
自動車業界を匠の技で支える「職人」特集。第2回は特許技術の開発にも携わった「鋳造の匠」に話を聞く

3DプリンターやAIをはじめとするテクノロジーの進化に注目が集まる時代だが、クルマづくりの現場では今もなおあまたの「手仕事」が生かされている。
トヨタイムズでは、自動車業界を匠の技能で支える「職人」にスポットライトを当て、日本の「モノづくり」の真髄に迫る特集「日本のクルマづくりを支える職人たち」をスタート。
今回は、「鋳造の匠」元木清秀(もとき きよひで)を取材した。
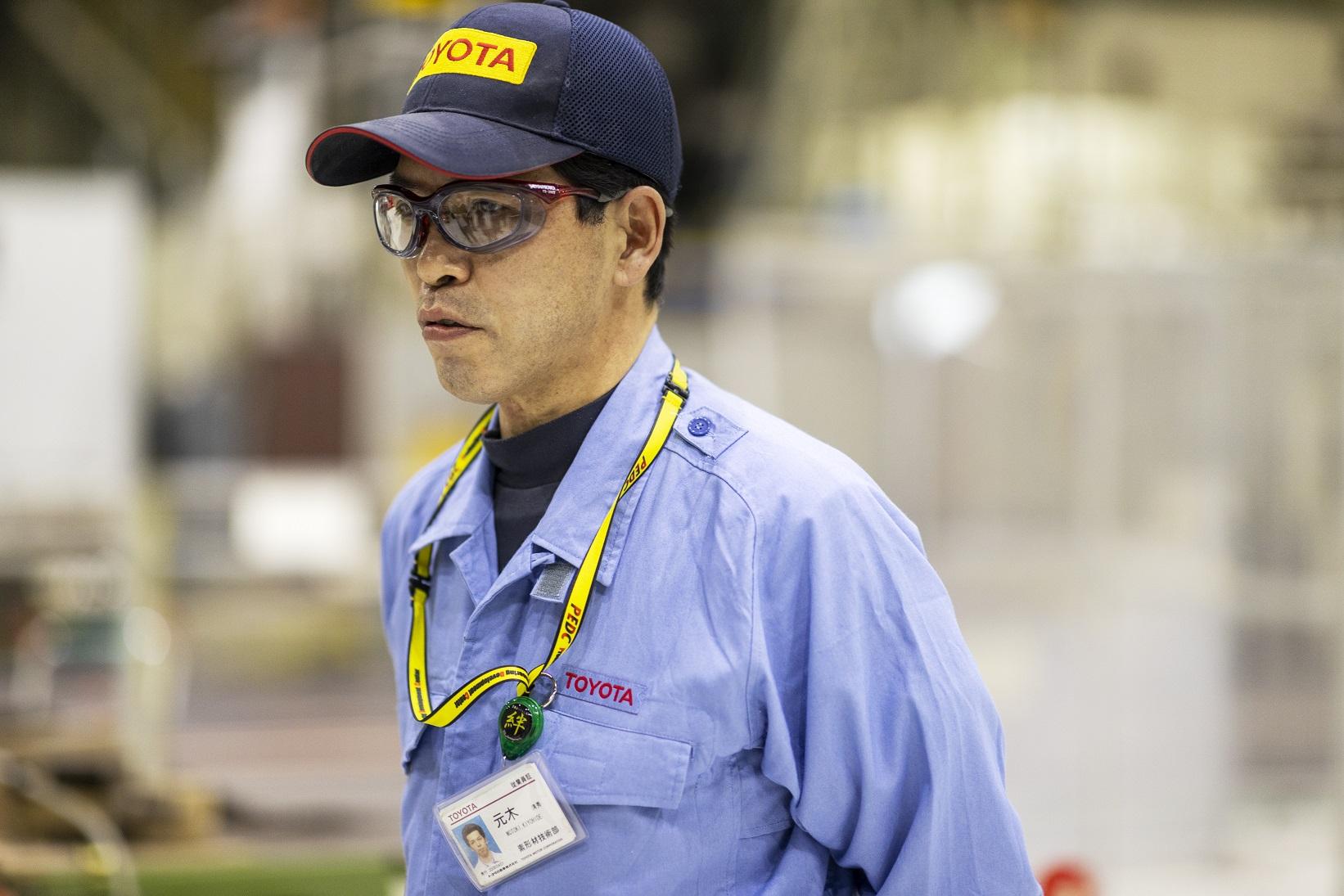
第2回 鋳造技術に魅せられた「鋳造の匠」 元木清秀
トヨタ自動車 明知(みょうち)工場 素形材(そけいざい)技術部 開発試作課 シニアエキスパート(SX)
トヨタを代表する鋳造職人
クルマには、鋳造(ちゅうぞう)で造られる部品が多い。
シリンダーブロックやシリンダーヘッドなどエンジンの主要部品。トランスアクスルケースやクラッチハウジングなど、エンジンからの駆動力をタイヤに伝える駆動系に用いられる部品。そして、アルミホイールやブレーキディスクローターなどの足回り部品。一部のボデー部品やハイブリッドカーのバッテリーケースなども鋳造で造られている。
