
自動車業界を匠の技で支える「職人」特集。第5回はミクロン単位で理想的なボデー形状を追求する「プレス金型製作の匠」に話を聞く

3DプリンターやAIをはじめとするテクノロジーの進化に注目が集まる現代。だが、クルマづくりの現場では今もなお数多の「手仕事」が生かされている。
トヨタイムズでは、自動車業界を匠の技能で支える「職人」にスポットライトを当て、日本の「モノづくり」の真髄に迫る特集「日本のクルマづくりを支える職人たち」をスタート。
今回は、「プレス金型製作の匠」和田安信 (わだ やすのぶ)を取材した。
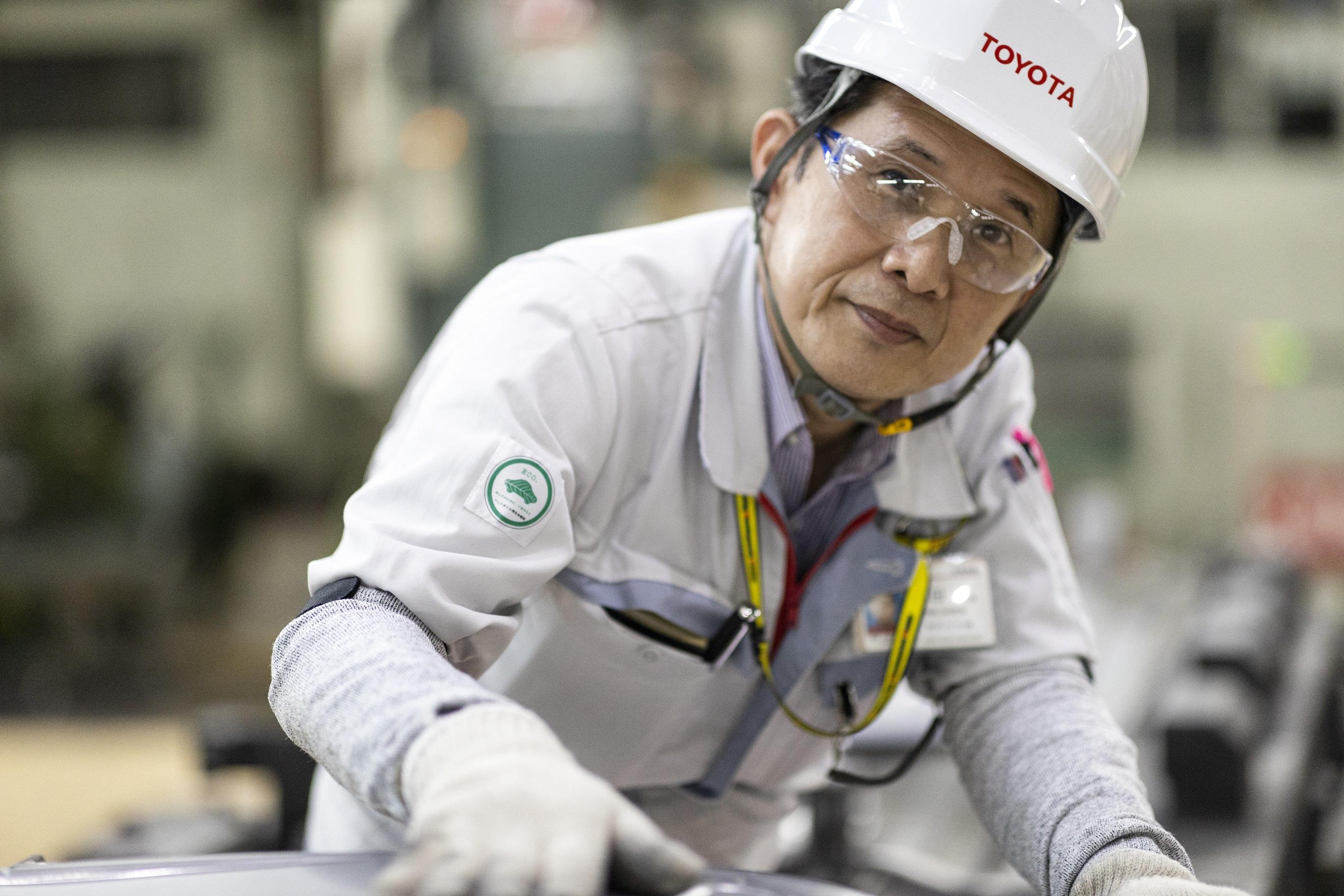
第5回 ボデーをつくるプレス機の金型を製作する「プレス金型製作の匠」 和田安信
トヨタ自動車 モビリティツーリング部 製品保証課 チーフエキスパート
ボデーづくりに欠かせないプレス金型
ボデーはクルマそのものであり、いくつもの大切な役割を担っている。
クルマの「見た目」を決めるばかりでなく、外界からの風雨や熱、寒さ、走行時の風や騒音から遮ることで乗員を守る役割。さらに万が一の事故や衝突の際、乗員の生命を守る役割もある。
それ以前にボデーはクルマの土台である。「走る・曲がる・止まる」というクルマの基本性能を支えるエンジンやサスペンションを筆頭に、すべての部品を組み付けるボデーがなければ、クルマは成立しない。だからボデーは強く軽く、内部は広く、そして外観は美しくなければならない。
そしてボデーは、フロアパネルやサイドシル、ルーフパネル、フロント、センター、リアのピラー(柱)やクロスメンバー、フェンダーやボンネット、トランクリッド、ドアパネルなど、クルマの中では大型の部品で構成される。しかも、こうしたボデー部品のほとんどが鋼板(鉄板)からつくられる。
では鋼板は、どのような方法でボデー部品に姿を変えるのか。
試作車の場合は板金職人がハンマーを握り手で叩いて成形することは、本連載の第4回でご紹介した。だが、生産車のボデーは一台一台、手作業で加工するわけにはいかない。
そこで使われるのがプレス加工という方法だ。使うのは大型のプレス機と、プレス機にセットする上下で1セットのプレス金型。

