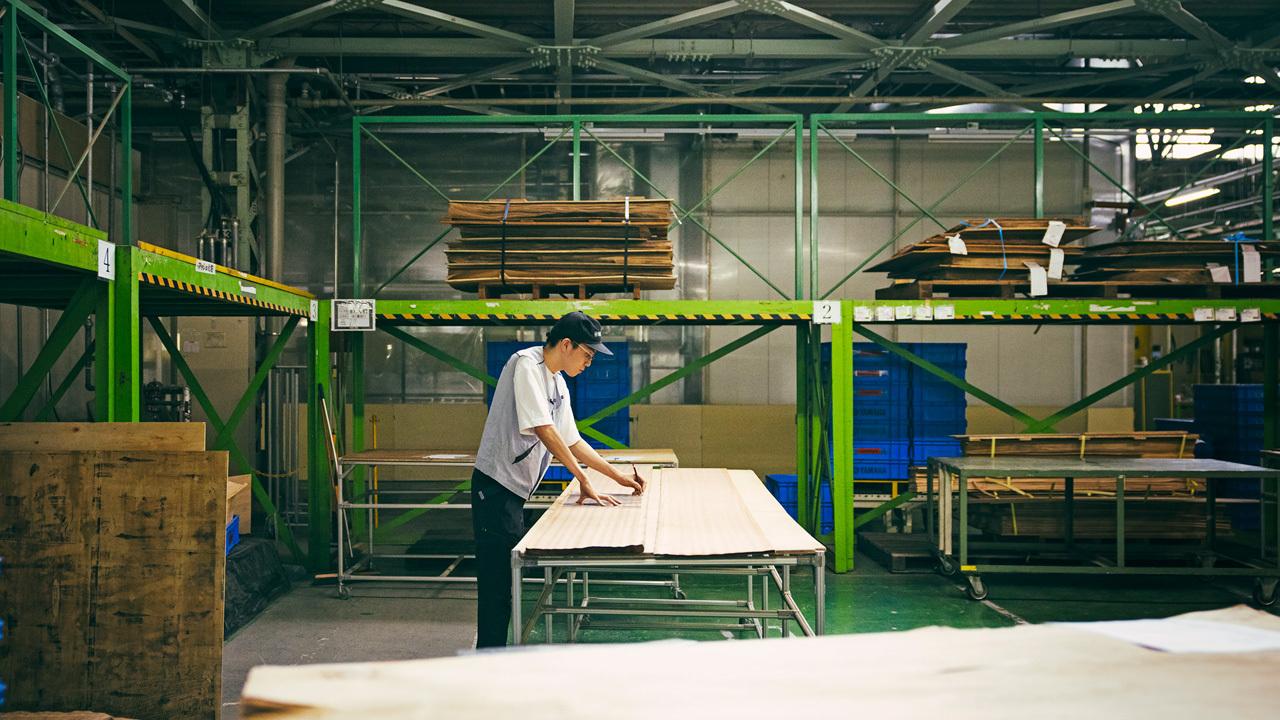
This is an ongoing series looking at the master artisans supporting the automotive industry. In Part 1 of the 17th installment, we speak with the sumikake (wood selection) master behind the new Century's beautiful wooden panels.
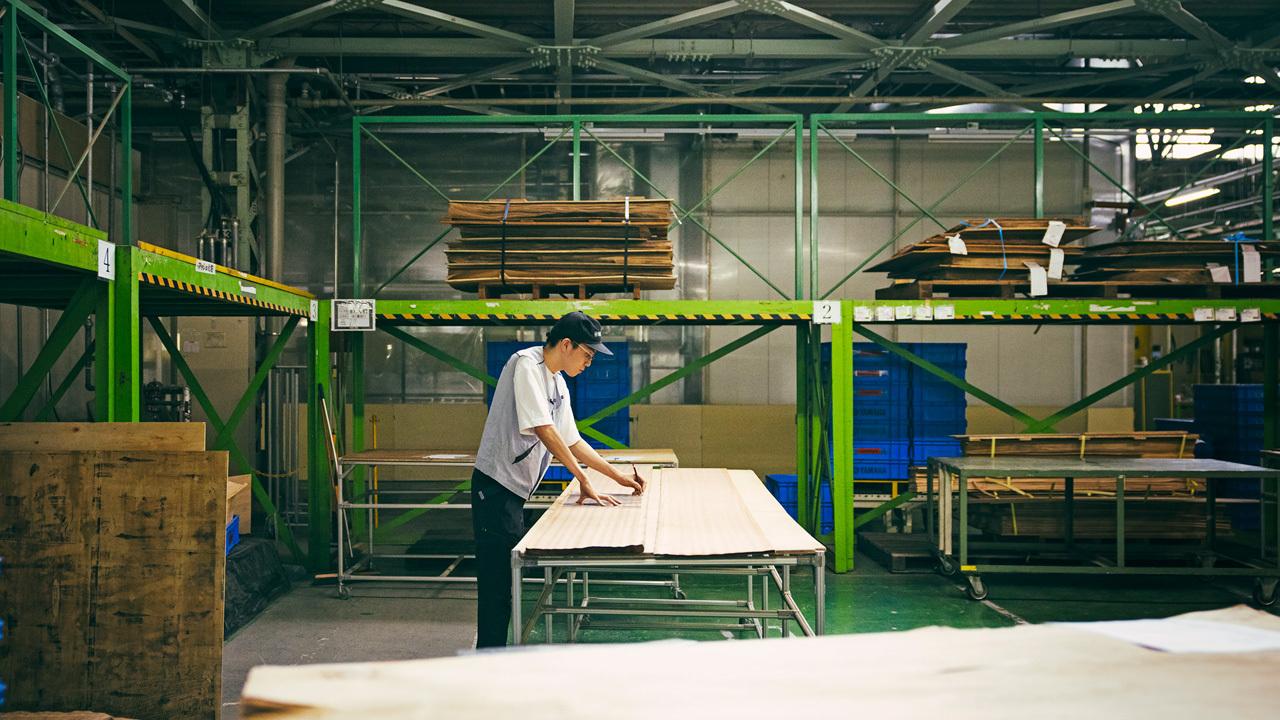
Handwork still plays an important role in today’s car manufacturing, even as technology like AI and 3D printing offer more advanced methods. This series features the craftsmanship of Japanese monozukuri (making things) through interviews with Toyota’s carmaking masters.
