
自動車業界を匠の技で支える「職人」特集。第3回は"トヨタの鍛冶屋さん"を名乗る「鍛造の匠」に話を聞く

3DプリンターやAIをはじめとするテクノロジーの進化に注目が集まる時代だが、クルマづくりの現場では今もなお数多の「手仕事」が生かされている。
トヨタイムズでは、自動車業界を匠の技能で支える「職人」にスポットライトを当て、日本の「モノづくり」の真髄に迫る特集「日本のクルマづくりを支える職人たち」をスタート。
今回は、「鍛造の匠」 安藤寿朗(あんどう としお)を取材した。

第3回 鉄の気持ちが分かる「鍛造の匠」 安藤寿朗
トヨタ自動車 明知(みょうち)工場 パワートレーン統括部 PT管理室 技能・育成グループ シニアエキスパート(SX)
トヨタの “鍛冶屋さん”
安藤寿朗は1968年6月24日、トヨタ自動車の地元・豊田市生まれ。高校を卒業して1987年4月1日に入社後、鍛造(たんぞう)による部品製造を業務とする第5生産技術部に配属されてから、主に試作と生産準備のエキスパートとして活躍してきた。
鍛造は鋳造(ちゅうぞう)と並んで最も古い金属加工技術の一つだ。真っ赤になるまで加熱した金属を片手ハンマーで叩いて変形させて、目指す形状のものを造る。鍛冶仕事、と言った方が分かりやすいかもしれない。今から半世紀ほど前までは、どの町や村にも鍛冶仕事をする鍛冶屋さんがいて、包丁やはさみ、鎌や鋤などの鉄の道具を手づくりし販売していた。だが、今では鍛冶屋さんの姿を見る機会はほとんどなく、この言葉も忘れられつつある。
