
トヨタの生産現場では当たり前のTPS。これを工場の外にも広げる活動が始まった。その成果を発表する合同発表会に密着した。

2021年3月30日、愛知県にあるトヨタグループの研修所で行われていたのは、「第1回 事技系職場 トヨタ生産方式自主研究会 合同発表会」だ。
まず、トヨタ生産方式(以下、TPS)とは何か、おさらいしておこう。TPSとは、「ムダを徹底的になくして、よいものを安く、タイムリーにお客様にお届けする」、トヨタの経営哲学だ。ここで言う「客」は、実際にクルマを購入する消費者だけではなく、自分の仕事の後の工程すべてを指す。
TPSの2本の柱が「自働化」と「ジャスト・イン・タイム」である。
ニンベンのついた自働化であって、自動化ではない。異常があれば止まるように、設備に人の知恵をつけて、不良品をつくらないようにする。「品質を工程でつくり込む」、「人を機械の番人にしない」というのが代表的な考え方だ。
一方、ジャスト・イン・タイムは文字通り、「必要なものを、必要なときに、必要な分だけつくる」ことである。
さて、今回の何やら名前の長い発表会。TPSを自主的に研究して発表する場であることはわかるのだが、事技系職場とはなんだろう?
事務職の「事」と、技術職の「技」を合わせて事技系職場。実際にクルマをつくる工場などの生産現場と区別してこう呼ぶ。具体的には、人事や経理、広報、部品調達、ソフトウェア開発などの、“非”生産現場を指す。
これまで生産現場では、工程それぞれの課題を丁寧に見極め、改善を続けてきた。自発的にTPSを学ぶ自主研究活動(以下、自主研)も30年以上前から行われ、TPSという共通言語を持った人材の育成に取り組んでいる。そしてそれが、トヨタを成長させる大きな強みとなってきた。
今回の発表は、工場では当たり前になっているTPSを、工場の外にも広げていこうという取り組みだ。生産ラインが流れる工場だけのもの、と思われがちなTPS。決してそんなことはない。トヨタの事技系職場に広がり始めたTPSについて、トヨタイムズの新人記者、森田京之介が取材した。TPSの原点とは?
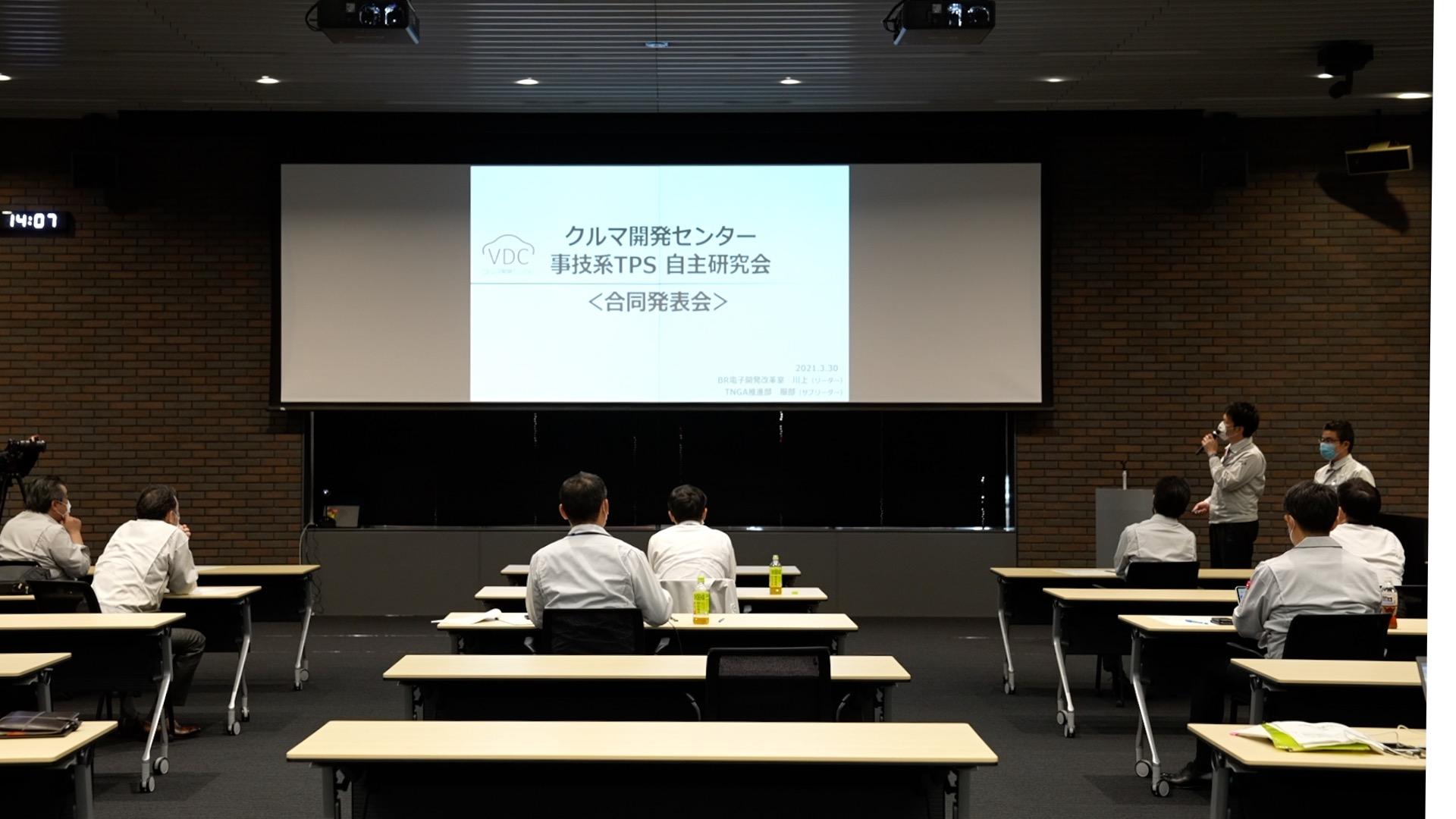
