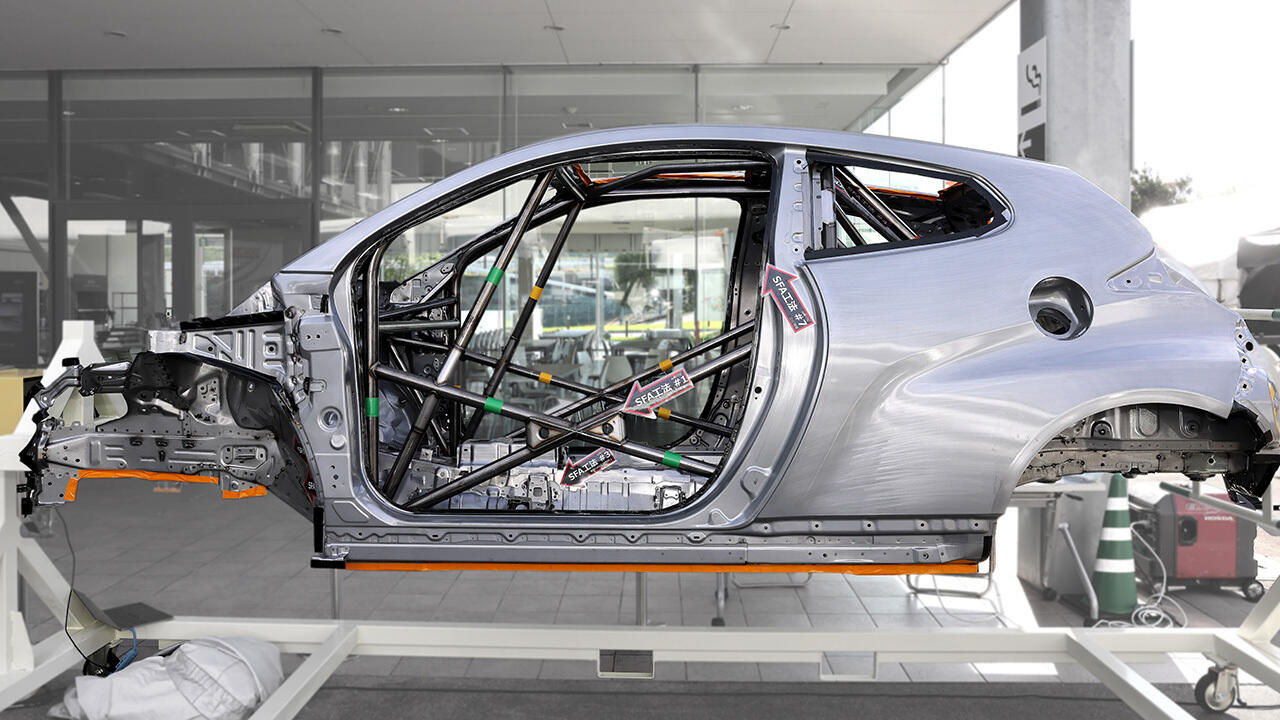
モータースポーツの困りごとを改善し、裾野拡大へ。世界初の溶接技術がスーパー耐久の現場で披露された。
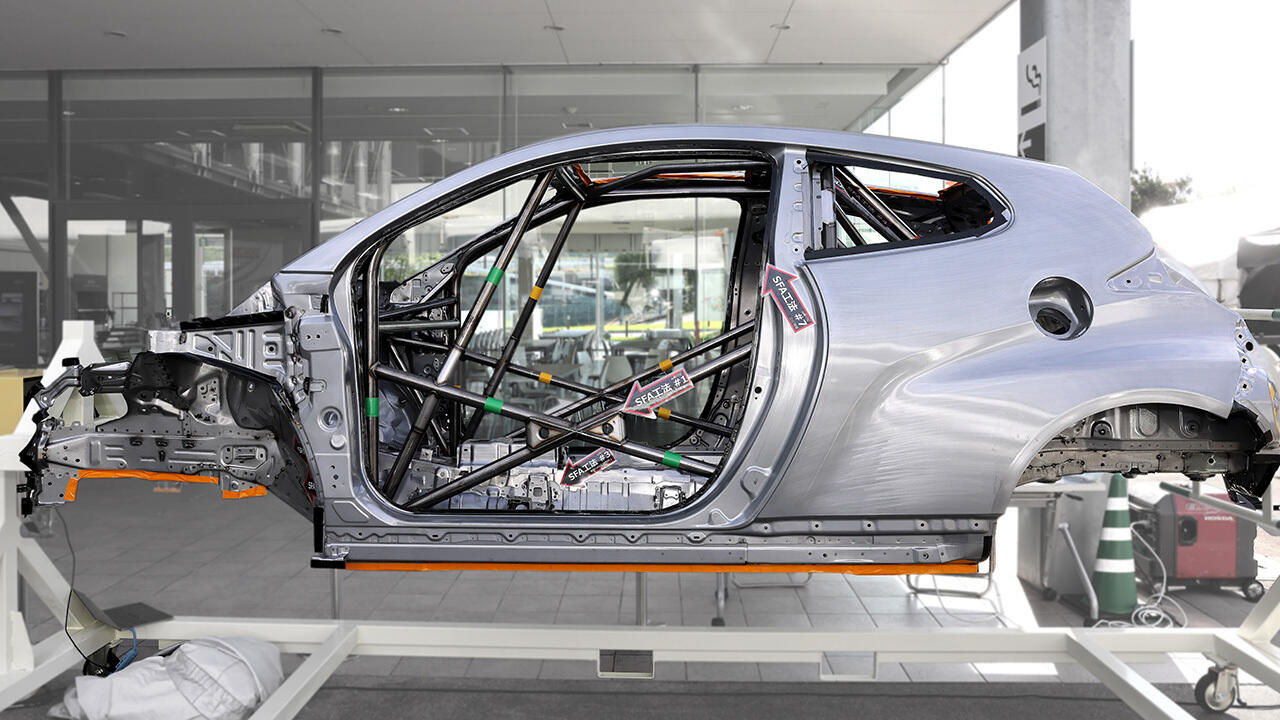
水素エンジン車やカーボンニュートラル燃料車、DAT(ダイレクト・オートマチック・トランスミッション)。これまでトヨタはさまざまな新技術を、モータースポーツの現場で鍛え、もっといいクルマづくりへと生かしてきた。
それらは、市販車の選択肢を広げることであり、モータースポーツの裾野拡大にも寄与するものだ。
そしてまた、モータースポーツをよりサステナブルなものにするかもしれない、世界初のアーク溶接技術「SFA(Sequence Freezing Arc-welding)」が披露された。
舞台は9月28、29日の両日、鈴鹿サーキット(三重県鈴鹿市)で開かれたENEOSスーパー耐久シリーズ(S耐)2024 Empowered by BRIDGESTONE第5戦。ROOKIE Racingは、この技術を取り入れたGRヤリス(32号車)でST-Qクラスに参戦した。
