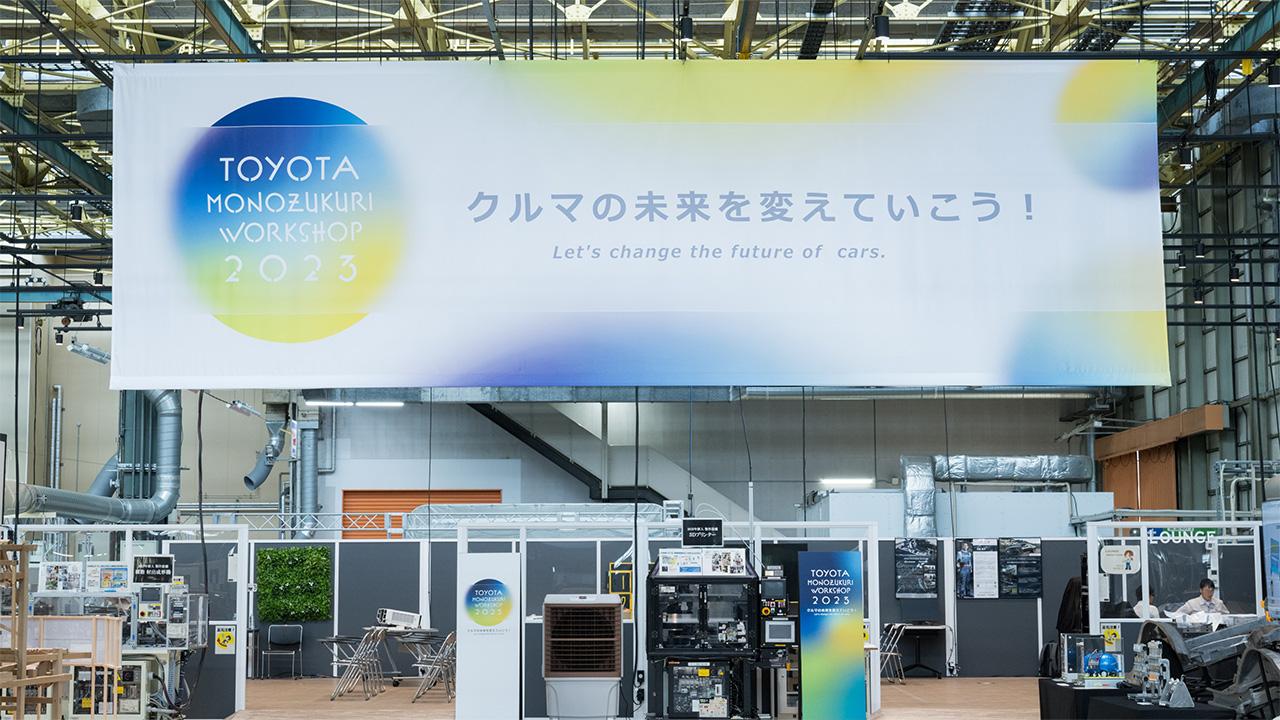
Toyota seeks to halve the number of manufacturing processes through its renowned craftsmanship and technological innovations. The company showcased the monozukuri genba, giving rise to advanced technologies that will change the future of cars.
