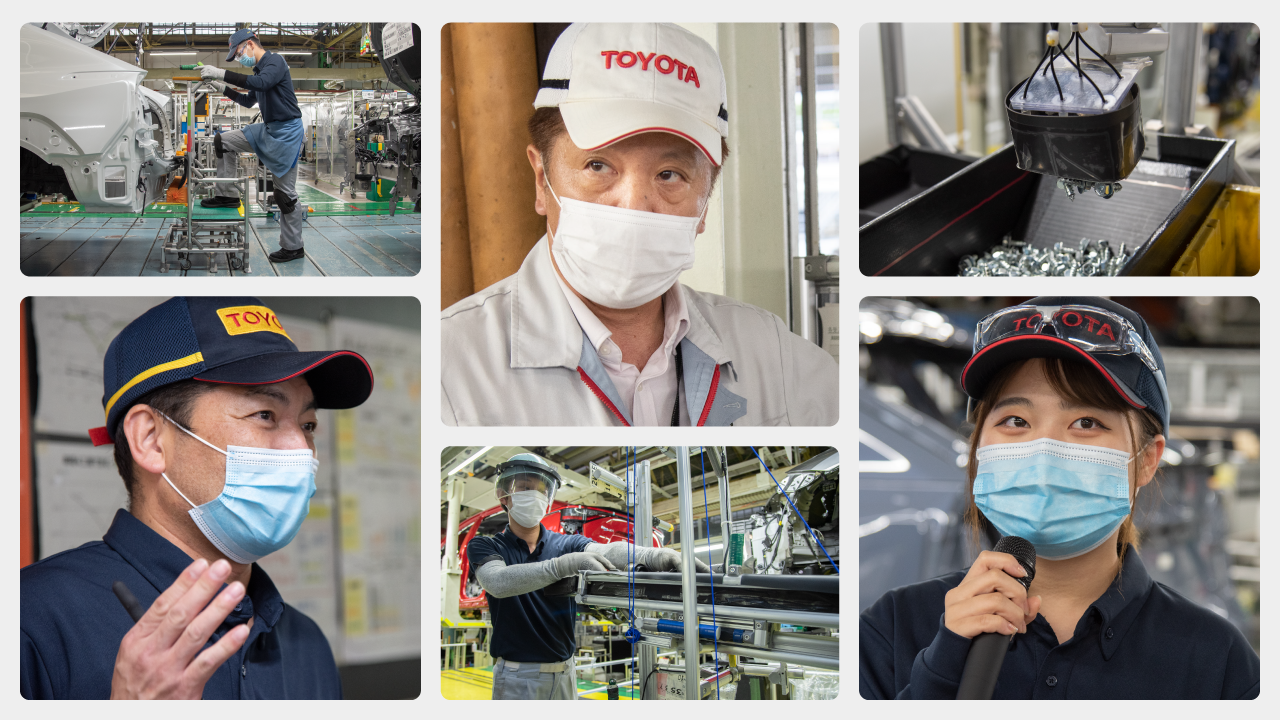
The differences go beyond color―cars of various sizes and powertrains stream down the same production lines. Toyota Times looks at how genba expertise and ingenuity make it possible to handle unprecedented challenges.
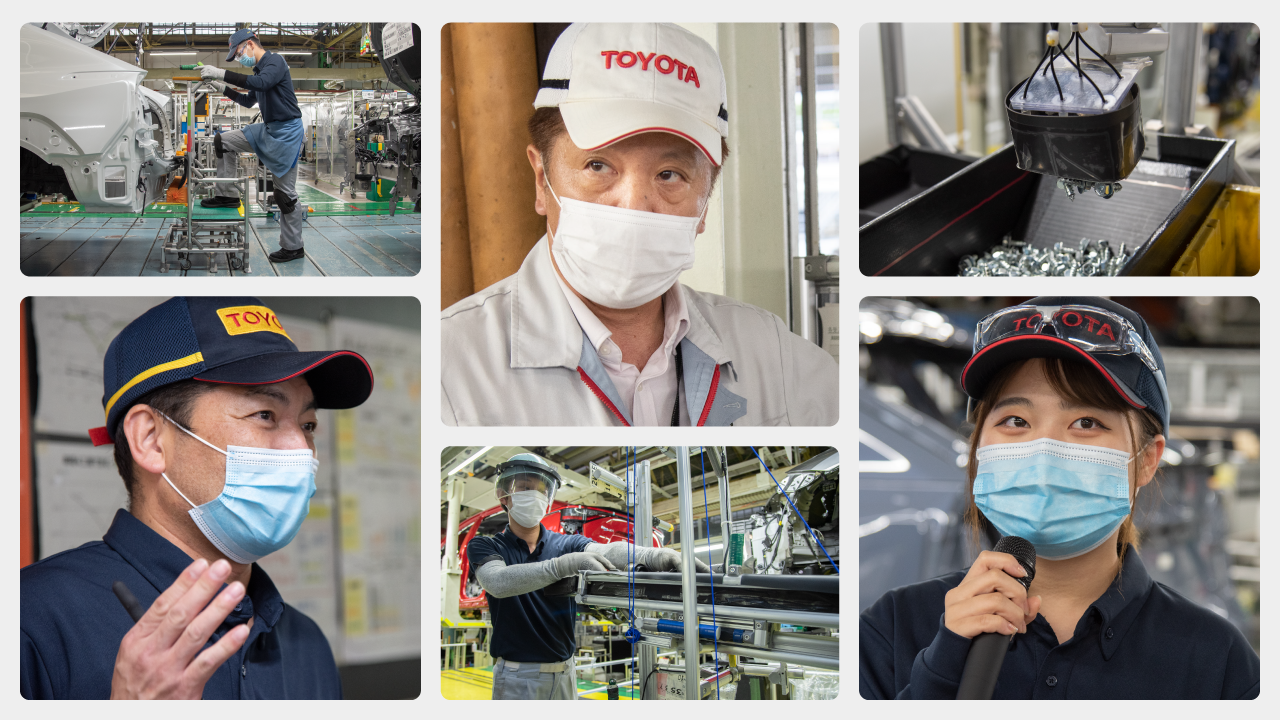
In June 2022, Japanese Prime Minister Fumio Kishida visited Toyota’s Motomachi Plant in Toyota City. Responding to the press after his tour of the production floor, the Prime Minister began with the following comment.
