
「問題意識はあったけど、進め方が分からなかった」。長年積み残された課題にトヨタと仕入先はどのように挑んだのか。

「本当にトヨタ、アイシンの方々も、うちの社員と一緒になって、改善に取り組んでもらって。時代が変わったと思います」。
黒田精機製作所(本社・愛知県名古屋市)の黒田敏裕社長は、笑顔で語った。
トヨタと仕入先の関係を探る連載。前回は2次仕入先(Tier2)の困りごとに対して、トヨタと1次仕入先(Tier1)が一緒になって解決に取り組む「グループ連携活動(グル連活動)」を紹介。活動に参加した、クルマの内装部品を手掛ける、林テレンプ(Tier1)・梅村工業(Tier2)の事例を取り上げた。
第3回も引き続きグル連活動に取り組んだ事例をお届けする。困りごとと分かりつつ、長年に渡って取り残されてきた課題に、トヨタ・Tier1・Tier2はどうアプローチしたのか?
後回しになっていた物流改善
黒田精機製作所はアイシンのTier1で、主にエンジンやブレーキの部品を生産している。国内外6カ所に拠点があり、その中で23年3月から11月の間グル連活動に取り組んだのが、養老工場(岐阜県養老郡養老町)だ。
ここの課題の1つが工場内での物流作業だった。
