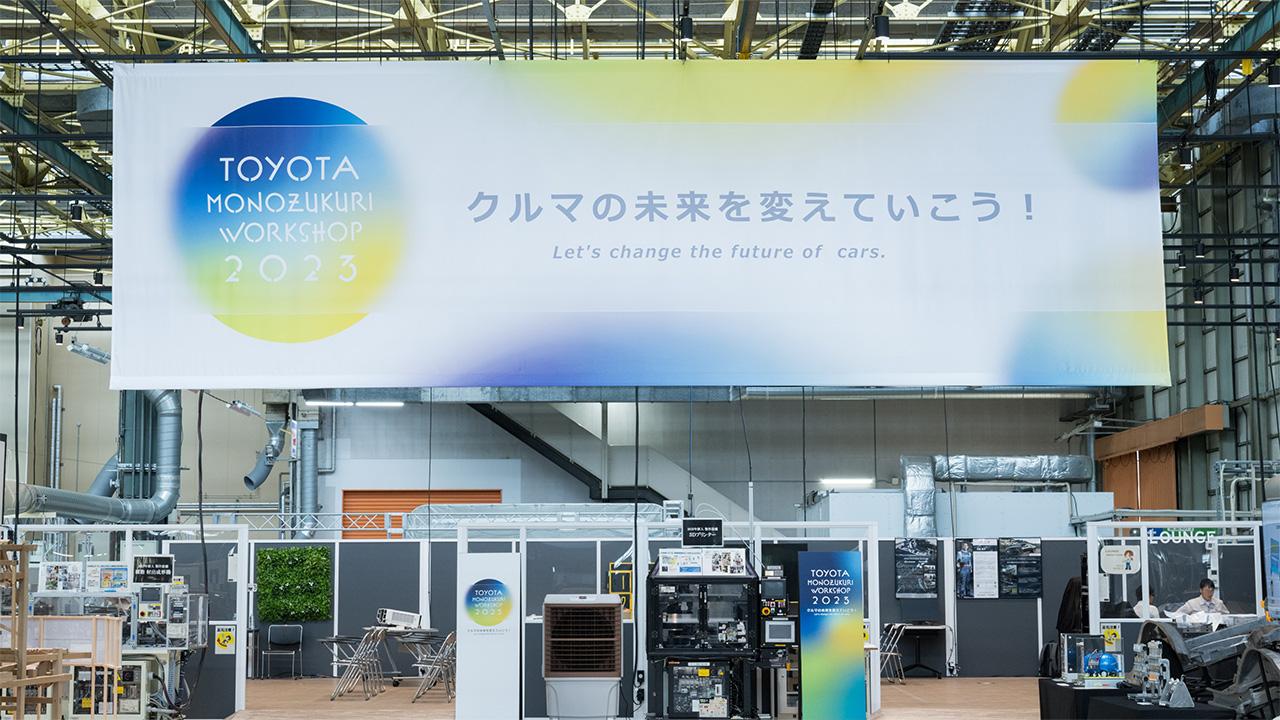
Toyota seeks to halve the number of manufacturing processes through its renowned craftsmanship and technological innovations. The company showcased the monozukuri genba, giving rise to advanced technologies that will change the future of cars.
Tackling logistics issues with vehicle handling robots
The Monozukuri Workshop also showcased technological developments aimed at tackling the so-called “2024 problem*” in logistics.
*From April 1, 2024, truck drivers' overtime will be limited to 960 hours a year. This is predicted to result in lower wages for drivers, higher staff turnover, worker shortages, and higher logistics costs.
For carmakers, logistics consists of transporting parts and finished vehicles. Parts from domestic manufacturers are delivered to production plants by truck or rail.
Meanwhile, finished vehicles are transported by car carrier trailers to Toyota dealers around the country and to ports for export.
The Motomachi Plant, for example, has a yard of approximately 40,000m 2 with space for 1,600 finished vehicles. Each day, some 800 cars are sent out in 160 shipments.
Truck drivers must repeatedly walk to fetch vehicles from among those lined up around the vast yard, then load them onto trailers parked in the loading zone. In rain or blazing heat, they walk some 8 km a day just within the yard.
To ease their workload, this month, Motomachi introduced a Vehicle Logistics Robot (VLR) to assist with transporting cars.
Built with technologies from the Teiho Plant, this autonomous robot is guided by high-precision GPS, which enables it to track its own position and chart a route to the destination.
With the GPS accurate to within a few centimeters, the robot moves underneath a car and lifts it up by grasping the tires. Depending on a vehicle's height and wheelbase, the cargo bed is automatically raised, lowered, extended, or retracted.
In this way, the vehicles are lined up in a pickup area directly in front of the loading zone. Drivers now only need to travel the short distance between the two, reducing their workload while also improving handling efficiency.
Toyota strives to alleviate the burden on drivers and create safe working environments.
As part of these efforts, the company is also looking to develop technology that will enable finished vehicles to drive autonomously from the plant to the yard.
Keeping pace with the times through faster evolution
The theme for this Monozukuri Workshop was “changing plant environments and the future of cars through human-centered manufacturing.”
Speaking at the event, CPO Shingo summed up Toyota’s strengths:
“We need to evolve monozukuri through combining skills and technology with digital and innovative technologies. Toyota has a TPS-based technique called lead-time reduction. I believe the strength of Toyota's manufacturing lies in being agile and continually taking on challenges, increasing the speed of evolution, and responding to the changes of the times.”
Robots honed by skilled workers, and takumi skills passed down to the next generation through the latest technology. Just as Sakichi Toyoda developed the automatic loom to make his mother’s job easier, TPS is continually enhanced by the desire to make work easier for others.
Toyota will keep striving to create plant environments that allow workers to thrive, along with ever more exciting mobility for users.