
Toyota Times uncovers the essence and core strength of the traditional Japanese monozukuri (making things), which is woven from the past into the future. The sixth interviewee is a master of painting.

While many people focus on advanced technologies such as 3D printing or AI when thinking about innovation, much of the work involved in car manufacturing is still done manually.
In this series, by interviewing some of the masters supporting Toyota’s manufacturing with their craftsmanship, Toyota Times uncovers the essence and core strength of the traditional Japanese monozukuri (making things).
The sixth interviewee is Keishi Miyachi, a master of painting.

Series #6 Master Painter Keishi Miyachi develops painting that protects cars, while giving them aesthetic value
Keishi Miyachi, Senior Expert, Coating Equipment Certification Section, Surface Finishing & Plastics Production Engineering Division, Vehicle Production Engineering Field, Production Group at Toyota Motor Corporation
Paint coating that protects and keeps car bodies beautiful
Paint protects cars against scratches, rust and other damage, and helps car bodies last longer by blocking dust, dirt and moisture in the air. It also suppresses the noise of a moving car, promoting a quiet interior. More than anything else, a car’s beauty is judged by its paintwork. No matter how wonderful a car is designed or performs, if the paint color and quality are not excellent, it is impossible to create a beautiful car that attracts people.
The thickness of a car’s paint is only about 1/10 mm (100 microns), and the coating that protects the body typically requires four layers of paint.
The first coating is called the electrodeposition coating, also known as the undercoating. As the car body is made of pressed and welded steel plates, this coating is applied to prevent rust. It is called electrodeposition because electric currents cause the anti-rust paint to be absorbed into the surface. By submerging the negatively charged steel plate car body in a pool of positively charged paint, the paint is evenly and seamlessly applied to the surface of the car body through the power of electricity.

After the electrodeposition coating is completed, and the paint on the car body surface dries, a resin (sealer) coat is applied. This process fills the joints and gaps in the steel sheet with a sealer to seal the inside of the car body, preventing water or dirt from getting inside. It also suppresses the running noise of the car. Sealing is also used in the construction field around areas that often get wet, such as kitchens and bathrooms. This process is different from painting in that it only concerns a small part of the car body.
The middle coating, which acts as a base coat for the main coat, is applied on the car body after the electrodeposition coating (undercoating) and the sealer coating. Due to the nature of the paint, the surface of the electrodeposition anti-rust coating becomes noticeably uneven. The middle coating is applied to correct this nevenness and to make the color of the main coat look vibrant.
Once the middle coat is dry, two layers of top coat are applied. This is also called the main coating. The main coating consists of a base color coat, which defines the color of the car, and a clear coat that gives the surface a beautiful luster. As a high-quality paint option offered for luxury cars, a third layer is occasionally added in between the base color coating and the clear coating.
This time, we are featuring an expert in this painting process, Master Painter Keishi Miyachi.
Dedicating himself to painting for 35 years since joining the company
Keishi Miyachi, born in 1967 and currently 54 years old, joined Toyota in 1986 after graduating from high school. Since then, he has dedicated himself to painting, and built up his career for 35 years. He was internally certified as a Class A Expert Technician in the field of painting process maintenance in 2000 and was promoted to Senior Expert (SX) in 2021. All 570 people in the Surface Finishing & Plastics Production Engineering Division recognize him as the best in the field.
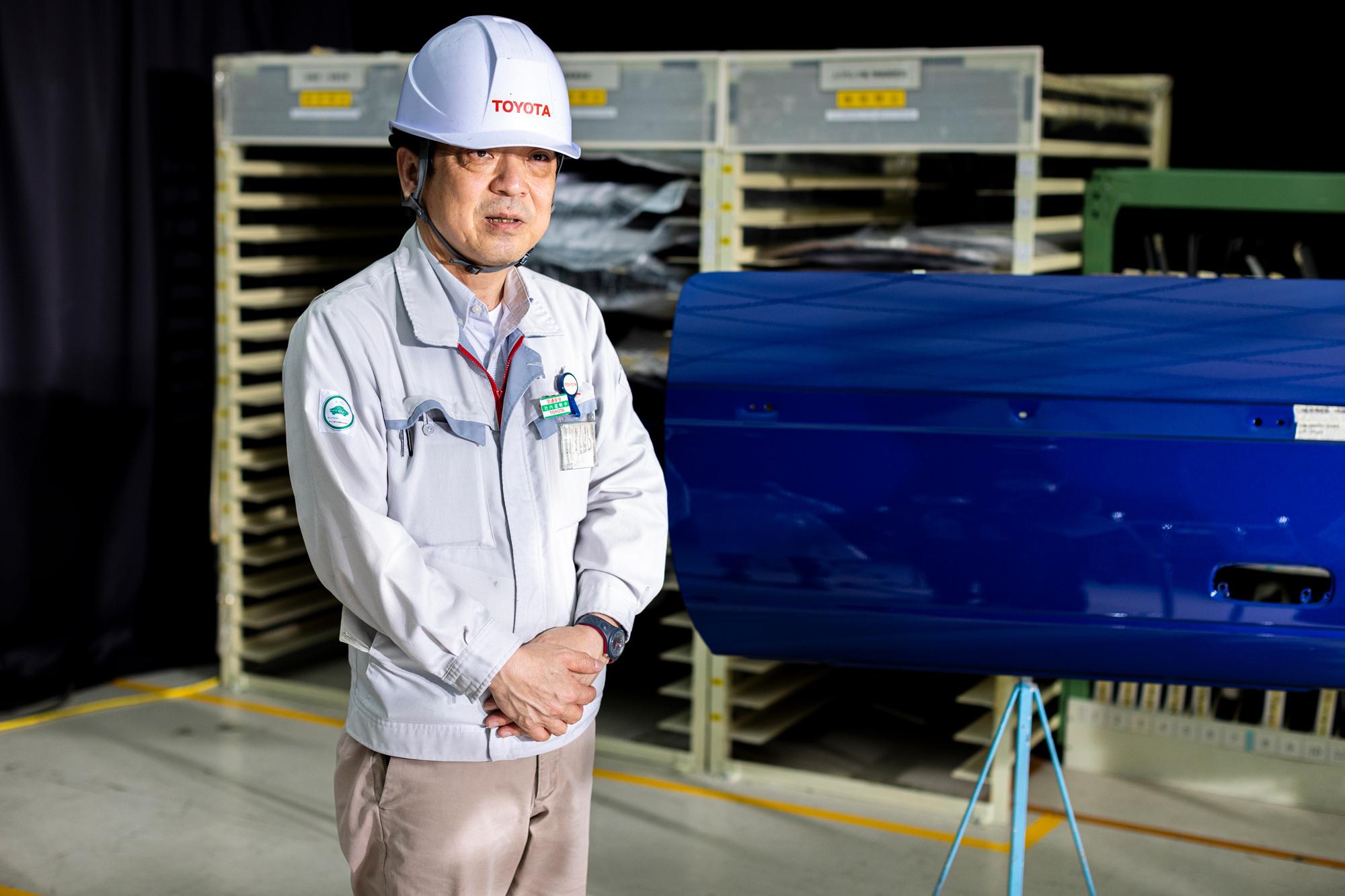
“I joined Toyota because I enjoy and like making things. I enjoyed painting plastic models since I was a child, and my interest in colors has increased even more since I joined my current workplace.”