トヨタの「良品廉価なモノづくり」、つまり高品質のクルマを低価格で提供するには、高度な鋳造技術が欠かせない。
鋳造とは5000年以上も前から使われてきた金属によるモノづくりの基本技術。その代表的な方法が砂型鋳造法だ。
砂を固めて作った鋳型(いがた)の空洞部分に高温で熱し溶解させた金属を流し込み、金属が冷えて固まったあとに鋳型を壊すと、中から空洞部分と同形の完成品が姿を現す。
金属を望み通りの形に成形できる加工方法で、大型で複雑な形状のものも造れる。たとえば、奈良県の東大寺の御本尊、台座を含めると高さ約18メートルという世界最大の金銅仏・盧遮那仏(るしゃなぶつ)も、台座の部分から頭頂部まで全部で8段、8回に分けて鋳造されたパーツで構成されている。
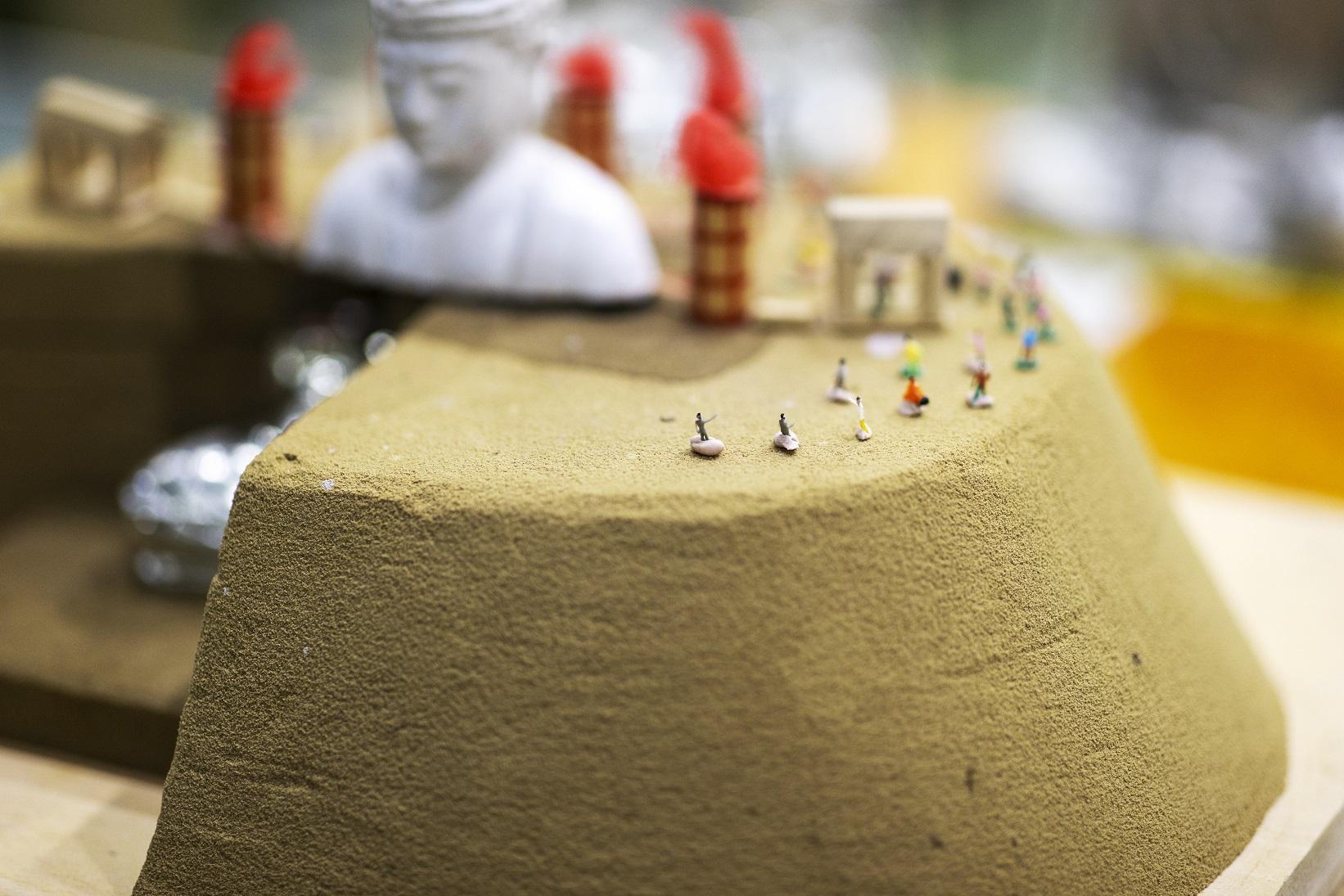
トヨタにはこの「鋳造の匠」がいる。愛知県みよし市明知町にある明知工場で試作部品の鋳造を担当。また、鋳造で造られる量産部品に不具合が生じた際のアドバイザーを務め、さらに若手社員に鋳造技術の基本を教えるなど人材育成にも携わる元木清秀だ。
1962年6月27日生まれの58歳。1981年3月1日にトヨタ自動車に入社してから鋳造ひと筋に歩んできた。
元木は2020年、日本の素形材(素材に熱や力を加えて造られた部品や部材)造りに関わる技術の研究開発振興を担う一般財団法人素形材センターから、優れた技術と技能を持つ鋳造技術者の模範として「素形材産業優良従業員表彰」を受けた。
