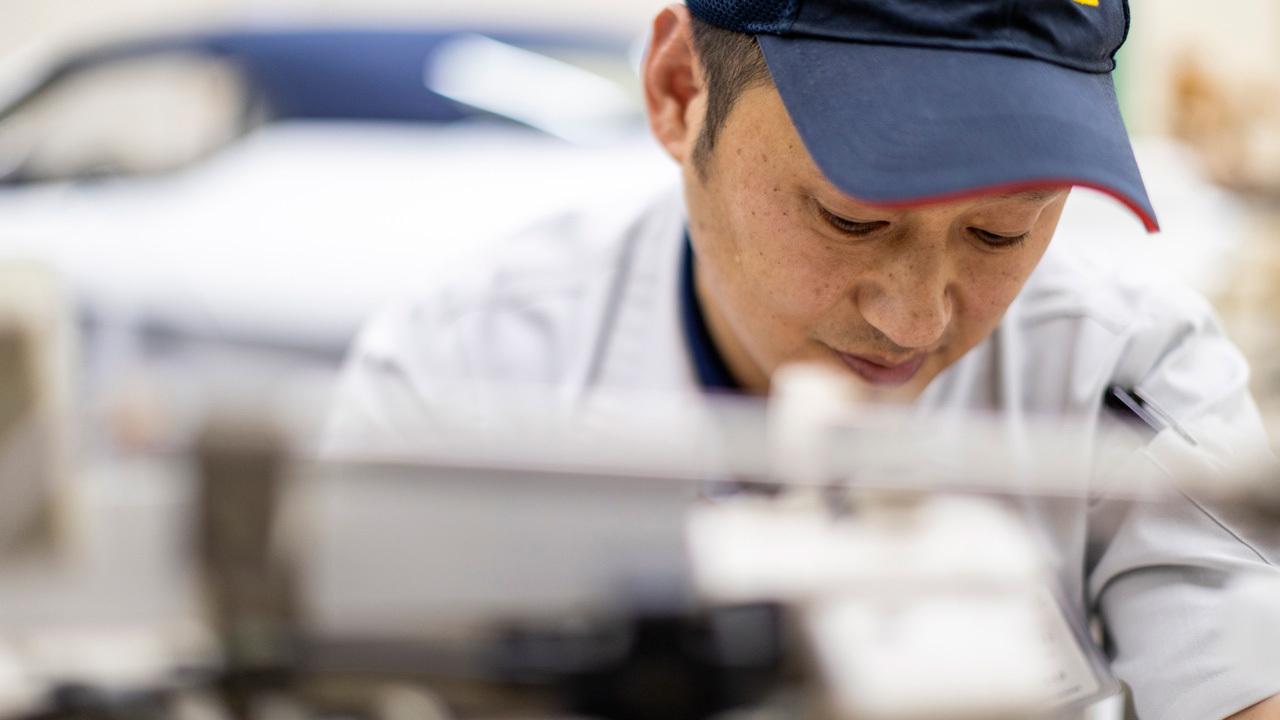
自動車業界を匠の技で支える「職人」特集。第8回は独自の技能で"質感"を徹底的に追求する「インテリア(内装)の匠」に話を聞く
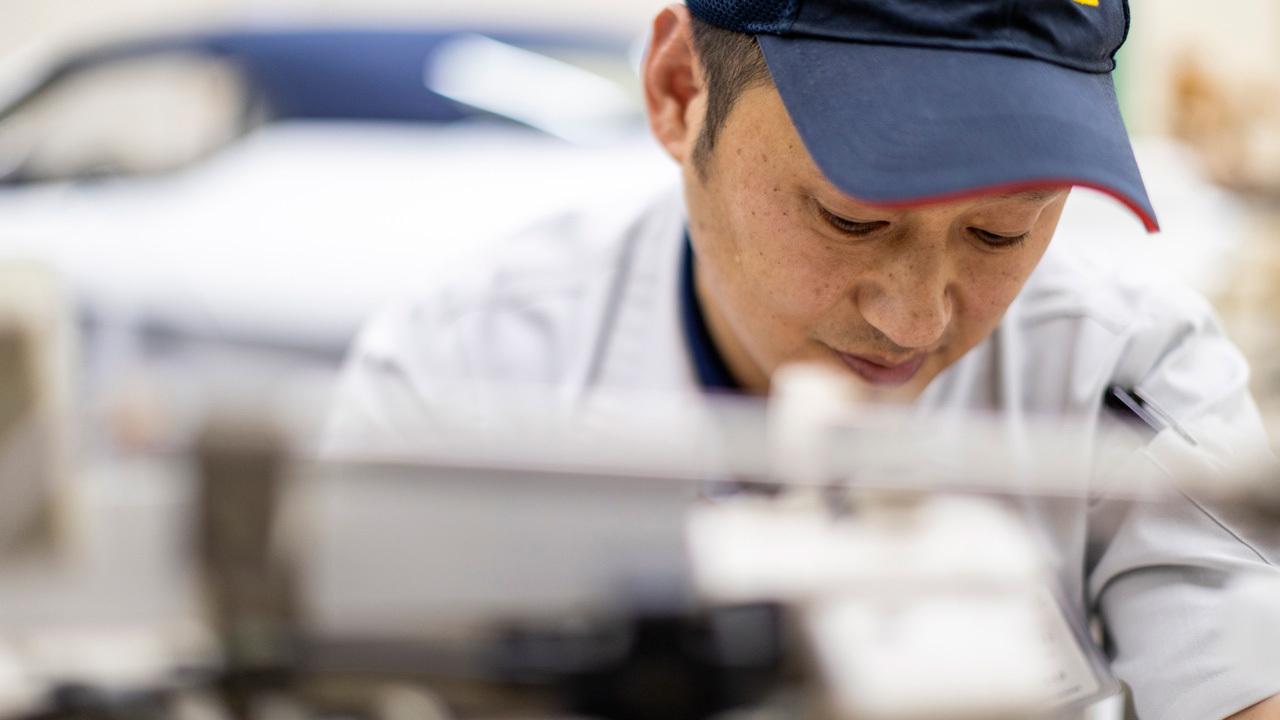
3DプリンターやAIをはじめとするテクノロジーの進化に注目が集まる現代。だが、クルマづくりの現場では今もなお多数の「手仕事」が生かされている。
トヨタイムズでは、自動車業界を匠の技能で支える「職人」にスポットライトを当て、日本の「モノづくり」の真髄に迫る「日本のクルマづくりを支える職人たち」を特集する。
今回は「インテリア(内装)の匠」、マルチモデラー山下真五 (やました・しんご)の後編をお送りする。
第8回 デザイナーのイメージをリアルに具現化する「インテリアの匠」山下真五
トヨタ自動車 クルマ開発センター デザイン統括部内装モデルクリエイト課 シニアエキスパート
素材選びから縫製まで自分の手で
マルチモデラー、山下真五の仕事場は、愛知県豊田市、トヨタ自動車社内のデザインスタジオ。そこには前編でも紹介した、レクサス「 LC コンバーチブル」のインテリアの原寸大モックアップが置かれていた。もし目隠しをして運転席に座らされ、目隠しを取ったら、本物のクルマだと思うはず。まさに実車そのままの完璧な仕上がりだ。