Miyachi is also at the forefront of his field as a contributor to Toyota’s water-based car body painting. In around 2000, automobile manufacturers around the world were doing their utmost to tackle environmental issues to protect the planet.
Until then, solvent-based (oil-based) paints containing volatile organic compounds (VOCs), which are organic solvents, were used for painting cars, especially for the middle and top coats. However, VOCs cause air pollution, contributing to photochemical smog, when they are released into the atmosphere as the paint dries. In order to significantly reduce this VOC emission and prevent automobile manufacturing from polluting the air, the amount of solvent-based paint must be reduced. In other words, we need to switch to hybrid paints that contain only a small amount of organic solvent, or water-based paints that do not contain any organic solvents.
We have entered a period of profound change in terms of painting cars. Miyachi led a team to establish new technologies and amassed a great amount of knowledge about water-based paint. Today, except for a few types of clear paint, almost all paints are completely water-based.
Developing car paints while guaranteeing productivity and quality
Currently, Miyachi is in a position to guarantee the productivity and quality of the coating process of all cars including Lexus models.
The designer decides the paint colors of the cars. Miyachi’s most important job is to think about how to realize the color chosen by the designer at the production site. He decides how to mix the paints, and what painting techniques are required. Not only does he have to eliminate defective products at the production site, but he must also guarantee consistent coating quality even when cars are mass-produced at a rate of 1,000 units a day. His responsibility lies in establishing the conditions to achieve good uality and ensuring it at the production site.

“No matter how attractive a car is, it can’t be approved for production unless consistent quality is guaranteed at the production site. Also, if it’s impossible to establish the conditions for non-defective products, I ask the design department to reexamine the design.” This is also an important part of Miyachi’s job.
Miyachi’s department also evaluates the repairability of the paint to check if it maintains its original color if and when the car is scratched and in need of repair.
Cars with certain colors will only be produced if Master Painter Miyachi approves them in terms of quality, productivity and repairability.
“My job at the painting shop site is to make more attractive cars with even better colors while utilizing the technology, knowledge and my experience up until now. I want drivers to feel happier with the colors of the cars. I think about that all day at work.”
It is also up to 54-year old Miyachi to train the next master of painting, who will be his successor.
Exquisite painting techniques that give birth to beautiful colors/automobiles
Miyachi is a craftsman of few words. His brilliant skills as a master of painting are recognized by everyone in the painting shop.
With hand-blown painting, even if the exact same paint is used, the color of the paint will change slightly if the thickness of the base color film differs by a mere 3/1000 mm (3 microns). The same can be said for the clear coating. The glossiness and the feel of the paint will change completely if the film thickness differs by only 5/1000 mm. Miyachi’s delicate senses can distinguish such minute differences.
Paint refinishing requires a sensitivity to detect the subtle differences in hue (shades or tones of colors), and judge whether it is going in the right direction or not. He is able to mix paint one gram at a time to reach the desired color, and skillfully operate the spray gun to achieve the ideal paintwork.
Miyachi’s skill is one of a kind when it comes to hand-blown painting and paint refinishing.
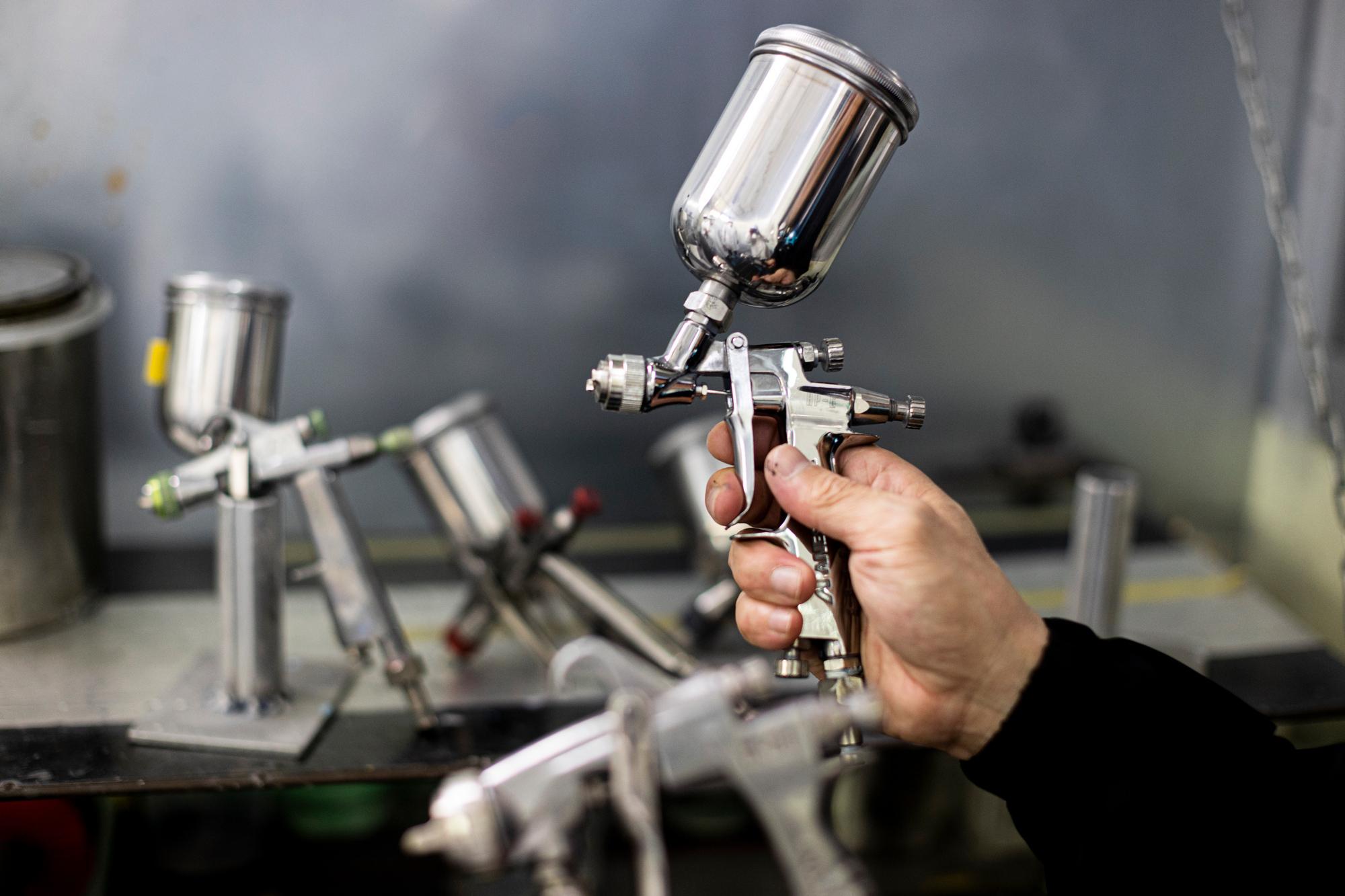
People may wonder why hand-blown techniques are necessary, now that the painting process is mostly automated.
