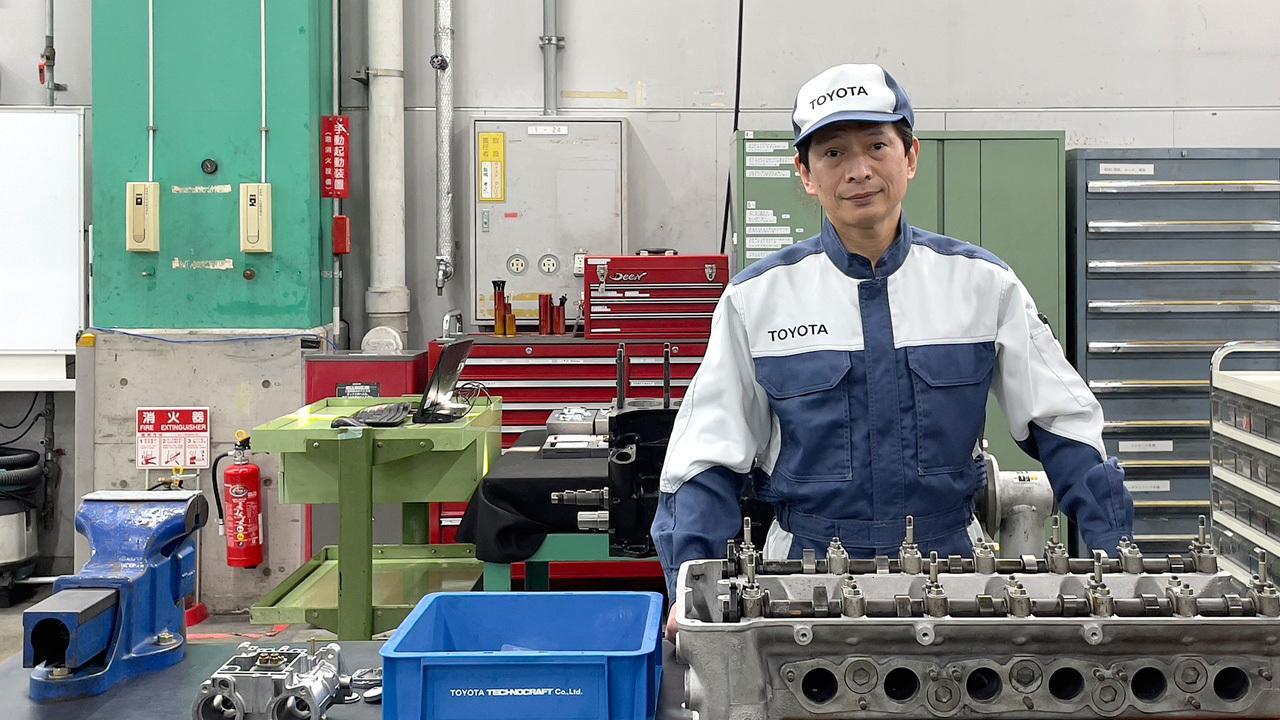
This two-part article features Koji Okada, an auto mechanic and master restorer who is using his exceptional skills and experiences in bringing legendary Toyota 2000GTs back to life.
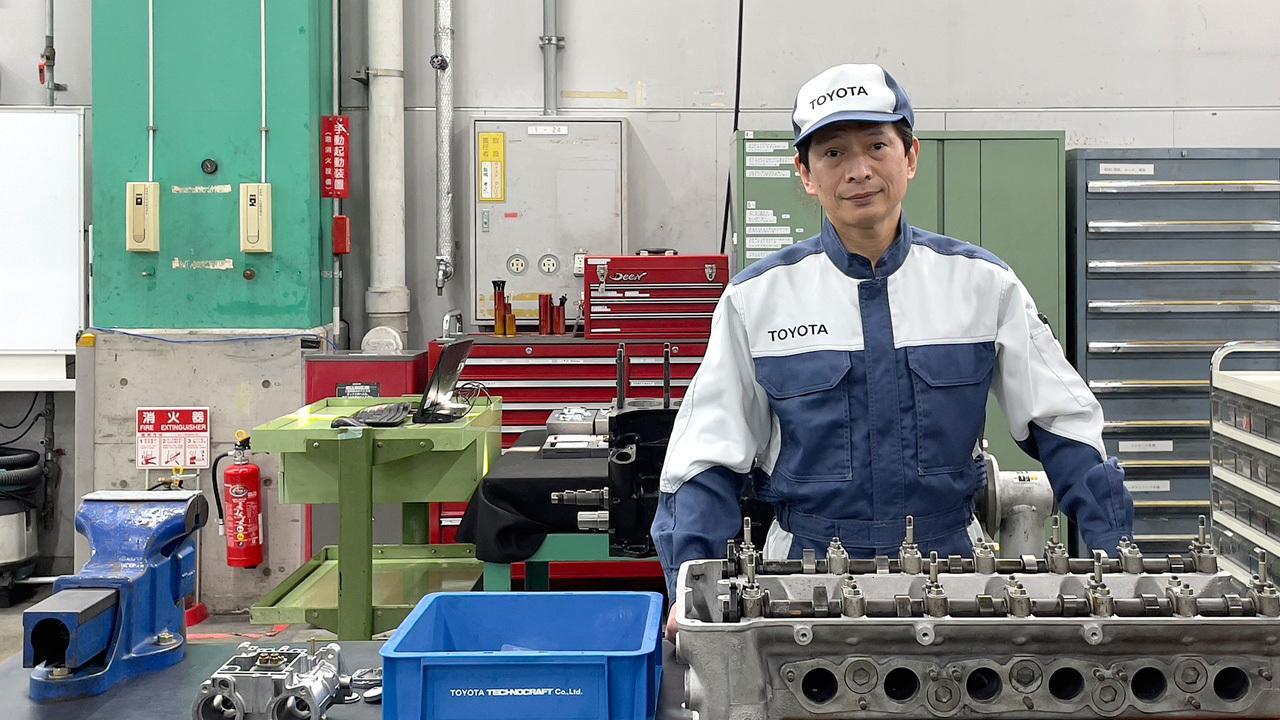
After introducing Koji Okada and his work in part one, here we move on to specific restoration work he is doing on a legendary 2000GT.
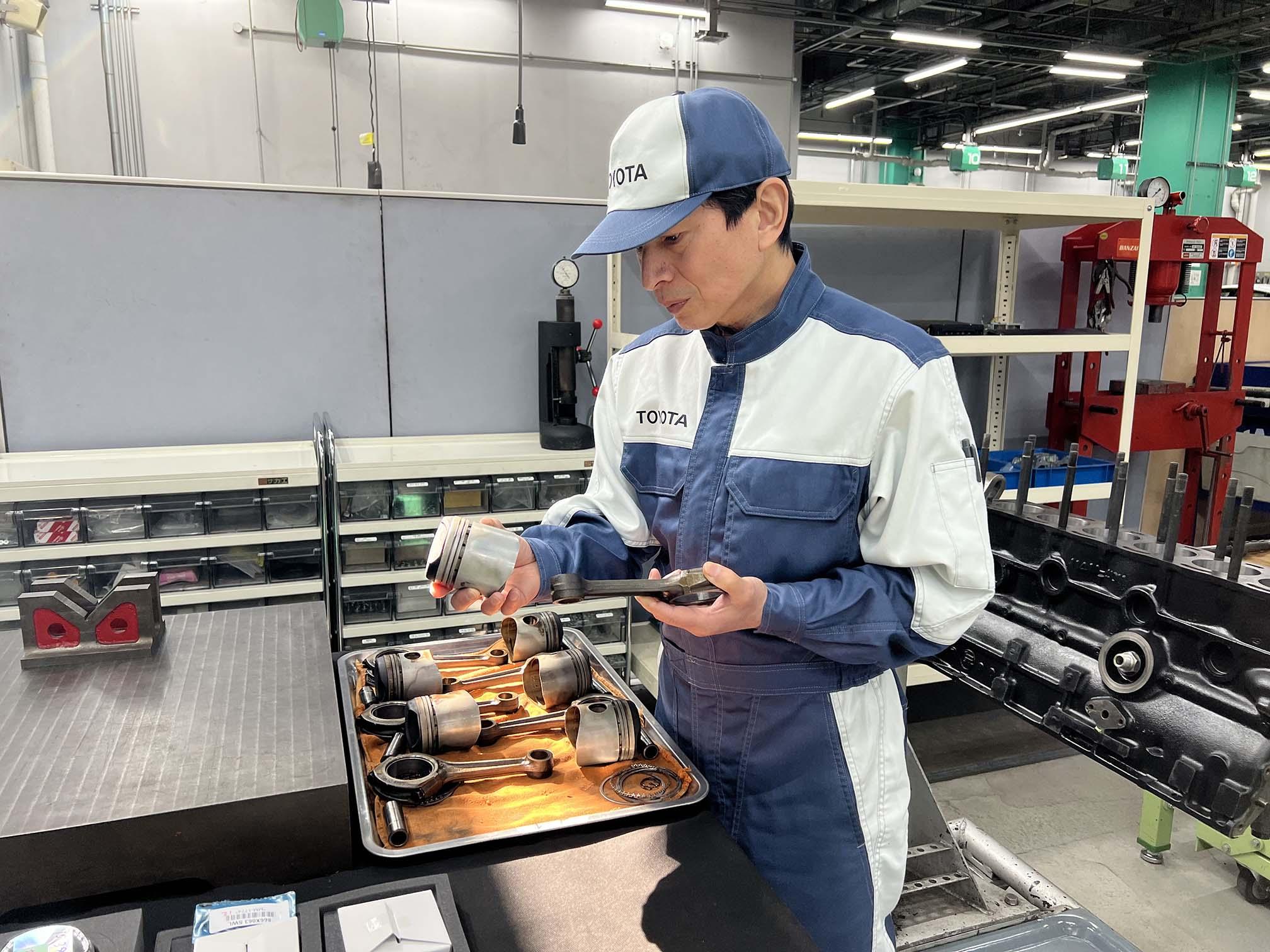
#9: Master restorer Koji Okada returns legendary sports cars to their glory days
Project General Manager, Service Division, Toyota Met-Logic
From a childhood love of cars and racing
Toyota Times visited Okada’s workshop to see how the Toyota 2000GT restoration work is proceeding.
Two Toyota 2000GTs, an early and a later model, are lined up side by side in a vast garage. One is under restoration at its owner’s request, the other is a company-owned car that serves as a textbook for restoration work. Both gleam like new.
Okada, 56 years old, says his love for cars inspired him to become an auto mechanic.
“I’ve loved cars since I was in kindergarten, and then around fourth or fifth grade came the supercar boom. I was obsessed with building plastic car models and even had some exhibited at competitions. I knew I wanted to work with cars in the future.”
Okada, who went on to technical college and became an auto mechanic, also loved motorsports. “That’s why I wanted to work on racing cars in particular.”
In 1985, Okada joined Toyota Technocraft, the Toyota Met-Logic predecessor that handled development and maintenance of Toyota’s motorsport vehicles through its subsidiary Toyota Racing Development (TRD).
Toyota Technocraft traces its history back to 1954 and the founding of Toyopet Seibi, renamed a decade later as Toyopet Service Center. In 1965, the company created the Special Development Division to develop and service vehicles for motorsport. TRD was later established to strengthen the division’s role.
Okada’s initial work in the Special Development Division included maintenance on museum display cars and Toyota’s racing vehicles, including the Celicas that achieved stunning success in the World Rally Championship (WRC).
