
Toyota Times uncovers the essence and core strength of the traditional Japanese monozukuri (making things), which is woven from the past into the future. The fourth interviewee is a master of sheet-metal welding.

While many people pay attention to advanced technologies such as 3D printers and AI when it comes to making something new, there is a lot of handmade work remaining in the frontlines of car manufacturing.
In this series, by interviewing some of the masters supporting Toyota’s manufacturing with their craftsmanship, Toyota Times uncovers the essence and core strength of the traditional Japanese monozukuri (making things).
The fourth interviewee is Eisuke Yoshino, a master of sheet-metal welding.
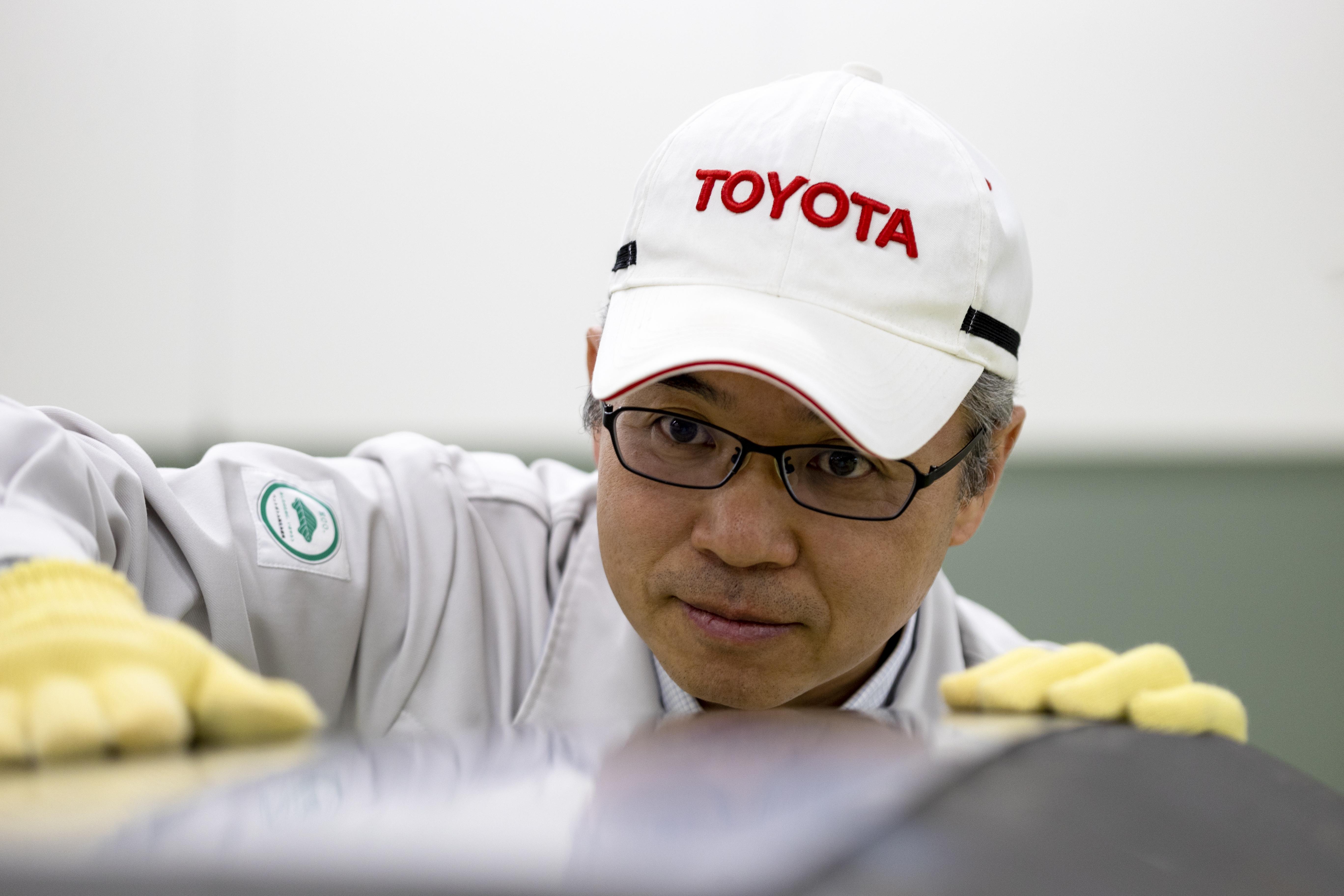
Series #4 Eisuke Yoshino, a master of sheet-metal welding who makes car bodies by hand from steel plates
Yoshino is Assistant Manager of Prototype Body Production Section, Technical Development & Prototype Division, Production Engineering Development Center at Toyota Motor Corporation.
Using hammers and welding to make prototype car bodies by hand
The first step of car body making begins with the designer sketching a design of the car. Then the engineering design divisions use the sketch to create design drawings for the entire car and the various necessary parts using cutting-edge 3D design software. Creating the drawings for the car body is part of this process.
Recently, 3D design software is being used to control machining tools to create parts straight away. However, this method cannot be used when making body parts that are larger than other function parts.
Generally, the body of a production car is made by pressing a large steel plate into the desired shape at once using a large press machine. Data from 3D design software is also used in this case, but a large mold is required to press such a large body.
Producing a large mold for a body is costly and inefficient. That is not a problem when manufacturing the body of a production car, but this method cannot be applied at the prototype stage of new models.
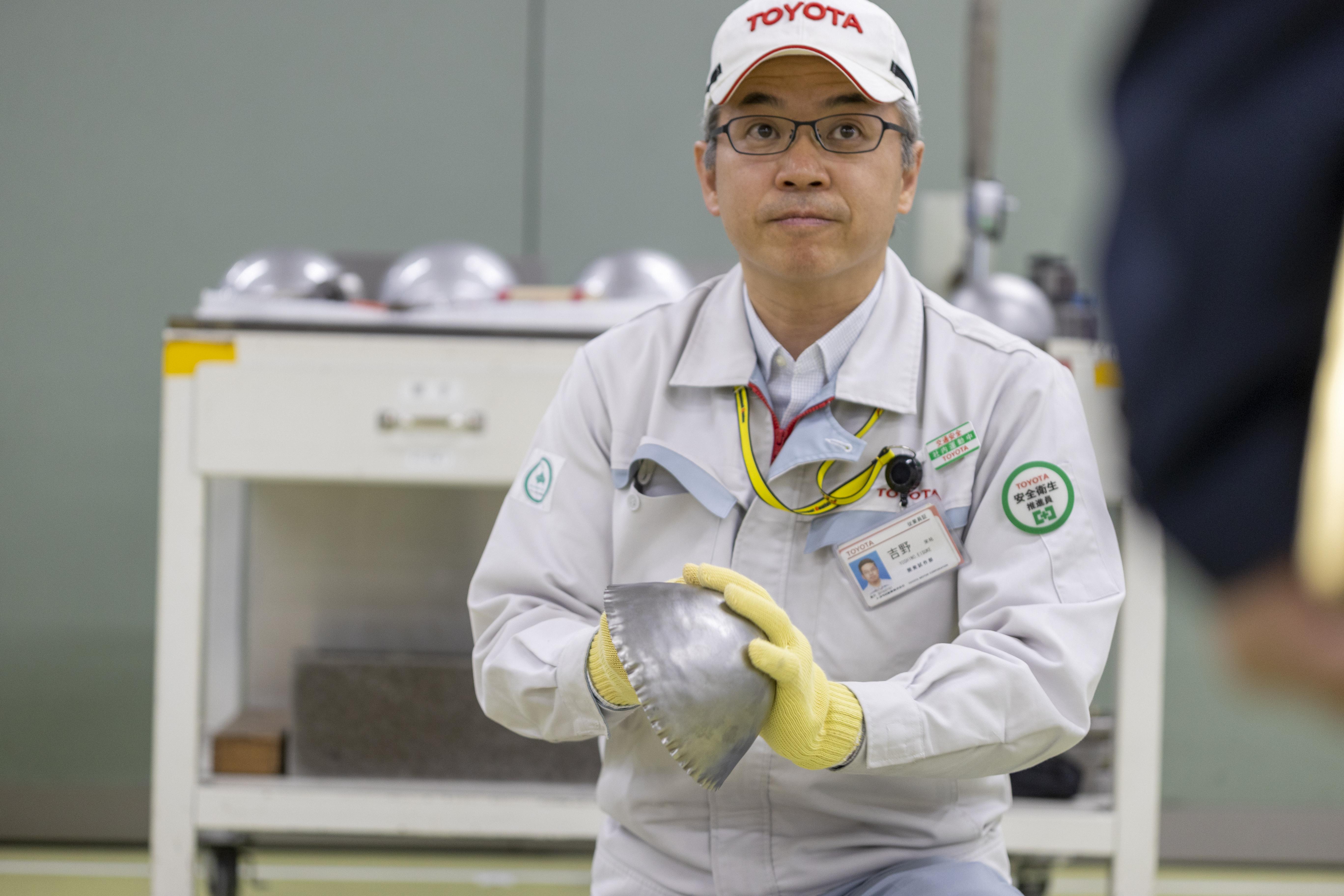
A newly developed car usually starts its journey as a prototype car. Then, the prototype goes through various tests and a thorough verification process to check for any issues with functionality, safety, durability or quality. Dozens of prototype cars are built and destroyed, and by solving the problems revealed along the way, the car eventually gets ready for production and sale.
