
This two-part article features Shingo Yamashita, a multi-modeling master who creates authentic interior designs with unique skill at achieving superlative tactile experiences.

While many people focus on advanced technologies such as 3D printing or AI when thinking about innovation, much of the work involved in car manufacturing is still done by hand.
In this series, by interviewing some of the masters supporting Toyota’s manufacturing with their craftsmanship, Toyota Times uncovers the essence and core strength built on traditional Japanese monozukuri (making things).
This is part one of our interview with a master of interior design, multi-modeler Shingo Yamashita.
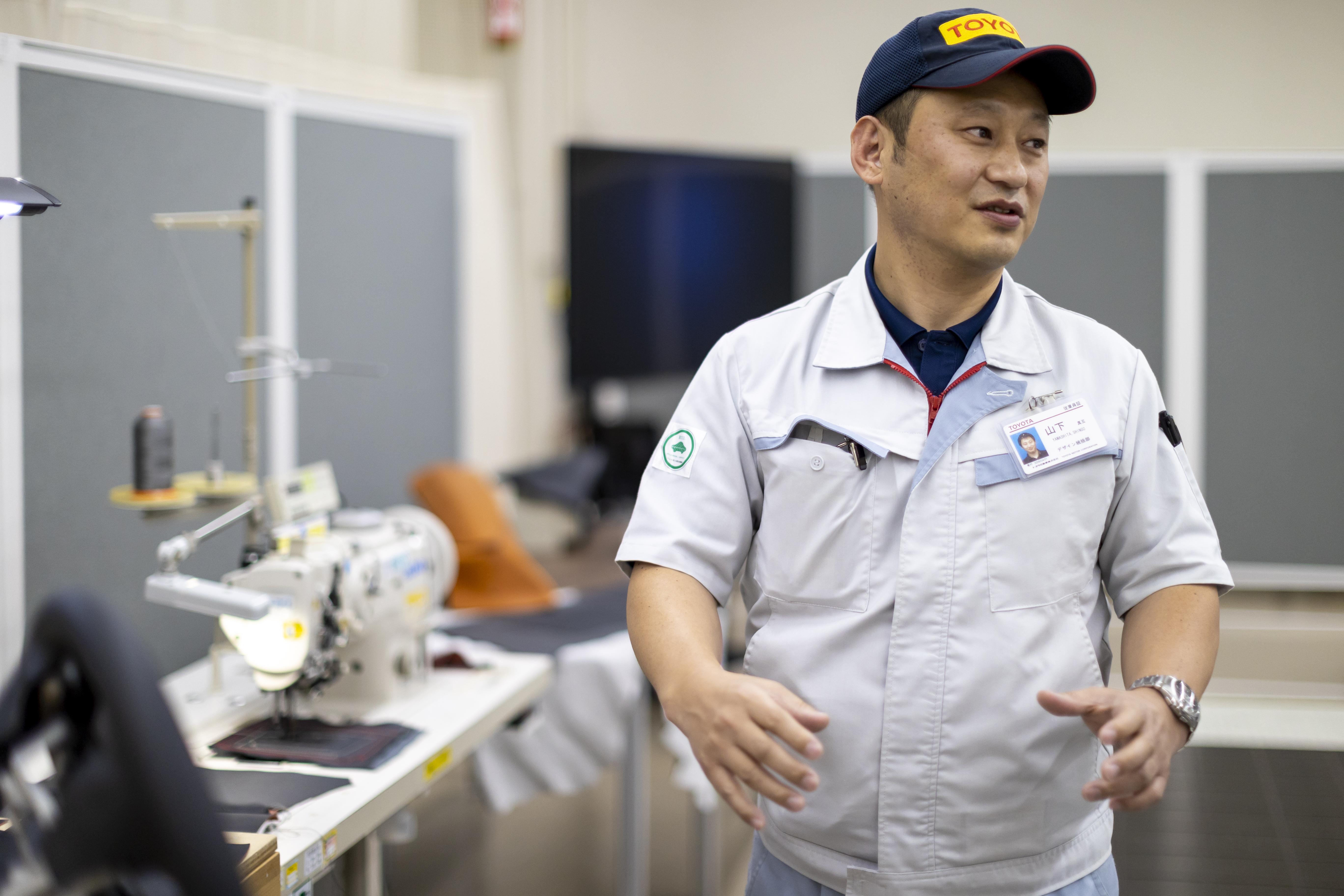
Series #8 - Master multi-modeler Shingo Yamashita turns designers’ visions into reality
Senior Expert, Interior Model Creation Section, Design Management Division, Vehicle Development Center at Toyota Motor Corporation
Full-size mockups of actual car interiors
In one corner of the Design Division stands a full-size mockup of a car interior. Every inch resembles an actual car–from the gauges and switches on the colorful instrument panel to the steering wheel, pedals, door trim and door handles. As you open the door, sink into the driver’s seat, and grip the wheel, you can’t help but feel that the machine is ready to drive.
This mockup uses the same materials as an actual car would to help finalize the interior design as part of the final stage of the design process.
