
自動車業界を匠の技で支える「職人」特集。第12回は足回り部品の強度試験を独自のノウハウで行う「ひずみゲージの匠」に話を聞く

3DプリンターやAIをはじめとするテクノロジーの進化に注目が集まる現代。だが、クルマづくりの現場では今もなお多数の「手仕事」が生かされている。
トヨタイムズでは、自動車業界を匠の技能で支える「職人」にスポットライトを当て、日本の「モノづくり」の真髄に迫る「日本のクルマづくりを支える職人たち」を特集する。
今回は、クルマづくりの現場で、足回り部品の強度試験を独自の方法とノウハウで担当する若き「ひずみゲージの匠」岡田卓也(おかだ たくや)の後編をお届けする。
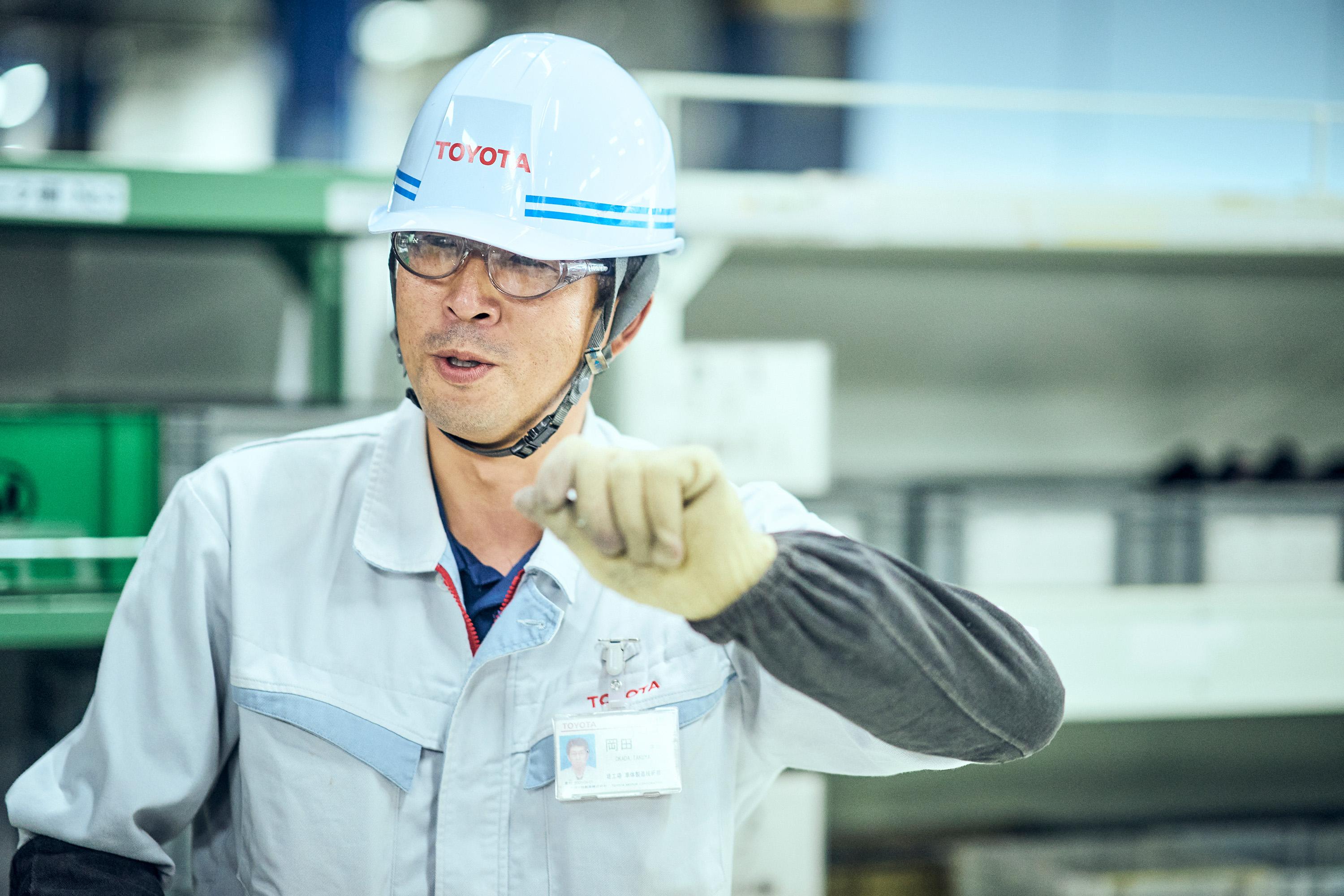
第12回 足回り部品の強度試験を独自のノウハウで行う「ひずみゲージの匠」岡田卓也
トヨタ自動車 生産本部 堤工場 車体製造技術部 プレス工程整備課 品質保証4係 チームリーダー
どんなセンサーをどのように貼り付けるかが難しい
岡田は実際、どのようにひずみゲージを使って足回りの強度試験をしているのか。愛知県豊田市にある堤工場 車体生技部 プレス工程整備課の職場を取材した。
