
Toyota Times uncovers the essence and core strength of the traditional Japanese monozukuri, which is woven from the past into the future. The second interviewee is a master of casting captivated by the casting technology.

While many people pay attention to advanced technologies such as 3D printers and AI when it comes to making something new, there is a lot of handmade work remaining in the front lines of car manufacturing.
In this series, by interviewing some of the masters supporting Toyota’s manufacturing with their craftsmanship, Toyota Times uncovers the essence and core strength of traditional Japanese monozukuri (making things).
The second interviewee is Kiyohide Motoki, a master of casting.
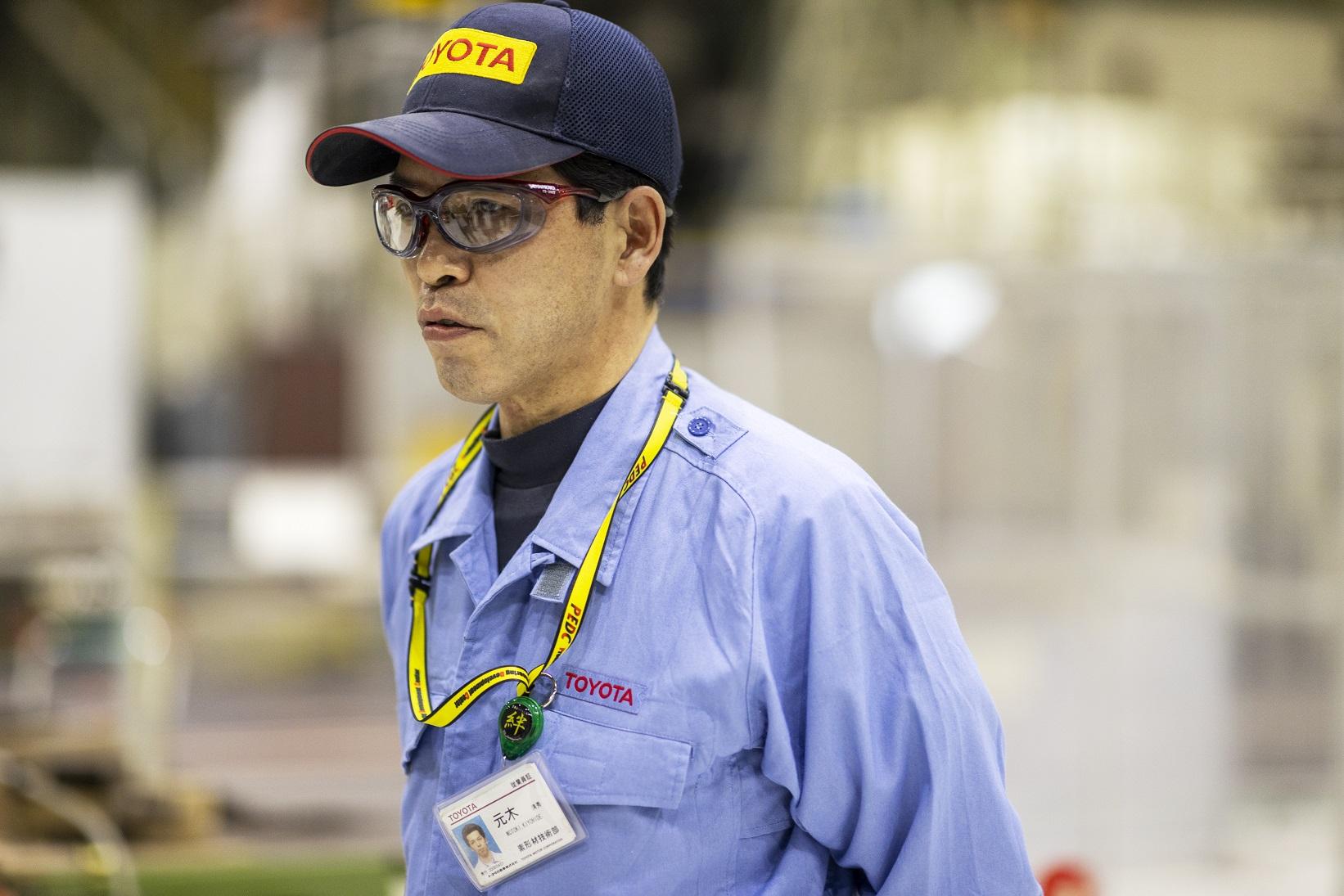
Series #2 Kiyohide Motoki, a master of casting captivated by the casting technology
Senior Expert (SX) at Raw Material Development Div., Myochi Plant, Toyota Motor Corporation
A master of casting at Toyota
Many car parts are made by casting. For example, the main engine parts such as cylinder blocks or cylinder heads, parts including the transaxle case and clutch housing used in the drive system that transmits the driving force from the engine to the tires, and undercarriage parts, such as aluminum wheels or brake disc rotors.