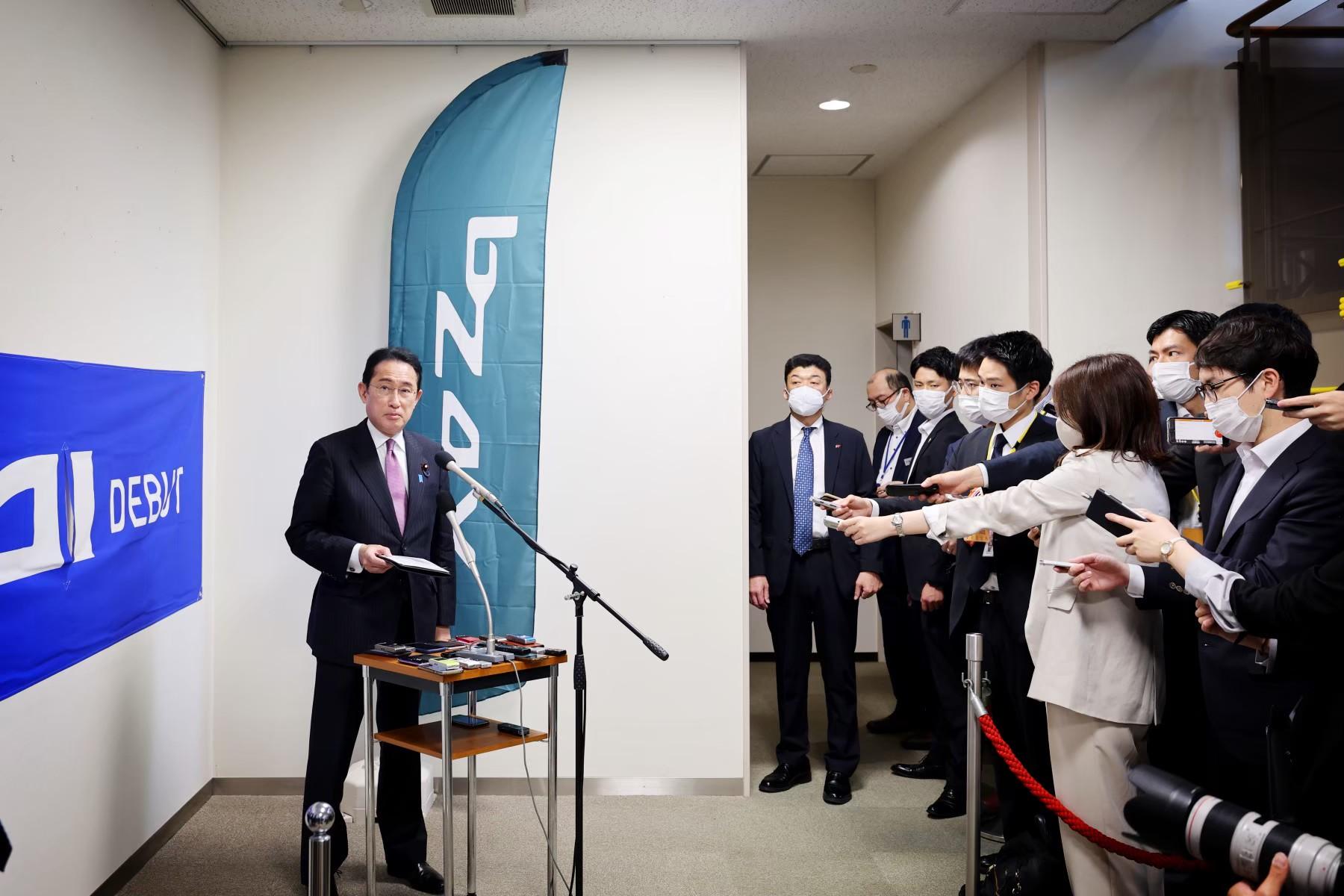
“I witnessed incredible efforts to make different models on one production line, including battery electric vehicles, to offer diverse options in pursuing carbon neutrality.”
“The word kaizen is now used globally to refer to various improvements in manufacturing processes, but it was very impressive to see exactly what that means on the production floor.”
The production line at Motomachi makes entirely different categories of vehicles, not only in varied shapes of sedans, SUVs, and minivans, but also with diverse powertrains, including gasoline engine vehicles, hybrids (HEV), battery electric vehicles (BEV), and fuel cell electric vehicles (FCEV).
Alongside efforts at this mixed model production, the Motomachi Plant is going through an unprecedented challenge this year. This report looks into the expertise and ingenuity that manufacturing frontline members use to manage future uncertainty.
Motomachi embraces a mixed model approach
The Motomachi Plant, known as the home of the Toyota Crown, began operating in 1959. It was established as a dedicated passenger car plant to fulfill founder Kiichiro Toyoda’s dream of making Japanese cars for the masses.
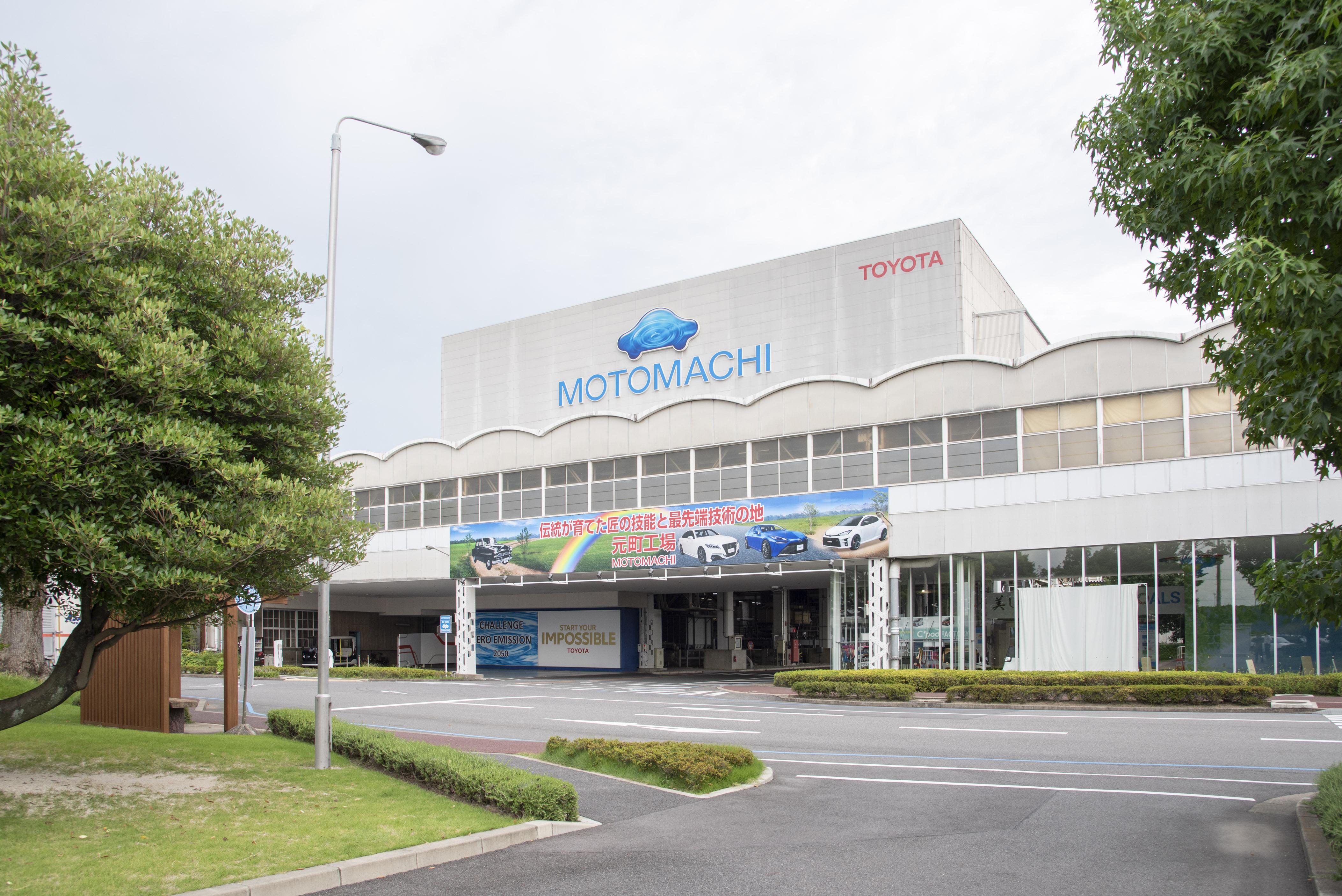
The plant’s production hit its peak in 1990, at the height of Japan’s bubble economy, pumping out 445,000 Mark II and Crown cars.