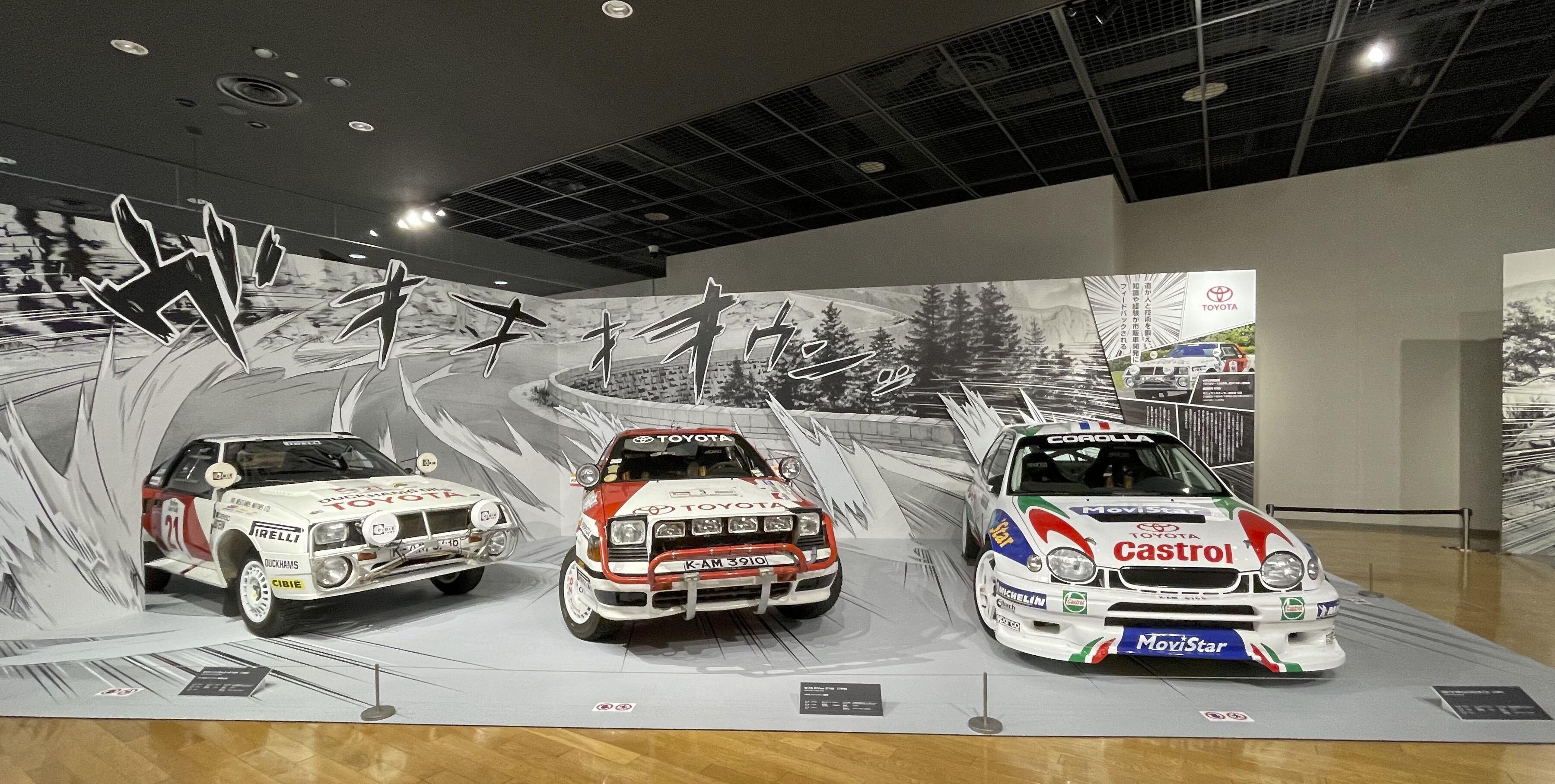
The division was also responsible for producing speed trial vehicles and the open-top model used in the James Bond film You Only Live Twice. After the 2000GT’s release, it remained closely linked to the vehicle as a designated service facility. The car’s beauty fascinated Okada from his first days at the company.
At first, he was forbidden from laying a finger on the cars and had to settle for watching the work of experienced colleagues from afar. After some two years at the company, Okada finally got the chance to work on the supercar of his dreams.
2000GT servicing relies on all senses
That brings us to Okada’s 2000GT restoration work.
“First was the engine tuning, which is the first thing I tackled, on the advice of senior colleagues. For normal maintenance, you’d first use an engine tester, but for the 2000GT your senses are more important,” says Okada. “Listen to the engine to figure out what’s wrong, until it becomes second nature—that’s what I was taught.”
In modern car engines, air intake systems are controlled electronically, using sensors to measure how much air is taken in then injecting an appropriate amount of fuel to create the optimum mixture.
The Toyota 2000GT, on the other hand, has an analog air intake system with carburetors, which create the appropriate air-fuel mixtures by drawing fuel into inflowing air using Bernoulli’s principle. The 2000GT’s engine featured three two-barrel carburetors, made by the renowned manufacturer Solex, which are linked up to run in tandem. Combustion conditions vary slightly between the engine’s six cylinders, and mechanics must draw on their intuition and ingenuity to tune each carburetor accordingly.
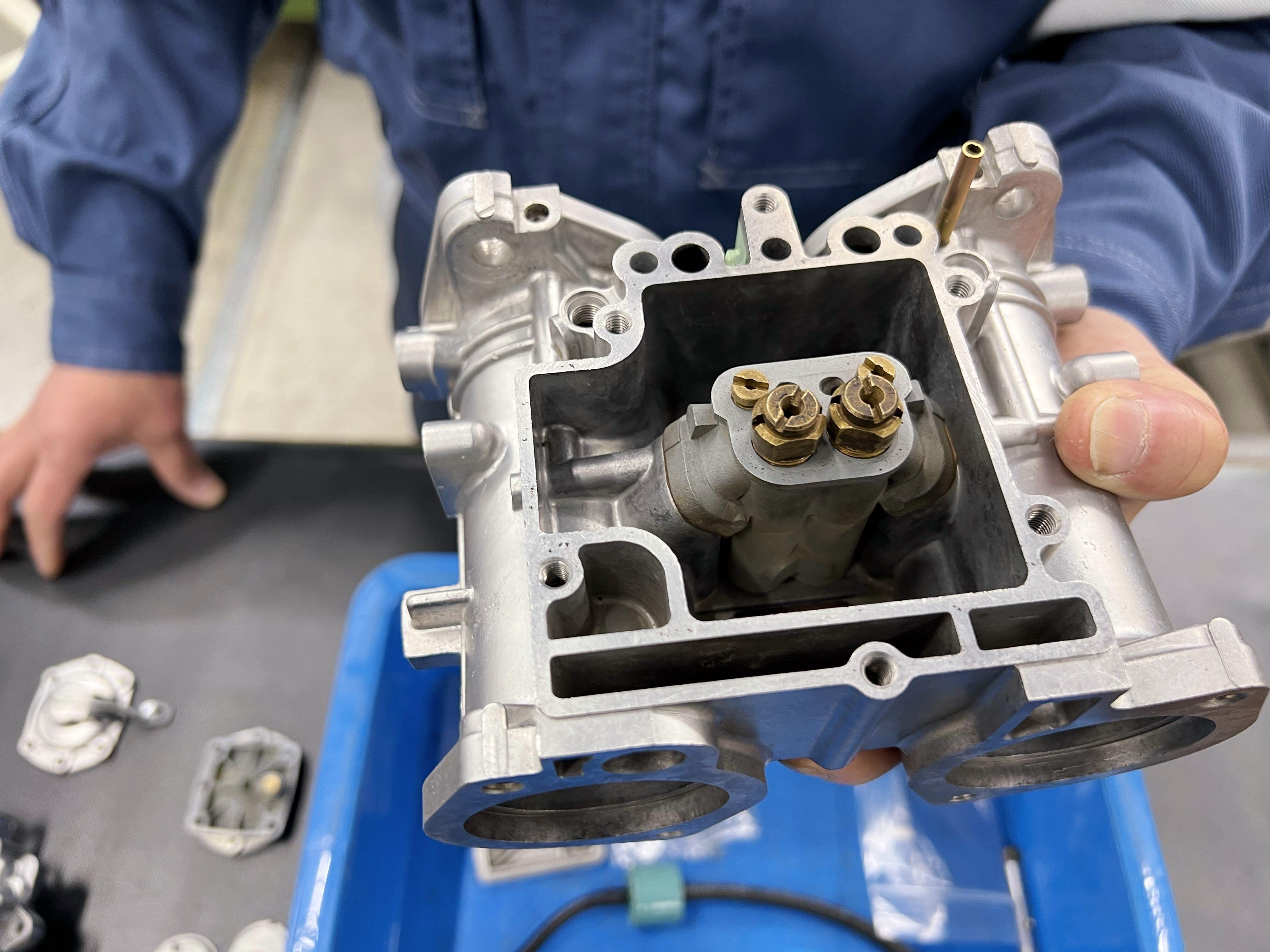
“If any one of the carburetors is not properly tuned, the corresponding cylinders may not ignite, or you may get incomplete combustion even if they do. When that happens the engine sounds uneven, so you can quickly figure out which cylinder is misfiring by listening to the engine,” Okada explains.
Okada gradually mastered restoration skills and know-how thanks to guidance from senior colleagues and hands-on experience on the two-decade old model’s restoration.