さらに鋳造技術の進化、発展に大きく貢献したことが高く評価され、表彰者の中からただ1人選出される「久保田長太郎賞」も受賞している。
ところで、この久保田長太郎賞の久保田長太郎(1882〜1964)とは、トヨタ自動車の鋳造部門立ち上げに尽力した伝説の鋳造技術者。豊田佐吉に見込まれ豊田織機に入社し、鋳造部門の責任者を務めた後、鋳造機械の開発・製造に取り組み、1927年に国産初の生型(砂型)造形機を開発。鋳物の世界では「鋳物の神様」と言われる人物だ。
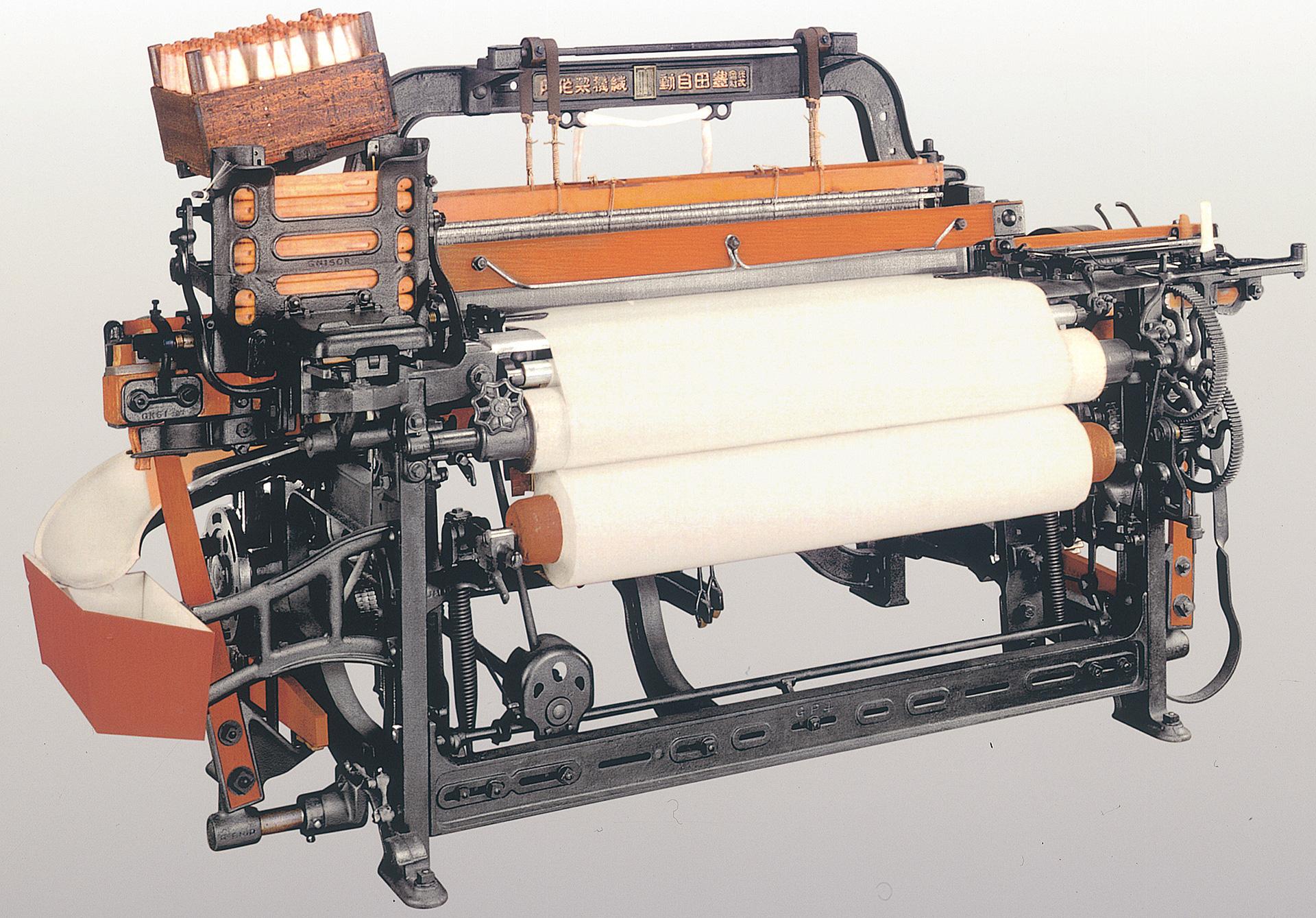
現在、トヨタの量産エンジンの鋳造パーツは、自動の砂型造型機や鋳造機(ダイカストや低圧鋳造など)を用いて生産されている。
しかし元木はこうした量産ラインではなく、少量生産で究極の工作精度と品質が求められる試作部門で、F1エンジンなどの部品を筆頭に、さまざまな試作部品の鋳造を担当してきた。
「鋳造を学び始めたのはトヨタ工業学園の2年生のとき。実は、入社時には量産ラインへの配属を希望しました。でも適正検査でハネられて、試作部門に配属されました。当時はそこに、町工場で経験を積んで入社したスゴ腕の鋳造職人さんが数多くいて、自分はその人たちの中で育ちました」
