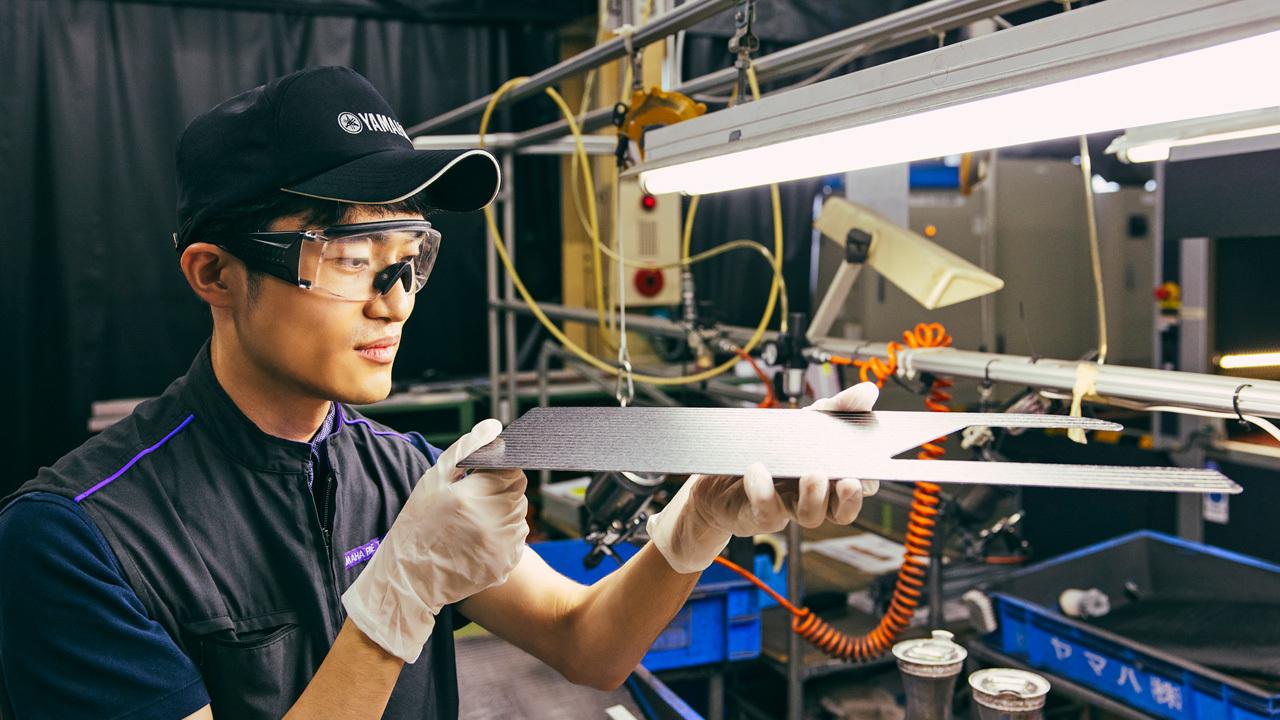
This is an ongoing series looking at the master artisans supporting the automotive industry. Here, in Part 2 of the 17th installment, we hear from the master decorative engineer behind the new Century's beautiful wooden panels.
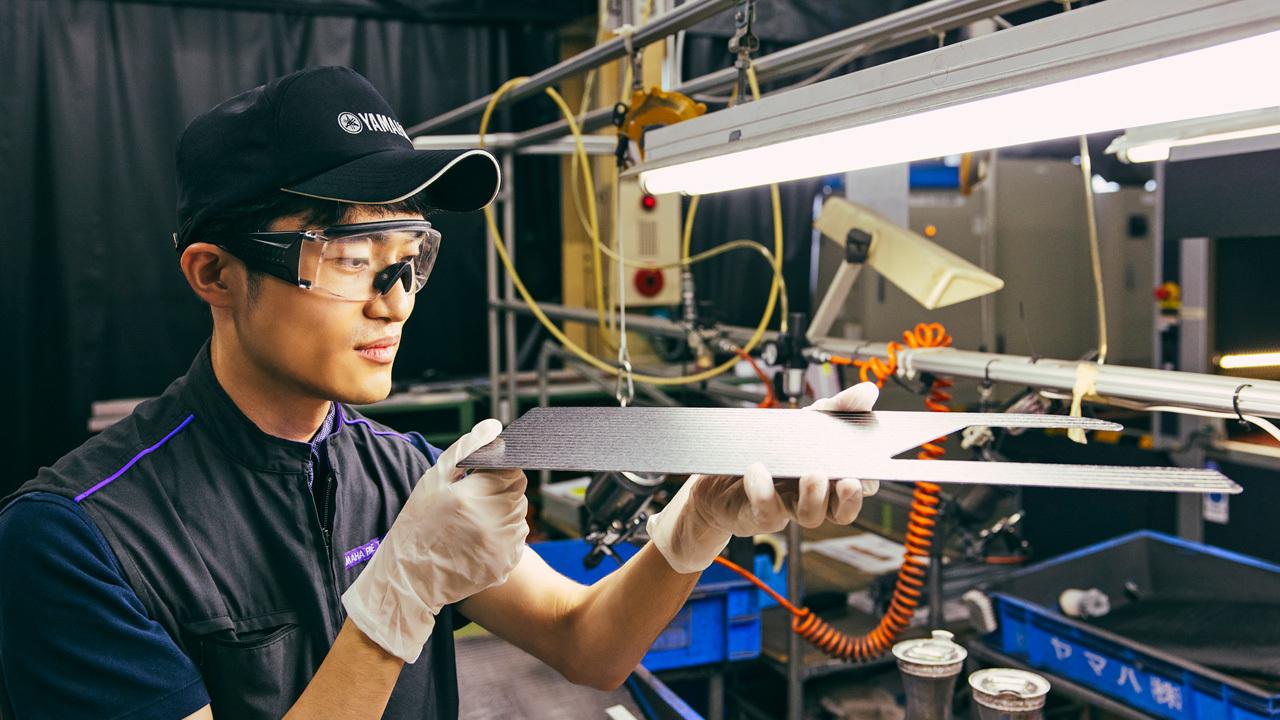
Handwork still plays an important role in today’s car manufacturing, even as technology like AI and 3D printing offer more advanced methods. This series features the craftsmanship of Japanese monozukuri (making things) through interviews with Toyota’s carmaking masters.
To mark the recent launch of a new Century, this is the fourth in a special five-part series showcasing the craftspeople who work on the model.