ある程度のボデー部品の形に切断した鋼板を、上下に金型をセットしたプレス機で挟んで1600トンの圧力を掛ける。すると、鋼板は金型のカタチに圧縮され変形して、金型に作り込まれた形状になる。このプレス加工を何度か繰り返すことで、鋼板は最終的にボデー部品に姿を変える。
トヨタ初の乗用車であるAA型自動車(1936〜1943年)は、最初の全鋼板ボデーの乗用車であり、トヨタでプレス加工によるボデー製作が始まったのはこのクルマから。
だが、AA型のボデーの多くは作業員の手叩きで成形され、当時の500トンプレス機で作られたボデー部品はごく一部だけだった。
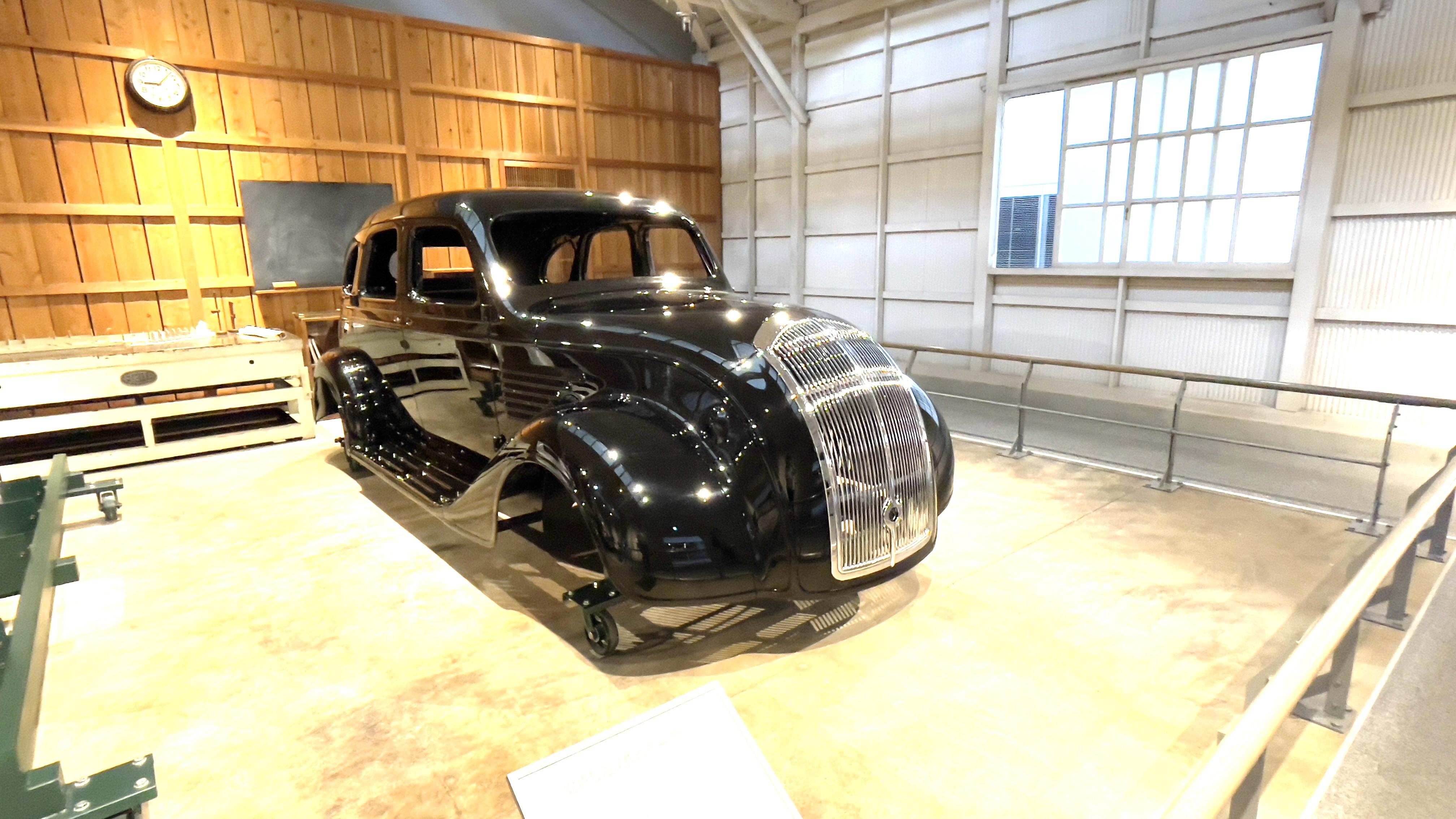
そして、トヨタでプレス加工によるボデー製作が本格的に始まったのは1955年1月に発売された初代クラウンから。
この初代クラウンを量産するために1959年に稼働を開始したトヨタ元町工場のプレス工程には、当時の最新鋭のプレス機だったアメリカ・ダンリー社製の600トンプレス機が初めて導入された。以降、トヨタのプレス加工技術はさらに進歩を遂げていく。
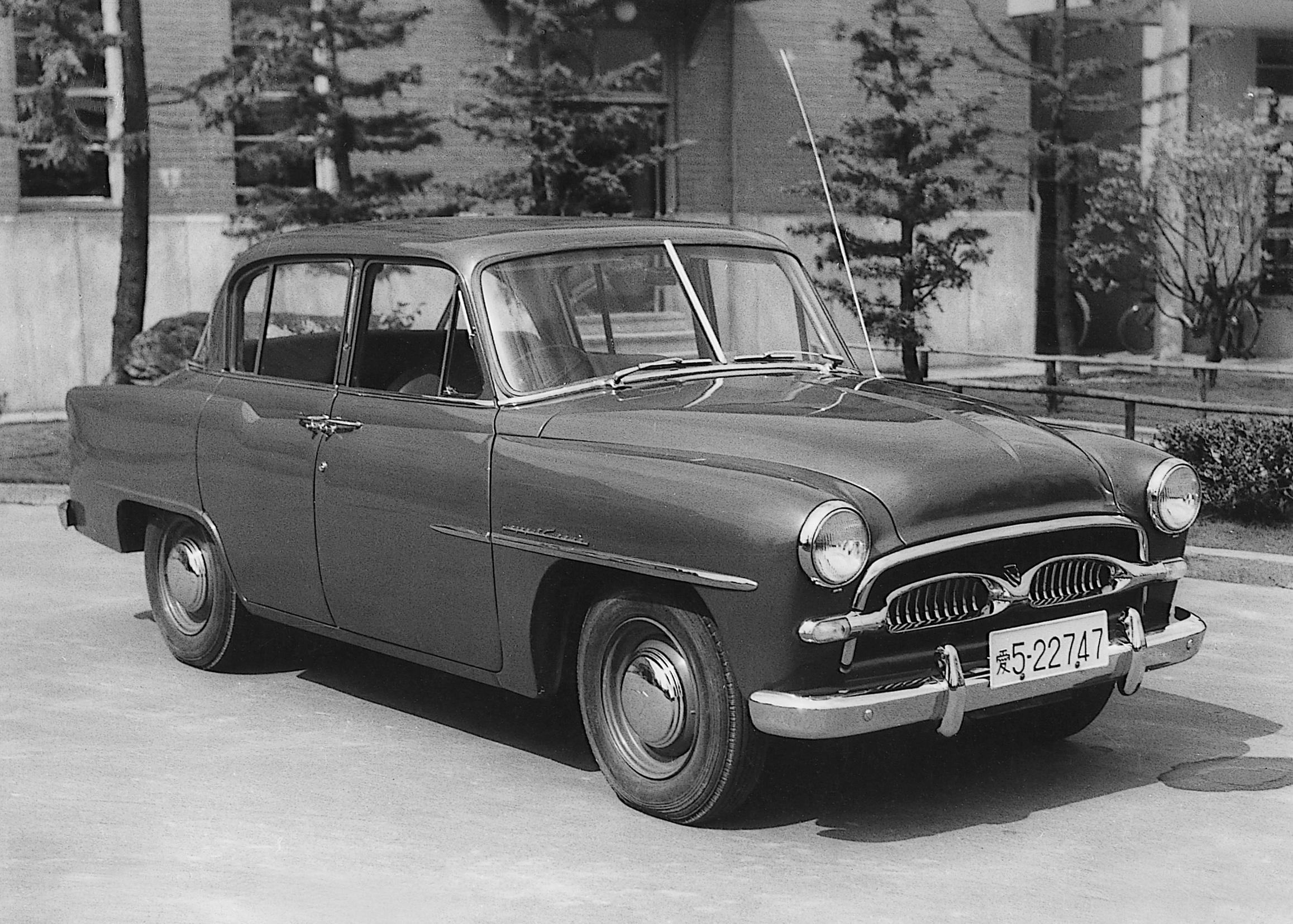
今回紹介する和田安信は、大型のボデー部品を作る大型プレス機で使うプレス金型づくりの匠。部内ではわずか2名しかいない専門技能「S級」の技能認定を受けた、プレス金型職人の頂点を極めた一人である。

「クルマは約3万点の部品で構成されていますが、そのうち、鋼板で作られる部品は約1000点。そのうちの約90%が金型によるプレス加工で製作されます。私はそのプレス加工で製作される部品の中でもいちばんの大物になるボデー外板のプレス金型をつくっています。部署としては工程整備というところ。1982年の入社以来、この仕事ひと筋です」
クルマのデザインを具現化する仕事
和田はみかんで有名な静岡県の旧・三ヶ日町(現・浜松市北区)に生まれ、旧・引佐(いなさ)高校、現在の浜松湖北高校の機械科を卒業してトヨタに入社した。トヨタを選んだのは、伯父がトヨタで働いていたことも理由だという。