In the old days, car body painting on the production line was done manually with a hand-blown spray paint gun. However, automation has been promoted for decades in order to improve coating efficiency, quality and reliability, and to carry out work safely and quickly. Nowadays, most of the painting of production vehicles is automated, meaning industrial robots are used for painting.

Toyota has also been actively working on automating painting processes for over 50 years. In 1994, an arm shaped painting robot was introduced with the capability to paint any part with consistency, while following the car body on the conveyor belt.
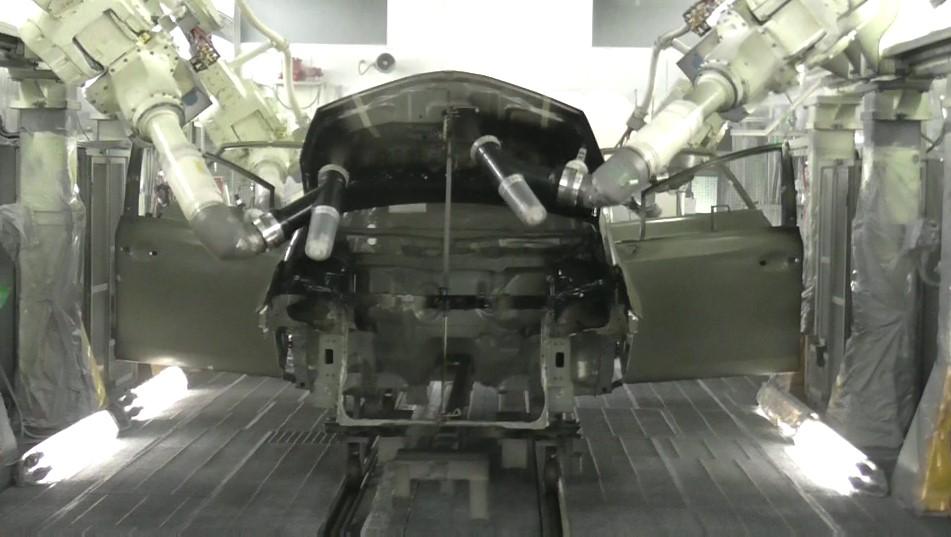
Both robots and painting technology have evolved dramatically compared to the past. The level of painting speed and efficiency is profound. For example, in the past, only 25 percent of the paint was successfully applied to the car body. In other words, 3/4 of the paint was wasted. However, the current success rate is up to 95 percent with the help of the latest technology, construction methods and equipment. Meaning that less than 5 percent of paint is wasted.
While hand-blown painting is still done for a small portion of luxury cars, recent painting lines utilize new robots with a “bell painting device”, developed in-house by Toyota, attached to their tips. As the robot skillfully moves its arms, the body flowing along the line is painted efficiently, beautifully and at great speed.
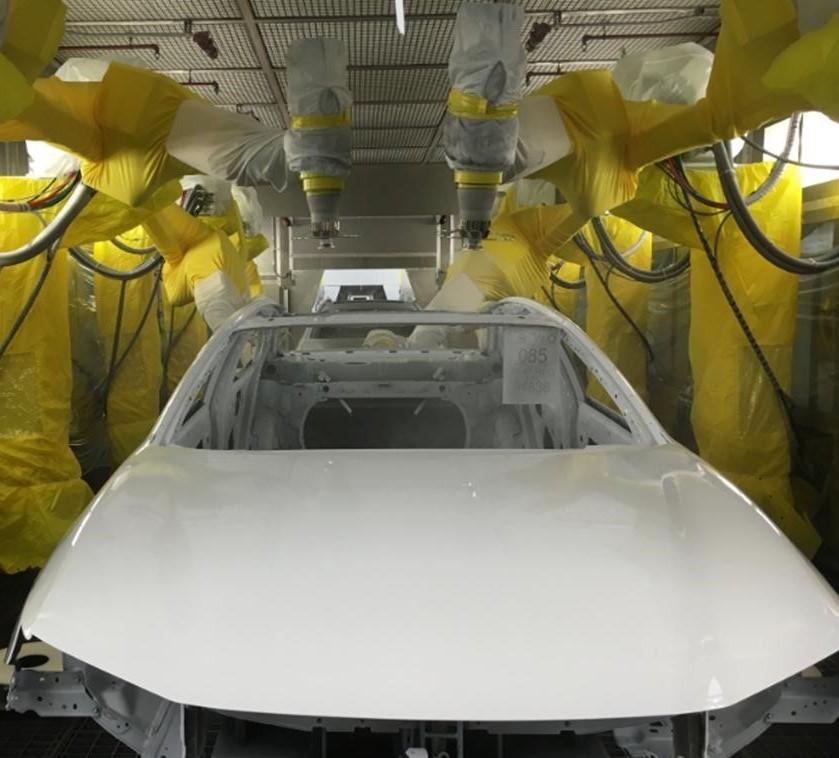

However, it is Miyachi and his team who teach the robot how to paint. The robot is just accurately mimicking the hand-blown painting techniques of a skilled human operating the spray gun along the shape of the car body.
“The method of painting varies depending on the type of paint. If we aren’t careful about changing methods to suit the type of paint, the paintwork will be uneven or show visible drips. Complicated car body shapes make the job even harder. If a person can't do the job well, neither can a robot.”
A delicate color palette and extraordinary spray gun painting skills
How high are Toyota’s standards for car painting? Also, as the one who realizes and manages the quality of painting, how delicate is a master of painting like Miyachi's sense of color?
The Surface Finishing & Plastics Production Engineering Division has a dedicated booth equipped with lighting that mimics sunlight to realistically evaluate the color of the paint. For this interview, they prepared an example. One door panel was painted with the latest paint and technology, while another had scratches that were manually painted over.