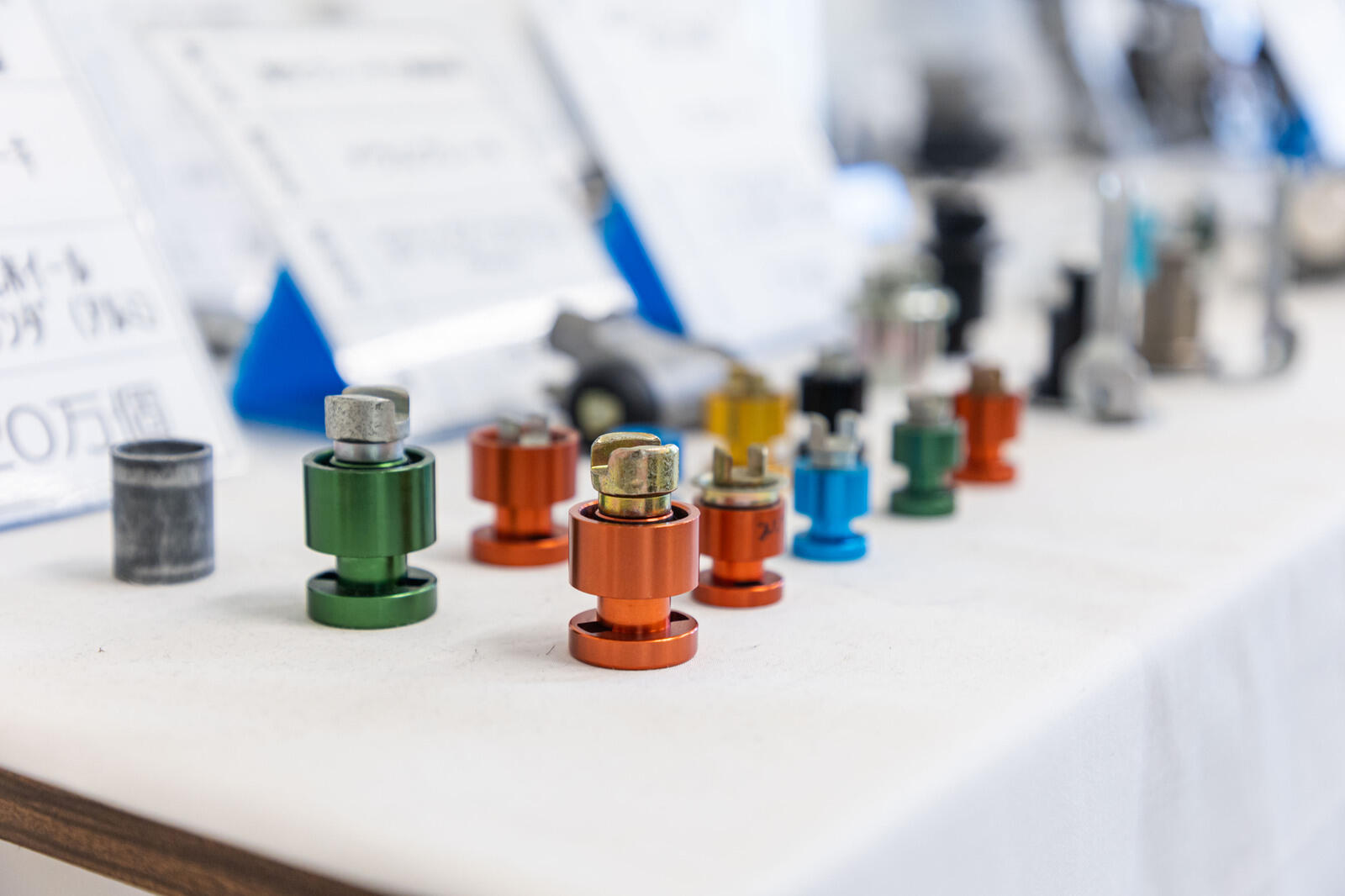
養老工場は40年ほど前に操業を開始して以来、生産数を増やし、現在は第3工場まで稼働している。
各工場にヤードを構えているものの、生産を優先するあまり、部品供給や完成品出荷に必要な動線確保といった物流構築は見直されてこなかった。
トヨタでは4S(整理・整頓・清掃・清潔)の「整頓」をやりやすくするための、「5定」という考え方があるが、この中の「定路」が後回しにされた形だ。
ちなみに「5定」については、以下の通り。
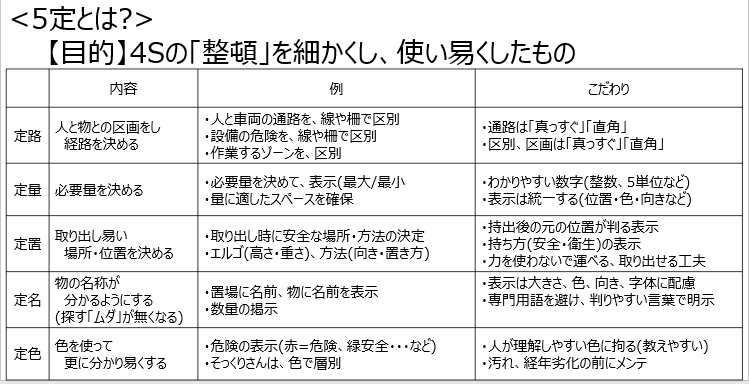
養老工場では物流作業を安全にムダなく行う標準化が図られず、入荷と出荷の機能が未分化のヤードでは作業のバッティングが起きたり、歩行者とフォークリフトの通行帯が混在してしまっていた。
こうした点は、作業者らの間でも問題意識としてあったが、長くこの状態が続いていたこともあり、「どう改善を進めたらよいか分からなかった」という。
グル連活動では、特に問題点の多い入出荷共用ヤードに焦点を当て、ここを出荷専用に変更。トヨタの工場と同様に床にラインを引き、人とフォークリフトの作業エリアを明確に分けて安全性を確保した。