To mark the recent launch of a new Century, this is the fourth in a special five-part series showcasing the craftspeople who work on the model.
One highlight of the Century’s interior is its natural wood decorative panels. We interviewed two craftsmen from Yamaha Fine Technologies who were involved in their development and production.
In Part 1, we shine the spotlight on Tatsuya Kaneko, a master of sumikake who selects the wood veneer used for decorative panel surfaces.
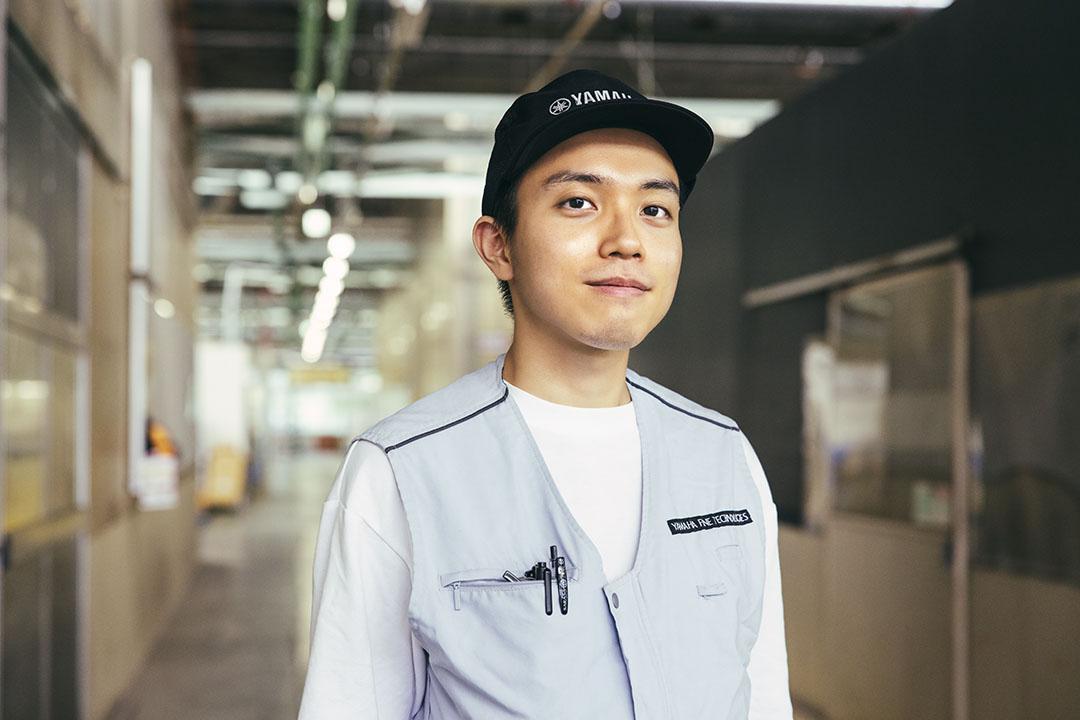
#17 Tatsuya Kaneko, a sumikake master with a keen eye for selecting wood paneling veneers
Production Department, Car Parts Division, Yamaha Fine Technologies Co., Ltd.
What is sumikake all about?
Decorative wood panels have been a regular feature in vehicle interiors since the days of classic cars. They offer a fine example of the rich stylistic and technical legacy that cars inherited from their horse-drawn forerunners.
Among a slightly older cohort of car enthusiasts, quite a few may associate wood paneling with the instrument panel of the Toyota 2000GT. In the interest of full disclosure, those stunning wooden panels that stretch out before the driver were actually the work of world-renowned musical instrument manufacturer Yamaha.
There are in fact two broad types of wood panels: so-called faux wood panels, which are coated in films or resins that emulate natural woodgrain patterns, and genuine wooden veneer panels.
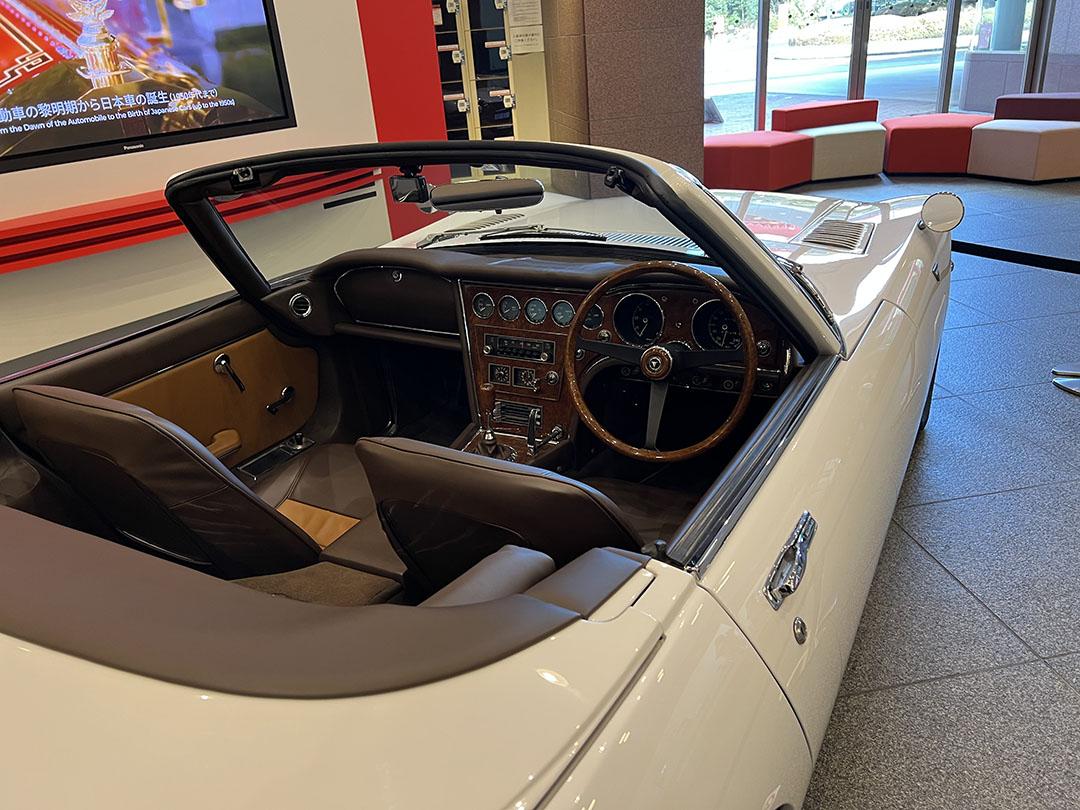
As mentioned, Yamaha began working on wood panels for the Toyota 2000GT in the late 1960s, applying woodworking and coating techniques cultivated through crafting pianos. Then, in the late 80s, a project to develop decorative panels for the first-generation Lexus LS led the company to set up a car parts department.