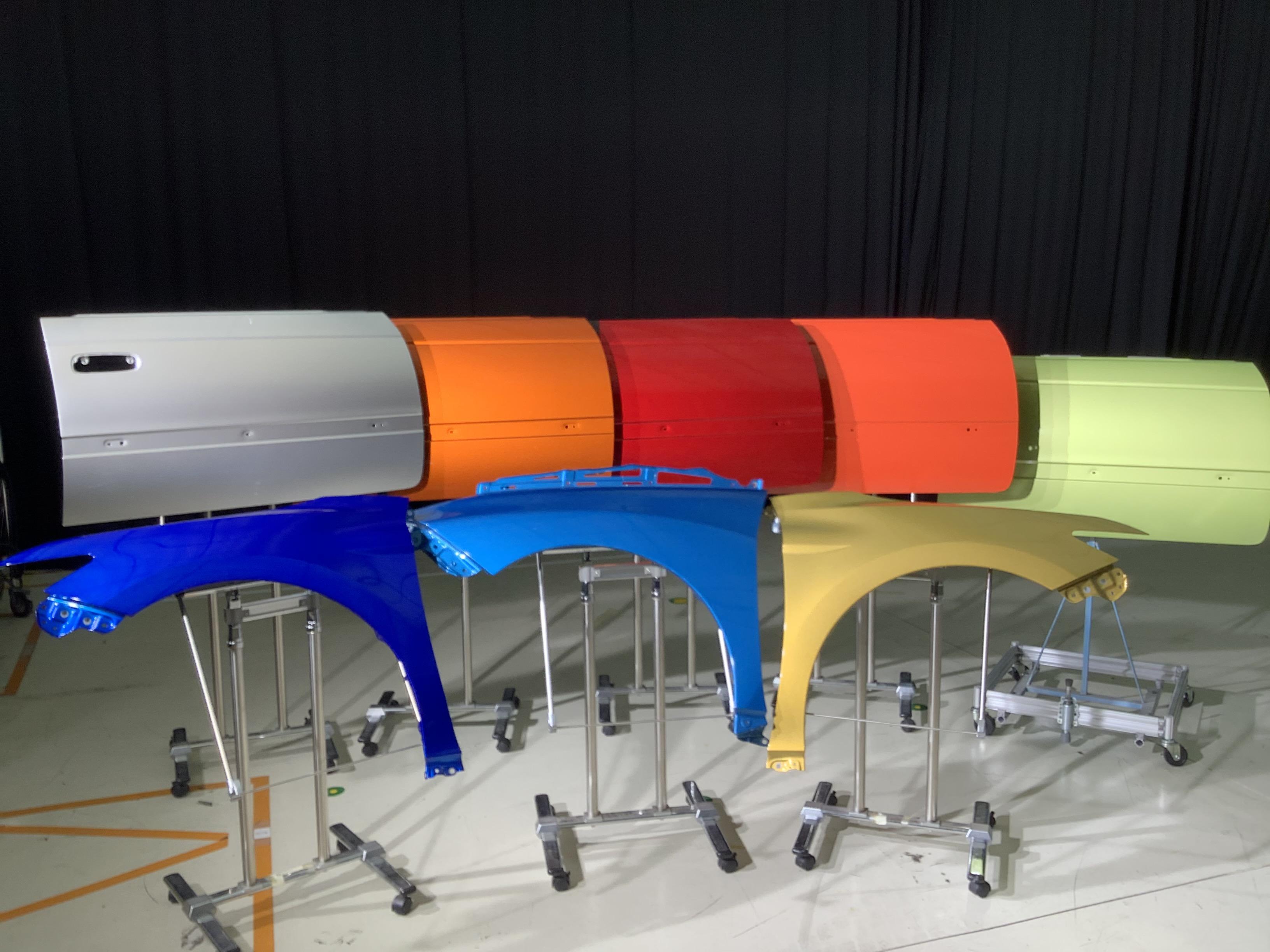
The latest high-quality painted door panels were placed side by side with the ones with standard paintwork. The beauty, vivid colors and deep luster were impressive, but what was even more surprising was how perfectly Miyachi had repaired the door panel by hand.

Miyachi explained the difference between a successful and an unsuccessful repair. However, to ordinary people who cannot tell the difference, both look brand new. It was difficult to find any sign of the repairs until Miyachi pointed them out.
In fact, Miyachi and his team at the Coating Equipment Certification Section have the ability to detect subtle color differences. It is impossible to work at the Coating Equipment Certification Section without these skills. Miyachi agrees that unless you are born with the ability to detect subtle hues, no amount of training can help.
Then, how sensitive are Miyachi and his apprentices to color differences? There was a test to check their ability to sort cylindrical blocks, each painted in different colors from light purple to green, in the order of gradation.
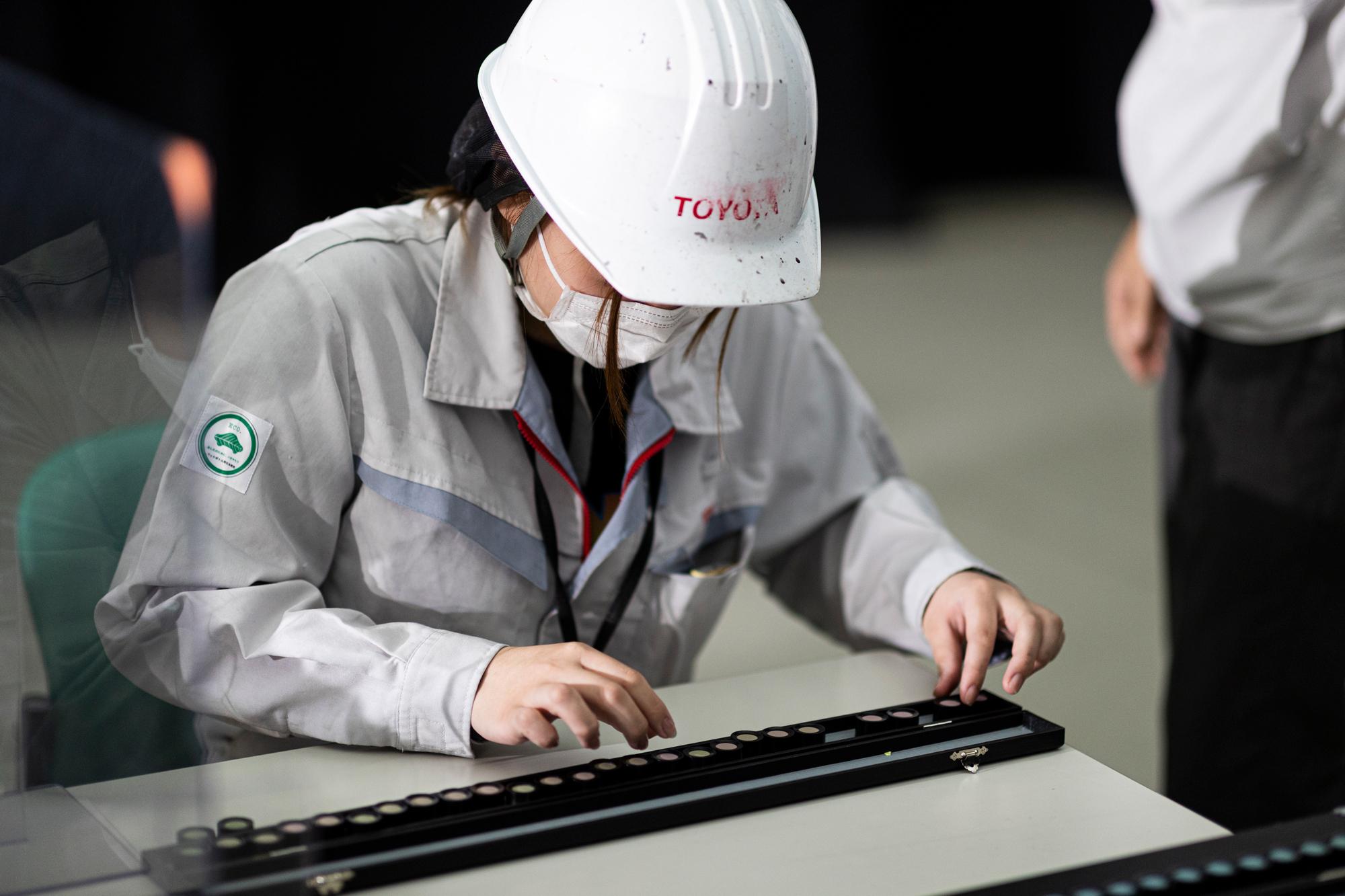
Sorting needs to be done in two minutes. The color differences are too subtle to detect and determine to the untrained eye, but the staff who have been working under Miyachi for about four years, quickly rearranged them perfectly.