Unfortunately, subsequent years saw a decline in volume, and over the past two decades, the plant has repeatedly dropped to single-shift operations.
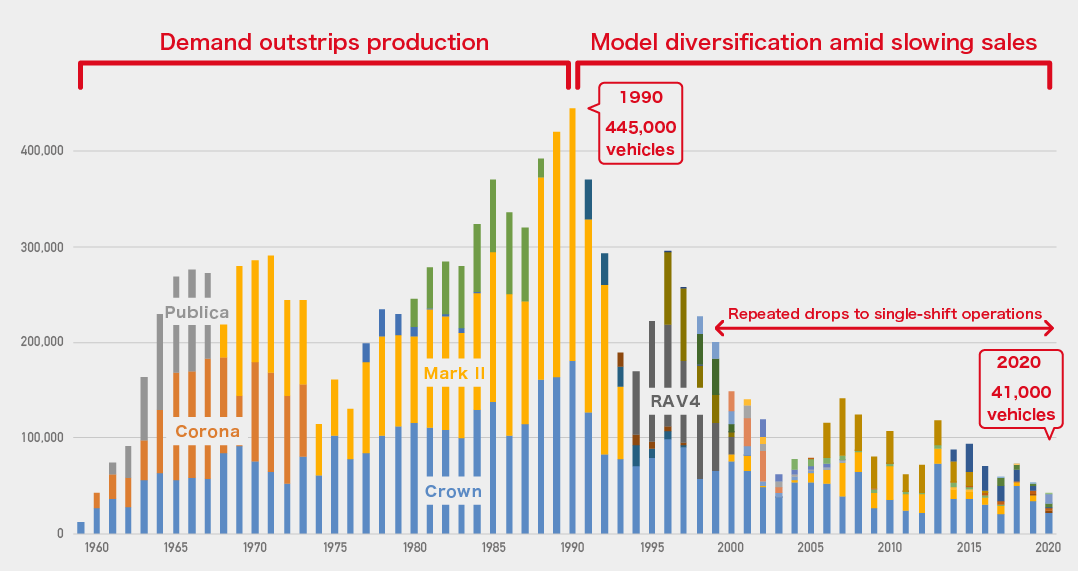
That year also marked a turning point in the number of models handled by the plant. Until then, Motomachi had produced at most three different models, with demand strong enough to sell whatever was made.
After 1990, five to six models became the norm, as Toyota entered an age where even new models struggled for sales growth within just a few months of launch.
In contrast to other plants operating on a two-shift basis with short takt times, Motomachi would return to single-shift operations every few months. After those years of difficult experiences, this year, it is producing 10 different models.
It is not unusual for an automaker to produce multiple models on one line. Still, in Motomachi’s case this time, the level of mixing has been kicked up a few notches with cars of different body types and powertrains.
Deputy General Manager Yuji Akari of the Final Assembly Division, who has spent most of his Toyota career at Motomachi, is enthusiastic about the changes, saying, “This plant will be able to make any car that comes our way.”

This is also an unusual year for the Motomachi Plant in that it will introduce four new models.
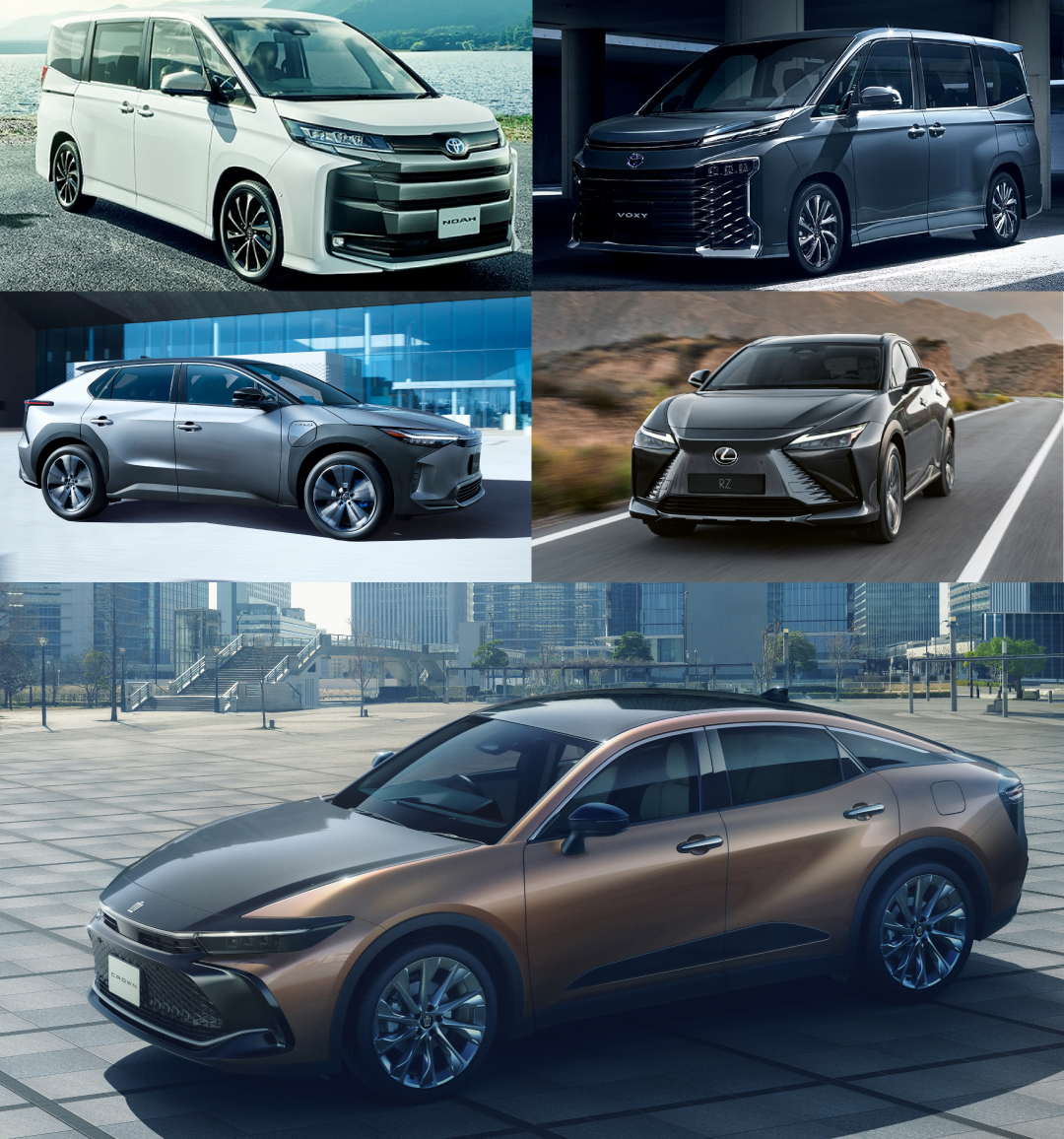
In preparation for this unprecedented project, Motomachi sought extra personnel for Assembly Line 1 last year. Along with many employees transferred from other plants, it also hired temporary staff.
