り込む。それがヤマトの輸送の仕組みだ。
また、通常の診察や休診日があるなかで、供給される病院側からは「いつ届くのか分からない」といった声も挙がる。
この課題に対し、ヤマトの輸送マネジメントシステムでは、医療機関の休診日情報や受け取る時間をデータ化し、輸送計画を立てることで、事前にいつワクチンが到着するかを明確化する。3日前までなら予約の変更も可能にした。
林営業企画部長
ワクチン輸送は、予約受注、在庫管理、輸送計画、品質の可視化といったロジティクス・オペレーションです。このシステムをヤマトは通常のビジネスで構築していたので、安全・安心な技術での輸送の分野で、コロナ収束に貢献できるのではと考えています。
医療従事者が医療行為という本来の業務に集中できるように――。ヤマトの輸送技術も、豊田市のワクチン接種を支える大きな柱だ。
このヤマトの輸送スキームとトヨタの会場構築は、接種会場での輸送側と受け入れ側という表裏一体の関係として、他の自治体でも次第に協働していくことになる。
「まずやってみる」ことが改善の一歩
もう一社、民間企業の存在がある。ヤマトの配送で使用する超低温氷をつくるためには-120℃が実現できる「超低温冷凍庫」が必要となる。その開発・生産を担うのが、静岡県沼津市のエイディーディー(以降、ADD)だ。トヨタは、この冷凍庫の生産性向上支援も行っている。
ADDの従業員数は39人。会社規模こそ大きくはないが、2001年の創業以来、半導体装置の開発・販売や修理保守といった専門分野において実績を積んでいる。今回トヨタから支援チームが派遣されることになったとき、ADDの下田裕人取締役は「トヨタの利益になるわけでもない。何か裏があるのかとも思いました(笑)」と振り返る。
下田取締役
ただ、トヨタイムズの医療防護ガウンの生産支援の記事を見たことがあり、トヨタの目指すものはわかっていましたし、実際に来てもらうと「我々と同じ目線でものを話し、上下がない人たちだな」と感じました。それで一緒にやってみて、吸収できるものはしたいなと。