「入社当時は生産ラインに配属されてクルマをつくりたい。そう思っていました。私が入社した1982年当時のプレス金型づくりはベテランのプレス金型職人による手作業が基本でした。約300名が手作業で、削った金型の粉で真っ黒になりながら仕事をしていました」
当時、工場の建物は古く、大型の設備や金型ばかりで「こんな汚いところで働くのか。しかも大型の金型が空中を飛んでおり(クレーンにて運搬)怖い職場だな」と思ったという。だがすぐに慣れて、先輩たちの作業を見ながら、先輩たちを超えたいという一心で、技能の向上に取り組んだ。
そんな和田が主に手掛けてきた仕事が、前述の通り生産ラインで使う外板パネルのプレス金型の製作だ。
クルマのデザインはデザイナーが手掛けるが、そのデザイン、特に外観のデザインを実際のクルマとして実現するには、和田たちプレス金型職人の技能なしには不可能なのだ。
デザイナーが描いた美しくてカッコいいデザイン。それが現実のクルマにできるかどうかは、ボデーの外板がそのデザイン通りに成形できるかどうかにかかっている。そして、それを実現するカギが、和田が製作している外板パネルのプレス金型なのである。
「ボデーの外板パネルの中でも“車両デザインの肝(キモ)”になる、いちばん大型の部品がボデーのサイド部全体を構成する『サイドメンバーアウター』。この部品の金型の大きさは長さ約4.5メートル、幅2.3メートル、重さは上下の金型を組み合わせた状態だと約30トンにもなります。この金型にわずかでも問題があると、上下の金型の間に大きな鋼板を挟んで1600トンもの力を加えて『ガシャン』とプレス加工する際に、パネルの一部が割れたり、ひずんでしまって美しく仕上がりません」巨大なプレス金型を手作業で、ミクロン単位で調整する
このサイドメンバーアウターをはじめ外板パネルのプレス加工による製造で使う巨大な金型は鋳物製。そして、この金型はまずコンピューター上でCADソフトを使って設計される。
次にこの設計データに基づいて、社外の鋳物メーカーが巨大な鋳物製の金型を製作。納入されたこの金型を、今度は社内にある巨大なNCマシン(数値制御)の加工機で切削して設計データ通りに精密に加工する。だがこの時点では金型は完成していない。