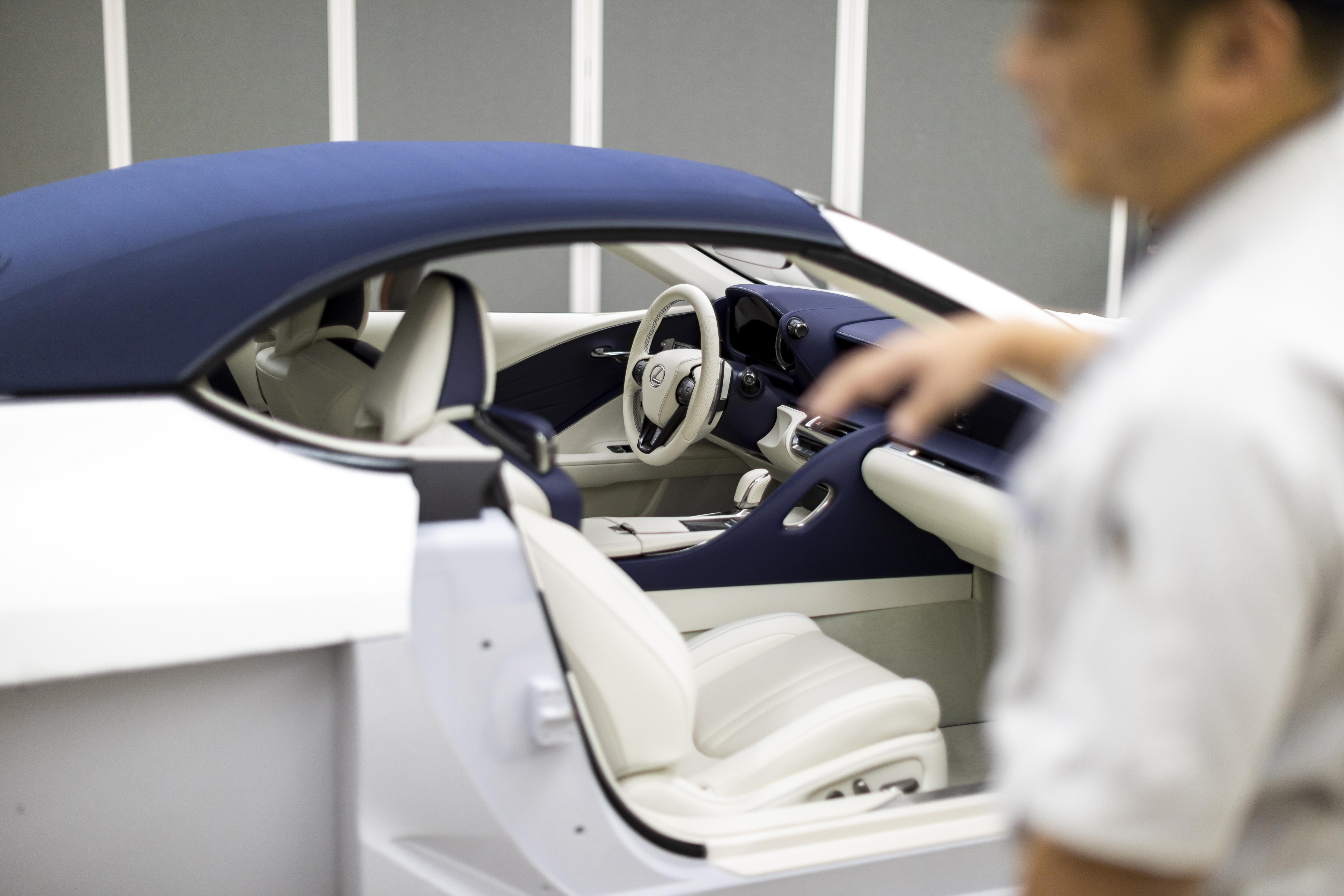
そのモデルの奥に、縫製用の工業用ミシンと作業台が置かれている。ここが山下の仕事場。まずは革巻きステアリングの、革巻きの作業を実演してくれた。この製作にも、素材から技能まで徹底的に追求する山下が、仕事で培った独自の工夫やノウハウが注ぎ込まれている。
普通なら皮革縫製作業などは、専門メーカーや専門の革職人に依頼するもの。だが山下は、13年ほど前、「プラド」のインテリアデザインを担当した際、デザイナーが求める「本物の革巻きの、しかも握り心地の良いステアリング」というデザインが提示されたときから、自身でこの課題に取り組んだ。「まさか自動車メーカーに入った自分がやるとは思わなかった」握り心地の良いカタチの造形から革の素材選びや高度な縫製作業に取り組んだのだ。
「プラドでは、使える合成皮革の中から、どの素材をどのように使えば『本革が巻かれている』ように見える、しかも『握り心地の良いステアリング』を実現できるのか、試行錯誤を重ねました」
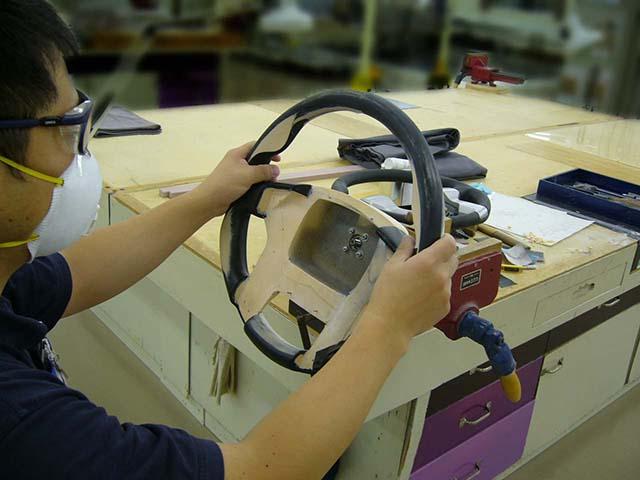
