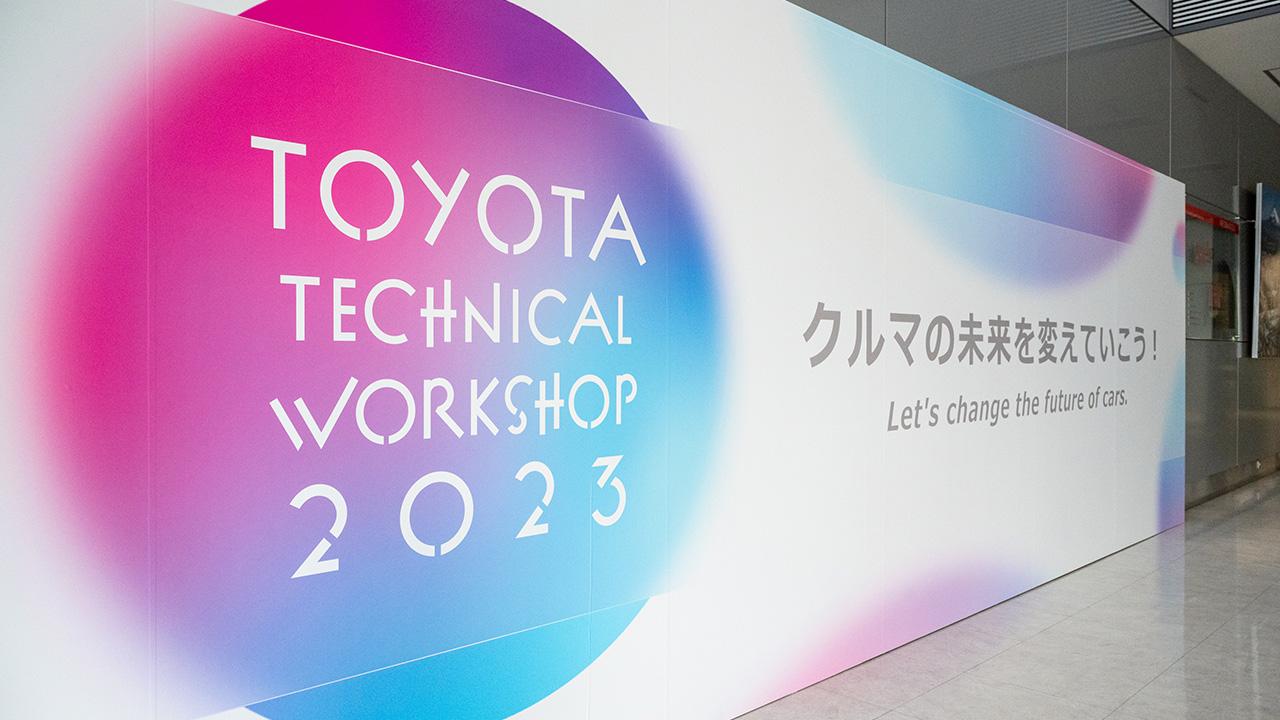
航続距離1,000kmを可能にする電池と電費改善、燃費・寿命・コストの3拍子そろったFCシステム――。トヨタが近い将来に導入を目指す次世代技術を公開した。
〈BEV〉2030年 350万台を裏付ける次世代電池
BEVファクトリー発足後、はじめて公の場に立った加藤プレジデントは「BEVで未来を変える。クルマ・モノづくり・仕事の仕方を変え、トヨタの未来の発展につなげる」と宣言した。
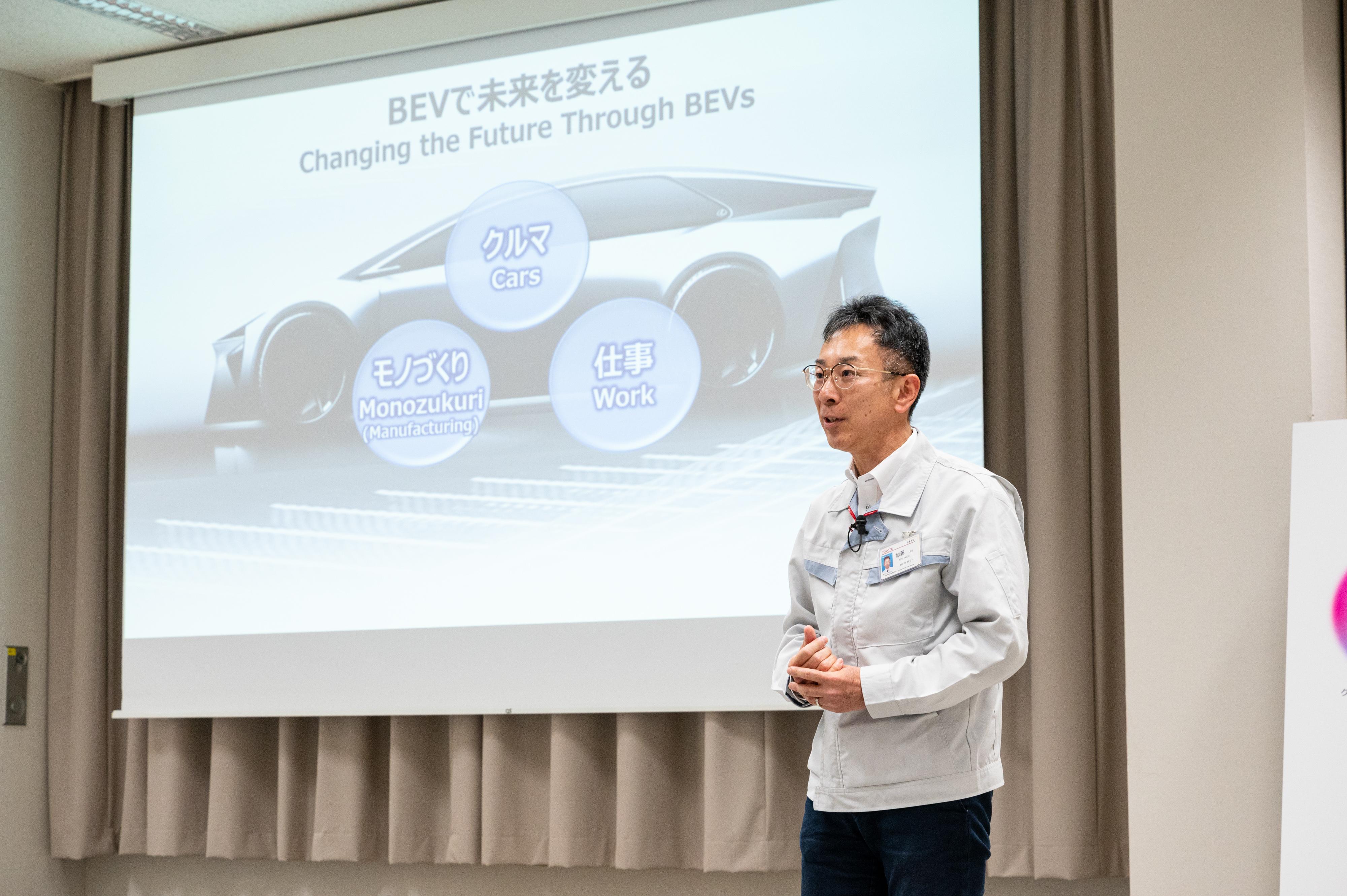
この場で示したのが、同組織から2026年に最初の次世代BEV * を市場に投入すること、そして、350万台のBEV販売を見据える2030年には、170万台を次世代BEVが占めるという見通しだということ。
