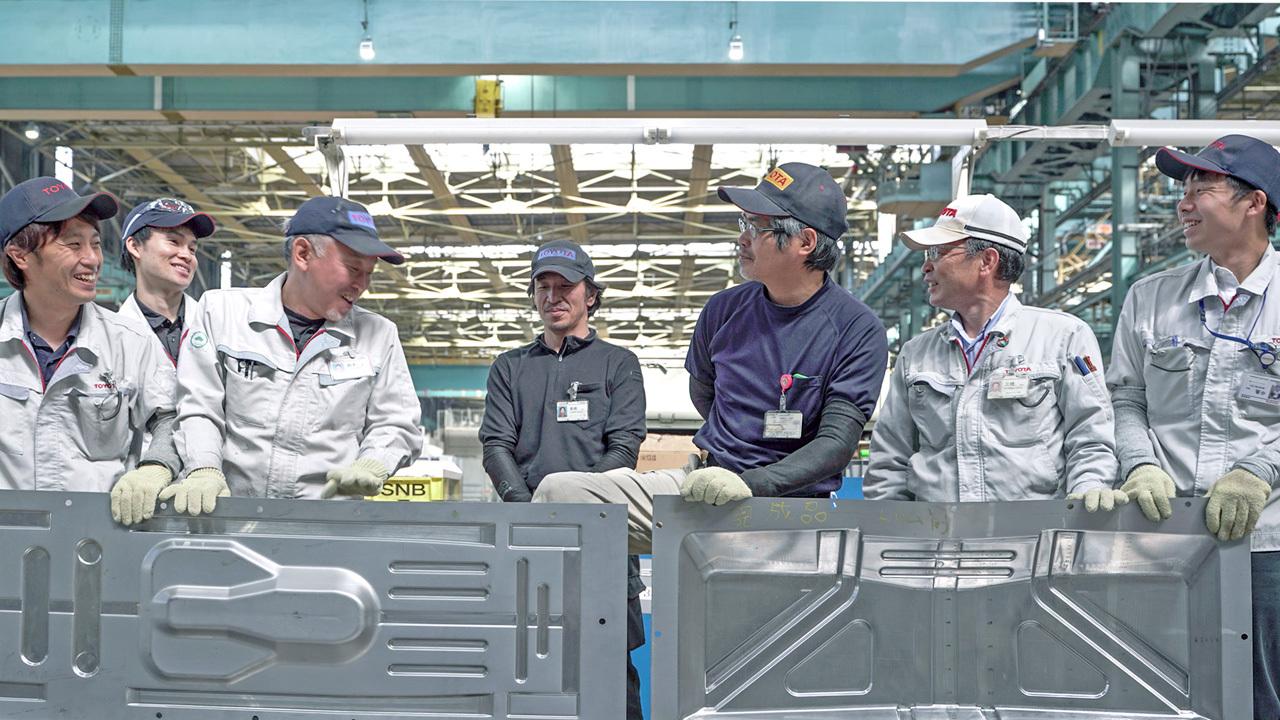
自動車業界が大変革期にある今、トヨタの原点に立ち返るべく始まった「初代クラウン・レストア・プロジェクト」。第6回では、腐食したボデーパネルを低コストかつ短時間で再生できる、画期的な工法についてリポートする。
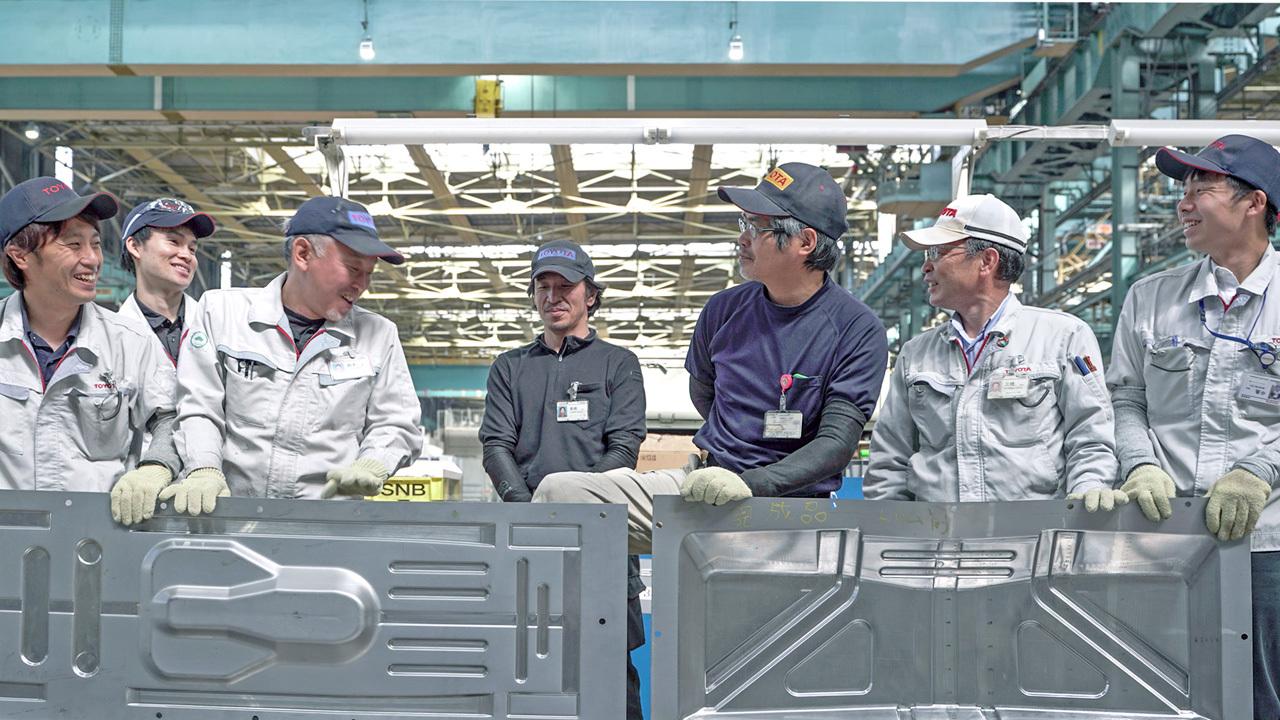
100年に一度の大変革期を迎えた自動車業界。トヨタ自動車ではあらゆる部門で前例のない画期的な取り組みがスタートしている。
そのひとつが2022年の春、社内の各生産工場から多彩な人材を集めて元町工場でスタートした「初代クラウン・レストア・プロジェクト」である。
トヨタイムズでは、その意義とレストアの現場をリポートしていく。第6回では、第4回で報告したボデーレストアで使われた金属加工技術「インクリメンタル成形」についてお伝えする。