鉄の鍛造の歴史は、一説によると紀元前1700年頃、小アジアで鉄器を発明したヒッタイト民族にまで遡る。
熱して叩くと金属の内部では大きな変化が起こる。金属の結晶は微細化され、結晶間のすき間が詰まって密度が高くなる。さらにバラバラだった結晶の方向も変わる。まるで木目のように規則正しく整うのだ。この線をメタルフロー(鍛流線)といい、金属の強度はこの方向でぐっと高まる。また叩くことで金属内部の不純物や炭素が外に排出され、その性質を変えることもできる。
鍛造加工は金属をより硬く、衝撃に強く、粘り強くする方法でもある。材料を加熱しないで叩くことで、より精密度を上げる冷間鍛造という手法もある。
「私はトヨタの鍛冶屋さん。普通の人はご存じないかもしれませんが、クルマには鍛造でしか造れない部品があるんです。だから鍛冶屋仕事は欠かせません」

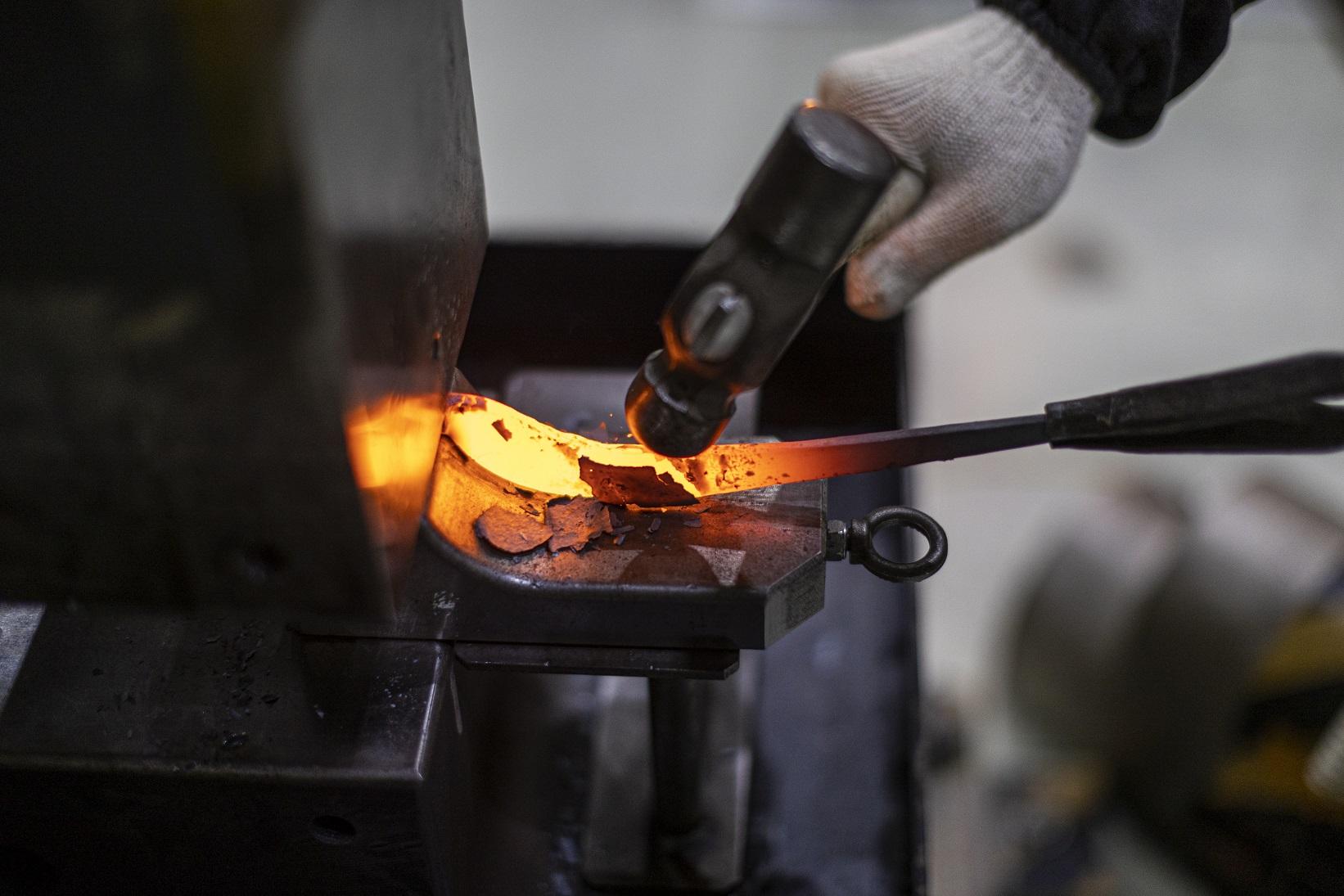
安藤は現在、明知工場内の育成センターでこの「鍛造の匠」として、金属材料からハンマーだけを使って手作業でモノをつくることから始まる鍛造実習を指導、鍛造という技術の素晴らしさ、難しさ、奥深さを後輩たちに伝えている。
クルマづくりに不可欠な鍛造
クルマはエンジンのシリンダー内でガソリンと空気の混合気が爆発的に燃焼することで発生するエネルギーで動く。そしてこの力を受け止め回転運動へと変換させるコネクティングロッド(コンロッド)やクランクシャフトなどのエンジン部品には、常に大きな力がかかっている。この力をタイヤに伝えるトランスミッションのギアなど伝達装置の部品、タイヤを支えタイヤが受ける路面からの力も受け止めるサスペンションの部品も同様だ。しかも、こうしたパーツは絶対に壊れてはいけない。壊れることは即、走行不能や交通事故に直結する。だから頑丈に造らなければならない。