Body parts and battery cases for hybrid cars are also made by casting. Advanced casting technology is indispensable for Toyota's philosophy of pursuing “ryohin-renka,” which means providing high-quality cars at affordable prices.
Casting is a basic technique that has been used in manufacturing metal for over 5,000 years. A typical method includes sand mold casting.
First, the metal is melted at a high temperature, and then poured into the hollow part of the sand mold to be made into a boilerplate. After the sand-made boilerplate is broken once the metal has cooled and solidified, a finished product identical to the interior hollow part appears.
This processing method allows metal to be molded into any desired shape, regardless of its size or complexity. For example, Rushanabutsu, the symbol of Todaiji Temple in Nara and the world's largest gold and bronze Buddha, measuring approximately 18 meters high including the pedestal, is composed of eight layers of casted parts done over eight casting processes to create everything from the pedestal to the top of the head.

Kiyohide Motoki, a master of casting, works at Toyota. He is in charge of casting prototype parts at the Myochi Plant, and serves as an advisor on problems related to mass-produced casted parts. He is also involved in teaching less-experienced employees the basics of casting techniques. Born in 1962, Motoki is 58 years old now. Since joining Toyota in 1981, he has dedicated his life to casting.
In 2020, Motoki received the Sokeizai Industry Employee Award given to exemplary casting engineers in recognition of their exceptional technical know-how and skills by Sokeizai Center, which is responsible for promoting research and development of technologies related to the production of Japanese sokeizai (parts and components made by applying heat and force to materials).
He has also been recognized for his outstanding contributions to the evolution and development of casting technology, and has received the Chotaro Kubota Award, which is given to only one person from among all the award winners.
Chotaro Kubota (1882-1964), whom the award was named after, was a legendary casting technician who devoted his life to launching Toyota’s casting division. He joined Toyota Industries after winning Sakichi Toyoda’s confidence. After taking charge of the casting division, he worked on the development and manufacturing of casting machines, and developed the first domestically produced green sand molding machine in 1927. He is known as the "god of casting."

Currently, casted parts of Toyota's mass-produced engines are produced by using automatic sand mold machines and casting machines (for die casting or low-pressure casting).
However, Motoki was not involved in such mass production lines, but was in charge of casting various prototype parts, including those used for F1 engines in the prototype division, where ultimate machining accuracy and quality are required in small-lot production.
I started learning casting during my second year at Toyota Technical Skills Academy. When I joined the company, I actually wanted to be assigned to the mass production line. However, I failed the aptitude test and was assigned to the prototype division. I was able to live and learn among many skilled cast craftspersons who joined the company after gaining experience at other plants in town.

Motoki laughed when he mentioned that he didn’t get in the department he had hoped for. However, it seems the people around him saw his great potential in becoming a master of casting.
Motoki was amazed by the skills of the senior craftspersons. He learned everything there was to know about casting from them and became Toyota's leading casting technician in reality and in name. Motoki says that he is still not satisfied with himself and his skills, and cannot always work with total confidence.
The work of casting is a series of trial and error and every day is a learning process. There is depth to the casting technique, and because we rely heavily on human skill, knowledge and experience, it is impossible to be quickly substituted by solely using machines. It may be the most difficult metal processing technology to replace.