With as many as 20 members joining each week, the line’s workforce personnel has increased to 1,000, with over 600 newcomers.
Following induction and training, the plant transitioned to a two-shift operation in April, and its third new model, the Crown, first rolled off the line in September. The groundbreaking challenge continues.
Mobile steps adapted to the mixed model approach
As the shapes of cars coming down the line change, so do the working postures of the people involved in assembly. The bZ4X SUV in particular has a large back door, making it difficult to pass the wiring harness through by leaning in from the rear of the car.
In assembly, the standards for two-handed tasks specify a maximum depth of 700mm, far below the 1,000mm needed for the bZ4X. Improvements were urgently needed to get production up and running.
The solution devised by Koshi Yamanaka of the Final Assembly Division was a set of mobile steps integrated with carts used to carry parts and tools.
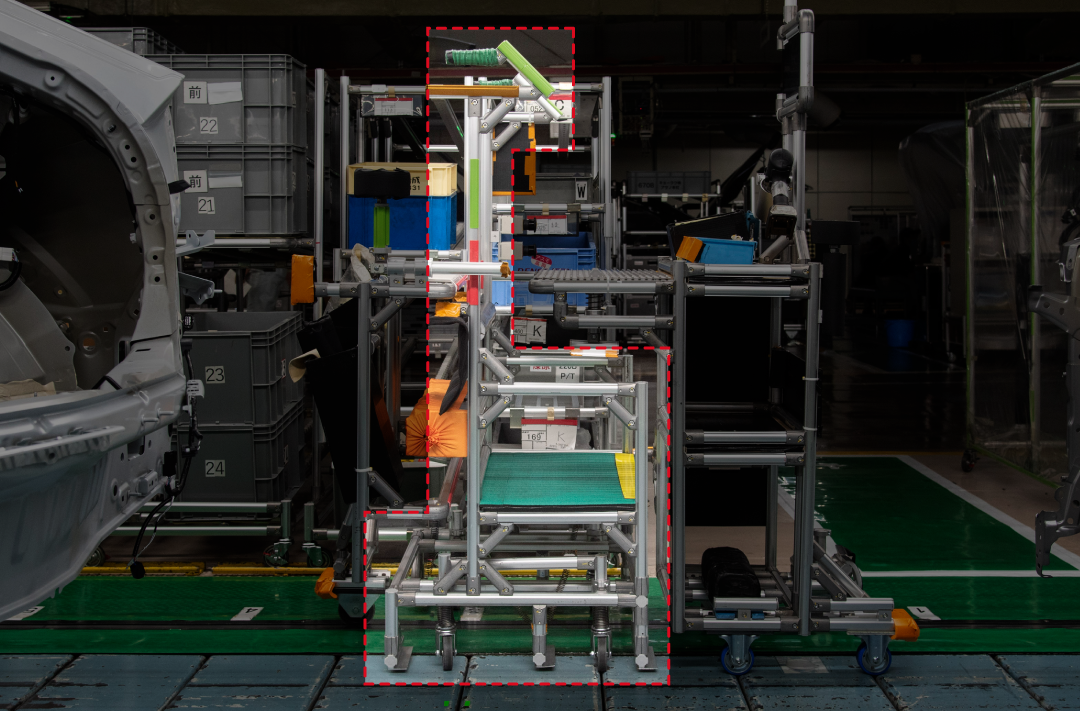
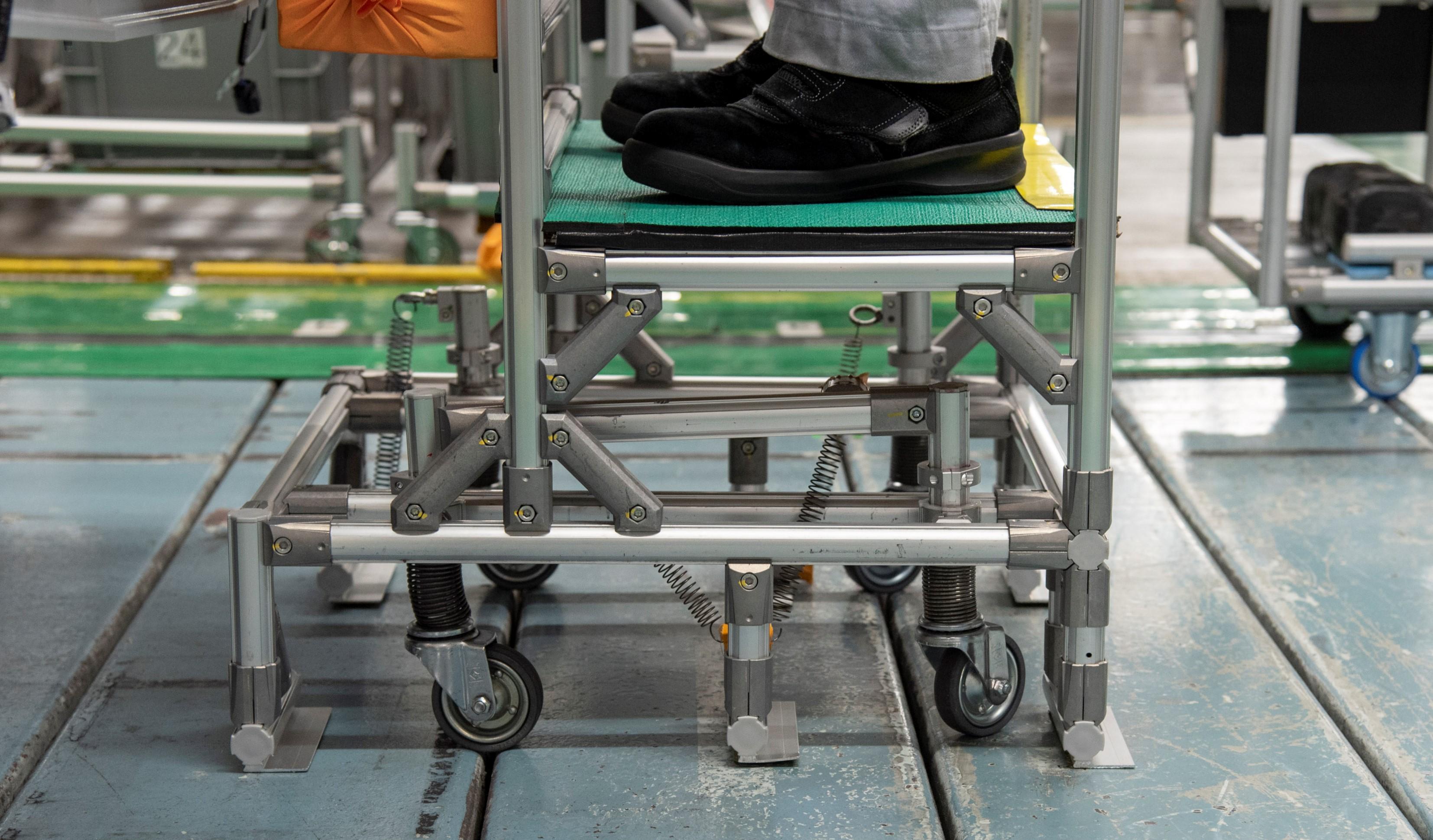
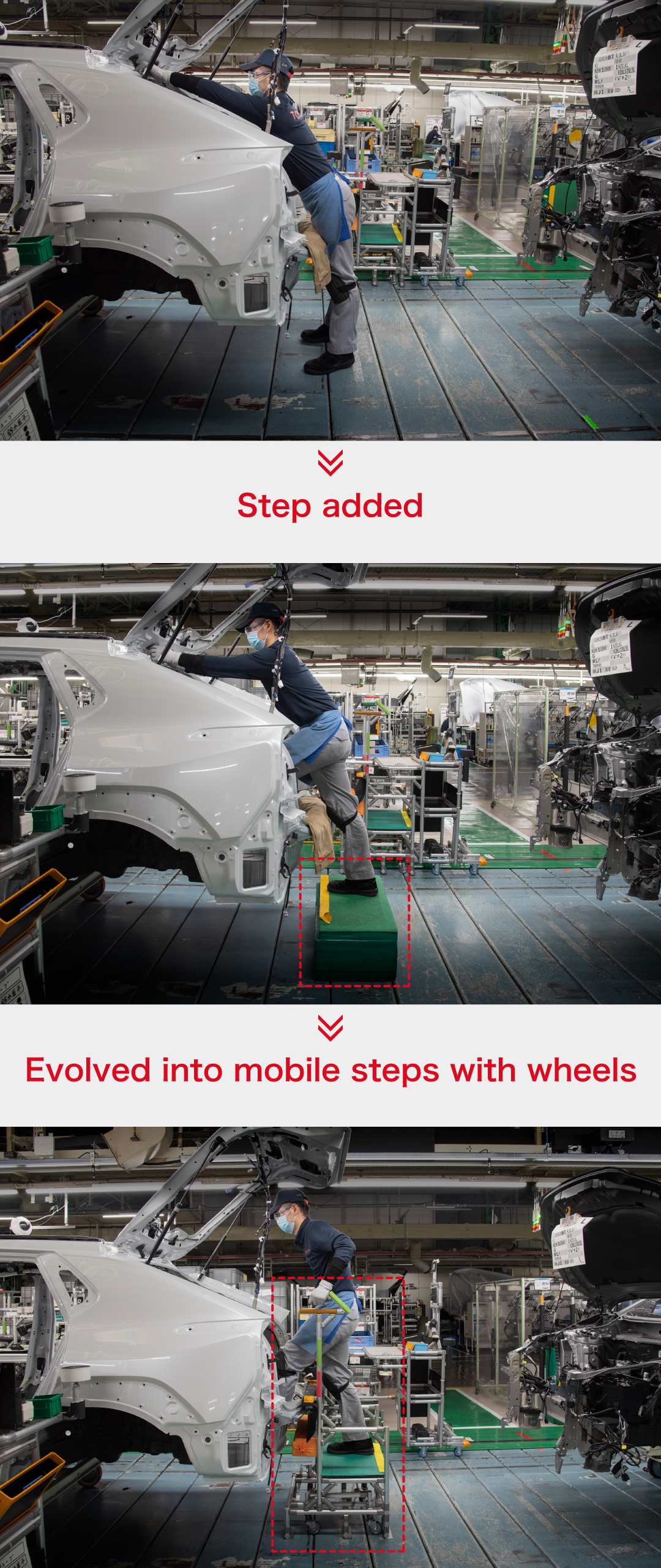
These new steps not only improve working posture, reducing strain on the body and making the job easier, but also provide a viewpoint from which staff can properly check their work.