ここからが、和田たち工程整備のプレス金型職人の出番であり、腕の見せどころ。この巨大な金型をプレス機にセット。鋼板を実際にこの金型で何回も「打って」みて、どんな問題、不具合があるかを確認して金型を調整(修正)していく。
「実際に金型を使って鋼板を『打って』みると、さまざまな問題が出てきます。大きなパネルの一部にシワやひずみが出たり、鋼板の一部が割れてしまったり。これをチェックして、こうした問題、不具合が出ないように、金型の表面を削るなどして『調整』していきます」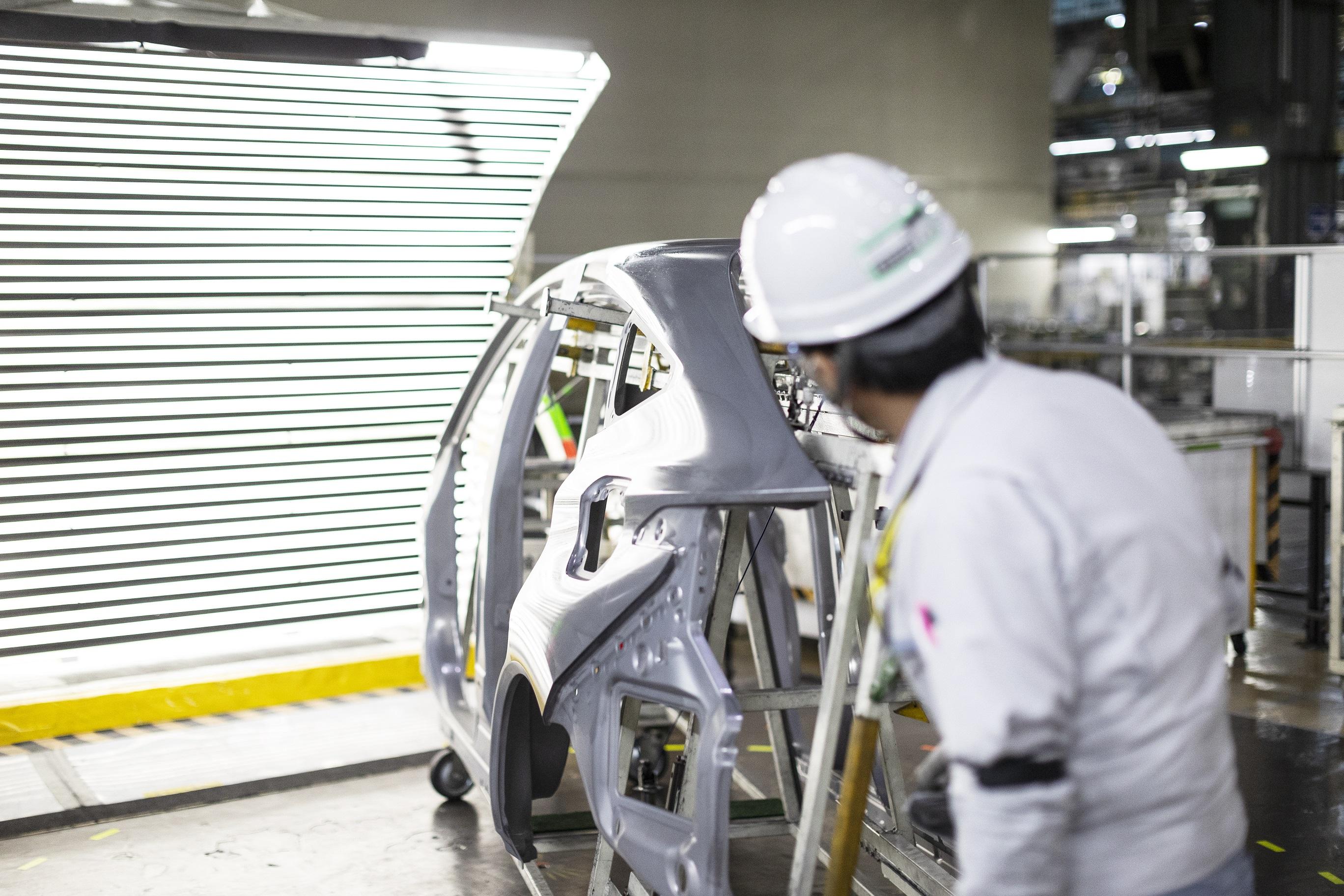
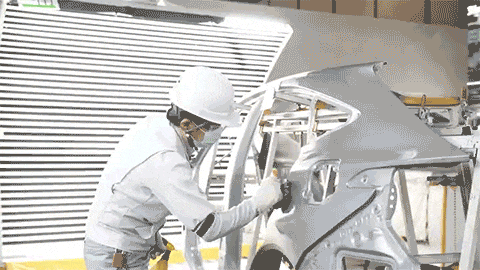
この調整作業はまさに「匠」の領域。
「まず打ってみた」外板パネルを、専用台に立てかけ、光の方向が整った専用の照明(フラットランプ)の光を当て、その光の通り具合やパネル表面の反射の様子を、目と指先で細かくチェック。パネルの表面にわずかでもひずみがないかどうか、どこにどんなひずみがあるかを確認する。
パネルの「割れ」や「シワ」は素人でもすぐに分かる。だが、外板パネルのひずみの場合は、普通の人の目には、どこに問題があるのかまったく分からない。だが和田には、外板パネル表面にある1/1000ミリ単位のごくわずかなひずみを即座に認識できるのだ。
「問題が出やすく、調整が難しいのは、パネルに設けられたラインが直線的ではなくカーブがつけられていて、そのカーブがだんだん小さくなる部分や、直線のライン同士がクロスしていてその『挟み角』がだんだん小さくなる部分。こうした部分は鋼板の“割れ”や“ひずみ”が発生しやすいのです」
この試しに打った外板パネルと、金型の両方をチェックして、和田は全長数メートル、何10トンもある巨大な金型に調整を加える。この「金型のチェック」の方法も、実にアナログなやり方だ。