さらに会場では、32号車と同じSFA工法を使って組み上げたロールケージも展示。
ロボティクスの活用により、これまでより大幅にリードタイムを短縮した溶接の新技術。その内容を取材した。
次のレースに間に合わない
開発の発端は2023年8月、モリゾウこと豊田章男会長が、フィンランドでTOYOTA GAZOO Racing World Rally Team(TGR-WRT)の製造現場を視察した際のこと。当時TGR-WRTでは、ホワイトボディ(塗装前の骨格やパネルが組み立てられた状態の車体)へのロールケージの組み付けに苦労していた。
ロールケージについて簡単に説明しておくと、競技車両の車体内部にかごのように組み込まれるフレームを指し、クラッシュ時に乗員を保護する役割を担う。競技規定で厳格に取り付けが定められている。
約50本のパイプからなるロールケージを車体へ取り付けるには、高度な溶接技術が求められ、従来は熟練の溶接工が、ボディの内側に1本1本手作業で組み付けていた。1台あたりにかかる製作期間は2~3週間ほど。レーシングカーをつくり上げる中で最も時間を要する工程だった。
このリードタイムでは、仮にラリーの参加者が廃車になるほどのクラッシュを起こしてしまうと、次のレースまでにはクルマの手配が間に合わない。トヨタ生産方式(TPS)の力でいかに早くボディを組み上げるかが課題だった。
GAZOO Racing Company GR車両開発部の川喜田篤史 主査と、産業用ロボットの製造などを手掛けている安川電機のロボット事業部ロボット技術部の柴田将太さんを中心に、開発は約1年に及んだ。
GR車両開発部 川喜田 主査
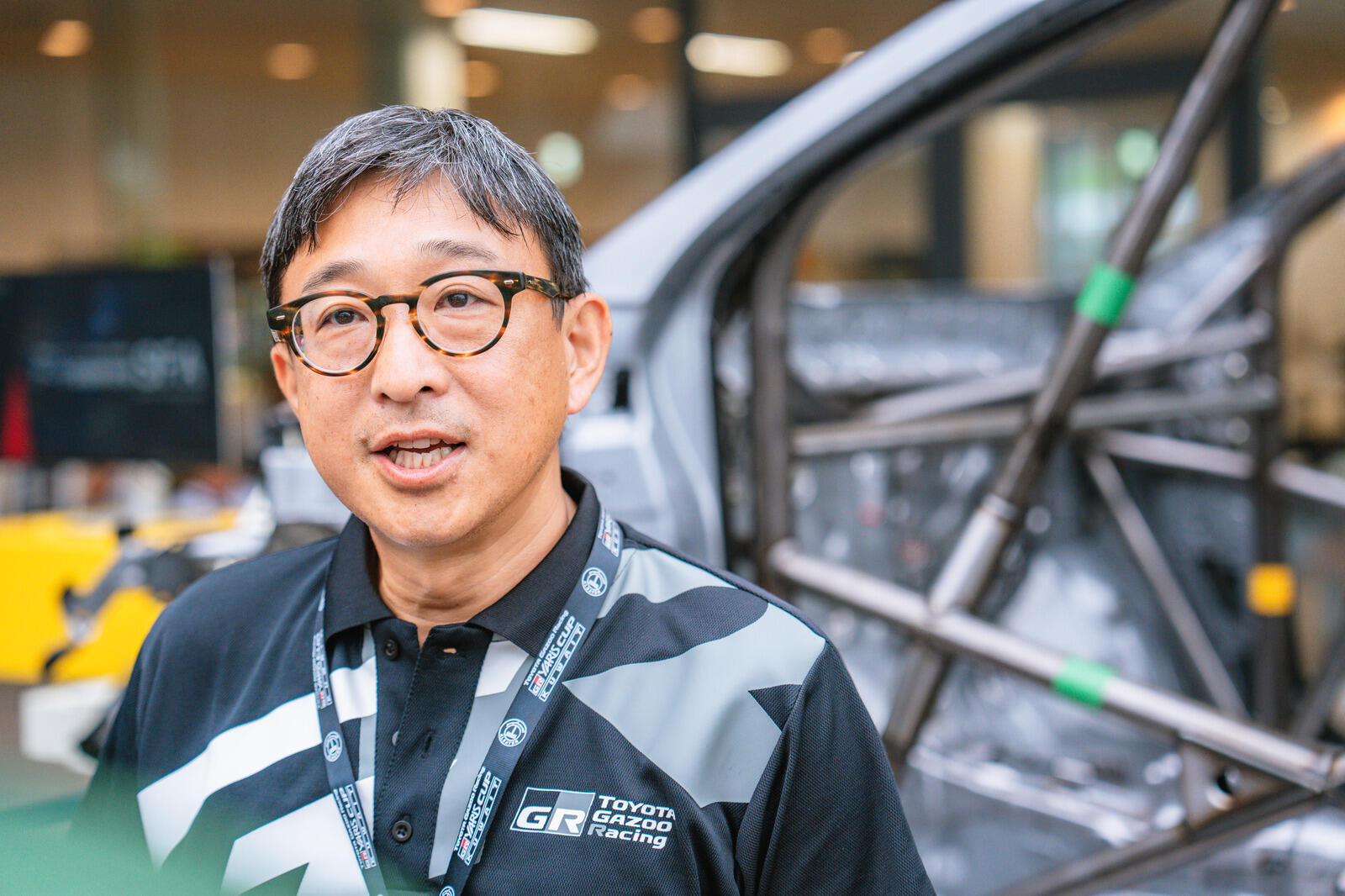
モータースポーツをもう少しサステナブルにしていくとか、参加していただく皆さんへもっと門戸を広げて、参加しやすい環境をつくっていくために、メーカーとしてどういったことができるかと考えたときに、ロールケージ付きホワイトボディをいかに早く供給できるかという課題認識でスタートしています。
ゆっくり、丁寧に
SFAでは、熟練の溶接工の技術を数値化。見えてきたノウハウをロボットに教え込んでいる。
そもそもロールケージの溶接に熟練工の腕が求められるのは、溶接時の熱でひずみが生まれてしまうため。熟練工はこのひずみを頭の中で計算し、手で感じながら矯正しているのだが、この匠の技がロボットには難しい。