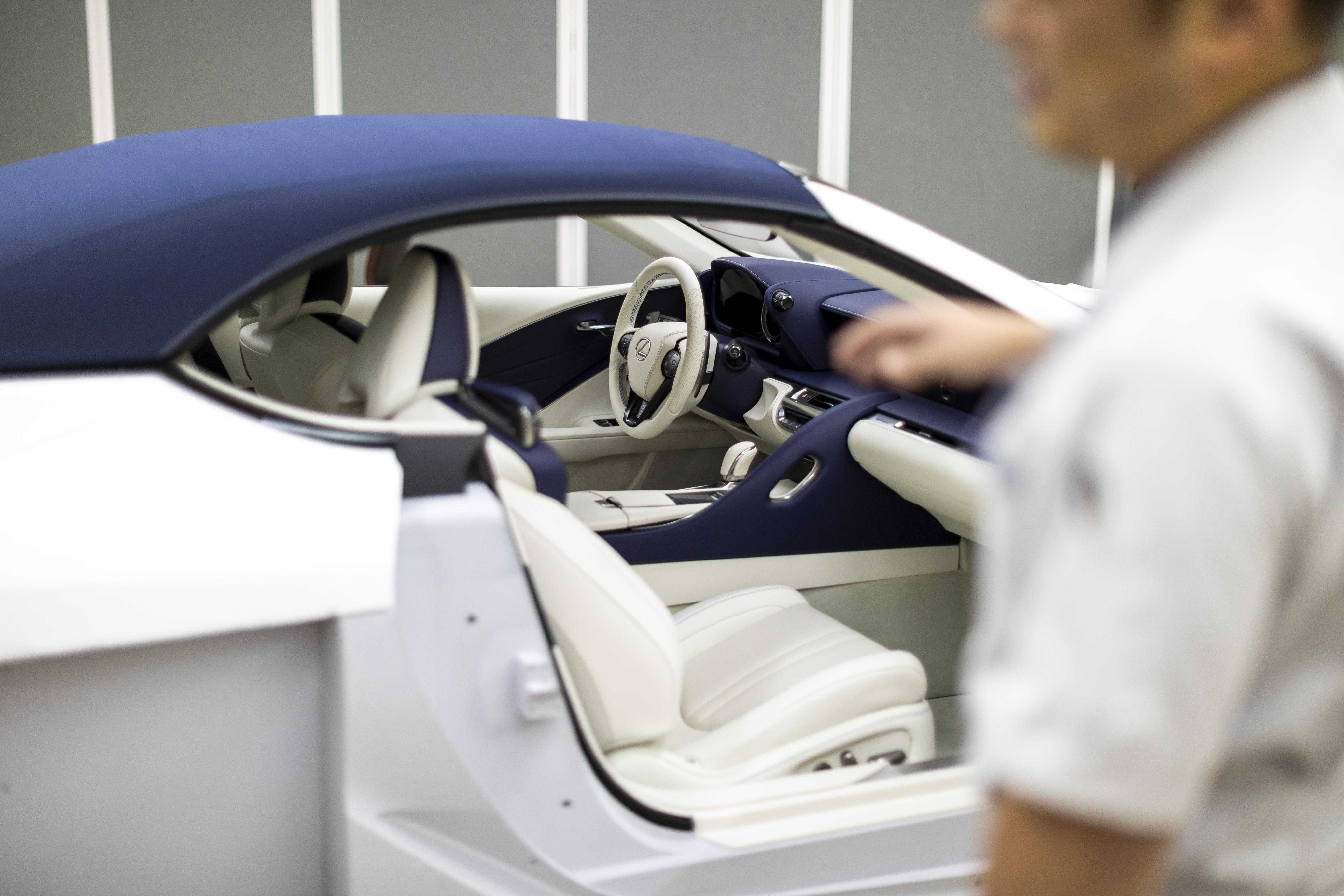
Shingo Yamashita is a hard modeler with an exceptional and versatile skill set to create such mockups. He is one of Toyota’s rare multi-modelers.
Even the leather that covers the steering wheel was flawlessly hand-sewn by Yamashita. “I never imagined I would end up working with a needle and thread at a car company,” he says with a laugh.
Interior design is as important as exterior
The inside of a car is a special space. Many people speak of the comfort a car offers, a feeling of relaxation they can’t find elsewhere.
The car is both a place of work and a place to rest and relax for drivers and passengers, who may sometimes spend long hours in their cars.
Therefore, a car’s interior design must combine functionality for safe, focused driving with a high degree of comfort for long journeys. There can be no compromise in areas that affect driving safety, such as driver and passenger seating positions, or the ease of operating the steering wheel, levers, or switches.
The tactile experience must also be pleasing, as drivers and passengers come into direct contact with a car’s interior. This often plays a more significant role than the exterior in defining a car’s image, value, or user satisfaction. The overall design of a car is formed by the synergy between its interior and exterior designs.
Interior design also faces the same strict constraints as a car’s exterior. How spacious is the interior? Where and how will the occupants sit? Where should you put the pillars, transmission, or air conditioner controls? A car’s interior must be designed to meet all the requirements created by of packaging, safety, and ergonomics considerations.
