
工場以外の非生産現場に広がり始めたTPS。実際に改善に取り組んだクルマ開発センターのTPSルームを取材した。

2020年8月にトヨタ社内で始まった「事技系 トヨタ生産方式 自主研究会」、略して「事技系TPS自主研」。前回の記事では、その合同発表会をトヨタイムズの森田記者が取材し、TPSのキーマンである友山エグゼクティブフェロー(以後、EF)と尾上TPS本部長に話を聞いた。
今回は、合同発表会で取り組み内容をプレゼンした部門の一つ、クルマ開発センターの「TPSルーム」を直撃取材。実際に改善が行われていた現場を見せてもらった。メンバーの汗が染み込む現場には、改善に真摯に取り組んだ数々の足跡があった。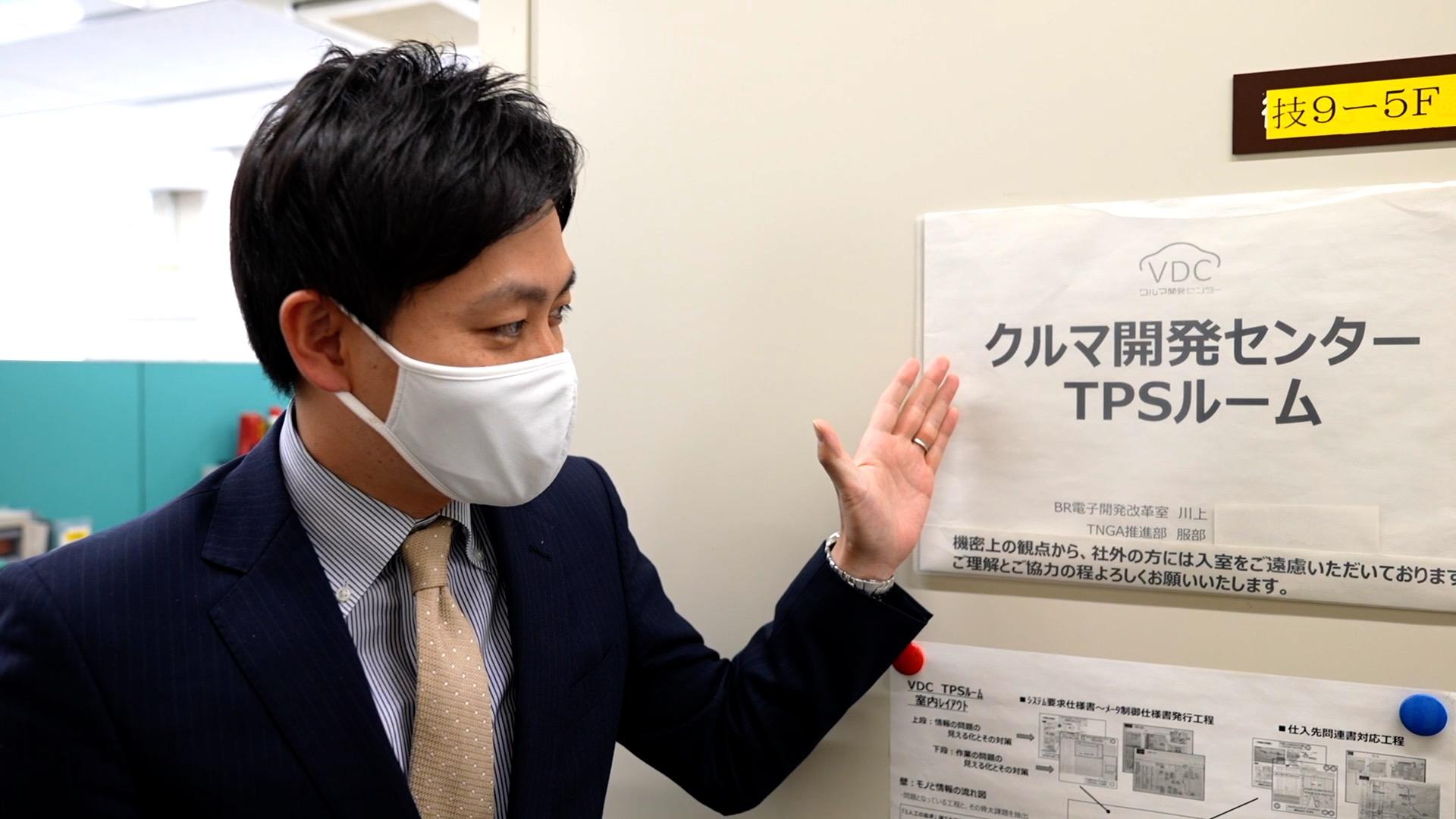
さらに、今回トヨタイムズは、クルマ開発センターの事業上のパートナーであるデンソーにもインタビュー取材。事技系TPSに対する忌憚のない意見を聞くことができた。
複雑化するメーターづくりの改善とは?