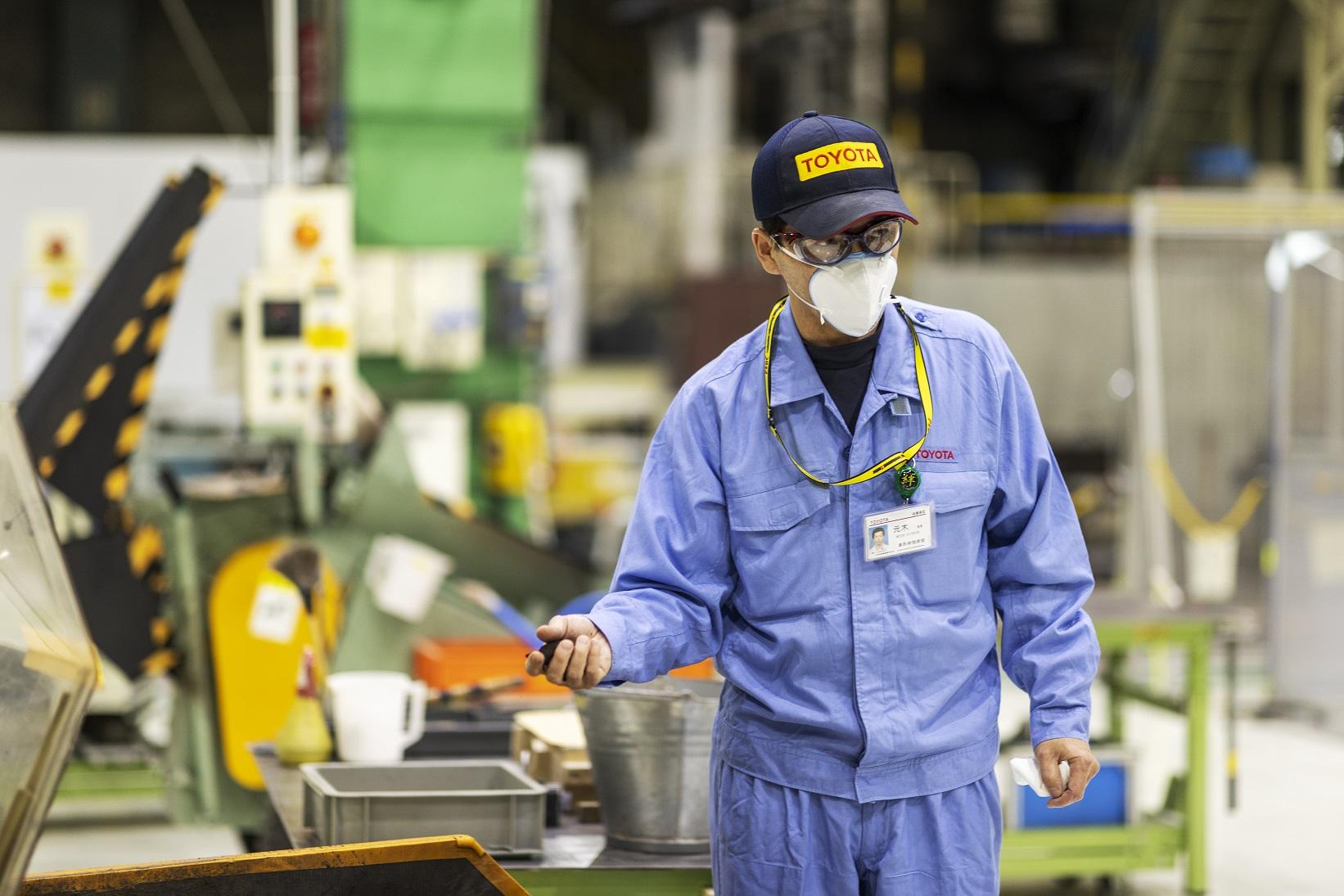
希望の部署ではなかったと元木は笑う。だが、周囲は当時から元木の「鋳造の匠」になる素質を見抜いていたのだろう。
先輩職人たちの技能に感銘を受けた元木は、鋳造に関するあらゆる技能と知識を学び、名実ともにトヨタを代表する鋳造技術者となった。今も「これで良い」と思うことはないし、決定的な自信を持って仕事をしているわけではないと元木は言う。
「鋳造の仕事は、毎日が試行錯誤の連続で、毎日が勉強です。鋳造という技術は奥が深く、人の技能や知識、経験に委ねられる部分が多いので、すぐに機械には置き換えられない。金属加工の技術の中でも、いちばん置き換えにくいものかもしれません」
モータースポーツエンジンへの挑戦
「鋳造の匠」である元木の仕事として見逃せないのが、トヨタF1プロジェクト(2002〜2009)をはじめとするモータースポーツ用エンジンのシリンダーヘッドやシリンダーブロックの製造だ。
F1マシンには、その時代の最高技術を結集したエンジンが搭載されている。当時、元木が手掛けたエンジンの最高回転数は毎分約1万8000~1万9000回転。市販エンジンの3倍以上という超高速エンジンで、700馬力以上のパワーを発揮した。