また10年ほど前、「ハリアー」では、「厚い革の硬い表情のデザイン」というテーマで質感モデルを製作する課題には、山下が持つ革の知識や製法技術を担当者に伝授し一緒になってつくり上げた。
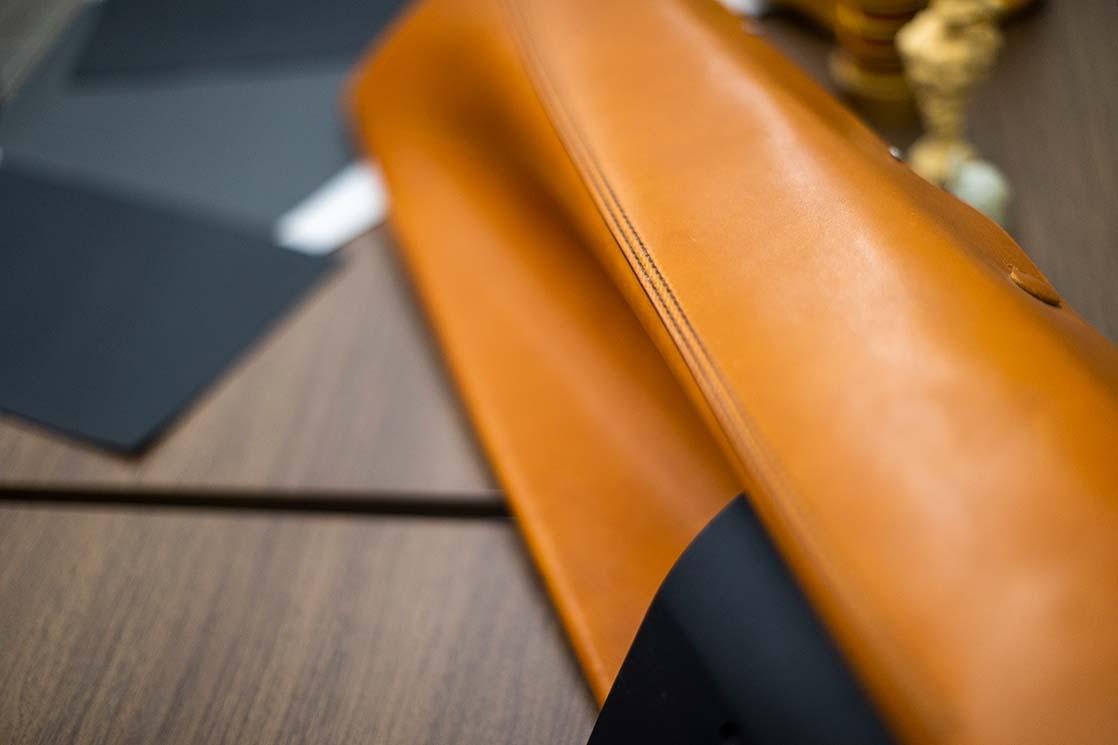
一部のモデルでは本物の革が使われているものもあるが、生産台数が多いトヨタのクルマづくりでは、コストのみならず耐久性、品質管理の観点からもPVCレザーなどの合成皮革素材を採用することになる。合成皮革といっても、さまざまな質感や機能を備えたさまざまなものがあり、必ずしも本革が優れているわけではない。
ステアリングのパーツに選びぬいた合成皮革を巻きつけて手縫いで縫製する。この作業を実演しながら、山下は当時の記憶を語ってくれた。その手つきはまるでベテランの革職人そのもの。ステッチの幅や長さを均等に保ちながら正確に縫い合わせていく。
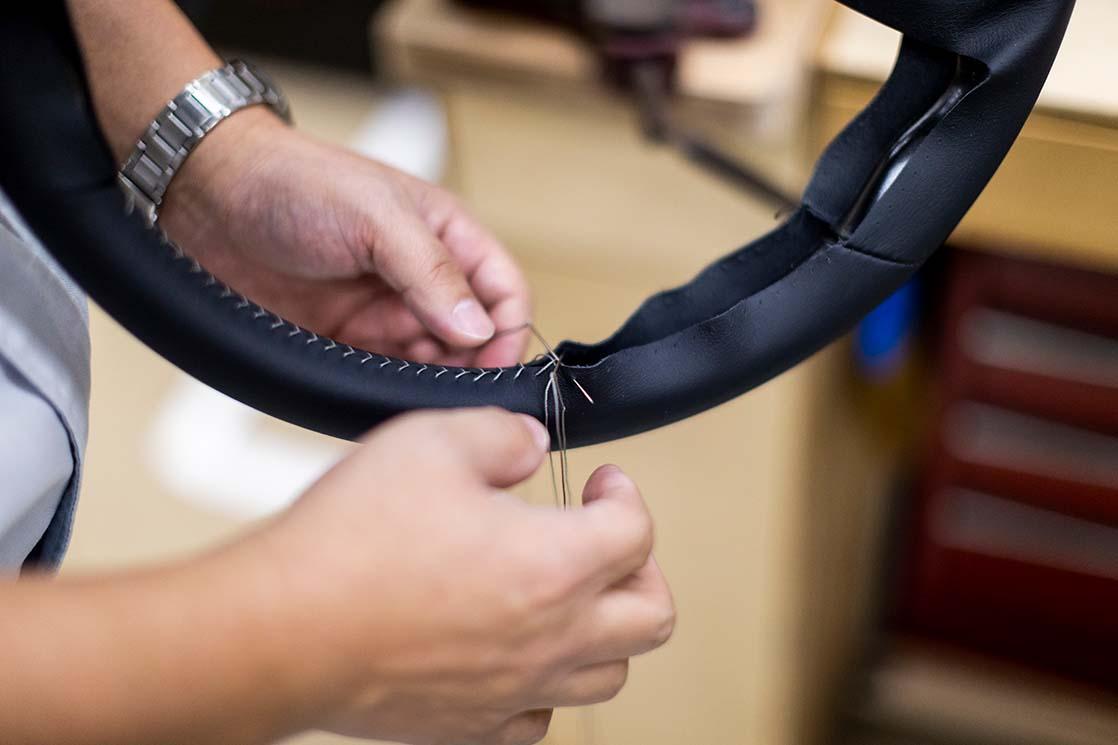
「最終的に本革らしく見せる方法としてたどり着いたのは、ステアリング断面のアール(曲率)を工夫することでした」