まずは、クルマ開発センターのTPSに取り組んだメンバーを紹介しよう。BR電子開発改革室の川上広紀リーダーと、TNGA推進部の服部正敬サブリーダー。この2人を中心に10数名のメンバーがクルマ開発センター内にTPSルームを設けて改善活動に取り組んでいる。
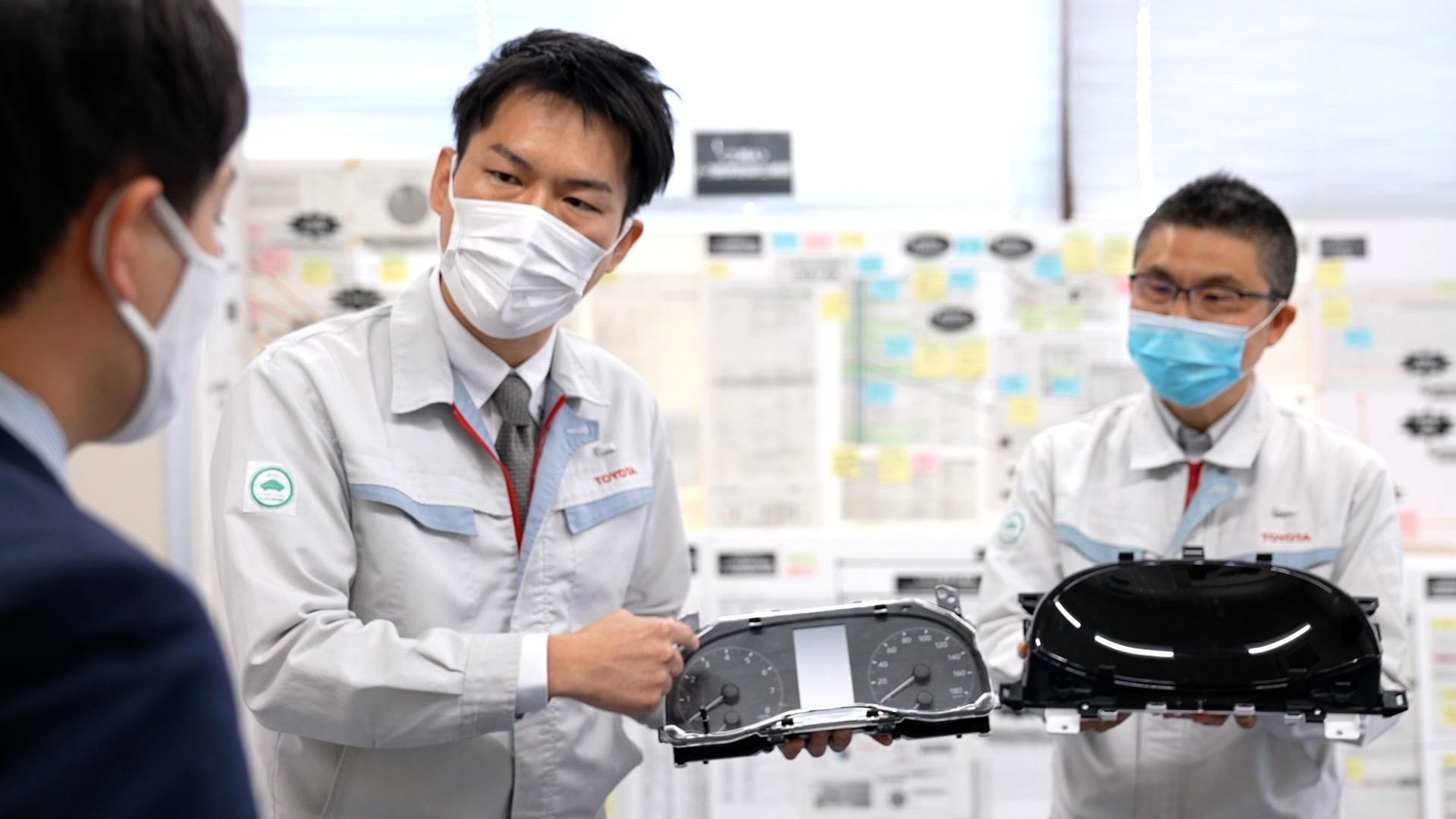
クルマ開発センターは、クルマの先行企画から量産開発までを一気通貫で担う組織で、前編でも触れたソフトウェア・ファーストなクルマづくりを推進している。今回彼らが改善に取り組んだのは、クルマのコックピットにあるメーターの開発業務。
川上リーダー
トヨタが“ソフトウェア・ファースト”を掲げていく中で、今後ますますソフトウェアへの付加価値や(開発の)スピードアップが求められます。その中でもメーターは代表部品なので、この改善を避けては通れません。メーターから改善を積み重ねて、ほかの部品にも応用していく考えです。
近年は特に、ユーザーへの警告やガイドを表示する液晶画面が大きくなり、多機能化しています。液晶に載せる情報やコンテンツが急増し、仕事がどんどん複雑になり開発の現場が困っていたため、改善に取組みました。スピードとエンジンの回転数をアナログで表示していたメーターも、最近は液晶画面が主流になっている。そのため、多くの情報を表示することが可能になったのだが、その分、開発段階ではさまざまな分野・領域の部署との調整が必要になり、業務にかかる人や時間も増加していた。このままでは、トヨタが掲げるソフトウェア・ファーストなクルマづくりができず、改善が必須の状況であったという。
ここで簡単にメーター開発現場の大きな流れを確認しておく。大きく分けて4つの段階がある。
自主研メンバーは②と③の改善に取り組むのだが、彼らにとっての次の工程、つまり後工程はサプライヤーのデンソーだ。前編で紹介したように、TPSの根本は「誰かの仕事を楽にしてあげる」こと。今回の場合、後工程であるデンソーの仕事を楽にしてあげることができたのか、ともに改善に取り組んだデンソーの従業員の本音については後述する。
TPSの出発点、「物と情報の流れ図」とは
クルマ開発センターのTPSルームに入った瞬間、目に入ってくるのが壁中に貼られた紙。□と□が→で結ばれ、大量の付箋がついている。
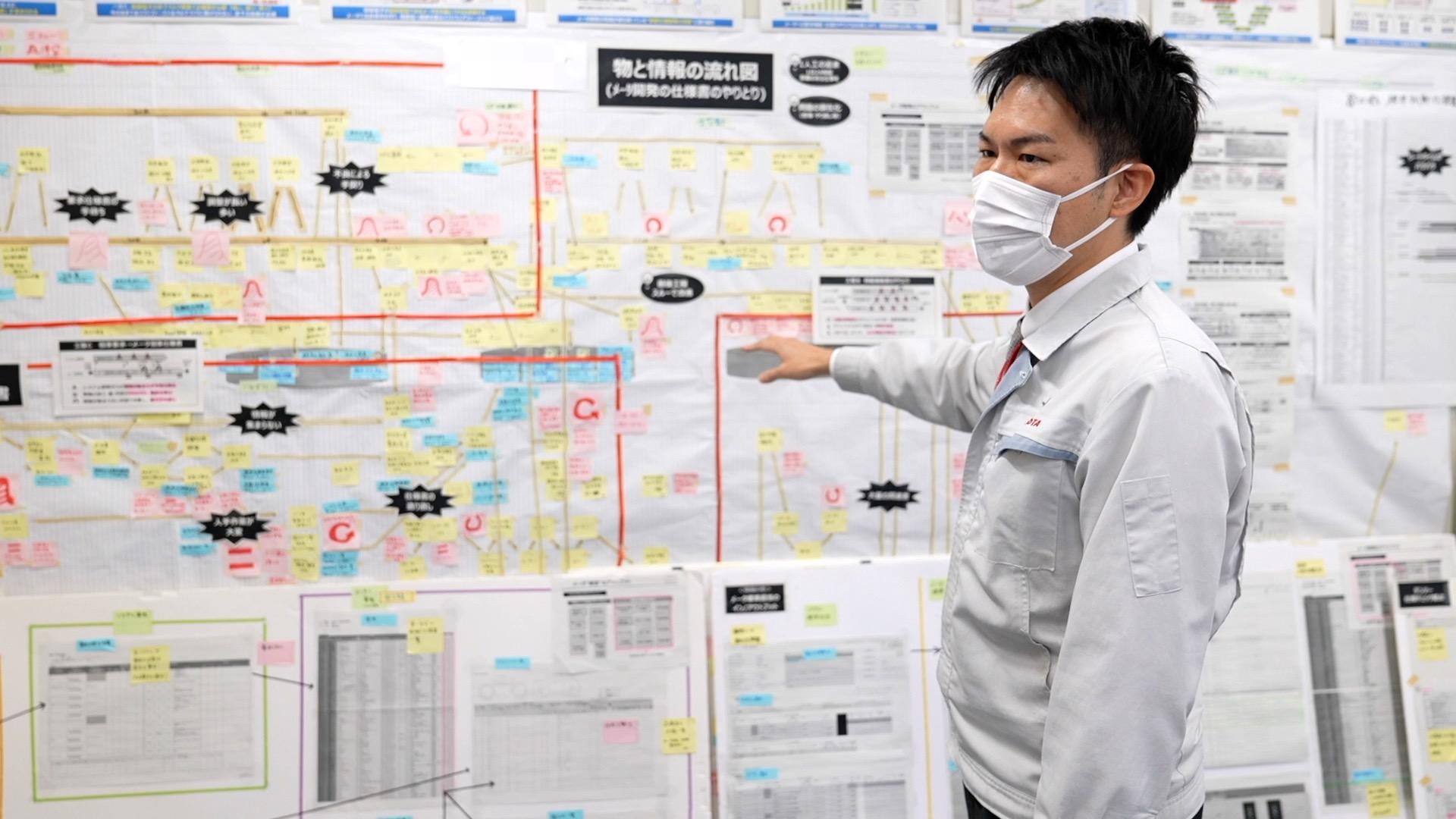
森田
部屋の中で存在感があるのは、この「物と情報の流れ図」ですね。
川上リーダー
