
An ongoing series looking at the master artisans supporting the automotive industry. For the 15th installment, we speak with a master craftsperson who assembles parts with no deviation from design values.

Handwork still plays an important role in today’s car manufacturing, even as technology like AI and 3D printing offer more advanced methods. This series features the craftsmanship of Japanese monozukuri (making things) through interviews with Toyota’s carmaking masters.
To mark the recent launch of a new Century, this is the second of a special five-part series showcasing the craftspeople who work on the model.
We spotlight master assembler Hiroki Tanaka, who installs parts such as the suspension and driveshaft onto the base car body as part of the assembly line process.
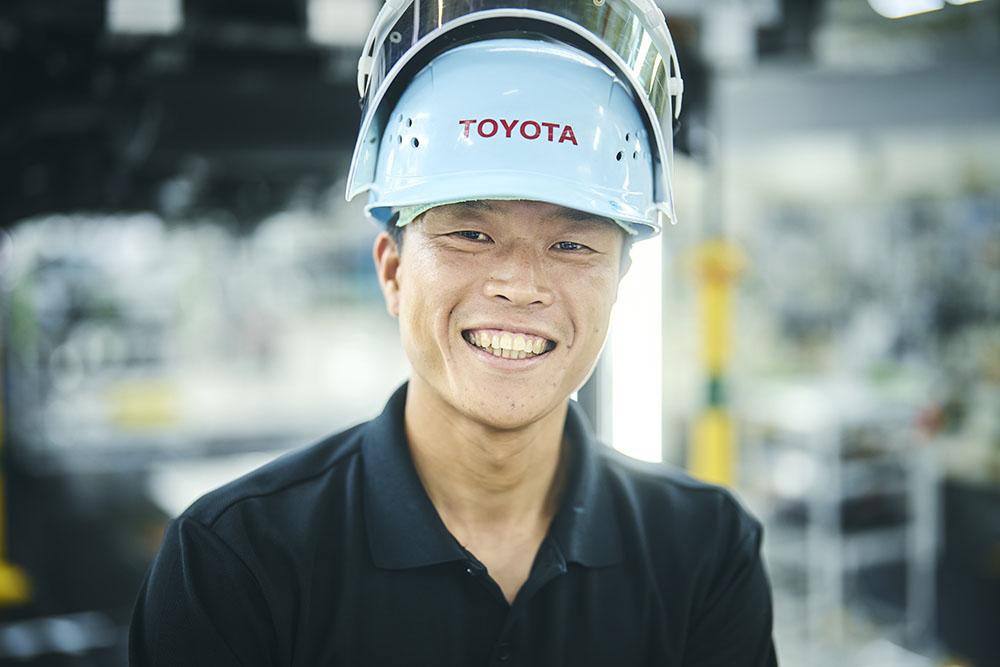
#15 Hiroki Tanaka, a master of high-precision body assembly
Expert, Final Assembly Div., Tahara Plant, Toyota Motor Corporation
The 40 Century craftspeople selected from 1,500
Counting every last screw, a car typically consists of some 30,000 parts. Some parts are made in-house by the vehicle manufacturer, while others come from outside suppliers.
The term “parts” also covers a broad spectrum, from components directly related to driving, such as the engine or suspension, to those that make up the body (doors, etc.) and interior, including the seats and steering wheel.
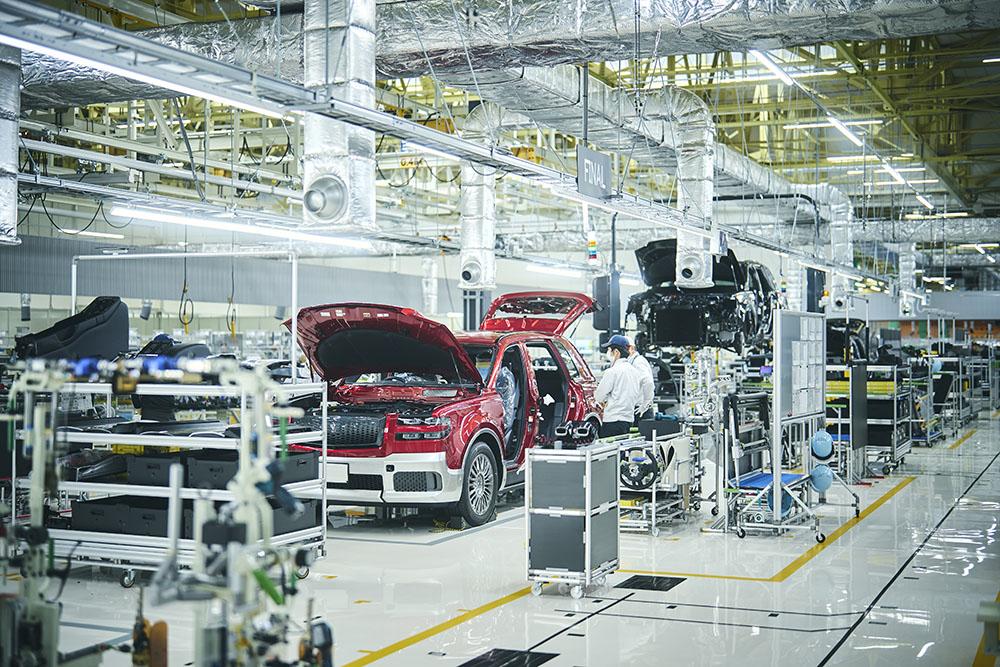
The assembly line is where these various parts from inside and outside the company are fitted onto the body that forms a vehicle’s base, ending up with a finished car. The Final Assembly Division at Toyota’s Tahara Plant (Tahara, Aichi Prefecture), where the new Century is produced, has a staff of around 1,500 engaged in assembly work.
To manufacture the new Century at Tahara, a 40-strong assembly line crew was chosen from among those 1,500 employees. The selection criteria specified highly skilled, quality-oriented personnel at the Expert (team leader) level or higher, with a meticulous approach to monozukuri. Tanaka was one of those who fit the description.