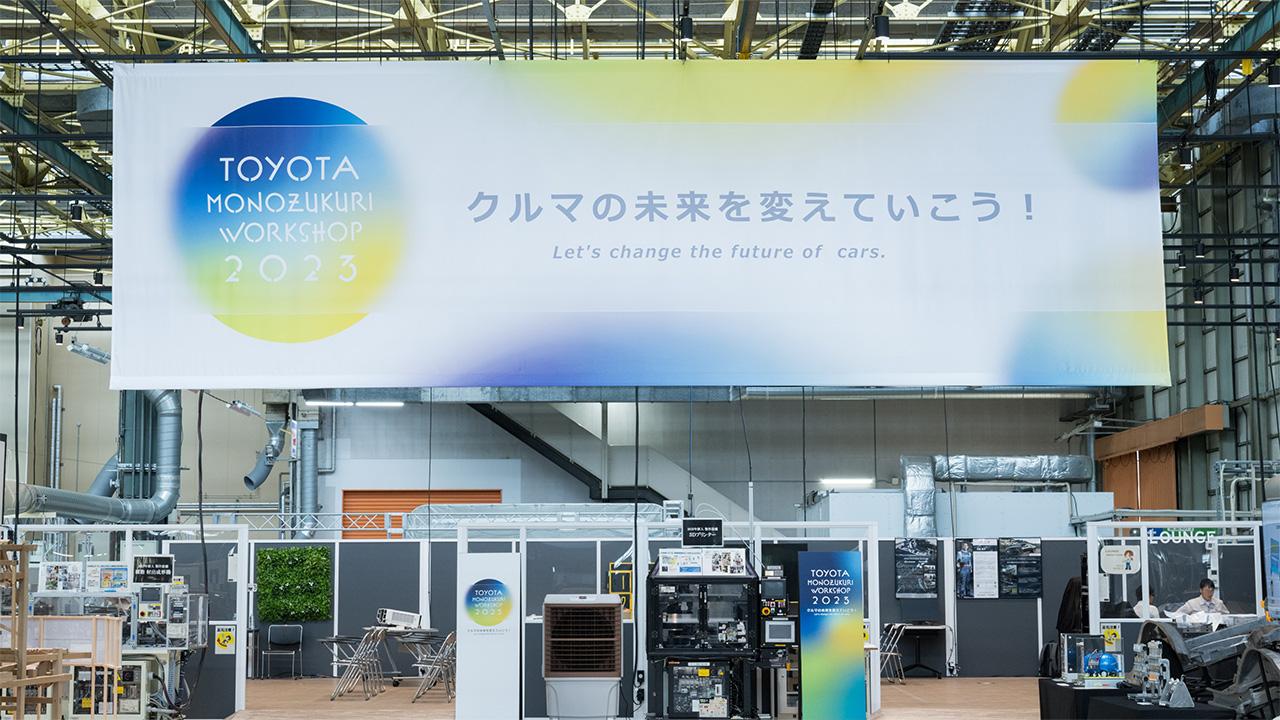
Massive parts emerging from the steam of a casting machine. Battery cells stacked with perfect precision. Skilled craftsmanship reproduced through augmented reality…
In September, Toyota invited the press into three of its plants—Teiho and Motomachi in Toyota City, Aichi Prefecture, and Myochi in Miyoshi, Aichi.
The event called the Monozukuri Workshop, showcased manufacturing that brings to life the advanced technologies presented at June’s Technical Workshop.
The Teiho Plant is a startup hub that creates “something out of nothing,” providing the equipment and production methods that underpin carmaking, along with the manufacturing to lead the way in new mobility.
Myochi is a casting plant that combines expert craftsmanship with innovative technology. It is also the birthplace of engine parts for motorsports, where a millisecond makes all the difference.
Finally, Motomachi is a multi-pathway mass production plant where nine different models, including hybrids (HEVs), battery electric vehicles (BEVs), and fuel cell electric vehicles (FCEVs), are built on a single line.
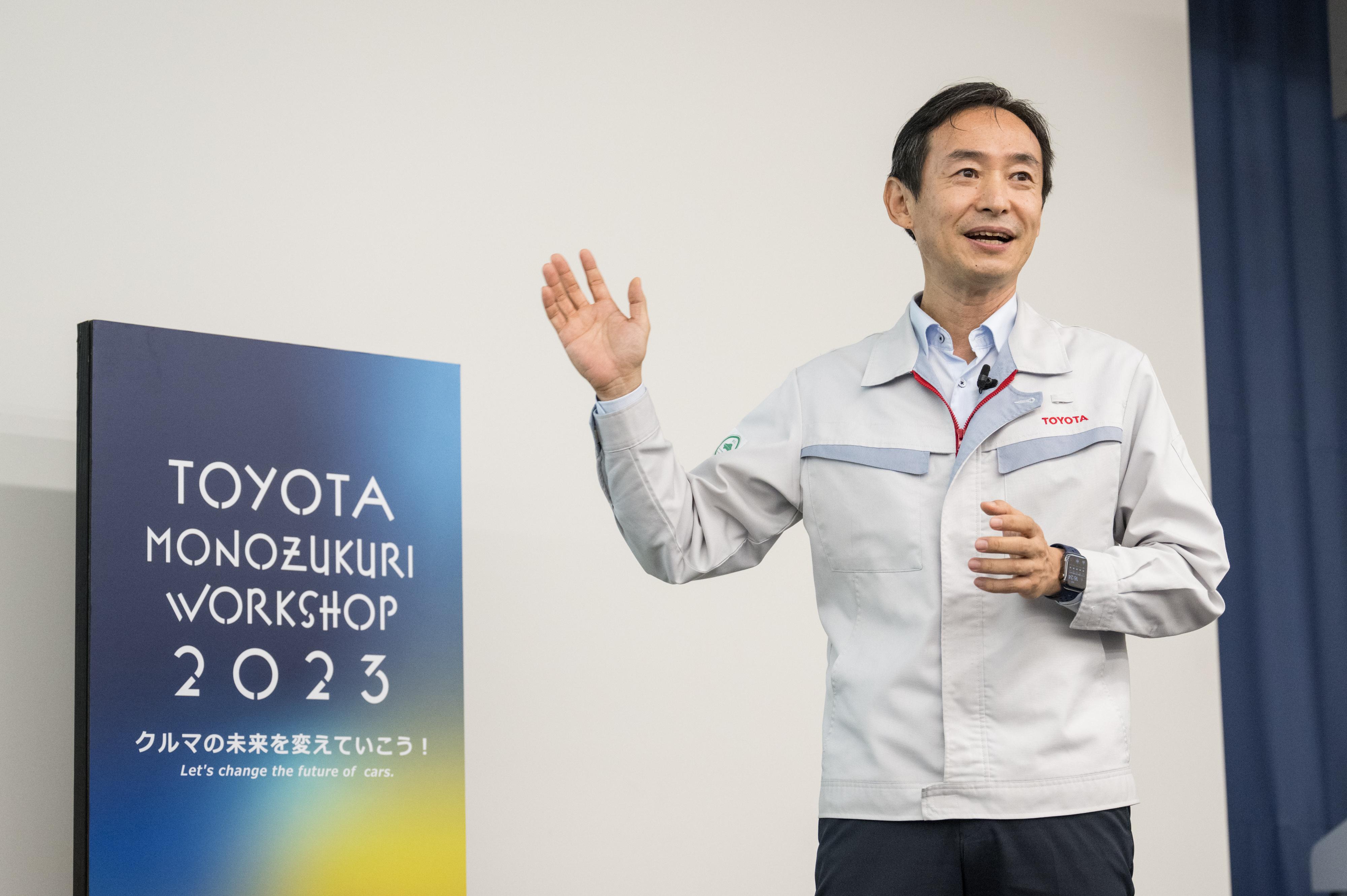
Kazuaki Shingo, who heads Toyota’s production as Chief Production Officer, shared his vision saying, “We will halve processes using Toyota's skills and digital and innovative technology, eliminate the barriers between development and production to provide new mobility quickly, and work to resolve issues at the foundation of monozukuri, such as factory carbon neutrality and logistics.”
Toyota’s monozukuri continues to evolve through the fusion of inherited skills and digital tools. Here we share some of the many genba examples presented at the workshop.
A next-generation battery line to drive the future of cars
At June’s Technical Workshop, the main drawcard proved to be Toyota’s battery technologies, starting with the all-solid-state battery. The necessary preparations are now being made by the Teiho Plant in the lead-up to mass production.
The plant has long been manufacturing the equipment used to create new products, including motors, batteries, and fuel cells. This time too, Teiho is tasked with everything from equipment design to assembly and installation at mass production plants.
Toyota is developing all-solid-state batteries, which offer faster charging and longer range, with the aim of commercialization in 2027-2028. Alongside the product itself, mass-production methods are also currently in development.