これはTPSを実践する上で非常に重要なツールです。「物と情報の流れ図」とは、実際に職場でどんな物と情報が流れているか現状を把握しながら書いていきます。単に“見える化”させるのが目的ではなく、停滞ややり直しなど問題が起こっている工程を顕在化させることができると同時に、関係者と同じ目線で議論が出来る非常に良いツールです。「物と情報の流れ図」とは、通称“物情(ものじょう)”。この物情を使って、前の工程と後の工程をスルーでとらえ、物と情報の停滞を把握して、全体のリードタイムを短くする。具体的には、業務の一括りを、一つの工程として□で囲い、物や情報がどう流れるかを書いてみる。流れ図が書けないところは、業務が曖昧になっている可能性が高い。物情を書くことで改善すべき課題が見えてくる。
川上リーダー
横軸が1日単位になっていて、2019年の夏から、2020年の夏までの期間の流れを示しています。具体的には、メーターの制御仕様のやりとりで、どんな物と情報が流れて、実際にサプライヤー(デンソー)にどんな仕様書が流れているのかをすべて“見える化”しております。
縦軸が担当者で、システム部署からクルマ開発センターのメーターの部署が情報を受け取り、トヨタの車両カンパニーで実際の車を作ります。そこにはメーターの車両担当がいて、最後は仕入先といったような流れです。
森田
たくさん付箋紙が貼ってありますが、これはなんですか?
川上リーダー
事技系職場の「物と情報の流れ図」の書き方は人それぞれで、問題を顕在化させるためにどのように進めるのがいいのか、非常に悩みます。今回の例では黄色の付箋紙は、担当が実際に何をしているか、工程を書いています。ピンク色は、問題や停滞が見えてきた部分です。ここで大事なのは、「どんな作業があるか」を書くのではなく、「実際に担当がどんな作業をしていたのか」を書くということ。頭の中でイメージして書くのではなく、実際に作業をしている担当者に取材して、事実をもとに工程を書いていくことで、本当の問題が見えてくる。
クルマ開発センターは、前工程から「メーターに〇〇の情報を載せてほしい」という依頼を受け(要求仕様書)、集約。「メーターとしてどのように動作するのか」などをまとめた制御仕様書を、後工程であるデンソーに発行して、実際にメーターを作ってもらう、というのが大きな流れだ。
では、どうやって問題や停滞を見つけるのだろうか。
森田
停滞についてはどのように判断していますか?
川上リーダー
単純に日数がかかっただけでなく、要求仕様書の手待ちがあったり、調整のやりとりが多かったりといった事実を確認して貼っています。「手待ち」と書いているものは、物と情報を待っている時間が長い、ムダな時間を指しています。
森田
