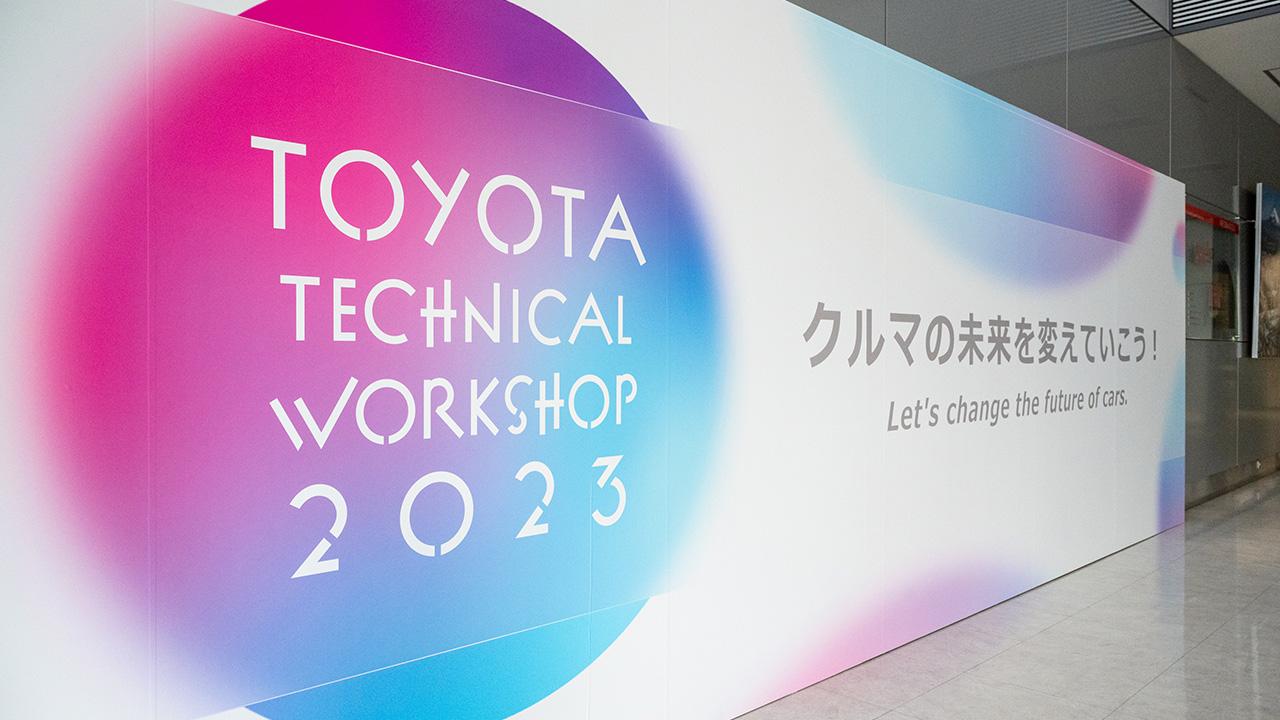
航続距離1,000kmを可能にする電池と電費改善、燃費・寿命・コストの3拍子そろったFCシステム――。トヨタが近い将来に導入を目指す次世代技術を公開した。
〈水素〉30年の開発の蓄積が次の燃料電池をつくる
水素については、これまで断続的に取り組みが紹介されてきた。
今回、水素ファクトリーの山形プレジデントは、開発、生産、販売まで一丸となって事業化を進めていく姿勢を打ち出し、「しっかりと数をまとめて、アフォーダブル(手頃)な商品を提供していく」と語った。
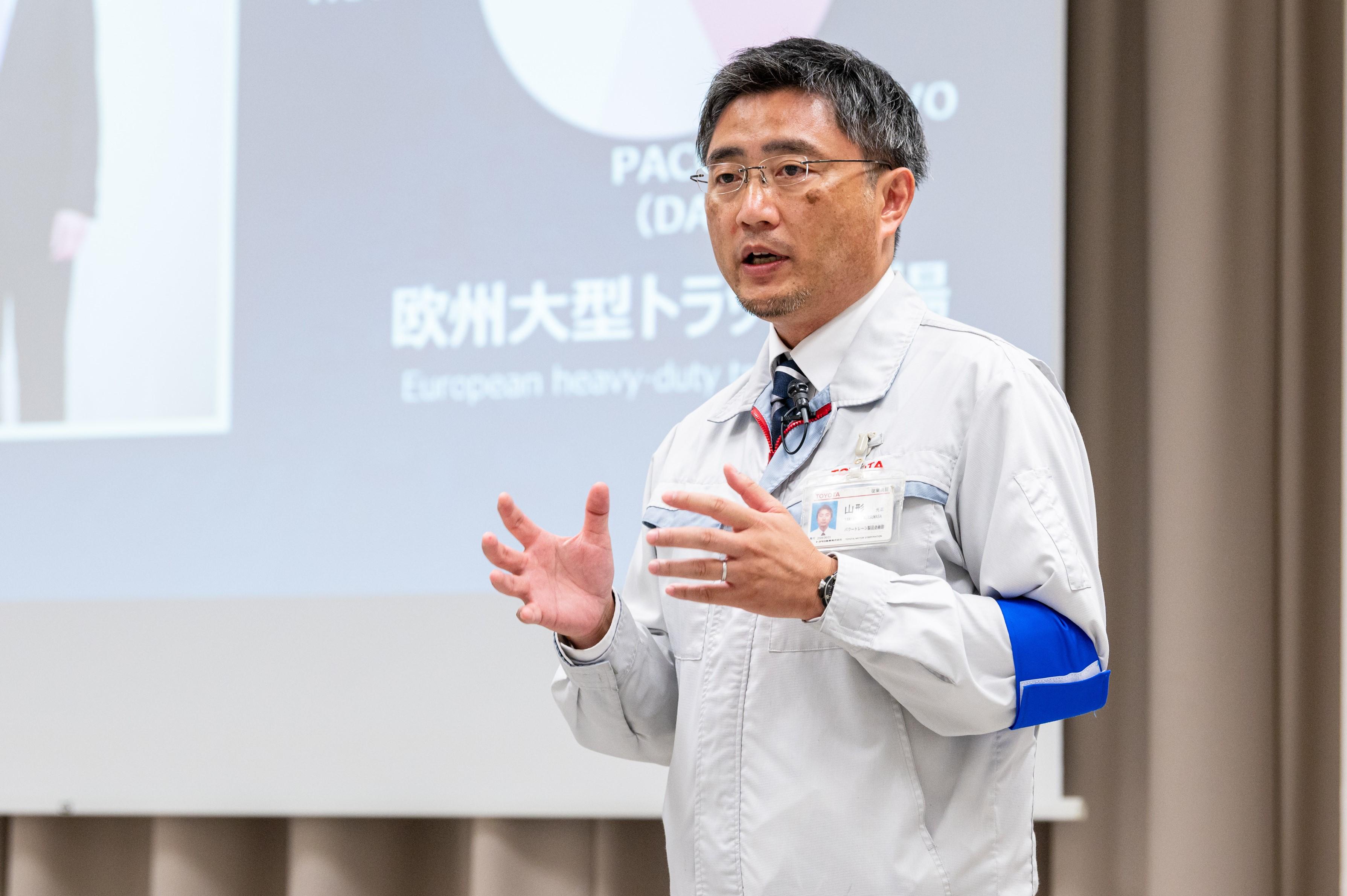
また山形プレジデントは、2030年に10万台分の燃料電池のオファーがトヨタに寄せられていることを説明し、燃料電池市場が商用車を中心に拡大していくビジョンも示した。