The sheet-metal craftspeople play a key role here in this creation process, as it was the case when Toyota manufactured their first prototype car, the Model A1 in 1935. They use an extremely primitive method that involves hammering to bend and manipulate a flat steel plate, followed by welding additional steel plates if necessary to bend or manipulate even further.
Eisuke Yoshino is taking the lead of this job at Toyota’s genba of the Prototype Body Production Section, Technical Development & Prototype Division, Production Engineering Development Center. In 2020, Yoshino was certified in Toyota as one of the dozen Class S Technicians in the area of molding and processing sheet-metal parts without any drawings.
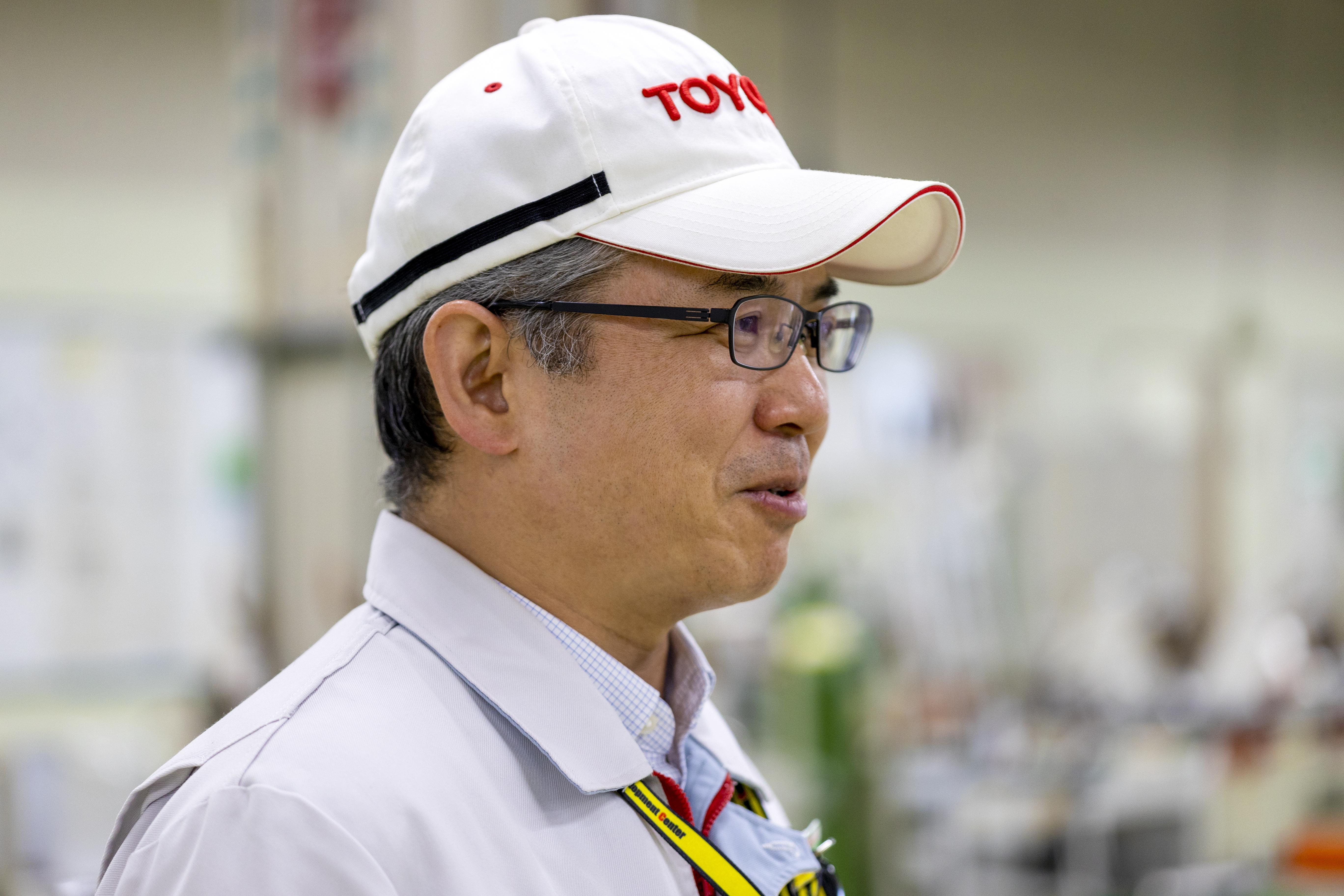
As a leader of the Prototype Body Production Section, Yoshino has made it his mission to pass on the traditional skills of Toyota's sheet-metal craftspeople inherited from the Model A1 era. He is one of the most skilled master of sheet-metal welding in Toyota.
Creating from scratch using 3D data
“Making a prototype of car body begins with viewing the visual data of the 3D design software on a display. Sheet-metal craftspeople can create something from scratch relying only on their past experience.
We can quickly look at an image to determine the size, decide where to begin, figure out where and how to bend the steel sheet and move forward while considering the thickness and quality of the material being used. We then consider how and in what order the work should be done while making things cheaper and more efficient. We also make our own jigs.”
Yoshino can imagine how to proceed the moment he sees the 3D design data. This job can only be done by a highly skilled sheet-metal craftsperson at his level. He said that it takes at least 5 to 10 years to get to that level.
“There is more than one way to make a prototype of car body. Depending on who is making it and the purpose of the prototype car, there can be a lot of differences even if it’s for the same product. There can be any number of correct ways to make it, so when I direct other craftspeople at the job site, I encourage them to think of their own way.”

The person in charge decides what method to use based on his or her skill set and the purpose of the prototype body. Will it be used for collision safety tests or endurance tests? Is it just to check the appearance? The approach varies depending on the purpose.