This unit was later moved to a group company, Yamaha Fine Technologies, becoming the Car Parts Division that has since helped to develop and produce wood panels for Toyota (including the current third-generation Century sedan), Lexus, and various other car manufacturers in Japan and abroad.
On board the new Century, the instrument panel and the model’s traditional tower console are trimmed with chic pinstripe woodwork. The development and fabrication of these decorative panels were also the handiwork of the Car Parts Division.
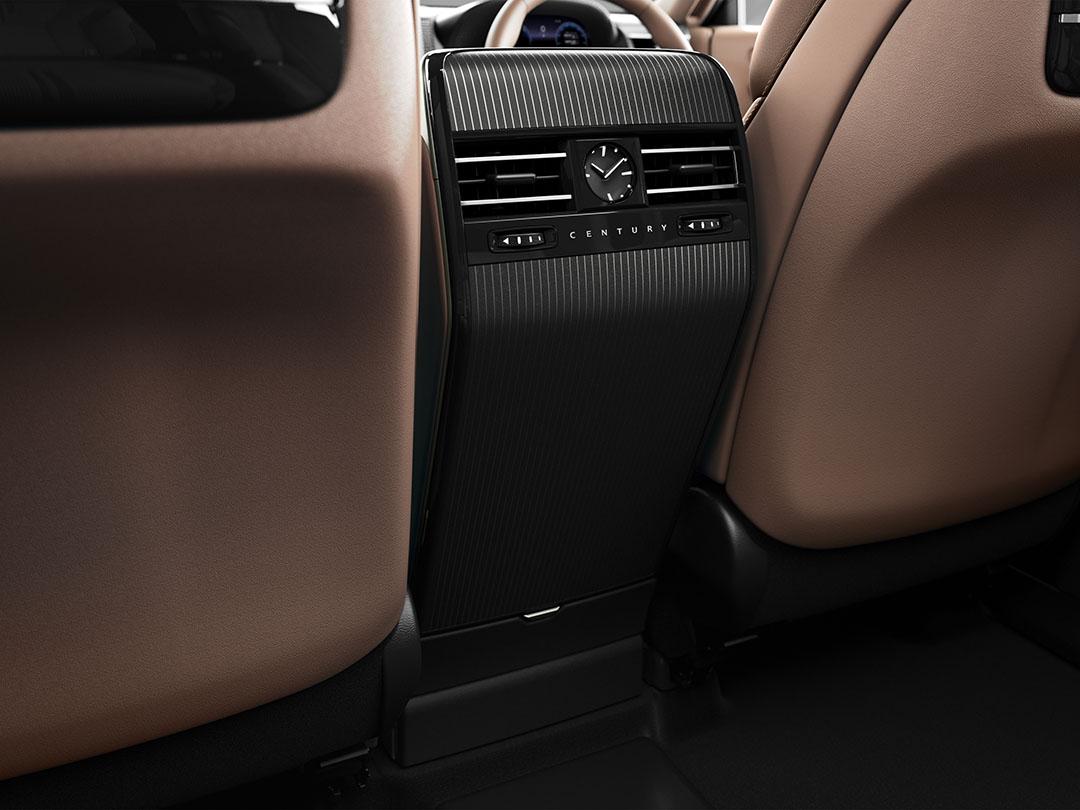