*電池やプラットフォーム、クルマのつくり方など、すべてをBEV最適で考えたBEV。電池を極限まで使い、電費改善も組み合わせて航続距離を1,000kmに。さらに心揺さぶる走りとデザインを兼ね備えたモデルでレクサスブランドから投入する
その次世代BEVへの搭載を見据える2つのリチウムイオン次世代電池が、今回初公開されたパフォーマンス版、普及版だ。
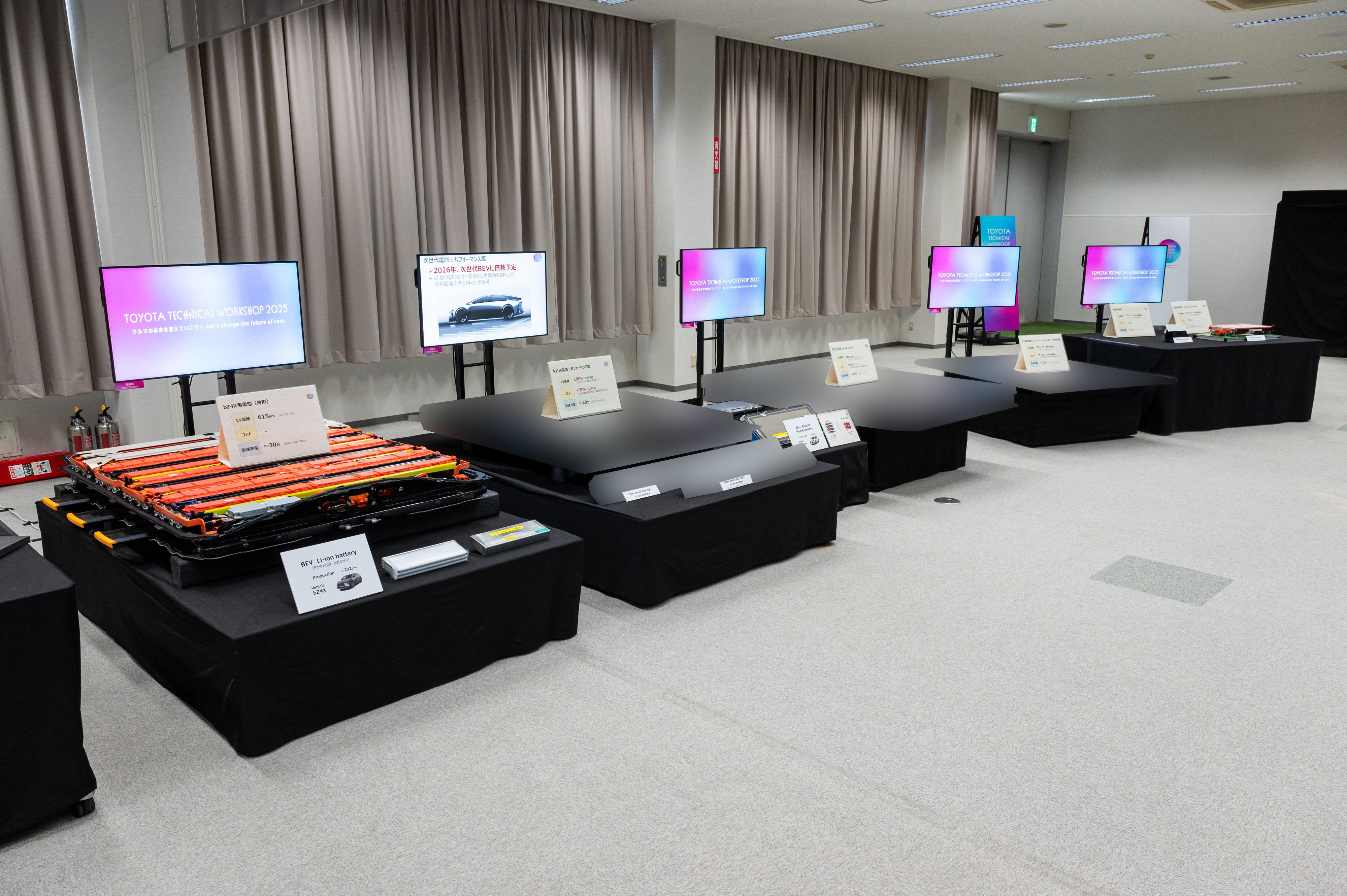
パフォーマンス版は、電池の高エネルギー密度化と空力などの車両効率の向上で、航続距離は従来型比2倍となる1,000kmへ。それでいて、コストは20%減、急速充電も20分以内を目標にする。