クルマのステアリングは、鉄やアルミニウムやマグネシウムなど必要な剛性と強度を確保する芯金の周りを樹脂や革などの軟質素材で巻き、一体化した構造になっている。また、クルマの安全性に直接関わる操縦系の部品だけに、法令で定められた仕様もある。
当初、山下は加工性の良いクレイを使って考えた断面形状を実現しようと試みたという。
「でもクレイだと柔らかい感触が残りしっかりと握ぎれないんですよね。手の感触って繊細なんですよ。そこで樹脂を自分で削って研究し、思い描いた断面形状を実現できました」
縫い方の違いでも、見た目の印象は大きく変わる。山下はステアリングを握ったときの手当たりに違和感が無く機能性にも優れた美しいステッチのラインを提案するよう心掛けているという。
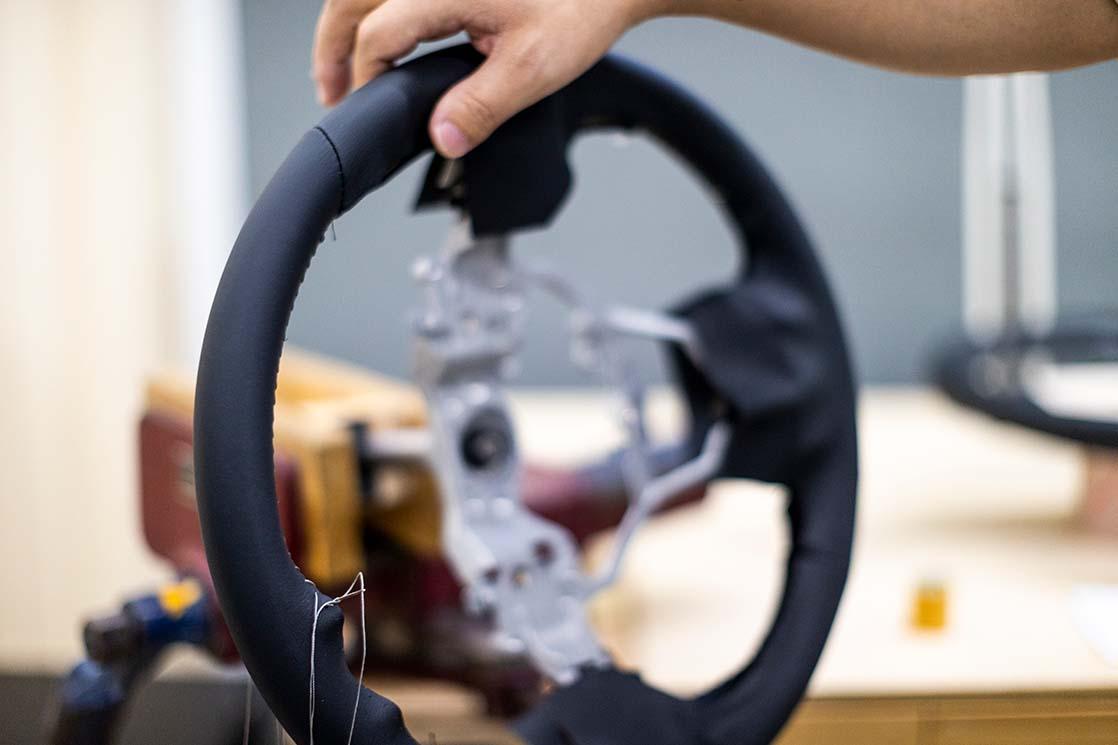
質感やエッジまでデザイナーの理想を追求
シートはシートメーカーが担当するが、それ以外の内装、インストルメントパネルやメータークラスター、センターコンソール、ドアトリムなど、山下はリーダーとなり高い質感で仕立てている。
高級車の場合は、革張りされた内装も多い。この革張りの内装でベースとなる樹脂の上に革素材を張り込む作業は、生産車の場合は一部を機械で行うが、試作の場合にはもちろん全て手作業。形状が複雑だと、それだけ作業は難しくなる。