“After confirming the purpose of the body, I determine what method to use to most efficiently produce the cheapest and highest quality products that meet the requirements. We sometimes rely on other departments for cutting, laser machining, pressing and so on. That combined with our manual work, allows us to produce the body in the best possible way,” says Yoshino.
Designers can freely sketch shapes on 3D design software, but that doesn’t always translate into the actual body making in real life. Some parts have to be cut and spliced to create a large body. In other words, the body must be divided into sections and welded together even if it is not sketched explicitly in the blueprint.
However, the strength of the parts decreases when cut and spliced. Therefore, the division must occur at the least problematic spot to maintain its strength depending on the purpose and application. The years of experience matter when judging where and how to cut and splice to make the desired parts in the design.
For new models under development, dozens of units must be manufactured by hand from steel plates that match the material of the prototype car within a margin of error of 0.1 mm. This must be done in a limited time while considering the purpose and application, following the design data and using their own jigs.
At any given time, cars are consistently viewed as the most cutting-edge of all industrial products, but their bodies cannot be made without the manual work of craftspeople like Yoshino.
A boy who loved plastic models and monozukuri
Born in Mie Prefecture located next to Aichi Prefecture, where Toyota is headquartered, Yoshino has dedicated his life to making car bodies by hand throughout the 33 years since joining the company in March 1987.
He first experienced working with sheet-metal processing when he was at Toyota Technical Skills High School (currently Toyota Technical Skills Academy). During his second year in school, he was selected as a "hammer forming sheet-metal trainee” for the Skills Olympics, and participated in the national competition in this field in his second year at Toyota.
In his third year, he took first place in Japan’s national competition, and this year he also participated in the WorldSkills Competition and won second place. He received a special award within the company in addition to receiving the Minister of Labor Award.
“It was my decision to go to Toyota Technical Skills High School. I researched schools on my own, and told my parents, ‘I want to go there’. I wanted to work in a job related to cars; it was actually a test driver that I desired to be when I first entered the school.
In my childhood, I would often make plastic models of cars. When I was in junior high school, I would also disassemble and reassemble the Super Cub. That’s why I was able to complete assignments with ease when I tried working with sheet-metal in school. I have always liked monozukuri, so I am happy with my current job.”
Both the teachers at the school and the bosses at the company must have spotted Yoshino's extraordinary talent and technological potential from early on. Yoshino was posted to the prototype body production section as soon as he joined the company, and was assigned the job of remodeling car bodies after successfully competing in the Skills Olympics. His talents have been on display at the genba ever since.
“The Skills Olympics has certain assignments, but when starting my job in genba, there were no fixed tasks. I was flustered at first, but I learned to like it. Back then, the Celica GT-Four was sweeping the WRC (World Rally Championship). While maintaining the appearance of the Celica GT, the body panel had been replaced with a thin steel plate to reduce weight.
I was also working on sending a white body (the state prior to mounting the engine, etc.) with reinforced parts to Toyota Team Europe, so I was very happy when that car won the championship.”
Followed by the work of modifying the body of commercial and rally cars, and “body remodeling” to make a prototype body for evaluation by remodeling the body when making minor changes to the current car, Yoshino has worked on special sheet-metal.
His job was to make event-cars to be exhibited at motor shows and toy shows relying only on design sketches without drawings or jigs after prototyping sheet-metal parts using materials that are difficult to process, such as aluminum, stainless steel, copper, titanium and special alloys.
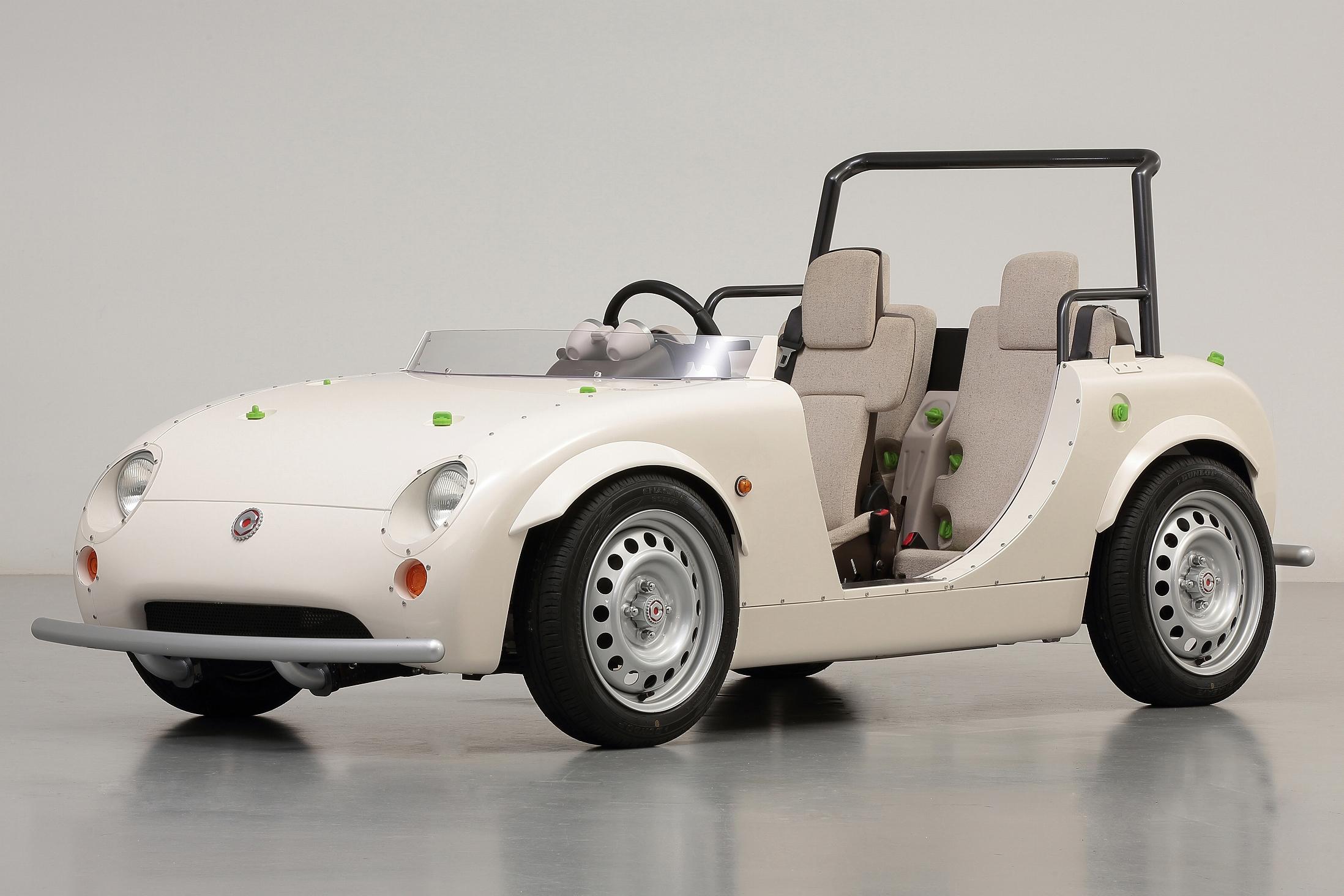
In particular, Yoshino told that the body production of the event-cars exhibited at the International Tokyo Toy Show from 2012 to 2017 and the demonstration of sheet-metal manufacturing at the same shows were memorable. He said that he was able to dramatically reduce costs and work time by devising a way to divide parts quickly and cheaply without any jigs.
Sheet-metal work that relies on instincts and feel
So, what exactly are Yoshino’s masterful sheet-metal skills? He demonstrated his hand working skills using a hammer in his genba.