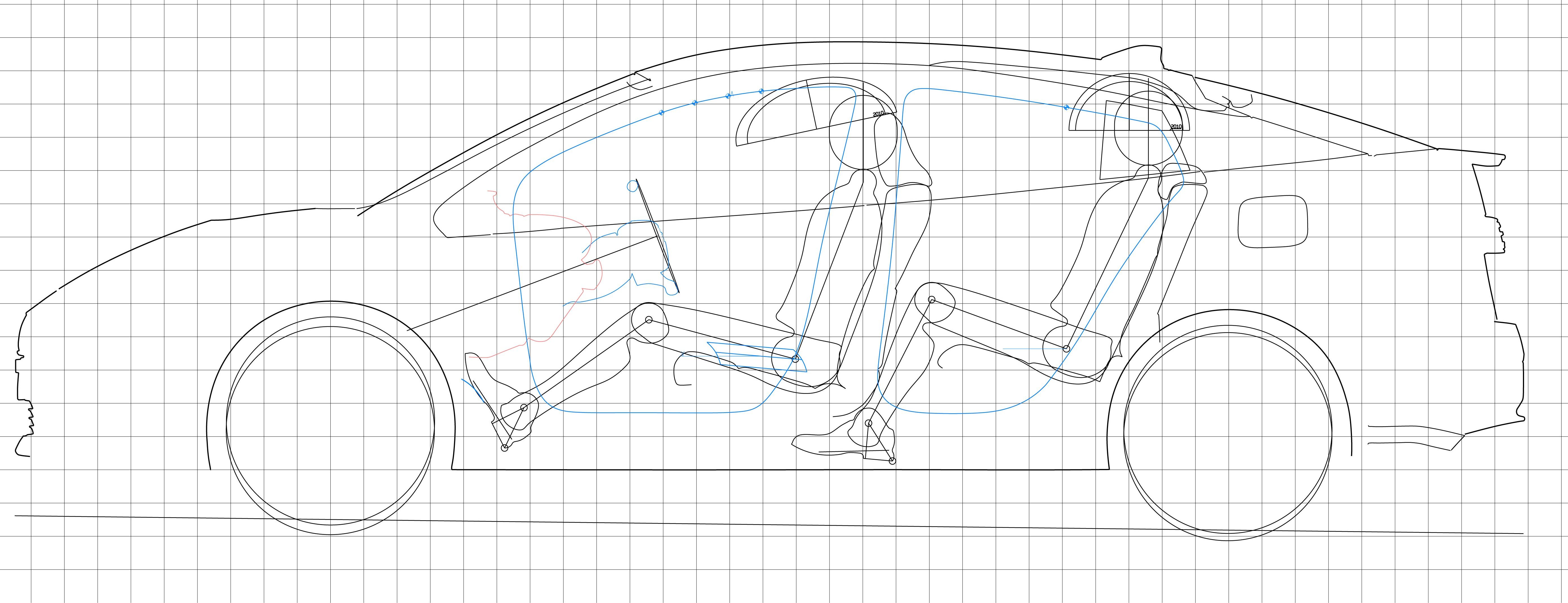
In this car design process, interior designers work together with hard modelers, the craftspeople who create models from the various materials used in actual cars.
Hard modelers communicate closely with designers to gain a deep understanding of their vision and ideas. Drawing on their own experience and expertise, modelers work step-by-step to give form and texture to designer’s sketches and virtual interior designs generated by 3D-CAD software.
With the design process becoming increasingly digital, designer sketches are first thoroughly reviewed and refined using digital tools such as 3D-CAD and 3D-CG. At this stage, VR is also used to review the interior space.
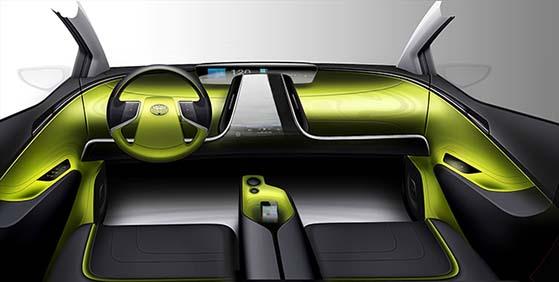
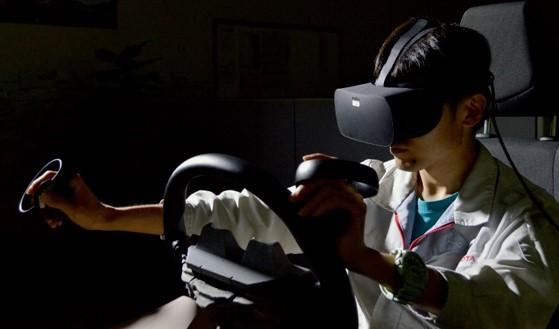
At the same time, design mockups of key parts are made using resins, metals and other materials similar to those used in actual vehicles. The purpose of these mockups is to check how a designer’s idea will look, feel, and behave when made real.
Based on these mockups, designers and hard modelers go back and forth between physical and digital models, thoroughly reviewing the interior design to find areas for improvement. Throughout this process, hard modelers may also make suggestions to designers.