測定器を使うこともあるというが、最終的な調整は目視や直線の定規を当てることで、また平らに削って直線を出した微細な砥石を当てることで行う。手に持った砥石で金型の表面を撫でるとき、その当たり方で、金型の状態がわかる。そこで、過去の仕事の経験を踏まえて、金型のどこをどう調整するかを考えるのだという。
「この砥石を金型に10回かけると、3/1000ミリほど表面を削ることができます。大きな調整が必要な場合は切削工具を、細かな調整にはサンドペーパーやこうした砥石を使います」
この調整作業を行う際、和田はプレス加工の際の、金型と鋼板の動きを頭の中でイメージしている。これがプレス金型職人には欠かせない感覚だという。ただ、それにはセンスと最低でも10年程度の経験が必要だ。「ひと声10年」と言われてきたと和田は言う。
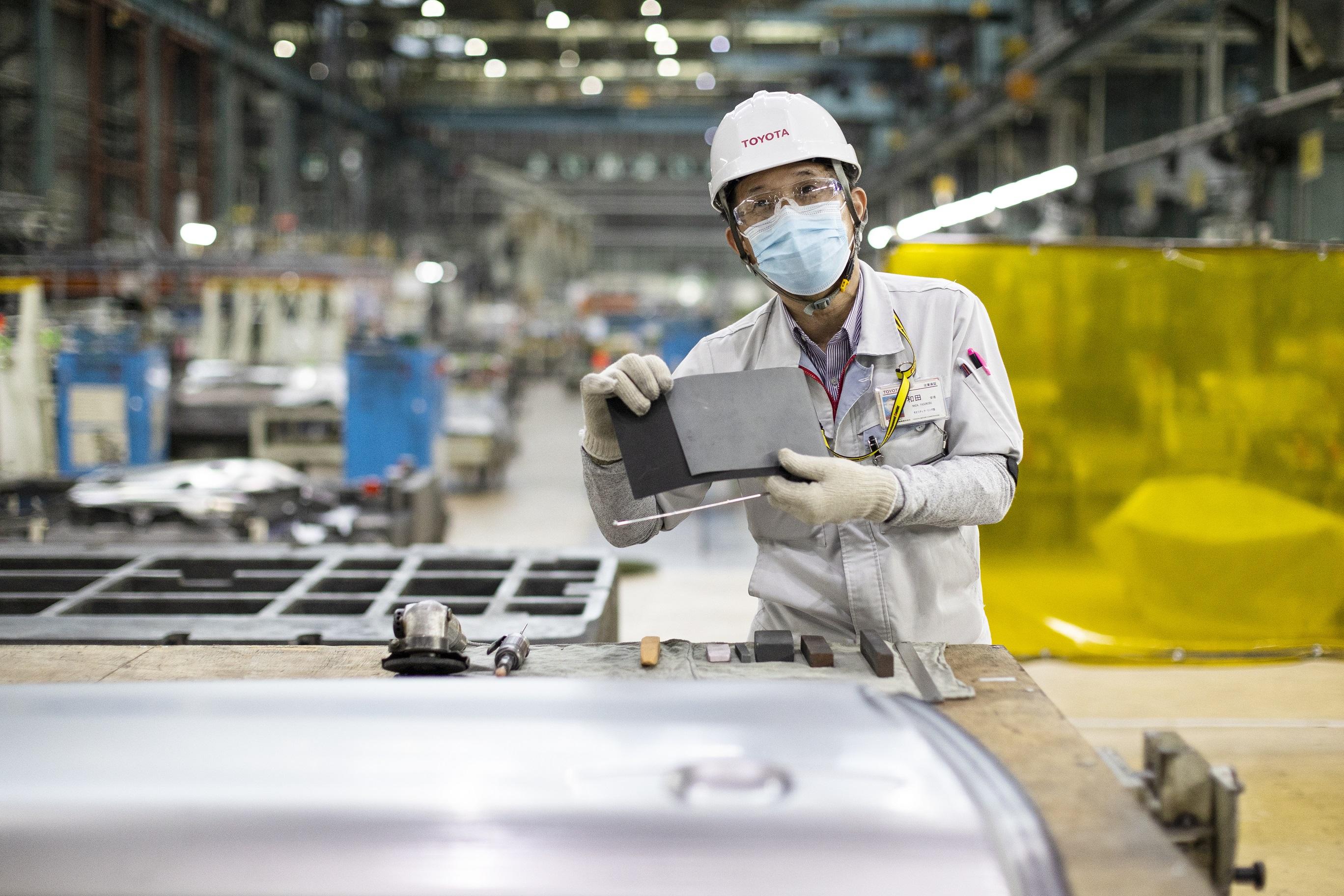
「狙い通りの加工ができるように金型を調整する方法は、実は一つではありません。どこをどう削ってどうカタチを変えるかは、職人一人ひとりでやり方が違います。どれが一番いい調整方法なのか、自分の経験と技能を総合して考え、作業を行います」
普通の人なら絶対に分からない大きな外板パネルのごくわずかなひずみを、光を当てて見ただけで即座に見抜く。
何メートルもある大きさ、数十トンもある複雑な形状の金型を、自分の目と指先の感覚、過去の経験を頼りにミクロン単位にまでこだわり理想的な形状に仕上げる。その感覚の鋭敏さ、繊細さと、卓越した技能にはただ驚嘆するしかない。


4年間も“働き続ける”プレス金型
和田たちがこの繊細な調整作業を繰り返して完成した金型は、生産ラインにある超大型のプレス機にセットされ、そのクルマがモデルチェンジするまでラインで使い続けられる。その金型の使用環境は驚くほど過酷だ。
実際の生産ラインでは、鋼板が1分間に約16枚というハイペースで加工される。つまりプレス金型は、3.75秒ごとに、1600トンもの圧力が連続で加えられることになる。
しかも、このハイペースでの加工が休みなく続く。現在、クルマは約4年のサイクルでモデルチェンジすることが多い。だから外板のプレス金型は、その4年間はこの過酷な試練に耐え続けなければならない。