こうして少しずつ「物と情報の流れ図」を書いていった結果、ピンク色の紙が貼られたところに、どうやら問題がありそうということですね。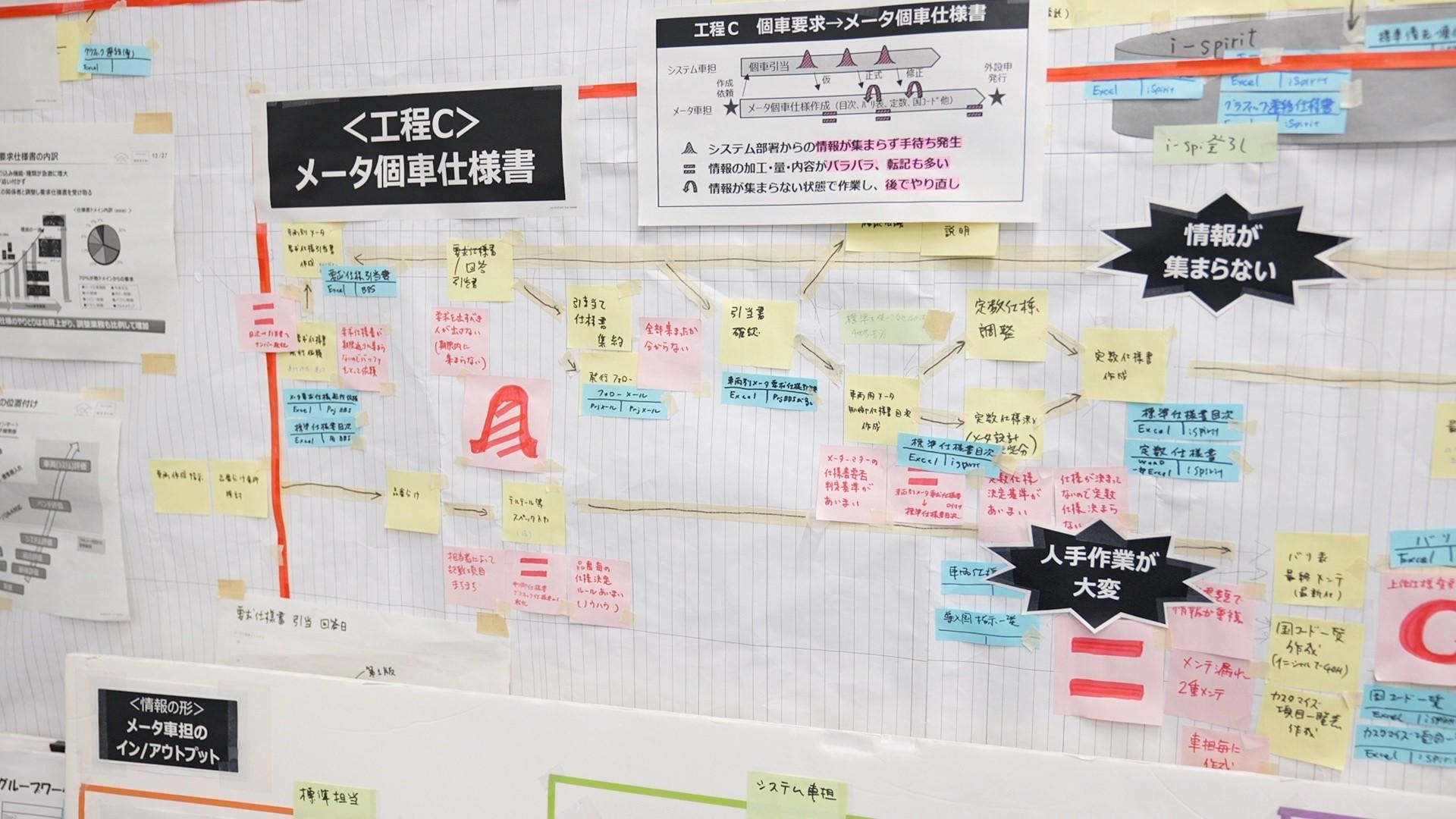
物情を書くだけで、自然と問題が浮かび上がってくるイメージだ。
作業時間を短くしつつ、負担も軽くする
今回の改善では、「物と情報の流れ図」に書かれた工程を3つに分けて、問題点を洗い出したという。まずは、システム部署がメーターの標準を設計するクルマ開発センターの担当者と話し合い、要求仕様書を発行。最終的にメーターの制御仕様書を作成する工程だ。
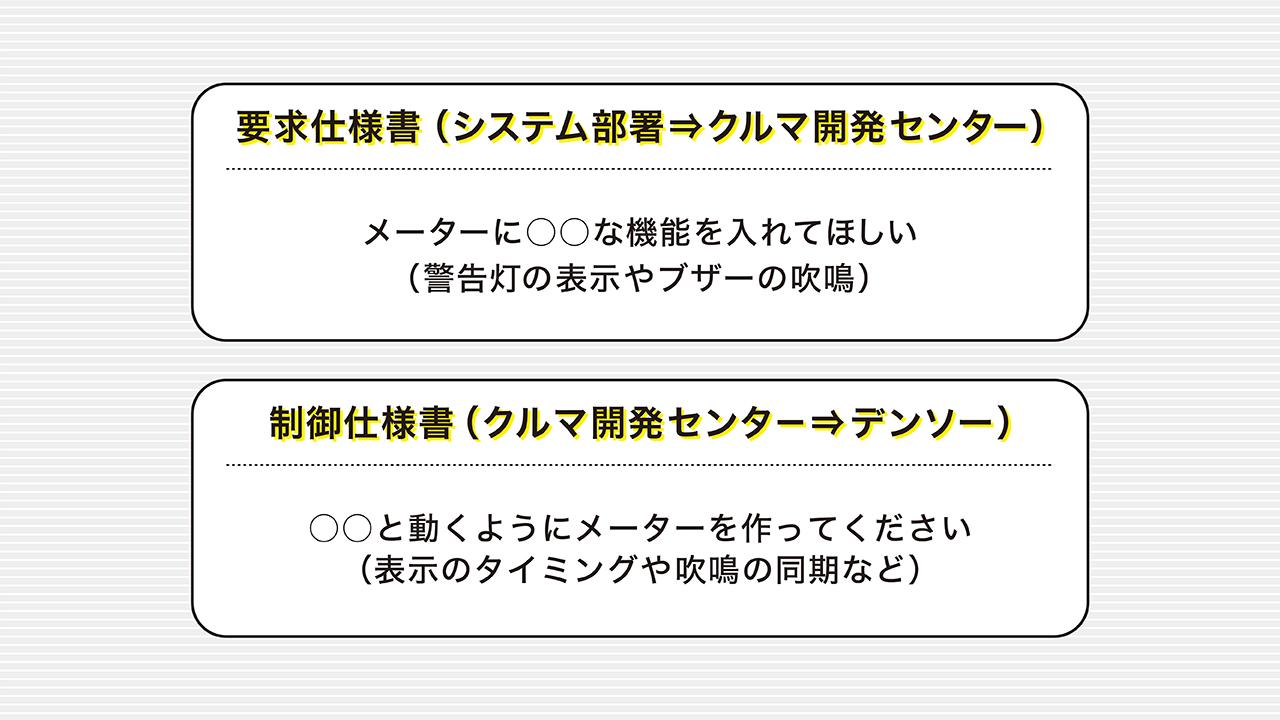
この工程にかかるリードタイムは120日。クルマ開発センターの担当者が、各システム部署に要求依頼をかけてから、デンソーに発注するまでに4カ月かかっていた。
なかでも時間がかかっていたのが、要求仕様書が完成するまでの意見交換の連携。クルマ開発センターは、納期を伝えたうえで、早めに各システム部署に要求を出すようお願いする。それをそのまま要求仕様書にまとめられれば楽なのだが、そうもいかない。なかなか要求が集まらないのだ。川上リーダー
「余裕があるよね」「まだ出さなくていいよね」と、前工程は思ってしまいます。なので、実際、締切間際に多くの部署がまとめて仕様書を出してくるので、ここで現場の開発担当者はすごく苦労しているのです。一方で、(依頼してから)初めの頃はあまり(要求が)来ない、ということも起こっています。
結果として、締切に欲しいレベルのものが来ず、要求仕様書の発行が遅れたり、自分たちで制御仕様書を作るときに「あれ、要求仕様書が、また間違ってるよ」ということで多少進みかけていたものが後退したりするのです。
ここでは、2つのムダが見えてきた。手待ちのムダと、不良・手直しのムダである。
最初に要求を出すようお願いしてから、2カ月間何も動きがないこともあったという。ムダな待ちの時間がある一方で、締切間際に作業が集中する。その結果、精度が落ちて、やり直しが発生する。そしてさらに時間がかかる。そして納期が差し迫るところで、現場の担当者に負担がかかってしまう。
この2つのムダの改善に着手した。まずは、取り掛かるのが早過ぎたということ。しかし、取り掛かるタイミングを遅らせれば、解決するのかと言えばそうでもない。川上リーダーが言うように、短期間で大量の要求を処理するとなると、現場の担当者が大変になる。つまり、スタートを遅らせたうえで、納期直前に発生しているやり直しを減らす必要があった。
そこで、どんなやり直しが発生しているのかを調べるところから始める。服部サブリーダー