2020年8月、事技系職場におけるTPS自主研が全本部・カンパニーで立ち上がり、24のテーマで改善活動が行われた。
今回の発表会では、総務・人事本部、事業・販売ビジネスユニット、クルマ開発センターの3部門がそれぞれの取り組みと成果を発表。前のTPS本部長の友山茂樹エグゼグティブフェロー(以下、EF)、そして尾上恭吾TPS本部長、TPSのキーパーソン2人が発表に耳を傾けた。
友山EFは、モータースポーツの話題でもよく名前が上っていたが、もともとの出身はTPSを推進する生産調査部で、“改善マン”としてキャリアを積んだTPSのプロフェッショナルだ。具体的な発表内容については、後日掲載する記事に譲るとして、TPSを事技系職場に広げることの意味について2人に話を聞いた。
尾上本部長は今回の取り組みのきっかけについて次のように話す。
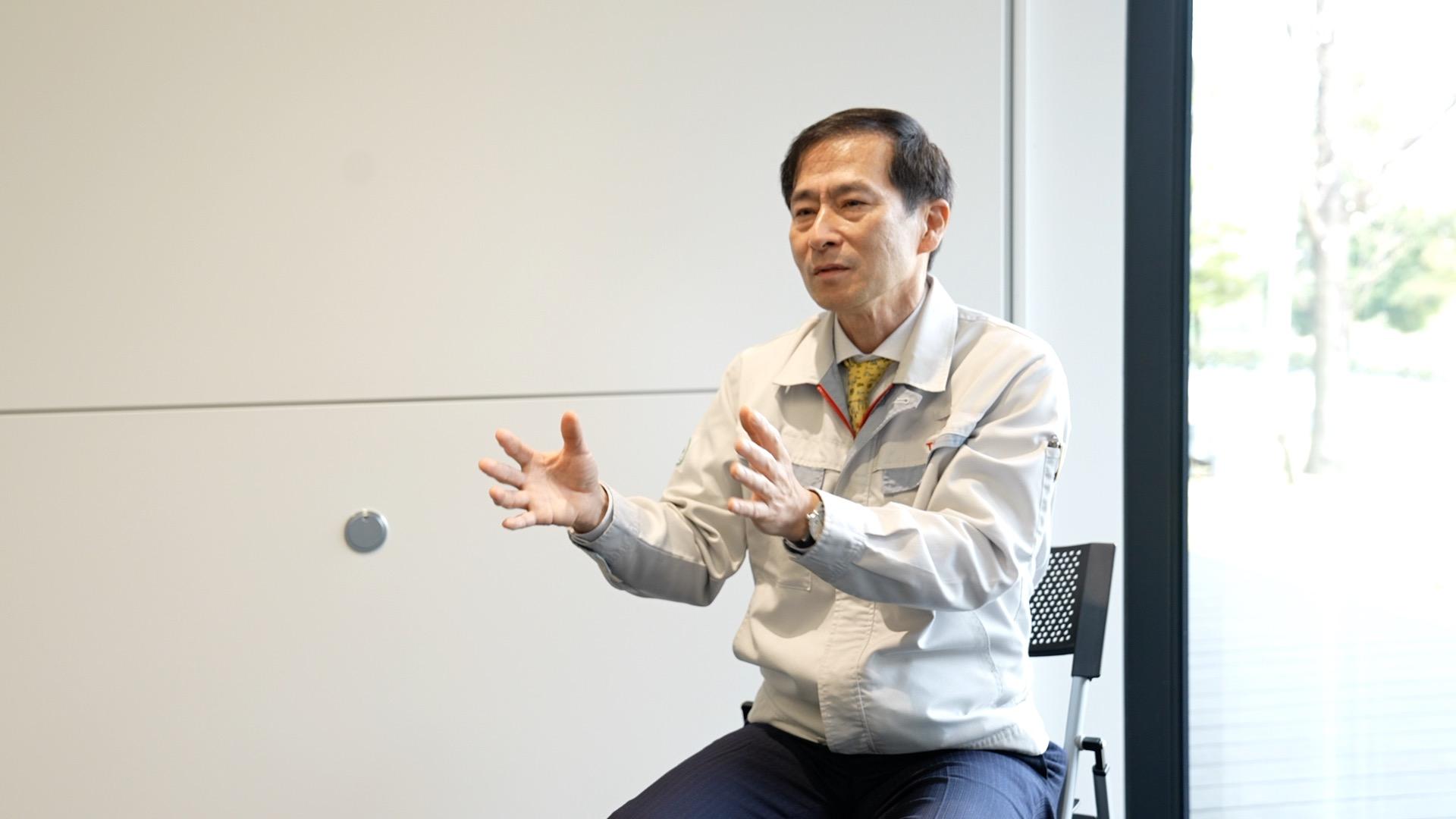
尾上本部長
実は、トヨタの従業員7万人中、事技系職は2万5,000人程度。2万5,000人のうち、どれくらいがTPSの勉強をしているかを調べたところ、1万8,000人はTPSの教育を受けていないことがわかったのです。
そんな状況で、TPSが今後のトヨタの文化になるのかという懸念はもちろん、事技職の従業員の一部は、将来会社経営を担う人材にもなります。そこで新たにTPSの教育システムをつくり始めました。
教育を受ければTPSの知識は身に付きますが、それが実践できるかはまた別の話。そこで、実際の改善を始めることになりました。尾上本部長が経営幹部に自主研を始めることを報告したところ、豊田社長から「最初の講演は私がやる」との提案があったという。それが昨年8月のこの記事である。

改善メンバーを集めたキックオフの場で語られたのが、春交渉の場でも言及があったTPSの豊田章男流の解釈である。
「TPSの原点は誰かの仕事を楽にすること」
これが改善メンバーの背中を押すことになったという。
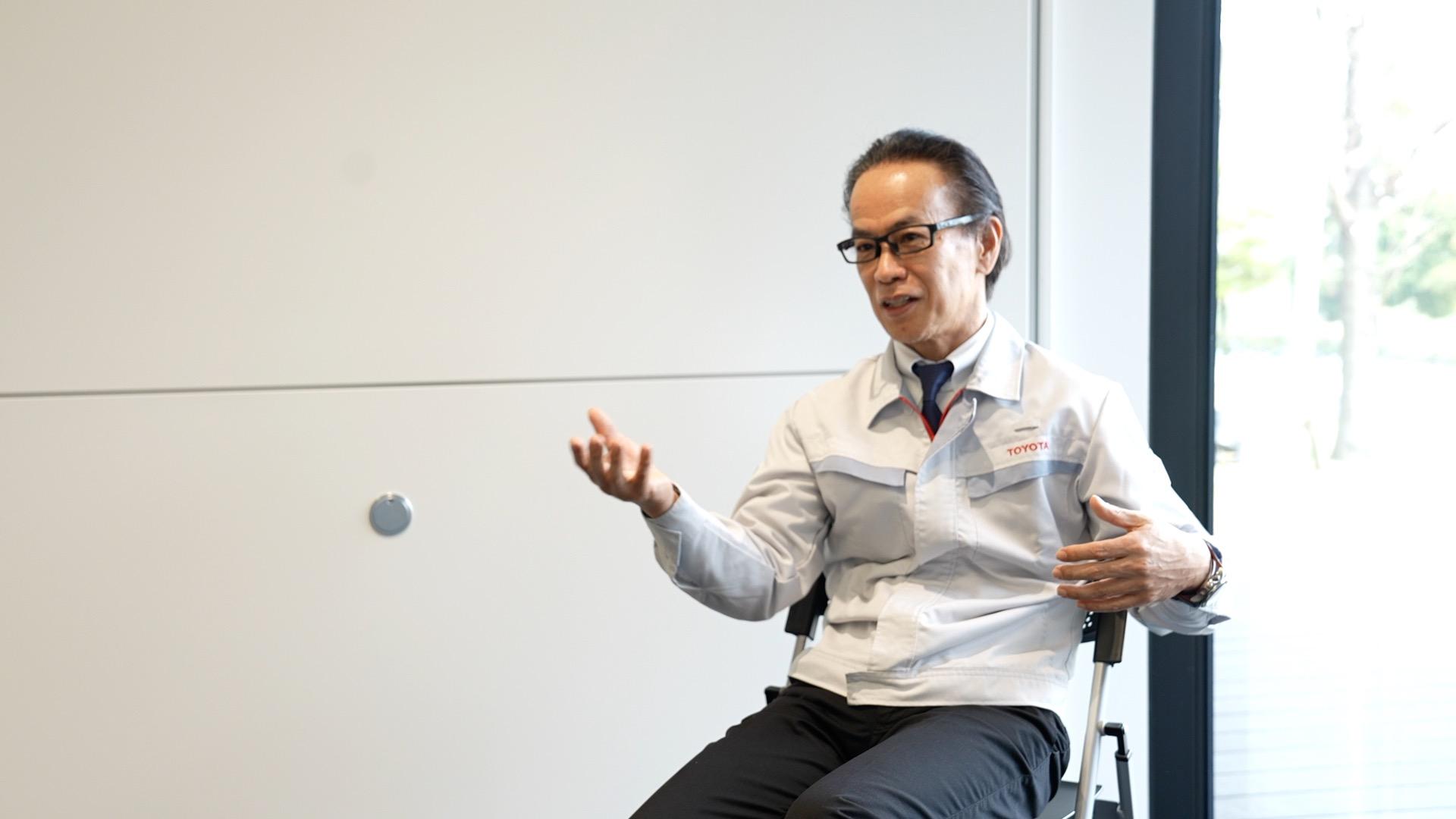
友山EF
