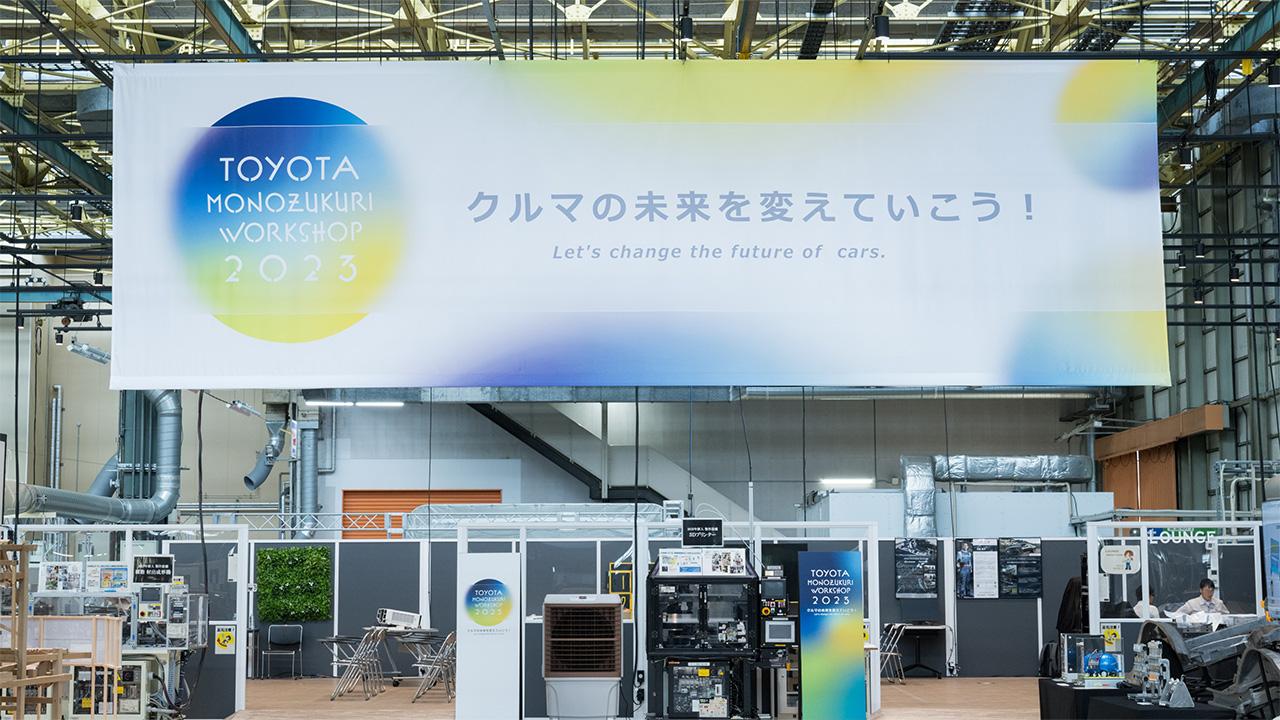
Toyota seeks to halve the number of manufacturing processes through its renowned craftsmanship and technological innovations. The company showcased the monozukuri genba, giving rise to advanced technologies that will change the future of cars.
Craftsmanship and TPS live on in giga casting
This year, the Myochi Plant that produces cast parts for Toyota’s cars celebrates its 50th birthday. It is also developing the company’s giga casting*, which has attracted much attention since the announcement in June.
*Technology for the integrated molding of car body parts that previously required dozens of components and processes. In the case of bZ4X, the rear section is reduced from 86 parts to one.