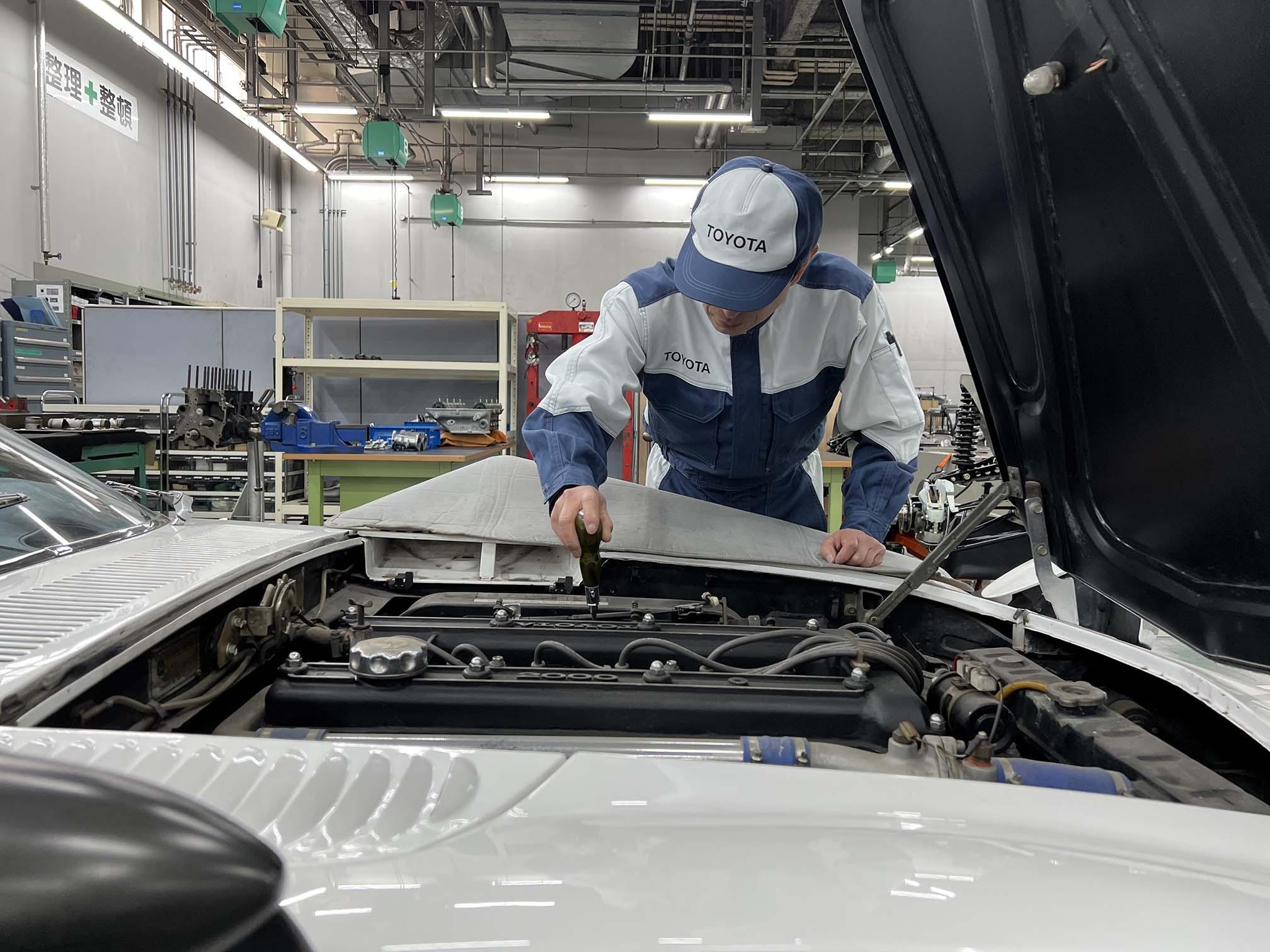
“Unfortunately, we couldn’t take on any servicing or restoration projects for about ten years in the 1990s because spare parts were no longer available,” says Okada.
In 2008, strong petition by a Toyota 2000GT owners’ club pushed the company once more to begin offering full restorations. Initially, the restoration work was carried out in a specialized plant producing motorsport vehicles in Yokohama.
“We could manufacture unobtainable parts, either in-house or through outside companies, with the technology, equipment, and expertise for producing motorsport vehicles, and handle sheet metal and painting internally too,” Okada explains.
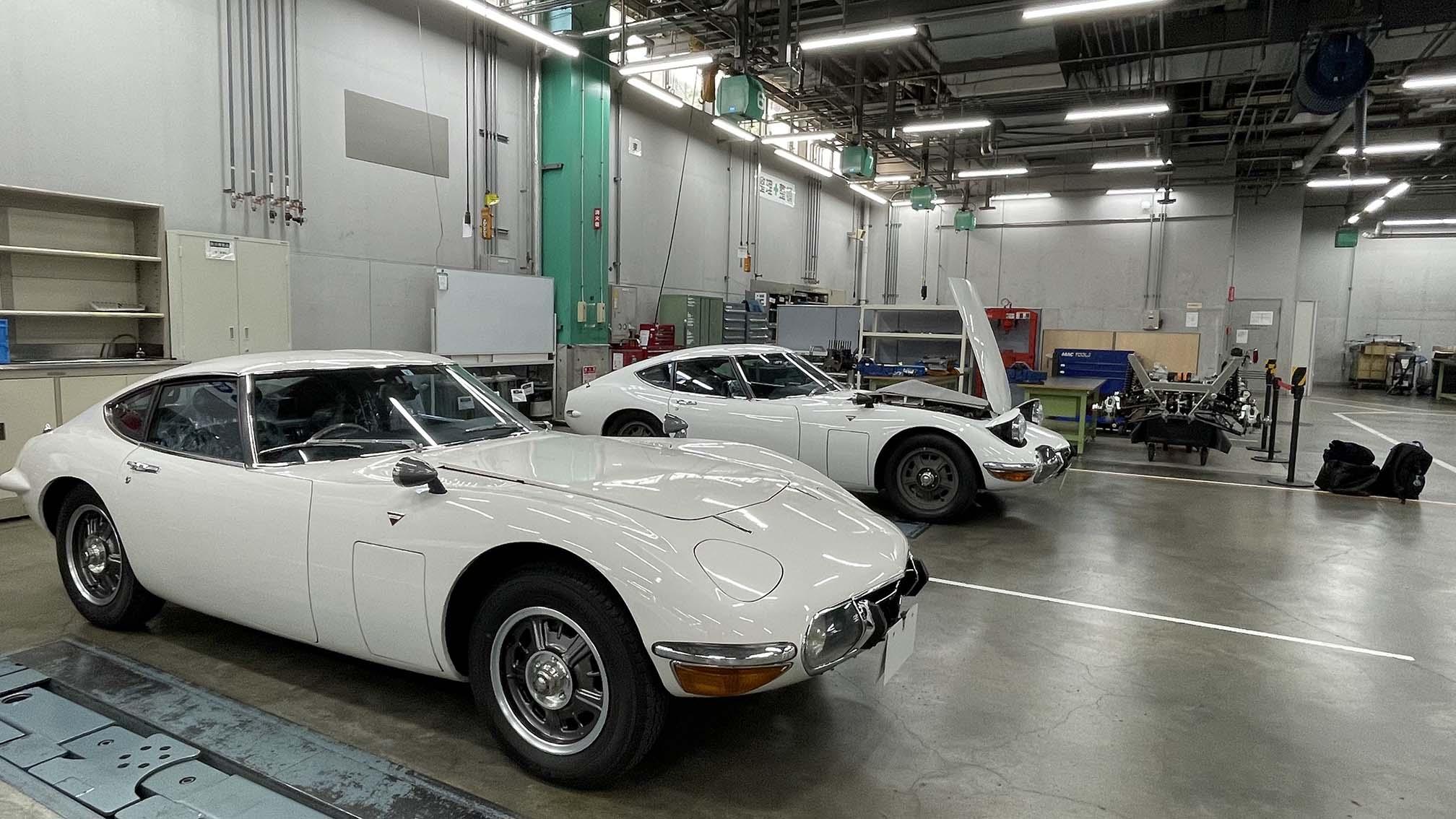
The first step in a full restoration is a thorough check of the vehicle.
“When a car comes into the garage, we first take it for a run if it’s drivable. We also do a complete inspection with testers to identify any issues. Depending on the condition, we may take 3D measurements of the entire vehicle to check for any deformation in the body.”
Then comes the real restoration work. The first step is a thorough disassembly and cleaning.
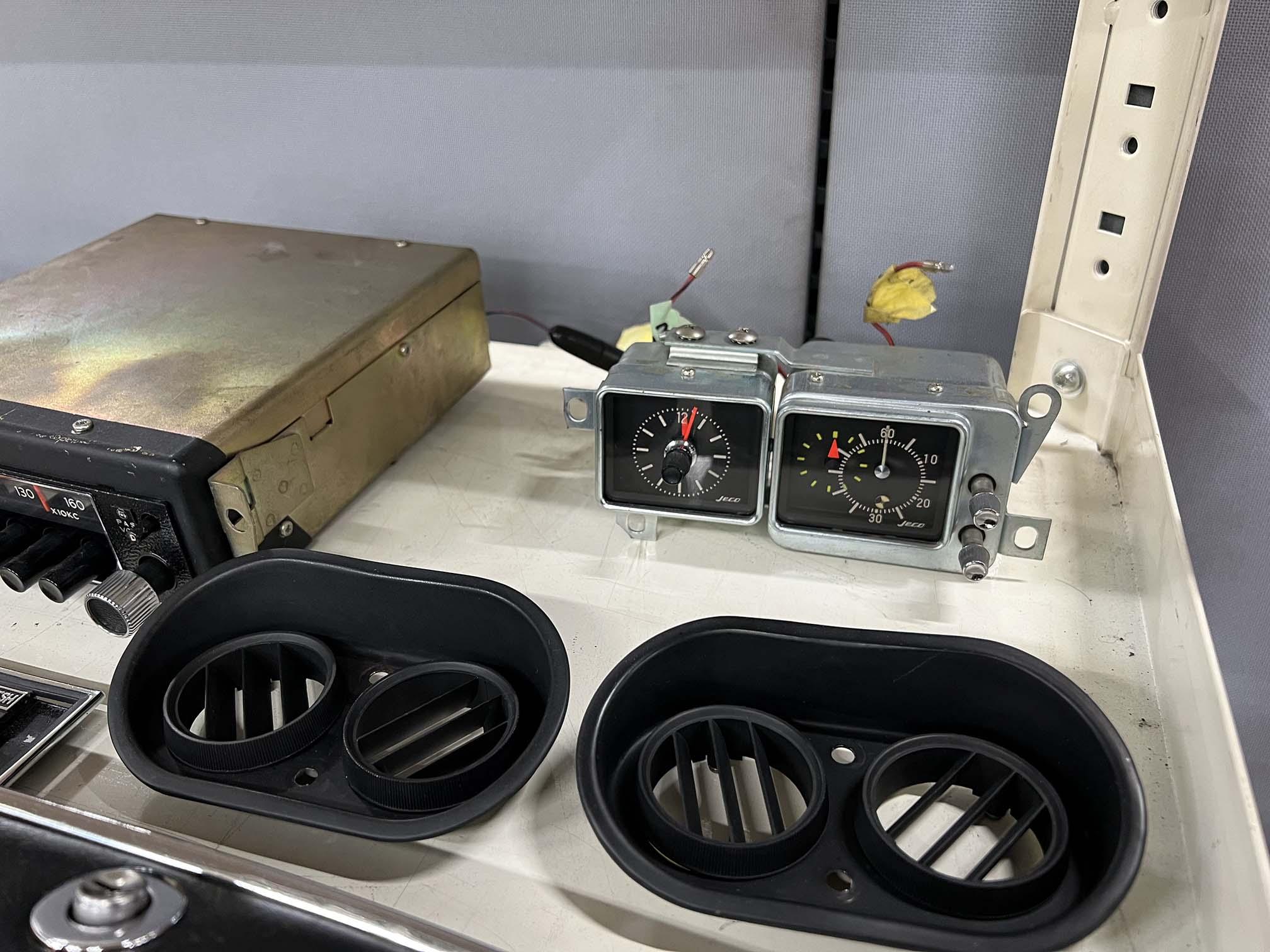
“We strip every possible part from the body and chassis—the engine, transmission, differential, suspension, steering, brakes—basically dismantling it down to the last screw,” says Okada.
However, some of these parts can’t be put back together once disassembled. How far do you go? That’s where Okada’s experience and expertise come into play.
Having dismantled the car, Okada must next check every part to determine whether it can be used as-is or needs to be repaired or replaced.
“Any original parts deemed usable are cleaned with sandblasting or wet blasting machines, then plated or painted as necessary. For unusable parts, we arrange for a replacement or make one if none are available. With plating and painting, we even try to get as close to the original color as possible,” explains Okada.