やはり、豊田社長の存在が大きいです。自らTPSを深く理解し、実践できるトップは、世界中の企業を見ても、恐らく豊田社長以外にはいないのではないでしょうか。それと、僕はトヨタに入って40年になりますが、それより前は別として、ここまでTPSを経営の前面に掲げたトップは見たことがありません。それだけに、豊田社長の存在感は、TPSのリーダーやサブリーダー、改善メンバーにとって、大きな心の支えになったのではないかと思います。
第1回のキックオフのときに、豊田社長が講話をしてくれました。その中で、「TPSはなんのためにやるの?」と問うたとき、ほとんどのリーダーが「自分の業務をもっと効率的にしたい」と答えました。
それを聞いた豊田社長は、「それは違うよ。TPSは誰かを楽にしてあげるためにやるもの」と語り、創業者の父の豊田佐吉が自分の母親を楽にさせたくて、機織り機をつくったストーリーを話したことに衝撃を受けました。
尾上本部長も、この社長の言葉が、事技系TPSを展開していくための共通の言語として役に立ったと話す。この「共通言語」というのは、まさにTPSそのものだ。
友山EF
実際TPSに取り組んでみると、職場の上司や中間管理職、GM(グループ長)、一般の社員、さらには派遣社員の人まで、価値観を共有することになります。
今まで職場ごとに縦割りだったものが、TPSという物差しで見ると、周りの職場におかしい点があるんじゃないか、自分の職場が迷惑をかけているんじゃないか、といった目線になります。職域や職層を超えた共通の価値観をTPSが提供することで、今までなかなか進まなかった改善が一気に進む可能性を感じるでしょう。今、TPSを事技系職場に取り入れる理由
友山EFは、「ジャスト・イン・タイム」、「ニンベンの付いた自働化」といったTPSの考え方は、生産現場に限らない普遍的なものであり、TPSが事技系職場に広がることがトヨタの競争力向上につながると力を込める。
友山EF
豊田社長は、2019年に、トヨタは、カーカンパニーからモビリティカンパニーに変革することを宣言しました。これは、同業他社以外にもいろんなコンペティターもいるなかで、生産だけでなく、アドミニ、技術、営業、サービス、すべての工程でリードタイムを短縮し競争力を上げていかなければならないことを意味しています。TPSは、今後トヨタが生き残るための大きな武器になると考えています。