「作業にデザイナー、設計部門などのメンバーが立ち会うこともあります。デザイナーからは『ここをもっとカチッとしたい』とか『もっとシュッとした感じにしたい』などと言われたりします。デザイナー一人ひとりで表現が違うので、その人がどんな人で、何を望んでいるのか、どうすれば希望に近づけることができるかを考えます」
革張りの内装では、目指すデザインに合わせてベースの形状や、革素材の下に入れるスポンジなどのクッション材の量、さらには革素材の巻き方や張り込み方を工夫する。何枚かに別れた革素材を縫製してつないだりもする。
「素材で本革らしく見えるか見えないかも大きく変わりますし、革素材の巻き方や中に入れるクッション材のスポンジの入れ方や量で、内装のエッジ(角)の部分の形状、見た目の印象も大きく変わります。厚い素材を使ったから厚く見えるわけではありません」
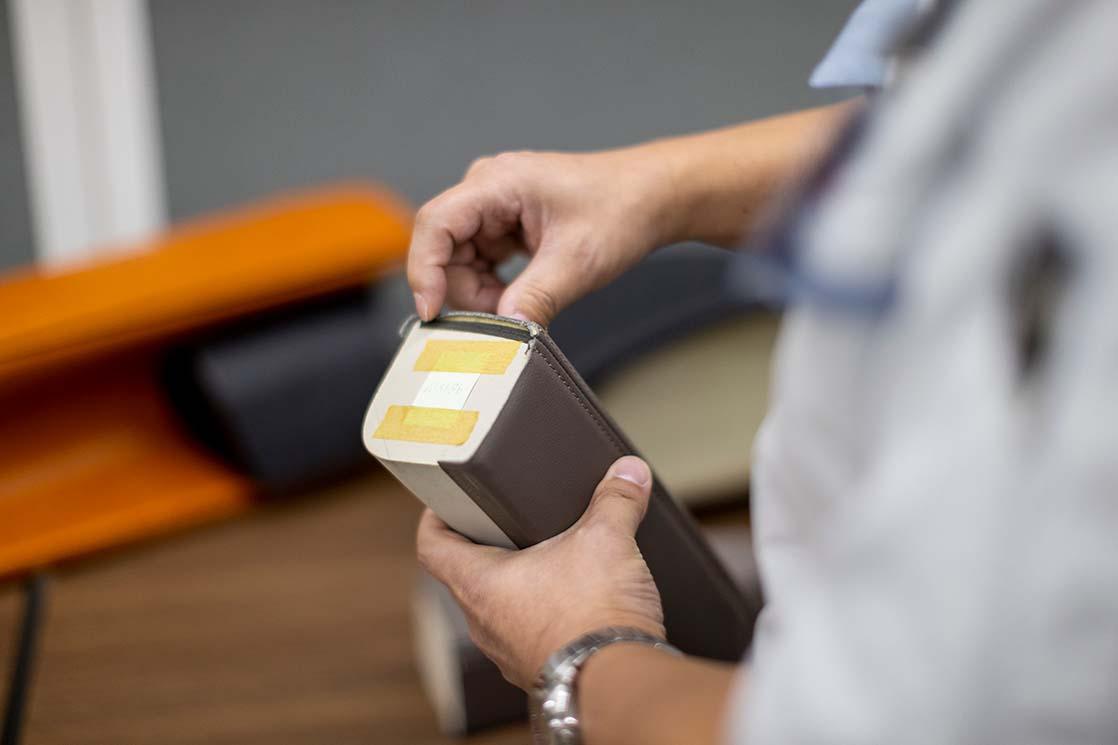
デザイナーからよく言われるリクエストの一つが、「メータークラスターやコンソールのエッジをもっとハードでシャープな印象にしたい」ということ。だが安全上の理由で、内装のエッジにはアール(曲面)を付けることが法律で決められている。だが山下は、革素材の厚さ、中に入れるクッション材の量や入れ方を工夫することで、アールを付けながら「ハードでシャープ」な見た目を実現する独自のノウハウを編み出した。