One highlight of the Century’s interior is its natural wood decorative panels. For this installment, we interviewed two craftsmen from Yamaha Fine Technologies who were involved in their development and production. Part 1 featured the artisan in charge of selecting the perfect wood for the panels.
This time, we shine the spotlight on Hikaru Ubukata, a master of decorative engineering who was involved in every step of turning the designers’ vision into decorative panels, from selecting materials to determining coating and finishing specifications.
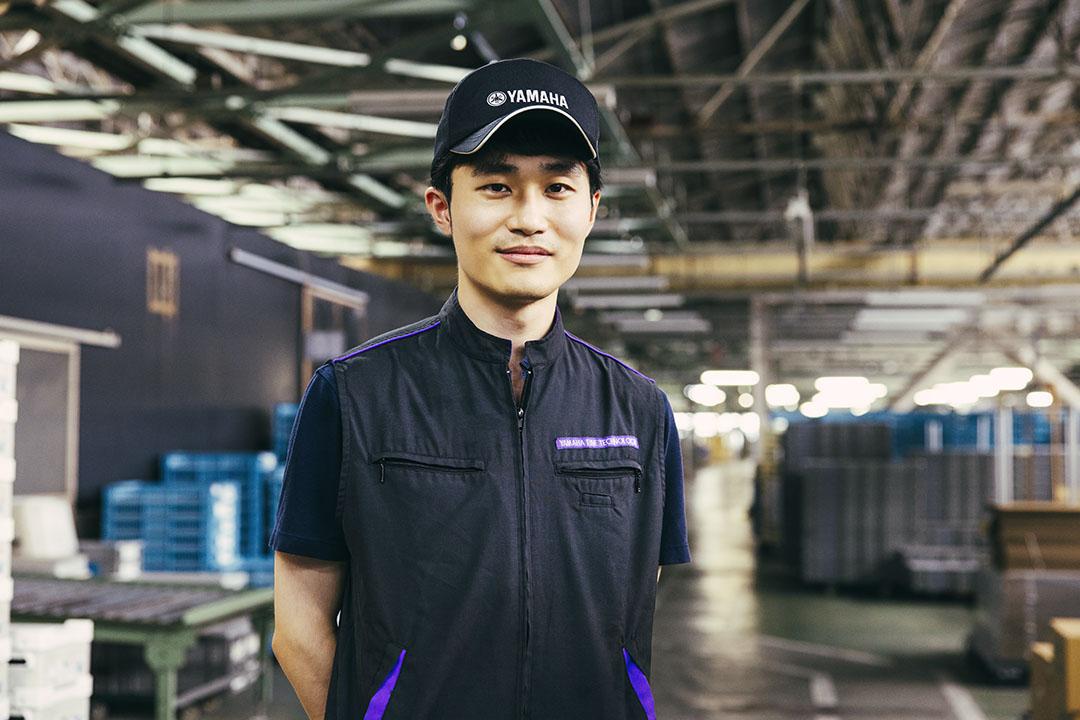
#17 Hikaru Ubukata, a master of decorative engineering who creates the ornamental panels dreamed up by designers
Supervisor, Production Engineering Department, Chemical Engineering Group, Car Parts Division, Yamaha Fine Technologies Co., Ltd.