また、トヨタがモノづくりで培ってきたTPSというアドバンテージを幅広く活用して、人間社会に貢献していくことも、トヨタに託された大きな社会的使命になるでしょう。トヨタは、モビリティカンパニーにモデルチェンジしていくなかで、ソフトウェアファーストという新しい考え方を導入している。これは、トヨタが得意とするハードウェアに先行してソフトウェア開発に取り組むという考えであるが、ソフトウェア開発という非生産現場でもTPSは活きてくるという。
友山EF
ソフトウェアの開発にしても、企画・設計、プログラミングをして、テストをするといった工程があります。工程ごとに良品基準を定めて品質をつくり込む、また、工程間の滞留を減らし、リードタイムを縮めていく。ここにTPSを適用することが、トヨタのソフトウェア開発において他社との差別化にもつながると考えています。
クルマはお客様の命を預かり、物理的に移動する価値を提供する商品です。タイヤもサスペンションもパワートレーンも必要です。ハードウェアはなくなることはありませんが、一方で、クルマの制御の多くの部分がソフトウェアにシフトしています。
だからこそソフトとハードを同期させながら開発し、品質を上げていかなければなりません。ハードの品質を上げることは、現在も工場でやっていることですが、ソフトの品質も上げながら、リードタイムを縮める必要があります。創業以来積み重ねてきた強みが100年に一度の大変革の時代を生き抜くうえでも大きなカギになりそうだ。とはいえ、TPSが事技系職場に浸透していくためには、多くの乗り越えるべきハードルがある。友山EFから出た言葉は“悩む力”だ。
友山EF
実際に取り組んでみたら難しさが分かり、改善メンバーは、おそらく職場の人と我々指導員の間に立って相当苦悩したのではないかと思います。
僕も実は、TPSを生産調査部でやっているときは、毎日眠れないぐらい苦悩しました。だから事前にメンバーには、「おそらく眠れないぐらい悩むよ。でも、それは“悩力”、すなわち悩む力が育っているから。心の筋肉がどんどん育っていると思って、眠れなくても気にすることはないよ」と言っておきました。誰かの仕事を楽にするために、目の前の問題と向き合い続けることはやはり体力のいることだ。実際に今回発表を行ったメンバーからも、大いに悩んだとの声が聞かれた。