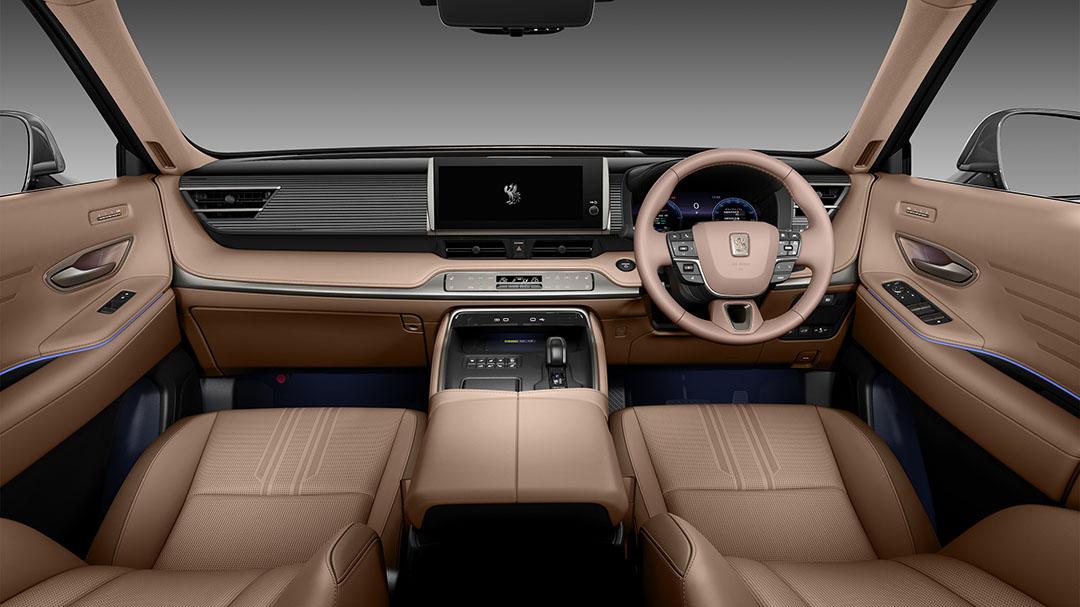
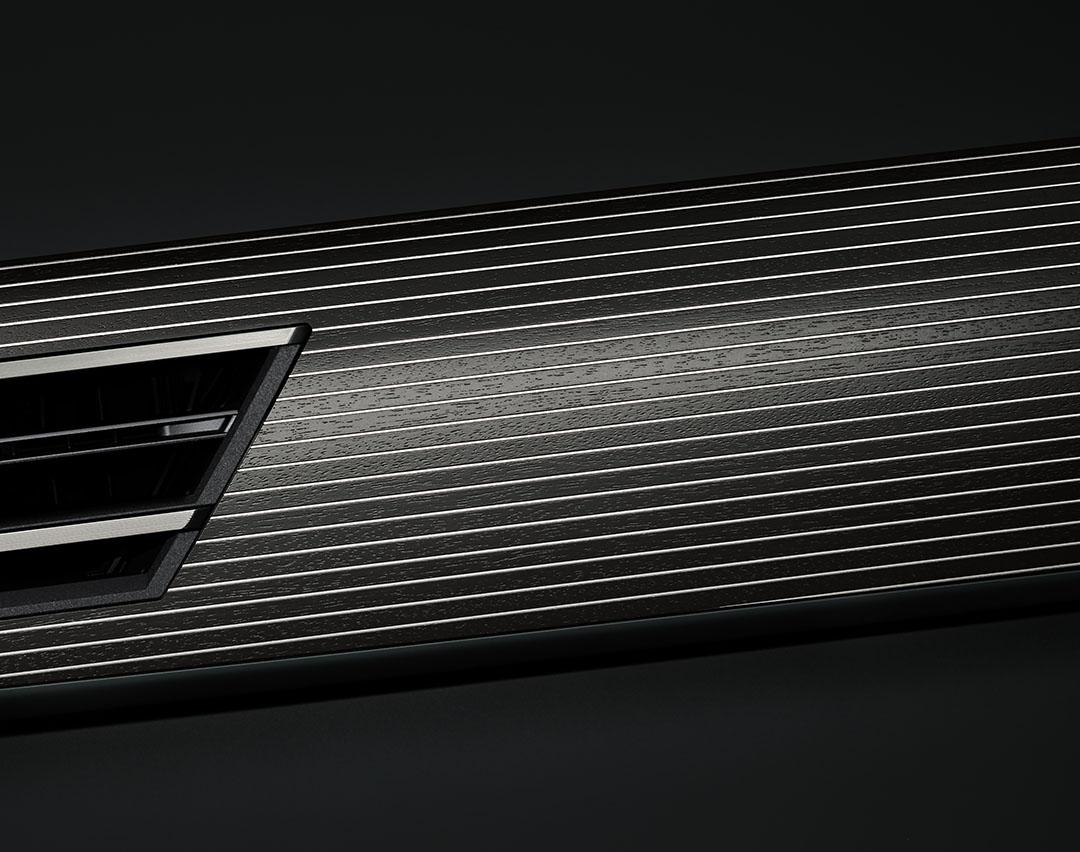
Within this process, Kaneko’s task first involves purchasing the timber used in wooden decorative panels—or more precisely, the veneers that have been sliced to a thickness of around 0.2 mm—from domestic and overseas suppliers.
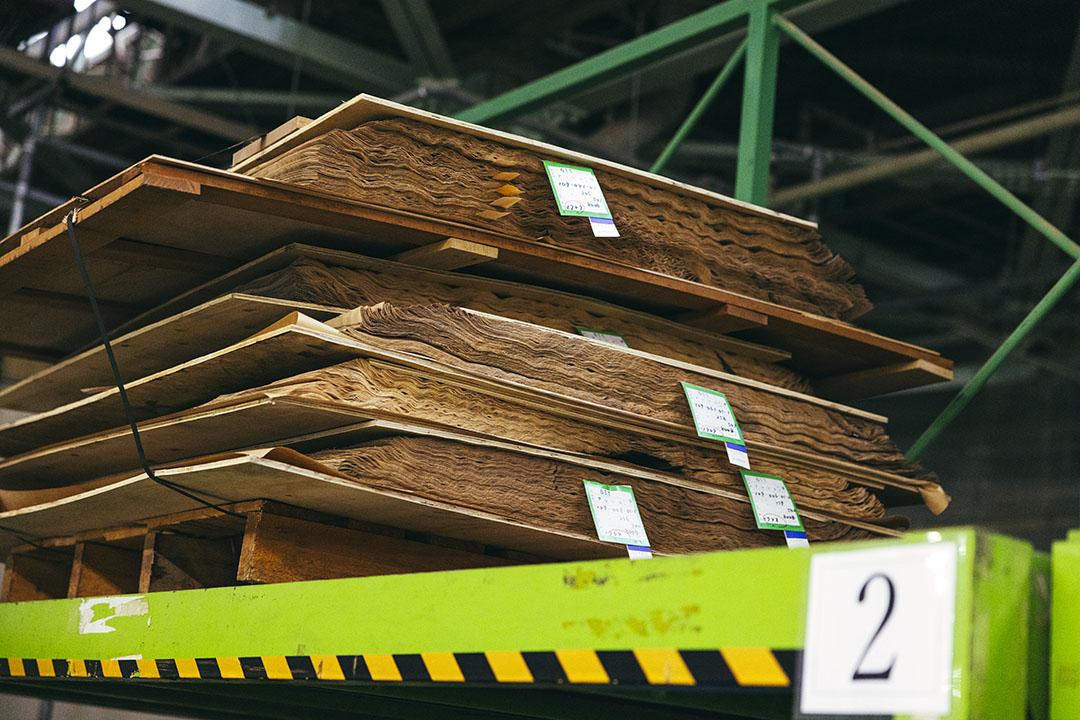
From there, Kaneko checks the procured veneer sheets against the shapes of decorative panel parts, selecting those with the nicest grain while avoiding any knots, chips, or other imperfections. This sorting process is known as sumikake.