開発をスタートして約3カ月、ひずみを計算しながらの溶接が難しいのであれば、「ひずみを生まないように溶接するには?」と発想を逆転。
従来の溶接だと、鋼材に熱が入り過ぎてしまうことが、ひずみを生みやすくしていた。そこでSFAでは、ロボットが人よりゆっくり1回1回間隔を開けながら溶接することで、熱を蓄積させず、ひずみを抑制。
溶接スピードは、60秒に1台というトヨタの量産ラインのタクトタイム(1つの製品をつくるのにかかる時間)に比べると、10倍も遅い。だが、「タクトタイムという概念を取っ払って」(川喜田主査)考えられるレーシングカーだと十分な速さだという。
効率が優先されるロボットに、あえて「ゆっくり丁寧に」作業させるというのは、安川電機にとっても挑戦だった。自身もドリフト競技に参加するほどのクルマ好きで、ロールケージなども自分で組むという柴田さんは、このように語る。
安川電機 柴田さん
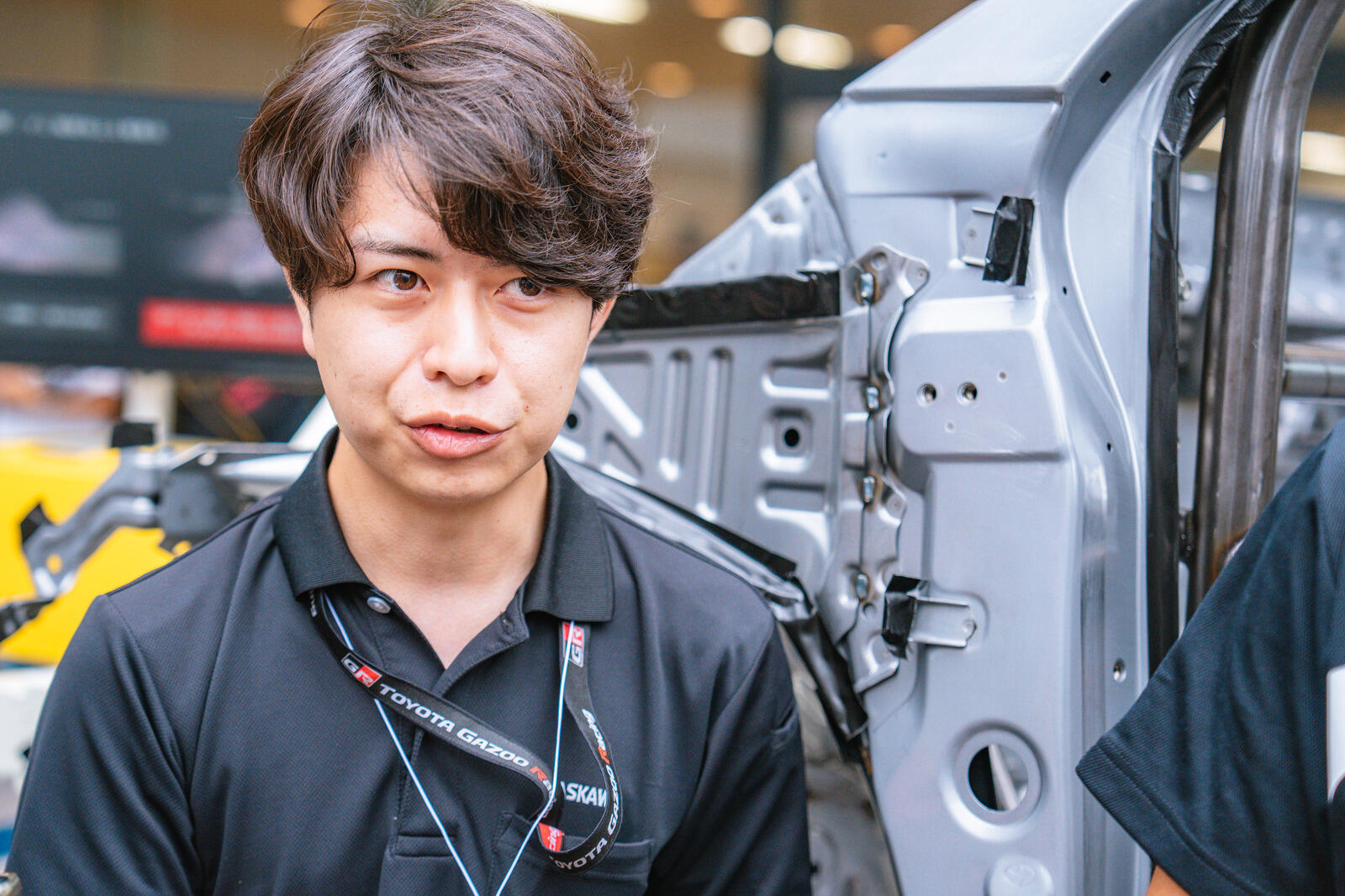
我々はロボットメーカーとして、これまではより速く・より効率的にクルマをつくっていくという領域でロボットを提供してきました。
今回のように、人よりゆっくり丁寧にという領域には踏み込んでいませんでした。そこへのチャレンジとして、(今までの)速くつくるという技術は使えなかったので、ゆっくり丁寧に時間をかけてつくるという技術に1年かけて取り組んできました。
SFAを用いることにより、ビードと呼ばれる溶接部は、薄く広くなり約25%軽量化。母材との溶け込みも深くなり、溶接部の強度は10~25%上がっている。
また、1回1回凝固させながら溶接しているので、溶金が自重で垂れず、これまでは難しかった上向きや上り/下り溶接もできるようになった。
このほか、スポット溶接*のような点でのアーク溶接や、2~3ミリの隙間の溶接も可能といった特徴も併せ持つ。
*重ねた鋼板を電極ではさみ、電流と圧力で鋼板を溶かして「点」で接合する方法。アーク溶接は、溶接用ワイヤーと鋼板を溶かして(合金化して)接合する方法。スポット溶接がやりにくい(電極ではさめない)部分に使われる。
またSFAでは、「副産物」として今まで溶接できなかった部位もできるようになっており、ロールケージだけでなく、ボディそのものの剛性も高められるという。