そんなときに、改善を前に進めたのは「仲間」の存在だったという。友山EFからも仲間をつくって一緒に悩むようアドバイスされたそうだ。その仲間をつくるうえで大事だったのは、「やってみて、それを見せる」こと。まず自分がやって見せて、その結果、誰かが楽になると、手応えを感じた周りも動き出す。好循環が始まるという。
尾上本部長は、違った角度からTPSの難しさを語る。尾上本部長
実際に仕事しているみんなは、自分がムダな仕事をしているとは思っていません。むしろうちの会社の人間は本当に真面目な人が多いので、与えられた仕事を一生懸命やっています。
森田
自分が一生懸命やっている仕事は、やはり否定されたくないし、むしろその価値を認めてほしいものですよね。そこに待ったをかけるのが、TPSの役割でもありますよね。
尾上本部長
改善というのは、ある意味、現状否定なんです。「今より良くしよう」と言うと、「あなたのやっている仕事は良くないから直そうよ」と言われているようにも聞こえます。そこの点は、上手にアプローチする必要がありますね。
「すごいな、ここまでやってくれたのか」と。「でも、ここまでやったら次これができるよね?」というようなアプローチ。やっぱり褒めて育てるのも大切かなと私は思ってるんですよね。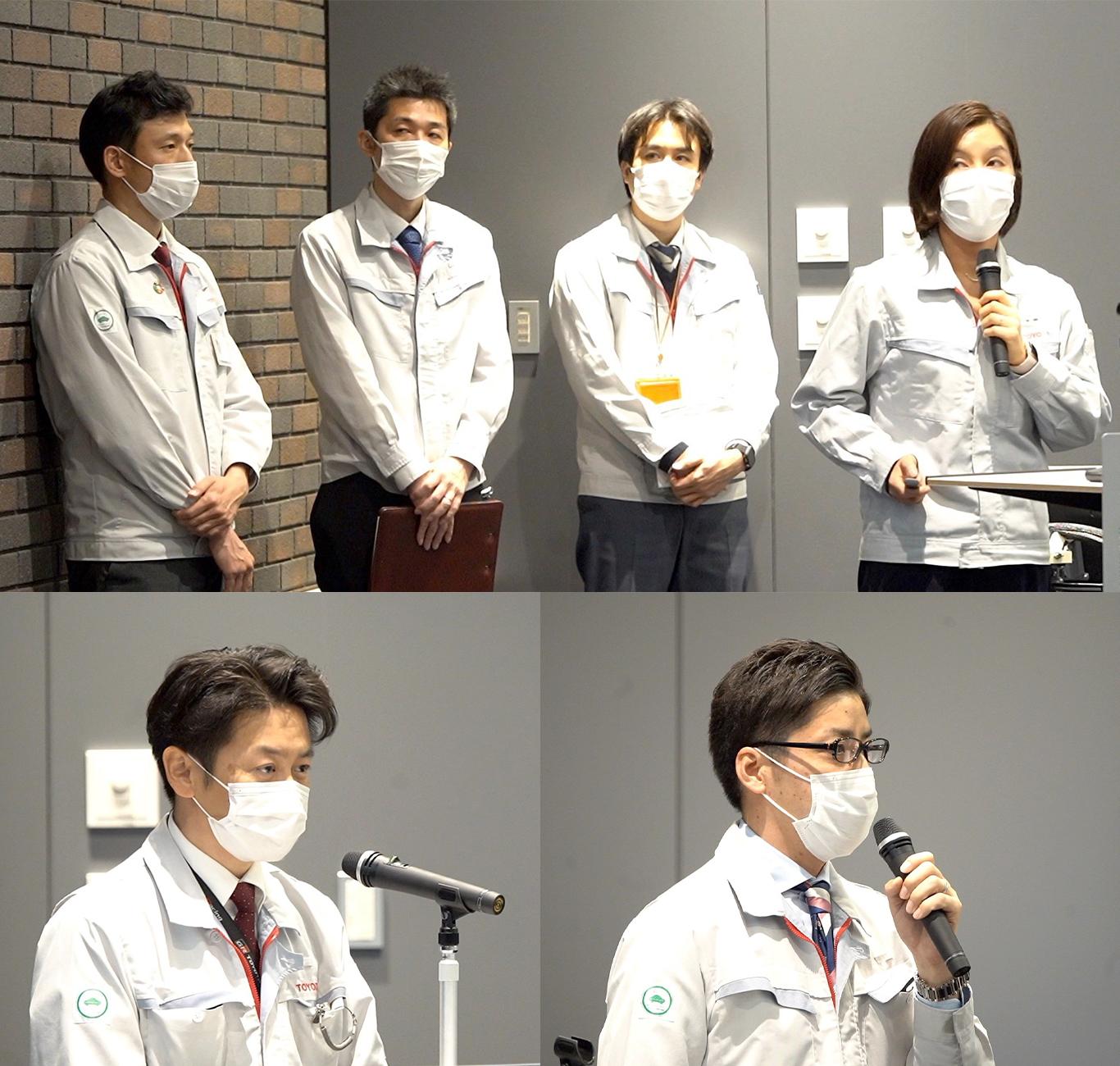
自分の仕事を見える化する
尾上本部長が、今回の活動以前に事技系職場で実際にあった改善事例を紹介してくれた。
一つ目は、ある技術部(法規認証部)のケース。その部署では、VIN(クルマ1台ごとに1つ付いている車両識別番号)の設定を担当している。このVINは、車体に打刻するときに一つでも設定ミスがあれば、そのクルマは廃車になってしまうほど重要な数字。それゆえ担当チームは、安心のため早めに作業を開始し、何人も、何度もチェックすることを長年積み重ねてきた。
改善前は新車の生産開始15カ月前にVINの設定を始めていたが、製造工場やエンジンの型式の変更などがあるたびに、VINを設定し直す。その数、なんと15回。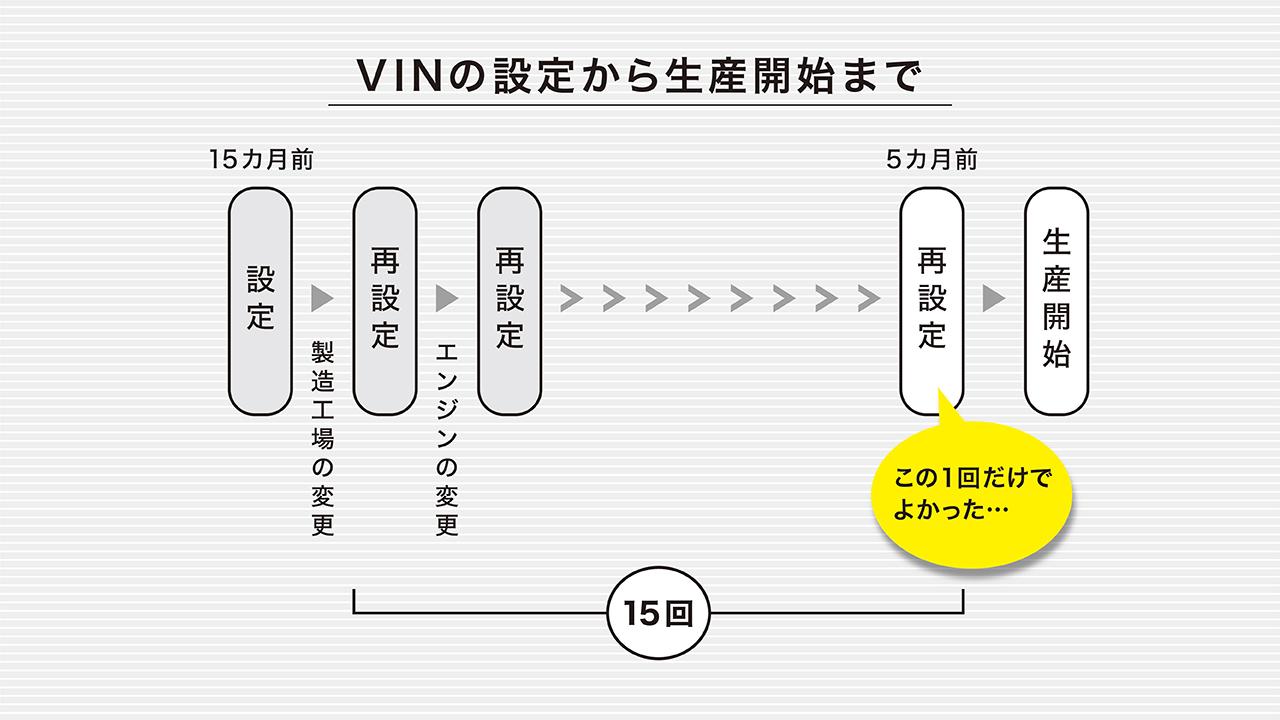