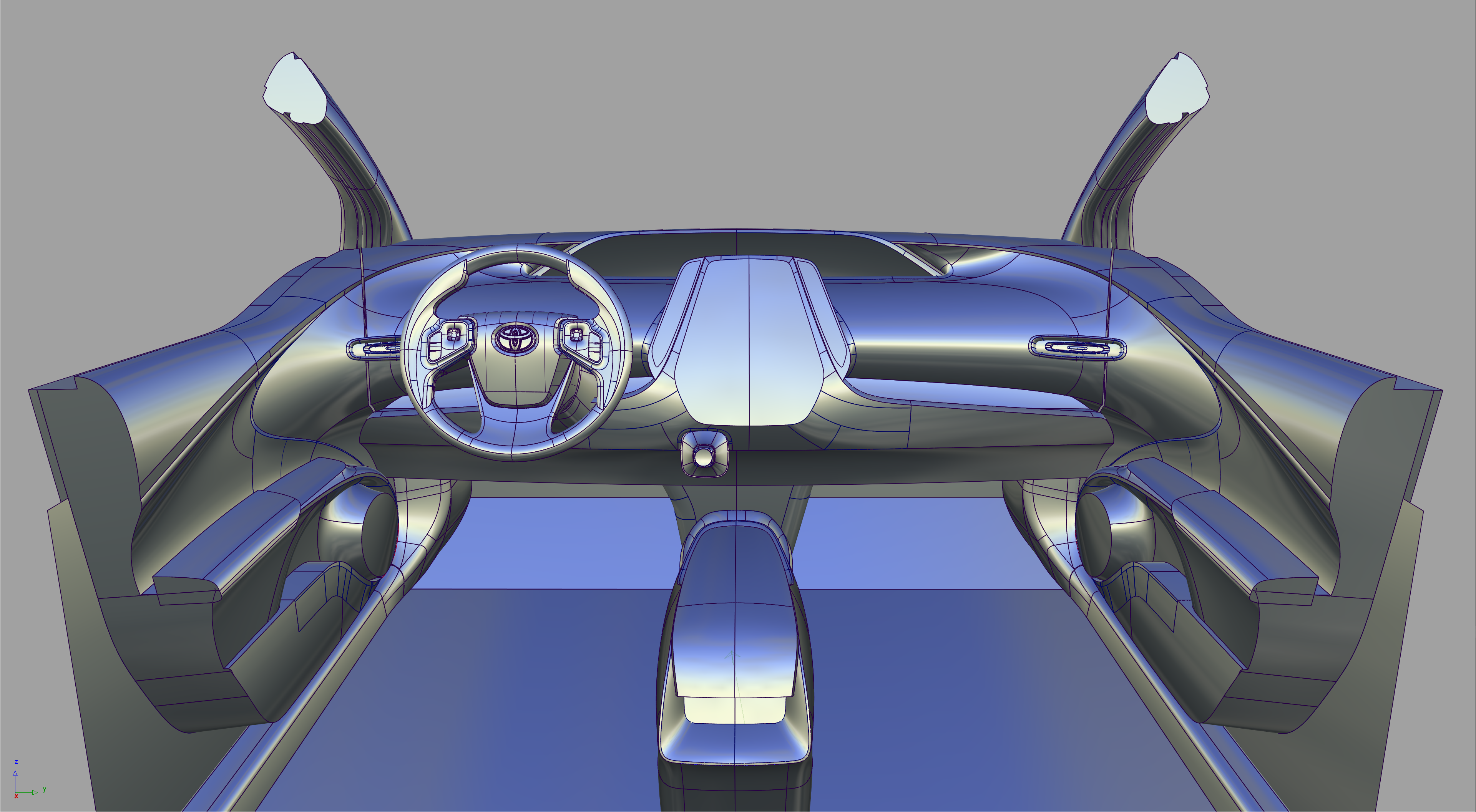
Once interior design specifications are finalized, it is time for the hard modeler’s knowledge and skills to truly shine. Using genuine car materials, they produce a full-size mock-up to be shown at an executive meeting to authorize the final design. Just as clay modelers are essential for exterior design, interior design cannot be achieved without a hard modeler.
From craft-loving youth to WorldSkills champion
Yamashita was born in Toyota City, Aichi in 1973. With his childhood home only a 15-minute walk from his current workplace, Yamashita is a true local. Growing up, he loved to craft and make things. By the time he was in junior high, Yamashita was delighting friends and family with his skillfully made creations.
“I also liked plastic models, and I made them a lot,” says Yamashita.
After junior high, Yamashita went on to Toyota’s in-house training facility, the Toyota Technical Skills Academy. In his second year, he was selected as a woodworking trainee for the National Skills Competition.
“I chose the academy because I enjoy making things, and the idea of learning while being paid to work appealed to me. In my second year, I found joy in woodworking and started training to compete in the National Skills Competition.”
In 1992, Yamashita won the Fighting Spirit Award in woodworking at the 30th National Skills Competition. He then went on to take silver at the 31st competition and gold at the 32nd. Then in 1995, Yamashita represented Japan in the 33rd WorldSkills Competition held in France. Among the gold-studded Japanese team, Yamashita was honored as the best in Japan. This not only made him a world champion in woodworking, but also the best among the Japanese competitors.
From hard modeler to a one-of-a-kind multi-modeler
In 1996, at the age of 23, Yamashita was assigned to the Design Division. He started working as a hard modeler tasked with creating car interior models and external parts from wooden forms. Thus began his daily education under the tutelage of workplace veterans.