冷凍庫の製造においてネック工程*となっていたのは、キーパーツである多段蒸発器(超低温にするために必要な、フロンガスを気化・蒸発させるための機器)のろう付けによる組付けだ。これまでは熟練の作業者がたった一人で組付けを担っており、生産台数は日当たり2台。1台つくるのに約270分の時間がかかっていた。
*もっとも時間がかかっていたり、生産能力や生産効率が低い工程

前述の宮嶋主幹は、現場に入って感じた印象を次のように語る。
宮嶋主幹
ろう付け一回の正味の作業時間は5秒くらいなんです。その準備の時間が10~20分かかっている。技術のある人が、これだけ時間をかけているのがもったいないなと思いました。(組付け作業担当者の)本来の業務である開発にも時間を割いてほしかったんです。ムダをなくして、その人の持つ力をより有効な仕事に向けることは、TPSの考え方にある「人間性尊重」なので。
ただ、トヨタの支援チームは誰一人としてろう付けを経験したことはない。そこで一度愛知に戻り、トヨタ内でラインを構築し、作業を再現してみた。
宮嶋主幹は「まずはやってみる。そうじゃないと、作業者がどこに困っているのか分からないので。でも難しくて全然できませんでした」と笑うが、そこまでやるトヨタの姿勢に、当初は身構えていたADDの作業者も疑問が晴れたそうだ。
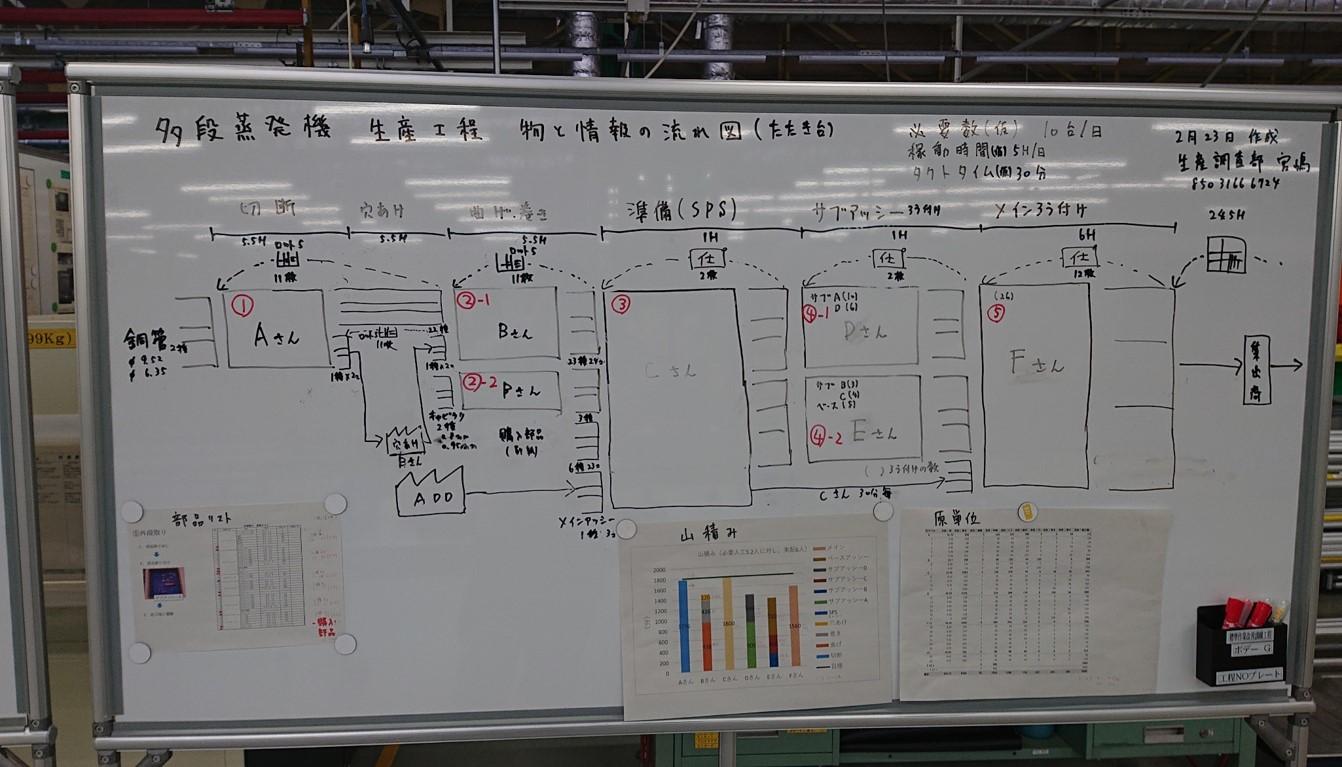
組付け作業担当者との対話を重ねることで、いくつかの改善が実践できた。例えば、これまではろう付けに必要な部品がバラバラに保管されていたために、取り間違えたり、保管場所と組付け場所を行き来していたが、製品にする部品1セットを専用の箱に整理することで準備時間を短縮。
高さがあっておらず、前かがみの姿勢となっていた作業台は高さを上げ、作業者が動き回らなくてすむよう回転式にした。
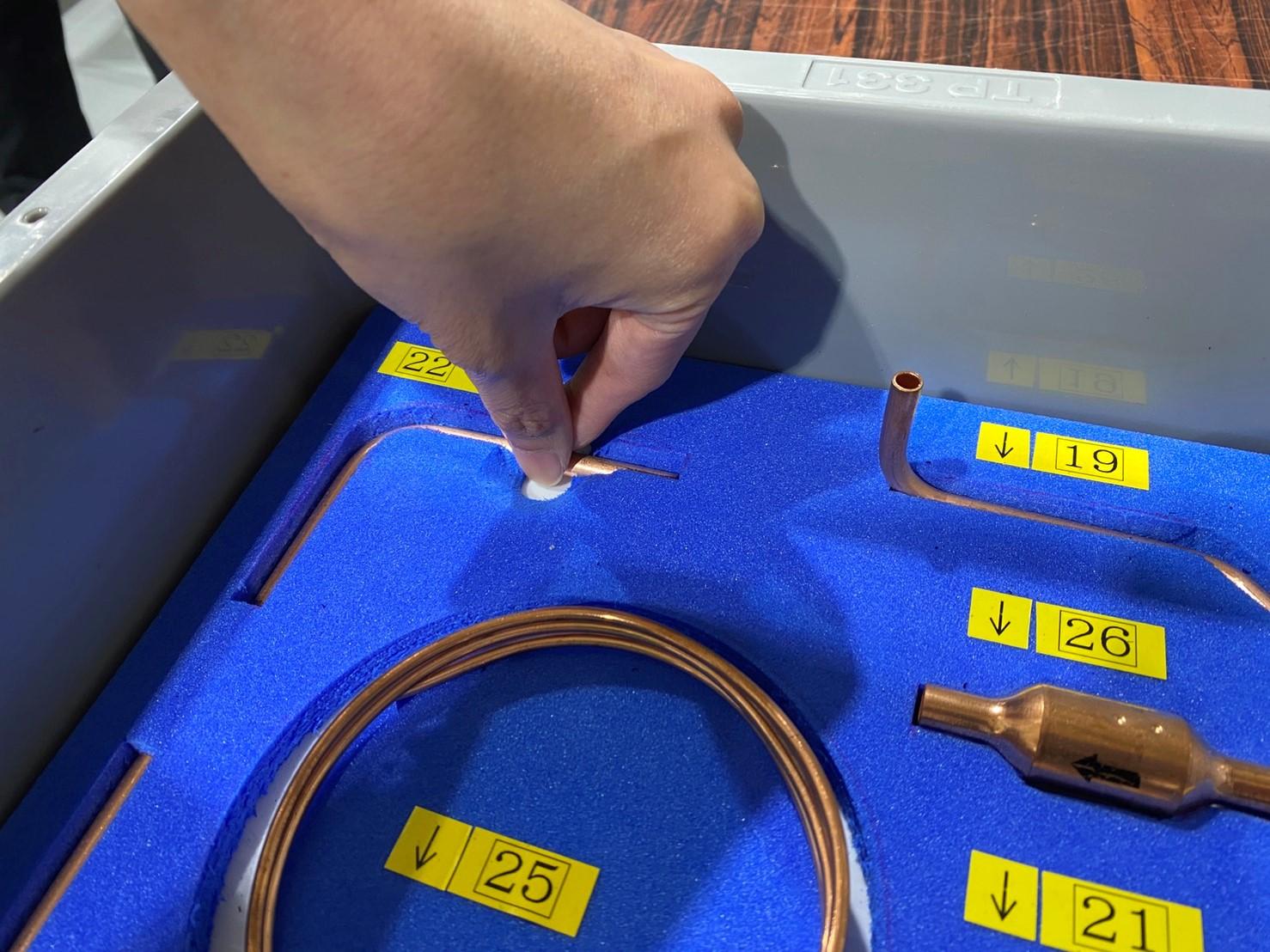


今回の支援チームの一員で、医療防護ガウンの生産支援も担当したトヨタ グローバル生産推進センターの鈴木浩主査は、改善のあり方についてこう語る。