画期的な技術でボデー部品をゼロからつくる
初代クラウンのボデーのレストア作業は、第4回でお伝えしたように、堤工場、田原工場、高岡工場、元町工場、開発試作部など、社内の各部署から集まった9名の精鋭メンバーの手で行われた。
ただ、ボデーや部品の状態、特にサビの進行は深刻なものだった。なかでも外からは見えないアンダーボデーと呼ばれるボデー下側、それもドア下部やホイールハウスなどはどうしても雨水が溜まる部分。特にフロアパネルやロッカーパネルの腐食は予想をはるかに超えていて、サビついた部分を切り取り、ゼロからつくるしかなかった。
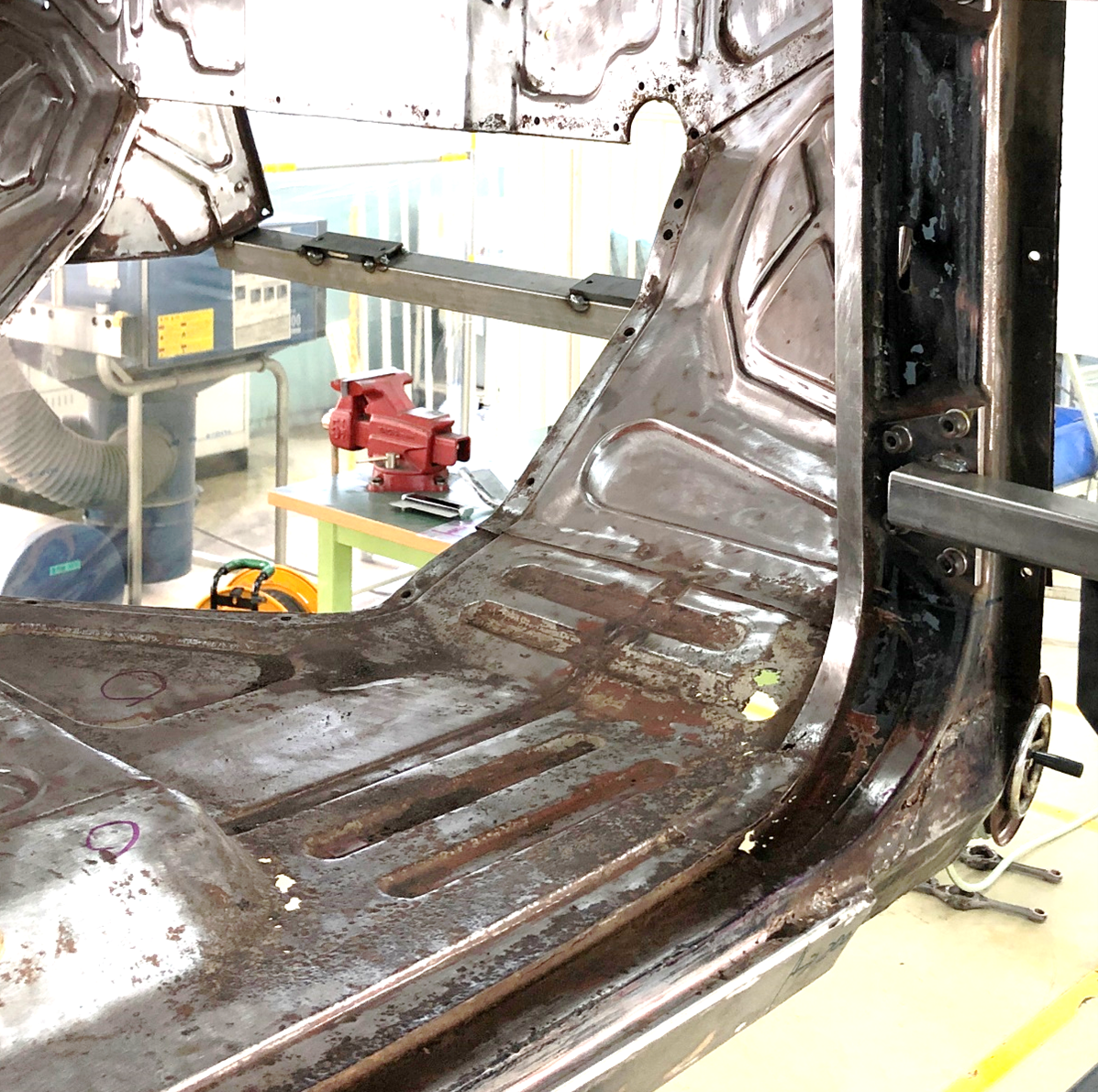