山下は何枚もの革素材を工業用のミシンで縫い合わせる作業も実演してくれた。このミシンによる縫製の技術も、もちろん自分で習得したもの。布よりずっと硬い革素材を正確に縫い合わせることはとても難しい。このステッチをデザイン意匠面の表現に使いたい、というデザイナーもいる。
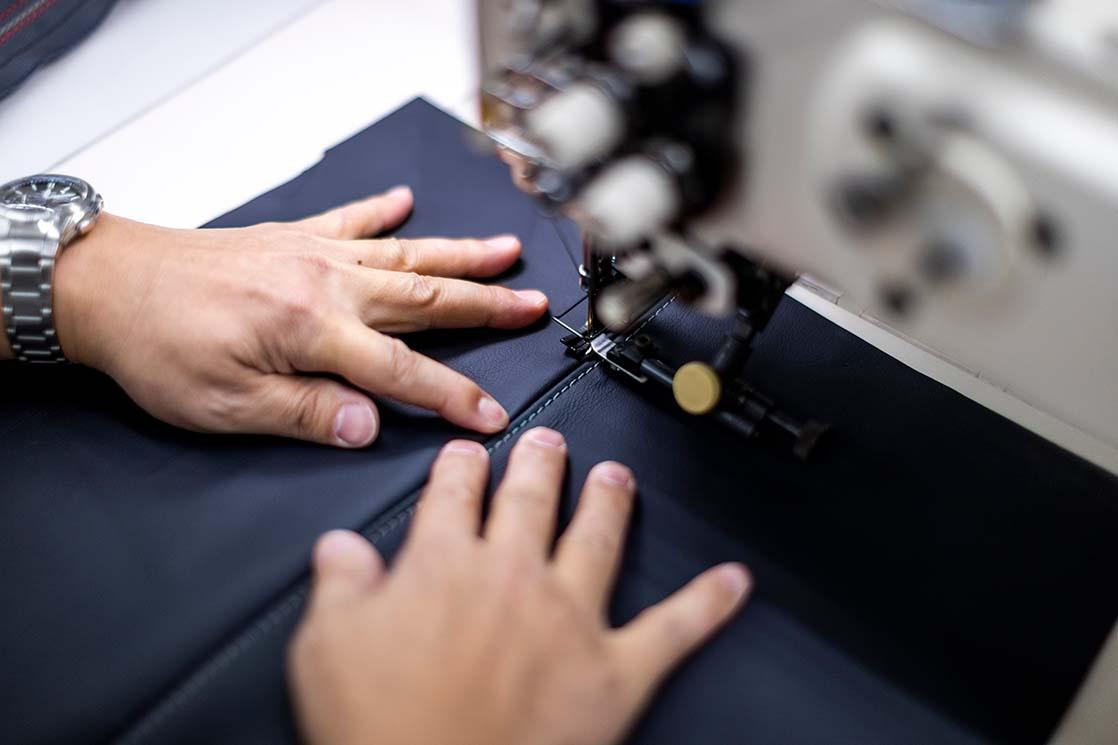
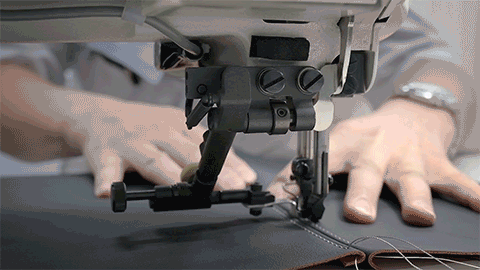
自ら完璧に美しく仕上げた原寸大のモックアップ。このインテリアデザインを生産車でどのように実現するのか。この方法を生産現場の担当者とともに考えることもある。手作業で完成させたデザインやその工程をリファインし、機械を使って効率良く低コストで実現しなければならない。
デジタル技術を駆使した仕事と手仕事を行き来できる「マルチモデラー」の山下の知識や経験、独自のノウハウや技能が、今ほど求められている時はない。
唯一無二の技能やノウハウを未来につなぐ
山下が今、取り組んでいる最大の課題。それは山下のような、デジタルと手仕事のどちらも理解し身に付けることができる後進の育成だ。