そのうえ、外板パネルのプレス加工は1回では終わらない。一気に成形しようとすると鋼板が割れてしまうから、プレス加工は何回かに分けて行われる。
なお、トヨタの場合は鋼板から最終的な外板パネルになるまで、例え高級車でも最大4回(4工程)のプレス加工で仕上げることが決められている。この場合、一つの部品のために4つの加工段階に応じた、違った形状の金型を準備しなければならない。
海外工場のマザーファクトリーとして
和田の部署が担当するのは、国内工場の金型の調整だけではない。
トヨタは世界各国に工場がある。そこで使う外板パネルのプレス金型も、ここで仕上げられたものが母型になる。ここで製作したものを海外工場に送って、それが現地の工場で使われる場合もある。また、ここで仕上げた金型を精密に計測してデータ化して、そのデータを現地に送り、現地でそのデータを元に金型を製作して使うこともある。
つまり、ここは世界のトヨタの外板ボデー製作のマザーファクトリーなのだ。
どちらの場合も、和田たちはその海外工場に数カ月は出張して仕事をするという。日本で製作して現地に届けた金型。現地でデータを元に製作したプレス金型。これを現地のプレス機に設置して、日本と同様の品質の外板パネルを生産できるよう、現地スタッフとともに金型を調整するのだ。
この工程整備作業を、和田たちは「再現」と呼んでいる。和田も中国に1年、インドネシアに3年駐在し、また世界中の造型工場に数カ月滞在して、この「再現」という時間のかかる難しい作業を行ってきた。
「海外のプレス機は日本にあるものとは仕様が違ったり、昔の設備だったりすることもあるため、日本から送ったプレス金型をただ設置しただけでは、日本と変わらぬ品質の外板パネルは生産できません。やはり試しにプレスを打ってみて、その仕上がりを確認して金型を調整する作業が必要です」
言葉が通じない中で、現地のスタッフとスムーズに仕事を進めるには、彼らに指導者としての実力を認めてもらわなければならず、それなしには彼らに納得して働いてもらえないのだと和田は語る。
技能を見せて信頼してもらう。そこからスタッフとのコミュニケーションが初めて可能になるという。