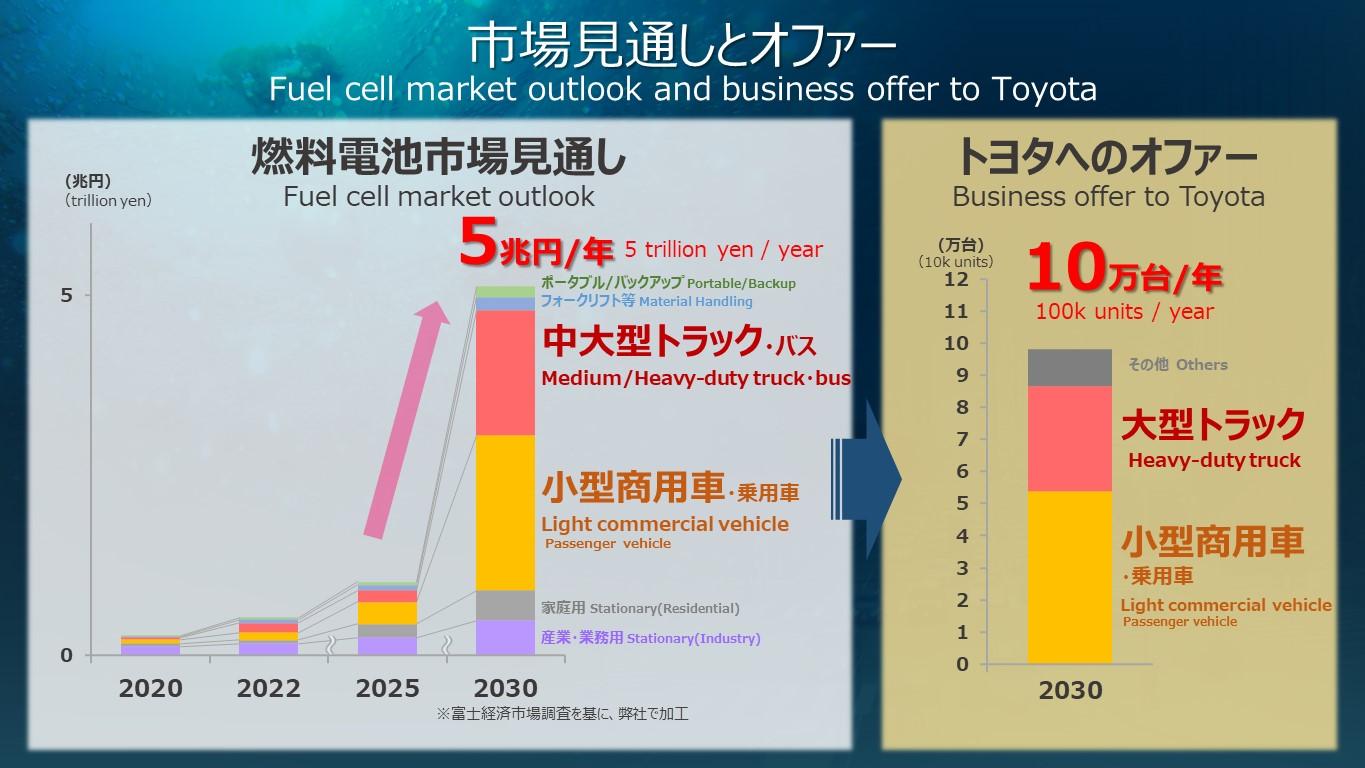
しかしながら、水素を使った燃料電池ユニットも、水素そのものも、まだまだ高額。
大型商用車などでの普及を進めていくため、展示エリアでは、商用に応える走行と燃費性能を向上させる次世代FC(Fuel Cell:燃料電池)システムや車載タンクの製造コストを抑える取り組みなどを紹介。水素の製造技術などについても解説された。
〈水素〉商用に応える次世代FCシステム
燃料電池は、酸素と水素を化学反応させて発電させる「セル」と呼ばれる薄い板状の回路を重ね合わせたスタック構造によって構成されている。
今回の展示では、発電量が現行の130%となる次世代のセルが披露された。
耐久性では、メンテナンスが必要になるまでの期間が従来のディーゼル車よりも2.5倍長くなり、クルマの寿命を考慮した場合、ほぼメンテナンスフリーとなった。