Piano-making expertise lives on in decorative panels
As we reported in an earlier article, the design concept for the new Century’s interior was “comfort and convenience through luxurious simplicity.”
“We set out to create a simple yet luxurious space that eschews ostentation,” tells Design Division General Manager Tatsuya Sonoda, who oversaw the entire design process.
A key element in bringing this interior concept to life is the natural wood decorative paneling that adorns the instrument panel and the Century’s traditional tower console.
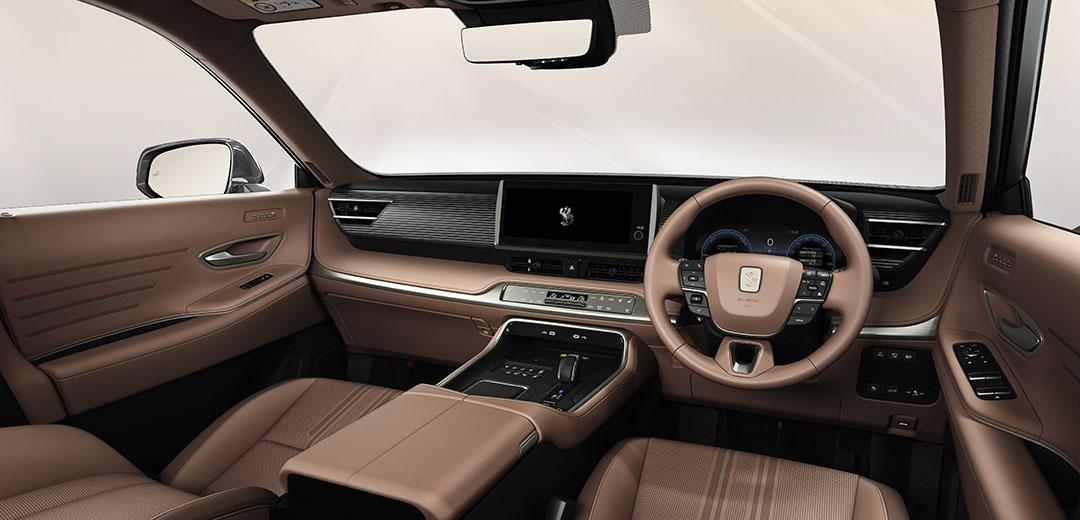

Instead of emphasizing patterns within the wood itself, these striking pinstriped panels feature a neat, straight grain painted in black tones and inlaid with sharp aluminum lines for a chic, premium feel.
Ubukata handled all aspects of the panels’ development.
Ubukata
For the decorative panels used in new car interiors, my job is to come up with everything from the kind of material (veneer) to the type of finishing and coating, and to set out the fabrication methods that would realize the customer’s (designer’s) vision.
The new Century’s interior design concept was “comfort and convenience through luxurious simplicity.” In the early stages of development, we were shown a mock-up of the interior, which helped me understand more clearly what Toyota was aiming for.