“I believe it also helped to boost the quality of our work,” says Yamanaka, commenting on the fruits of his kaizen efforts.
A mixed approach sparks logistics reform
With more car models come more parts. The receiving area for Assembly Line 1 parts has a floorspace of 2,700㎡ , but even this won’t be enough when all four projects are up and running.

To compensate for the shortfall, a new parts receiving area was set up in a separate building away from the line in late March. Since this alone would be inefficient, the team also came up with a way to solve an existing challenge.
The Motomachi Plant’s assembly building is much longer than wide, stretching 300m from east to west. Previously, the sole receiving area was located at the eastern end, from which parts had to be taken all the way around the building.
Now, parts delivered to the new receiving area can be transported by large trucks to the plant building’s west side and supplied directly to the line. With the plant split into east and west halves, the job of supplying parts is shared with the old receiving area.
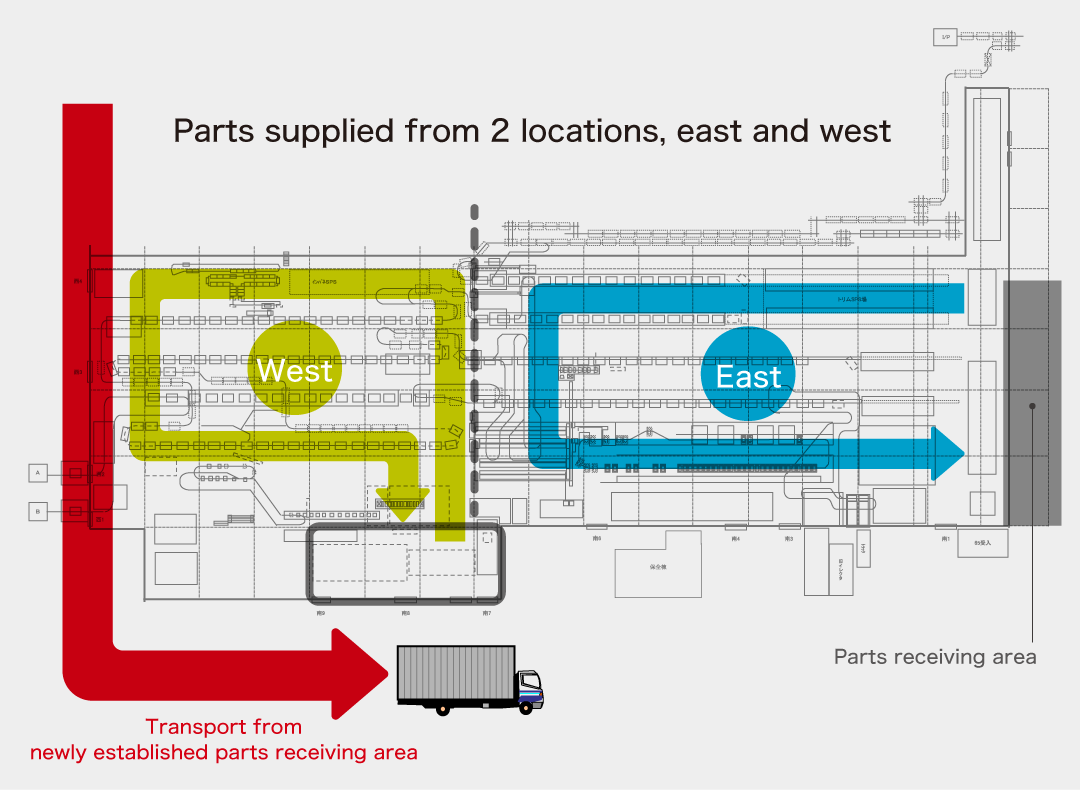
The project was overseen by Kazuhiro Kotani of the Final Assembly Division, Logistics Section, who says the changes have cut down the distance traveled by each logistics vehicle and alleviated traffic congestion within the site.