また、現行のセルに比べ、スタックを構成するコストは半分、航続距離は20%伸び、東京―大阪間であれば、途中で充填しなくて済むように改善されている。
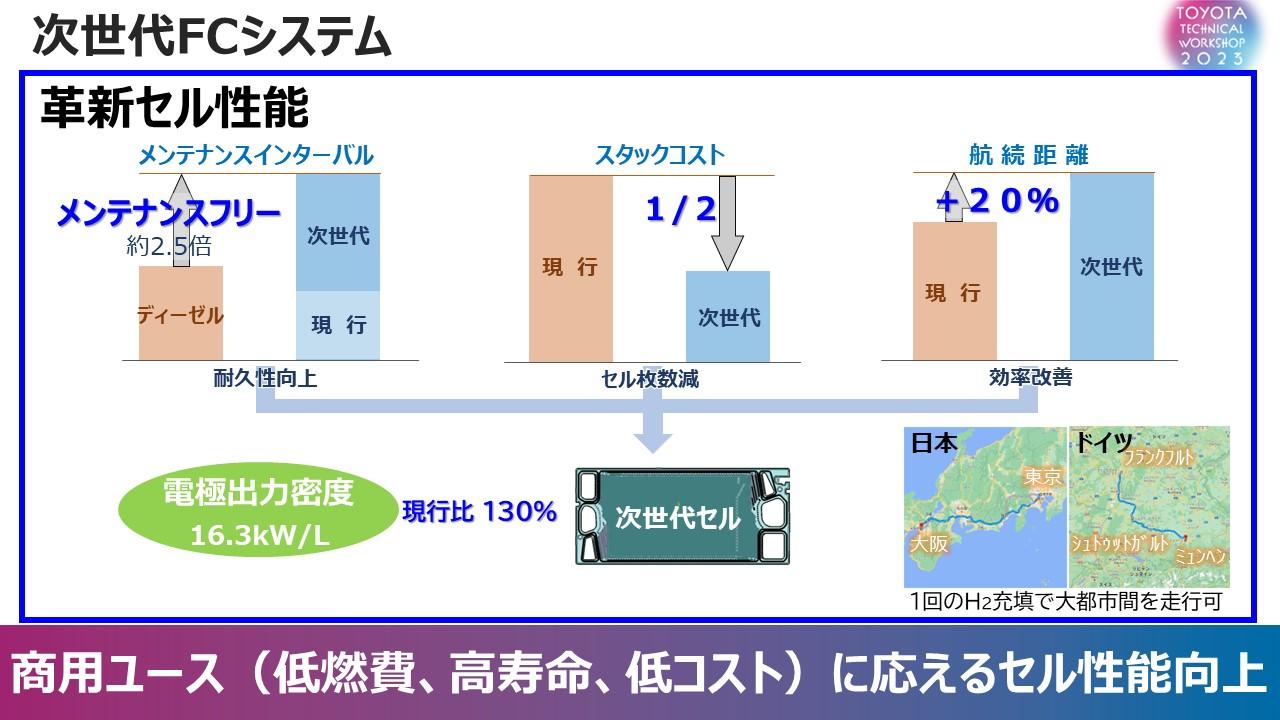
この次世代セルには、トヨタが積み上げてきた30年の知見が反映されている。
セル内部で起こっている現象をリアルタイムで計測・解析。ナノスケールで化学反応をシミュレーションする予測。そして、化学反応を起こすための触媒の精密な塗工。
高度な技術力により、腐食などによる劣化を遅らせ、製造に必要な材料も安価となった。高い競争力を持った次世代セルは、2026年の実装が予定されている。
〈水素〉クルマづくりの技術で水素を「つくる」
次世代FCシステムの性能を向上させつつ、水素そのもののコストを削減する取り組みも紹介された。