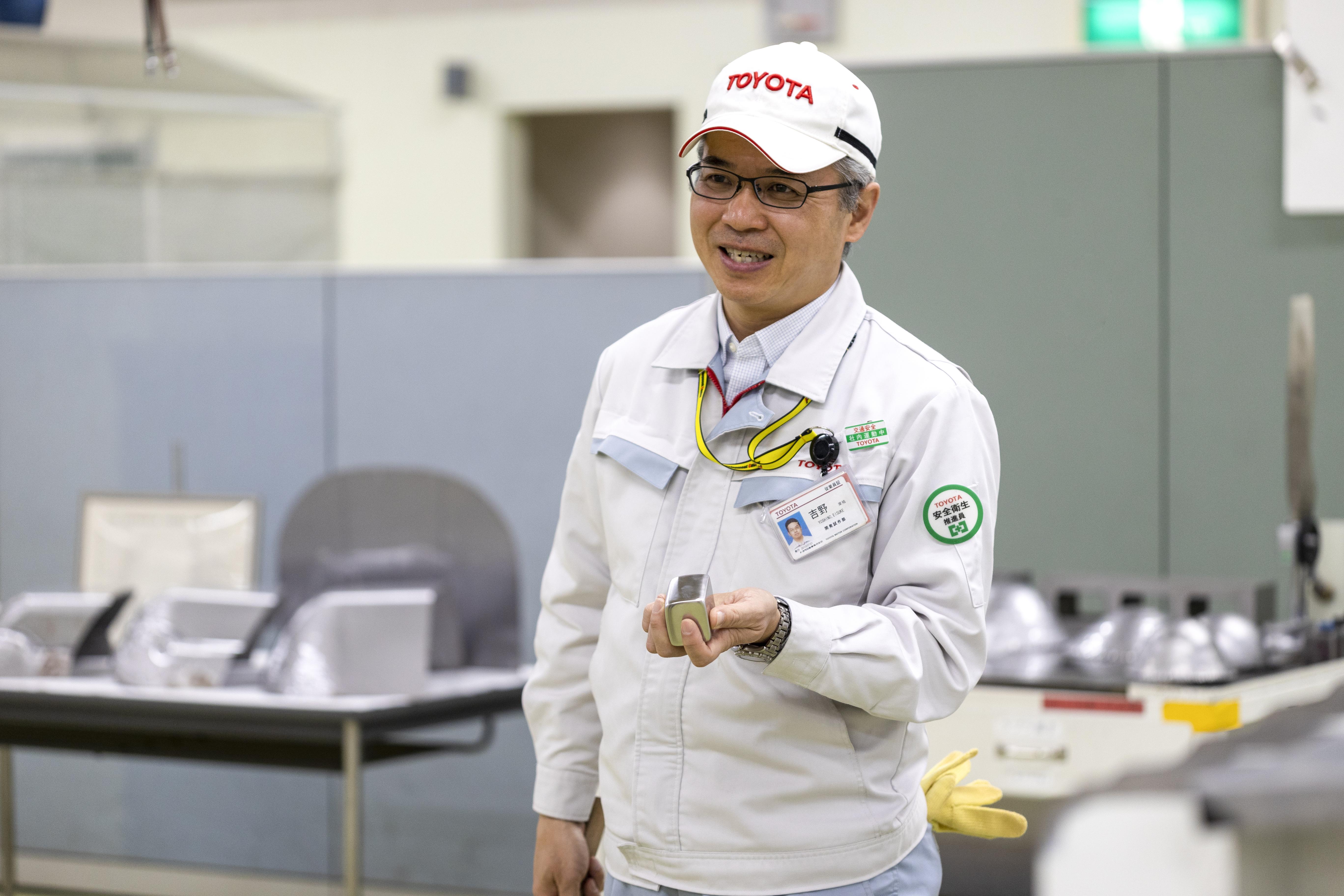
Yoshino’s tools, including metal hammers, wooden hammers and backing plates are all handmade by himself. They were spotless regardless of their heavy use. The shine of the metal hammer was particularly surprising. He chooses the materials himself, hands it over to someone else for process and finally completes it himself.
All sheet metal craftspeople working in this department have their own tools. The material of the tool must match the material one is working with, but knowing what material to use is equally important as the sheet-metal craftsperson. Each craftsperson is especially particular about the material of their hammers. Yoshino makes and uses a resin material called Bakelite in addition to wood. This is the knowledge that he inherited from a master of sheet-metal, who was a world champion in the WorldSkills Competition.
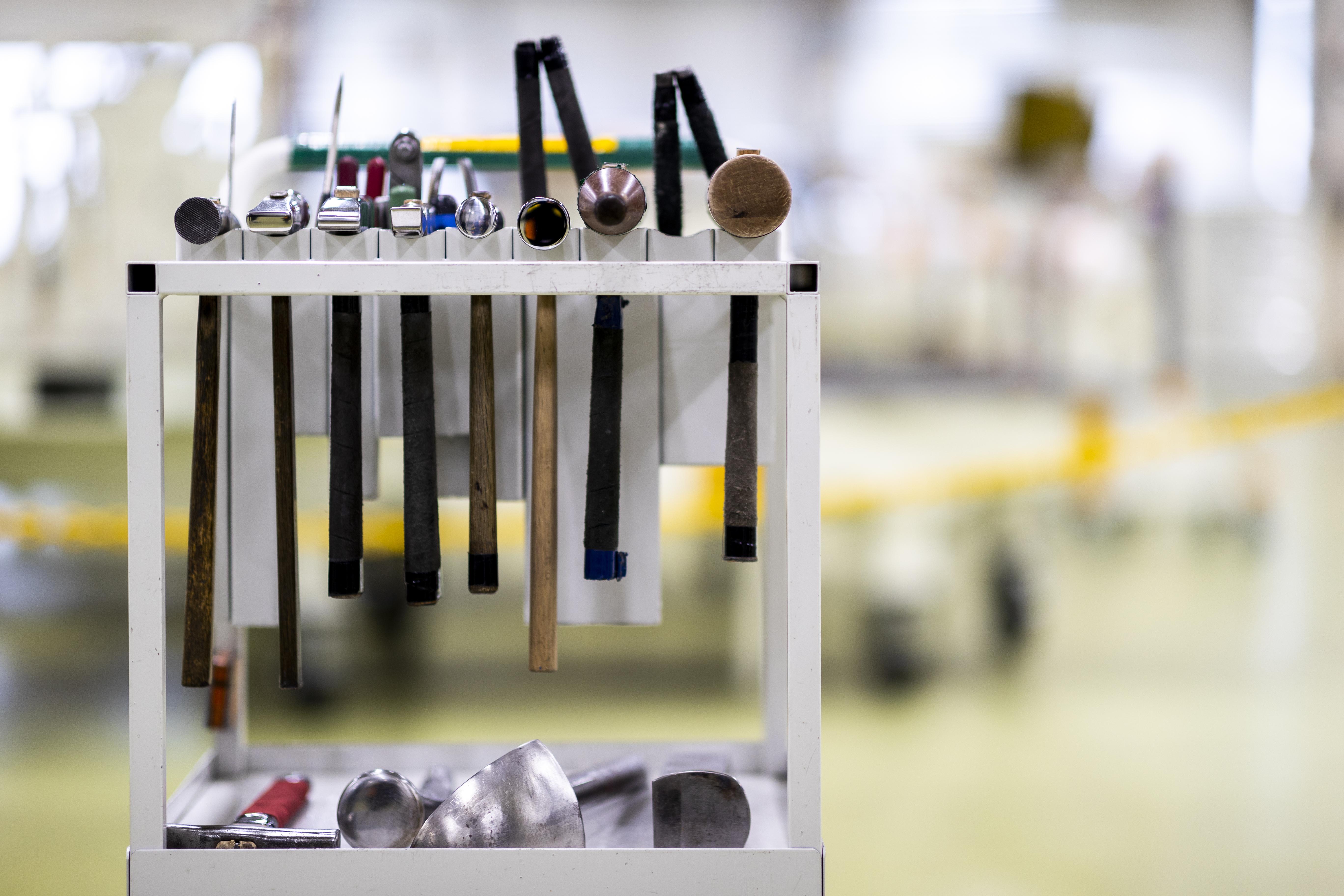
“I can immediately tell the skill of the sheet-metal craftsperson just by looking at their tools, especially when I see their worn-out hammer, which is the most important tool in sheet-metal work. If the tools are well maintained, this craftsperson is definitely skilled.”

