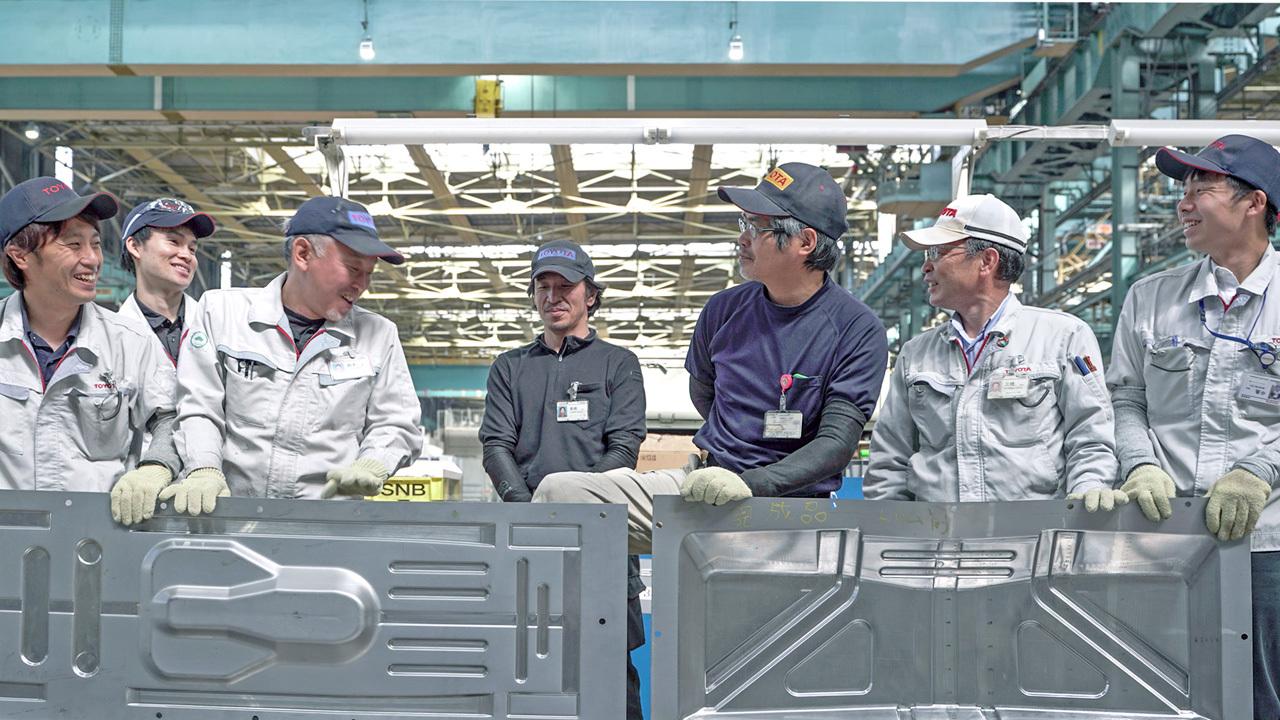
自動車業界が大変革期にある今、トヨタの原点に立ち返るべく始まった「初代クラウン・レストア・プロジェクト」。第6回では、腐食したボデーパネルを低コストかつ短時間で再生できる、画期的な工法についてリポートする。
困難を極めた「成形データ」の作成
とはいえ、インクリメンタル成形によるボデーパネル製作は簡単ではなかった。コンピュータで制御する自動加工機には、どこをどのような形状にするかを指示する3D-CAD設計ソフトでつくられた加工データが必要だ。このデータ作成が困難だったのだ。