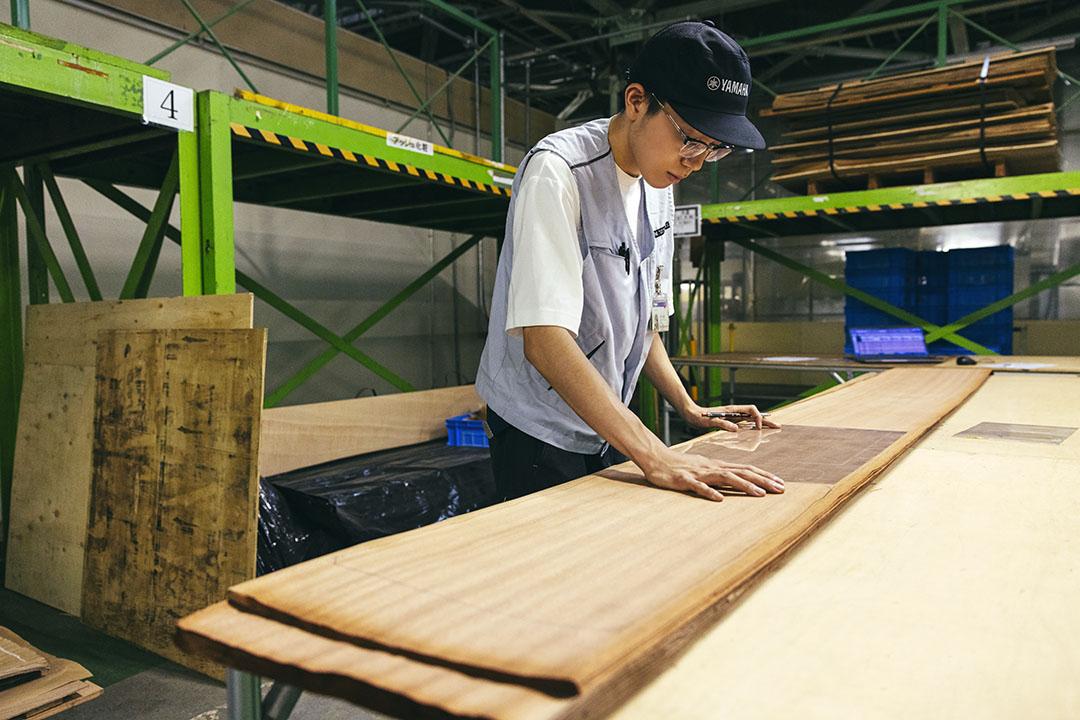
Kaneko
The term sumikake comes from the ink (sumi) lines that carpenters make when selecting timber, but in practice, I use pencil to mark out the veneer.
With natural wood, you inevitably get knots and splits. When visiting suppliers, we visually inspect the grain to select timber with the fewest defects carefully. Then we check it meticulously again during sumikake.
Even if there aren’t any flaws, we won’t use sections where the grain patterns aren’t nice, for example, or there is little patterning to begin with.
Without much patterning, the piece won’t look cohesive when finished as a decorative panel. The texture also becomes harder to see with each layer of paint applied.
The key in sumikake is to visualize the finished decorative panel.
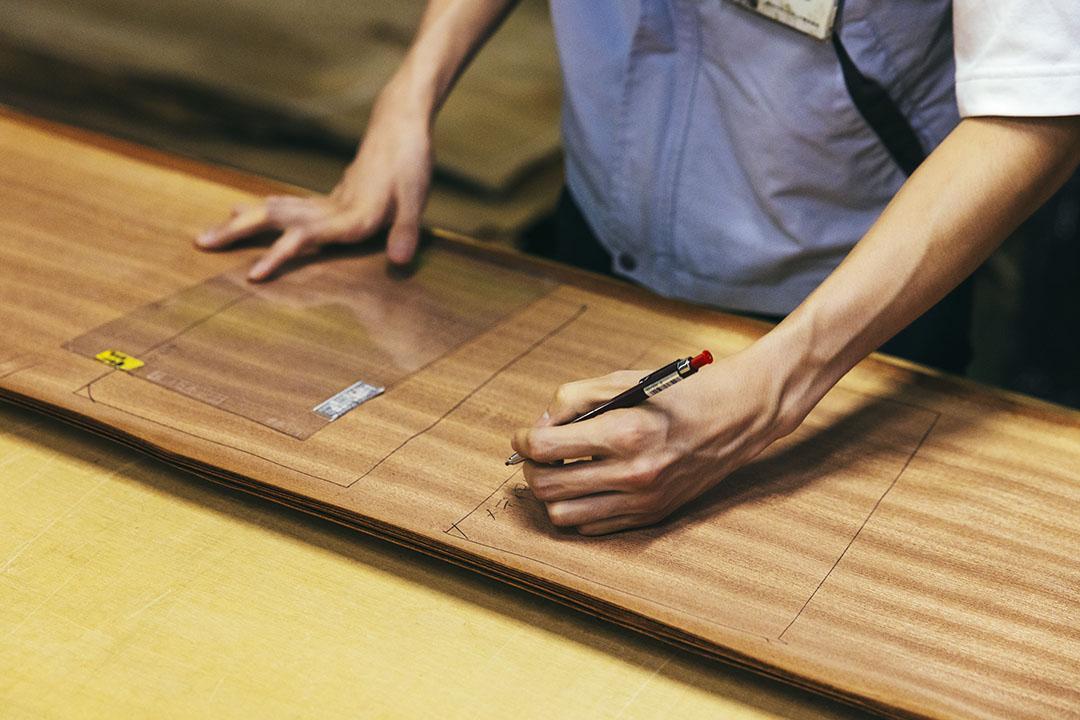
Selecting designs that appeal to customers’ sensibilities
According to Kaneko, for veneers with intricate grain patterns, the sumikake process may leave as little as 20% of material usable for parts.