External parts included grilles, lamps, wheels, and other components which are difficult to fabricate with industrial clay. In the design prototype stage, the hard modeler heats plastic materials in an oven, and molds them to look just like genuine parts.
“They can teach you the basics, but then it’s up to you to hone your skills. It eventually becomes a battle against yourself. Some people struggle with that, but I personally enjoyed every bit of it.”
By 2001, after a decade at Toyota, Yamashita was also serving as an instructor for skills competitions.
Around this time, Yamashita also branched out from woodworking to tackle various other fields, including welding, 3D-CAD operations, NC machining and even partial modeling in clay. Yamashita established a unique position as a multi-modeler by mastering range of skills required to produce physical models beyond the bounds of a conventional hard modeler.
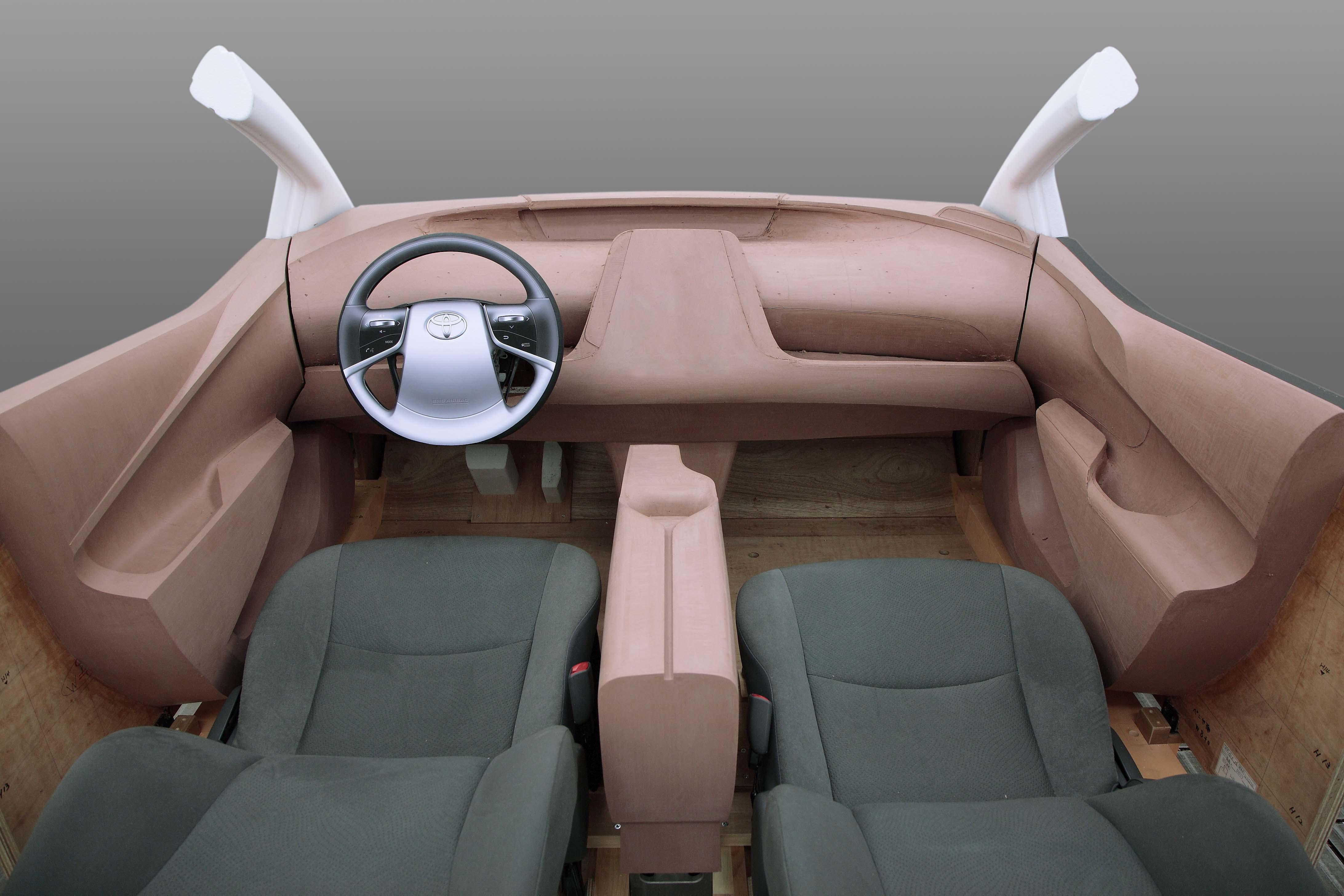
To create a full-scale mockup for the final design review, parts made of wood, Styrofoam, clay, resin, metal, and other materials are assembled onto a steel frame base before painting and applying the leathers and fabrics typically found in a car interior.
As a multi-modeler, Yamashita is able to create a full-scale mockup of an actual car almost from the ground up, using the optimal methods to perfect it in the shortest possible time.