佐藤SX、高橋EX、高山の3人は、初代クラウンのボデーとその構成部品であるボデーパネルがどのような構造なのかを、まず徹底的に調べることにした。
佐藤SX
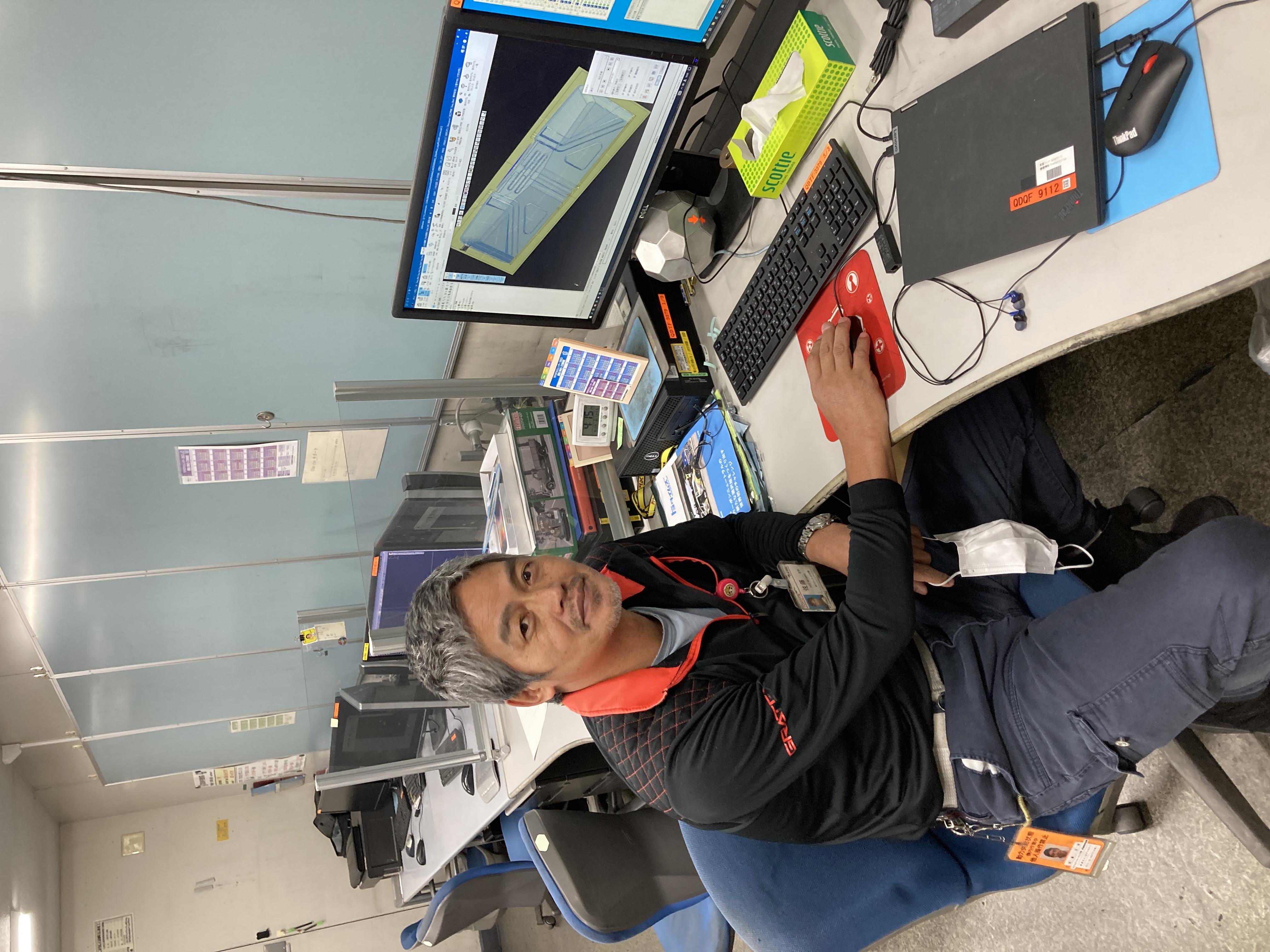
調べてみると、ボデーをつくった先人の知恵や技術、こだわりのモノづくりを感じ、感動しました。
いくつもの部品をつないでつくっているのに、溶接と仕上げが素晴らしいので、まったくつなぎ目が分からない。
アンダーボデーの構造も今とは全然違います。今は一体になっている部品が多いのですが、昔は多くの部品を組み合わせてつくっていたので、工程数も多かったでしょう。でも、その工程をどう効率良く進めるか、よく考えられていたことも分かりました。
高橋EX