They can tell the subtle differences in the hues. Even though the colors look the same to an ordinary person, they see them as totally different colors. This experiment made it clear that each person’s sense of color is very different.
Next, in a paint refinishing booth, Miyachi demonstrated how the paint refinishing on the door panel is done.
For the paint refinishing, first they scrape off a thin layer of paint around the scratched surface. This process is called sharpening. Then, paints and additives are mixed one gram at a time to carefully create the paint used for the refinishing. In the case of metallic paint, fine aluminum powder is added to the paint to reproduce the shine.
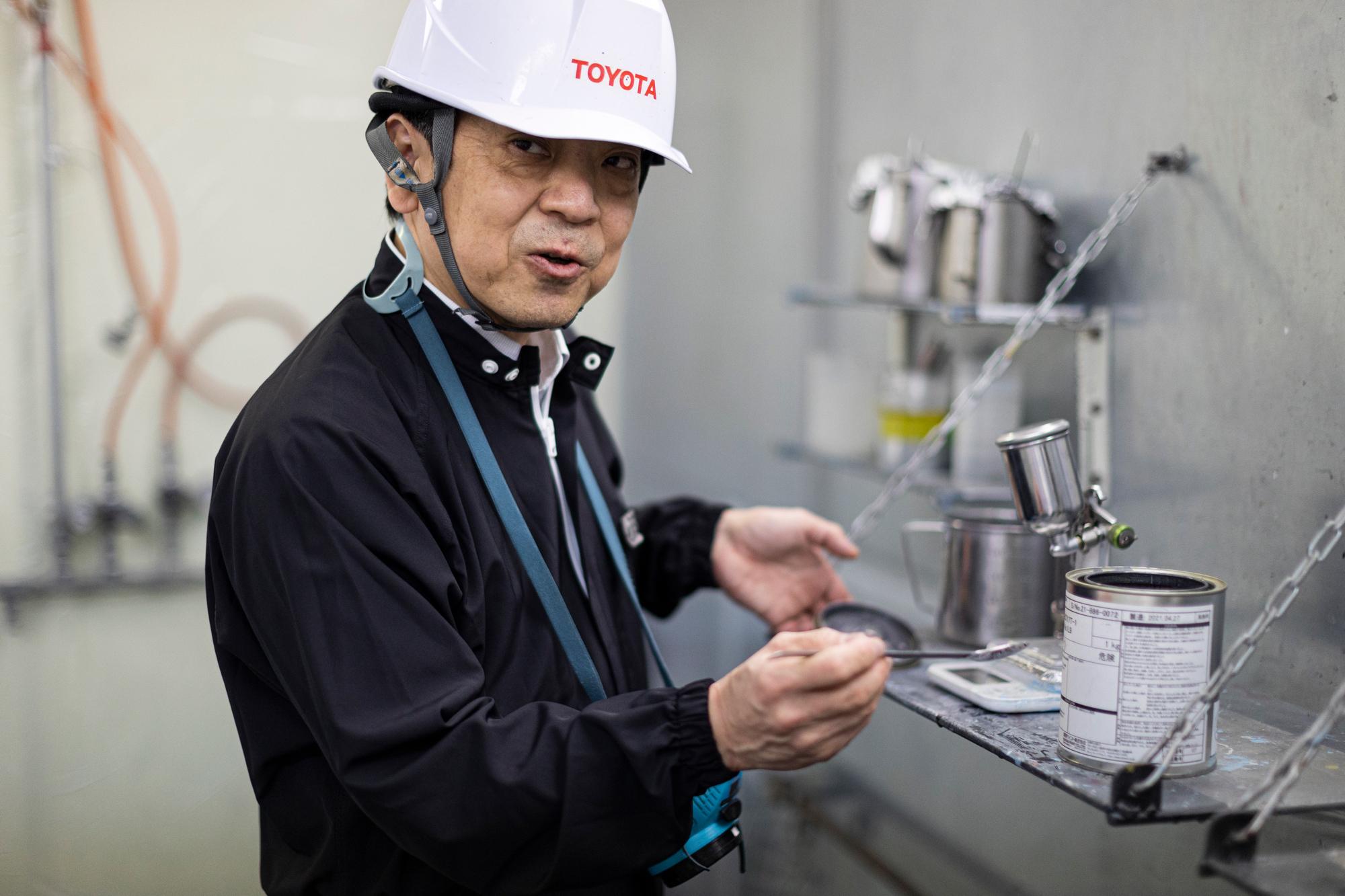
What colors and additives should be mixed together to create the desired paint? This is when Miyachi’s extensive experience shines. He fills his spray gun with the paint for the refinishing, and manually spray paints the sharpened part.
“The original paint is not the same as the spray paint mix used for repair. Regardless of that, we still try to match the color of the paint to make it look seamless, and make sure the repair is undetectable. This is the biggest challenge in the paint refinishing process. We do our best to cover up the flaws.”