安全・安心に働くことができる職場環境の構築はトヨタでも最重要とされており、活動でも「安全最優先」とアドバイスがあったという。
入荷機能は別の入荷ヤードに集約。結果として「材料の入荷→工場内への供給→完成品の集荷→出荷」が一方通行で流れるようになり、バッティングも解消された。
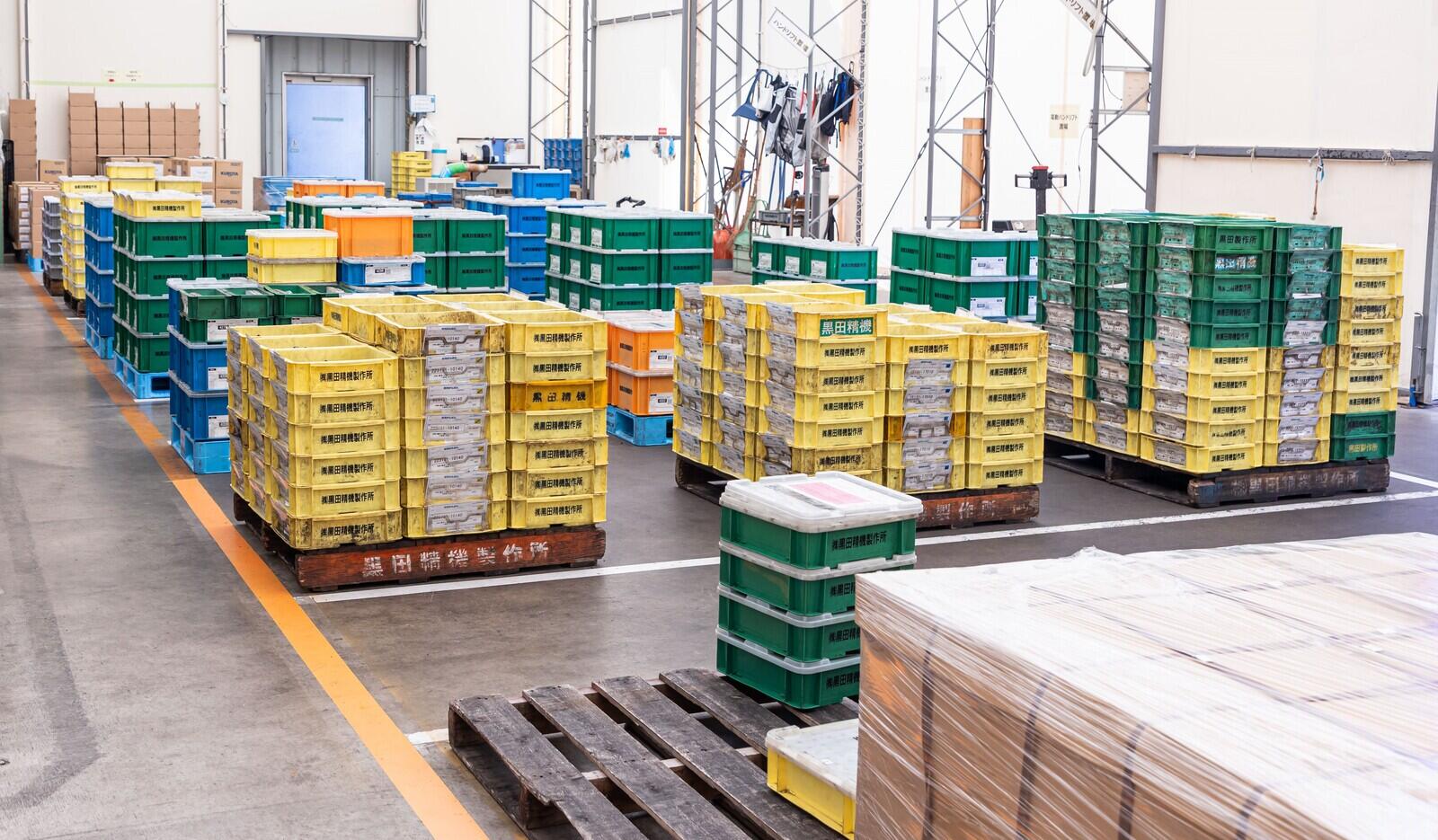
また、入荷機能を移したことでフォークリフトが立ち回りやすいスペースも確保。出荷品は便ごとにレーン分けされ、後工程の物流ドライバーからも「作業がやりやすくなった」という声が届いている。
「かんばんポスト」で進捗管理も簡単に
効率的な構内物流の構築に向けては、養老工場で一番運搬量が多く、移動距離も長い第1工場をモデルに取り組んだ。
最短の集荷ルートを設定するため、完成品や通い箱*の適切な置き場、集荷量といった基本的な情報を調査。台車へ通い箱を載せたり、集めた完成品を出荷用のパレットに移し替える、いわゆる要素作業の洗い出しには、トヨタやアイシンのメンバーも参加し、移動も含めた各作業にかかる時間を測定した。