Challenges in producing motorsports engines
One of the casting master’s must-see works is the cylinder heads and cylinder blocks manufactured for motorsports engines, including the Toyota F1 Project (Toyota was fully engaged in Formula One between 2002-2009).
An F1 machine is equipped with the best engine with all available technologies at the time. As for the engine Motoki worked on back then, the maximum number of engine revolutions is about 18,000 to 19,000 per minute. It was an ultra-high-speed engine that was more than three times as fast as a commercial engine, and produced more than 700 horsepower.
The cylinder head and cylinder block are the most important parts of the engine body and determine the output, characteristics and durability. Also, since it requires massive power, fragile parts will start to break if the internal metal structure is not uniform.
Moreover, in order to burn fuel efficiently and move the piston smoothly at ultra-high speed, it is important to seal the combustion gas and reduce friction to a minimum by producing the cylinder head and its interior parts with accurate dimensions to the micron level.
Also, since the number of revolutions is about three times as much as a standard car engine, the heat generated during combustion is also tripled. Therefore, if there is not enough space (water jacket) for cooling water to flow inside the cylinder block, it will break down.
Casting is a unique manufacturing method that can solve all of these problems most effectively. Moreover, in order to win the race, it is necessary to simultaneously minimize weight and maximize power.
To do this, starting with the casting method, Motoki and his colleagues evaluated everything about manufacturing the heads and blocks. The casting method developed during this process later became Toyota's patented technology.

Also, they can ensure the quality by using a CT scan to eliminate blowholes (small bubbles created during the casting process) inside the metal, and make sure there is no sand in the water jacket during the casting process by using a fiberscope. As a result, they achieve a zero-defect product ratio, and in so doing gain the unwavering trust of the team.
The casting technology and expert knowledge developed by Motoki and his colleagues were fed back not only to race engines such as the IndyCar, but also to engine manufacturing of commercial vehicles. The technology gained from racing activities within Toyota is still alive, evolving and developing.
Passing the defining skills of casting to the future


Currently Motoki is teaching the defining skills for casting to other members who will be tomorrow’s leaders. The basis of casting is sand casting, which uses both a wooden mold identical to the desired metal parts and a mold (sand-made boilerplate) made of sand. Motoki demonstrated the hand casting process to us, which is one of the manual casting methods he teaches to young employees. Once he starts working, his expression changes dramatically. He uses all five senses to immerse himself in the work.

Casting with a sand-made boilerplate is done by embedding a wooden mold into the top and bottom frames that are firmly compacted with sand. After the wooden mold is removed, molten metal is poured into the space where the wooden mold used to be.
First, a wooden mold is embedded into the bottom frame containing sand, which is to be hardened. Then, a device called a sprue stick is planted in the sand to create a hollow cavity to allow the molten metal to be poured into the sand-made boilerplate. The sprue stick is removed after the top frame, also packed with sufficient sand, is stacked on, and once the stacked frames are placed at a 90-degree angle, the top and bottom frames can be separated.
Then, the wooden mold is removed from the bottom frame, and after using a scraper to carefully carve a passageway (runner) for the molten metal to be injected in the space created inside the sand-made boilerplate, the top and bottom frames are stacked once again.