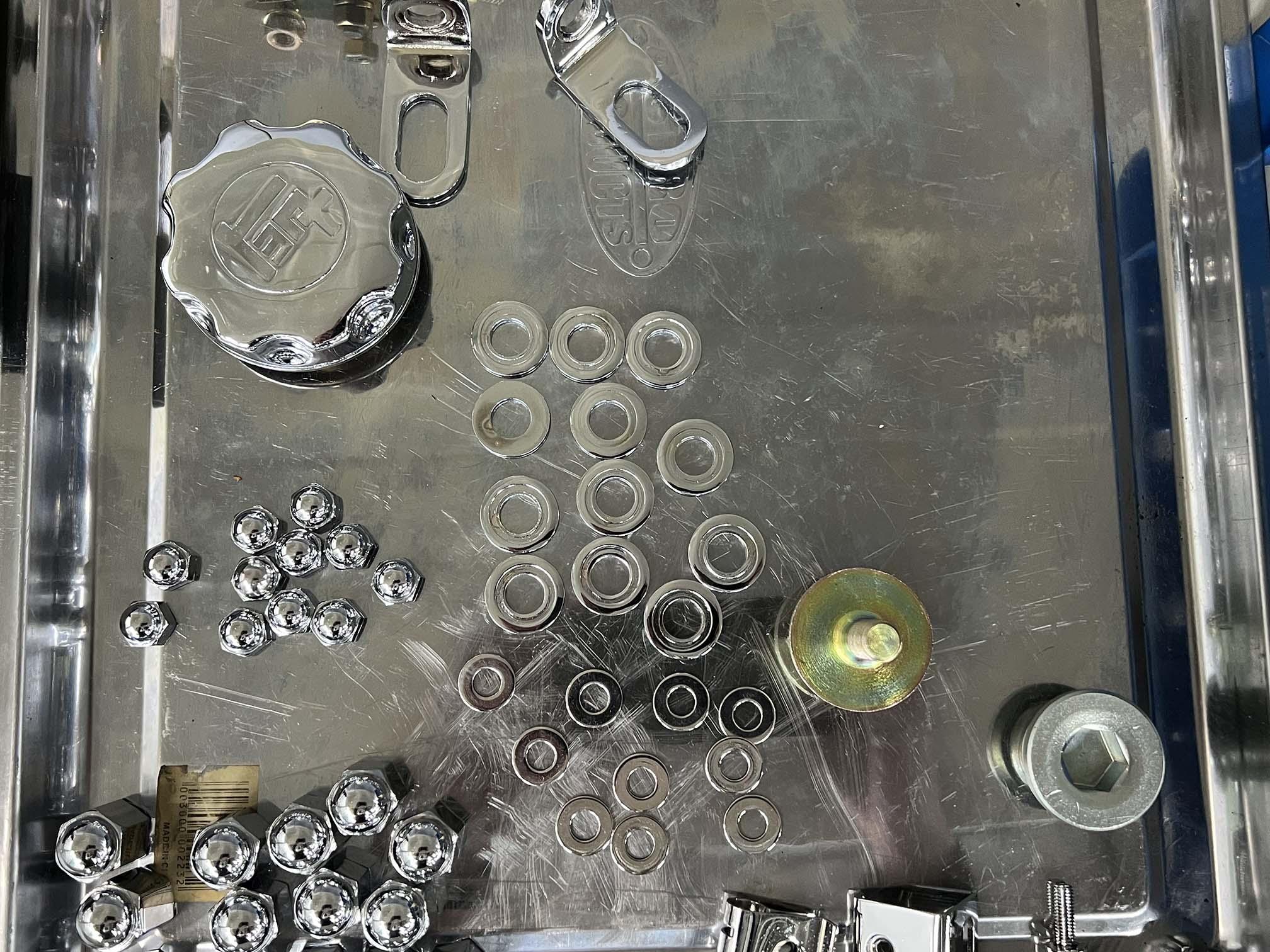
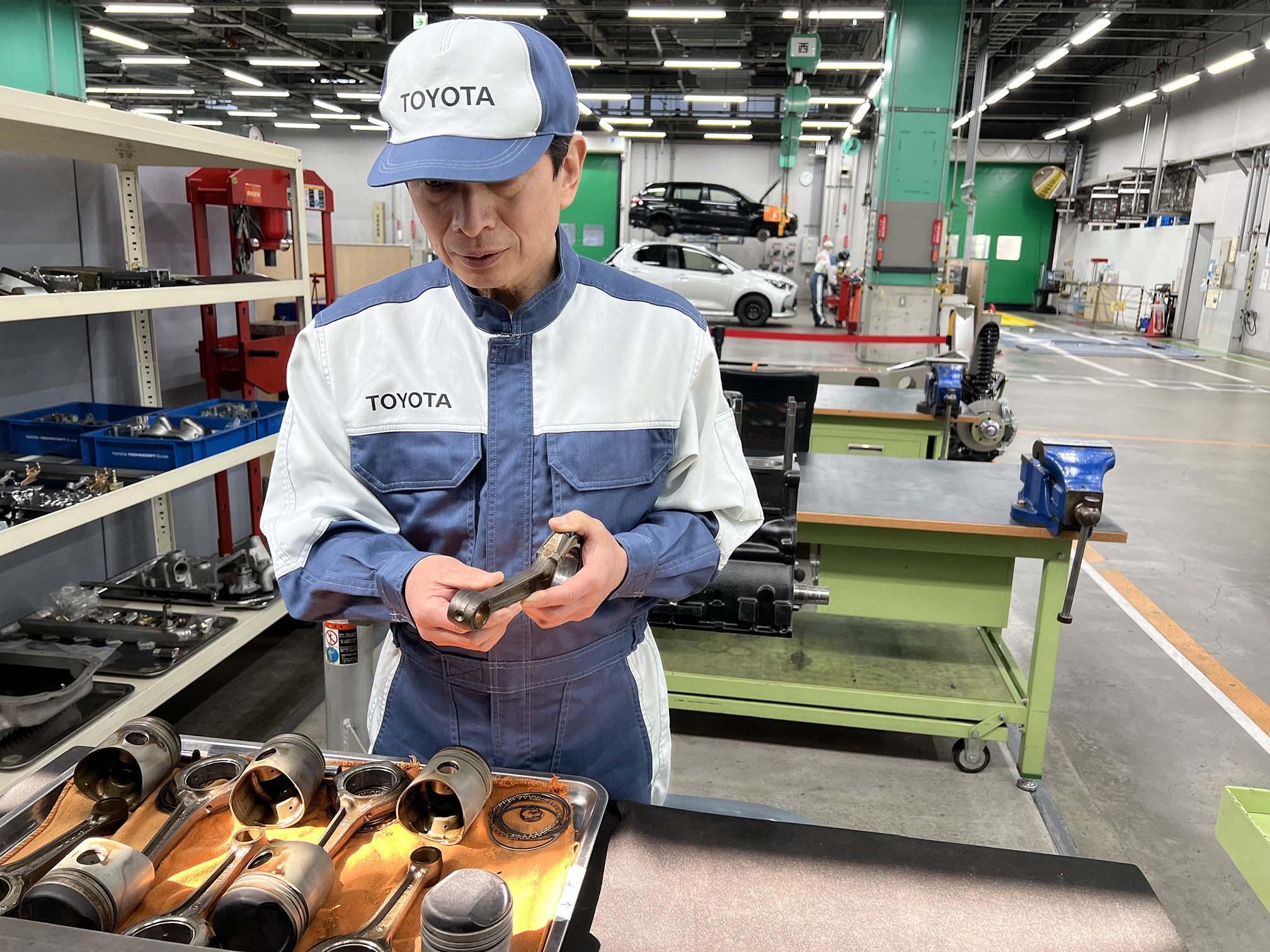
Okada’s workshop is also equipped with large machines that can clean entire engine blocks or cylinder heads. Arranged on workbenches were an engine block and cylinder head cleaned by these machines and partially painted, along with pistons, crankshafts, and connecting rods awaiting reassembly. Besides the cylinder head, the camshaft that controls intake and exhaust valves, and the camshaft gears, gleam like new.