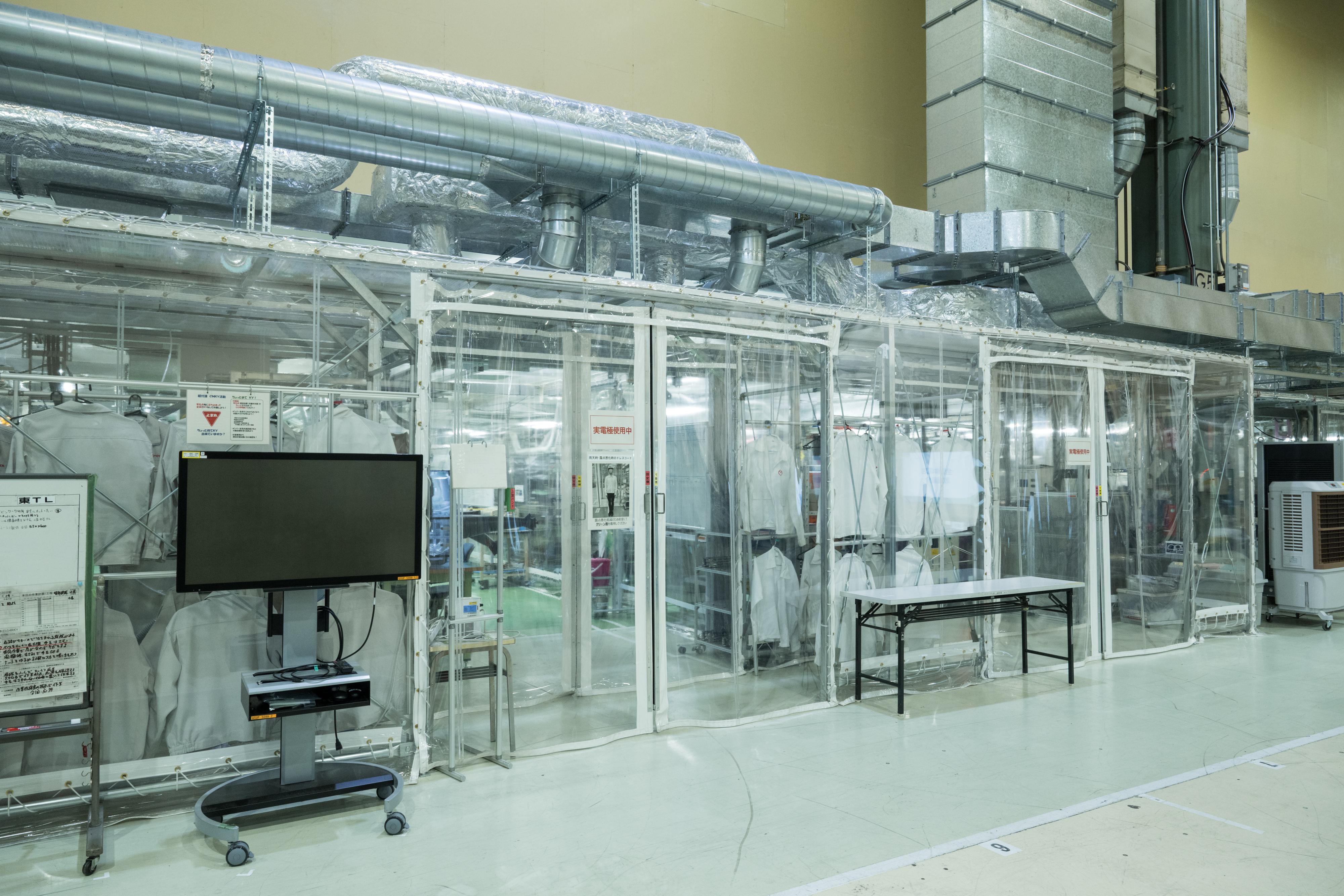
Current battery production consists of three main processes: materials processing, battery processing, and battery assembly.
While the sequence is the same for all-solid-state batteries, to ensure the battery’s performance, the assembly process requires high-speed, high-precision stacking that doesn’t damage the materials. This is one of the key technologies for mass production.
The equipment developed by Toyota solves this problem by making the pallets that carry and receive batteries all move at the same speed; that is, at zero relative velocity.
In addition, the pallets and machinery are equipped with karakuri mechanisms to prevent misalignment as batteries are passed through. Together, these solutions enable the high-speed, high-precision stacking that is crucial for mass production.
Also on display were production facilities for the popularization version of Toyota’s next-generation battery, which will feature a supersized bipolar structure.
In a regular battery, individual current collectors are coated as either an anode or cathode, with one of each paired to make a set (see diagram at left below). By contrast, every current collector in a bipolar configuration is coated with an anode and a cathode on opposing sides, making for a simpler structure that requires only one-third as many components (diagram at right).

At the same time, material costs will be reduced by using lithium ferro phosphate (LFP) for the cathode in place of rare metals such as nickel and cobalt.
To compensate for lower energy density and maintain battery capacity, the current collectors will have a thicker coating of LFP, using the space gained through employing a bipolar structure with fewer components.
However, to make these batteries a reality, Toyota must overcome three difficulties: applying the material evenly, doing so at high speeds, and simultaneously sealing all the cells. What’s more, all this needs to be achieved in batteries large enough to power a car.