普及版は、HEV(ハイブリッド車)のニッケル水素電池で採用実績のあるバイポーラ構造をBEV電池にも適用。
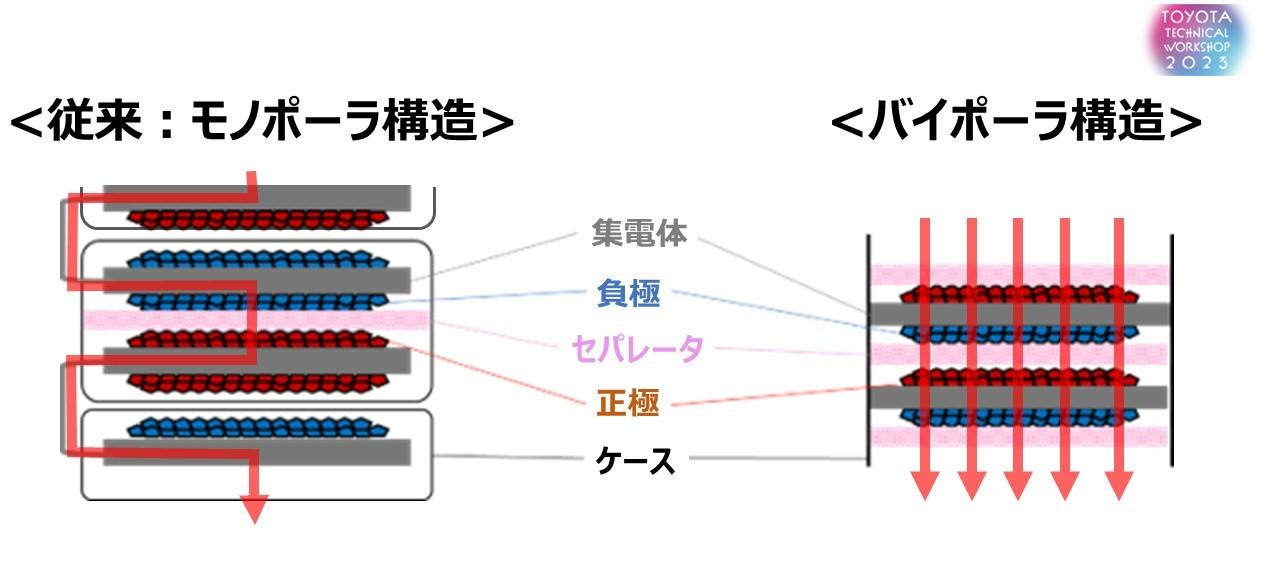
航続距離は従来型の20%増、急速充電は同じく30分以内にとどまるが、部品点数を4分の1~5分の1程度に抑えられるため、コストは40%減を見込む。
そして、この2つの次世代電池の「いいとこどり」をしたのが、ハイパフォーマンス版。正極にハイニッケル系素材を採用し、バイポーラ構造と組み合わせる。
こうすることで、パフォーマンス版との比較で航続距離は10%増え、急速充電は20分以下を保ちつつ、コストは10%減らせる見込みだ。
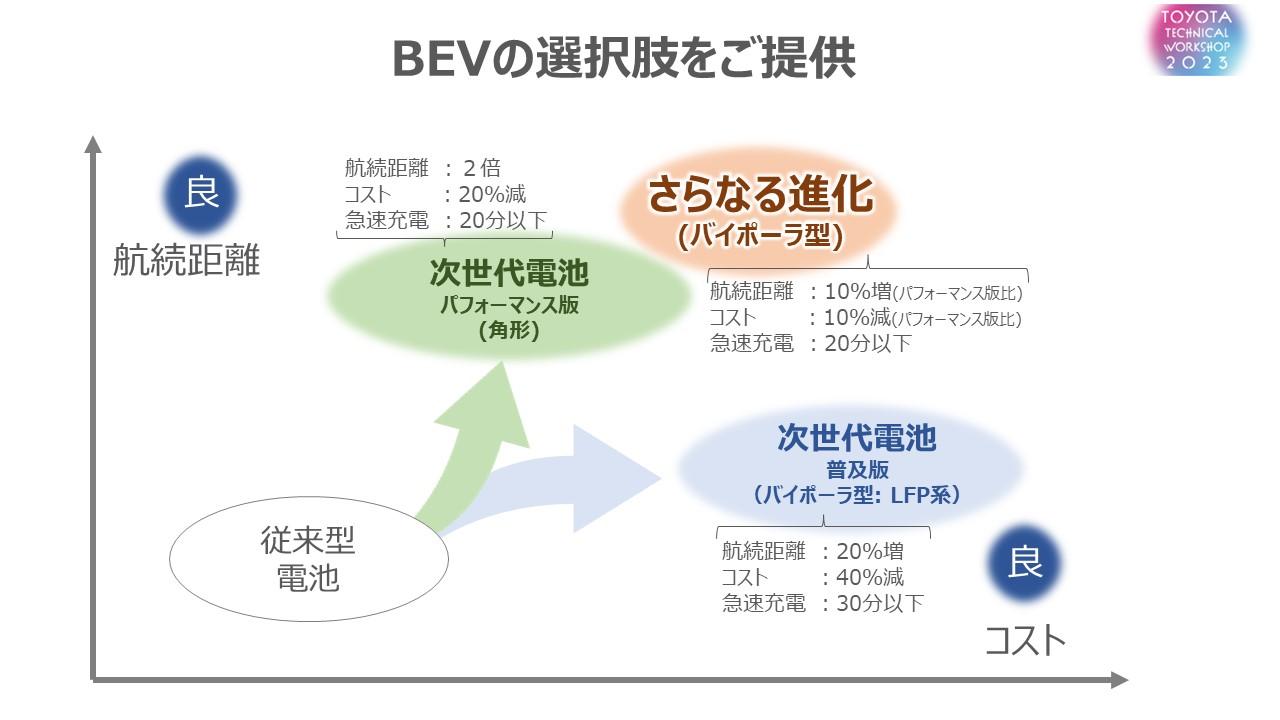