トヨタではいま、新しいモノづくり、クルマづくりへの挑戦が続いている。試作車と生産車の間にあったギャップをできるだけ少なくする、「自分たちがつくったものが、お客様の手に届くようにしよう」という挑戦だ。
しかも新車の開発期間はどんどん短くなっている。トヨタはこの課題を、デジタル技術を使い、情報やノウハウを共有すること、そして各部門のコミュニケーションを濃密にすることで克服しようとしている。
だが、すべてをデジタル化すれば解決できるわけではない。インテリアデザインは最終的に、山下のようなマルチモデラーの手仕事なしには完成しない。リアルなモデルでなければ最終評価はできない。
特に手仕事の技能継承がとても難しい、と山下は語る。
「今の子たちは最初からデジタルで仕事をしています。つまり手仕事をする機会が昔よりも激減しているんです。だから手仕事の技能がなかなか深化しない」
革を手仕事で張り込む作業では、どのように革を伸ばせば上手にできるのかを、常に考えながら作業をするという。
「毎回、張り込む対象の形状が違うので、どういうふうに張り込んでいけば上手に張れるかを考えながら作業します。ただ、このやり方はマニュアル化できるものではないんです。だからなかなか伝えられない。失敗するのが一番勉強になるのですが、今は失敗する時間も与えにくい状況です」
納期が迫っている作業は、どうしても上手なベテランにやってもらうことになる。これでは若手への技能継承は進まない。
「デジタル技術はうまく使えばいい。デジタルも日々進化していて、昔は布を使って型取りするしかなかった複雑な立体も、最近は3D-CADで展開図までつくれるようになってきました。これからは、木型のような道具を使う伝統技能と最先端のデジタル技術を融合させて、最適なモノづくりを行うこと。これが大切になるでしょう」
今後はカーボンニュートラル性に考慮したリサイクル系の素材を使う機会も確実に増えてくるだろう。こうした素材をどう使うかも自分にとって課題だと山下はいう。
「マルチモデラーにはこれから先、さまざまな技能を身に付けることはもちろんのこと、多彩な創造力、構築力、審美眼が求められることになります。ただ審美眼の磨き方は人それぞれ。こればかりは伝承できないですね」
「他の人には無理でも彼ならできる」と頼りにされる、社内でも唯一無二のマルチモデラー、山下真五。より魅力的なクルマづくりに、後継者育成という新たな、しかも難しいテーマを加えて、山下の挑戦はさらに続く。
(文・渋谷 康人、写真・前田 晃)