In tackling these challenges, the company is drawing on 26 years of battery production technologies honed through its HEVs, along with bipolar nickel-metal hydride battery technology and expertise, precision coating used for FCEVs, and various digital technologies.
Changing the plant environment with self-propelled assembly lines
In June, BEV Factory President Takero Kato introduced the concept of “halving BEVs.”
“New modular structures and self-propelled assembly lines will halve production processes and plant investment,” he declared. “In addition, we can halve production preparation lead times through the potential of digital twins*.”
*A method that involves digitally reproducing an identical version of the real world for use in simulations, etc.
The new modular structure presented at the Motomachi Plant entails dividing the underbody (the lower part of a vehicle’s body, including the front frame and the cabin/trunk floor) into three sections—front, center, and rear—each fitted with its own parts.
This approach is expected to improve work efficiency since workers will no longer need to climb inside a vehicle during assembly.

After parts are assembled onto each module, and the three sections are combined, the car proceeds forward autonomously. With this new vehicle structure, seats and other components can be mounted before the roof and side panels are attached, simplifying the designs and operations of robots and other equipment.
This self-propelled assembly line utilizes the vehicle control and sensor technologies that Toyota has cultivated through the development of autonomous driving.
Cameras throughout the plant track the cars, keeping them moving along the set route at 0.36 km/h.
Eliminating the need to convey vehicles offers greater flexibility in plant layouts. The system also saves billions of yen in capital investment and drastically shortens the years-long lead times for switching to new models.
A simplified line concept using unmanned transport robots has already been trialed in part of the welding process for the NOAH and Voxy models, providing feedback to assist with issues in the development of next-generation BEV equipment.
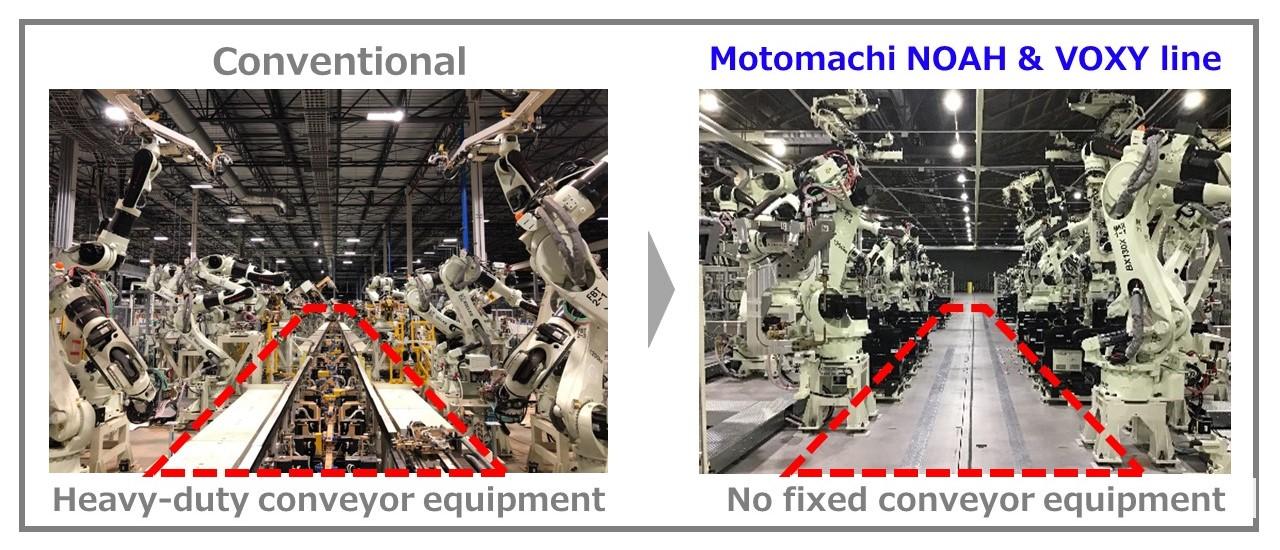
An employee involved in the development outlined the aim as “helping workers while boosting competitiveness by shortening lead times and cutting costs.”
For plant equipment and mass-produced vehicles alike, Toyota has brought every step of the process, from development to production, in-house. Drawing on these strengths, the company is striving to simplify and automate operations to minimize the need for heavy transport machinery and respond more flexibly to change.