「電池にも選択肢を」。フルラインナップメーカーのトヨタらしい、お客様のニーズに柔軟に対応できる開発を進める。
〈BEV〉全固体電池の「新技術」を発見
なお、この場では「BEVのゲームチェンジャー」とも言われている全固体電池の新情報も伝えられた。
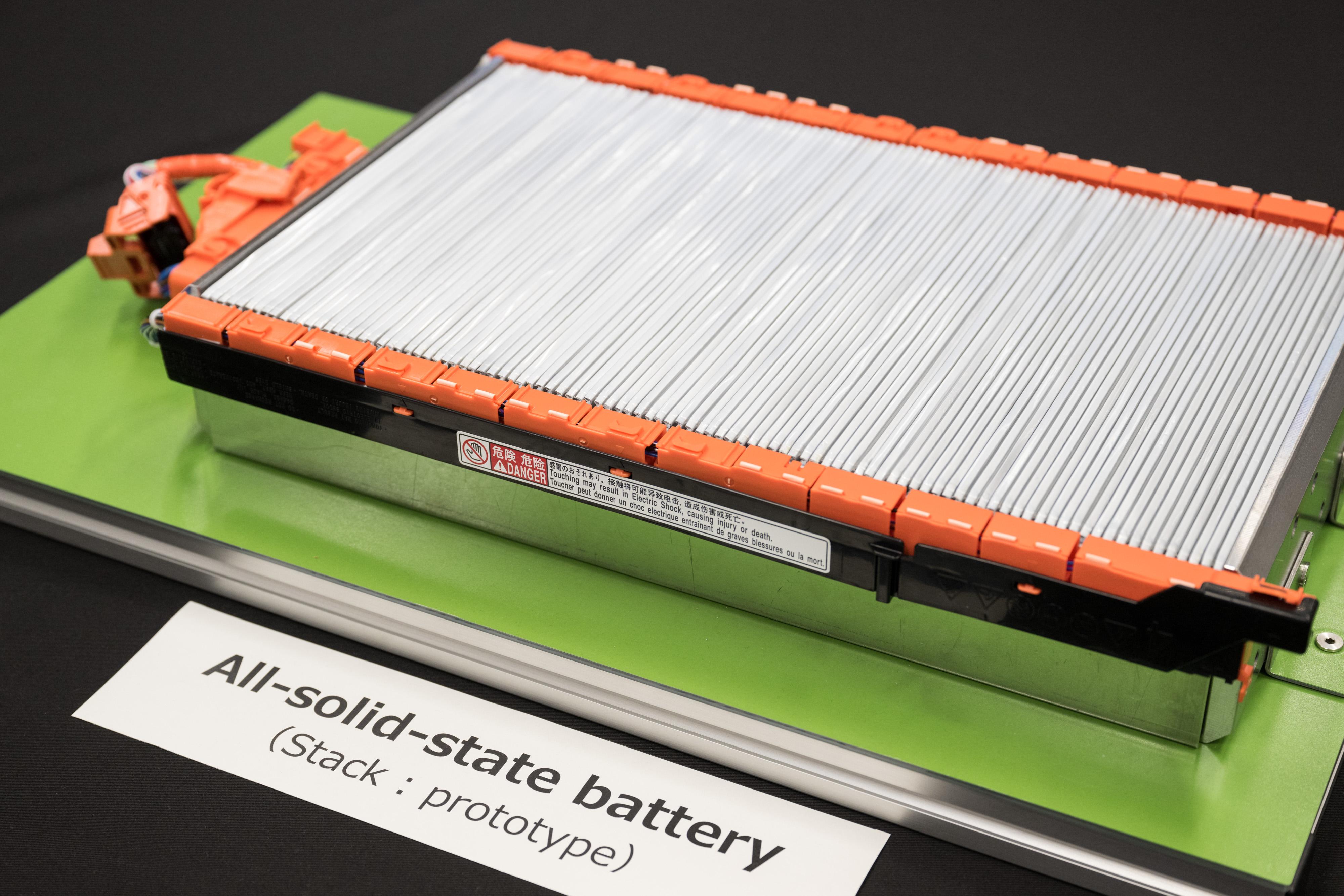
全固体電池は電解質が固体となるため、イオンの動きが速く、高電圧・高温への耐性がある。これにより、高出力化、長い航続距離、充電時間の短縮などが期待されている。
一方で、課題とされてきたのが、電池寿命の短さ。電池の充放電で固体電解質が膨張と収縮を繰り返す中で、亀裂が生じ、イオンが正極と負極の間を通りにくくなることがある。
今回トヨタは、この課題を克服する新技術を発見したという。今後はコストの課題を解決できるよう、量産工法の開発に取り組んでいく。