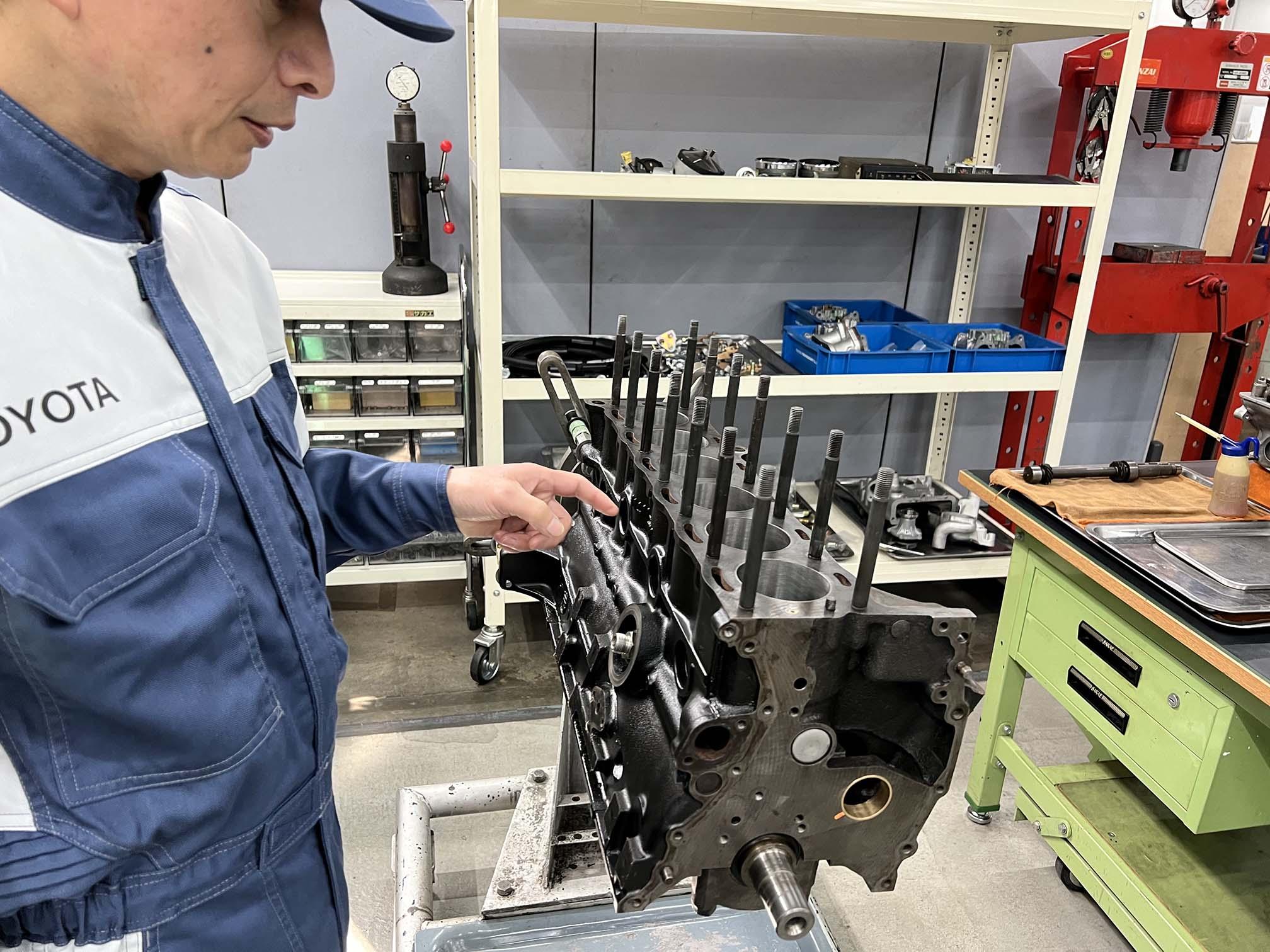
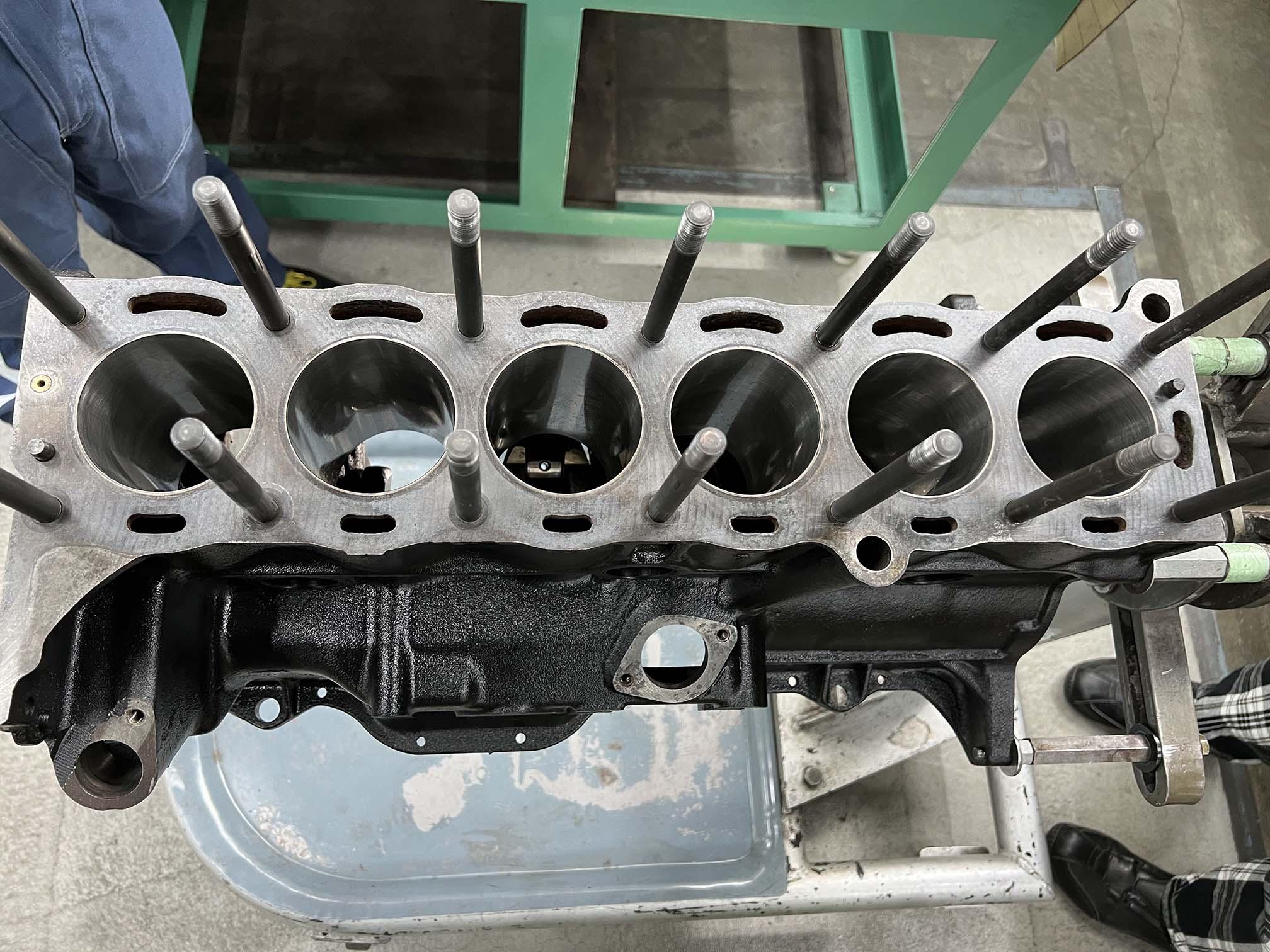
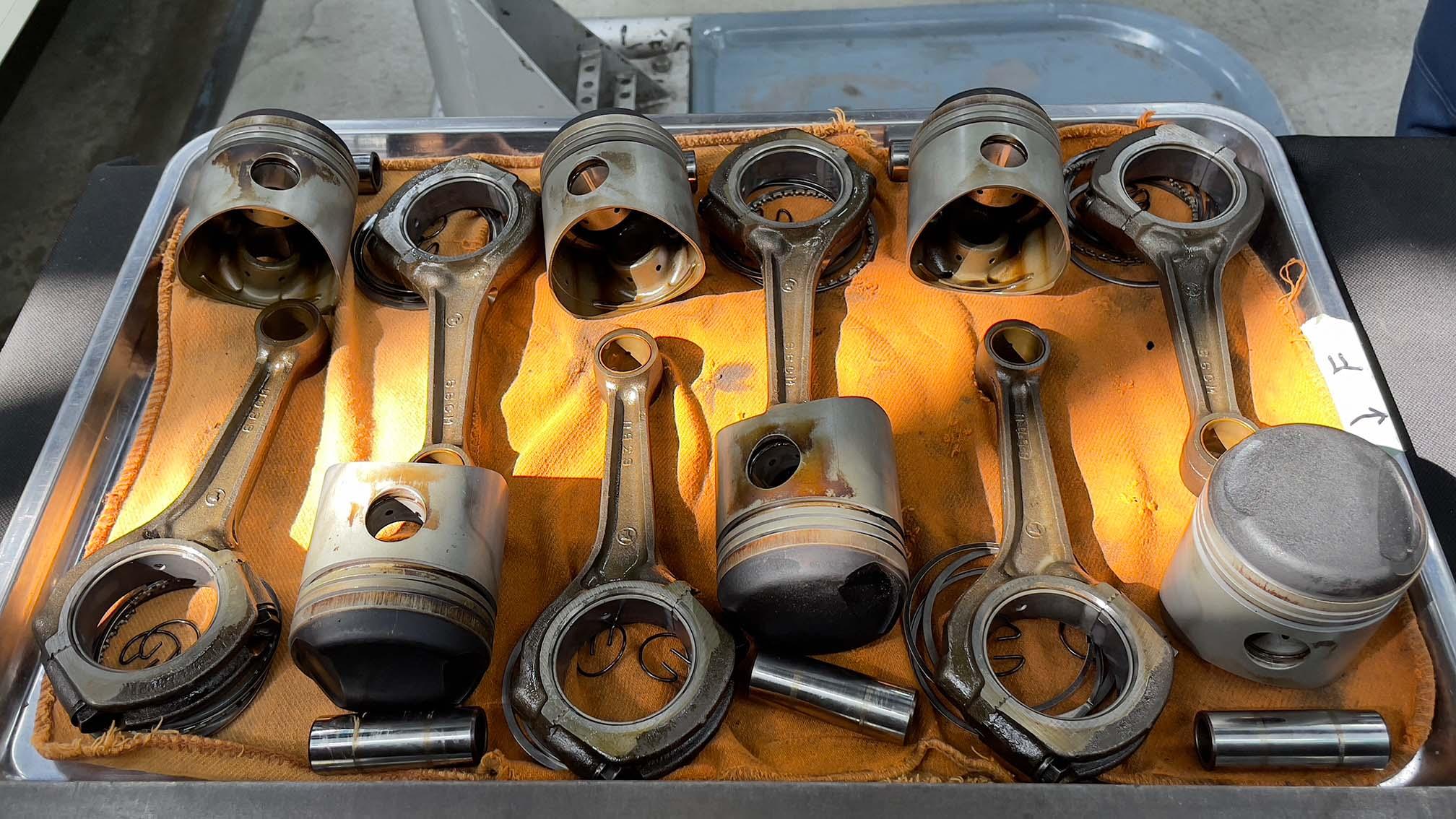
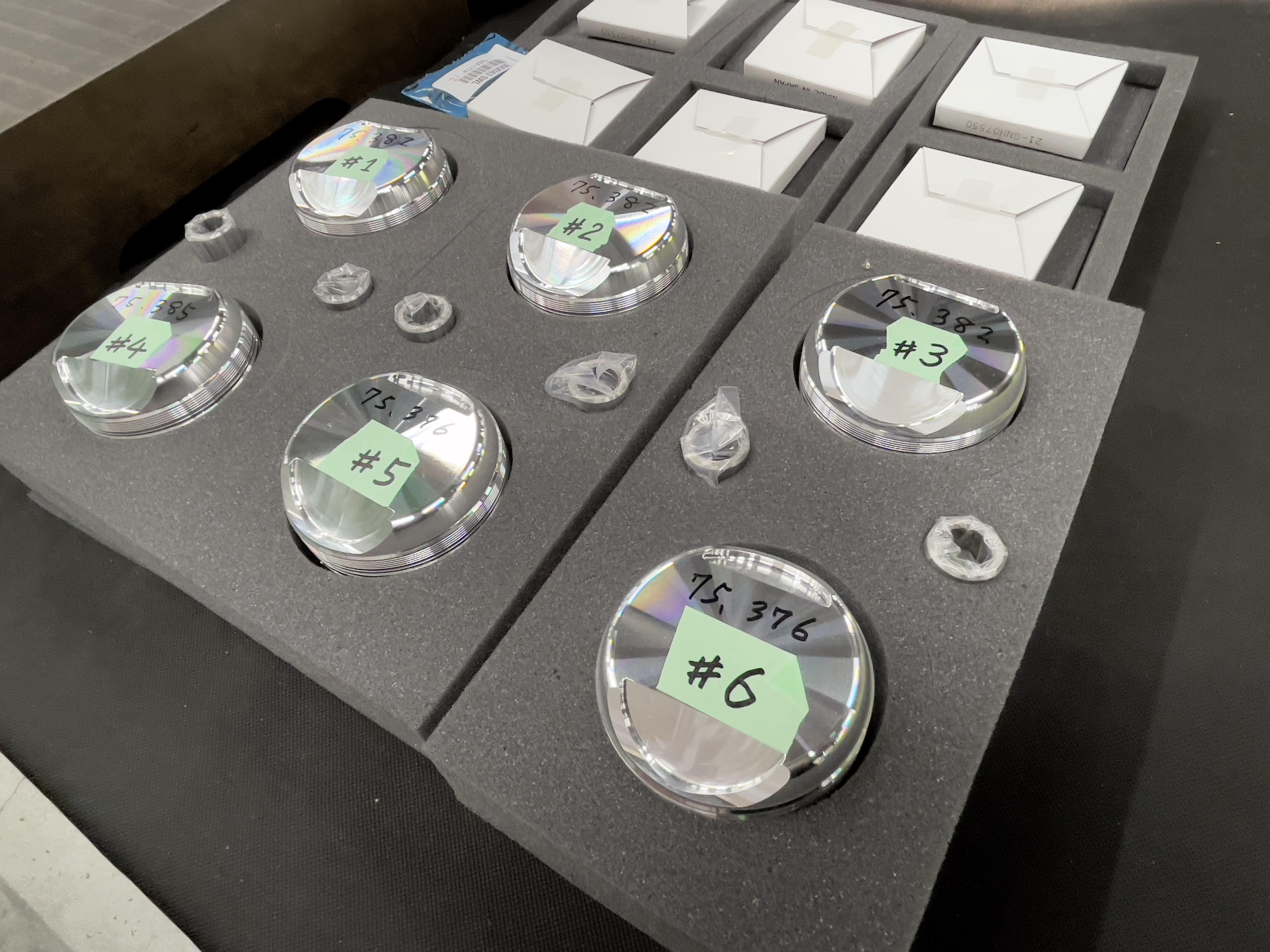
“For this engine, we will use the original connecting rods, but the pistons and valves were too worn out and no longer usable. We’ll replace them with new parts produced for us by a specialist manufacturer. They take about two months to make,” says Okada.