The wood he uses also comes from various tree species, including ash, walnut, and maple. When performing sumikake on such a wide array of wood, Kaneko underscores the need to be well-versed in the aesthetics and characteristics of their different grain patterns.
Since grain patterns and imperfections both vary by tree species, when he was first tasked with sumikake, Kaneko struggled to distinguish patterning from knots and other flaws.
He says sumikake is particularly challenging with trees like ash, which has a pronounced grain and is used in models including the Lexus IS, and claro walnut, commonly found in the wood paneling of European luxury cars.
Kaneko
Despite spending more than eight hours a day with the veneers for at least my first year of sumikake work, I didn’t feel confident handling it alone.
The only way forward was to develop a discerning eye by observing a range of wood grains from various tree species, checking with senior colleagues to see which patterns worked best and which were unusable, while also learning what interior designers and car owners were looking for.
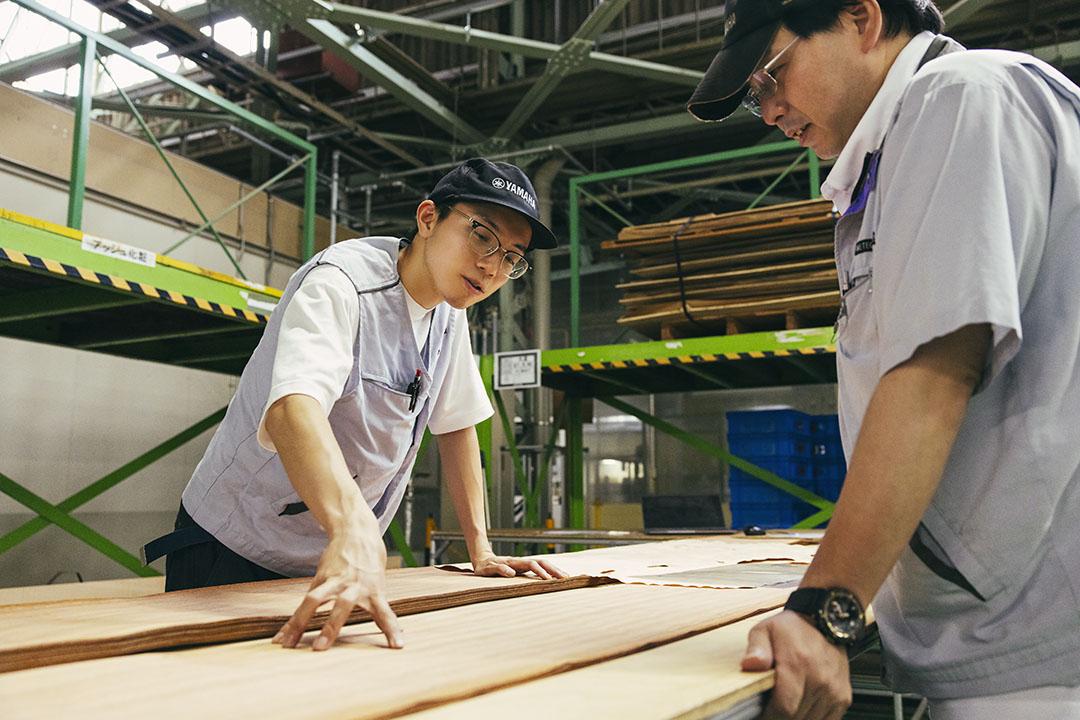
The sumikake is about refining one’s own sensibilities to select designs that appeal to the sensibilities of customers. This, says Kaneko, makes the job hard for robots or computers to replace. On the contrary, as a highly individualized task, it requires a team effort to control quality and improve accuracy.
Kaneko’s team manages this through weekly review sessions that bring together the staff in charge of sumikake and quality control. Here, veneer samples with various grain patterns are used to check that everyone is on the same page when it comes to judging what is acceptable and what is not.
Quality control staff also check every sheet of veneer that is procured and undergoes sumikake by Kaneko and his colleagues. Sharing data on rejected veneer materials among the team serves to improve the accuracy of quality control.
Lexus LS wood panels spark a connection
Born in 1997, 26-year-old Kaneko loves building plastic models and other things with his hands, a passion that led him to a technical high school in his hometown of Hamamatsu City, Shizuoka.
When searching for a job after graduation, he learned about the Car Parts Division at Yamaha Fine Technologies and applied to the company because it offered the chance for “hands-on monozukuri,” including woodworking and painting.
Kaneko
I saw a Lexus LS, which was launched in 2006, when I was visiting a used car dealer with my father when I was in high school.
The interior wood paneling was what’s known as birdseye maple–named for its distinct pattern–and it left a strong impression.
I learned that these wooden panels were the work of Yamaha Fine Technologies, which made me very keen to join the company.