「ひずみゲージは使い捨てで、計測したいものに瞬間接着剤でサッと貼り付けて使います。このいちばんベーシックなものは、だいたい1個500円くらいですね。貼り付ける作業のとき、私は椅子に座らず膝を床に付けて“無の境地”に入って行うことにしています。『1個500円。1個500円』と頭の中で唱えながら、失敗しないように気合を入れて(笑)。私は手が大きいので、細かい部位に貼り付けられるようになるまで苦労しました」
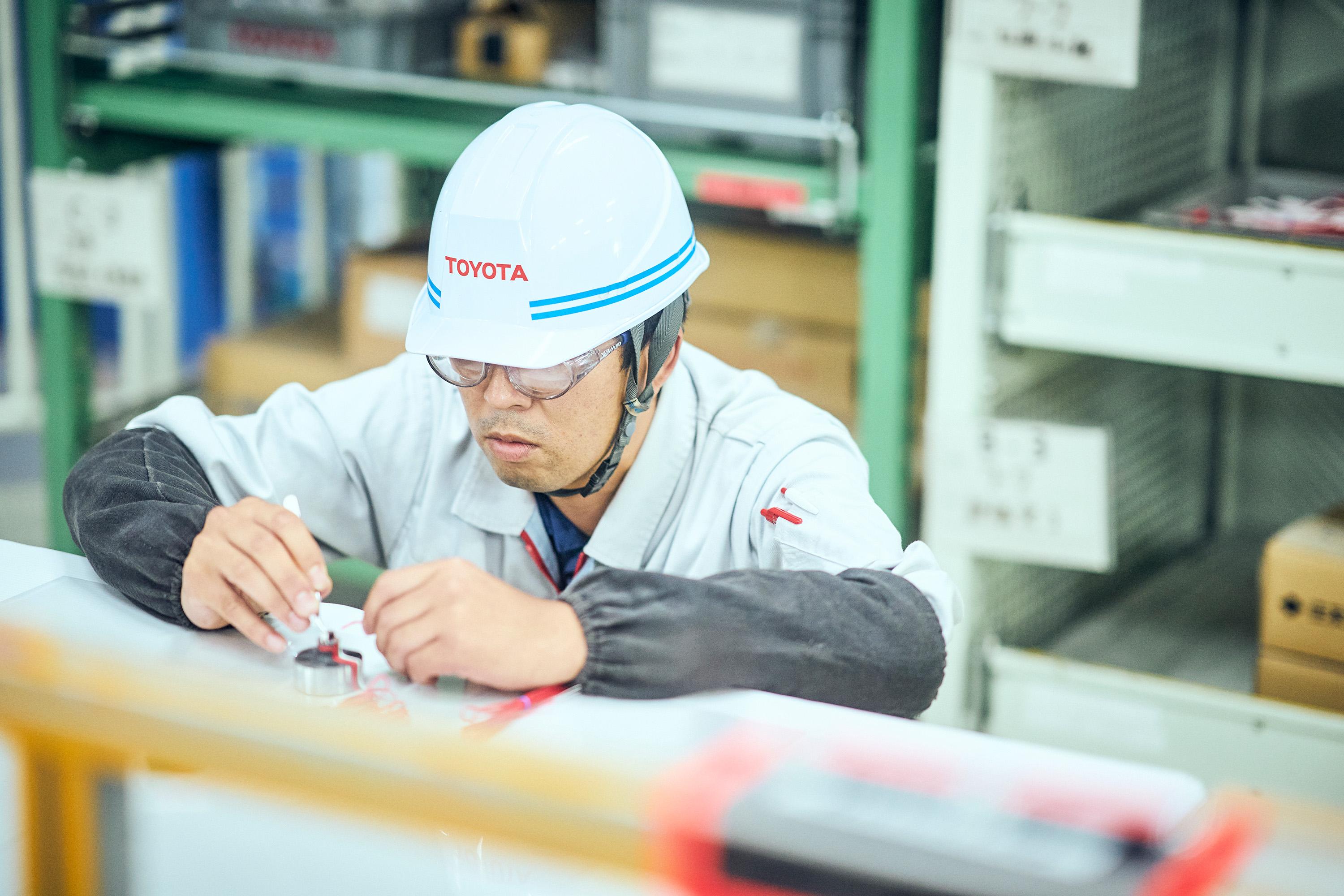
岡田はいつものデスクでその作業を実演してくれた。ひずみゲージを貼り付ける位置にケガキ(印となる点や線)を付け、瞬間接着剤を数滴付けると一瞬で作業は完了した。
だが、ひずみゲージの使用説明書にも書かれているが、難しいのは、その使いこなし。ひずみゲージの計測値は設置した場所で大きく変わる。だから、部品の応力=強度を測定するときは、計測するモノの適切な位置に、適切な方法でセットしなければならない。もちろん、基本的な配置や測定の方法はマニュアル化されている。しかし、それはあくまで基本に過ぎない。
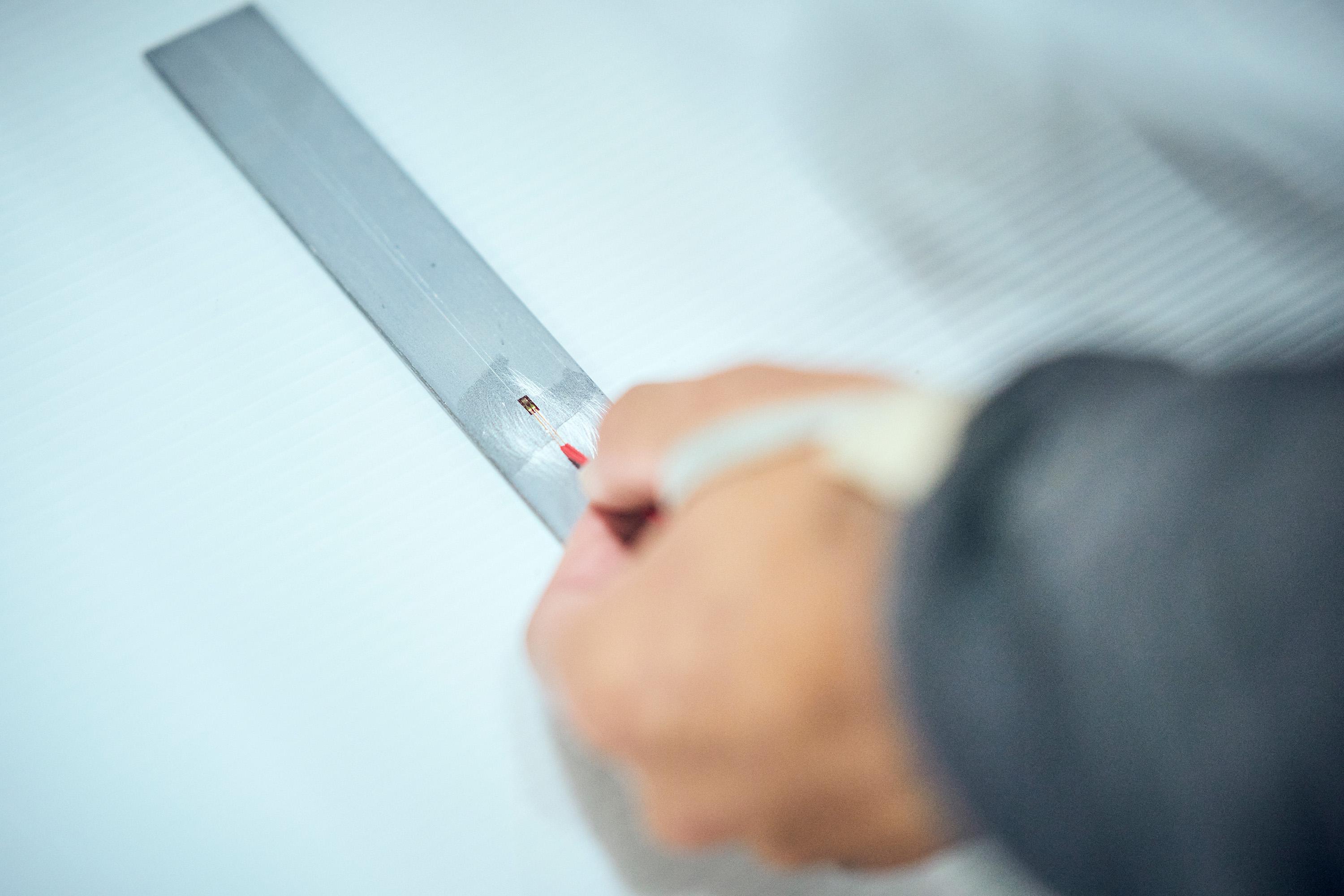
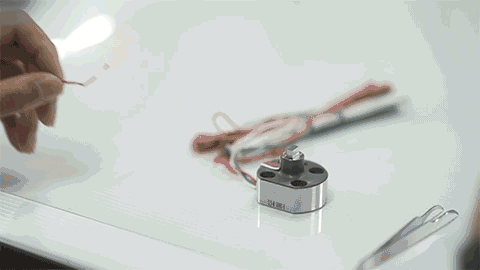