鈴木主査
腰が曲がっているなと思ったら、「上げてみますか? どうですか?」と話をします。勝手に改善することは「改悪」です。改善は上から目線のものではなくて、人間どうしの会話であり、つながりなので。
改善の積み重ねにより、5月末時点で、270分かかっていた作業は120分と半分以下に短縮され、さらに作業者も1人から2人に増員することで、日当たり15台まで生産できる体制が構築できた。「人間どうしの会話」がさらなる生産性向上につながる。
市民が安全・安心な生活を取り戻せるように
そして豊田市における集団接種開始日の5月30日。多くの関係者の想いが詰まった青い保冷ボックスが堤工場の厚生施設に届いた。
10時になると、接種者が続々と会場に入ってくる。大きな滞りはないように見えるが、宮嶋主幹は「まだまだいっぱいやることがある。医療従事者、市役所関係者、会場運営者と一丸となって全員参加でこれからも改善をやり続ける。トヨタでは「改善後は改善前」と言われている。今日も、開始10分でレイアウトを変更したが、最終日の最後の方が接種するまで、我々の改善は終わらない」と意気込む。

接種が始まって2週間。レイアウトの変更や医療従事者を中心とした会場応対者の動作を見直すことで、受付開始から会場を出るまでの所要時間は一人当たり30分~40分かかっていたのが20~30分(15分+αの接種後待機時間を含む)へと短縮。トヨタ施設を使った会場の日当たり接種人数も、当初の1会場540人から3会場合計2700人まで対応できるようになった。
しかし、まだまだ道半ば。ここからさらなる改善を続け、最終的には、一人当たりの所要時間20分の定着化を進め、3会場合計の日当たり接種人数4000人以上を目指す。
今後も、トヨタ施設を活用した集団接種会場が豊田市の周辺地区に順次立ち上がり、同時に、会場あたりの接種人数も増加する。“医官民”が総力となって取り組む「豊田市モデル」は始まったばかり。市民が安全・安心な暮らしを取り戻せるその日まで、取り組みは続く。