シリンダーヘッドとシリンダーブロックはエンジンの本体を構成し、出力や特性、耐久性を決める最重要部品。しかも強大なパワーが求められるので、内部の金属構造が均一でないと弱い部分から壊れてしまう。
また効率良く燃料を燃焼させ超高速でピストンをスムーズに動かすために、シリンダーヘッドやシリンダー内部をミクロン単位まで正確な寸法に仕上げることで、燃焼ガスを密閉すると同時に摩擦を極限まで減らすことが大切だ。
また、回転数が一般車のエンジンの約3倍のため、燃焼時に発生する熱も約3倍になる。だから、シリンダーブロック内部に冷却水を流すための充分な空間(ウォータージャケット)を設け冷却しないと壊れてしまう。
鋳造はこのすべての課題を高い次元で解決できる唯一無二の製造方法なのだ。しかも「レースに勝つ」ためには、軽さと強さを究極のレベルで両立させなければならない。
そのため、元木たちは鋳造方法からすべてを見直してヘッドとブロックの製造に取り組んだ。この過程で開発された鋳造方法は、後にトヨタの特許技術となっている。
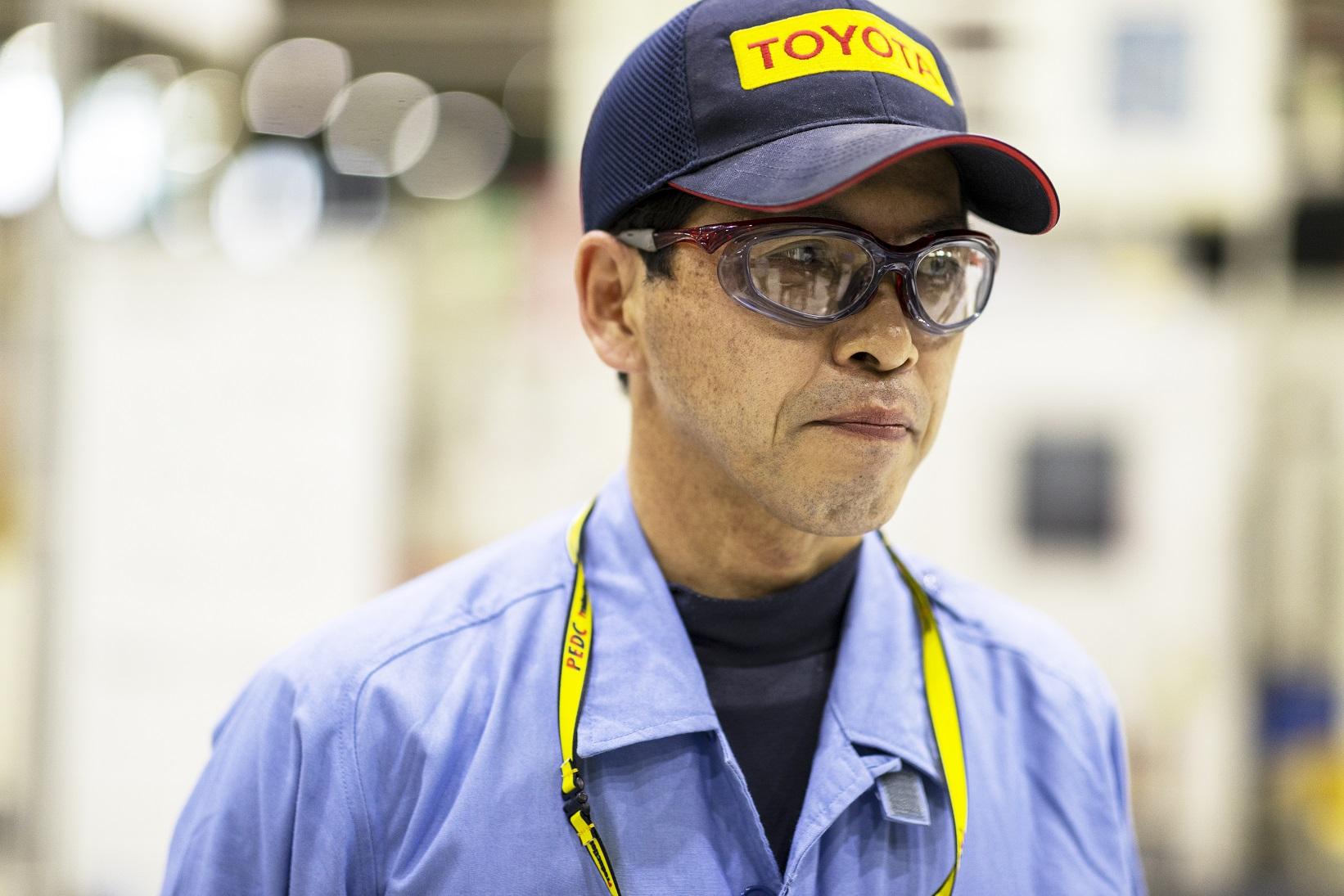
さらにCTスキャンを使って金属の内部に“す”(鋳造過程で凝固収縮によりできてしまう微少な空洞)がないことを、ファイバースコープでウォータージャケット内に鋳造時の砂が一粒もないことを確認するなど、品質管理を徹底。その結果、良品率100%、つまり不良品ゼロを達成してチームから揺るぎない信頼を獲得する。