今回の初代クラウン・レストア・プロジェクトが「自動車メーカーとして当時のモノづくりの再現にこだわった(新車同然の)復元」を目指しているため、チームメンバーにとってそれは当然の選択であった。
ボデーパネルをゼロからつくる上での最大の障害が製造コストである。量産車と同様にプレス型を使ってボデーパネルをつくろうとすると、莫大な費用と時間がかかる。
「日本のクルマづくりを支える職人たち」第5回に登場した、ボデーパネル用の巨大なプレス金型の価格は1セットで数千万円にもなり、その製作と調整にも長い時間がかかる。だから何万台も生産する量産車のボデーパネルにしか採用できない。
また、昔ながらの手叩き板金によるボデーパネルの製作も、生産の現場には熟練の職人技を身に付けた「板金の達人」がいるから可能ではあるが、時間がかかる。
これらの問題を解決しなければ、このプロジェクトの目的の一つである、自動車メーカーだからこそ可能な、高い技能を駆使した低コストで高品質なレストアは実現できない。
パブリカのレストア時から注目していた工法
初代クラウン・レストア・プロジェクトを立案したプロジェクトメンバーは、当初からこの課題について認識していたため、本プロジェクトがスタートする以前から課題の解決法について、社内外でリサーチを重ねていた。
その結果、社内のモビリティツーリング部ですでに導入されていた「インクリメンタル成形」という手法に出合った。パブリカのレストア時から注目していた工法である。
2022年4月にスタートした初代クラウン・レストア・プロジェクト。ネジ1本に至るまでクルマの分解作業が進んだ6月、特にサビと腐食がひどいことが判明したのが、前述した通りフロアパネルとロッカーパネルだ。
少なくともこの2つのパネルは、何らかの方法でゼロからつくるしかない。そこでモビリティツーリング部の佐藤正則SX、高橋将志EX、さらに担当技術員の高山滉平に、インクリメンタル成形によるフロアパネルの製作を相談した。