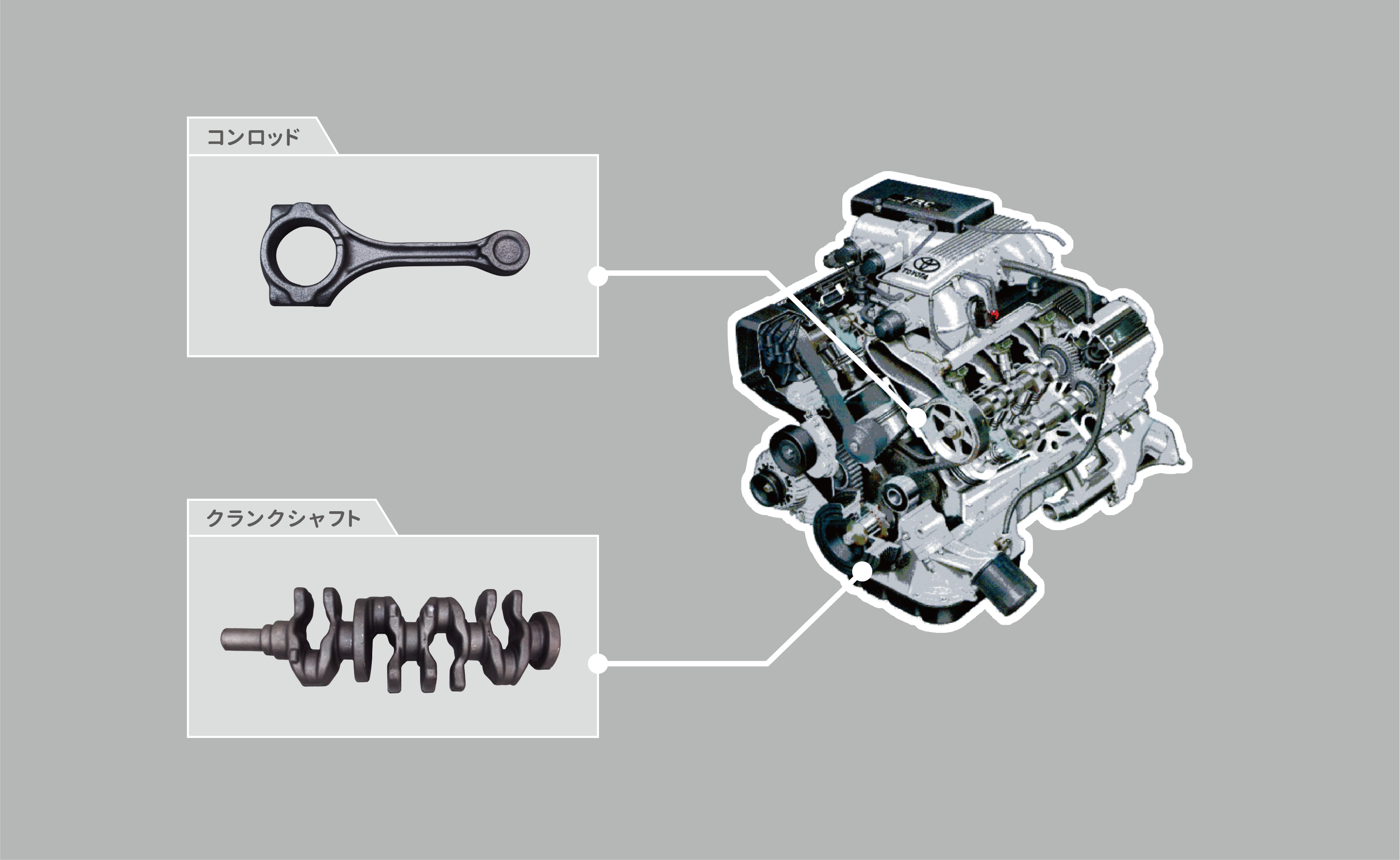
このような重要部品の製造に欠かせないのが鍛造技術である。そして、トヨタはクルマづくりのために今から80年以上も前の創業当初から、この技術の研究と発展、技術者の育成に取り組んできた。
トヨタ自動車の鍛造部門は1934年1月に豊田自動織機製作所に設けられた、自動車用鋼材を研究・開発する製鋼部に始まる。ここにはアメリカから輸入した蒸気で動く鍛造機が設置されていたと記録にある。そして1938年11月、完成した挙母(ころも)工場で鍛造部品の生産が始まる。トヨタ産業技術記念館の資料によれば、挙母工場には1/2トン、1トン、2トンという3台の蒸気で動くフリーハンマー(プレス機)があり、金型を使わない「自由鍛造」で、何と4人がかりで部品造りを行っていたという。
トヨタは鍛造による近代的な工業生産の草分け的存在であり、安藤はこの歴史と源流技能を受け継ぐ数少ない存在である。
柔道から鍛造の道へ
安藤は子どもの頃、モノを分解することが大好きだった。またクルマも大好きだという。ただ、トヨタに入社したのはクルマ好きだったからではない。
「私は普通科高校の出身です。柔道で愛知県のチャンピオンになって、スポーツ推薦で入社が決まりました。でも入社直前の練習で大きなけがをしてしまったのです。かなりの大けがで『現役続行は不可能だ』と言われました」