On the Century assembly line, workers are assigned to one of four sections: Trim, which includes the instrument panels and roof; Chassis, which installs the engine, suspension, and PHEV batteries; Final assembly, which includes seats, doors, and windows; and Tuning/Fluids, which handles things like engine coolant and brakes. Together, the line assembles three Centuries a day.

More specifically, the work entails fitting each part using an assortment of wrenches, screwdrivers, and other tools and jigs of various sizes.
As part of the chassis team, Tanaka installs bulky, heavy engine and suspension components, which require operating a torque wrench with a meter-long handle.
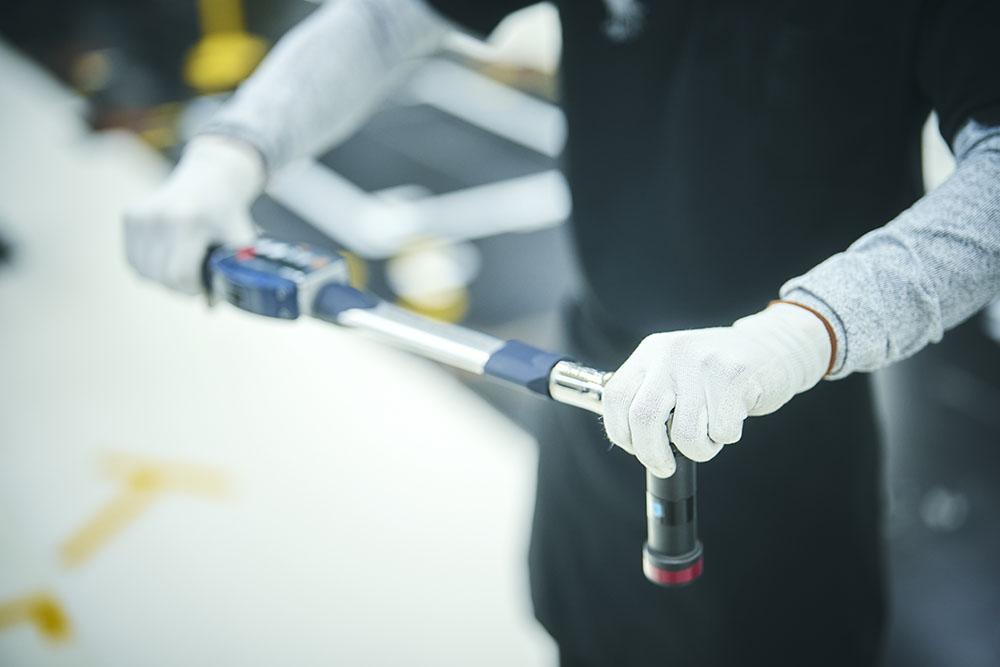