The finish significantly changes depending on the size of paint particles, amount of air pressure, discharge rate, distance from the panel and speed of the spray gun movement.
If the paint particles are too big or small, they will not blend with the original paintwork. If the discharge rate is too high, the paint will drip, and if the distance between the spray gun and its target is not perfect, the paint will not create a mist. Additionally, the application speed also greatly affects the final product. It is a world that relies on sense, intuition and experience.
During the paint refinishing, Miyachi wields the spray gun with his entire body. He changes the direction of the spray paint from upwards to downwards, and vice versa. This is to straighten out the aluminum particles in the paint. Miyachi is able to manipulate the paint at a particle level.


After being internally certified as Class A Expert Technician in the field of painting process maintenance, Miyachi mastered this paint refinishing technique over the course of 10 years under the guidance of his predecessor and mentor, Senior Expert Takeo Kumagai.
“Paint refinishing is a lot more difficult than normal painting. Light colors, especially achromatic colors, are tough. I was often called out by my mentor, Mr. Kumagai. I had to think of what to do and find a solution on my own.”
What combination and ratio of paints and additives should be used during the paint refinishing at production sites or car dealers? It is also Miyachi’s job to change the recipes for the paint used in refinishing depending on car color.
Cars with even better colors that make riders happy
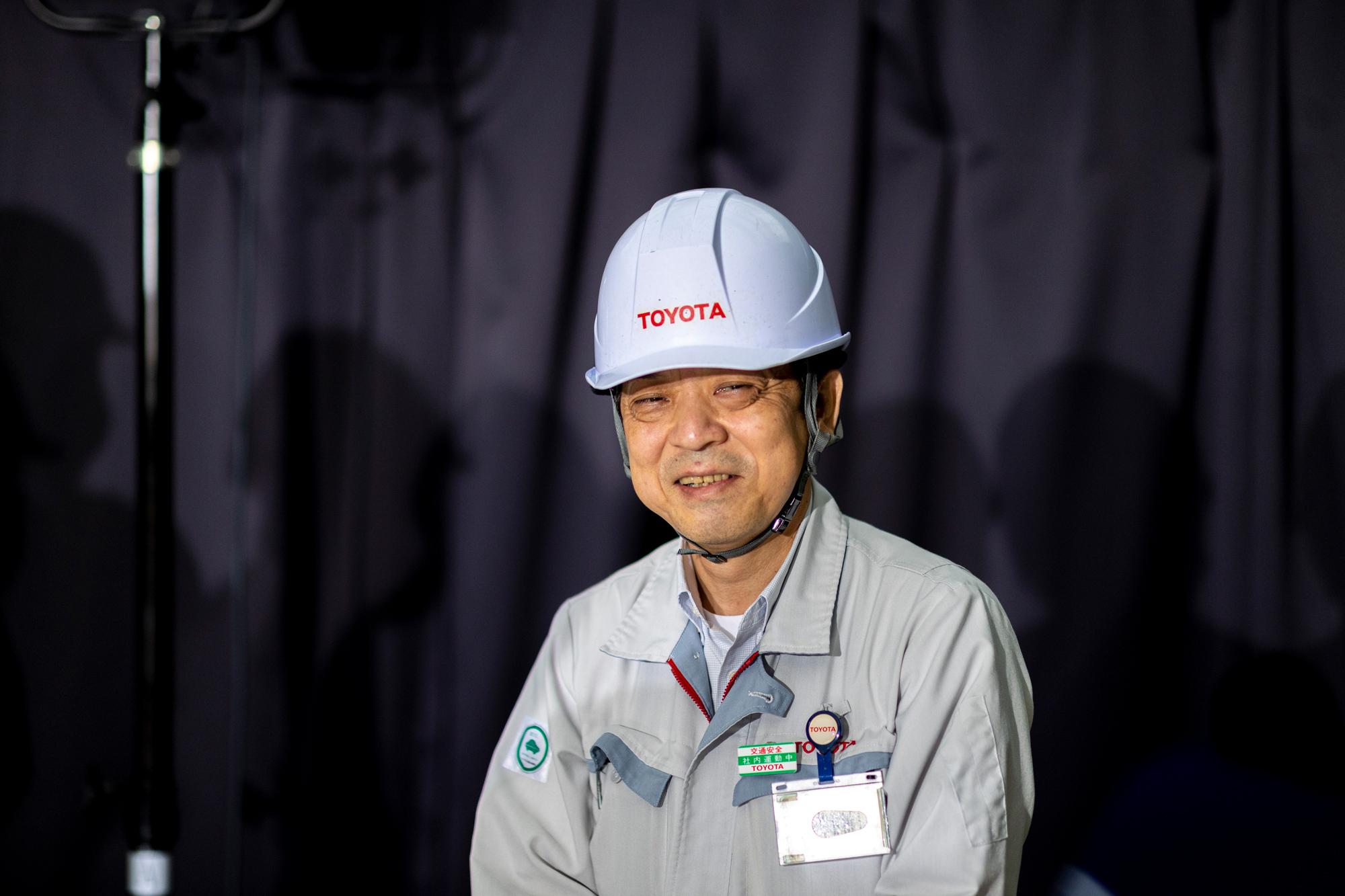
Toyota’s painting master, Keishi Miyachi, has exquisite taste in colors and an incredible skill set for painting. When he sees cars running in the city, he can’t help but notice the color of the cars. It also makes him proud to see his paintwork out in the world.
At the production site, Miyachi is now also working on developing ultra-luxury paintwork, a grade above luxury paintwork.
“Recently, there has been an increase in the number of customers who want to pay more for a car with even better color. Other companies are also creating more incredible colors. I want to find a way to still be the best, and create even better, more beautiful colors. I want to produce cars with great colors that make the people who see or ride in them happy.
One of the ultra-luxury paintwork Miyachi created, after the major hit color Red Mica for Lexus models, is Radiant Red for the Lexus LC. The red color profile changes depending on the light and angle, accentuating the elegant coupe body.