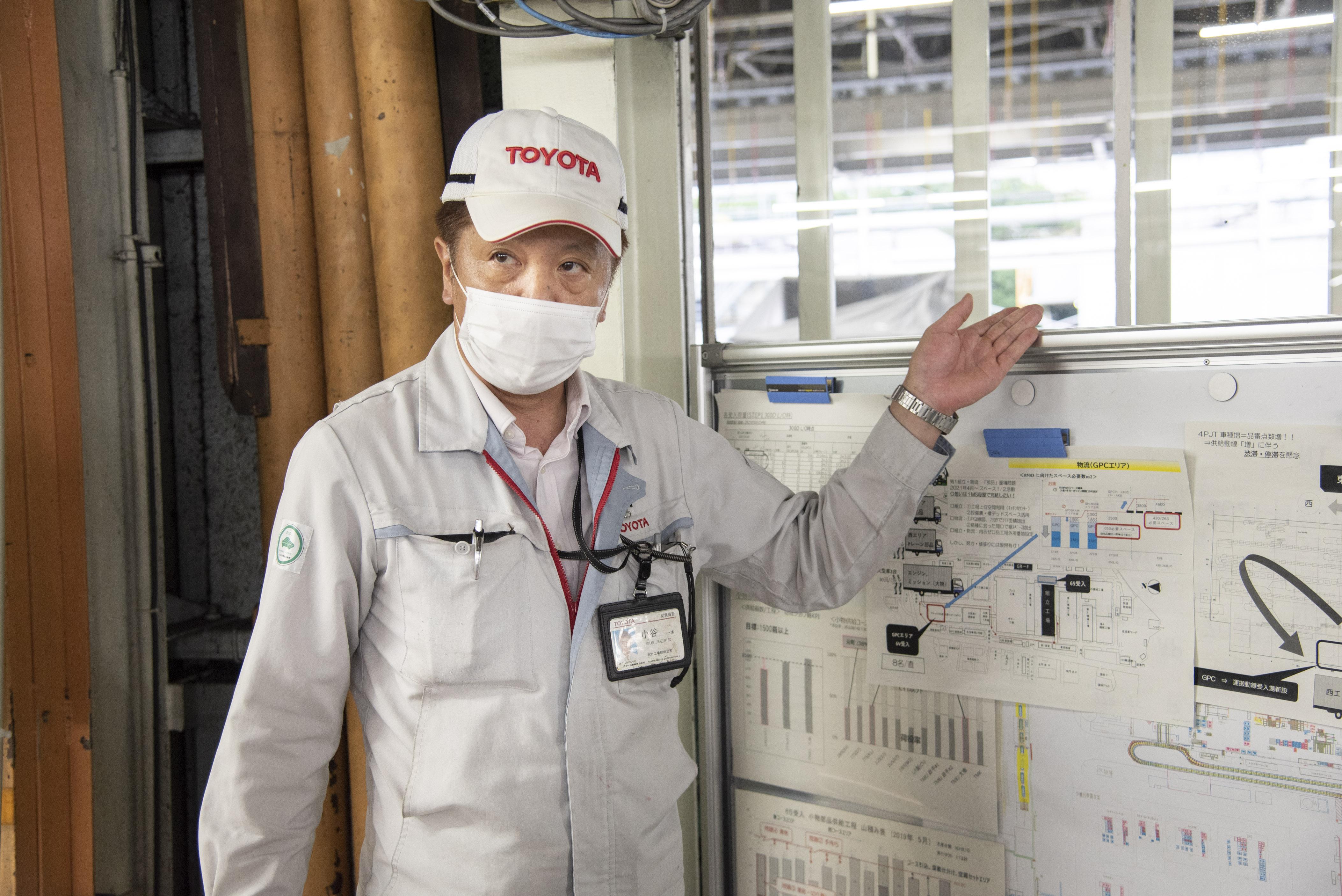
Kotani also established a training program where employees are learning new skills to handle the additional truck and forklift operations that accompany the new receiving area.
Color-coded floors a two-for-one improvement
Chassis Line 2, which assembles car platforms, immediately stands out as different from the rest. Its floor is painted in sections of yellow and green.
The yellow coloring was adopted as a visual cue to potential dangers, helping workers avoid injuring colleagues or colliding with the hangers where vehicles are suspended. As a bonus, the paint makes this section 70 lux brighter than the rest of the plant.

On this line, the work involves looking up at the underside of the car. Black cars and other dark colors presented a challenge by making it difficult to locate holes for attaching bolts and rubber components.
In the past, they would place fluorescent lights on the floor or headlamps on helmets to deal with this problem, but the bright lights actually made things harder to see.
According to Akari, changing the floor coloring has resulted in “just the right level of brightness, not as glaring as fluorescent lights.” An improvement in safety for workers has also made operations more efficient.
Executive Fellow Mitsuru Kawai made the following comment when he visited the plant.
“This line not only dispenses with powered aids such as air and motors, but also makes spaces brighter without using electricity. This is truly a carbon-neutral assembly line.”
The genba spirit handed down to new colleagues
As already mentioned, over 60% of those working on Assembly Line 1 are new to the team. This situation would demand closer communication, but the pandemic only made things harder.
Along with the drop in break time conversations, the plant shutdowns meant that many people stayed home, limiting the chances for chats in the workplace. Thankfully, the kaizen efforts undertaken during that period began to gradually bridge those gaps.
When newcomer Runa Yamazaki of the Final Assembly Division received her assignment, a senior colleague asked if she had trouble with any of the tasks; since everything was new, she said, “I was worried because I couldn’t even tell which parts were difficult.”

Watching her work, Yamazaki’s supervisors and peers helped identify awkward movements and offered advice. One such improvement was related to the portable parts containers commonly known as “bento lunch boxes.”
The assembly stages that Yamazaki handles require two types of impact drivers, the tools used to tighten bolts.
Traditionally, when the tasks using one of the impact drivers were finished, line personnel would return to the cart where parts and tools were kept, swap it for the other driver, and resume work—finishing off one car involved two return trips to the cart.
However, by punching holes in the bento boxes and adding hooks, the containers could now carry both impact drivers and parts at the same time and be secured to the car while working.