デジタルデータ化できない感覚、技能、経験
ところで、最初に述べたようにこのプレス金型の世界でも、モノづくりのデジタル化、データ化が進んでいる。
2000年以降、プレス金型はCAD/CAMの精度が向上し、和田たちの技能もデータ化しようという取り組みが進められている。
「データ化にはもちろん良いことがあります。例えば、現地で金型の調整に失敗した場合は、設計データを使って現地で機械加工から金型を作り直すことができます。そこから調整作業をやり直すことができる。これは昔なら不可能なことでした。これはデータ化された恩恵ですね」
和田たちはトヨタの他部署と同様に、プレス金型づくりの作業や技能を徹底的にデジタル化、データ化する取り組みを進めている。
だが、プレス金型づくりにはデジタルデータにできない、感覚と技能でしか伝えられない、経験を積まないと分からない繊細な部分がどうしてもあるという。こうした感覚と技能をどう伝えていくかが、和田の部署の大きな課題だ。
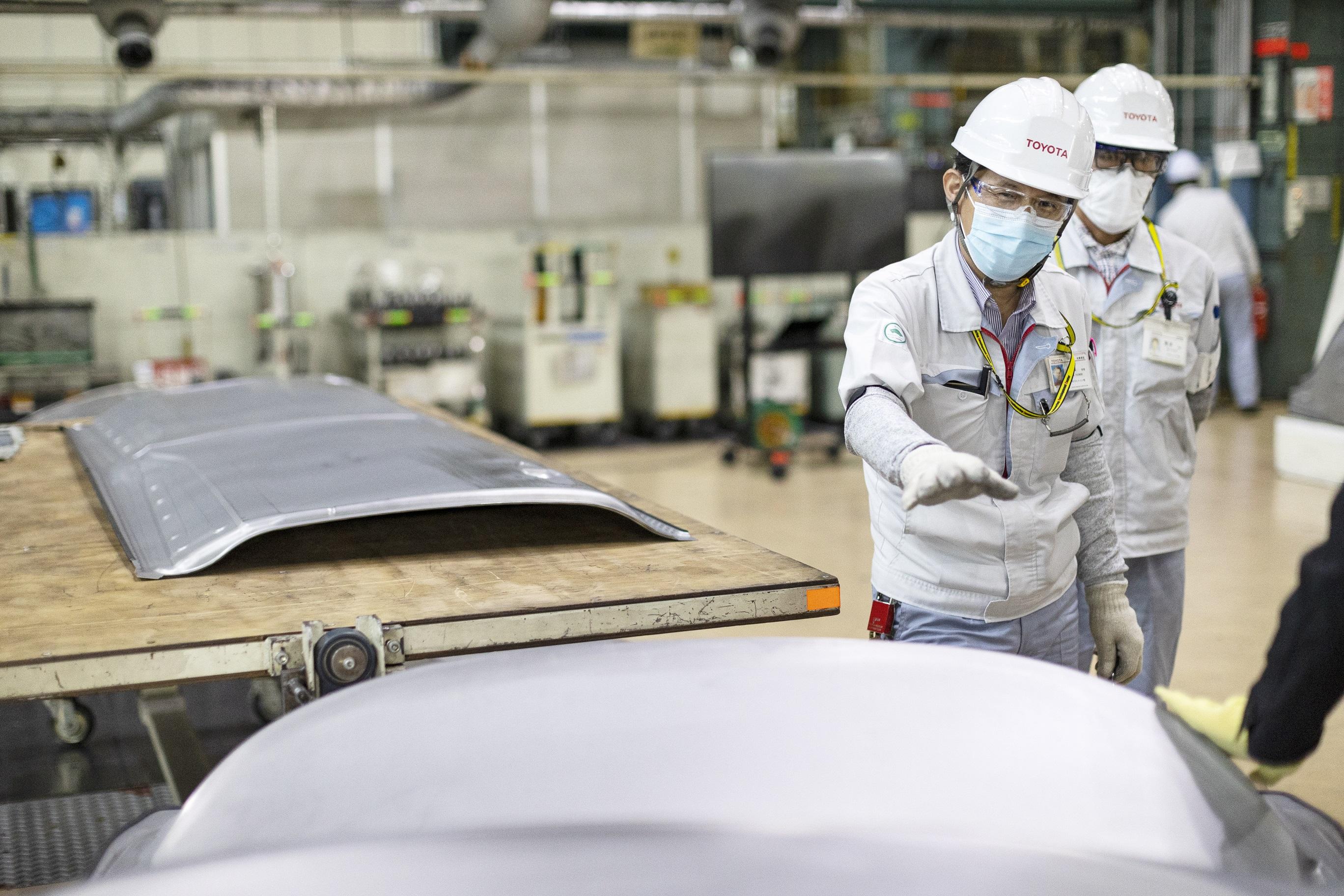
「金型によるプレス加工には、実際に加工してみないと分からないことがたくさんあります。私には、3D設計ソフトで設計されたプレス金型をディスプレイの画面で見たとき『何か問題が起こりそうだ』くらいは分かります。ですが、どんな不具合が起こるかは、実際に打ってみないと分からないのです」
特に難しいのは経験を積ませることだ。和田の時代には「失敗すること」が許された。だが今は設計から生産までのリードタイムが短く、後進の若い人たちにはその時間的な余裕がないという。この問題を何とかしたい、と和田は語る。
「プレス金型づくりのデジタル化。それに対応できるデジタル人材を育てることはこれからの時代には欠かせません。でも、プレス金型づくりがすべてデジタル化されて、プレス金型職人が不要になることはないでしょうから」「もっといいクルマづくり」のために
プレス金型職人として、トヨタの頂点の一人に登りつめた和田。だが「自分はまだ一人前ではない。もっと成長しなければならない」と和田は語る。