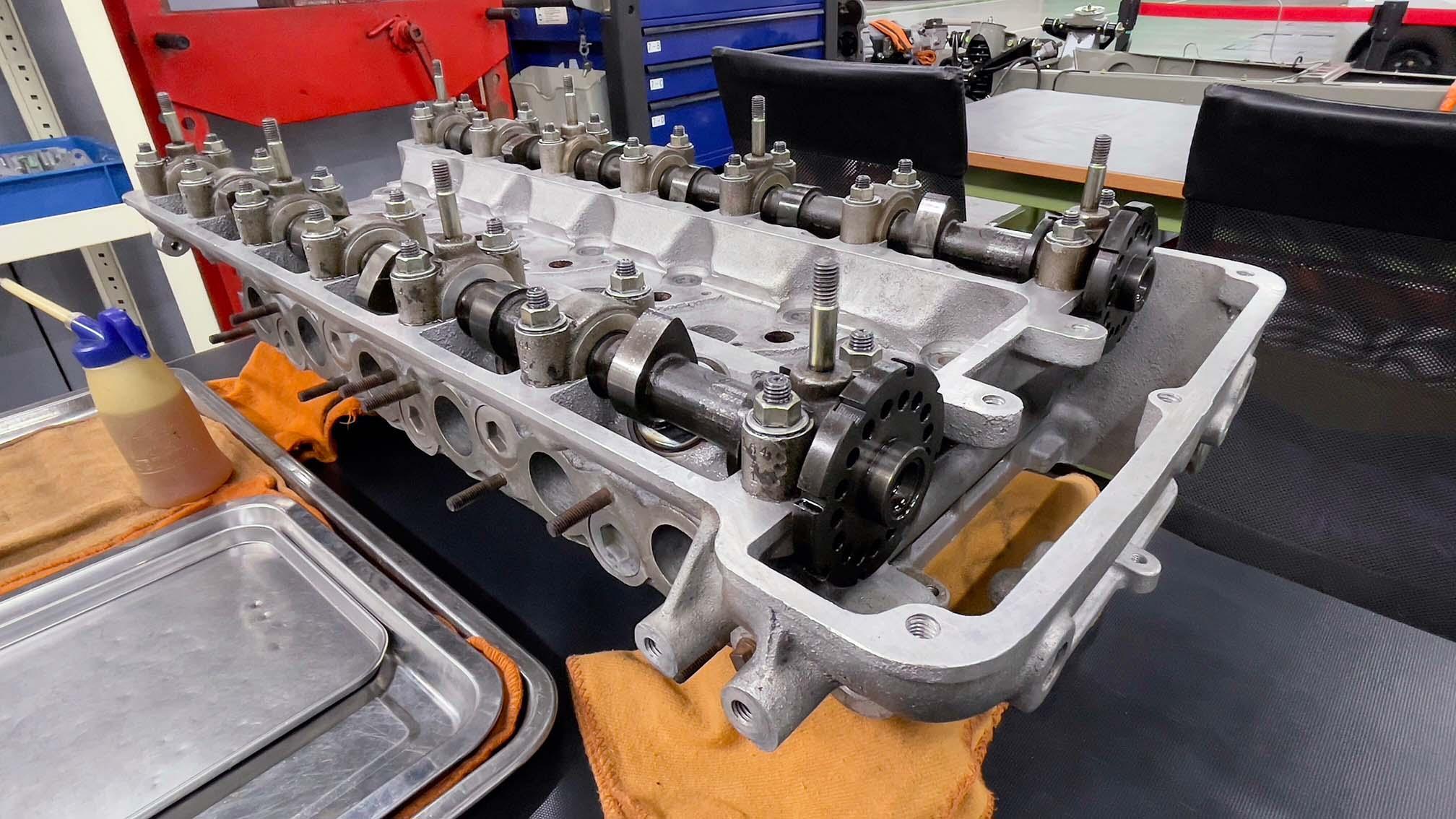
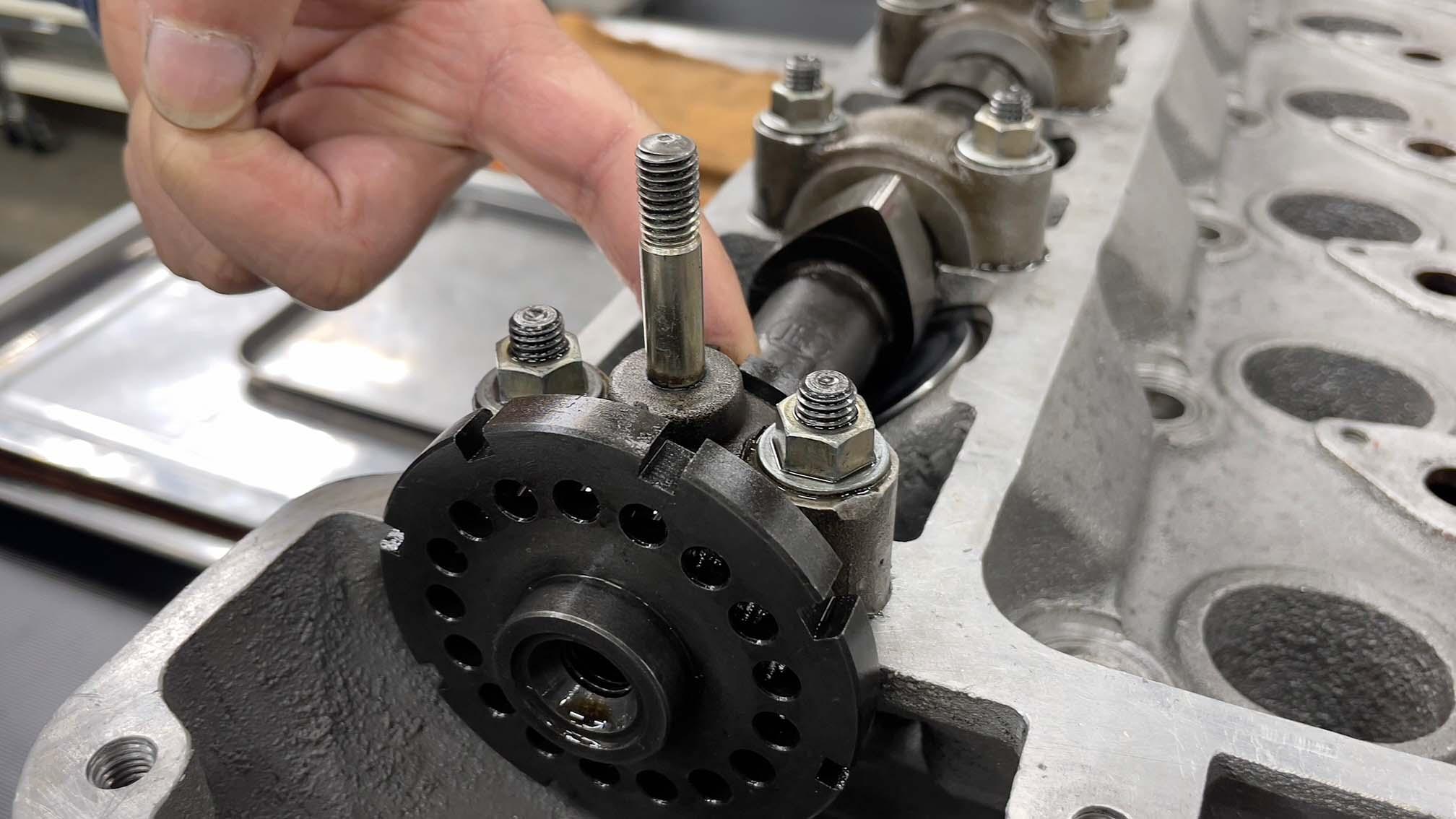
“There are many holes in the camshaft gear to allow for precisely adjusting valve timing. That’s one of the unique features of the 3M engine,” Okada shows the part.
Okada will overhaul the alternator and starter, while a seat specialist is entrusted with refurbishing the driver and passenger seats.
One of the biggest challenges is the walnut and rosewood dashboard and steering wheel, originally made with the craftsmanship of Nippon Gakki (now Yamaha). In the past, the company assisted with refurbishing, but now Okada and his colleagues have mastered the techniques and restore the interior themselves.
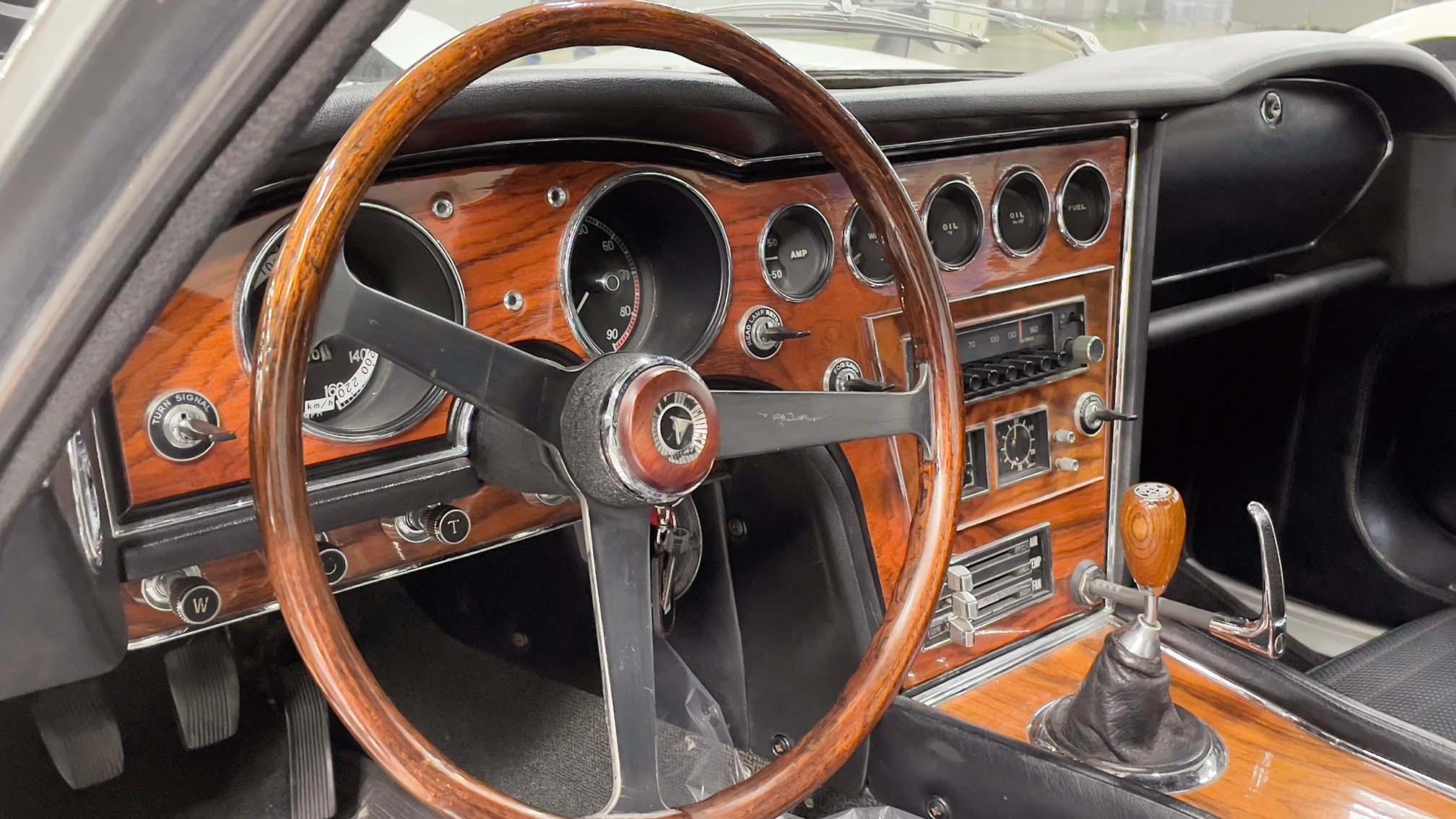
“With a steering wheel made of wood and steel, the wooden part delaminates over the years, and we repair it by splicing wood back in,” explains Okada.