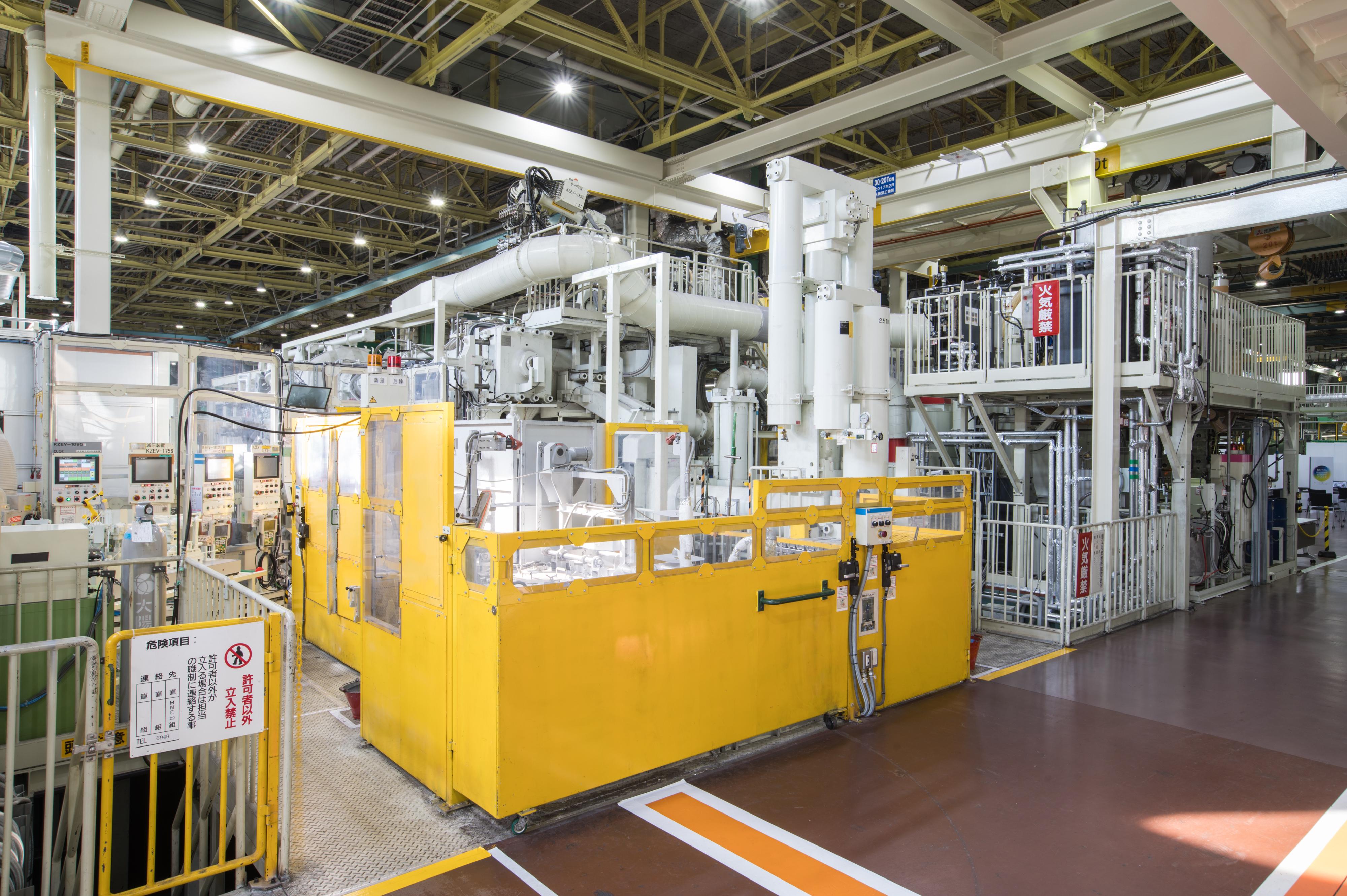
The process starts with injecting molten aluminum alloy into a mold at high speed and pressure. In a matter of seconds, the material is cooled from 700°C to 250°C and solidified, then the mold is opened to remove the integrated cast part.
Aiming to use giga casting in mass production, Toyota presented genba efforts to improve productivity by reducing two types of waste.
The first is downtime during mold replacement. Whereas a typical changeover might take 24 hours and require a large crane, giga casting molds, which weigh more than 100 tonnes, lead to even greater time loss.
By contrast, Toyota’s approach to giga casting divides molds into two types: general-purpose molds that remain mounted on the machinery, and specialized molds whose shape differs by car model. During a replacement, only the compact specialized molds detach themselves automatically from the general-purpose molds.