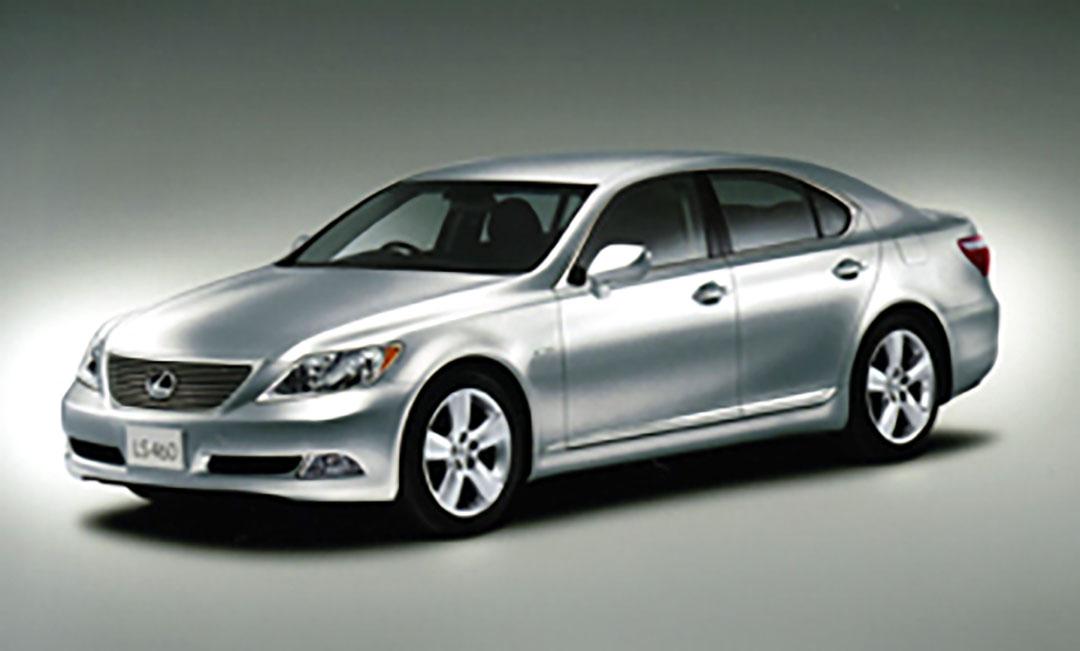
Given this background, Kaneko recalls how thrilled he was to be placed in charge of the Century, Toyota’s most prestigious model.
Kaneko
For the new Century project, the interior design theme of “luxurious simplicity” was shared in advance, even with those of us handling the sumikake.
The wood we use for the veneer is known as sapele. In contrast to trees like walnut, for example, which have bold, prominent grain patterns, the neat, straight grain gives it a very subtle elegance.
This timber exemplifies luxurious simplicity. I’m taking even greater care with sumikake than usual, so that discerning customers who appreciate genuine wood can enjoy the beauty of the decorative panels when they see the instrument panel and tower console up close.

The ideas behind the new Century’s decorative panels
Generally, decorative panels are coated with a high-gloss finish, similar to the sheen of a piano body. For the new Century, however, designers opted for an “open pore” finish that deliberately showcases the vessels and other unique textures of natural wood.
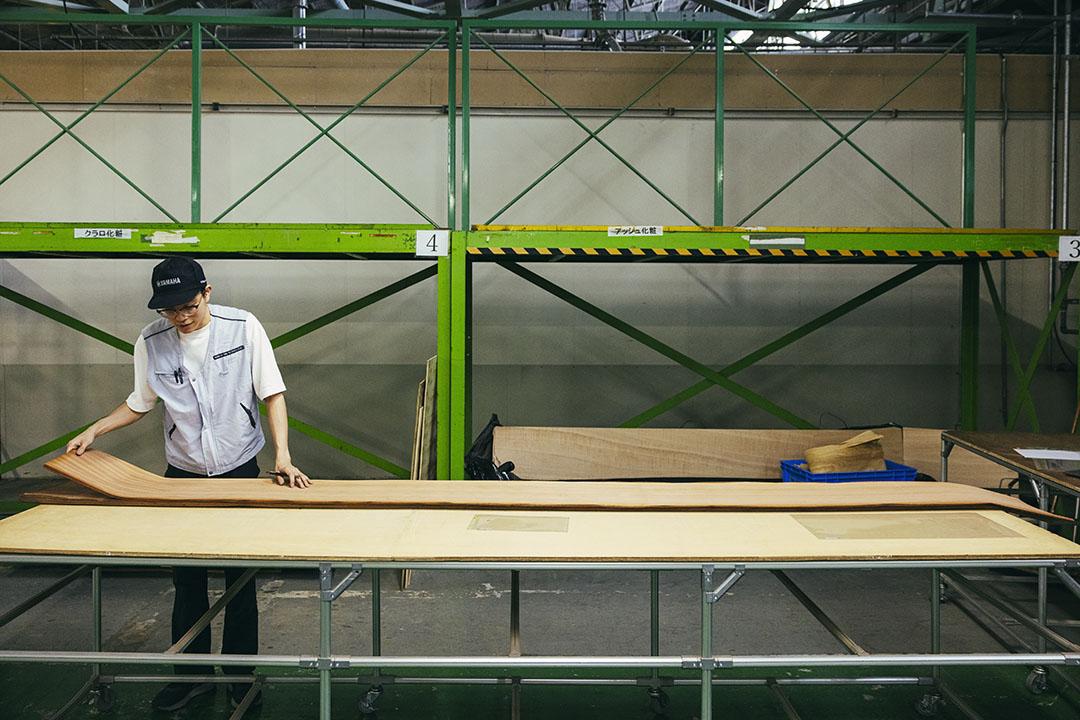
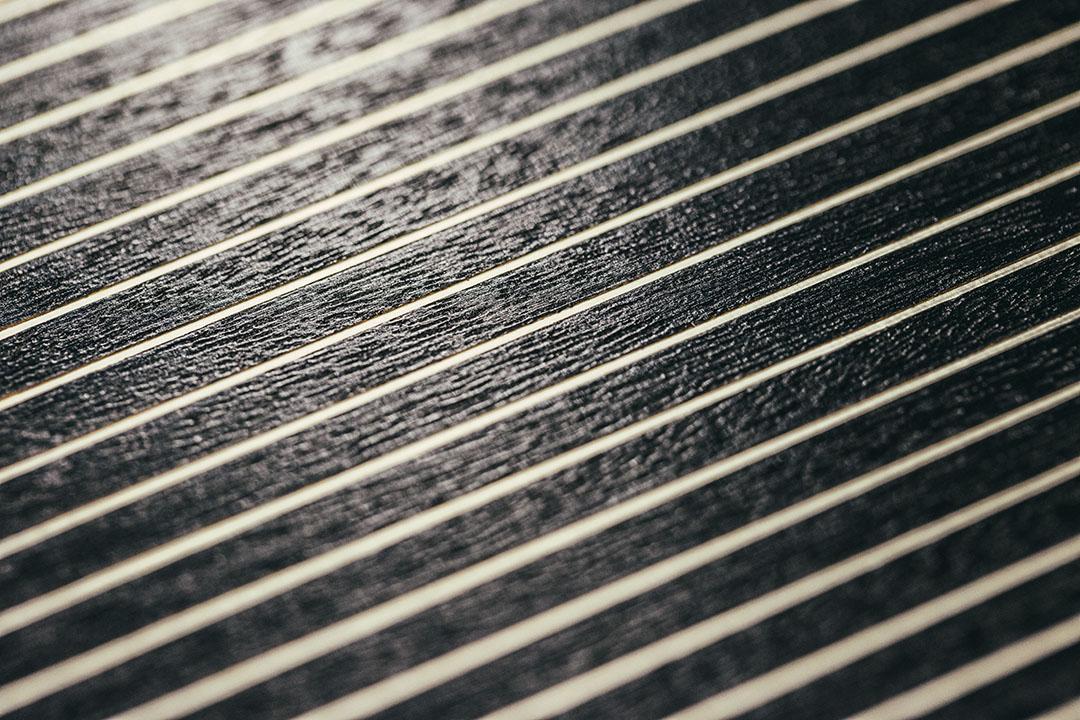
The pinstripe pattern is created by adding thin aluminum lines to the wood veneer.