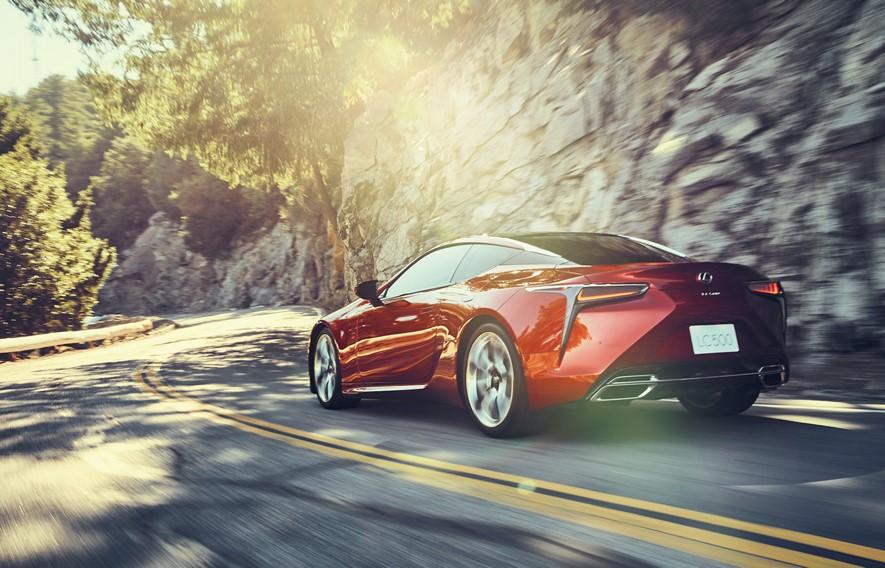
The ultra-luxury paint color Force Blue developed for the new FCEV Mirai is also the work of Miyachi and his team. The deep exquisite shine in the blue is nothing like anything seen before. This is done by two base color coatings with a clear layer in between. It is an example of an elaborate coating structure that allows light to shine through the outer base color while the inner layer reflects the light to create depth. Four additional layers of paint after the middle coating are required for this effect.
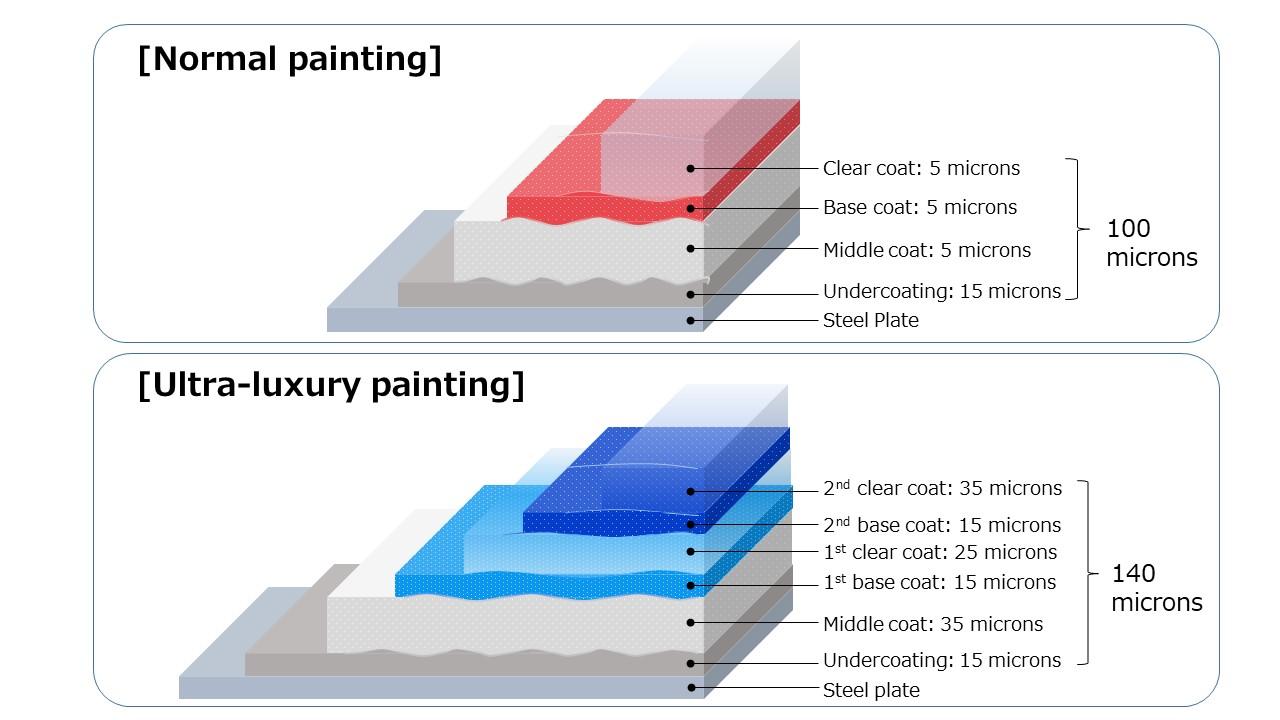

Moreover, Gin-e iLuster, one of the color options for the Lexus flagship sedan LS, uses a new sonic method to coat a high-density vapor-deposited aluminum onto the surface of the paint to create a deep shine. This is also one of the ultra-luxury paint colors that Miyachi and his team created.
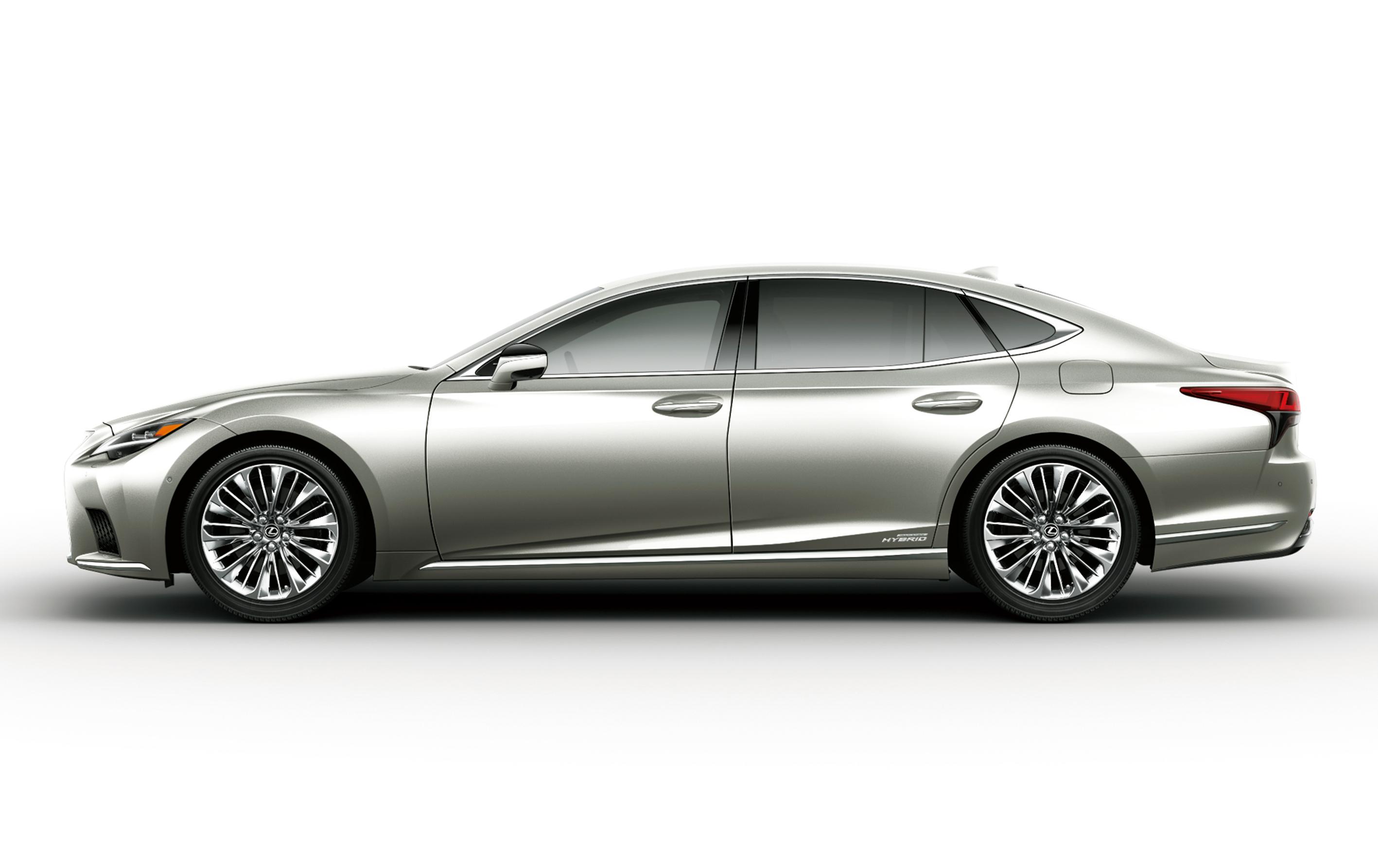
Educating future painting masters
Master Painter Keishi Miyachi is absolutely committed to the serious task of finding his successor.