ひずみゲージが開発されてからすでに70年近くが経過し、モノづくりをはじめさまざまな現場で広く使われている。だがメーカーのマニュアルには「使用者の長年の経験とノウハウが必要です」と書かれている。測定する材料や目的に合わせて治具や工具をつくるなど、細かな工夫が不可欠なのだ。
「大切なのは測定の仕組みや目的、方法を徹底的に考えること。これはひずみゲージ以外の測定器を使う場合も同じです。前にもお話しましたが、きちんと測れないなら測らない方がいい。測定の原理からしっかりと考えておかないと正確な測定はできません。また、測る材料の知識も不可欠です」
外部からは見えない部品内部の状態を可視化
岡田がひずみゲージを使って主に行っている試験は、フロントおよびリアサスペンション部品の疲労強度試験と変形強度試験だ。
クルマが走り、曲がり、止まるたびに、足回りの部品には繰り返し大きな力がかかる。設計段階から想定していた程度の力でも、繰り返し強い力がかかることで、鋼やアルミ合金などでつくられた足回り部品には、目に見えないダメージが「疲れ」のように蓄積し、少しずつ強度が損なわれていく。これが金属疲労だ。
金属疲労が限度を超えると、部品の内部に目に見えない小さな亀裂や破断が起きて強度が低下し、やがて壊れてしまう。つまり走行不能など、事故につながる深刻な事態が起きる。
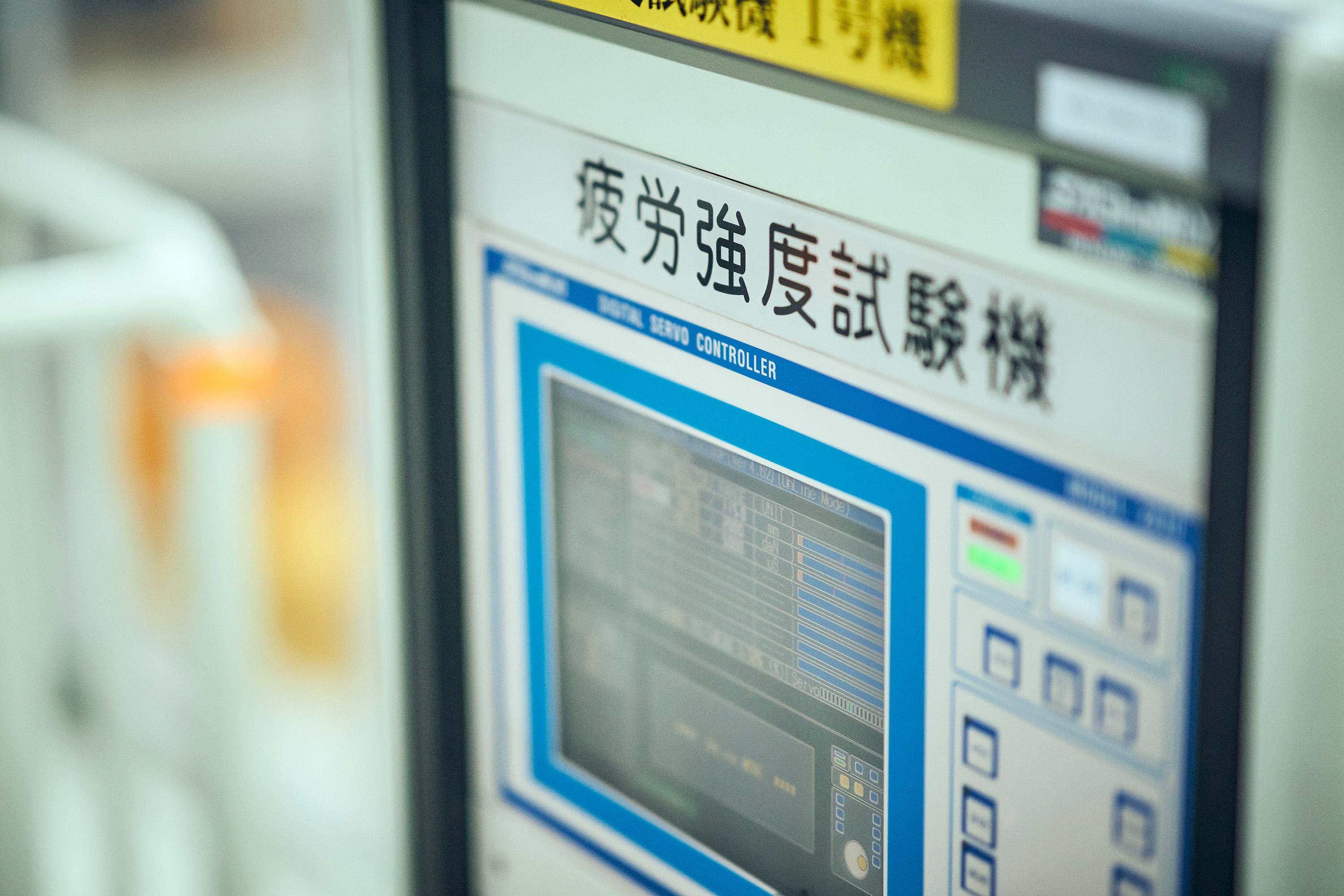
疲労強度試験は、ひずみゲージを貼り付けた足回り部品を油圧で稼動する試験機にセットして、走行時と同様に部品に繰り返し力を加えることで、その疲労強度を測定する試験だ。このとき部品にセットしたひずみゲージから、内部でどのくらいの応力が発生し、どのくらいの変形が起きているかを測定できる。そして、加える力の大きさや回数を変えて何回も試験を繰り返すことで、部品の強度の限界が分かる。クルマの走行安全には欠かせない試験だ。
「外からは見えない部品内部の状態が、ひずみゲージの計測データを見れば分かります。たとえば、ごくわずかでも素材の内部に亀裂ができると、それが数値の変化として現れます。そろそろ壊れるな、ということも数値で分かります。数値の変化が大きくなると直後にバン!と壊れます」
疲労試験にはクルマの急発進・急停止を想定した前後疲労試験、クルマがコーナリング中の状況を想定した左右疲労試験、一般道や悪路の走行で起きるクルマの上下動を想定したトランピング疲労試験がある。