一つひとつ分析していきました。すると、約8割は誤記やルール順守ミス。決まりに従っていない、ということが分かってきました。
川上リーダー
ほとんどが誤字脱字のやりとりだったり。そのほか、「このフォーマットにはどう書けばいいんですか?書き方が分からないので、教えてください」といった問い合わせが多いことも見えてきました。例えば、“「解除」という言葉の英訳は「deactivate」”というルールがあるにもかかわらず、「cancel」と記入するミスがあり、再入力を要求する、といった具合だ。
ここで、「誤字脱字に気をつけてください」「きちんとフォーマットに従ってください」という相手への要求ではなく、「なぜそうしたミスが発生するのか?」に目を向けるのが、TPSだ。
技術部では、システムへの入力後の確認にはチェックシートを使うことが多いという。「〇〇を確認したか?」などの質問があって、マスにチェックを入れていくものだ。ところが、そのチェックシートの確認内容が、誰がやっても同じ答えになるものになっていなかった。担当する人によって、答えに差が出てしまう内容であったために、あるときには気がつけていたミスに、気づけないときがある。バラツキが出ていた。
作業する人によって出来るものが変わってしまう状況。これを改善するときに役立つのが、標準作業だ。完成品の品質基準を明確にして、その基準をもとに、バラツキがあった作業を標準化していく。前編でも触れた「品質を工程でつくり込む」という考え方だ。
今まで長時間かけていたものを短くする。それだけでは現場に負荷がかかる。だから、ムダの原因を突き止めて解消していくことで、現場の負担を軽減する。その結果、120日かかっていたリードタイムは、35日まで短縮されたという。後工程の声に耳を傾ける
上記のほかに改善に取り組んだ課題が2つ。
一つは、クルマ開発センターが発行した制御仕様書に対して、仕入先であるデンソーから大量に問い合わせが相次いでいた問題。問い合わせの多くが、仕様書の不備や誤りなどであった。単純な不良をデンソーに流してしまい、迷惑をかけていたという。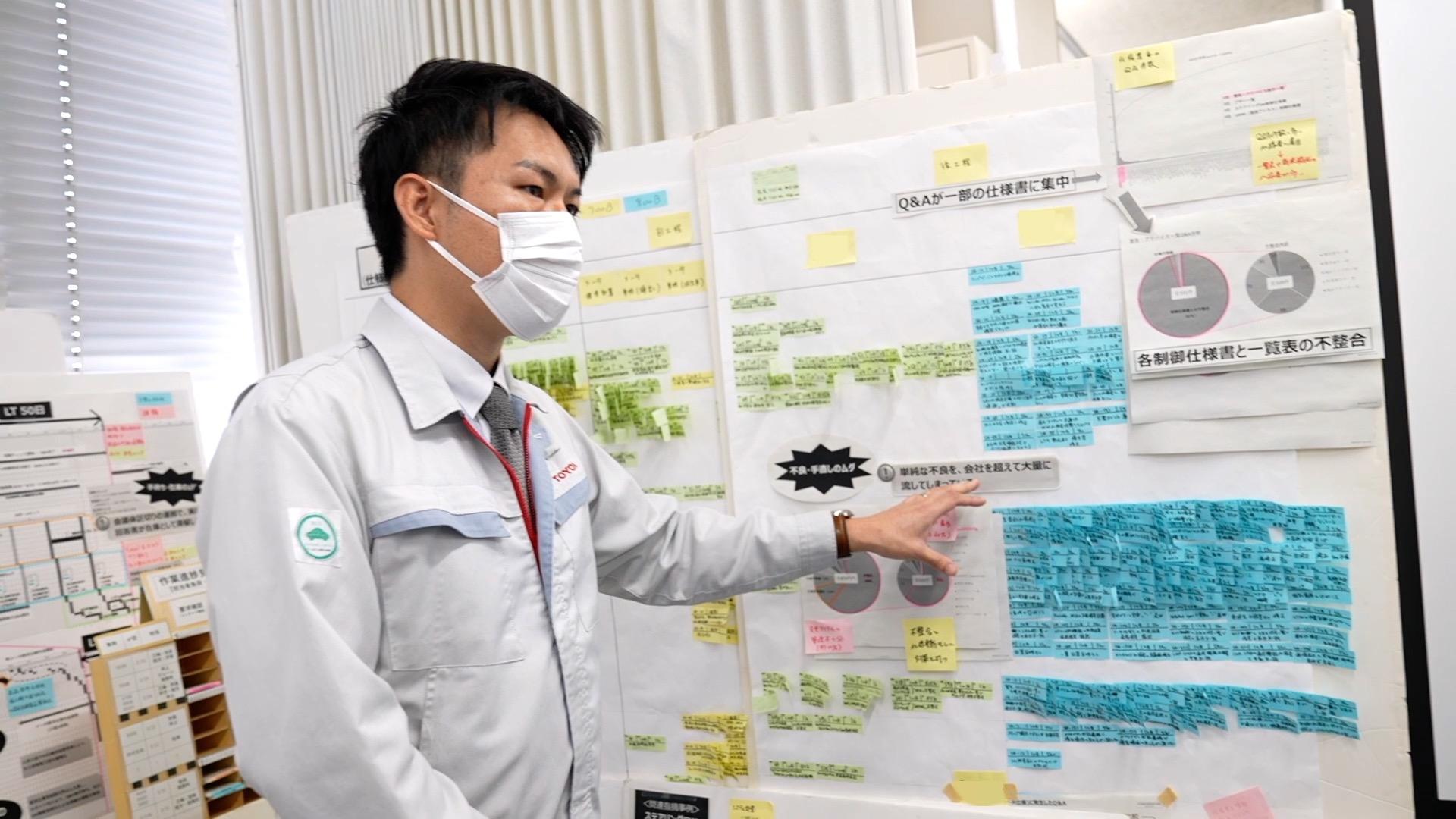
もう一つは、クルマごとのメーターの仕様を決める工程。車種によって仕向け地が異なり、スピードの表示形式をキロにするのか、マイルにするのか、など細かい仕様を決める。こうした細かい仕様をメーターの品番ごとに定義してまとめたものをバリエーション表という。このバリエーション表の作成過程において、集めるべき情報の種類が定まっていなかったり、人による転記作業が多かったりと、完成する表の内容にバラツキがあった。