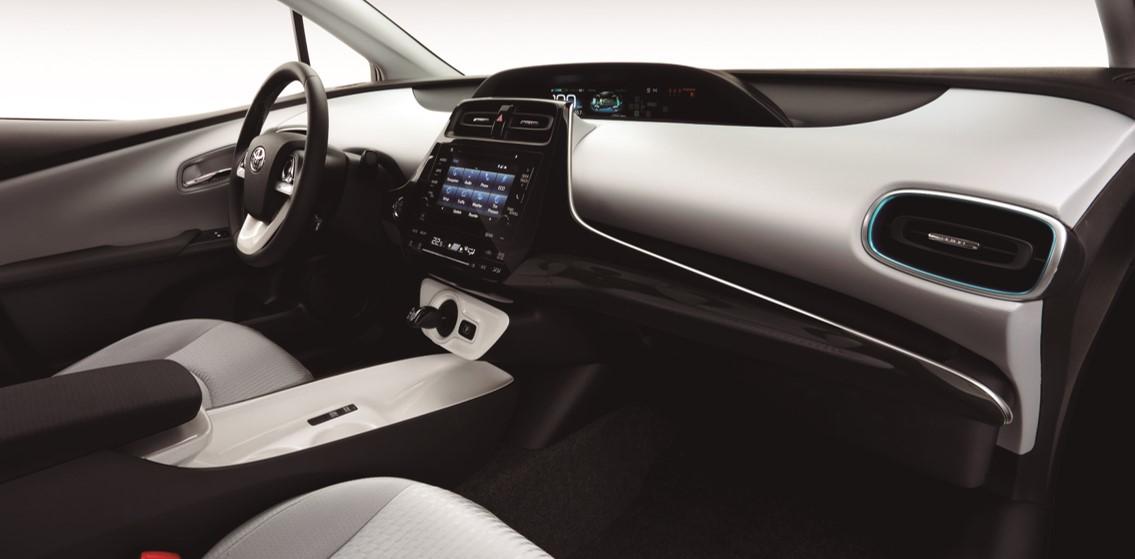

“Having started out in woodworking, each skill and technique I learned and improved opened up new possibilities in monozukuri. But there is still plenty of room for improvement. I want to master other new skills to make ever better products.”
Yamashita currently holds an M-Class certification in modeling skills, one of Toyota’s highest technical qualifications. Even so, he’s not satisfied yet.
Pursuing monozukuri in private life