*拠点間を行き来しながら部品や製品を安全かつ効率的に運ぶための箱。生産現場や運ぶものに応じて中敷きを変更し、さまざまなニーズに対応する。
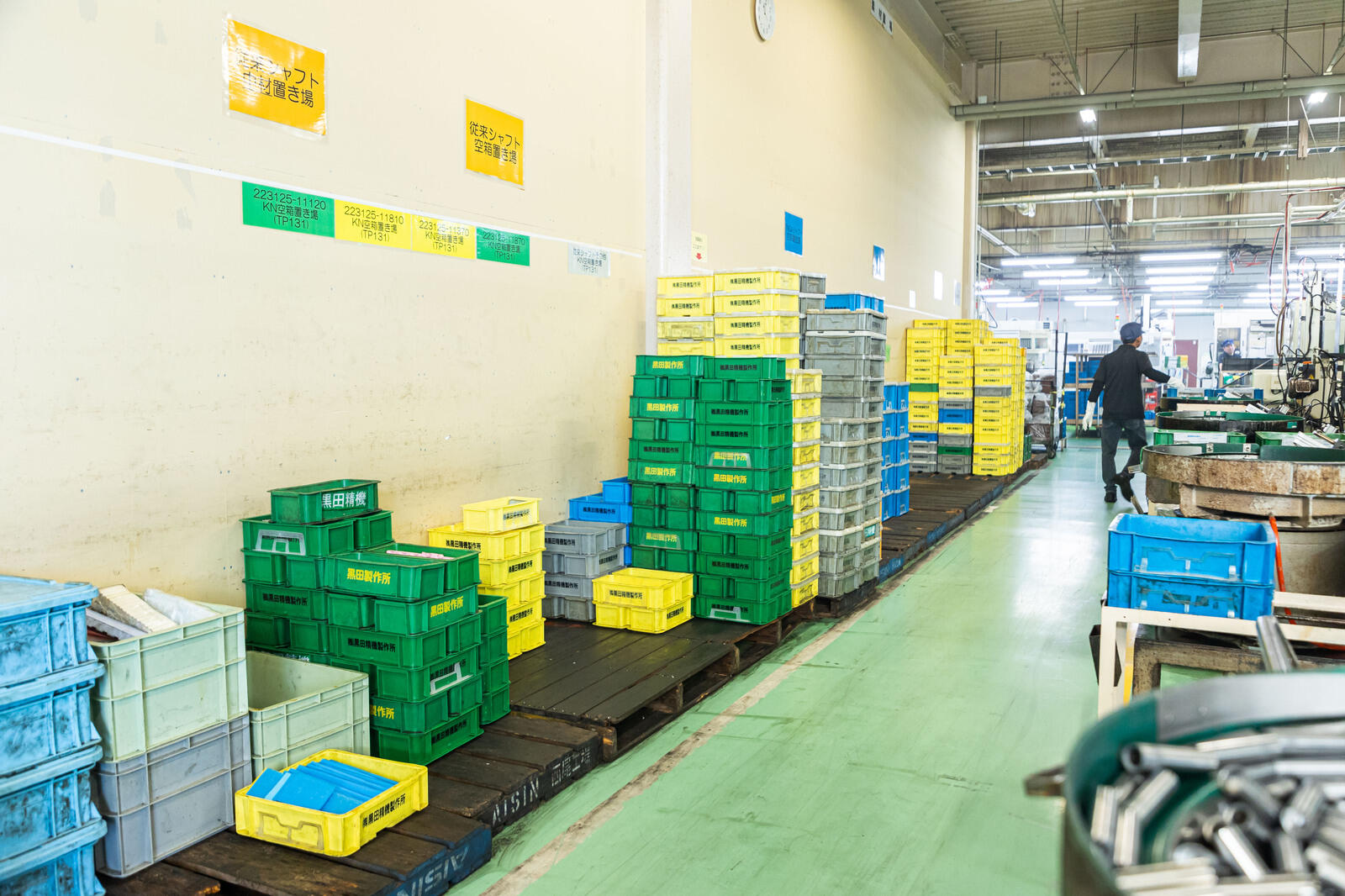
運搬方法では、「実空(みから)運搬」を採用。
作業者は出荷ヤードを出発して、完成品の集荷場所に向かう途中で空箱(空)をピックアップ。集荷場所で完成品の入った箱(実)と交換して、出荷ヤードに戻ってくる。
グル連活動前は、完成品の集荷を複数人で行っていたこともあり、集荷作業の重複や空箱だけの運搬というムダが発生していた。現在は集荷作業者を一人に絞ったことにより、こうした問題も解消されている。
このほか、出荷ヤードには「かんばんポスト」を設置。集荷スケジュールが一目で分かるようになり、作業監督者も進捗管理がやりやすくなった。運搬作業をカンとコツに頼っていた以前は、とにかく完成品を出荷ヤードに運んでいたが、「必要なものを必要な時に必要なだけ」運ぶ後工程引取りの考え方が生かされている。

こうした改善活動の結果、養老工場の物流現場では活動前後で2人の省人に成功し、生産性向上につながった。
作業者たちは、「1年かけて教えてもらったことをムダにしたくない」と今も改善を続けている。