佐藤は、もともとはプレス型補正 (溶接、精度修理、品質調整)のスペシャリスト。人財育成に関わりながら、自らも新たな挑戦を続け、さまざまな技能を持ち合わせていることから、インクリメンタル成形の人材として抜擢された。インクリメンタル成形についても今年で12年目になるベテランだ。
「依頼が来ても断らないこと。加工できそうにない形状でも、相手に寄り添って、一緒に考えること」を大切にして仕事をしてきた。
高橋も、これまで試作部品製作(板金、溶接。レーザー)、型補正、パネル面検査を担当するなど、さまざまな技能を有している。第35回技能五輪全国大会で金メダル(曲げ板金)を取るなど、輝かしい経歴の持ち主だ。
仕事では、まず事前の検討をしっかり行うことで、後戻りを極力なくし、効率よく業務をこなすことを意識してきたという。
モノづくりの現場で注目されるインクリメンタル成形とは
高山
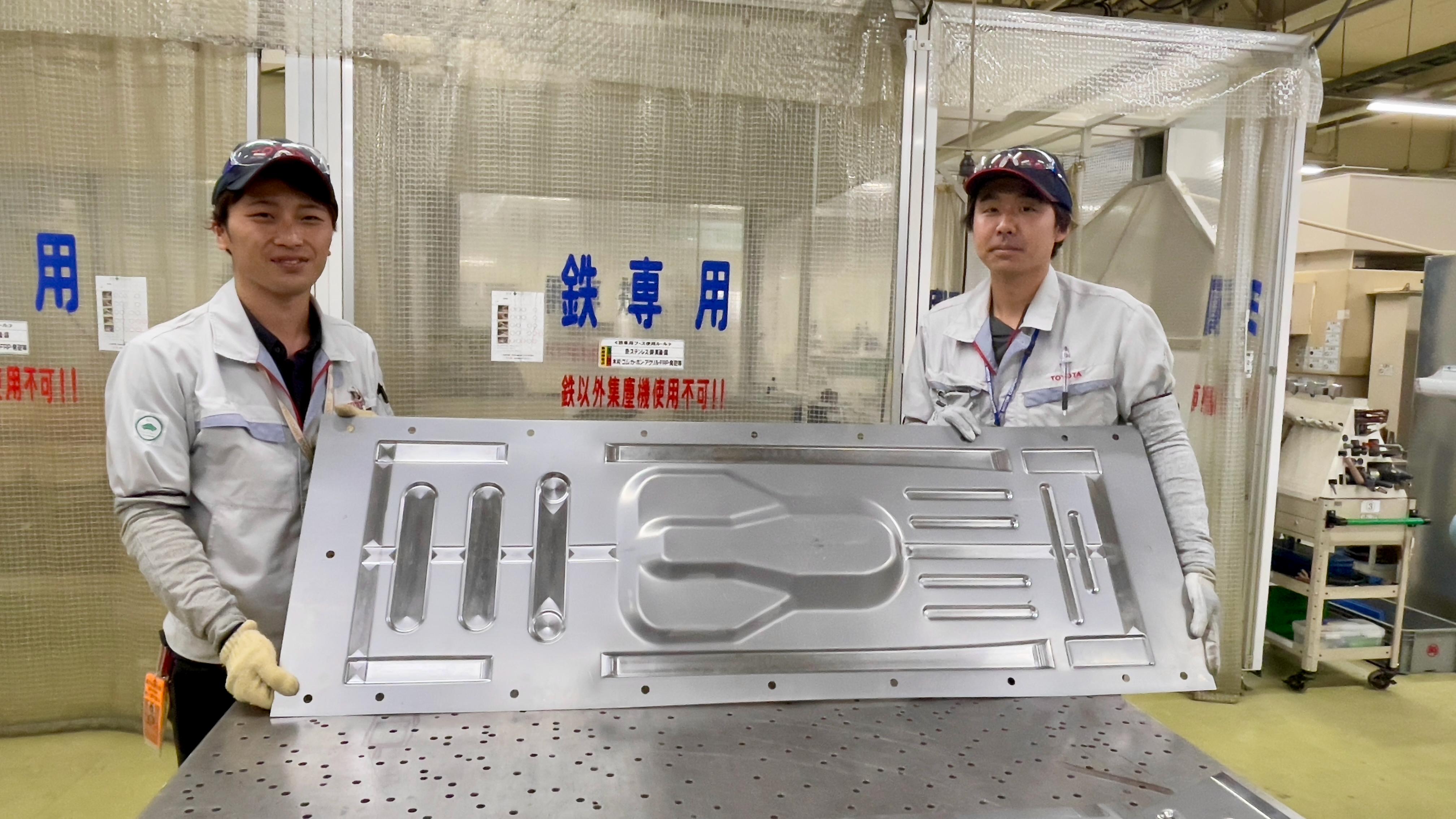
インクリメンタル成形は、金属の薄板の一部に棒状の工具を押し当てながら動かしていくことで、金属の薄板を狙った形状に加工する技術です。削るのではなく、力を加えて材料を徐々に変形させて加工します。
具体的には、金属の平板を加工機にセットして、棒状の工具をコンピューターで数値制御しながら平板に力を加えることで変形させます。
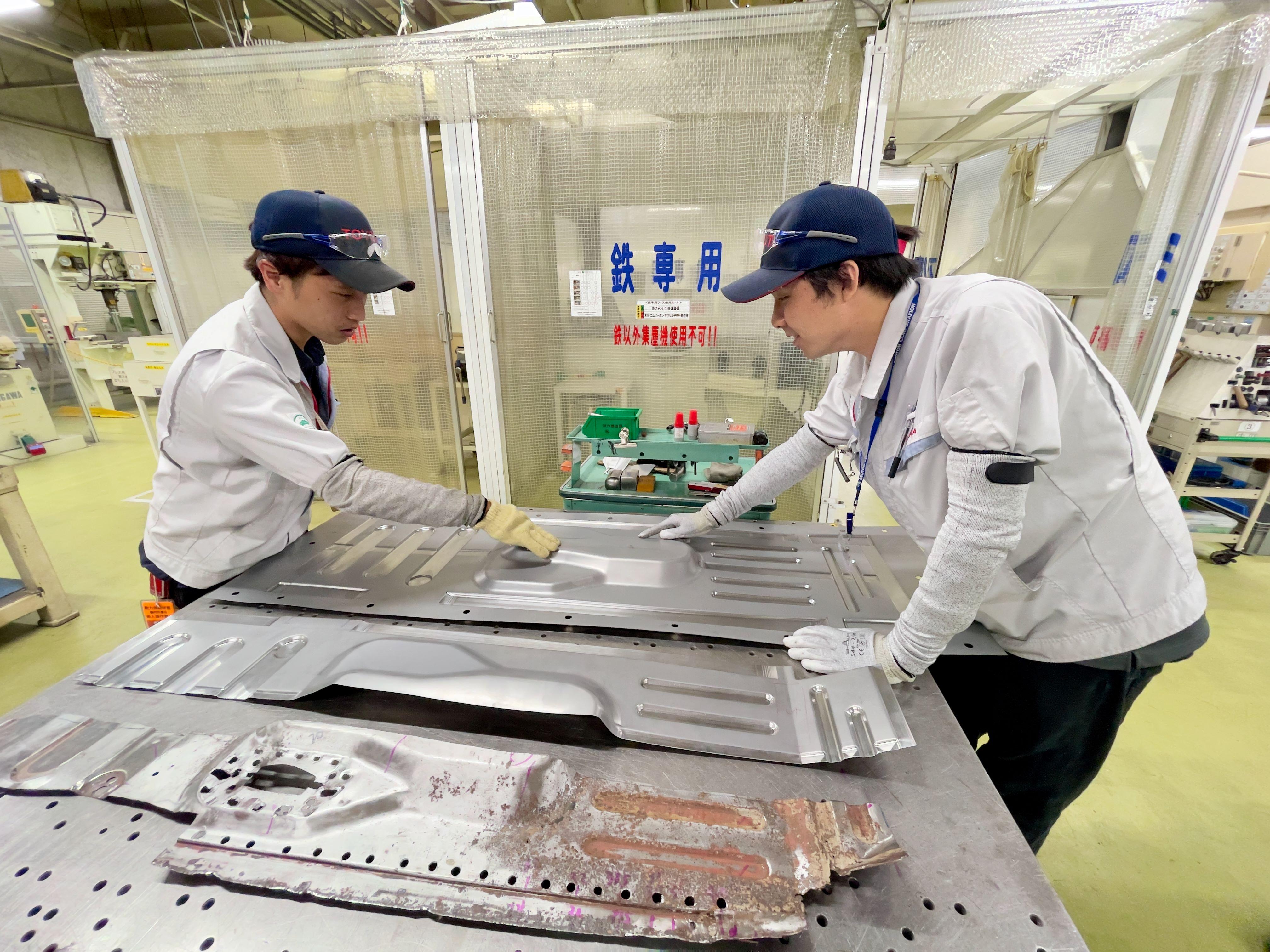
高山の所属するモビリティ―ツーリング部ではすでに2012年から、この技術を「iQ GRMN SuperCharger」のドアに、文字を立体的に加工し表現するために導入していた。