こうしたレースプロジェクトを通して元木たちが開発した鋳造技術やノウハウはインディカーなどのレースエンジンはもちろん、市販車のエンジン製造にもフィードバックされた。トヨタの中でレース活動から得られた技術は今も生き続け、進化と発展を続けているのだ。
鋳造の“源流の技能”を未来へ
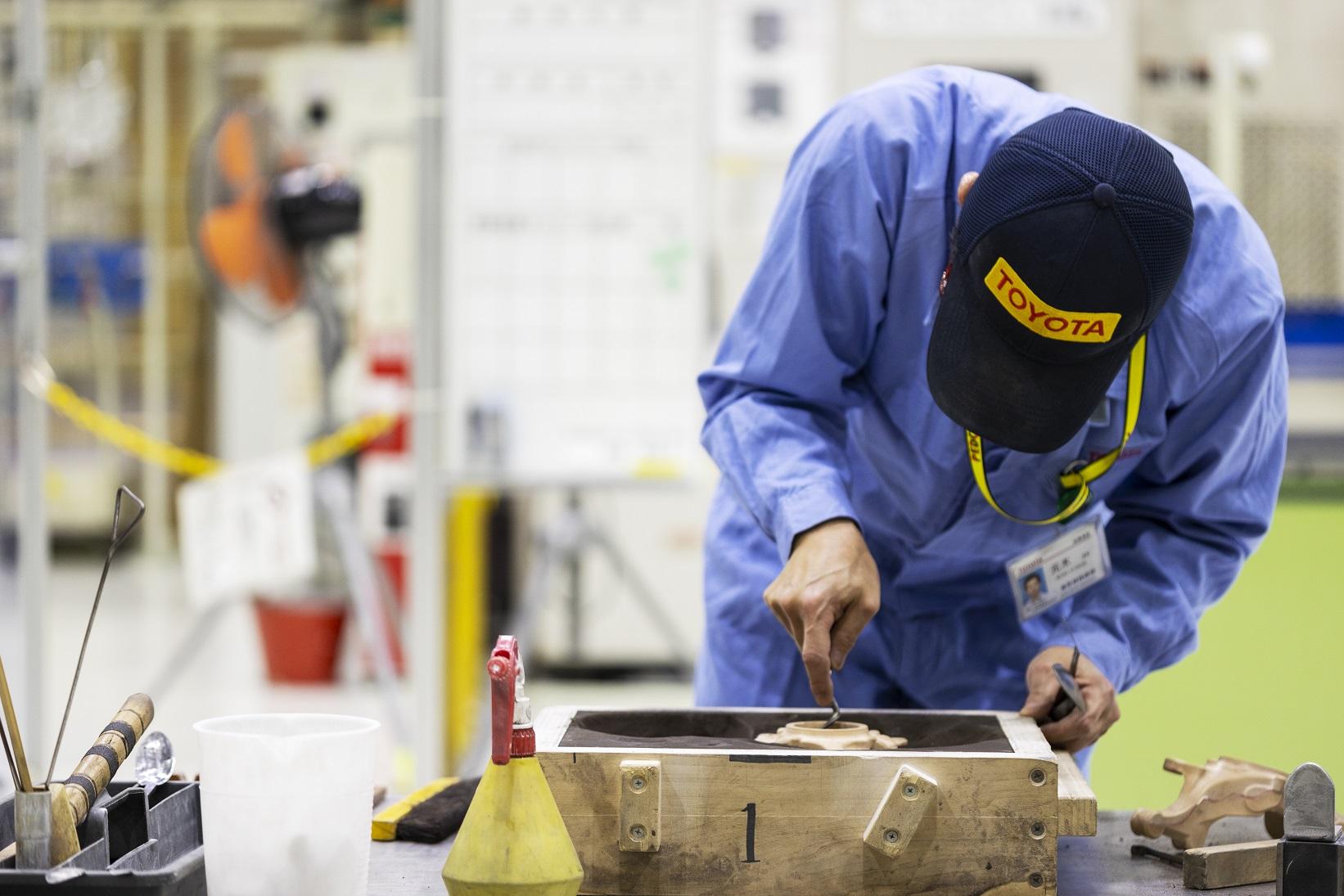

元木は今、トヨタ自動車の未来を担う若手社員に鋳造の「源流技術」を教えている。
鋳造の基本は、製造すべき金属パーツと同形の木型と、砂を材料とした鋳型(砂型)を使った「砂型鋳造」。
元木は「手込め鋳造」と呼ばれる、若手社員が学ぶ手作業による砂型鋳造の一部を実演してくれた。作業に取りかかると、元木の表情は一変。五感のすべてを動員して作業に没頭する。
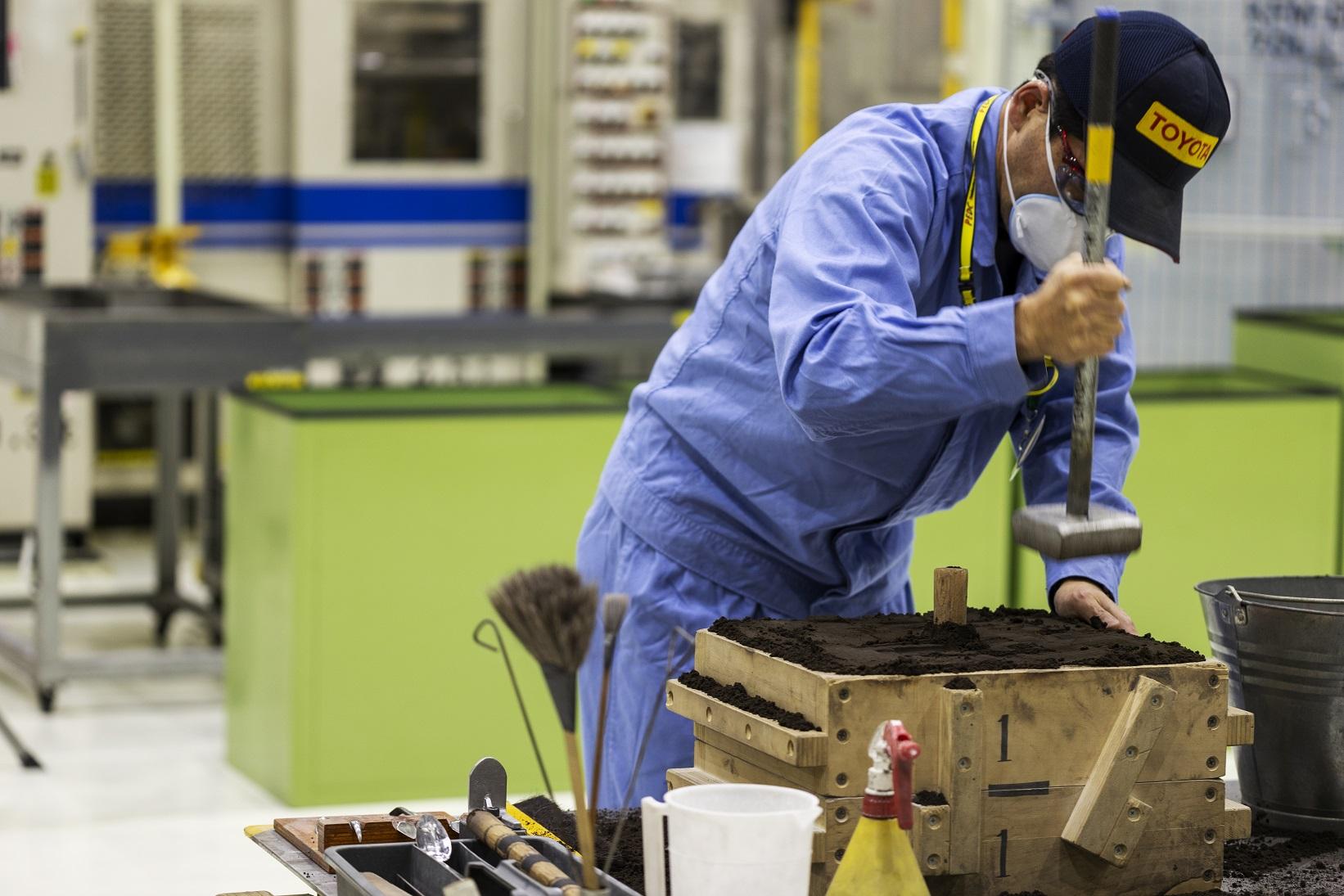
砂型による鋳造は、砂が詰められた上下2つの枠の中に木型を埋め、木型を取り除くとできる空間に、溶けた金属(溶湯)を流し込むことで行う。
まず砂が入った下枠の中に木型を埋めて砂を固め、さらに溶湯を砂型の内部に通す空洞をつくるために、砂の中に湯口棒と呼ばれる棒を立てる。