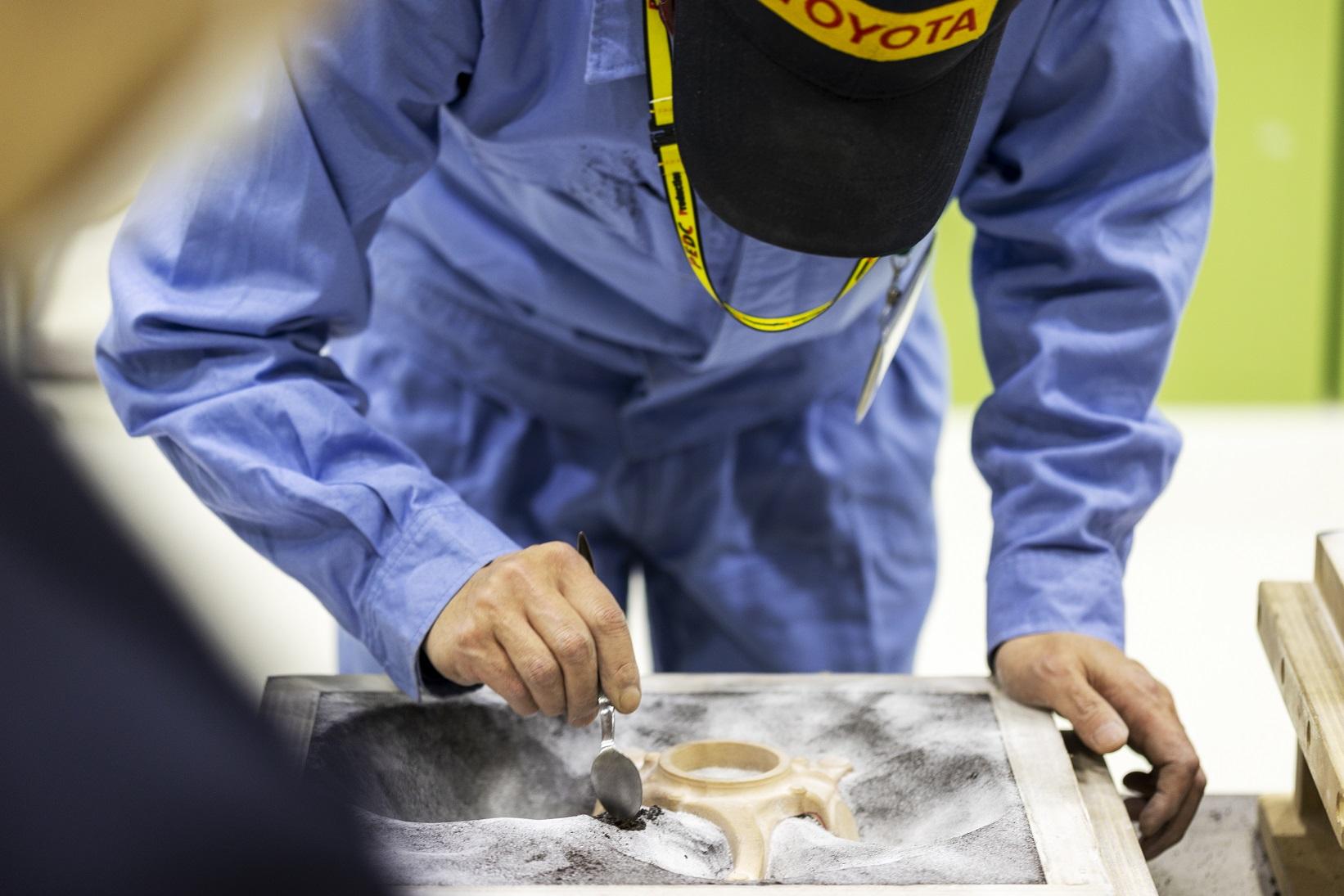
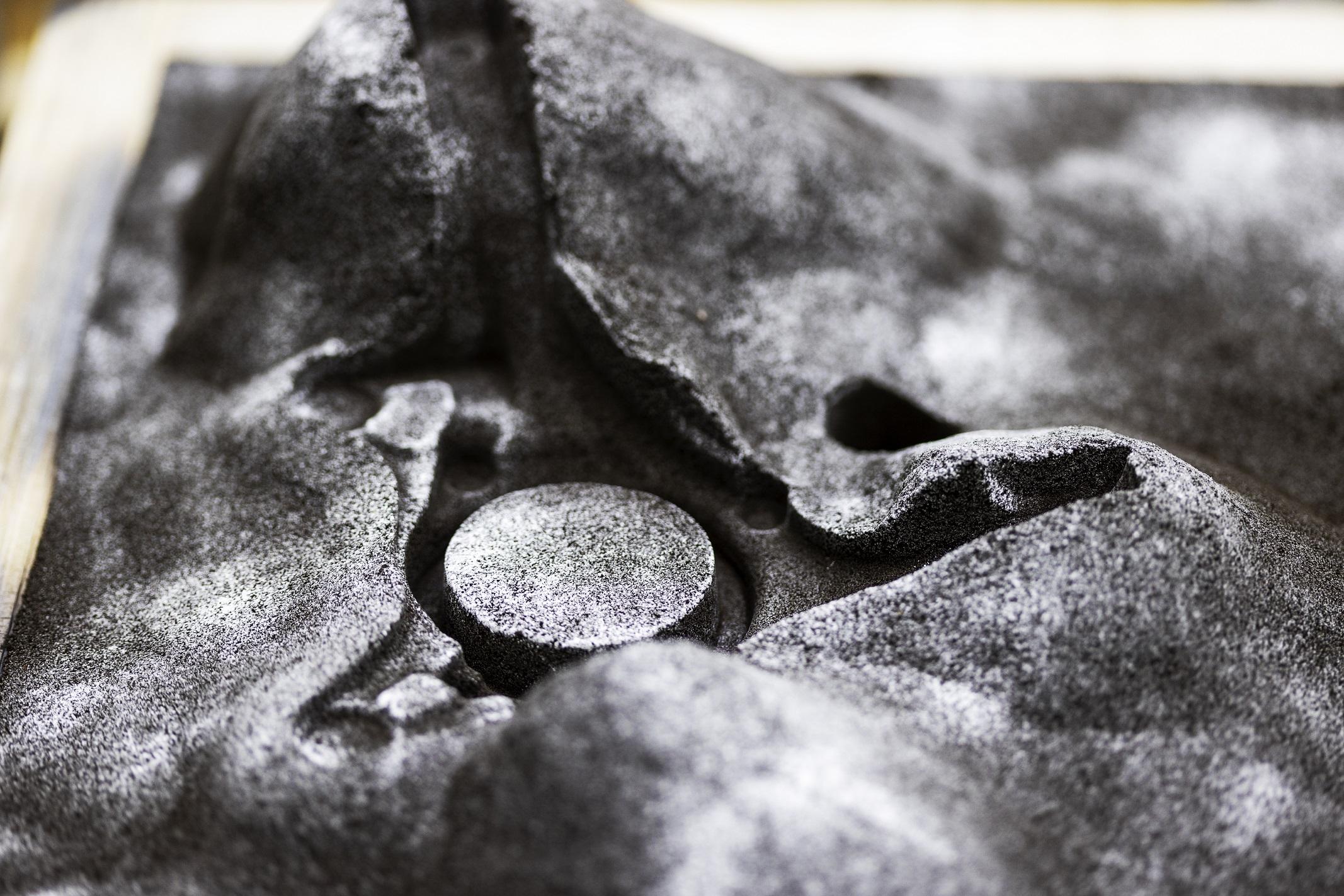
Molten metal is poured in from the sprue of the completed sand-made boilerplate using a ladle, and once the metal has hardened, the sand-made boilerplate can be broken revealing a metal part that is identical to the wooden mold.
When Motoki removed the wooden frames and broke the sand-made boilerplate once the aluminum alloy inside had solidified, the casted part appeared. Motoki finally smiled after looking serious throughout the entire process.