さらに、トヨタは2021年に「全固体電池の導入はHEVから」としていたが、BEV用電池として、2027~28年の実用化にチャレンジするという計画の見直しも明らかにした。
なお、パフォーマンス版はプライムプラネットエナジー&ソリューションズと、普及版、ハイパフォーマンス版、全固体電池は豊田自動織機と開発を進める。トヨタグループの知見を結集して、実用化を目指す。
〈BEV〉ロケット技術を応用した空力技術
BEVの性能を決めるのは電池開発だけではない。走行抵抗の低減、エネルギー回生のさらなる拡大、クルマ全体のエネルギー・熱のマネジメントなど、車両開発とセットで考える必要がある。
そんな車両開発のアイテムとして、加藤プレジデントが紹介したのが、三菱重工業 宇宙事業部と共同検討する空力技術。ロケットの極超音速技術を自動車に応用した。
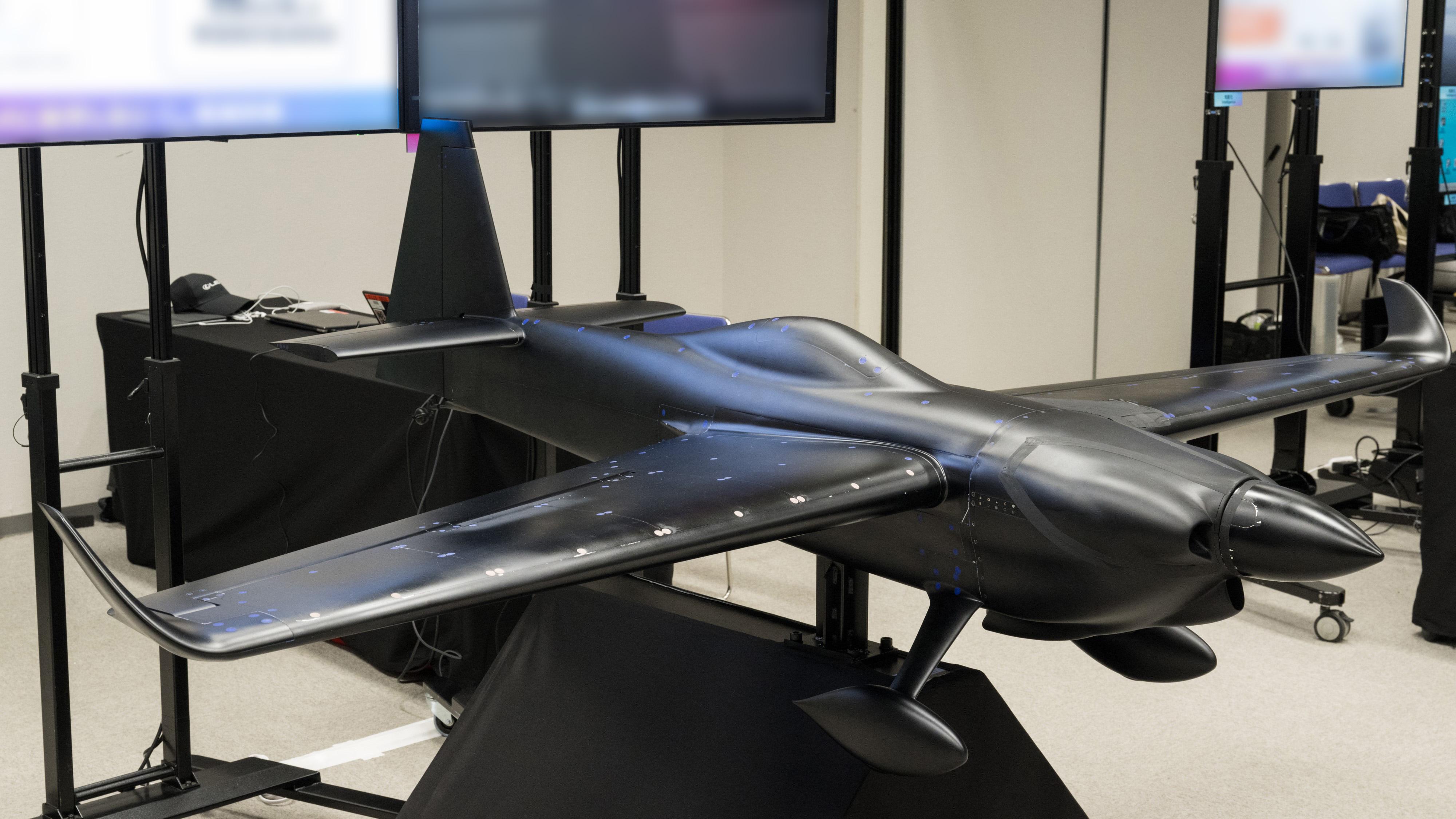
ロケットの空気による摩擦や圧縮されることで発生する空力加熱から機体を守る技術の知見をクルマの速度域で検討。
ボディ表面への処理などにより、空気の流れと接している箇所をコントロールすることで抵抗を抑えることができるようになる。
空気抵抗を表すCD値が既存のボディで0.20だとすると、その1割に相当する低減効果が期待される。
さらに注目すべきは、ボディ形状も、スチール、アルミといった素材も問わないということ。カッコいいデザインと空力が両立できる。そんなポテンシャルを秘めた技術だ。
3年後の実用化を目標に開発を進めている。
〈BEV〉モノづくりの進化で投資も工程も半分に