もうひとつの変形強度試験は、縁石への衝突など通常の走行とは違う事態を想定して、足回り部品にタイヤから加わる衝撃的な力を試験機で再現し、部品がどのくらいの力でどのくらいのダメージを受けるかを確認するものだ。こちらもクルマの安全確保には欠かせない。
岡田は入社以来、この強度試験の仕事ひと筋に経験を積み重ね、持ち前の探究心から、先輩から受け継いだノウハウをさらに発展させ、ひずみゲージをはじめ、さまざまな測定器を使った独自の計測法を確立。常識では不可能とされてきた測定を次々と実現してきた。
普通なら「測れないもの」を測る
そんな岡田のところには、評判を知った社内のさまざまな部署から「既存のやり方では測れないけれど、何とかこの部品の強度をテストしてくれないか」という相談がひっきりなしに持ち込まれる。「岡田なら何とかしてくれる」。そんな口コミを聞いた人々が訪ねてくるのだ。
「できないとは絶対に言いたくないんです。測れないものを何とか測る。それが自分の腕の見せ所だと思っています。特に、前向きに開発している人の相談には必ず応えたい」
そんな岡田が記憶に残っている仕事のひとつが、ボデー外板の塗装工程での熱ひずみのリアルタイム測定だ。ボデーの外板の内側には、クルマの静粛性を確保するためのゴム系の特殊塗装が行われる。しかし、この塗料を乾燥させる際に「熱ひずみ」により、外板に凸凹が生じるという問題が起こる。