続いて上の枠を重ね、そこにも砂をしっかりと詰めたら湯口棒を抜き、上下の枠を重ねた状態で90度に立ててから2つの枠を離す。
そして下の枠から木型を取り除き、砂型内部にできた空間に溶湯が流れる道(湯道)を、ヘラで砂を削って丁寧に作り込んだら、上下の枠を再び合わせる。
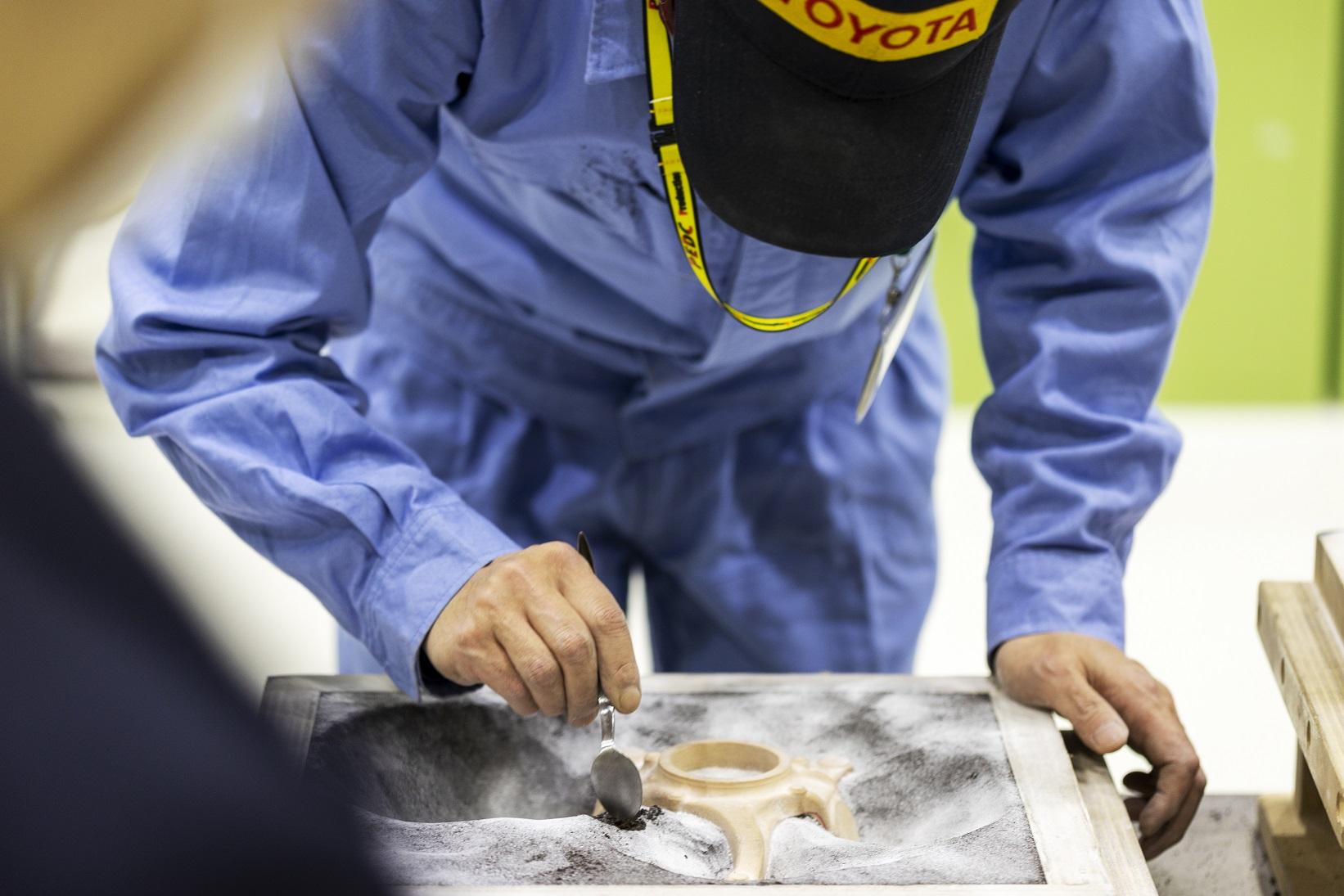
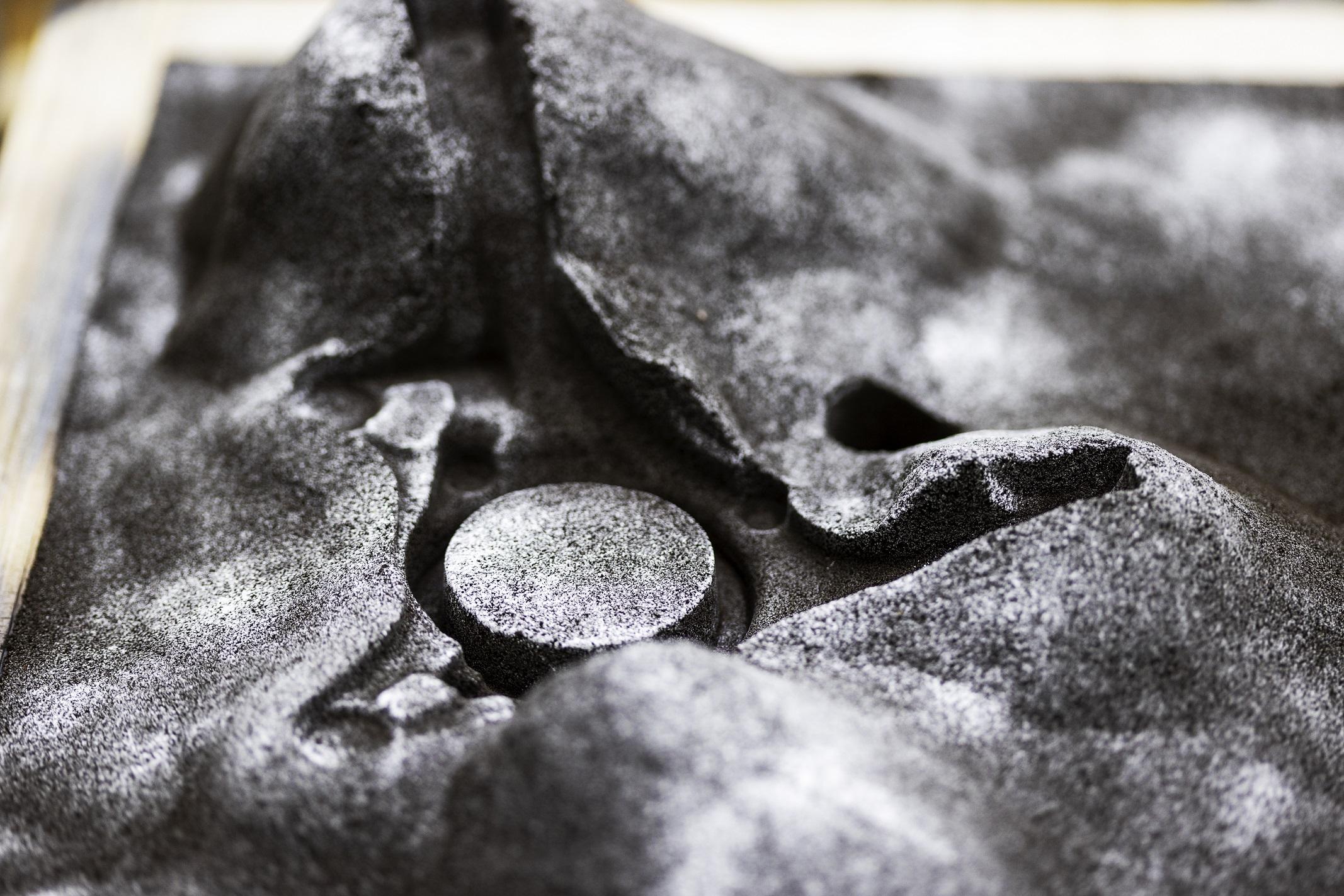
こうして完成した砂型に、ひしゃくで汲んだ溶湯を湯口から流し込み、金属が固まるのを待って砂型を壊すと、木型と同形の金属部品が姿を現す。
砂型の中でアルミ合金が固まったのを見計らい、元木が木枠を外して砂型を壊すと、その中から鋳造部品が現れた。すると、作業中は厳しかった元木の顔が一転、笑顔に変わった。


“鋳造の面白さ”を伝えたい
「鋳造の匠」元木にとって、鋳造は単なる仕事ではない。これほど面白くて楽しいモノづくりの方法はないと元木は言う。
「鋳造の魅力は、無から有を、金属素材から一気に形あるものを造れること。鋳型を取り除き、出来上がったモノが現れる。このときのワクワク感が何よりもうれしい。しかも、ほかの方法と違い、鋳造はやり直しが可能です。鋳型はすぐに作り直せるし、金属もまた溶かせばいい。失敗してもすぐに再チャレンジできる。この鋳造によるモノづくりの楽しさを、技能とともに若い人たちに伝えたい」