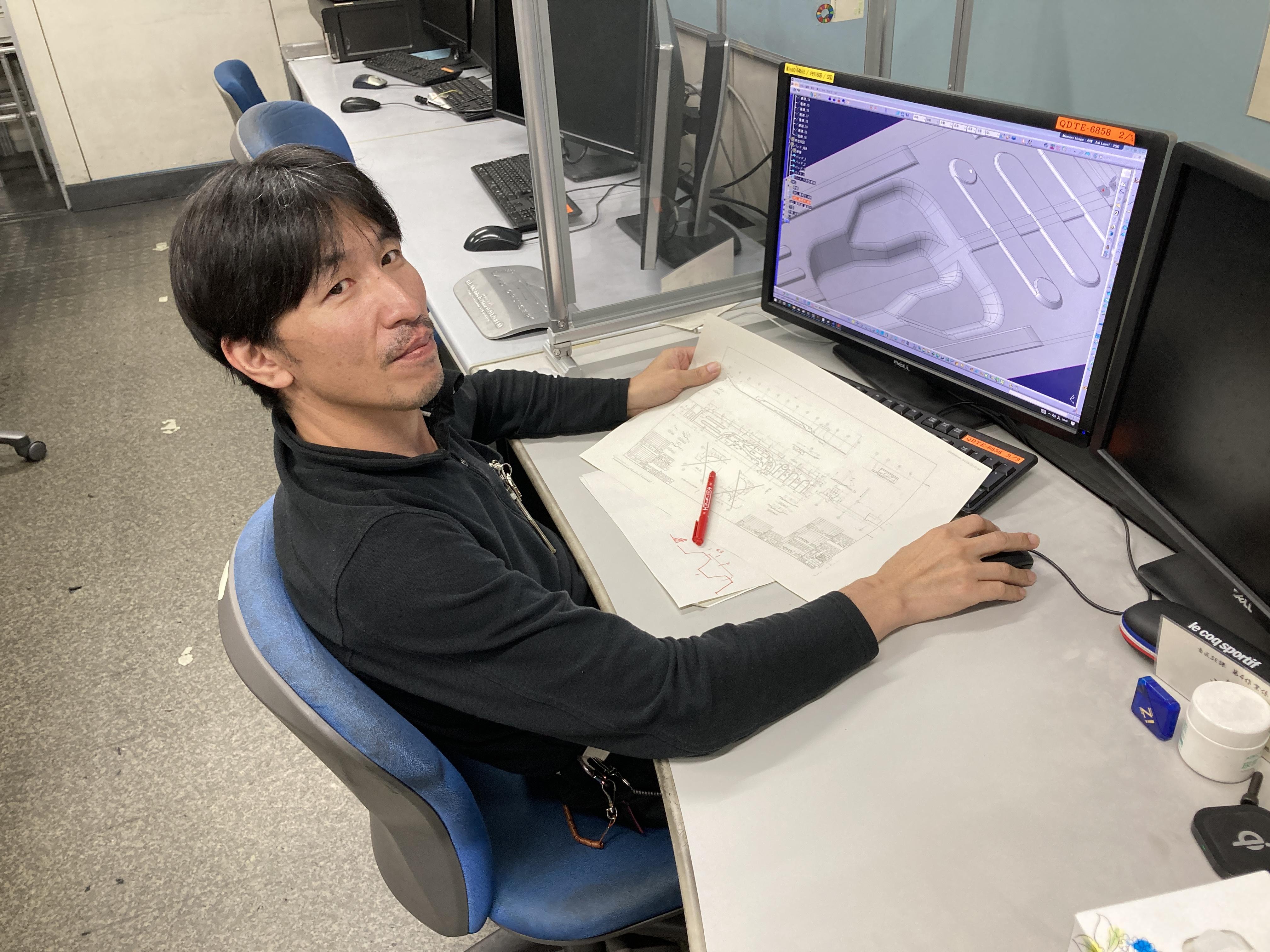
加工データの作成を、最初はリバースエンジニアリングで行おうとしました。つまり、レストアする初代クラウンのパネルを測定器で実測して、その形状をデータ化してみたのです。
ところがパネルがボロボロなので、正確な測定ができない。データの精度が悪かったのです。
そのため、当時の図面を読み解いて、一からデータ化することになりました。図面から製品を製作するのは、若い頃に参加した技能五輪の経験から、さほど苦ではありませんでした。何しろ、図面を読み解くのはモノづくりの基本ですから。
とはいえ、当時の図面はもちろん手書き。しかも何度も修正が加えられていたので、読み解くのにはかなり苦労したという。