柔道選手として未来を夢見ていた安藤にとってこの事態は、耐え難い大きな挫折だったに違いない。だが安藤は柔道ではなく「鍛造の道」を極めることを決意する。
「同期の新入社員は工業高校などで鍛造の実習経験がある人たち。でも私は鍛造のことなど何も知りません。そもそも、普通科出身の人間がこの部門に配属されるのは珍しいことなのです」
仕事ができなければここにいる意味がないし、仕事は楽しんでやりたい。そのためにも、仕事ができるようにならなければ。安藤は当時、そう考えていたという。
「自分は負けず嫌い。下手だ、ダメだと言われて『やってやろう!』と思いました。技能で先輩を抜いて見返してやりたい。そう思ってがむしゃらに技能の習得に取り組みました」
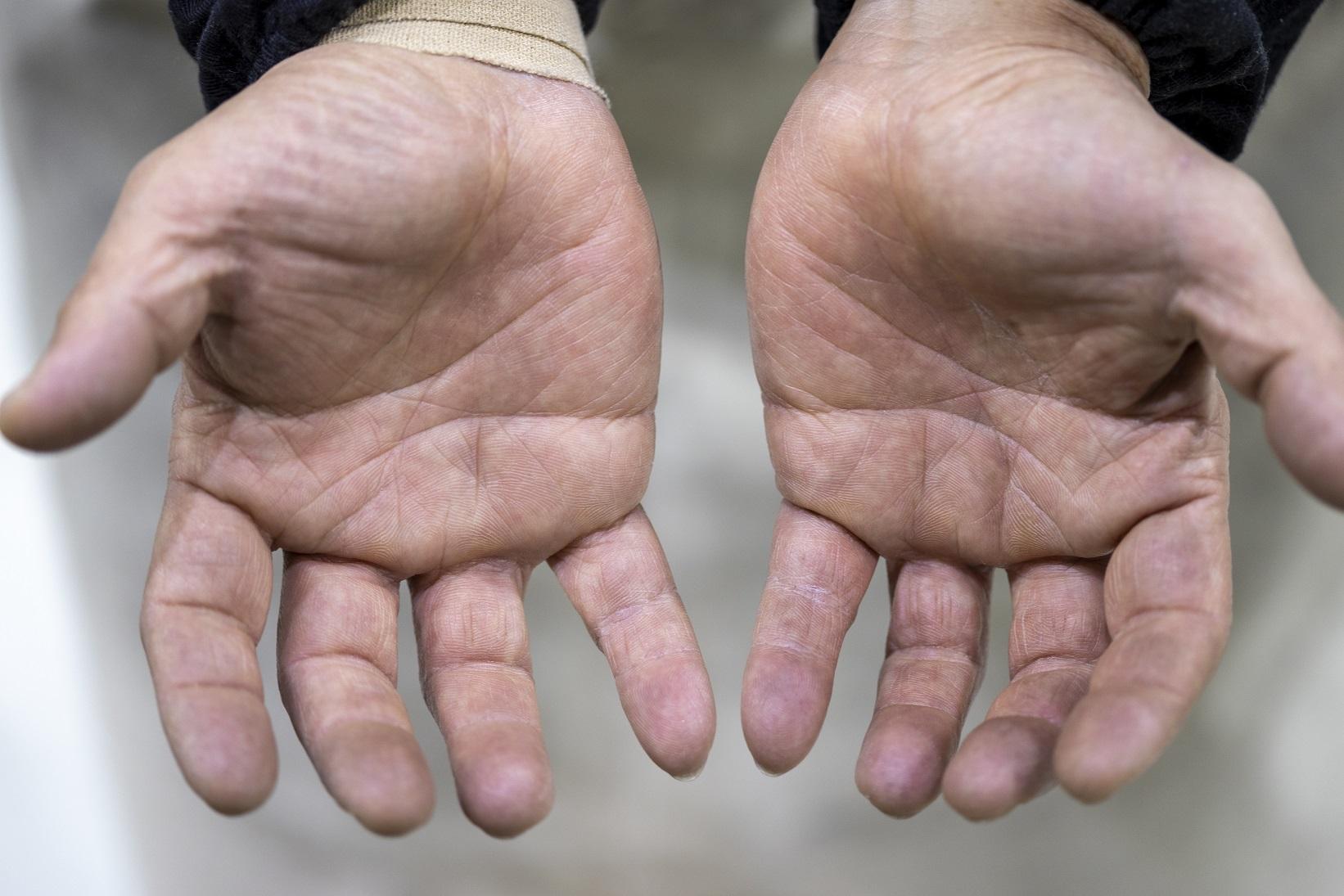
安藤を魅了した「鍛造」の魅力
鍛造部門はかつて、トヨタのモノづくりの現場でもっとも辛いところといわれた。キツい、汚い、危険の三拍子が揃った、いわゆる3K職場だったという。金属の塊を真っ赤になるまで加熱して高温にし、何トンもの力が出るプレス機や手に持ったハンマーで、大音響とともに何回もたたく。現場は過酷な環境になるのは当然だ。
中学校を卒業してトヨタに入社し、鍛造の現場から副社長にまで上り詰め、現在はトヨタのエグゼクティブフェローを務める河合満(かわいみつる)は、あるビジネス誌のインタビューで「入社当時、鍛造部門だけはキツいから嫌だなと思った。配属されたときは辞めることを考えた」と語っている。