尾上本部長
最初の14回やらずに最後の1回だけやったらどうでした?
担当者
すっきりしました。最後の1回だけでよかったことに自ら気づくことができました。
最終的に使用されたVINが決まったのは、生産開始の5カ月前。つまり、仕事に取り掛かるのが早過ぎたのだ。そのせいでムダなやり直しが発生していた。なぜ最初から気がつかなかったのだろうという簡単なことが、長年続けていると見えなくなっている場合がよくある。こうしたムダに気がつくことがTPSの第一歩だ。
もう一つは経理の決算業務。経理部門では、3カ月に1回の四半期決算のたびに、従業員が夜遅くまで残って作業するのが当たり前になっていたそうだ。
そこで、改善に着手した。決算に携わる56人全員の仕事について見える化。「何をやっているの? 」「後工程はどこ?」「なんのためにやっているの?」といったことをすべてリスト化し、次の工程の担当に1つずつ聞きに行った。すると、実は10%が「いつもこの書類をもらっているけど、使っていない」ということがわかった。
なぜそんなムダな作業をしていたのか。「10年前にあるトラブルがあって、念のためにやり始めて、それ以来ずっとやっている。でも、1回も使ったことない」そうだ。実際に次の決算でその作業をやめても、まったく問題はなかった。
これを入り口に、ムダを一つずつ潰し改善を重ねた。その結果、1年後には決算業務工数の30%を低減できたとのこと。
この活動をきっかけに、税務申告、原価の設定、資金運用や火災保険の契約更改など本部内の多数の職場でTPS活動が広まっていった。生産調査部のコーチを受けTPSの本質を学び、新人から業務の中核を担う中堅社員まで、見よう見まねながらも、自分たちでムダを見つけ改善を実践。職場全体でTPSの価値基準に則り、改善に取り組む風土が醸成されていったそうだ。
尾上本部長
これによって浮いた仕事で新たな仕事ができるようになります。本当に意味のある仕事ができるようになったのですが、そういう部分がまだまだ事技系職にはあると思っています。