With these Just-in-Time mold changes—replacing only what is needed, when it is needed, in the quantity needed—Toyota is aiming to bring lead times down to 20 minutes or less.
This division of molds and automated mounting/detaching is the culmination of improvements made over many years of handling every aspect of mold design, fabrication, and maintenance in-house. When molds expand or contract under the heat of casting, the general-purpose and specialized parts may become misaligned, with the latter unable to release. The necessary clearance is maintained by the skills of mold craftsmen.
The second type of waste stems from defects and reworking. In its giga casting analysis technology, Toyota uses proprietary simulation software that draws on expertise accumulated in the mass production of engine blocks and other components. Takumi skills have also been digitized and incorporated into parameters and computation methods to create quality products.
Amid a general trend toward using commercially available equipment, in-house development allows Toyota to add parameters or change computation methods. Building high quality into the machinery reduces the number of defects.
Driven by the skills of experts with intimate knowledge of casting, as well as the waste and lead time reductions made possible by the Toyota Production System, the company’s monozukuri continues to improve and evolve.
Harnessing expertise and ingenuity in mixed model production lines
The Motomachi Plant commenced operation 64 years ago. Today, it is a mixed model production facility like no other, with a single line producing nine different models—including those currently in preparation—spanning four different powertrains and three body types.
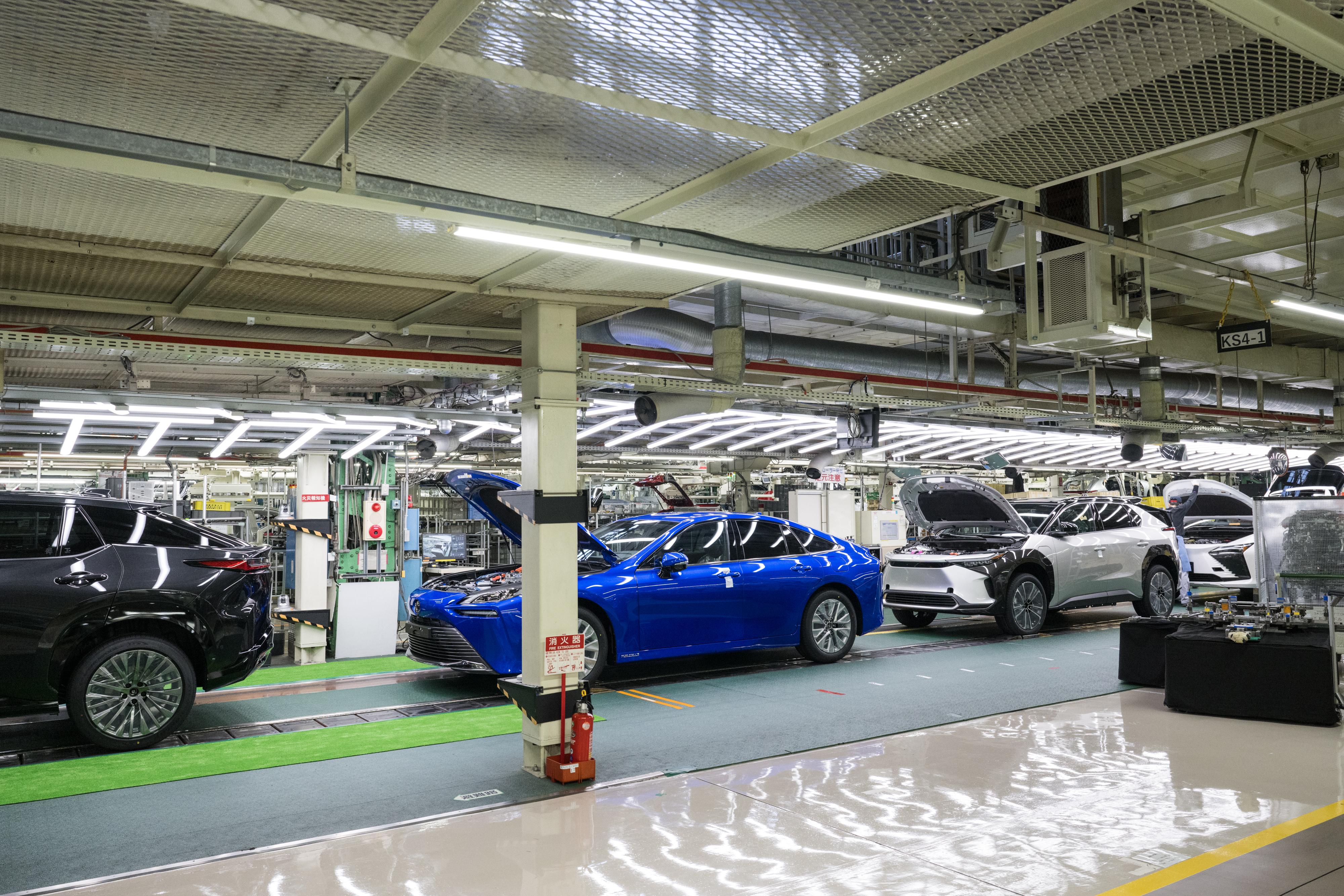
Instead of lot production consisting of single-model batches, TPS enables Toyota to employ a “one-piece flow” approach, in which cars are made in the same sequence as ordered.
As a result, cars of different shapes come down the line one after another, sedans followed by SUVs and minivans.
Naturally, work times and processes vary between different cars. Toyota’s production, however, maintains efficiency by offsetting these workload differences with process scheduling optimized according to customer needs, evening out the work times.
In the genba, workers use platforms known as “universal modular trays” to standardize the process of installing different power units in vehicles.
Power units of varying shapes and weights stream down the line, including HEV engines, e-Axles, and FC stacks.
These are loaded onto the UM trays using the same base platform with simple attachments to accommodate any power unit. This is a perfect example of a device developed jointly by the genba and manufacturing engineers to enable one-piece flow production.
For details on various other genba innovations that make mixed model production possible, check out our previous article.