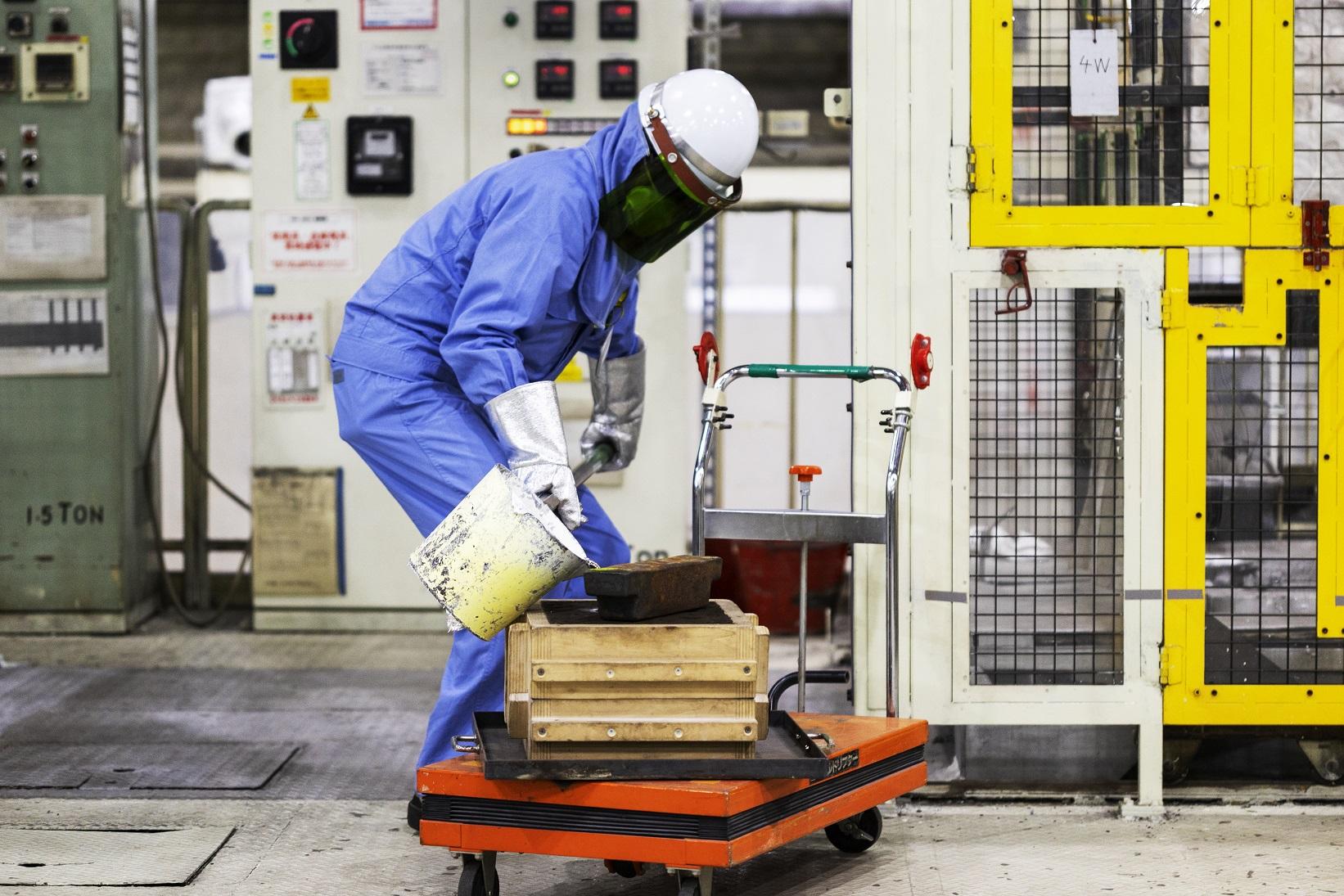
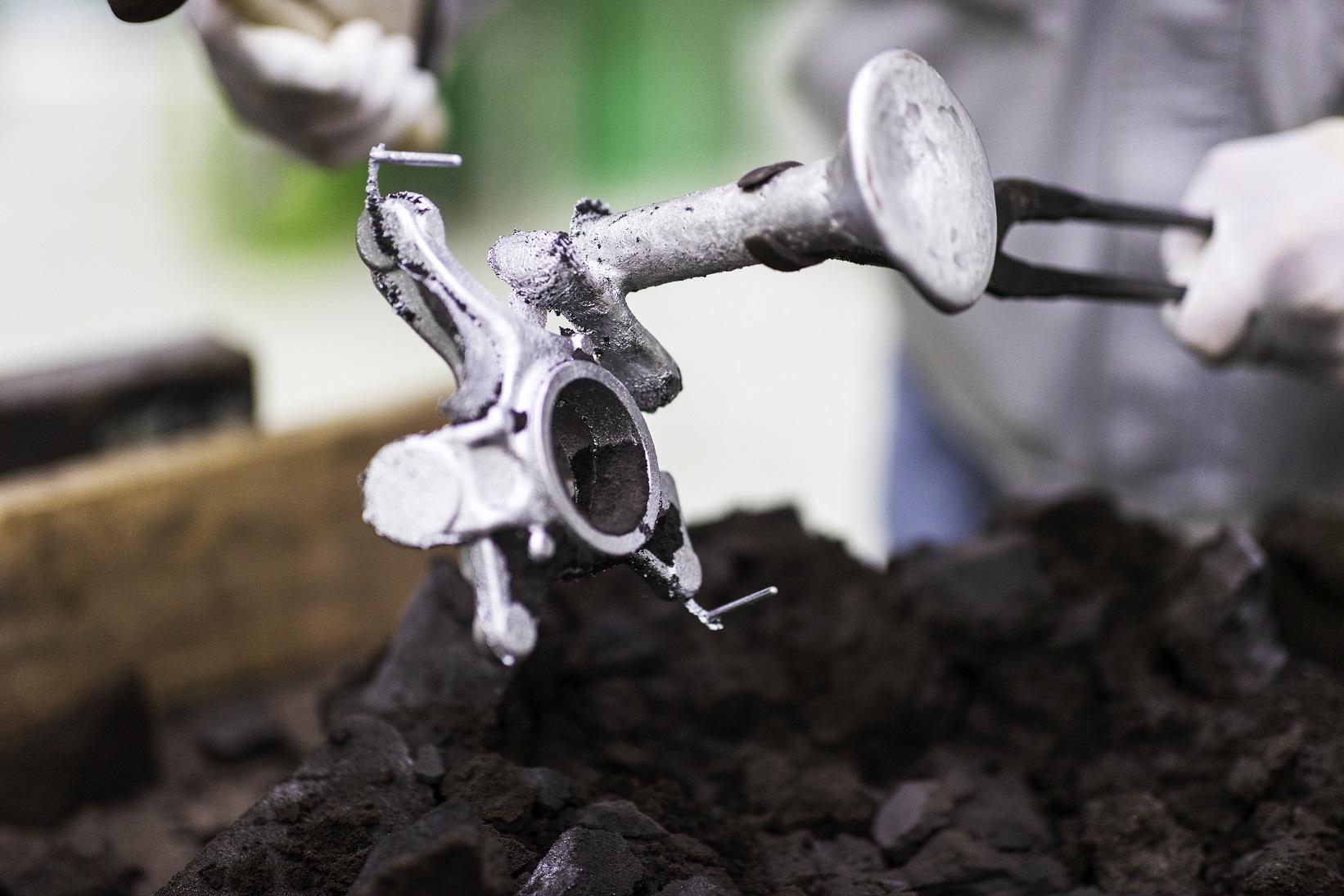
I want to convey the joy of casting
Casting is not just a job for the master of casting. Motoki is convinced that no other monozukuri process is more interesting or enjoyable.
The best thing about casting is creating something tangible instantaneously from nothing using metal. The finished part appears once the casting is removed. This moment excites me more than anything. Also, unlike other processes, casting allows for some trial and errors. You can always start over with casting and melt the metal again. Even if something goes wrong, you can instantly redo it. I want to convey this joy of monozukuri through casting to the younger generation along with the skills to do it.