さらに、そのバリエーション表の形式自体も、トヨタ車体やレクサスなど車両製造を担当するグループごとによっても一貫されていなかった。
つまり、これらを受け取る後工程のデンソーにとっては、バラバラなものを統一する必要があったのだ。
川上リーダー
クルマごとに物と情報の量と形が異なるので、デンソーにとって非常に扱いづらいものになっていて、その都度来る情報を自分たちが使いやすいように一度転記していたのです。そういったムダな作業をさせてしまっていたことに気がつきました。
ここでも、バラツキを改善するために各作業を“標準化”することに取り組んだという。その際に意識したポイントが、後工程である「デンソーにとって必要な物と情報の量・形」に基づいて標準を定義することだ。
川上リーダー
実際にバリエーション表はデンソーにどんな使われ方をするのか?また、どんな形であればうれしいのか?ということを会話しながら、標準の形を決めています。
トヨタ目線で都合のいい情報、レクサスにとって都合のいい情報。しかし、それを受け取っていたデンソーは使いにくく、(余計な)作業が必要となっていたので、「デンソーがどういうカタチで情報をもらうとうれしいですか?」というように標準を議論しています。
デンソーに実際に足を運んで、バリエーション表がどのように使われているか、現地現物で確認。現在もバリエーション表の統一に向けて作業している最中だという。
仕入先が語る、ほんとのところ
今回の事技系TPSの取り組みは、客観的にどう見えたのだろうか?そして、実際どんな成果を感じたのだろうか?クルマ開発センターの後工程であり、トヨタの社外でもあるデンソーの担当者に話を聞くことができた。インタビューに応じてくれた和田担当次長と吉田課長は、単なる後工程ではなく、今回の改善に一緒に取り組んだメンバーでもある。
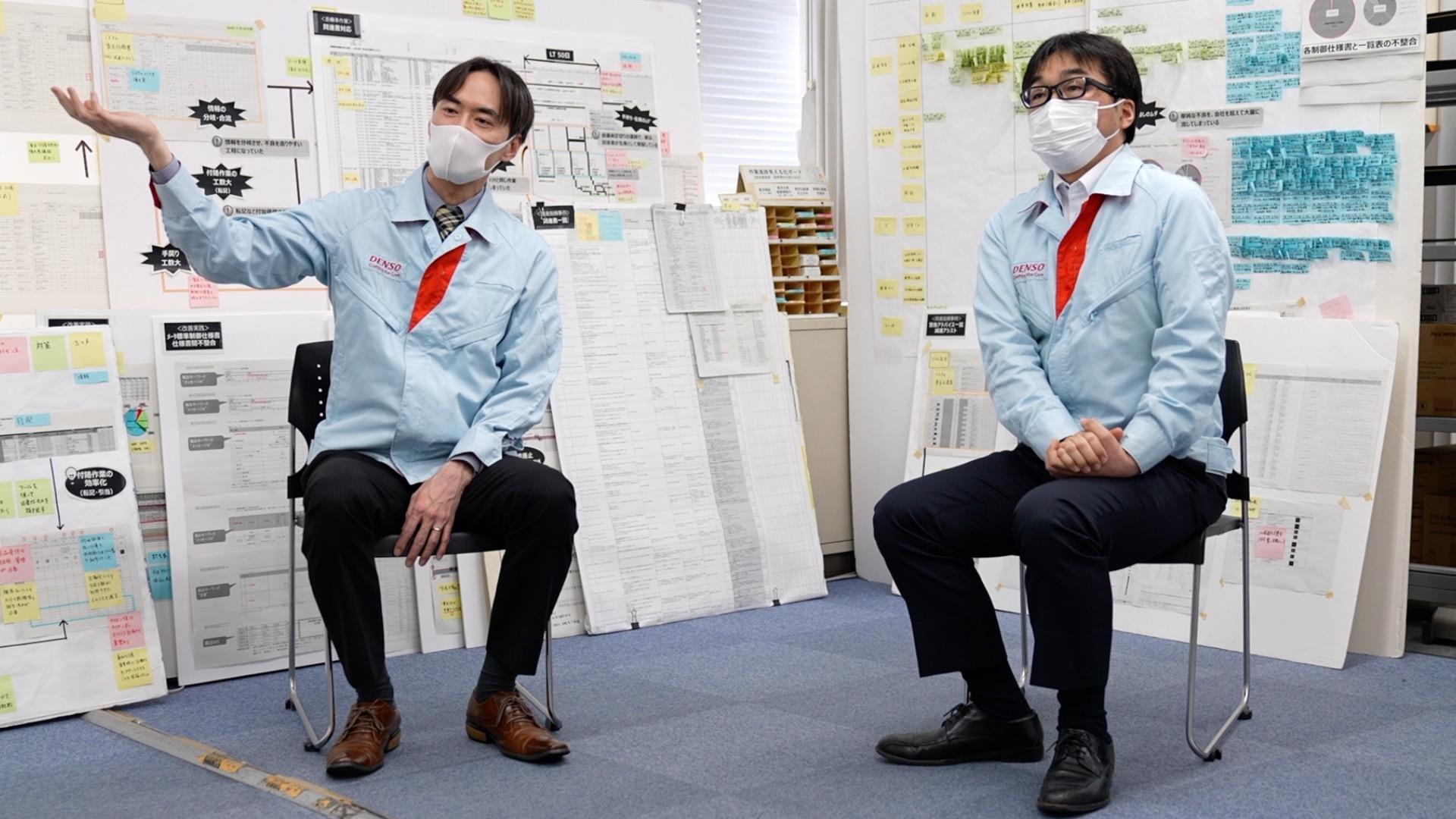
森田
今回、関係仕入れ先としてデンソーのお2人にもトヨタの事技系のTPS自主研の取り組みに関わっていただきましたが、この話が来たときに、率直にどう思われましたか?
和田担当次長(デンソー)
昨年9月に話をもらって、第一声で言わせていただいたのは、「本気でやるんですよね?」という言葉でした。どこまで深くやるつもりなのかを最初に確認したいと思ったからです。と申しますのは、今までも同様の活動をトヨタさんと一緒にやらせていただいた経緯が過去に幾度かあったからです。
森田
どこまで本気なのかを問いたいと思われたのは、どうしてですか?