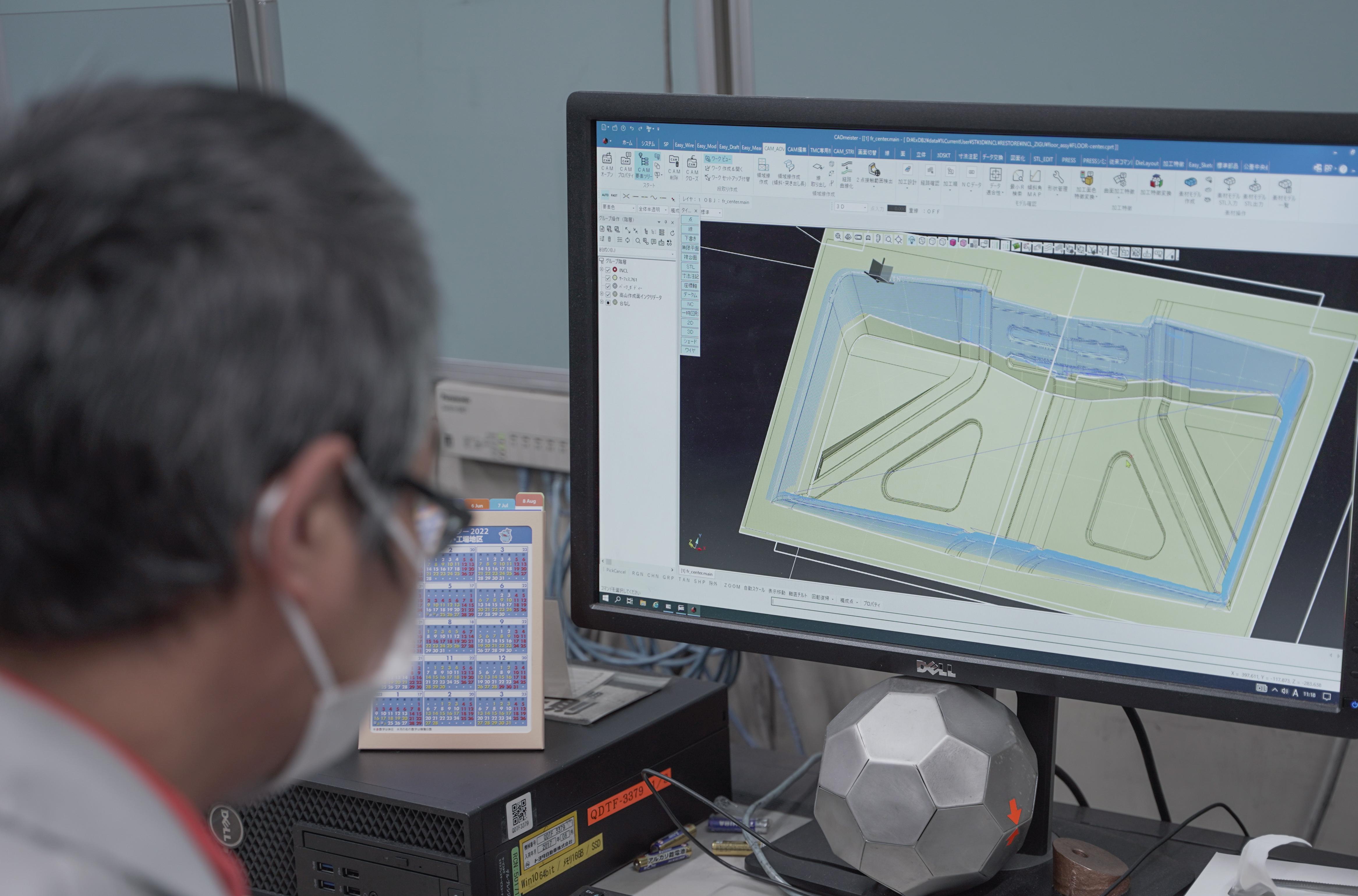
実は3人にとって、大きな1枚の金属板から複雑な形状のパネルをつくり出すのは、今回が初めての挑戦だった。
成形する量がかなり多いため、加工中にパネルが割れたりシワができたりすることが何度も起きたという。
そのたびに3人は、なぜ不具合が発生したのか、部位ごとに問題を整理し、プレス加工の補正と板金加工、ふたつの経験で培ったノウハウを活かして、加工データを変更して、トライ&エラーを繰り返しながらボデーパネルの製作を続けた。