だが安藤は、経験と勘を頼りに手作業で鍛造によるさまざまな試作部品造りを行う先輩たちから指導を受ける日々を送るうちに、鍛造の素晴らしさ、面白さ、奥深さに魅せられていった。
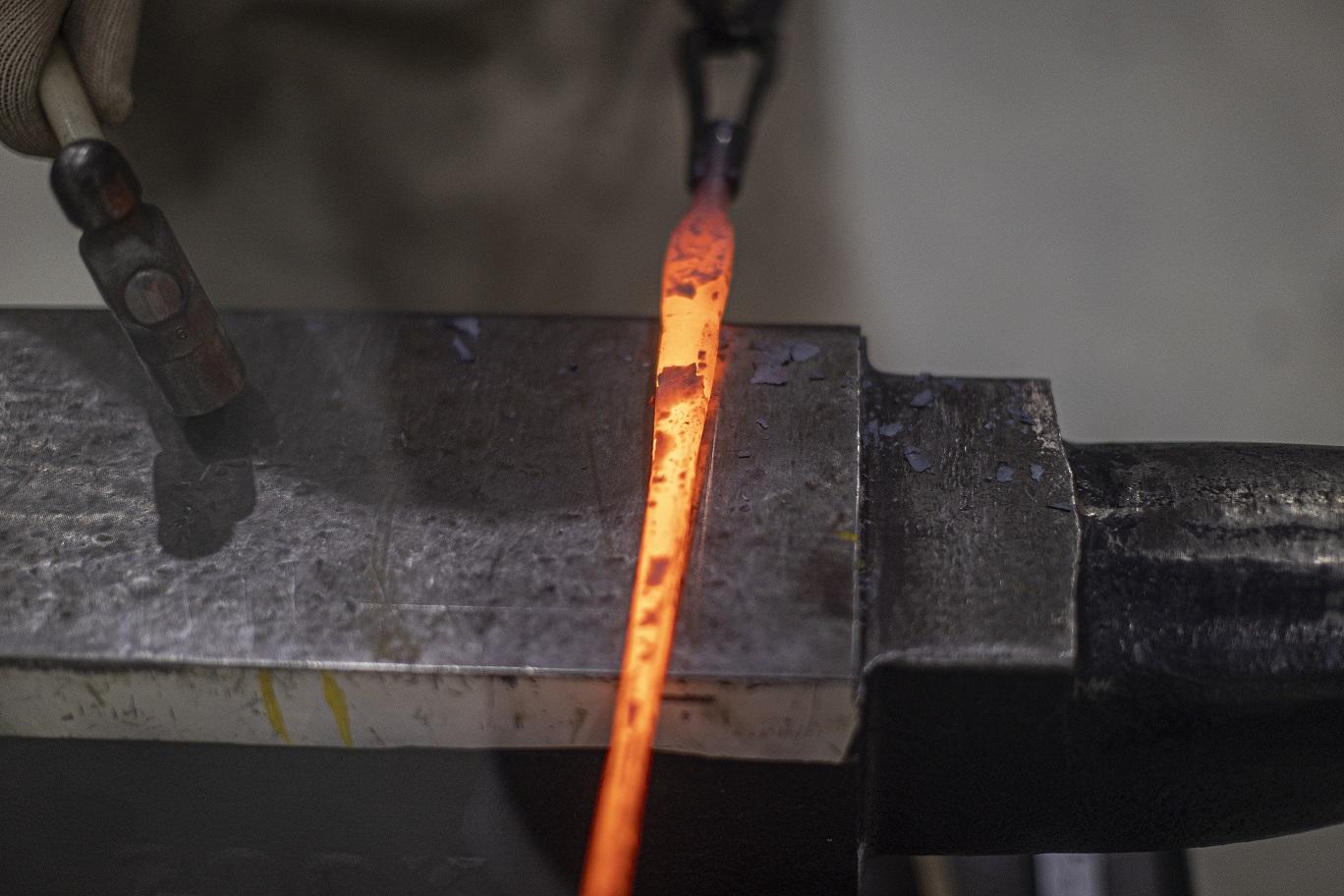
「熱を入れることで硬い金属を目指す形状に造形できる。しかも、鍛えることで強くできる。これは切削や鋳造など他の技術では不可能なこと。だから鍛造でなければ造れない部品も多い。新しいクルマをつくるとき、部品造りの方法に鍛造が選ばれると『やっぱり鍛造だろう』と、誇らしい気持ちになりましたね」
設計部門と協力し、鍛造により低コストで高品質な部品造りを実現する生産準備も安藤の仕事だった。この構造は鍛造で造れるのか。製造しやすくするためにはどのような形状にして、どんな手順で造ればいいのか。トヨタのクルマには安藤のこのノウハウ、工夫が生かされている。
全自動化された今だからこそ
とはいえ、トヨタは他社に先駆けて鍛造作業の機械化、自動化を積極的に進めてきた。たとえば安藤が生まれる4年前の1964年には、エンジンの主要部品であるコネクティングロッドの製造に、初めてアメリカ製の自動鍛造プレス機を導入している。
現在では、クランクシャフトも含めて多くの鍛造部品が、材料の投入から完成品に至るまで、コンピューター制御の全自動機械で一貫生産されている。もはや3K職場は完全に昔の話。だが、安藤はそんな今だからこそ、未来のために手仕事に始まる鍛造の源流技能の継承が不可欠だと熱く語る。