As Yoshino pounds the steel plate with a wooden hammer on a metal surface plate or a wooden platform, the flat material gradually turns into a three-dimensional object. The rhythm of the hammer creates a steady pulse. The sound he makes with the metal or wooden hammer mimics a Buddhist chant.
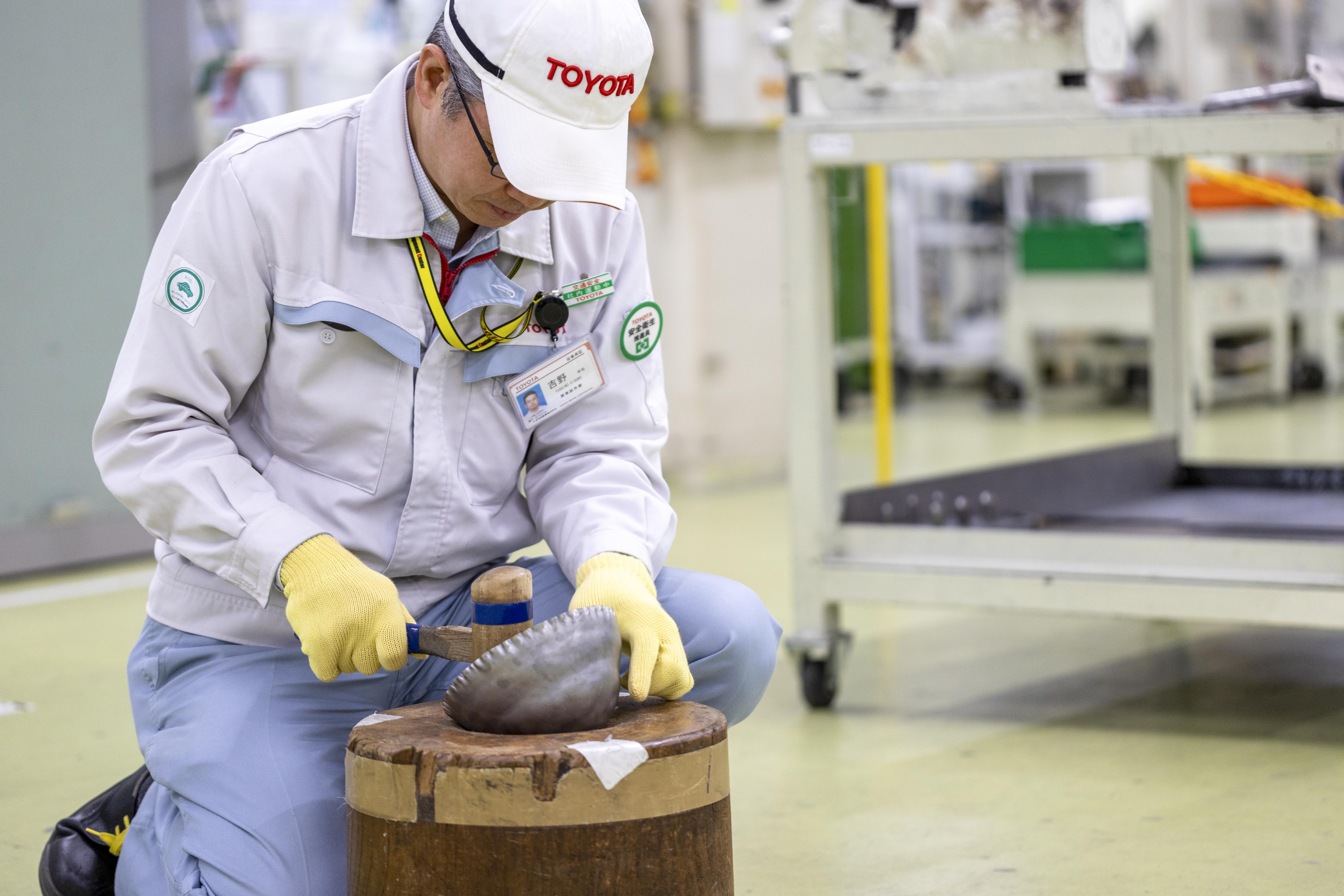
On his offer, the interviewer from the Toyota Times editorial team tried hitting the flat steel plate laid on a surface with Yoshino’s hammer. It wasn’t for creating any shapes, just for hitting the plate with the hammer. However, even though the exact same hammer was used to hit the steel plate, it didn't make the clear high pitched resonant sound that Yoshino made. Instead, it sounded low and dull.
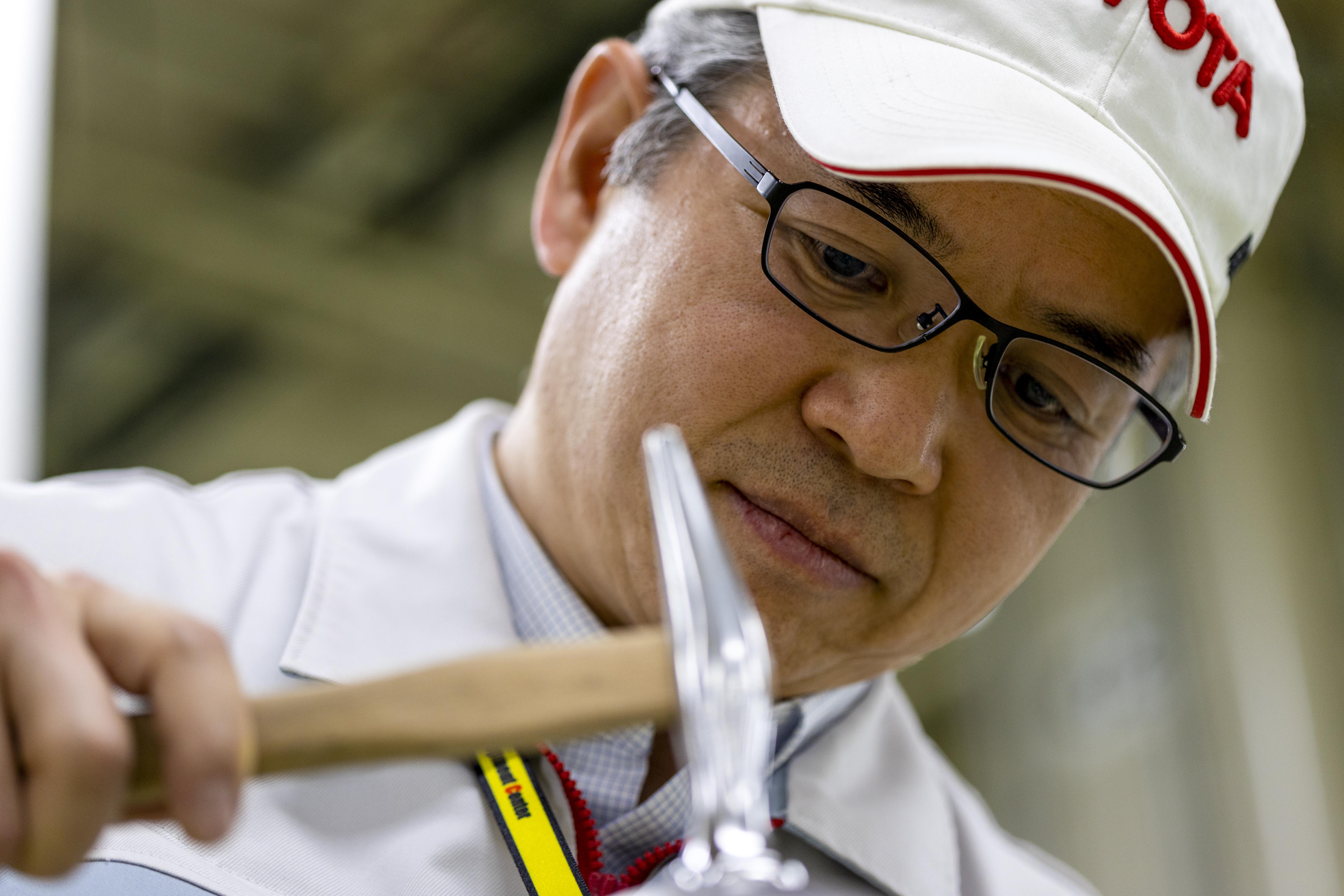
“The dull sound is due to the force of the hammer not successfully transferring to the steel plate, because there is a gap between it and the surface. The clear resonant sound proves that the steel plate is flush against the surface, and the force of the hammer is indeed transferring to the steel plate. Once you understand the hammer’s center of gravity and learn how to wield it correctly, the hammer will steadily bounce back, and you'll be able to use it with precision and ease.”