さらに、小さなパーツを別々につくるのではなく、一枚の金属板の中に2つのパーツを一緒にしてつくり込むことで効率化を図るなどの工夫も今回、初めて行った。
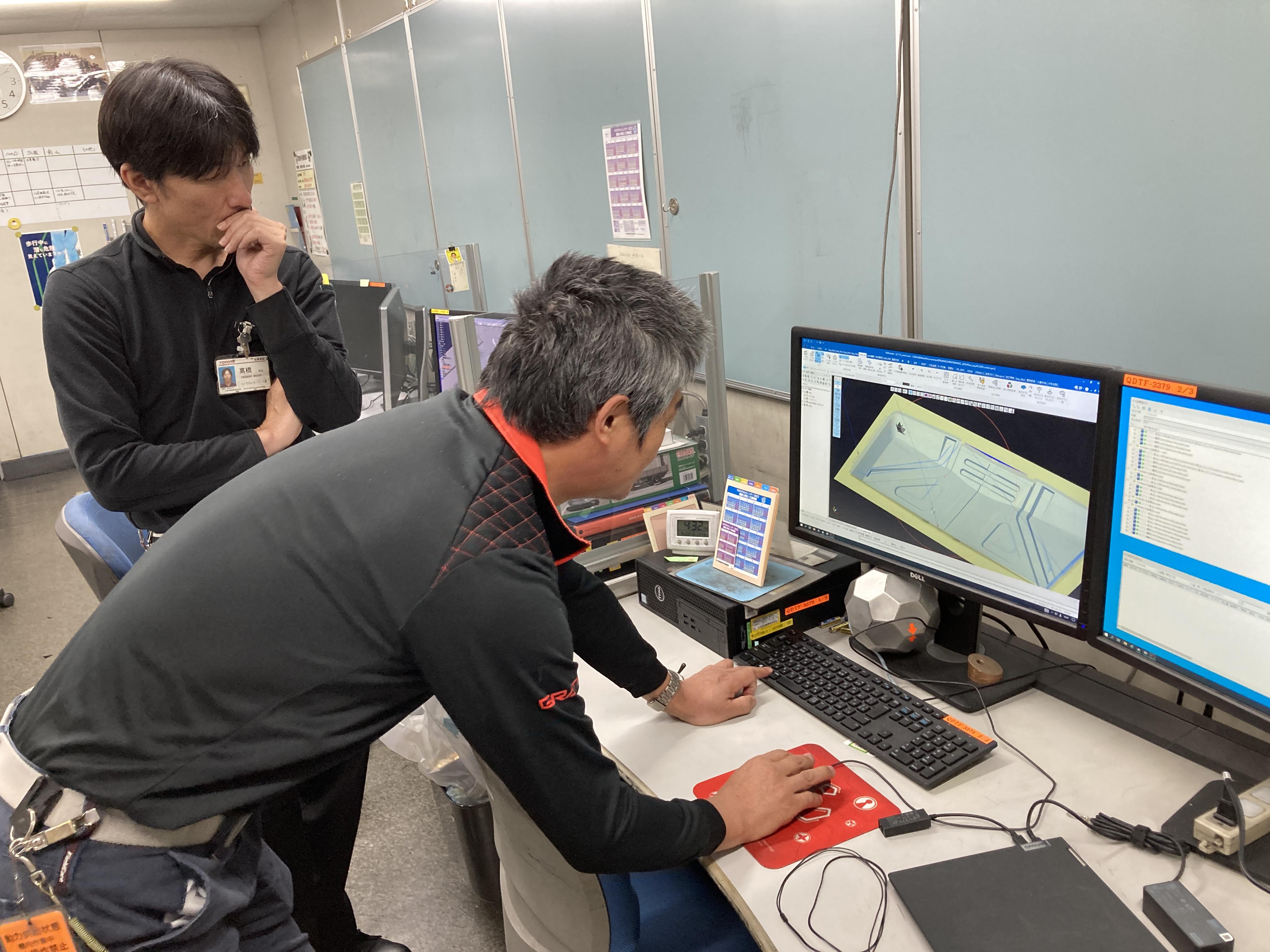
最新技術×古いクルマ=未来のクルマづくり
高山はモビリティツーリング部でこの技術を手掛けて3年目。それ以前はプレス加工を担当する「プレス屋」だった。
高山、そして彼をサポートした佐藤、高橋も、今はこの技術に無限の可能性を感じているという。
高山
プレス加工とは違って型がないので、加工データを変更することで、何回でも部品の修正ができます。
問題点が分かったら、ボール工具の軌道(パス)を修正してまた加工すればいい。これもインクリメンタル成形の特長です。