On the next workbench lay the retractable headlights, disassembled, and cleaned. Although spares aren’t available, according to Okada these parts are relatively durable. The only problem is sourcing the motors that open and close the headlights.
“We used to work with a company who would rewind and repair the coils on the motors, but they’re no longer in business. We're currently looking into substitute motors.”
Arrayed on a shelf along the wall are the speedometer, tachometer, clock, radio, and other parts that had made up the driver-side instrument panel. All have been meticulously polished and are ready for mounting.
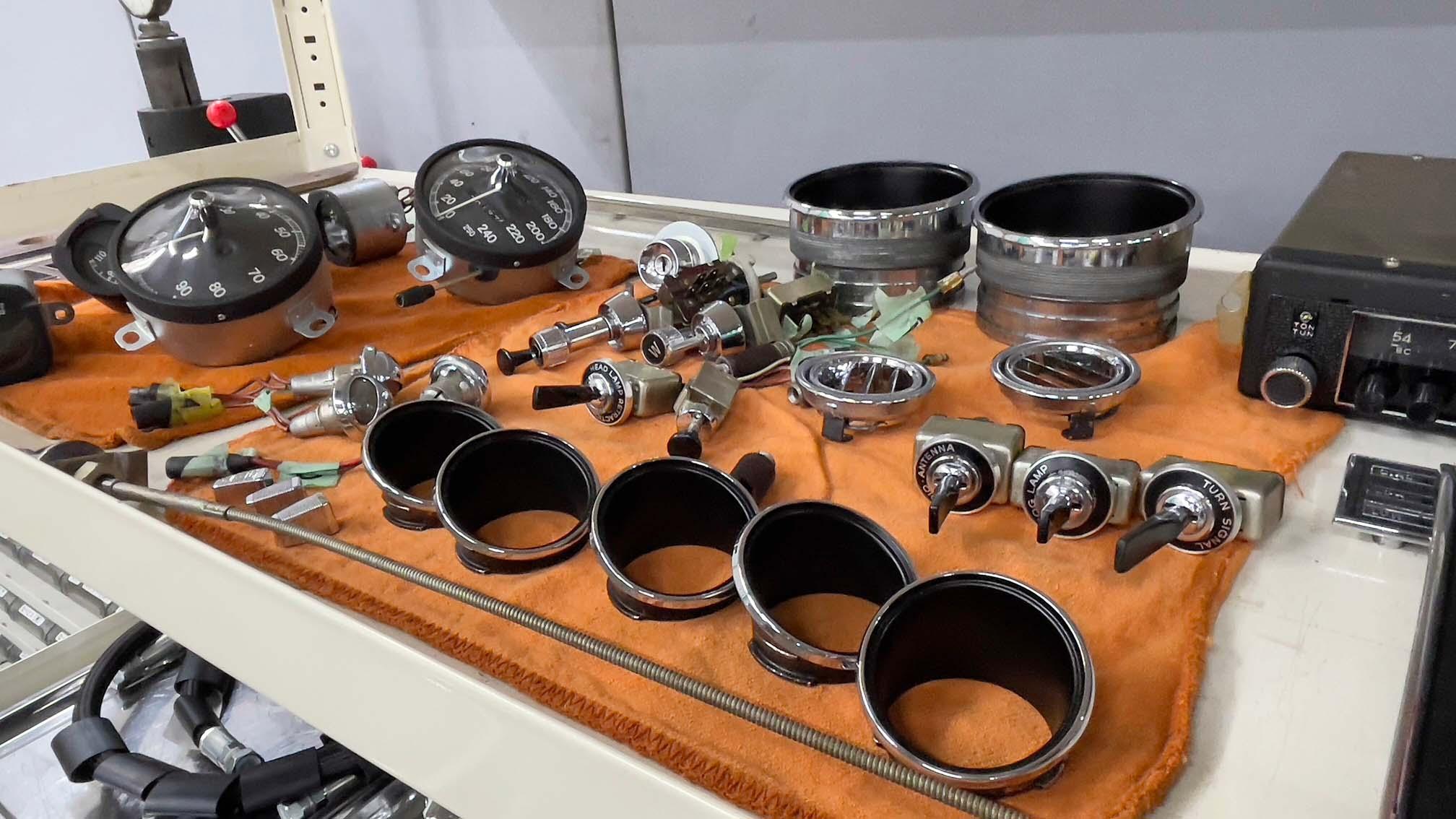
An even bigger surprise waited nearby—the X-shaped backbone frame that forms the 2000GT’s core. Shiny disk brakes and brake pipes were mounted at the four wheels. Sitting alongside was a beautifully restored transmission looking like new.
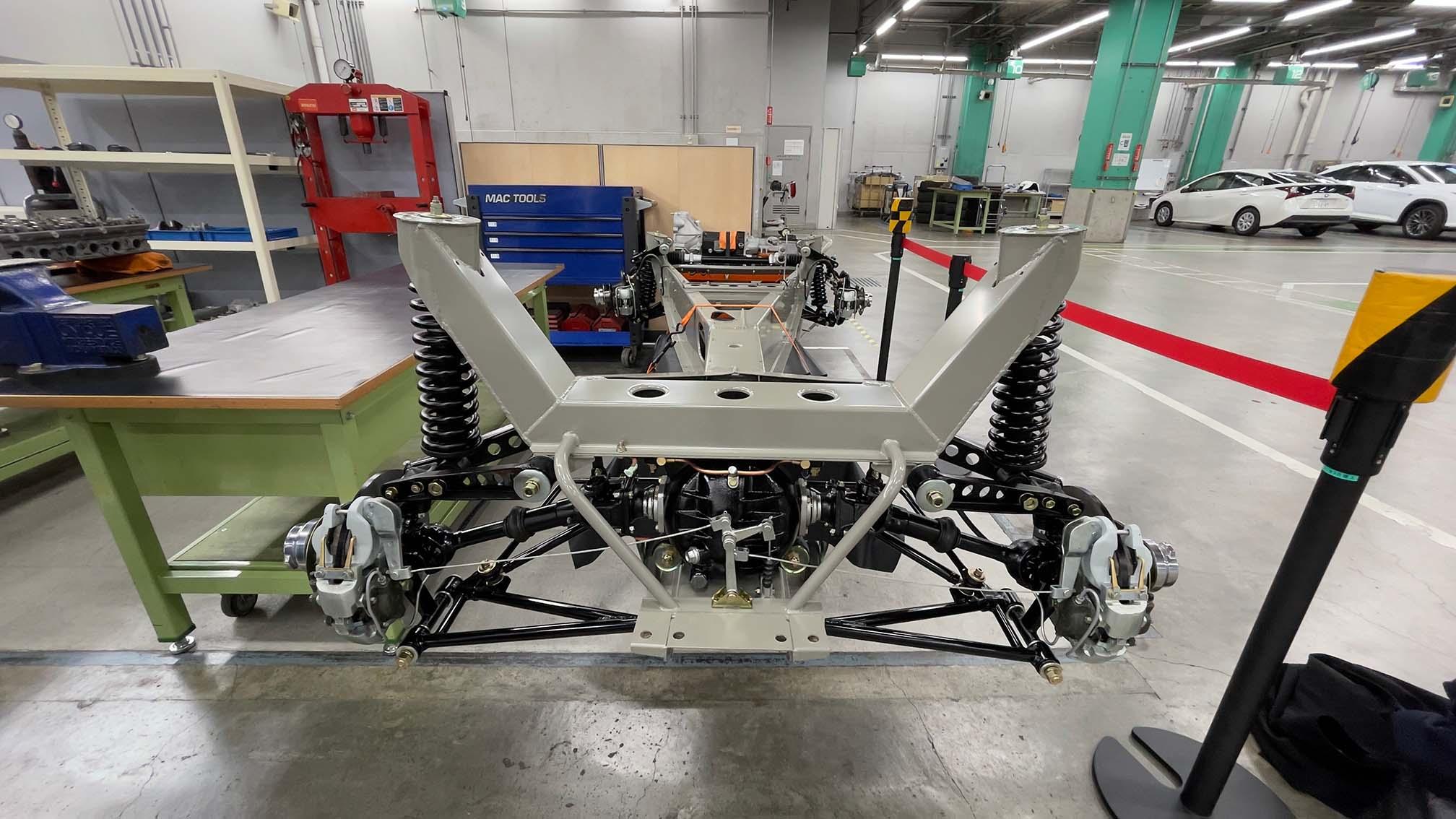
“Unfortunately, the box-like internal sections of the Toyota 2000GT’s frame tend to trap water, so they’re often in poor condition. For this X frame, we rebuilt the corroded parts from scratch. We also applied electrodeposition coating to prevent rusting of the internal parts,” explains Okada.
The car’s primed body awaited its main coating in a painting booth. Like the original, this body had been hand-hammered out anew by sheet metal artisans.