和田担当次長(デンソー)
言いづらくはありますが、過去には途中で挫折してしまった活動もあったと感じています。これまでのいろいろな活動を踏まえて、今回はどういう仕組みでどこまでやろうとしているのかを教えてほしいという思いでした。「本気ですか?」「途中で挫折した過去」、いきなり強烈な言葉が並んだ。では、なぜ今回も協力してくれることになったのだろうか。
聞けば、今回の取り組みが、トヨタ全社をあげて、しかも、そのための専属部隊を設けてTPSをやっていくところに、本気度を感じたからだという。自主研のために結成されたチームが、クルマ開発センターを助けるという想いで取り組んでいるところを見て、今回は「うまくいくかもしれない」と思ったそうだ。
吉田課長(デンソー)
今回、かなり忌憚のない意見を言わせていただいているんです。「トヨタさんも、まだここができていませんよ」などと、結構厳しい意見を私から申し上げましたが、それに対して川上リーダーからは、「指摘いただきありがとうございます。もっとどんどん言ってください」とお返しいただけました。それならば、「もっと申し上げます」という流れになり(笑)、とても円滑になっています。一緒にTPSに取り組んでいくなかでカギとなったのが、遠慮なく困りごとを伝えられる関係値だ。そもそも、こうした忌憚のない言葉が最初から出てくるところが、この数か月の間に築かれた両者の関係性を物語っている。
ここで、2020年4月1日、デンソーの広瀬製作所の開所式で従業員を前に語った豊田社長の言葉を紹介したい。豊田社長
トヨタグループの総力を結集し、この大変革の時代をともに生き抜いていく。そして、日本の未来、モビリティの未来を創造していく。
そのためのグループ戦略です。
そこには、「上から目線」も「下から目線」も必要ありません。
必要なものは、もっといいクルマをつくるという「志」だけです。
トヨタとデンソーが、「上も下もない」関係をつくり、グループ全体に示していく。
吉田課長(デンソー)
仕様書の品質があまり良くないまま、われわれ仕入先のところに出てきます。それを受けて、われわれが、「この仕様書は、たぶん間違っていますよ」と、問題連絡書をたくさん出すことになります。それを防ぐために、トヨタさんに対し、「仕様書の品質は、こういうチェックをすると上がるんですよ」といった情報を提供させていただきました。
森田
語弊を恐れずに言えば、被害者だからこそ分かる痛み。「こういうことで苦しんでいます」と。
吉田課長(デンソー)
そうですね。具体的な事例を出して、「われわれはこうやってそれを発見してるんですよ」、「こういうやり方をすると、この不良を事前に発見できますよ」と(お伝えしました)。では、これまでの取り組みの成果についてはどのように感じているのだろうか。
吉田課長(デンソー)
これも忌憚のない意見で言わせていただきますと、組織的にこれを常に続けられる状態が次のステップかなと思っています。現在は、とりあえず改善が始まりました。そして、改善のやり方はとりあえず分かって、やってみたら成果が出ました、という状態だと思います。ここで終わらず、取り組み内容を組織の業務プロセスに組み込んで継続していくことが、次のステップではないでしょうか。
和田担当次長(デンソー)
メーターの仕様書を触る部署の方が今回一緒に活動をさせていただいたクルマ開発センター以外にもたくさんいらっしゃって、全てのメーター仕様書を触る人たちにまで効果が出せるところまでもっていけるかどうかは、これからの課題だと思います。
550万人に広がり始めたTPS
2本の記事にわたって紹介してきた事技系TPS自主研。
生産現場では当たり前のTPSを事技系職場に広げよう、ということで始まったのがこの活動であるが、今回紹介したように、社外にも着実に広がっている。仕入先であるデンソーへの取材を通じて、その広がりの大きさを実感することになった。