パスをつくる場合にはどこをどのくらい叩くのか、ベテランの板金職人のノウハウをフィードバックしています。
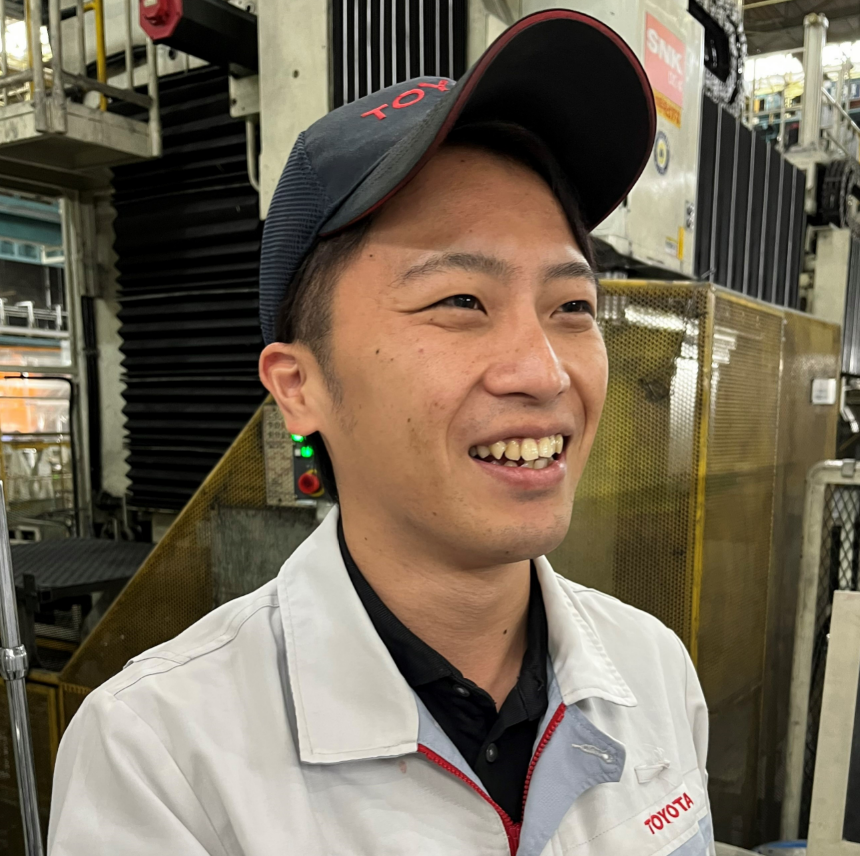
また、関係会社や仕入先様では古い型を補給部品生産のために何年も残し続けているという課題があり、インクリメンタル成形でその課題を解決できないかを検討しています。
今のインクリメンタル成形では下型(に相当する治具)が必要なのですが、この治具を汎用化すれば、もっとコストを下げることができます。
トヨタ社内でレクサスやGRなどを中心に、新型車の生産に用いられているインクルメンタル成形。これまでは鉄やアルミなどの金属材料の加工に使われてきた。