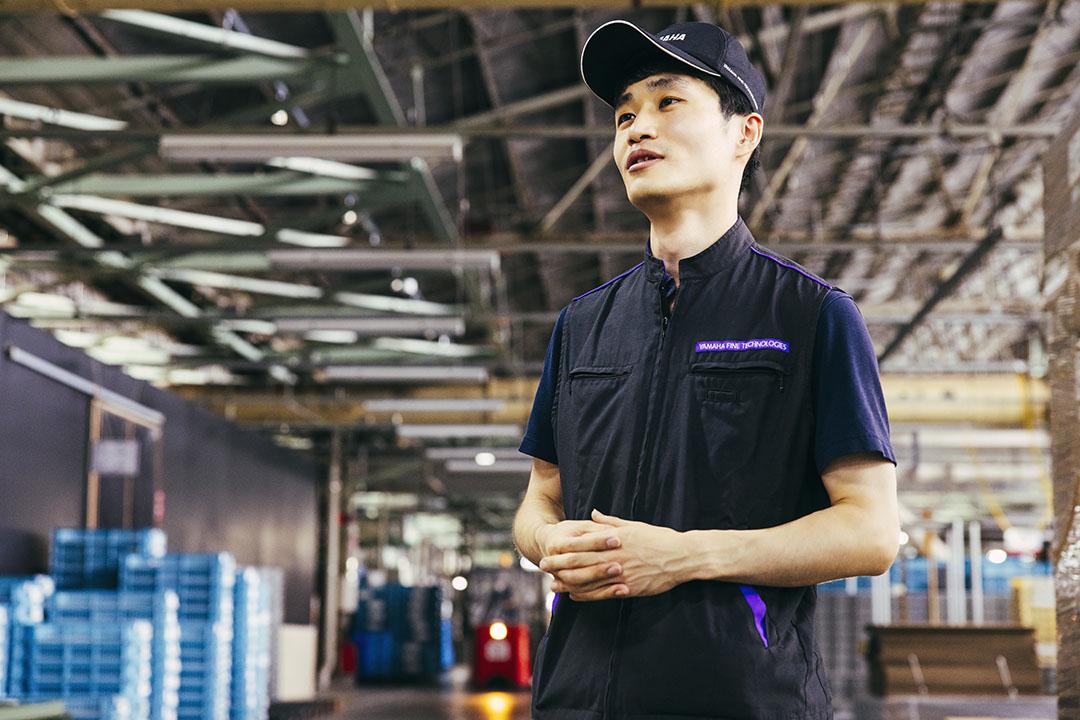
At the same time, Ubukata also notes that upon seeing the mock-up, he remembers thinking, “This is going to be a tough project.” What exactly did he mean?
Before we delve deeper, let’s take a brief look at how wooden decorative panels are actually made.
The panels produced by Yamaha Fine Technologies are three-ply sheets consisting of a 0.2 mm-thick wooden veneer, an aluminum plate, and a backing material. These materials are bonded using a specialized press.
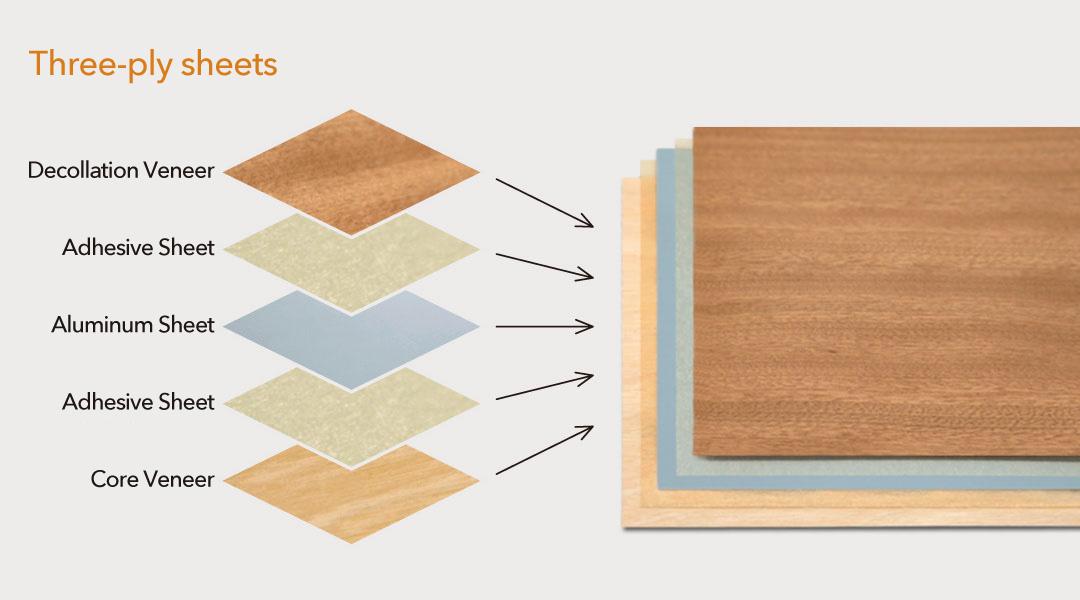
They are then punched out into individual part shapes and molded onto the underlying resin structures. This is where the flat three-ply sheets are formed into three-dimensional components.
Next, they undergo a finishing process that involves painting, coating, grinding, and polishing, before the final steps of hole drilling and other necessary machining.
As we mentioned in Part 1, these woodworking, painting, and polishing processes draw on the technologies Yamaha has cultivated in the manufacture of grand pianos. Regardless of specifics such as wood type, finish texture, and hues, the techniques used for making car interior parts are essentially the same.