今回の活動の成果として、デンソーの2人が強調していたのは、後工程の困りごとを聞く姿勢だ。和田担当次長(デンソー)
ここまでデンソー側に下りてきて、意見を聞いていただいたことはないと思います。今までも意見は求められていましたが、その意見がどうトヨタさんの中で生きてきたかというのは、懐疑的だったんですね。それが冒頭の「本気でやるんですよね?」という言葉にもつながっているのですが、そこを1本にまとめてくれたのが、今回の活動。また、事技系TPSということで、全社で旗振りをして、その事例として取り組ませていただいたので、ここまでのことがやれているのだと思っています。そのうえで、事技系TPS自主研について次のように評価する。
和田担当次長(デンソー)
トヨタさんの思想、TPSは、各部門にしっかりと根付いていますので、自分たちの工程でそれぞれ改善を一生懸命されていると思います。そこをわれわれにまで広げて、「じゃあ、デンソーさんにとってどうなの?」というところまで目を向けてくれたのが、今回の事技系TPSが踏み込んだところだと思います。豊田社長が最初に提示したTPSの解釈、「誰かを楽にしたい」という思想が、しっかりと体現されていた。そして、その思想はデンソーを通じて、さらに外へと広がっていく。
和田担当次長(デンソー)
われわれとしても今後、デンソーの中で発信していかなければと思いますし、またデンソーの発信が他の仕入先への発信にもつながっていくと考えています。ですから、決してデンソーの製品だけとか、メーターという視点だけではなく、トヨタとわれわれ仕入先との関係を含め、大きく広がるのが理想です。最近、豊田社長がエールを送っている、自動車業界で働く550万人も含めて、「自動車業界の構造的なところにも切り込んでいきたい」という大きなメッセージのひとつの活動なんだと感じています。
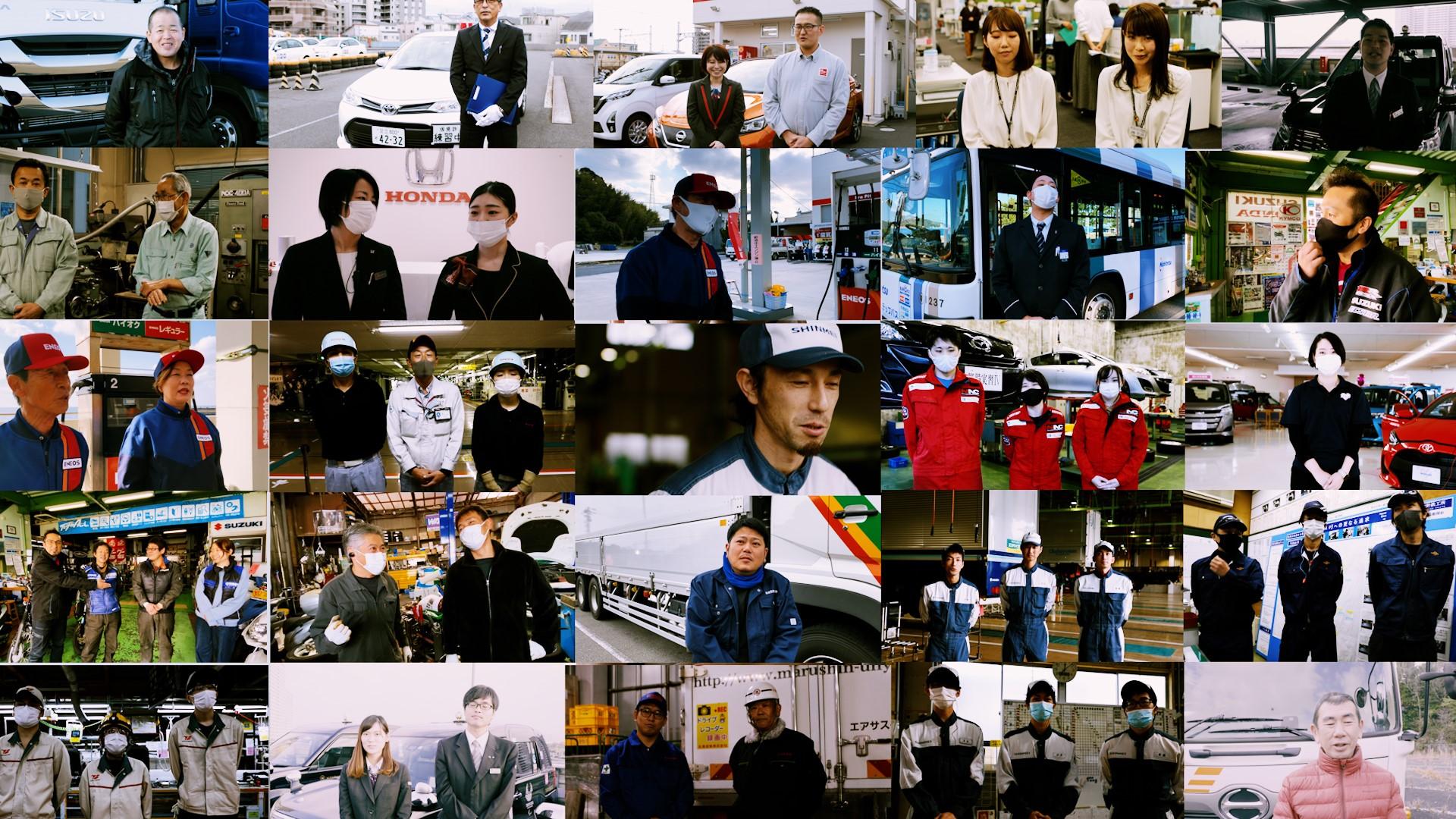
今年1月、自動車工業会の豊田会長から、自動車業界で働く550万人に向けたメッセージが発せられた。「100年に一度の大変革期」を生き抜くために、今こそ自動車産業550万人の力を一つにするときであり、それぞれの一歩が大きな力になる、という強いメッセージだった。今年のトヨタの春交渉では、「自動車産業を支える550万人にどうやって貢献していくのか」というテーマで議論が行われた。
デンソーの和田担当次長から、550万人という言葉が出てきたのが、非常に印象的だった。
和田担当次長(デンソー)
最初に、(豊田社長に)「誰かの仕事を楽にするために」と言っていただいたおかげで、今回の活動を始めることができました。われわれにも協力会社がありますので、同じ考えのもと、やりとりをしていかないと、活動は広がっていかないのではないでしょうか。それが実現すれば、たぶん全ての工程で本当のジャスト・イン・タイムができてくると思います。豊田社長がおっしゃっていた「TPSは誰かのために」という考え方は、私も、一緒にやっているメンバーの心にもちゃんと響いていて、今後も大きく広めていこうという想いでいます。今回のクルマ開発センターの取材では、具体的な改善活動について細かい部分まで見させてもらった。もちろん、リードタイムが縮まった、不良が減った、などの目に見える成果も重要だ。
だが、TPSの大きな柱は、これに関わる人々の想い、その広がりにあるのかもしれない。後工程であるデンソーの2人が、自分たちの後工程のことをすでに考え始めている。これが、今回の取り組みの成功を物語っている気がした。TPSに終わりはない。(編集・庄司 真美)
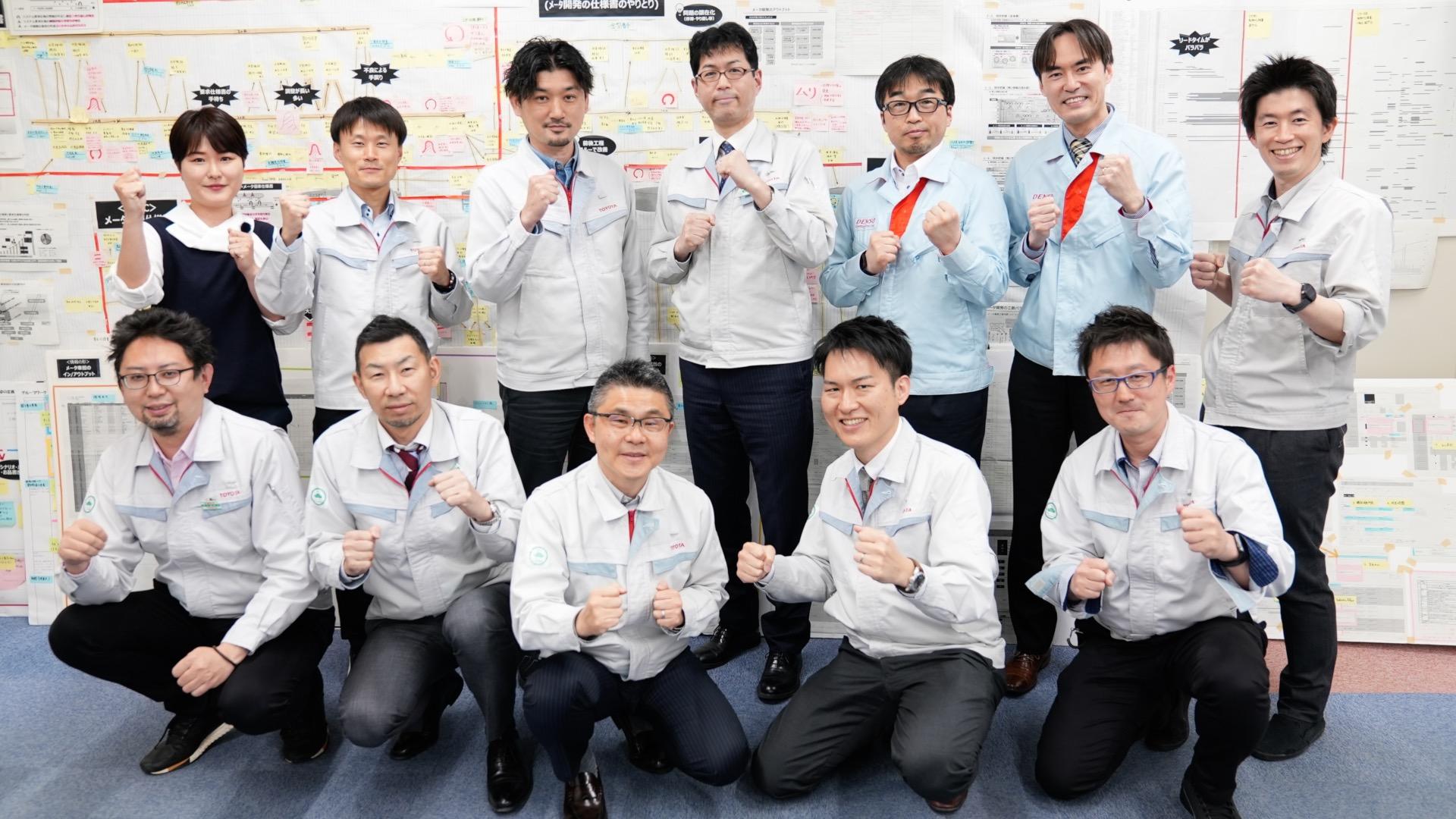