金型不要で加工コストが大幅に削減できるうえに、開発期間が短縮できるインクリメンタル成形は、低コストで多品種少量生産ができる塑性加工技術として、近年、自動車業界に限らず注目されている技術だ。自動車業界でも各社が技術開発にしのぎを削っている。
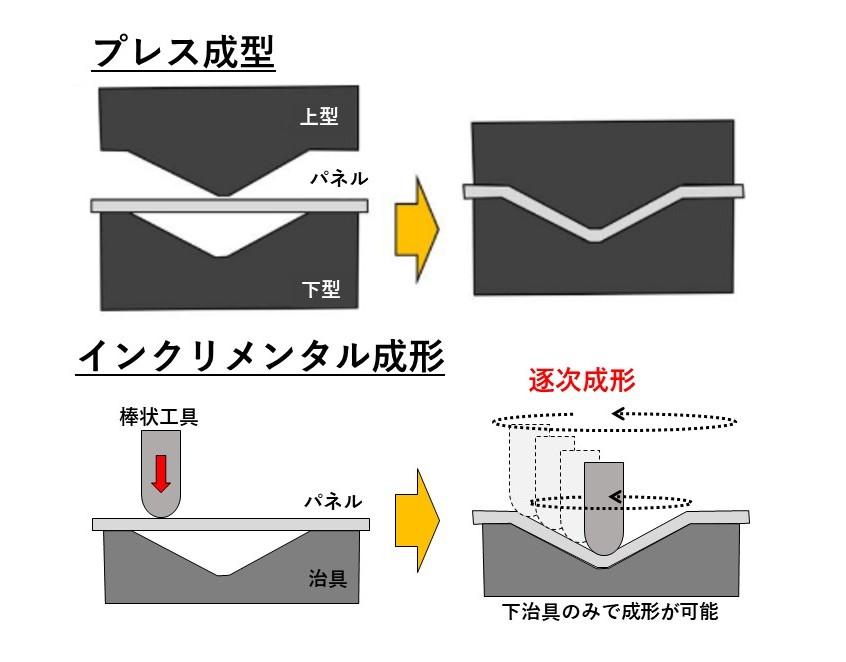
同じボデーパーツについて、型を使って手叩き板金でつくる場合は、1枚ごとに熟練の板金職人が何日もかけて製作する必要がある。
しかし、数値制御による自動加工機で行うインクリメンタル成形ならば、いちど加工データを作製してしまえば、必要になったときにスイッチ一つで、つくることができる。だから、補給パーツなどの製造にも最適だ。
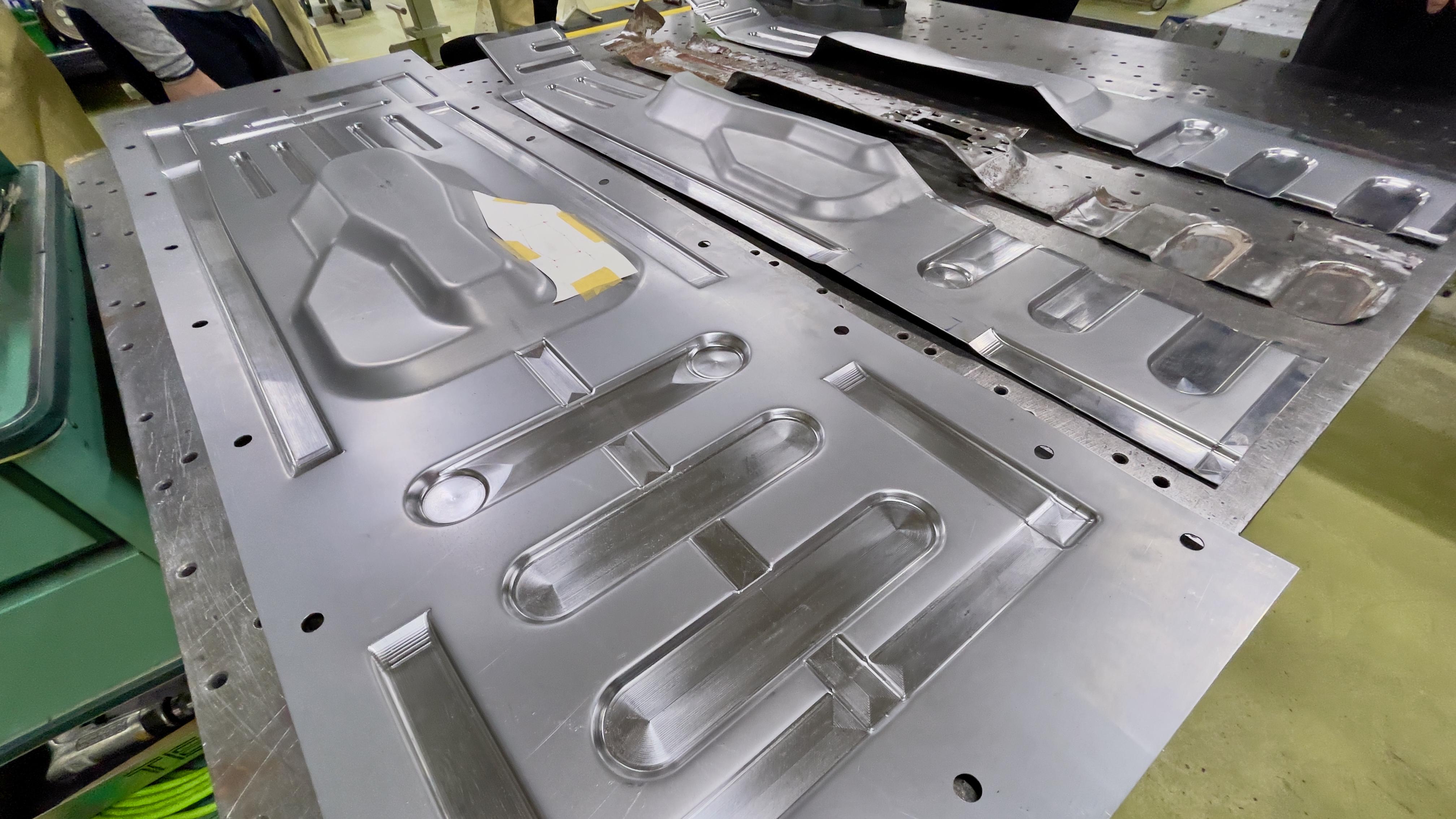