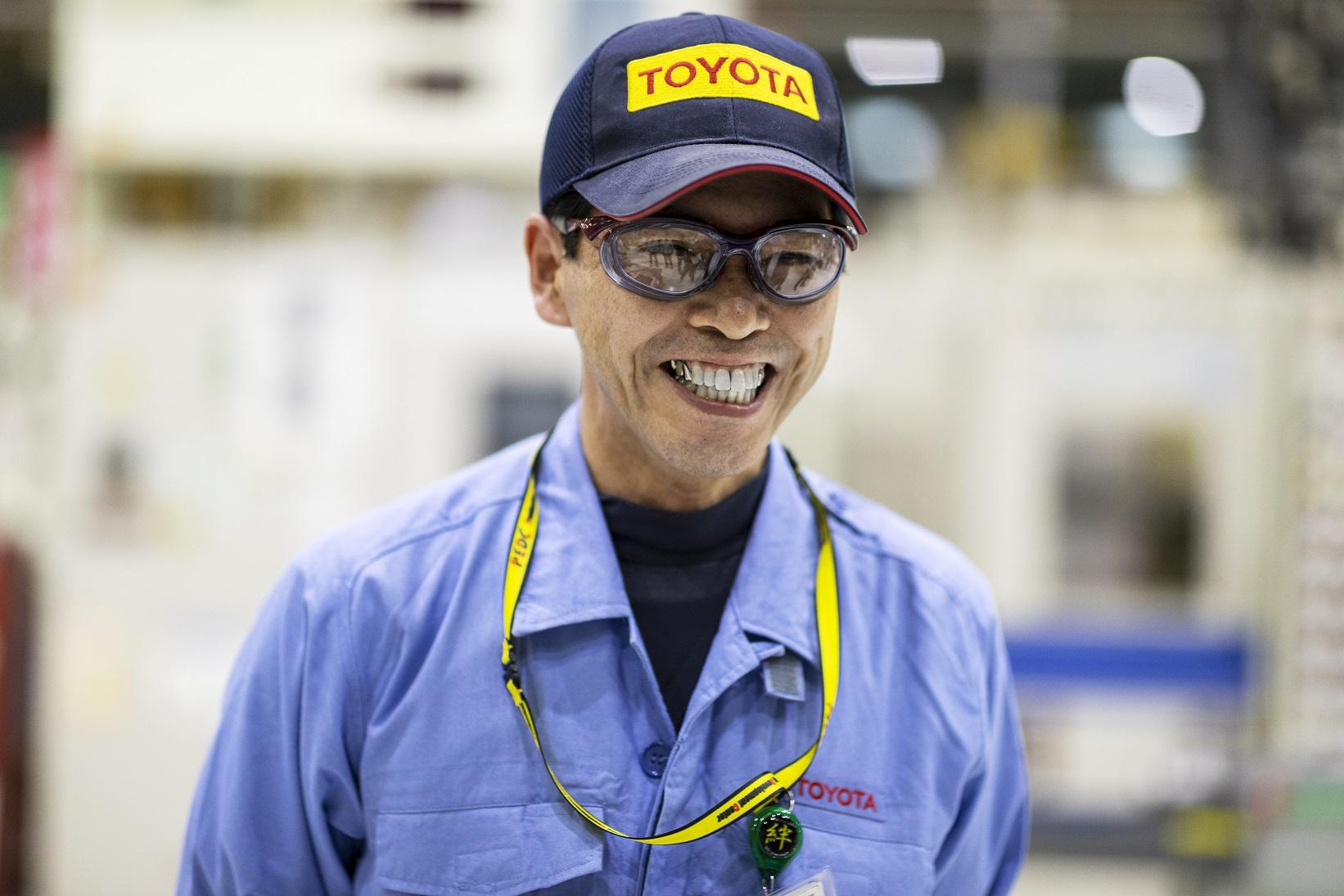
鋳造作業では、溶湯が鋳型の空洞部分に行き渡るように、しかも金属が固まるときに“す”ができないように、鋳型を企画・設計することが大切だ。これを「鋳造方案」という。
他の部門と同様、いまトヨタの鋳造によるモノづくりの主役は大型の自働機械だ。そして、その鋳造方案はコンピュータによるシミュレーションで作られている。だがそれでも、機械を操作する鋳造技術者には、数値化できない鋳造の“源流の技能”を身に付けることが不可欠だと元木は言う。
「溶けた金属がどのように振る舞うのか。どうすれば、溶けた金属を思い通りの場所に流すことができるのか。これを感覚で理解していなければ、機械で問題が起きたとき、解決することはできません。そのためにも、鋳造のすべての作業を自分の手と感覚を頼りに行う手込め鋳造の技術を習得することは大切なのです」
トヨタの「鋳造によるモノづくりの未来」は、若い社員たちが元木の「源流の技能」を継承できるかどうかにかかっている。そして元木はいま「手込め鋳造」の技術伝承を通じて、若い社員たちと未来を作っているのだ。
(文・渋谷 康人、写真・前田 晃)