「熱ひずみを測定・解析して解決を図りたい」。この塗装部門からの依頼で困ったのが、ひずみゲージの耐熱性だった。岡田は遮熱&冷却機能のある木製の箱を自作し、ひずみゲージ全体をその中に入れることで、不可能だったこの測定を実現した。
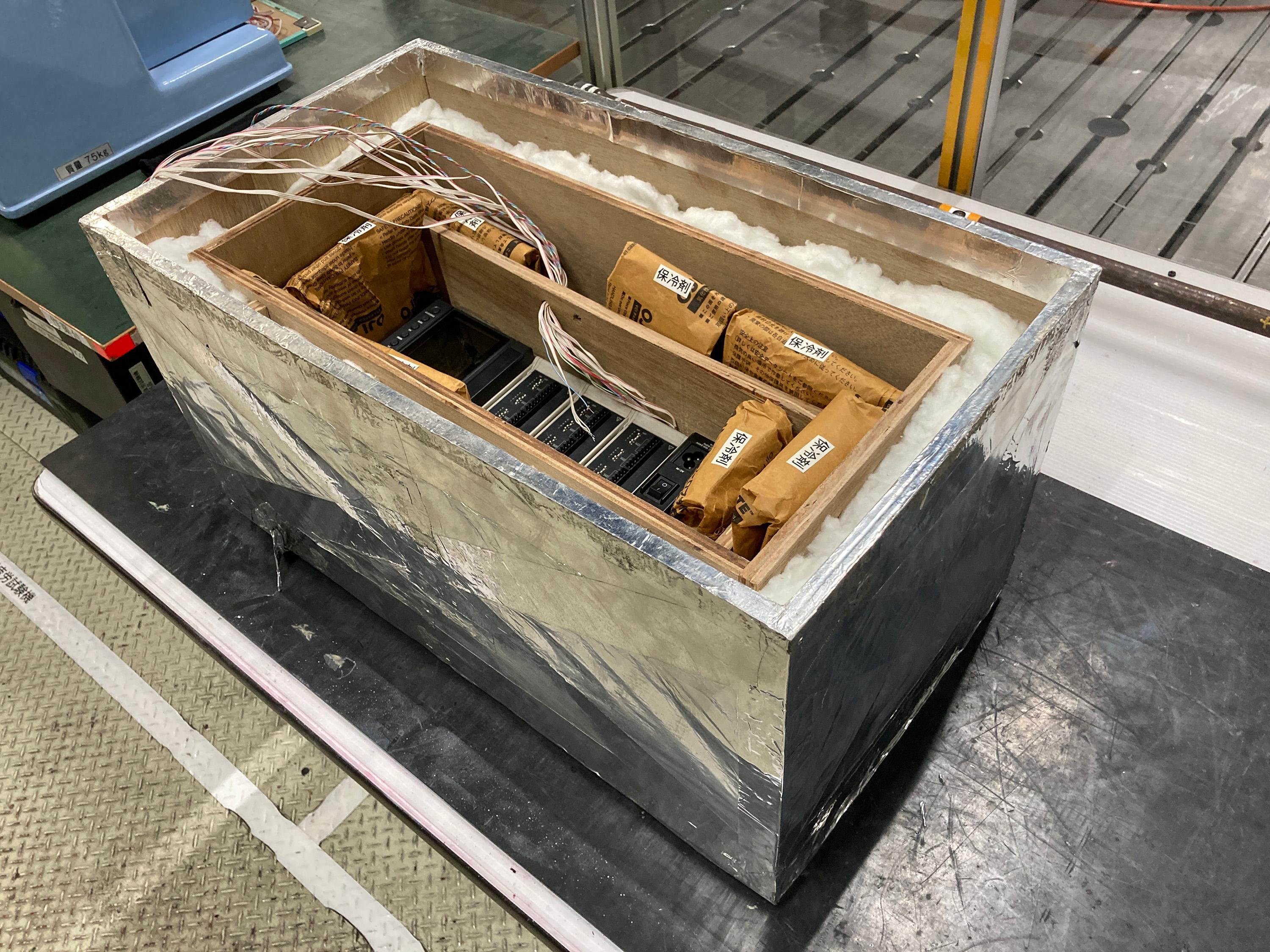
パラリンピック選手の競技用義足開発も
岡田が行ってきた「ひずみゲージの匠」としての仕事には、アスリートの支援もある。トヨタ自動車所属のパラ陸上競技のアスリートとして、2016年のリオ・パラリンピックの400mリレー(100m×4)で銅メダルを獲得した短距離走のスペシャリスト、佐藤圭太選手。2017年に始まった彼の競技用義足の開発だ。
「佐藤選手はそれまで市販の義足を競技用に流用していたのですが、耐久性に問題がありました。そこで佐藤選手の競技用義足を開発する『チーム佐藤』が社内で結成されたのです」
だが、生技管理部の統括でスタートしたこのプロジェクトに義足づくりの知見はなく、ゼロからの開発だったという。そのため、2017年の年末に最初の競技用義足が完成したものの、初試走で、それもジョギングを20m行った段階で壊れてしまったという。