「金属材料を鍛造で加工するときの最適な材料温度、型温度、潤滑剤被膜の条件を鍛造加工点の『良品条件』と言います。この『良品条件』がどこにあるかは、言葉やマニュアルでは伝えることができない“暗黙知”の次元にあります。つまり、一人ひとりが実際に加工を体験して、感覚でつかむしかない。
鍛造に限らず、すべての作業が自動化された現在でも、モノづくりに携わる技術者には『手作業によるモノづくりの感覚』が欠かせません。機械の中で材料がどのように形を変えるのか。これが想像できるようにならないと、何かトラブルが起きたとき、うまく解決できないのです」
安藤のこの思想は、安藤が入社した当時の現場で班長だったエグゼクティブフェロー、河合満の「モノづくりの思想」そのものである。明知工場の「鍛造道場」は、この思想に基づいて設置された。ここは鍛造のほか、同特集 第1、2回で取り上げた木工や鋳造などさまざまな源流技能、手作業による仕事のノウハウとスキルを未来に受け継ぐための教育の場。安藤は鍛造の源流技術とともに、モノづくりに対するこの考え方も若手に伝えているのだ。
「鉄の気持ち」を理解する
安藤は鍛造道場で、鍛造の上級者が取り組む鍛造実習、「フリーハンマー」と呼ばれる、金型など一切使わず手持ちの片手ハンマーとエアー駆動のフリーハンマーだけで、丸い鉄の棒から片手火箸を作る作業を実演してくれた。

作業着に作業用の手袋、ヘルメットと安全用の分厚いフェイスシールドを着用した安藤は、ガスバーナーで1000℃以上に真っ赤に加熱した鉄の棒を、火箸ではさみ、フリーハンマーと手にした片手ハンマーを使って叩いていく。すると、まるで手品のように鉄の棒は火箸に姿を変えた。まったくのフリーハンドでの作業だ。