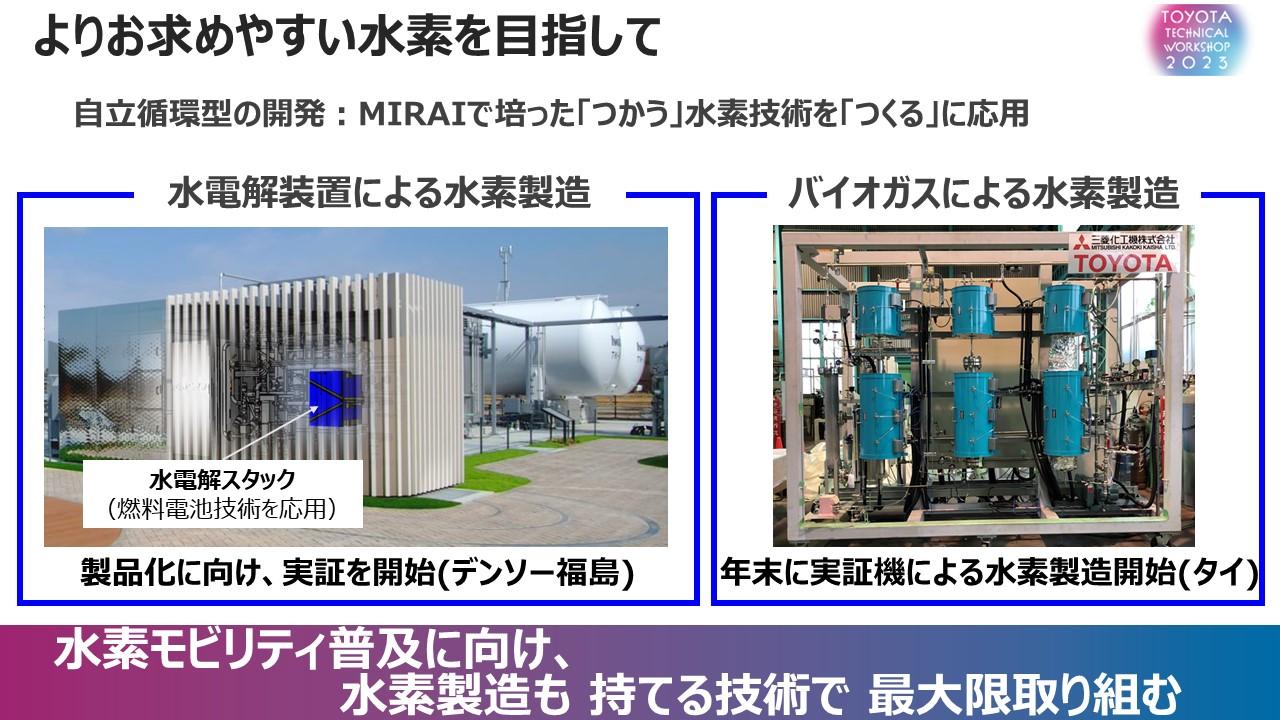
デンソー福島で3月に公開された水電解装置では、MIRAIの燃料電池技術が応用されている。
水素と酸素を化学反応させて発電するMIRAIの電池と、水を電気分解して水素をつくる装置では、セルに使用している部品の9割が同じで水素製造にも本気で取り組んでいる姿勢を示した。
また、タイの鶏糞から発生したバイオガスを使う水素製造では、三菱化工機と共同開発した実証機を将来的にタイに持ち込み、現地での製造・消費へ検討が進んでいることが報告された。
〈水素〉乗用も見据えタンク異形化
大型商用車に水素を搭載するためのタンク。従来は直径約50cm、長さ約2mの円筒形で、カーボン繊維などを素材とするものが使われている。