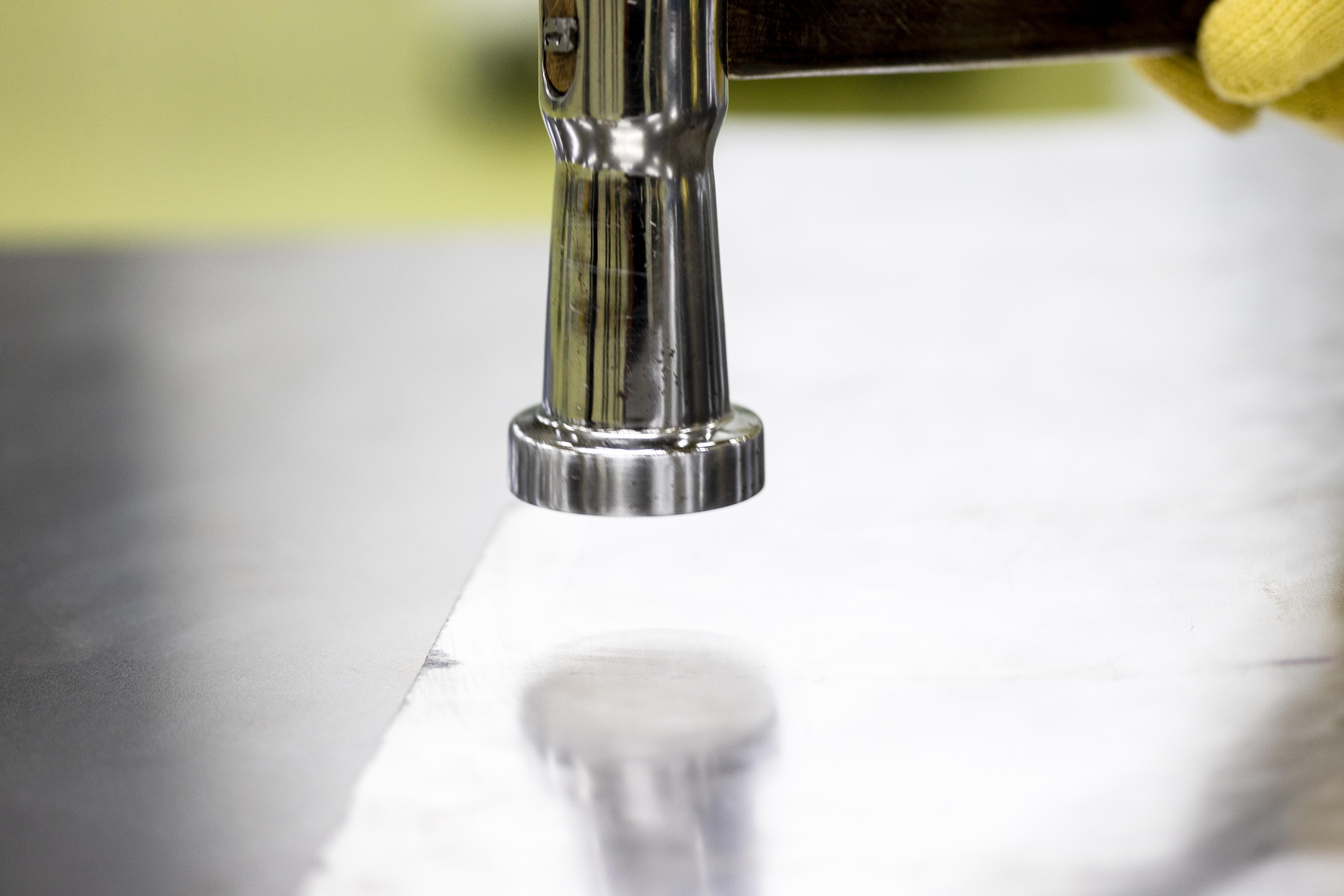
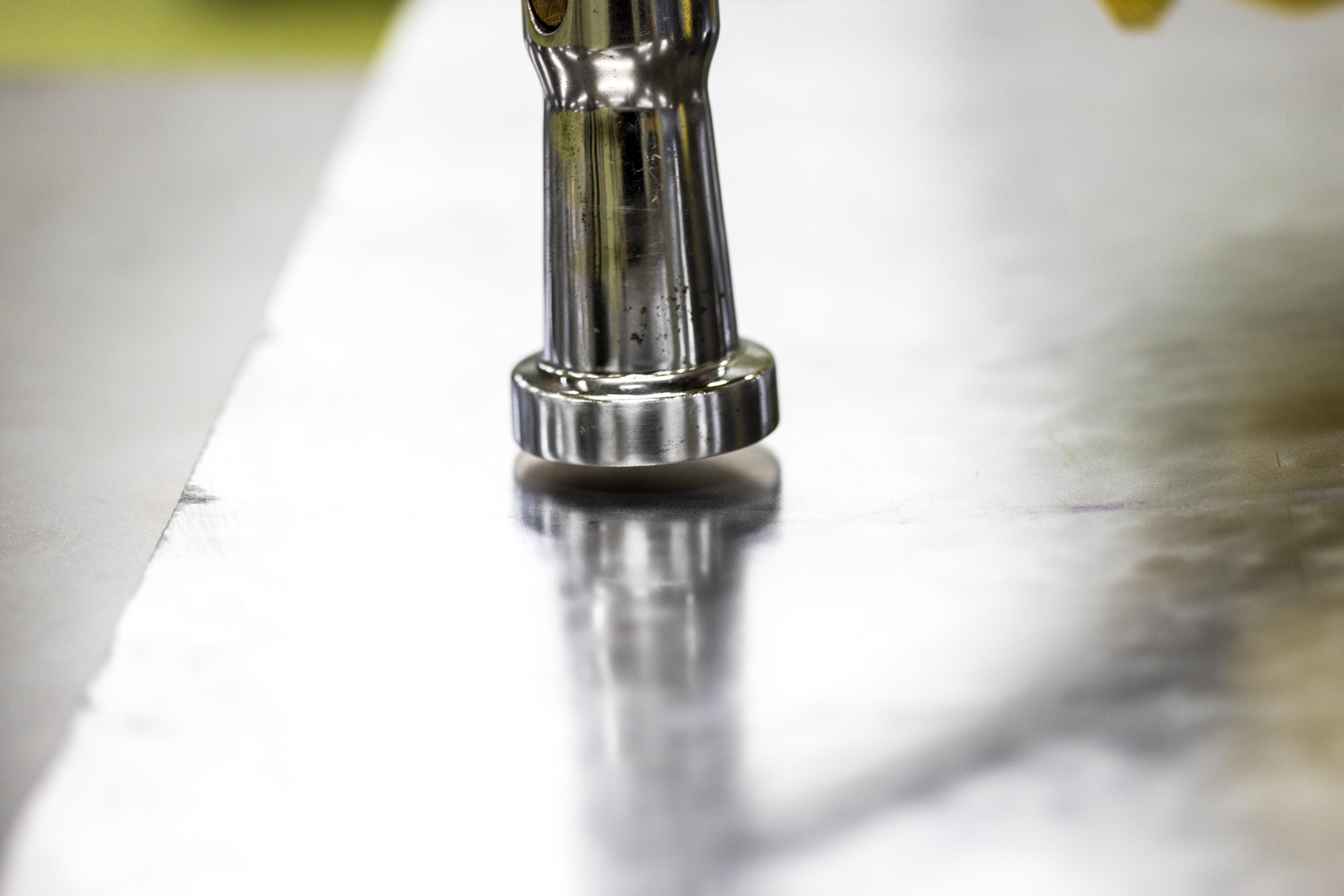
Moving his hands while sharpening his instincts and listening to the sound-this is beyond logic. It is a world of intuition and feel that solely relies on instincts. With these instincts, he is able to create car bodies from design data within a margin of error of 0.5mm.