次世代BEVという「商品の進化」を支えるのは「モノづくりの進化」だと加藤プレジデントは言う。
「モノづくりの未来は2分の1。言うなれば『BEVハーフ』。モジュール構造と自走生産は、工程と工場投資を2分の1にする。さらにデジタルツインの力で、生準(生産準備)リードタイム2分の1を実現する」
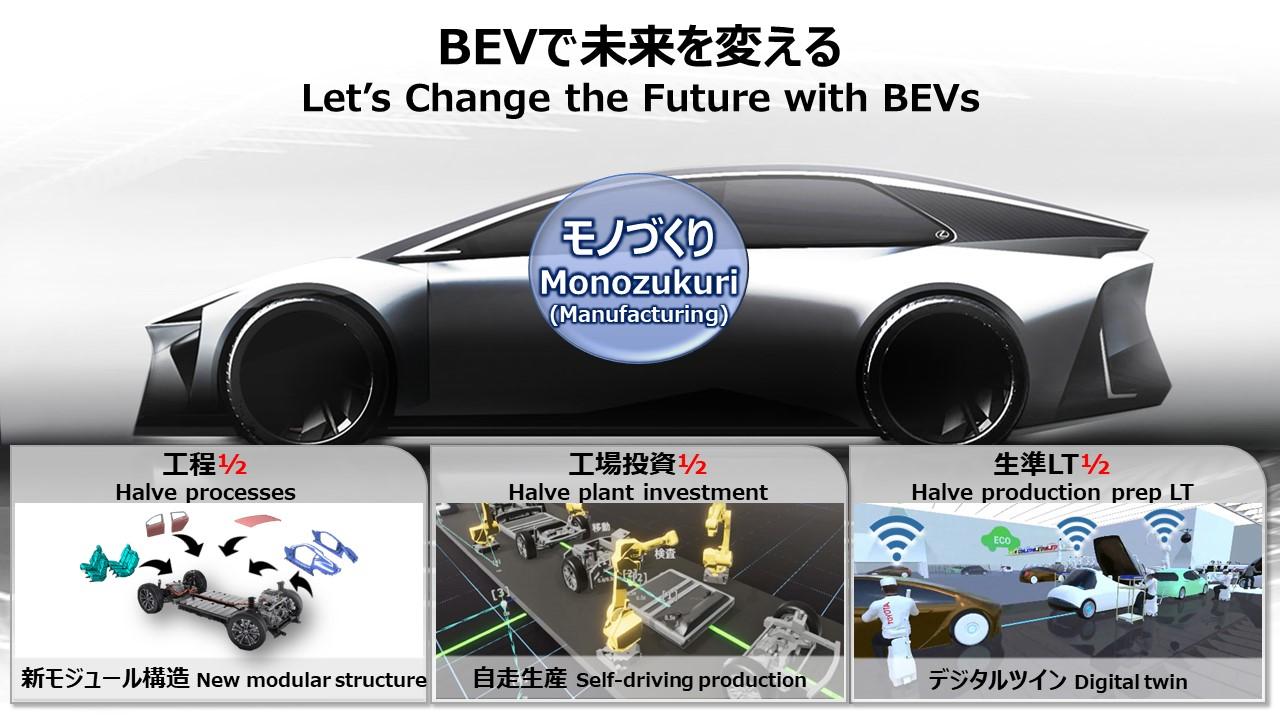
次世代BEVでは車体をフロント、センター、リヤに3分割した新モジュール構造を採用する。
電池が搭載されるのはこのうちのセンター部分のみ。フロント、リヤは影響を受けないので、電池の進化を素早く車両に取り込むことができる。
そして、このモジュール構造を実現する生産技術の一つがギガキャストと呼ばれる鋳造工法だ。
現在、bZ4Xのリヤ部分は、86の板金部品、33のプレス工程でできている。それをアルミダイキャストで一体成形することで、部品点数も工程もたった1つにすることができる。
コストも重量も従来以下を目指すとともに、トヨタの強みであるTPS(トヨタ生産方式)も織り込んで、生産性も上げていく。

あわせて紹介されたのが、組立中のクルマが自ら走り、次の工程に移動する「自走組立ライン」だ。
極端に言うと、フロント、センター、リヤの3つの部品に、電池、モーター、タイヤ、無線端末がついただけの状態で自走する。
こうすることで、ラインからコンベヤをなくすことができ、工場のレイアウトが自由自在に。年単位に及ぶ量産に向けた準備期間や、数十億円に上る工場投資を削減することができる。
3年後の導入をめどに開発を急ぐ。