このタンクを1種類に規格化することで、タンクにかかるコストが25%削減し、普及を加速できることや、気体の水素を液体にすることで体積を減らし、荷室を広く確保できることなどが説明された。
水素ファクトリーでChief Project Leaderを務めることになる濱村芳彦統括部長(水素事業領域)は、タンクの形状について、佐藤恒治社長から「なぜ丸くないといけないのか?」と聞かれたエピソードも紹介。
「佐藤社長も技術屋。答えは分かっている。分かっていて聞いている。なので、売り言葉に買い言葉じゃないが『いや(丸くなくても)できますよ』と」
そこで披露されたのが、開発中の鞍(くら)型と平型のタンク。タンクの異形化により、既存のクルマへの展開やデザインの自由度につなげていく。
また、次世代FCシステムのセルもハーフサイズで開発が検討され、小型から大型まで、搭載車種にとらわれず展開することを視野に入れていると示された。
社内にも向けられたテーマ
BEV、水素を中心に、トヨタの盛りだくさんの技術を発信したテクニカル・ワークショップ。メディアをはじめとするステークホルダーへの理解活動という目的に加え、もう一つ、社内に向けられたメッセージもあった。
エンジニア出身の中嶋副社長はこう語る。
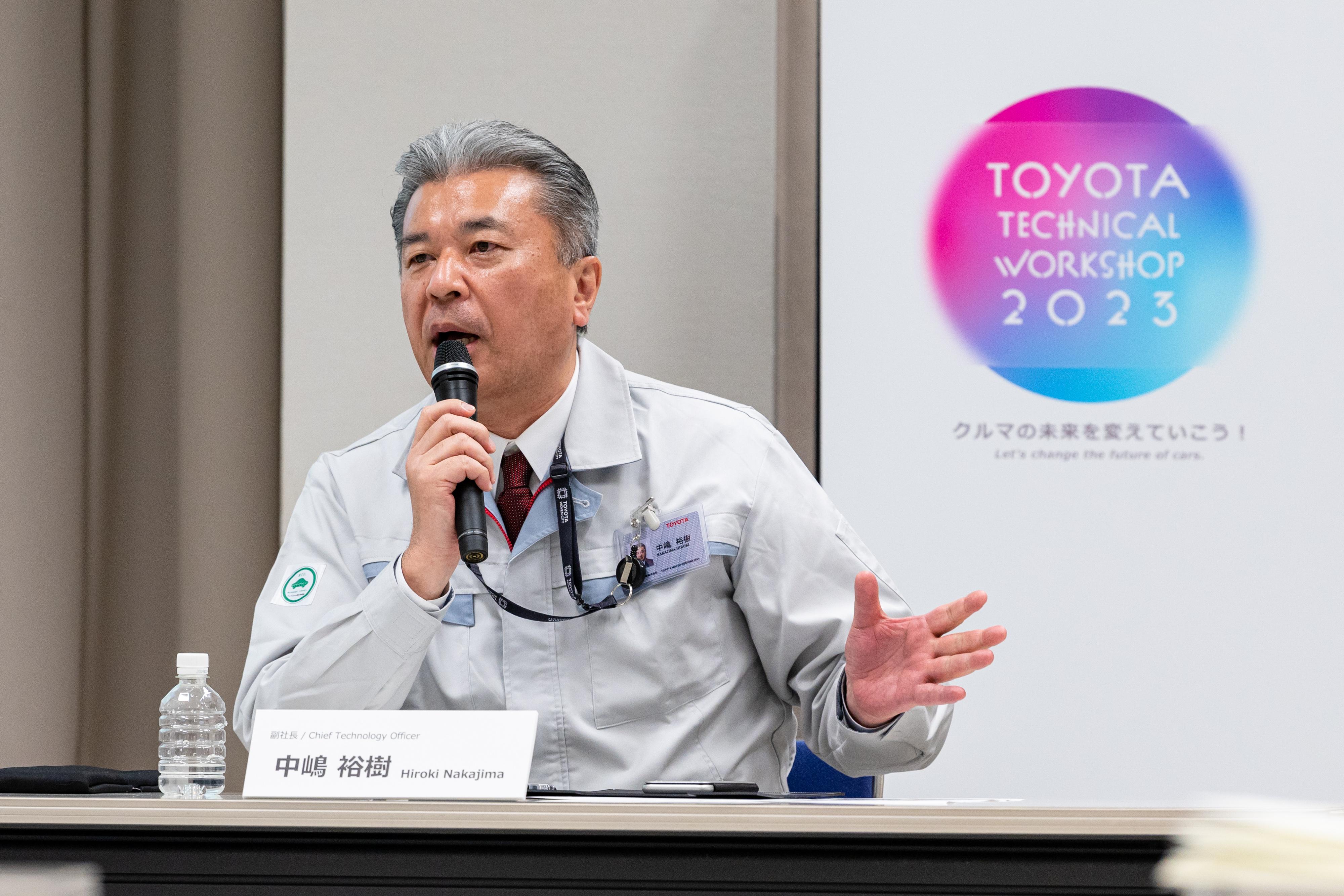
「技術者が自ら、話して伝える経験をすることによって、既に世の中に発している『クルマの未来を変えていく』というテーマに、自分がどう働きかけていくか考えるきっかけになると思う」
エンジニアが研究の成果を自ら伝え、世間のフィルターを通し、客観視する。それを通じて、お客様のニーズを知り、さらなる研究・開発につなげていく。
技術開発の現場で、「もっといいクルマづくり」のサイクルをさらに回していく。