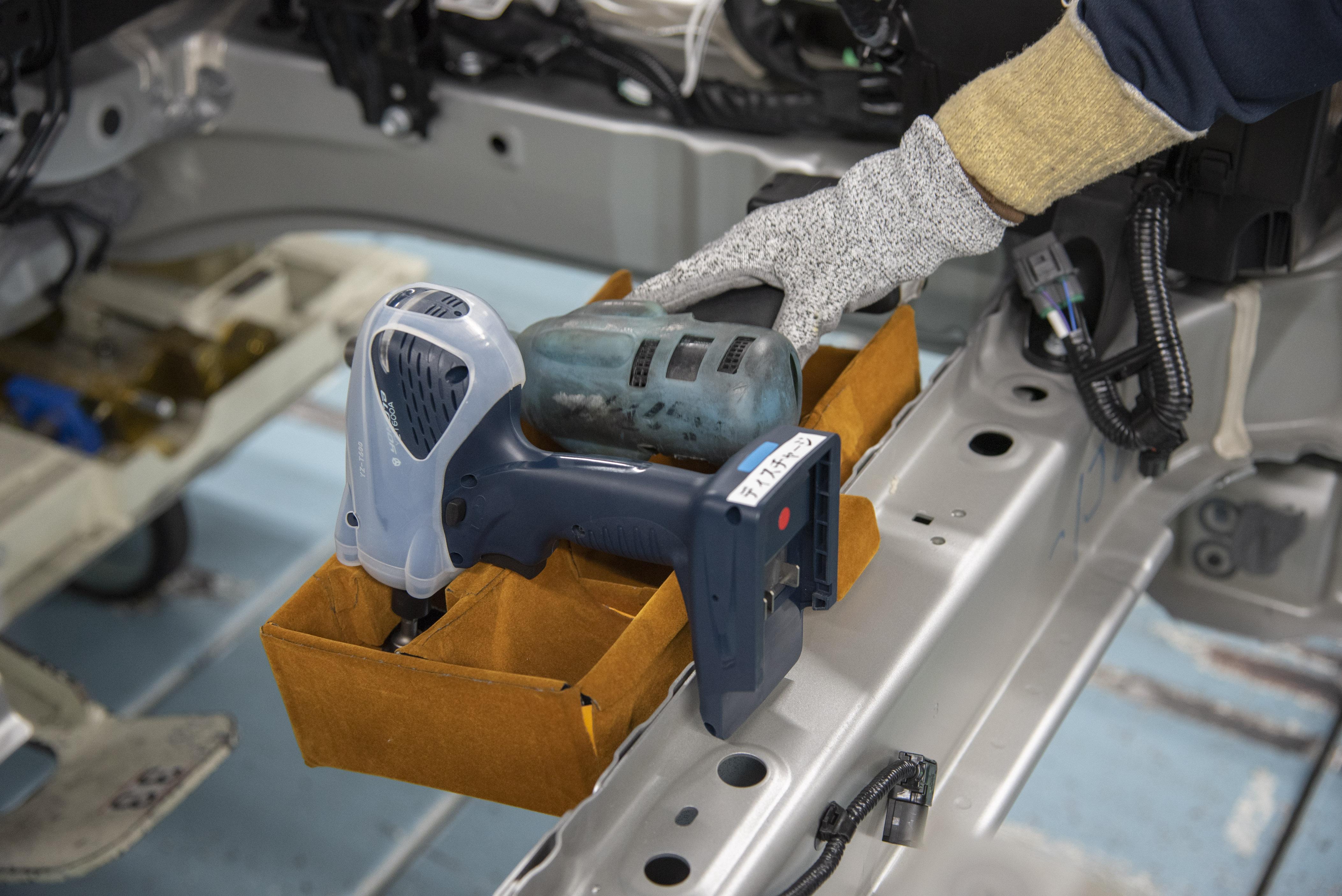
The hole sizes and the shape of the supporting point were also adjusted to keep the drivers stable. “The process not only taught me about kaizen but also helped me get to know my colleagues,” said Yamazaki with a smile.
Mamoru Katada of the Final Assembly Division, who leads the door line team, transferred to Motomachi last June from the machining section at Toyota’s Shimoyama engine plant.

Machining and assembly are entirely different jobs. Despite some trepidation, Katada has learned his role as a leader in the new workplace and taken on the responsibility of coordinating others who, like him, have no prior assembly experience.
In the face of major environmental changes, the fundamentals tend to fall by the wayside. Katada worked to raise his team’s awareness and make improvements regarding dropped objects.
On a moving line, those who panic and try to pick up dropped parts risk injury. As such, Katada reinforced the rule that a supervisor must be called when something is dropped. He also devised ways to prevent parts from being dropped in the first place.
One example is the “chameleon,” a simple mechanism that retrieves the necessary number of bolts using the power of magnets.
When an impact driver is picked up, the magnets, suspended on a line, are lowered into a parts box to grab the bolts. Returning the impact driver to its original position hoists the bolts to where they can be easily reached.
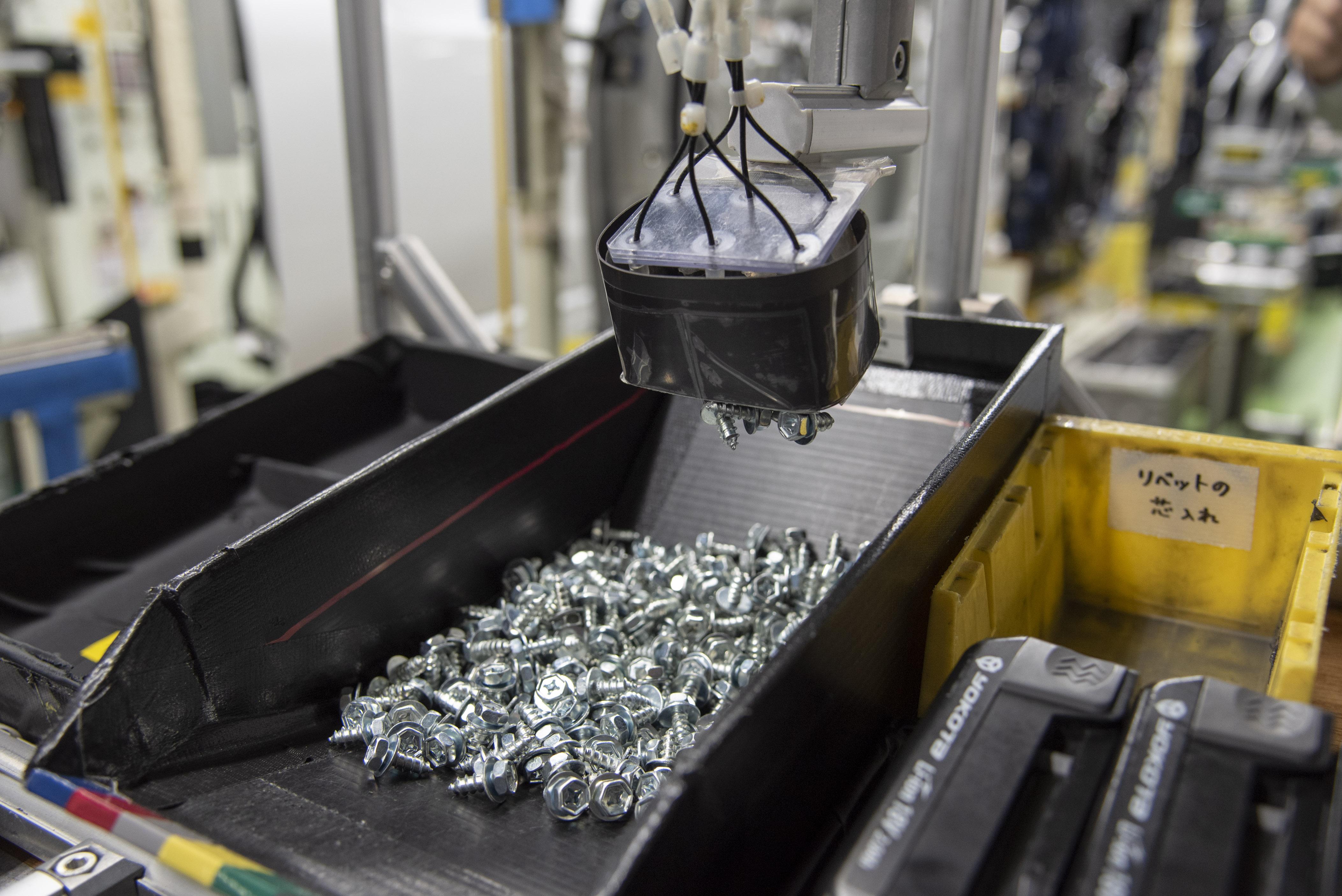
Chassis Line 2 operator Yuya Otake also came to Motomachi last June from manufacturing engines at the Kamigo Plant. He worked to improve the temporary storage area for intermediate shafts, which transmit the steering motion to the wheels.