In the sumikake process, Kaneko says he pays particular attention to the arrangement of vessels to make the aluminum lines appear straighter, with greater clarity.
Kaneko
Nowadays, faux wood treatment technologies have gotten so good that, at a glance, the average person can’t tell a faux wood panel from a real one.
That said, natural wood has an allure that faux wood can never have, such as the way shading contrast shifts with the viewing angle.
I want to continue devoting myself to this craft so that I can share the wonder of natural wood with customers through decorative panels.
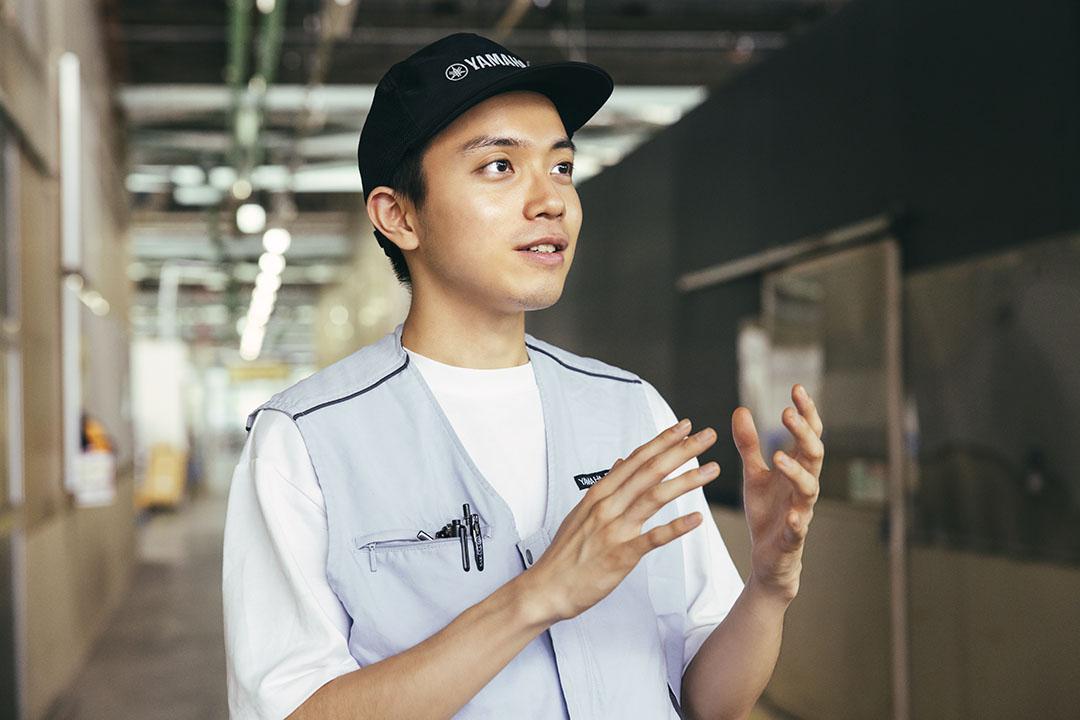
For decades to come, Kaneko’s sumikake work will live on in the wooden panels that form part of the interiors of Century and Lexus vehicles. As a craftsperson, he says this gives him a great sense of fulfillment.
As an indispensable element of these elegant, inviting interiors, the decorative panels personally selected by Kaneko will no doubt continue to bring smiles to the customers on board.
Part 2 will feature a master decorative engineer who was involved in all aspects of the new Century’s wooden panels, from suggesting the type of wood to development. He tells the inside story of how countless hurdles were overcome to turn vision into reality.