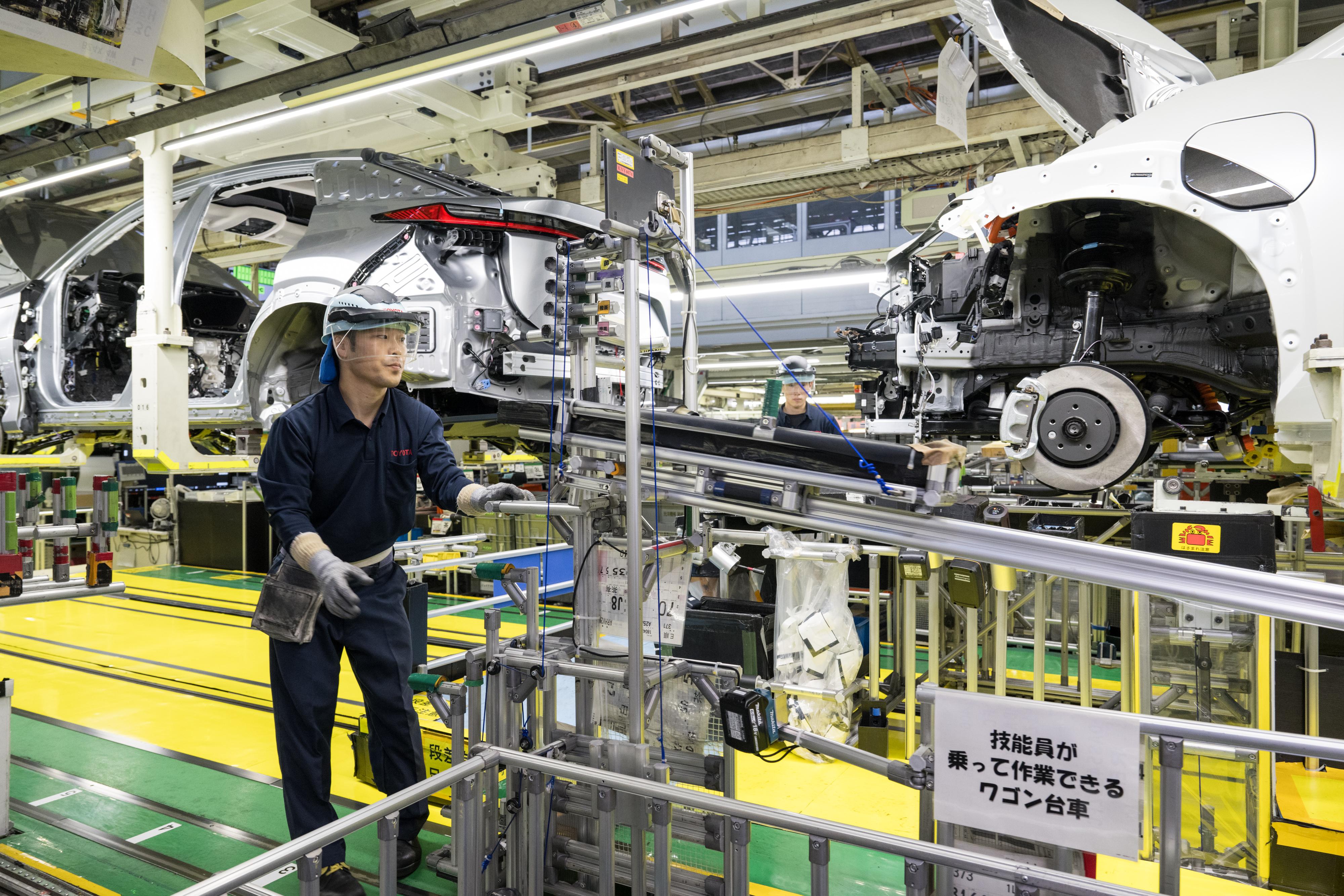
Digital twins help develop skills and equipment
Finally, we would like to share some examples of how digital technology is being used in the development of production equipment.
Before coming into the hands of genba workers, this equipment usually undergoes a process of design, parts machining, and assembly.
However, the drawings prepared in the design stage may include parts whose shape proves impossible to machine. The equipment may not run properly after being adjusted, or the people on the production floor may find it hard to use. Much of the manufacturing lead time is taken up dealing with such issues, causing waste through defects and reworking.
To tackle this, Toyota’s current process uses 3D drawings and involves genba workers from later stages of production, who view the drawings as they are being prepared and share expertise that is incorporated into the designs.
To put it another way, the company is transforming the way employees work through a holistic approach that encompasses the entire equipment manufacturing process. As part of efforts to shorten lead times, Toyota is aiming to eliminate reworking by bringing forward and synchronizing jobs.
At the workshop, the Teiho Plant showed how a handmade 150-inch monitor displaying full-size models of equipment is used to test actual work operations, leading to more sophisticated drawings.