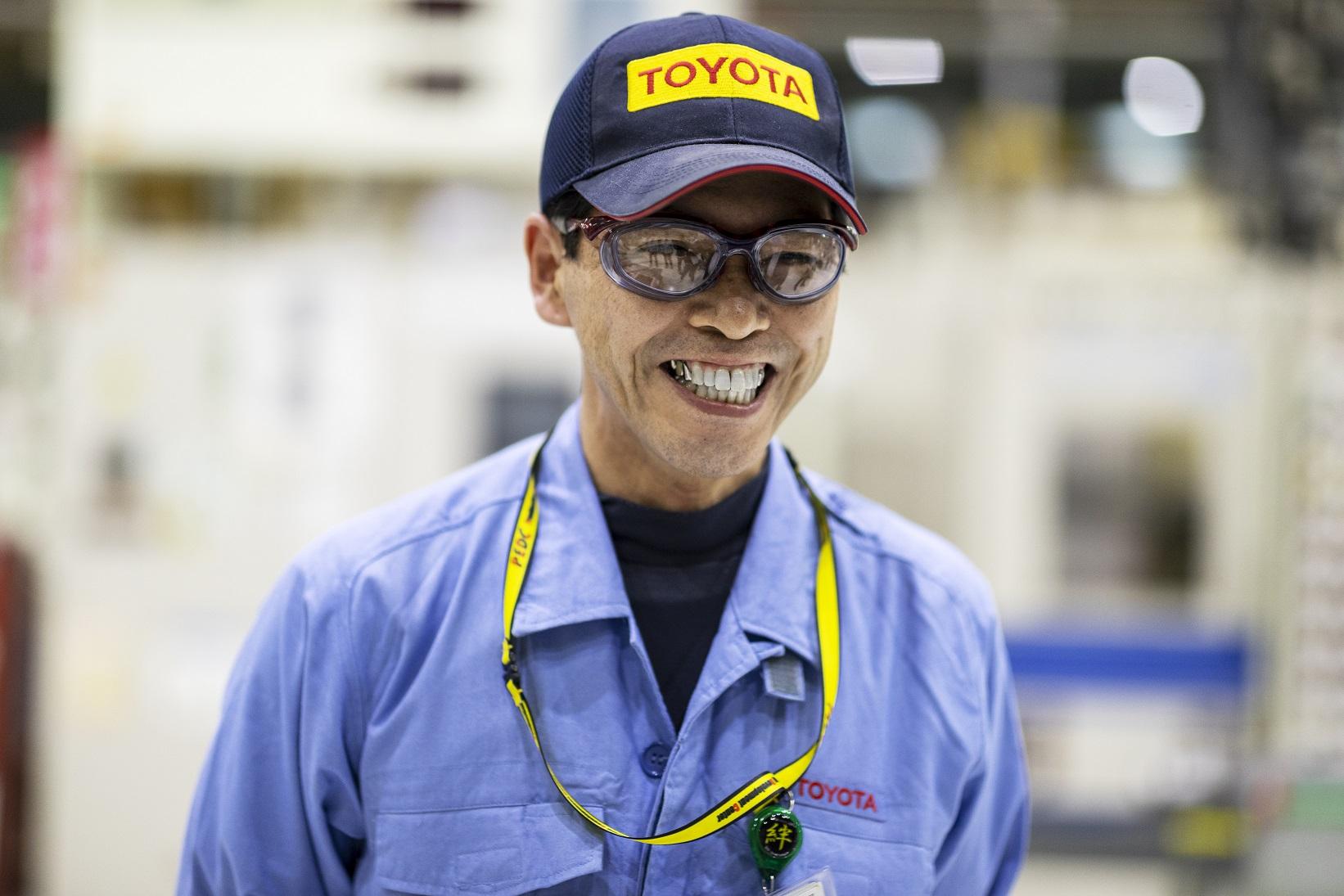
It is important to plan and design the cast during the process so that the molten metal is spread evenly in the hollow space without creating blowholes while the metal solidifies. This is called a casting plan.
Similar to other processes, much of Toyota’s casting is done primarily by large automated machines. In this case, the casting plan involves computer simulations. However, Motoki is convinced that the casting technicians operating these machines must still possess the unquantifiable defining skills for casting.
How does molten metal perform? How can you control the molten metal so that it goes where you want it to? It is impossible to fix any issues caused by the machine without having good instincts. Therefore, it is essential to learn hand casting skills, which involve overseeing the entire casting process solely relying on your own hands and instincts.
The future of Toyota’s monozukuri through casting depends on whether younger members with less experience can inherit Motoki’s defining skills. By passing on the skills of hand casting, Motoki is in essence molding the future with the younger generation.
(Text: Yasuhito Shibuya, photo: Akira Maeda)