安藤は作業をしながら、常に材料と無言で対話をしている。一目見ただけで材料の温度を把握し、最適な手順とタイミングで、最適な力を加えて、手作業だけで素材を鍛えて目指す形に仕上げる。
「手作業による鍛造で良いモノづくりをするためには、五感を研ぎすまして、材料の温度や変形する量を常に感じ取り、どうすれば素材の形を目的の形状に成形できるか、作業しながら考え続けることで、鍛造加工点の感覚を身に付けるしかありません」
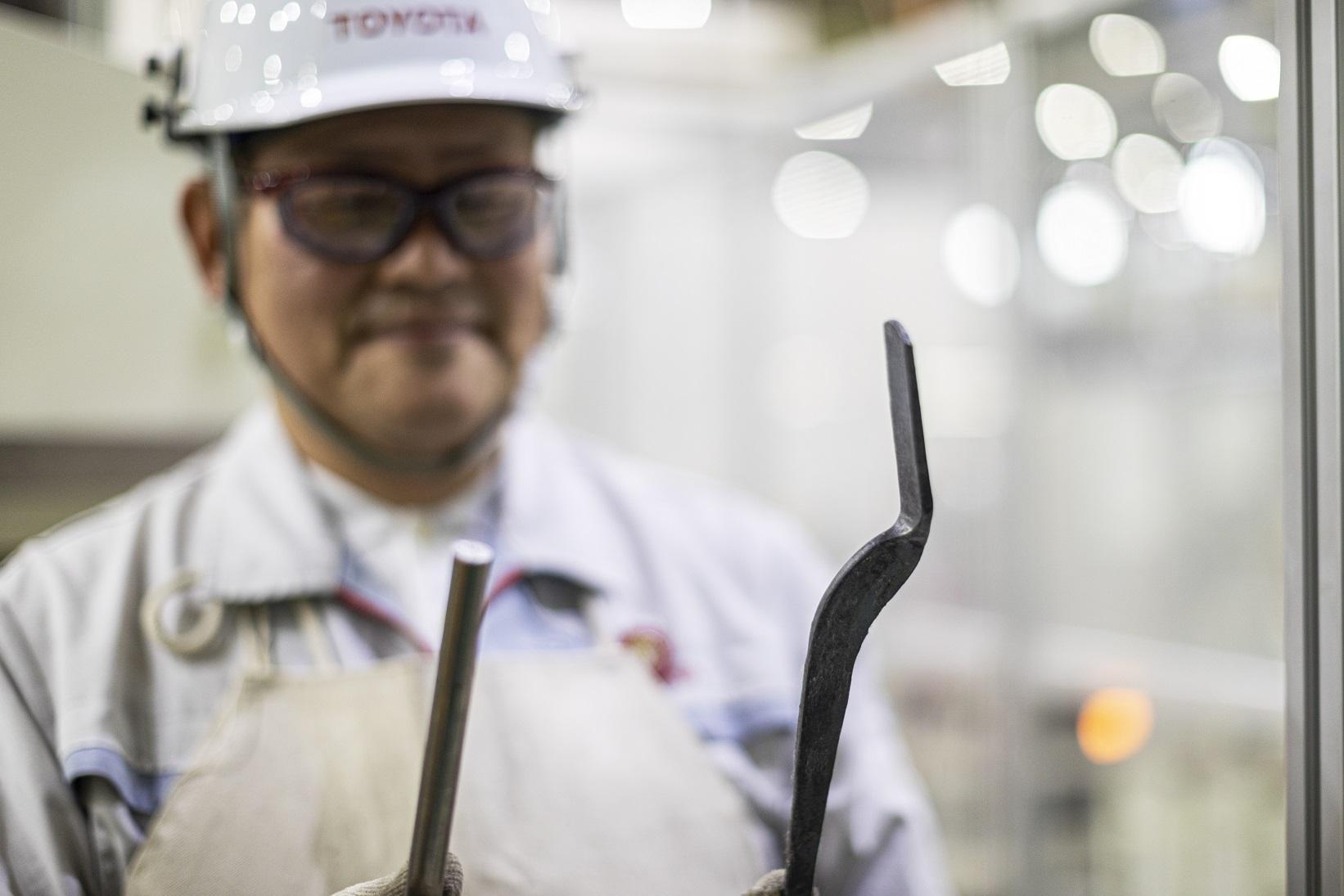
安藤はこの感覚を「鉄の気持ち」という言葉で表現する。材料の気持ちが分からなければ、理想のモノづくりはできない。これは鍛造に限らず、優れた職人すべてに共通する大切な感覚と言っていいだろう。
「私はよく実習生たちに『鉄の気持ちになりなさい』と言います。私は常に『鉄の気持ち』を考えている。ただ十数年付き合いましたが『アルミ(ニウム)の気持ち』はまだ分からない…。これからはクルマの電動化・軽量化で、これまで以上にアルミや新素材の出番が増えることは間違いありません。ぜひ『アルミや新素材の気持ち』が分かるようになりたいですね」
クルマづくりに欠かせない鍛造技術の“暗黙知”の伝承と、新素材への対応。そして、暗黙知を形式値化することで技能と生産技術へのスパイラルアップを図っている。「鍛造の匠」安藤の挑戦は今も続いている。
(文・渋谷 康人、写真・前田 晃)