だが社内では世界で初めて、この技術を樹脂部品に適用する取り組みも進んでいる。その一例が「レクサスLC 特別仕様車 “EDGE”」のFRバンパーカナードだ。
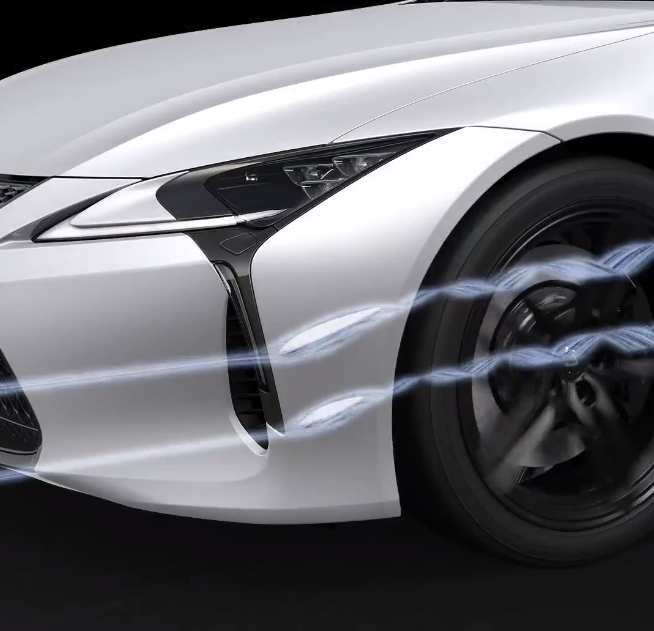
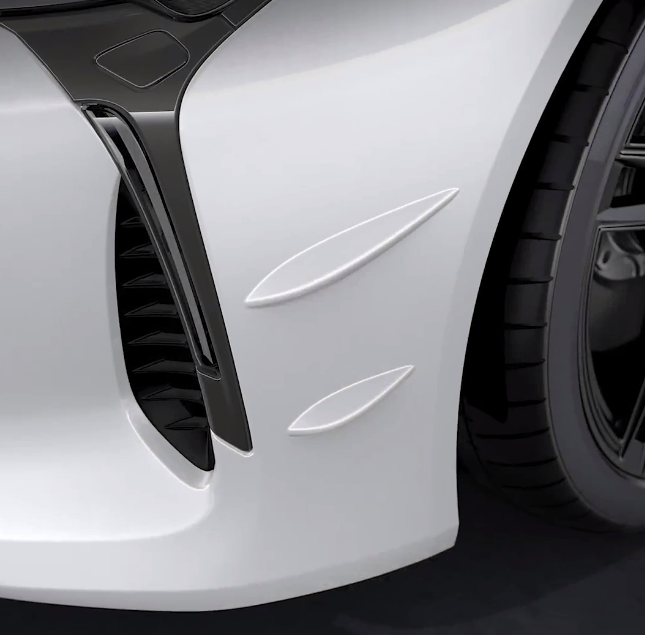
高山
樹脂部品へのインクリメンタル成形の適用は、これからのクルマづくりを変えられると思っています。既存のバンパーのような樹脂部品に対して、低コストでデザインを変更することができます。
将来的には、お客様が自分の嗜好に合わせて、多くの選択肢の中から自由にデザインを選択できるような新しい価値を提供していきたいです