In 2005, Yamashita spent three months assisting operations at ED2, Toyota’s European design center in Nice, France.
In 2007, he provided similar assistance during a three-month visit to Toyota’s U.S.-based design studio, Calty Design Research in Ann Arbor, Michigan.
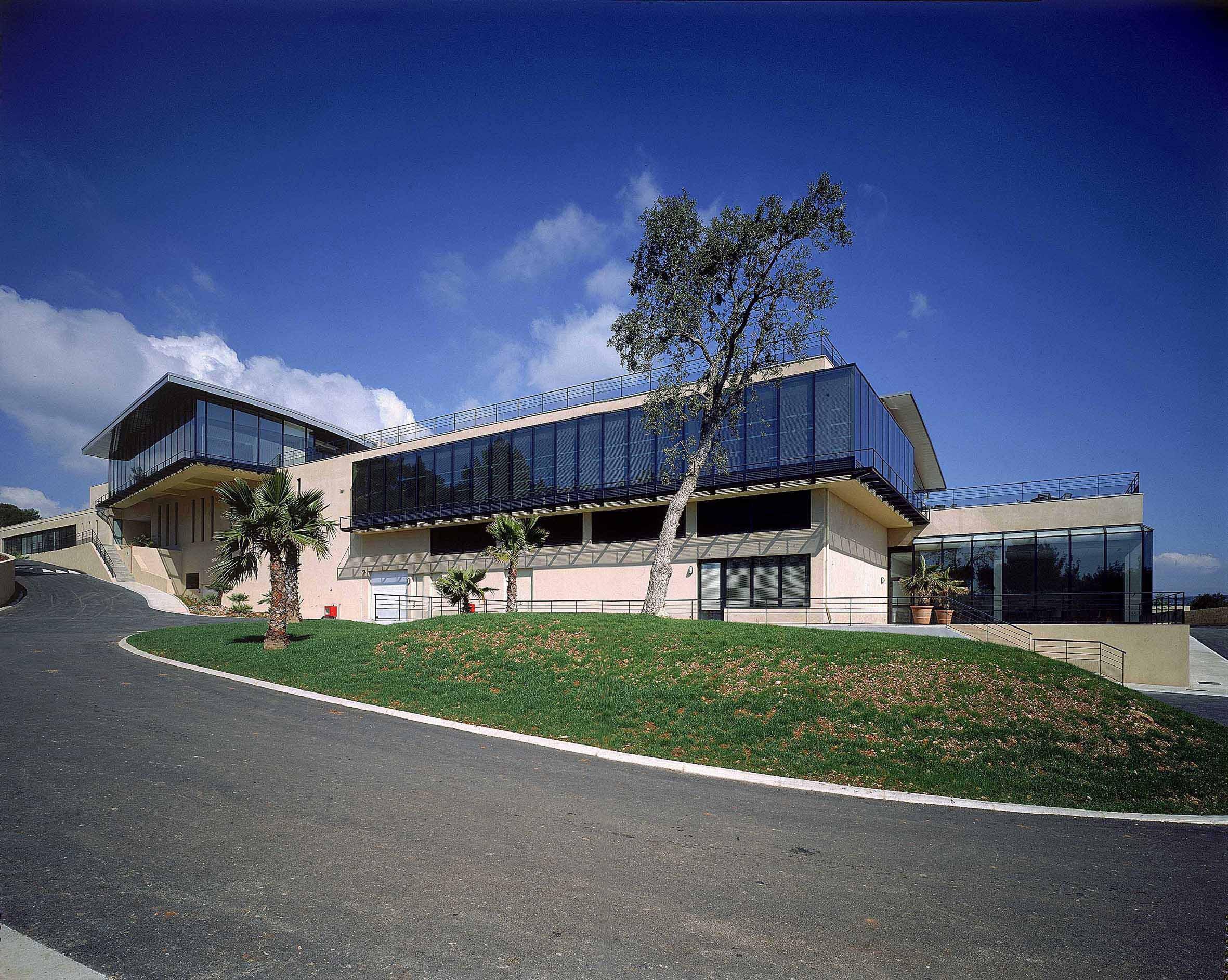
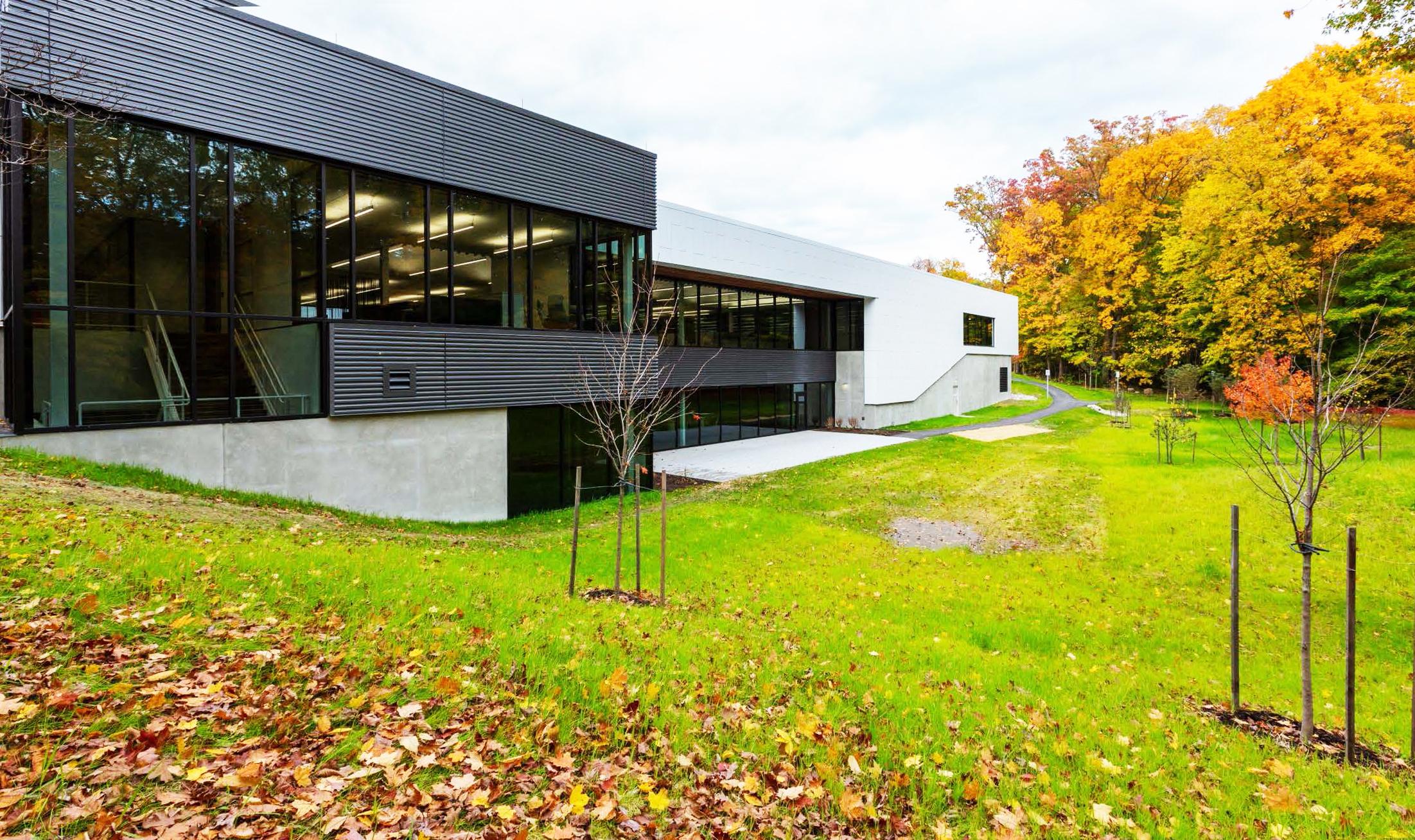
In 2015, on being promoted to group leader at the age of 42, Yamashita traveled with designers to the Milan Furniture Fair, an Italian trade fair showcasing furniture and design. They wanted to learn about upcoming trends in interior design.