“Can the skills of sheet-metal working be quantified for the purpose of passing them on to future generations? This has long been debated, but honestly, I don't think it is quantifiable as of yet. Right now, I can only teach these skills to my juniors through trial and error and having them obtain the necessary instincts, but perhaps it will become more quantifiable as digitalization and AI become advanced,” Yoshino said.
Passing the defining skills of sheet-metal working to future generations
Similar to traditional craft, it is extremely difficult to pass on defining skills that rely on instinct. However, passing on these defining skills is absolutely necessary in car-making.
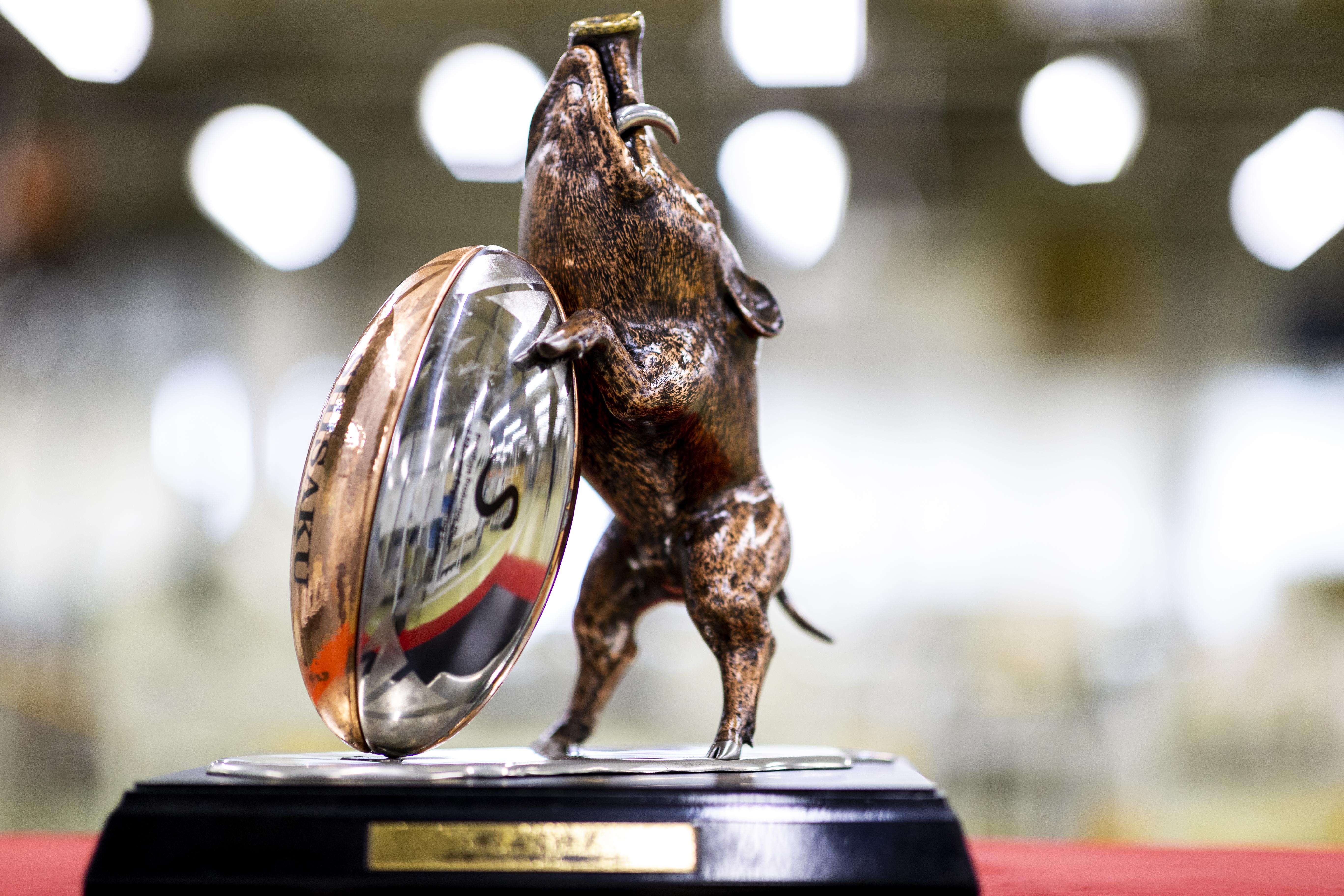
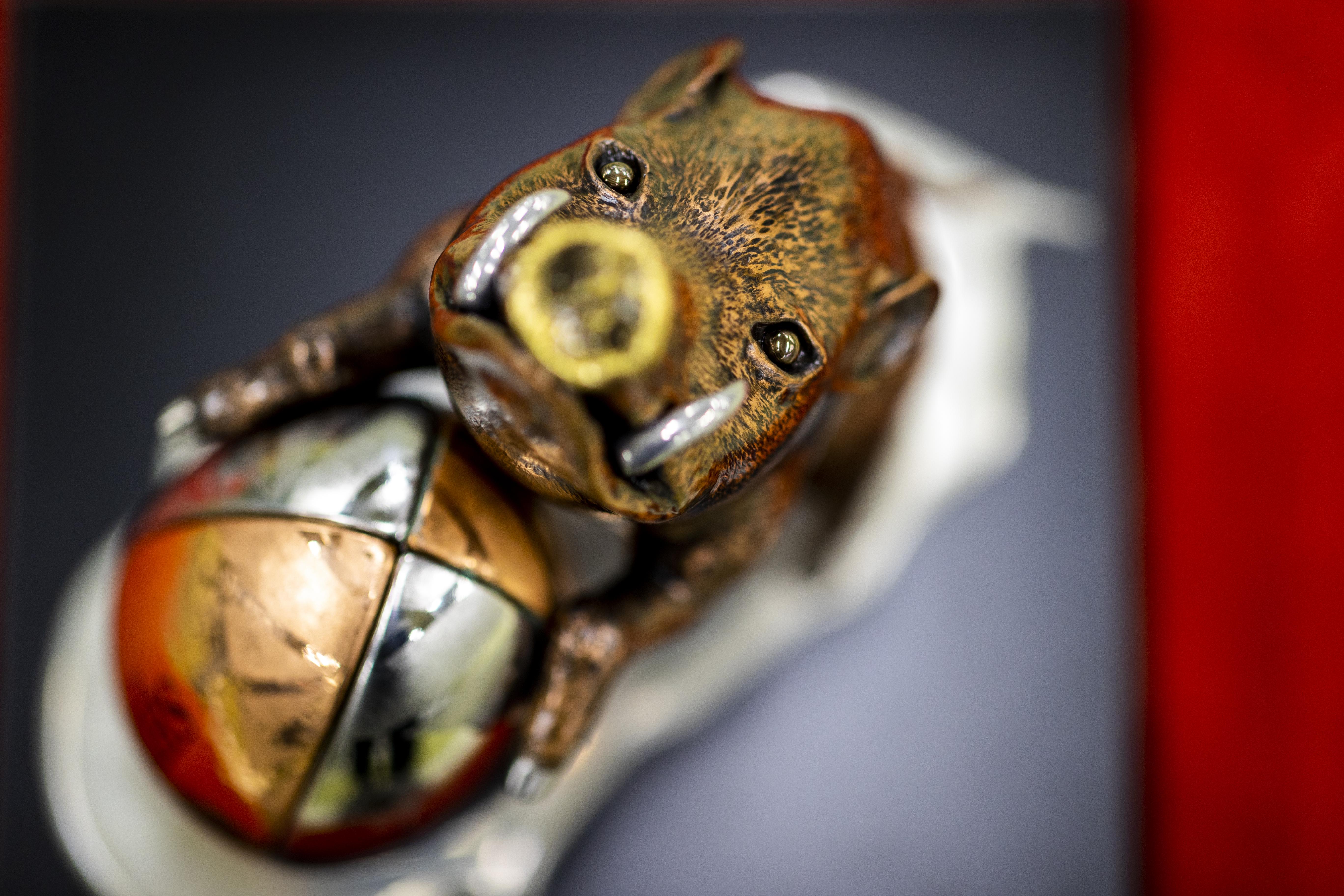
“I can create any shape with my hands and a hammer. This is what attracts me to sheet-metal working,” says Yoshino, who never compromises when it comes to his own personal growth on top of educating and passing on skills to his juniors. He continues