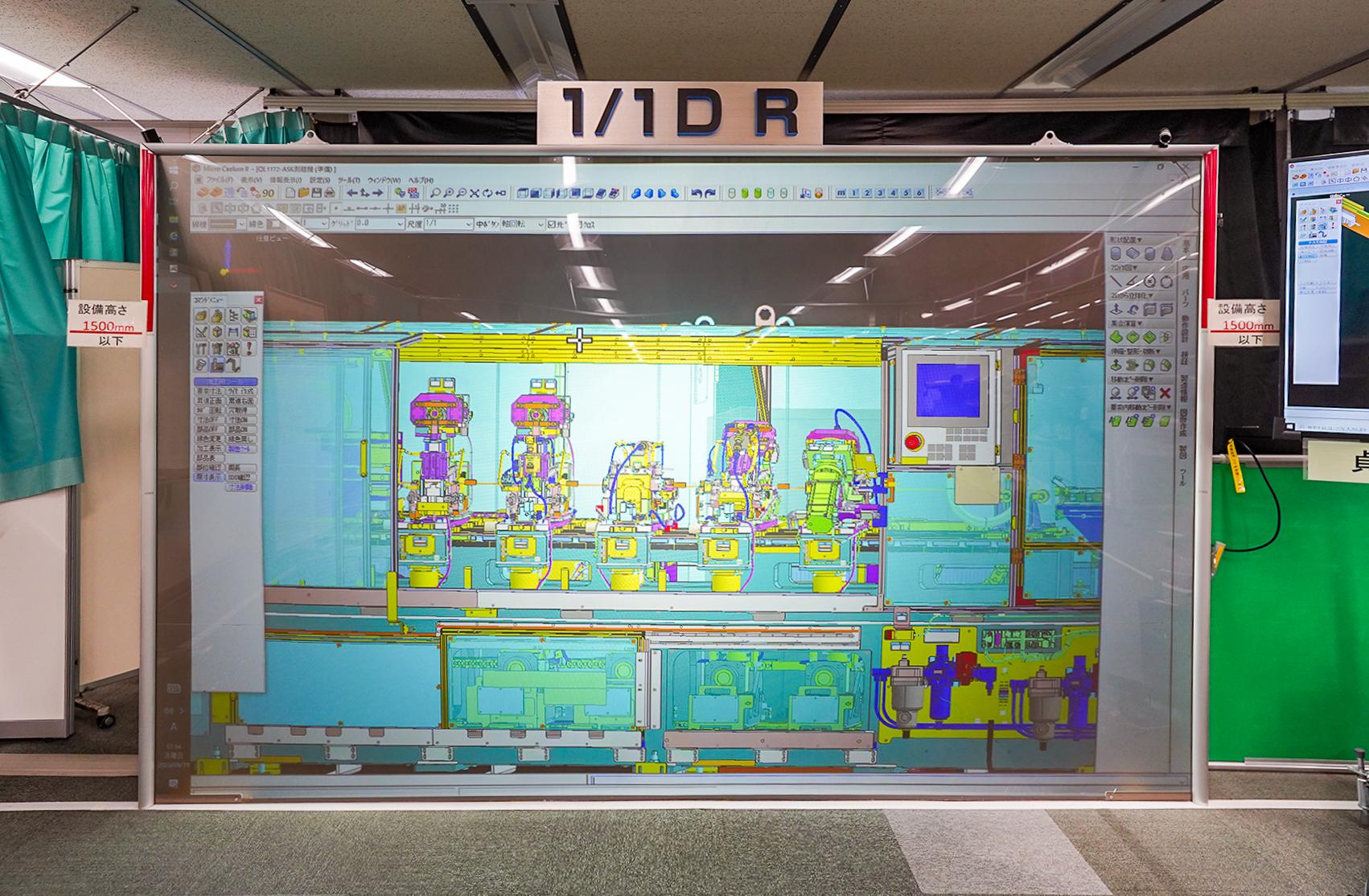
Digital technology is also used to visualize aspects that a monitor alone cannot capture, such as the depth of an apparatus or how equipment will be installed in the plant.

These efforts have reduced rework to one-tenth and halved production lead times while also lowering equipment costs by one-quarter.
The company is now working to expand such digitally-driven monozukuri within the group and manufacturing partners, seeking to maximize the competitiveness of the entire Toyota Group.
And these technologies are not only used to develop new equipment.
The Teiho Plant also showed how the cutter input for a machine producing metal parts was first automated digitally before transferring the solution to the genba.
Similarly, tools for developing genba personnel were also on display, including training machines that use AR technology to teach specialized skills which are difficult to explain and tend to be treated as tacit knowledge.
Both of these examples were created by genba manufacturing employees who had learned about digital technologies.
“Spurred on by Chairman Akio Toyoda’s call to become a digital world leader within three years, workers at various genba have laid the foundations by acquainting themselves with digital technologies,” explained Production Engineering Development Center President Yoshihito Kondo. “As the next phase, we look forward to seeing the fruits of their efforts rolled out in mass-production plants.”
Generally, using digital tools is a one-way process, with such technologies often helping design things for the genba. However, Toyota aims to create constantly evolving plants through interactive digital twins, where frontline improvements are enhanced digitally before being fed back to the genba.