Yamashita says that such occasions present the perfect opportunity to deepen his understanding and knowledge of design and materials, while honing his skills and style.
One of Yamashita’s current monozukuri endeavor is leathercraft. Although he had enjoyed it as a hobby, the inspiration to turn it into work came while crafting a leather steering wheel for a mock-up.
The handbag below was Yamashita’s prize-winning entry in a leathercraft contest. At first glance, the high-quality leather and elegant sewing would not appear out of place among luxury brand products.
“I care about authenticity. When I buy a designer brand bag for my wife, I don’t just look at the design, but also the material, the workmanship in the details, and even the sewing. Even designer bags can be made with poor materials and craft.”
Yamashita’s pursuits aren’t limited to leathercraft. He also creates astonishingly detailed wooden sculptures, including an intricately carved qilin (a mythical Chinese creature). His work is now in the realm of artistry.
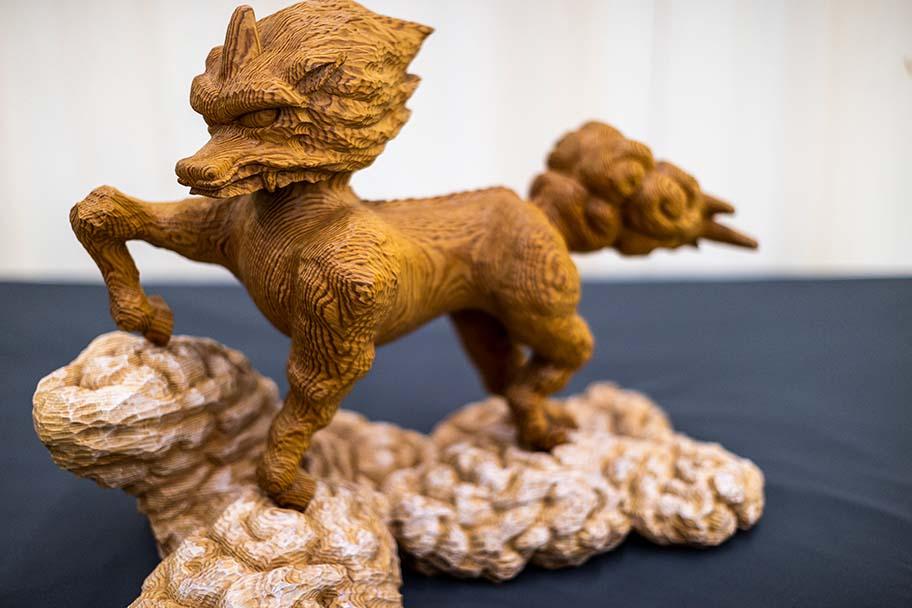
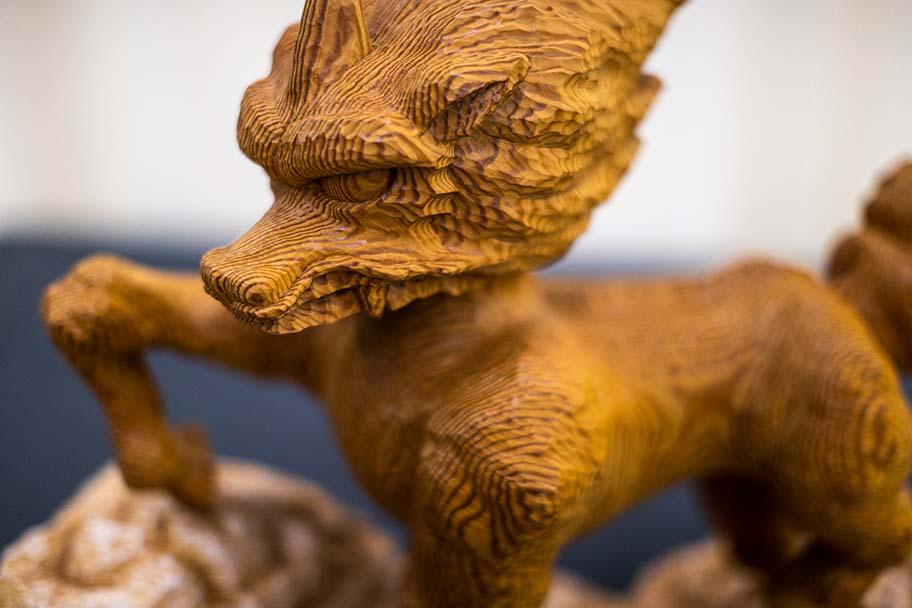
“Quite a few of the other hard modelers here also try their hand at monozukuri competitions. Many of us just love making things.”
Yamashita says that to create better products, it is important to hone your aesthetic sense and become familiar with genuine items and materials. To that end, one must constantly develop an appreciation of the “authentic” by attending exhibitions and lectures showcasing art and master craftsmanship.
This is the spirit of a true craftsperson. Had he not joined Toyota, Yamashita would undoubtedly have found success in traditional crafts or other forms of monozukuri.
The second part of this article delves into the full-size mockup production process led by Yamashita.
(Text: Yasuhito Shibuya, photo: Akira Maeda)