to try new things and train for the future by working with designers to turn a sketch into a three-dimensional metal object, or welding challenging materials such as titanium.
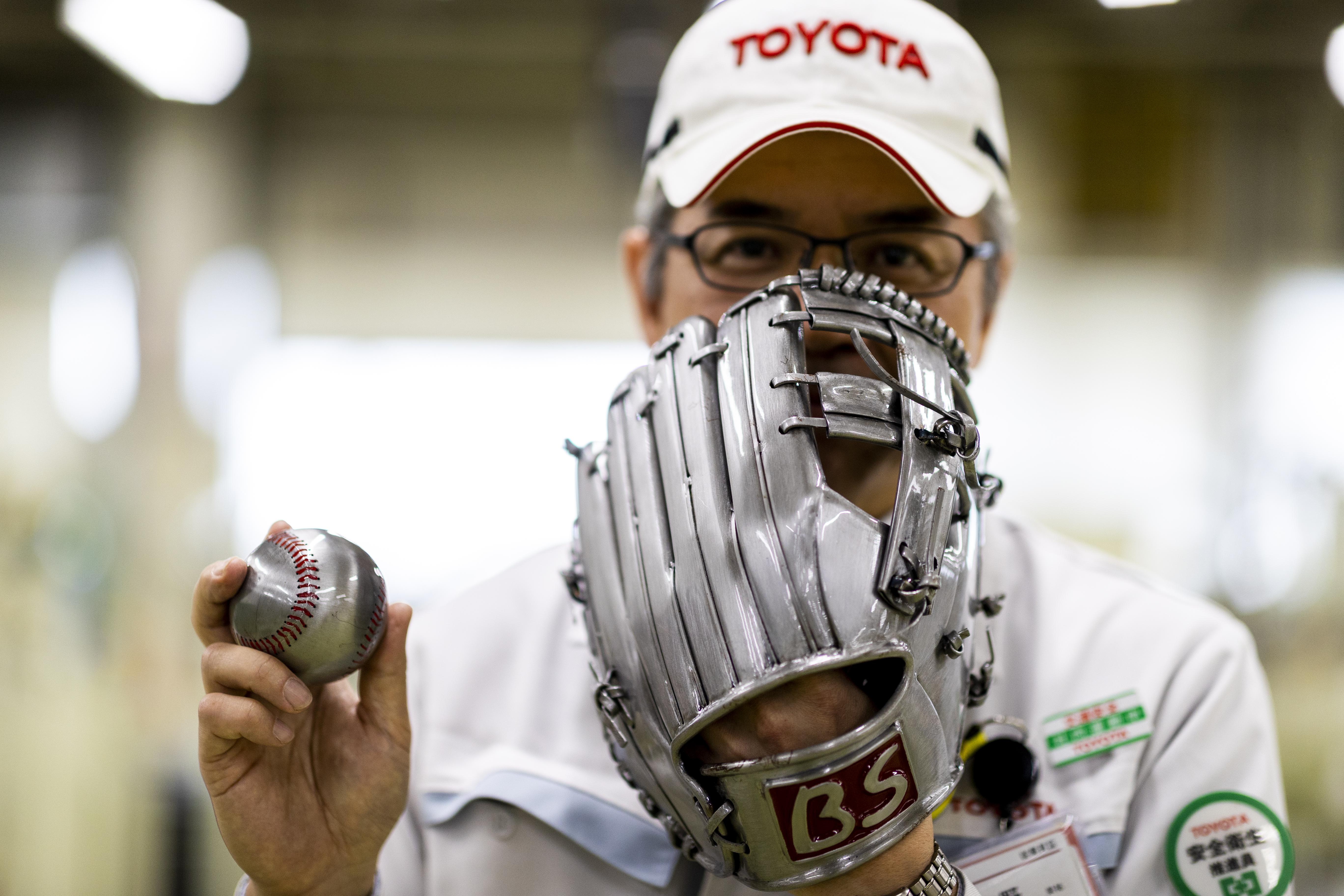
“There has been an uptick in plates made of materials that are difficult or impossible to process by hand, such as high tensile steel. Also, in the manufacture of press molds and jigs, the design data of 3D software has made it possible to make things faster than in the past, for example by eliminating paper drawings”.
That said, the traditional skills for processing steel-plates by hand are still essential for making cars, and must be passed on. Nevertheless, it takes a long time, over 10 years, to master these skills. How can we acquire these skills more efficiently and faster? I’d like to keep that in mind while passing these defining skills on.
Master sheet-metal welder Eisuke Yoshino, who creates something from nothing. His challenges continue.
(Text: Yasuhito Shibuya, photo: Akira Maeda)