Previously, a temporary storage area had been set up in a fixed location, meaning the bulky parts had to be carried long distances.
With both hands occupied, workers risked falling over and injuring themselves or damaging the parts. This arrangement also often meant intruding on colleagues working on other stages of the assembly process nearby.
To resolve this situation, the team introduced a mechanism that allows the shaft to slide to the work position under its own weight.
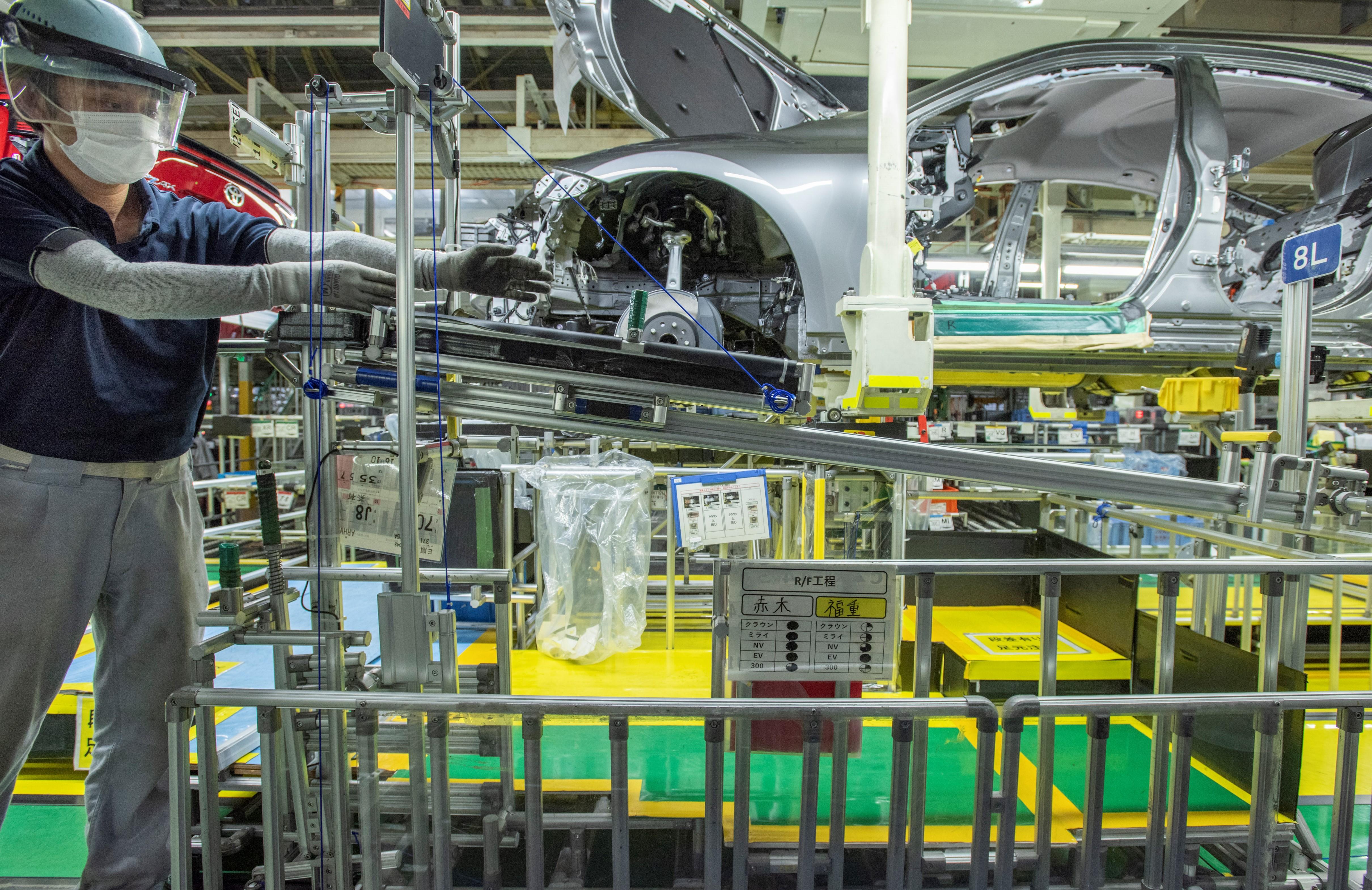
Otake shared his ambition for further kaizen, saying, “People are full of different ideas. I too want to come up with various ideas for improvements.”
Instrument panel line group leader Kenji Nagano transferred into the role in January from a different post in the plant.

“We cannot build quality cars without ensuring that our people understand the purpose of what we are doing.”
Embracing his supervisor’s lesson that simply carrying out preset tasks is not enough to maintain high-quality standards, Nagano began by studying the workplace’s background of goal setting and quality initiatives until he had a solid understanding.
He then shared his findings with those in his group. As their understanding deepened, their reactions in meetings began to change.
Whereas at first people just listened, the second time around some began to take notes; after a few sessions, group members began raising their hands to offer responses.
Nagano was also hopeful in his outlook. “I think we’ll see the results once the line is running. If new problems arise, we’ll go back to the basics and drill those ideas into our team to ensure future projects are successful.”
A vast project sustained by steady effort
With its diverse personnel, the Motomachi Plant is taking on an unprecedented challenge by starting up four projects and running multiple models on the same lines in a year.
What sustains these efforts is not state-of-the-art equipment, but rather the steady improvements made by every genba member.
“We’ve modified our processes time and again, going from 100 cars per day one month to 150 more/less the next, six to seven times a year,” says Akari. “Each time, the equipment must be rearranged. That might be fine if the takt times and processes don’t change, but our plant doesn’t work like that.”
There’s no telling whether the things that worked well on stopped lines will all go smoothly when operations resume.
Even so, the Motomachi Plant has drawn on the expertise and ingenuity of its people to overcome production swings, model changes, and other environmental shifts.
The unwavering pursuit of kaizen continues out of a commitment to the colleagues who work at Motomachi, the suppliers who provide parts, and above all, the customers who eagerly await their new cars.