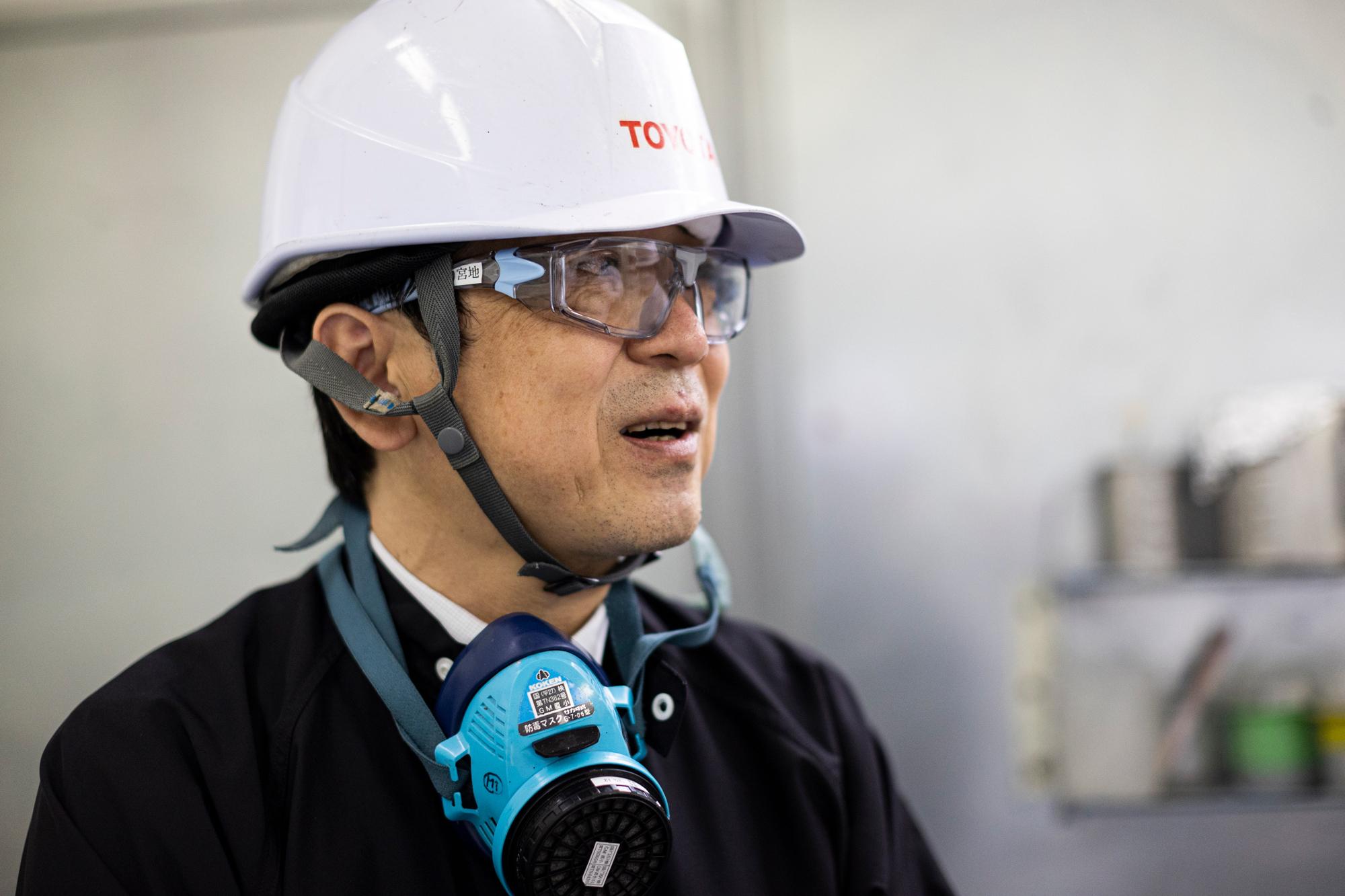
“Most paintwork is automated nowadays, so there aren’t that many opportunities to hand-blow spray paint with a gun in hand. I try to find ways to create opportunities to get junior employees excited about painting. That way, I can convey the joy of painting to them.”
Through various social contribution activities, such as the production of the in-house Declaration of Health Monument, work presented in the children’s ride design exhibition and the cars offered for the Olympic and Paralympic Games Tokyo 2020, Miyachi and his colleagues in the Coating Equipment Certification Section create opportunities for junior employees to experience hand-blown painting.

“I want them to understand the importance of hand-blown painting technique and its principles through experience. However, not everyone can obtain this skill set even if they try hard. Therefore, I can’t just simply push my agenda. I have to respect that person’s sense and personality, and patiently pass on the skills over time.”

Now, Master Painter Keishi Miyachi is hard at work developing even more beautiful paintwork and training the next generation in the painting booth. His challenges continue.
(Text: Yasuhito Shibuya, photo: Akira Maeda)