まずは「物と情報の流れ図」を使って業務を見える化して、「本当にこれはやらなければならない仕事ですか?」と問いかけるのが、TPSの役割。自分の仕事を確実にすれば、後工程のやり直しがなくなります。すると、自分の仕事も後の工程の人も仕事が楽になって、なおかつリードタイムがぐんと縮まるようになります。
トヨタでは、本当に意味のある作業を正味作業という。その作業が付加価値を高める作業なのか考える。TPSには「すべての従業員にできるだけ意味のある作業をしてもらいたい」という想いが込められている。
「改善後は改善前」
2人は、今回の事技系TPS自主研をこう振り返る。
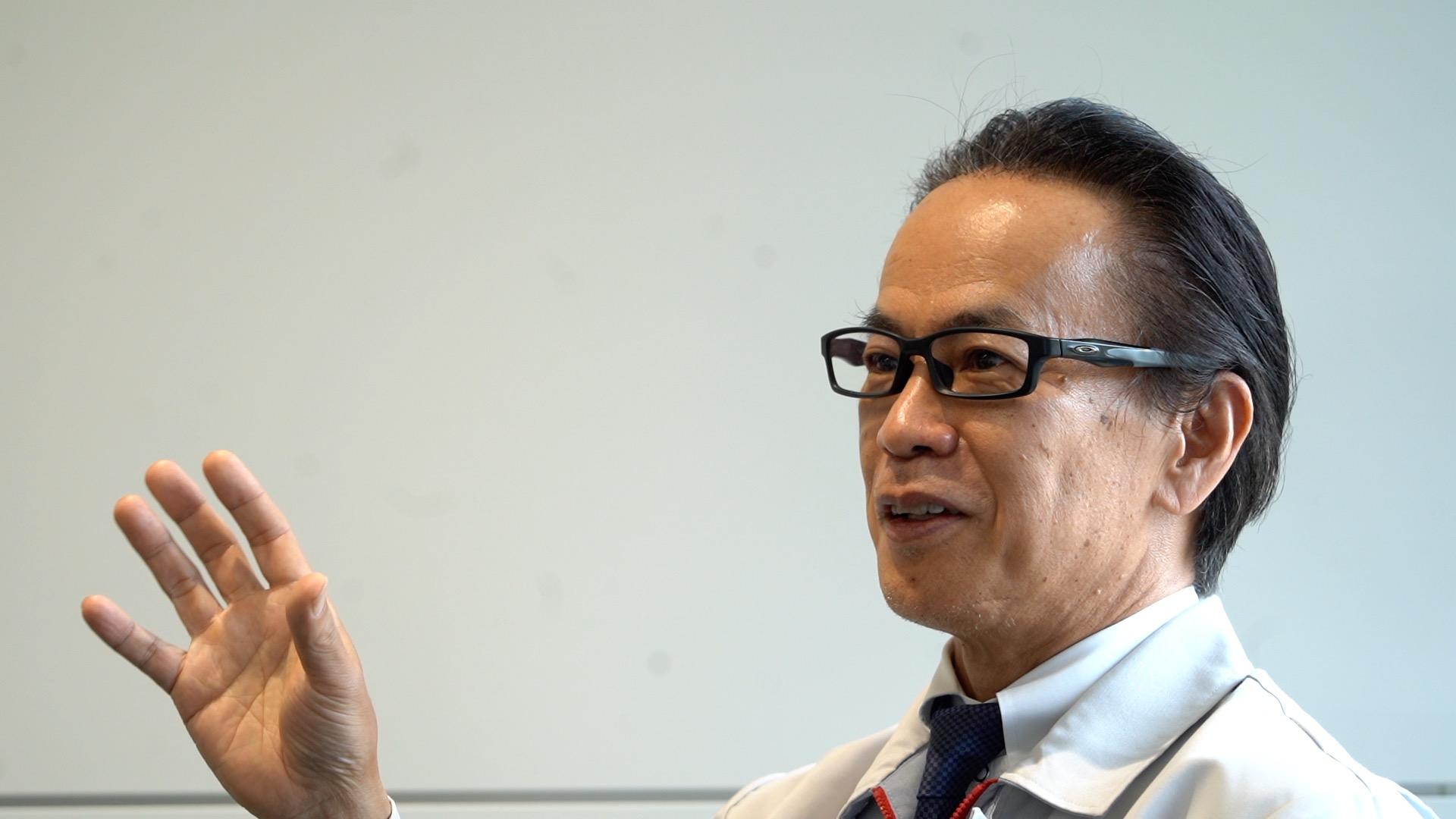
友山EF
今回のアプローチでは最初に、「仕事には必ず工程という概念があるので、あなたの仕事を工程に分けて、そこに『物と情報の流れ図』を線図で書いてください」と伝えました。「物と情報の流れ図」を書いてもらえば、問題や対策が見えてきます。そうなると、指導員やリーダーたちが同じ意識で俯瞰して見ることができるようになります。職場のあらゆるメンバーが同じ意識で問題点を見られる環境をつくったことが、導入部分としては成功だったと思っています。
ある部署にフォローに行ったら、実際に問題点が見えて、リードタイムを縮めることができたと目を輝かせながら報告してくれたので、胸が熱くなりましたね。一方でこんなエピソードも。
友山EF
今回の合同発表会を行うことを豊田社長に伝えたら、「なぜ発表会なんかするの?」と言われました。豊田社長曰く、「この手の発表会は発表者を褒め称えて『ご苦労様でした』で終わりがち。そんなものは経営的には意味がなくて、TPSなんかじゃない」ということでした。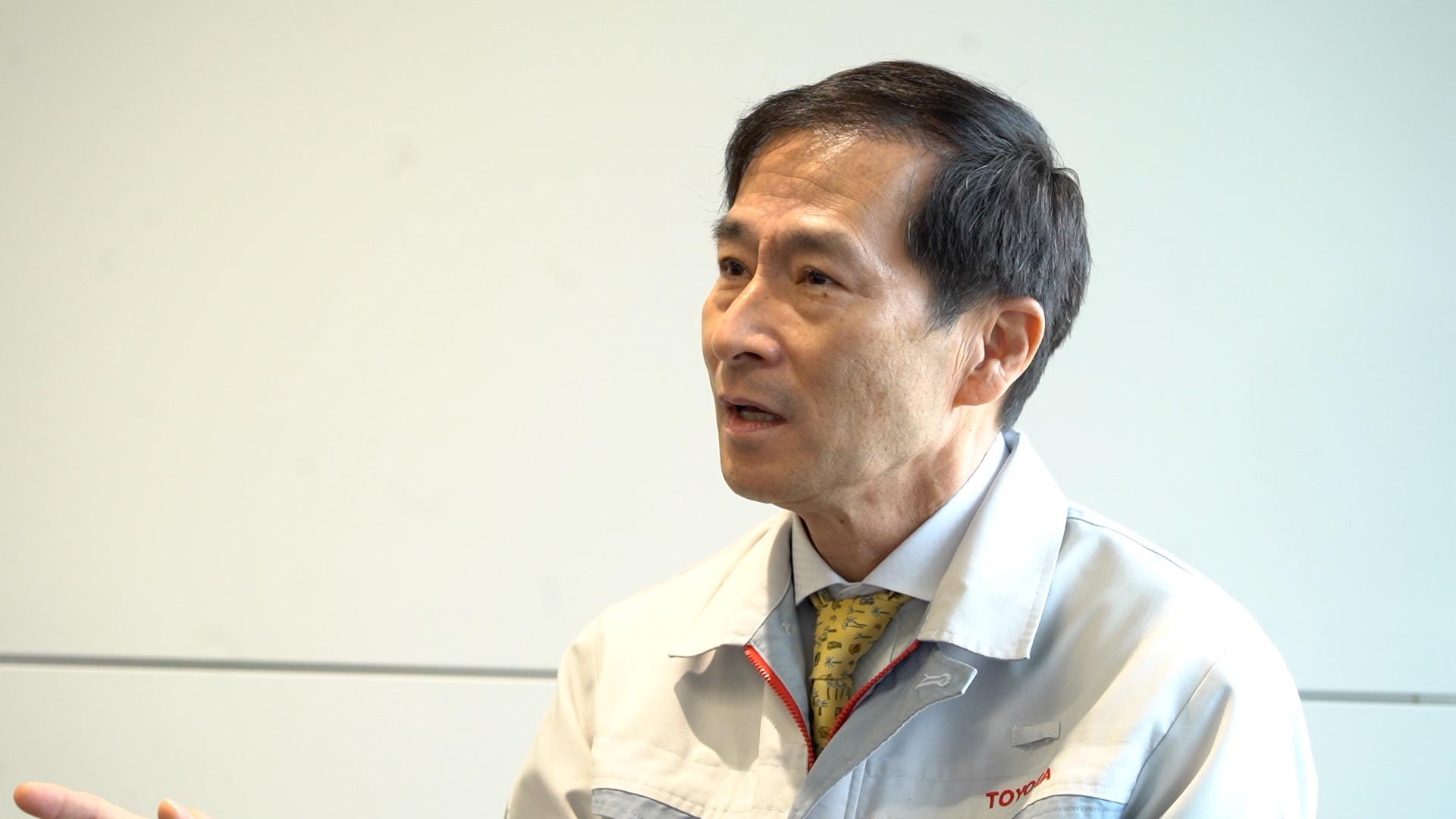
尾上本部長
豊田社長も「Continuous Improvement」と言っているように、改善に終わりはありません。友山さんが好きな言葉は、「改善後は改善前」。これは私もずっと使わせてもらっていて、「ここまでやれた。だから改善後だけど、今日から改善前だよね」と言っています。トヨタに“変人”を増やしたい!
では、どのように改善が広がっていくのか。
友山EFは独特な言い回しで、今後の展開に期待する。