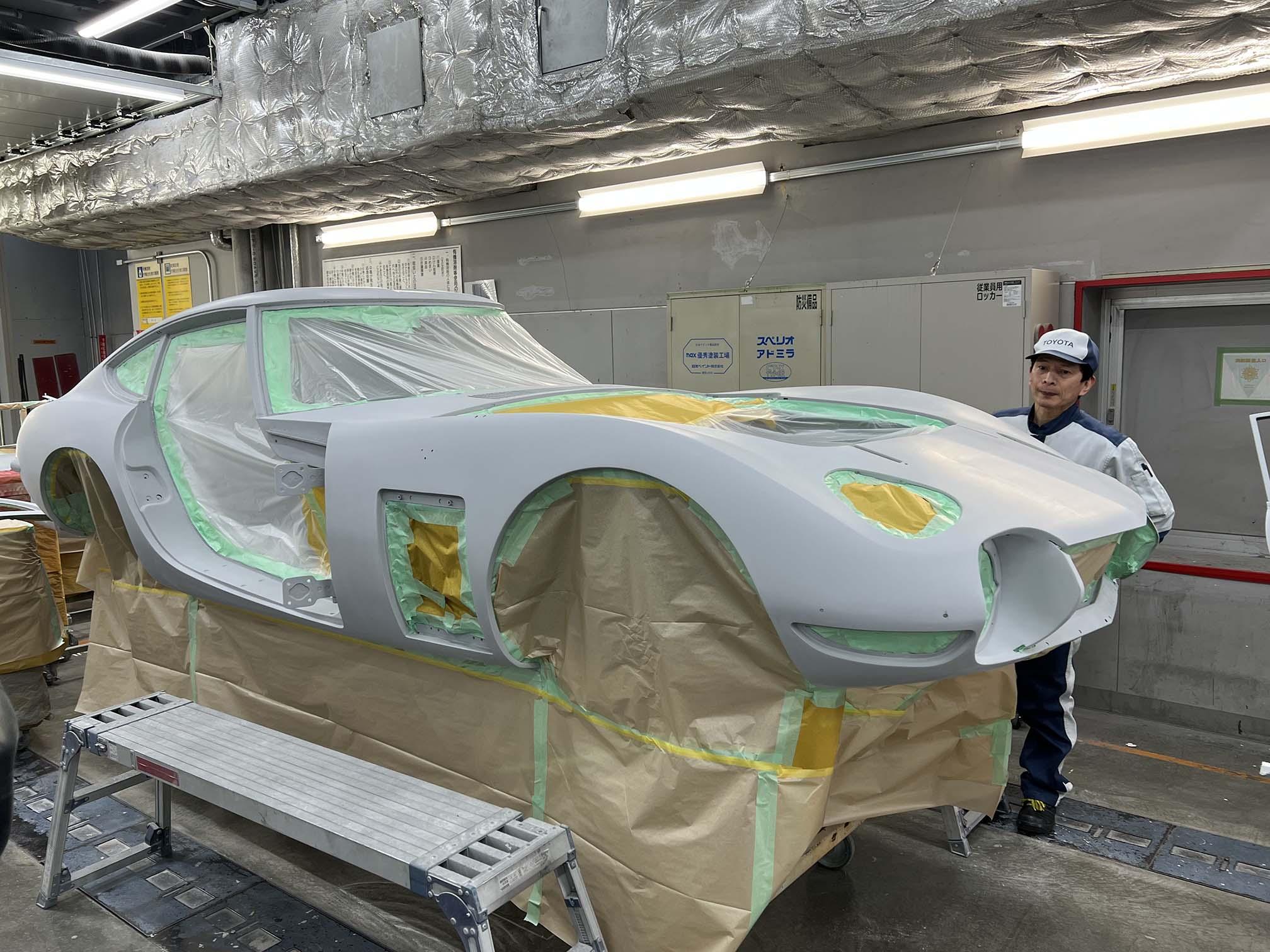
“For the undercoat, the best way is to dip the body in a paint pool as we do with today’s cars, but instead we applied it by hand, just like the original,” says Okada.
Sharing the art of full restoration with future generations
The work of restoring a car goes far beyond the bounds of an auto mechanic’s job. Full restoration in particular requires special skills and knowledge.
This work is mostly carried out by independent vintage car specialists, each with their own methods and equipment. For that reason, it is difficult to return a car to its completely original condition with genuine parts, even with a full restoration.
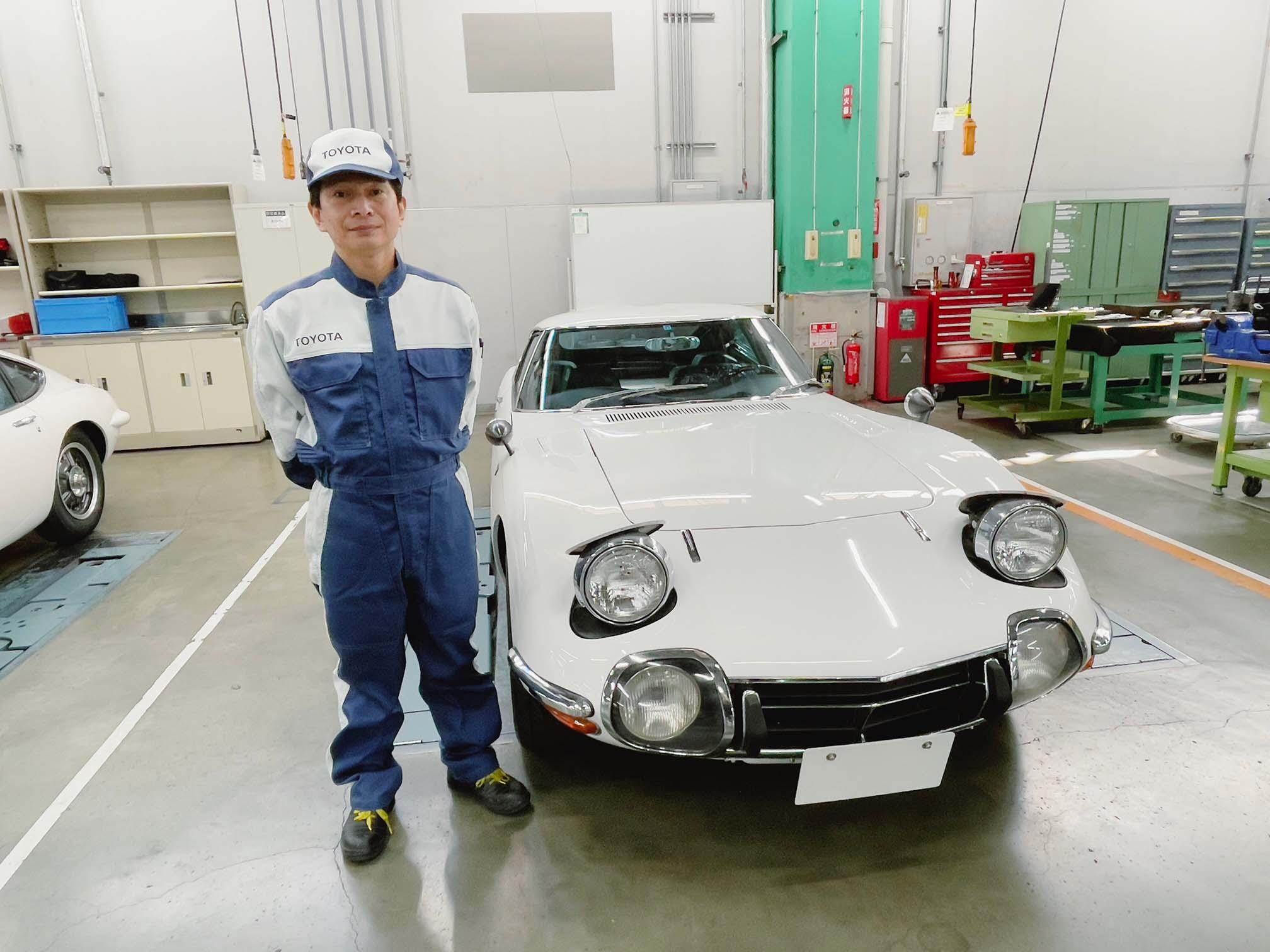
But Okada and his colleagues have long worked to maintain Toyota’s race vehicles and dedicated themselves to servicing the company’s cars. They know these machines inside and out, making their 2000GT essentially that of genuine manufacturer restoration. This full restoration approach of pursuing the car’s original state is rarely seen, either in Japan or elsewhere in the world.
“We want to fulfill the owners’ wishes of restoring the car as close to its original condition as possible,” says Okada. “We want to help pass these beautiful cars on to future generations in the best state possible.”
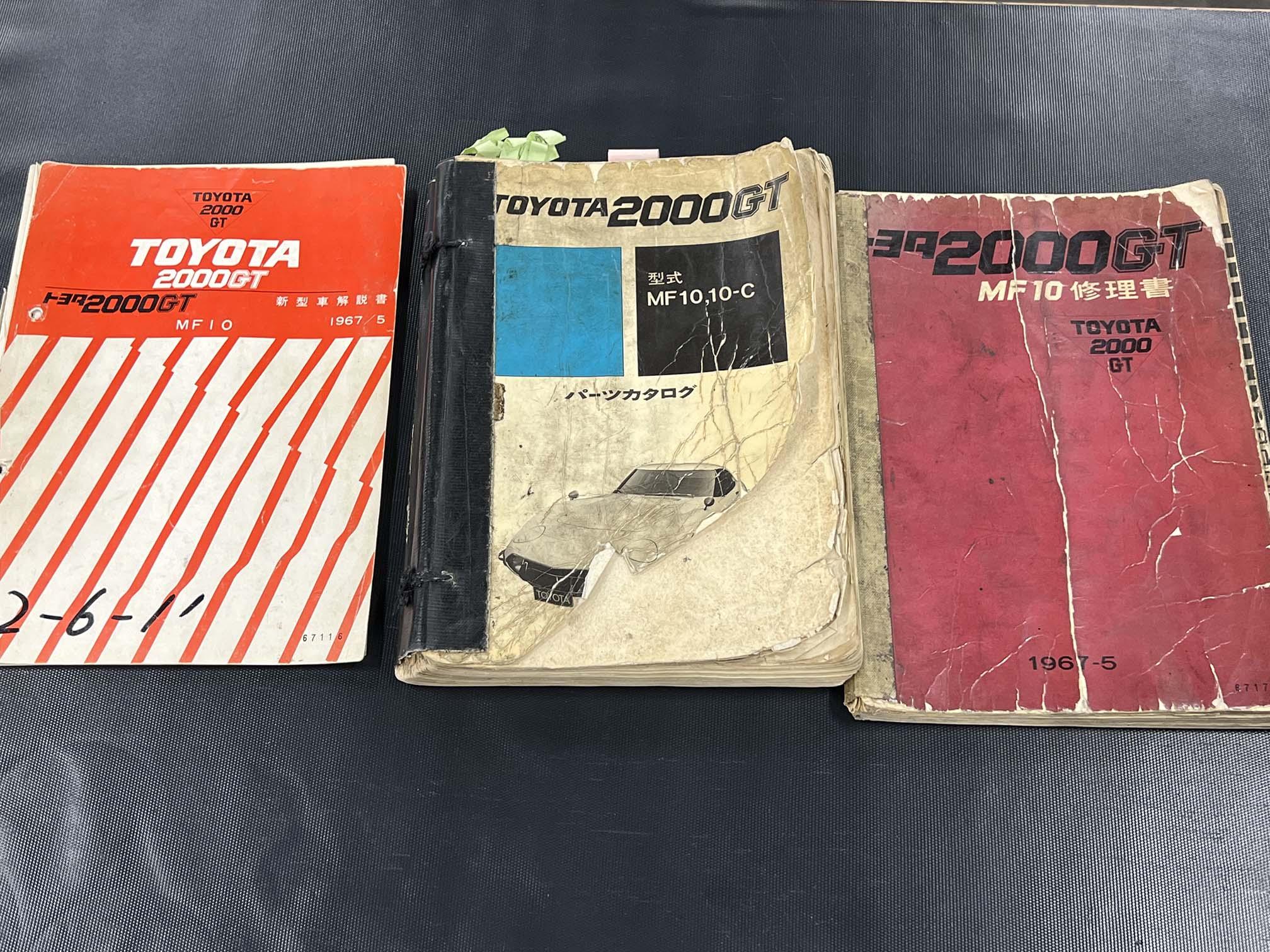
To that end, Okada is also engaged in passing on the restoration skills and expertise built up through his extensive experience to younger colleagues.
The Toyota 2000GT, created half a century earlier by Japan’s auto industry as the country’s first supercar, is reborn in the hands of Toyota’s master restorer, Koji Okada, and the young mechanics inheriting his craft. Thanks to their efforts, each drive by its owners will continue to evoke the beauty and performance of the car’s glory days.
(Text & photos: Yasuhito Shibuya)
Note: Toyota Met-Logic does not accept requests from individual customers or automobile service providers