今後も技能・技術を磨き、一人でも多くのお客様の笑顔につなげていきたいです。
トヨタの原点ともいえる初代クラウン。そのボデーパネル製作におけるインクリメンタル成形の採用は、初代クラウン・レストア・プロジェクトが、単なる旧車のレストアではなく、クルマづくり、クルマ社会の新しい未来を創る取り組みであることを示す何よりのエピソードだ。
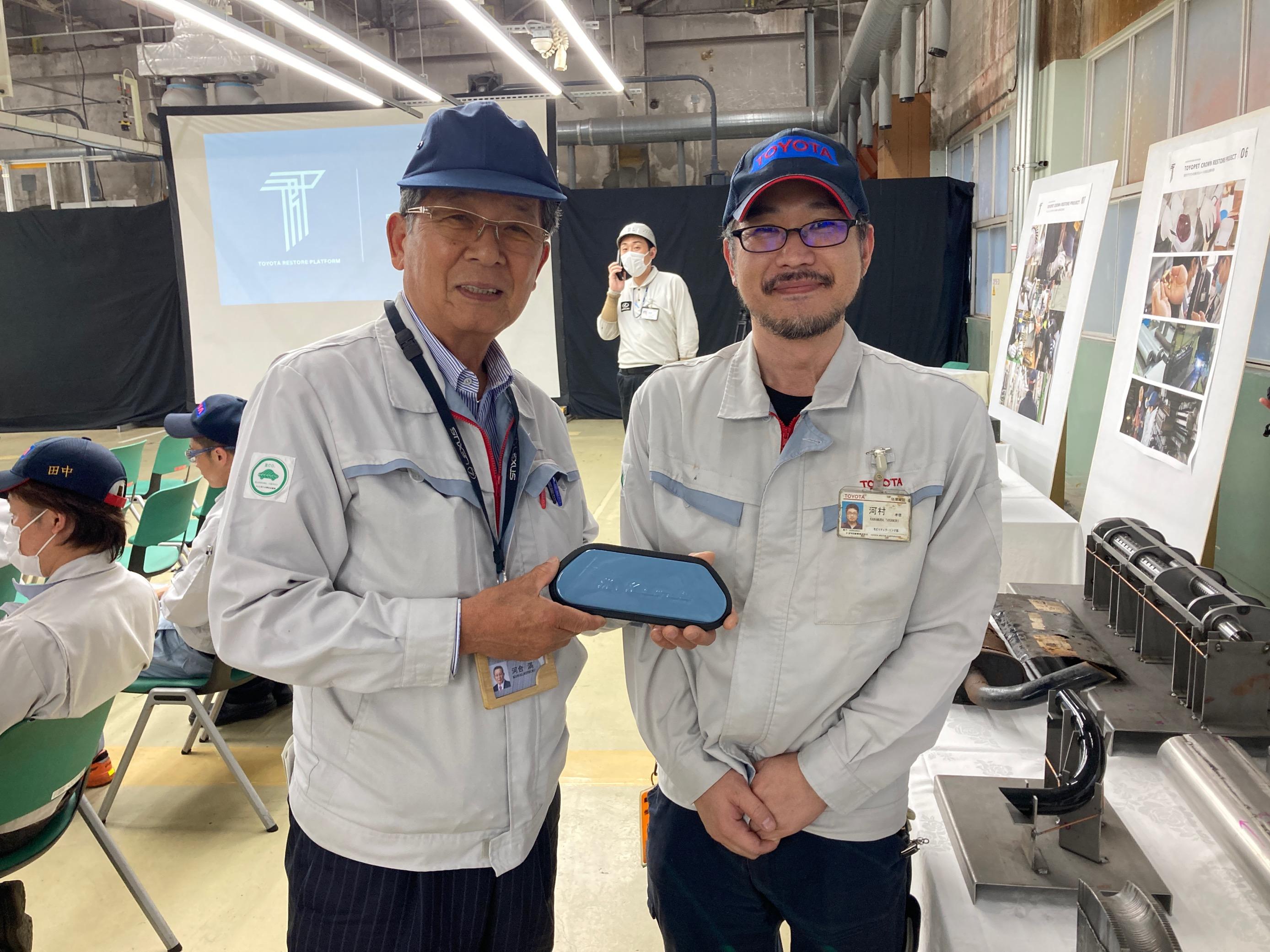
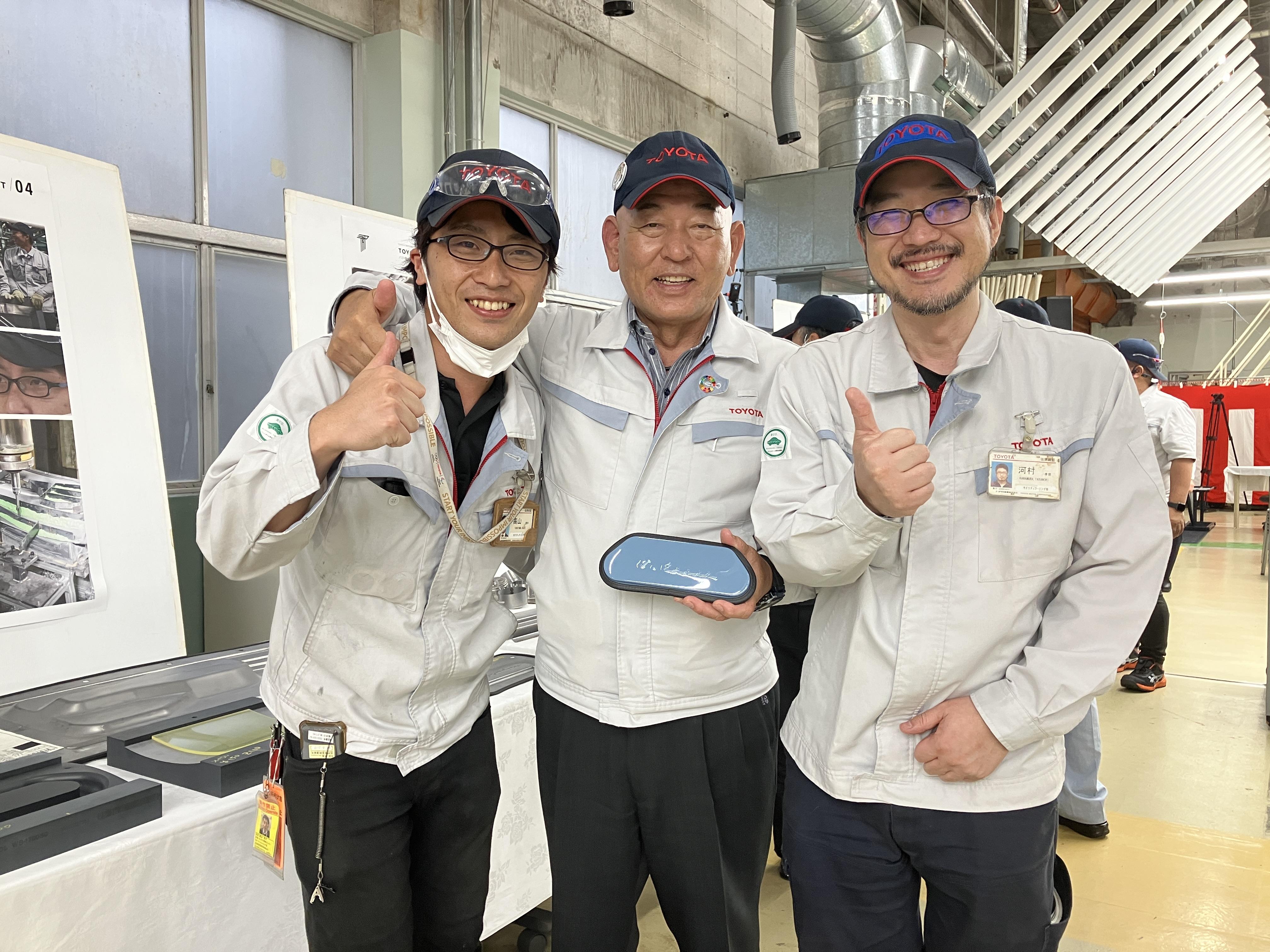
次回第7回では、鋳造におけるモノづくりのDNAの継承と若手の活躍についてお伝えする。
(文・渋谷康人)