友山EF
世間一般的にTPSを信奉して推進する人は、“変人”ですよね。だってTPSは、「どんどん異常を顕在化しなさい。その異常が分かったらすぐに直しなさい」と訴えてきますから(笑)。
TPSを自分の価値観として持った人は、世間一般的には“変人”。普通は自分がやってきた物事をいきなり変えることには抵抗があり、変えるなら、異常が出て来ない楽な方に変えたくなるものです。
でも、“変人”がたくさんいるから、トヨタ自動車はコンペティティブになるのです。しかもこういうことは一朝一夕ではできません。
今回の自主研に参加したみなさんは、そういう意味では“変人”になりました。この小集団が新たな“変人”をもっと増やしていくようになれば、トヨタの体質が強くなっていくでしょうね。
ここで言う“変人”とは、「変化を好む人」、「変化に適応できる人」のことだ。
尾上本部長は、改善が改善を呼ぶ好循環が生まれていくという。
尾上本部長
やりだしたら止まらないと思います。
(TPSを確立した)大野耐一さんの言葉で、「かくすればかくなるものとわかりなば、やむにやまれぬ改善魂」という言葉があるのですが、一度改善をやり出したら、もう改善は止まらない。自分が今日やった改善を次の日に見て、こんなぬるい改善をしたのかと腹が立つぐらいでやっと一人前だと。
改善をすると、さらに改善したくなる。そしてまた次につながる。そういうやむにやまれぬ改善魂が、製造現場だけでなく、事技系部門でも育てば、トヨタは本当に強い会社になるのではないかと思います。今回発表した3つの部門すべてが、すでに次の改善に取り組んでいると話していた。発表内容は、どれも大変な苦労を想像させるものばかりだった。「誰かの仕事を楽にする」のは簡単ではない。
しかし、この取り組みが広がれば、今度は自分がその「誰か」になるかもしれない。最後はみんなが「誰か」になる。これこそ、トヨタが目指す「幸せの量産」ではないか。生産現場から非生産現場へと広がり始めたTPSが、トヨタを強くする可能性を大いに感じた。
後日、実際にTPS自主研に取り組んだクルマ開発センターの改善現場を直撃した。その模様については別の記事で紹介する。
(編集・庄司 真美)