それは今から10年あまり前の2009年、豊田章男が社長に就任してから、トヨタのクルマづくりが変わったからだ。
「社長が『もっといいクルマをつくろう』と宣言してから、大きくクルマづくり、特にボデーのデザインが変わりました。社長の言葉で、デザイナーや私たち車両デザインに関わるスタッフが『もっとカッコいいクルマをつくっていかなければいけない』というように、意識が変化したんです。それまでトヨタのボデーは、プレス加工でひずみが出にくいし、金型もつくりやすい、“まるっとした”デザインが多かった。いろんな理由からプレス要件があり、その要件に沿ってデザインするとそのようになっていたからです。

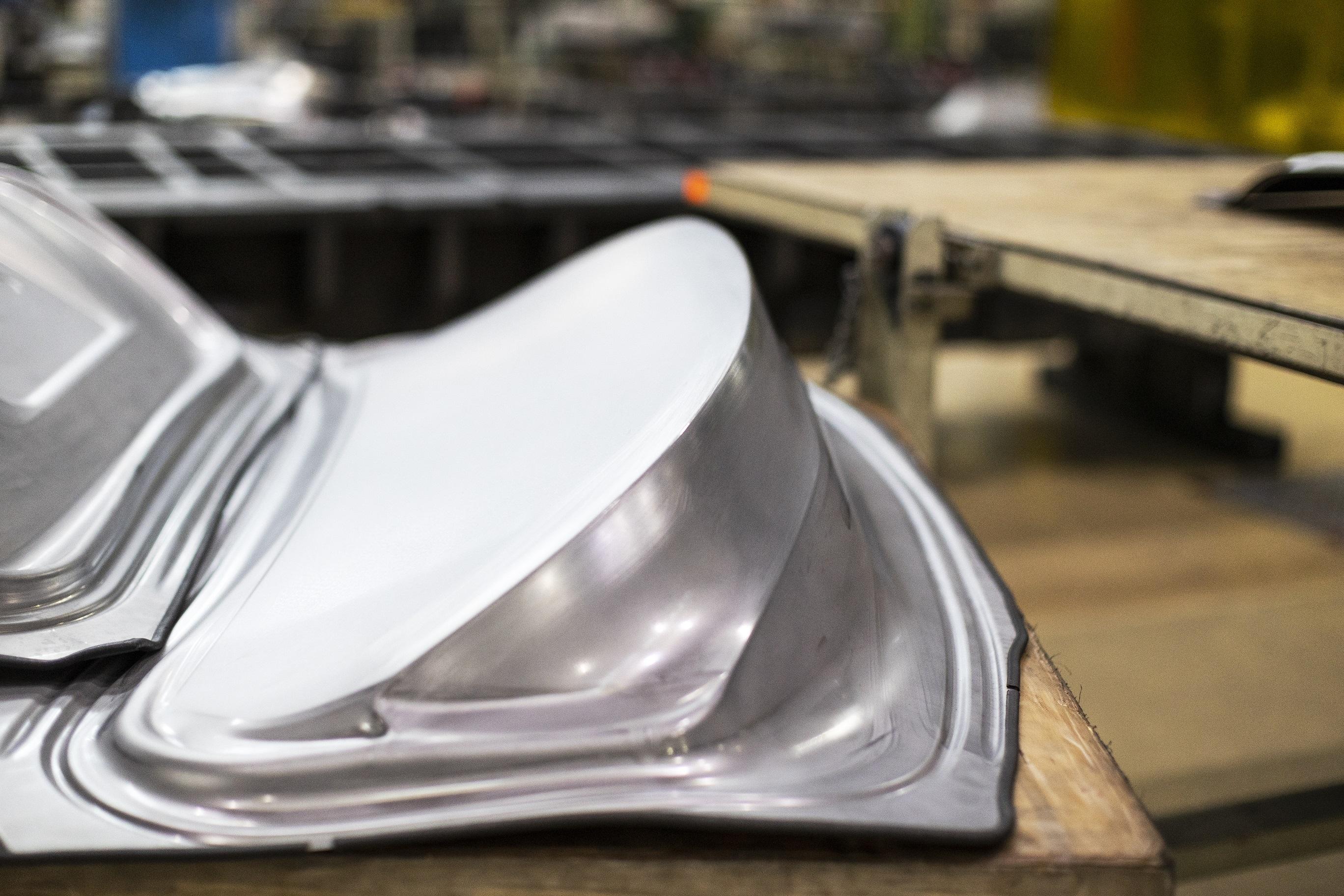
だが、社長のこの一言が現場を変えた。デザイナーがカッコいいクルマをせっかくデザインしているのだから、何とかしてデザイナーが意図したそのデザインを実現しようと、現場の空気が一変した。デザイン部門との交流も始まった。和田たちは今、これまでのトヨタ車にはなかった、エッジがシャープなデザインへの挑戦を続けている。
「あれから10年あまり。素材も技術もデザインもどんどん変わって進化しているので、勉強と挑戦の連続です。そういえば、LEXUS ISのカタログの、リヤフェンダーとラゲージまわりのデザイン解説で、プレス技術に触れてくれたことは、前代未聞のことでした。うれしかったですね」
ところで、前述したようにトヨタ車のボデー外板のプレス加工は最大でも4工程、つまり4回のプレス加工で完成させることになっている。ところが欧州の高級車は6工程が一般的。つまり和田たちは4工程で6工程以上の品質を実現することに成功したのだ。だが技術と技能をさらに磨けば、3回で同じ加工が実現できるはずだと和田は語る。
クルマを運転していて、周囲を走るカッコいいクルマを見ると、気にせずにはいられないと語るプレス加工の金型の匠、和田安信。デジタル時代の中での源流技能の継承。そして自身の知識や技能のさらなる向上。プレス加工の現場から「もっといいクルマづくり」を目指す和田の挑戦はこれからも続く。
(文・渋谷 康人、写真・前田 晃)