「この開発に当初、私たち車体製造技術部は参画していなかったのですが、2018年にチームから協力要請があり、開発に加わることになりました」
岡田たち車体製造技術部に課せられたミッションは、走行時に義足にかかる応力の正確な把握。そして強度試験による義足の確実な強度の保証だった。
そこで岡田は、ひずみゲージをはじめ各種センサーを義足に取り付け、佐藤選手に試走してもらい、自らも並走しながらデータを取った。開発した義足の疲労試験も行った。
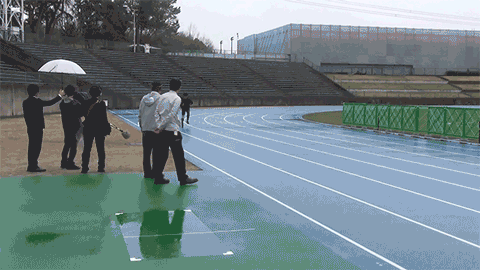
「メンバーからは『100m走のアスリートと並走するなんて無茶だ。ついていけるわけがないし、センサーの電線も切られるぞ』と笑われましたが、それはもちろん想定済み。それでも、切れるまでデータが取れればいいと思ってやったんです」と岡田は笑う。
岡田はこうして得られたさまざまなデータを、義肢装具士も加わった義足の製造チームにフィードバック。このクルマづくりの技術とノウハウを結集した結果、最終的にはチームが目標としていた、より速く走れて、しかも3年間・36万歩以上の耐久性を持つ競技用義足が完成した。
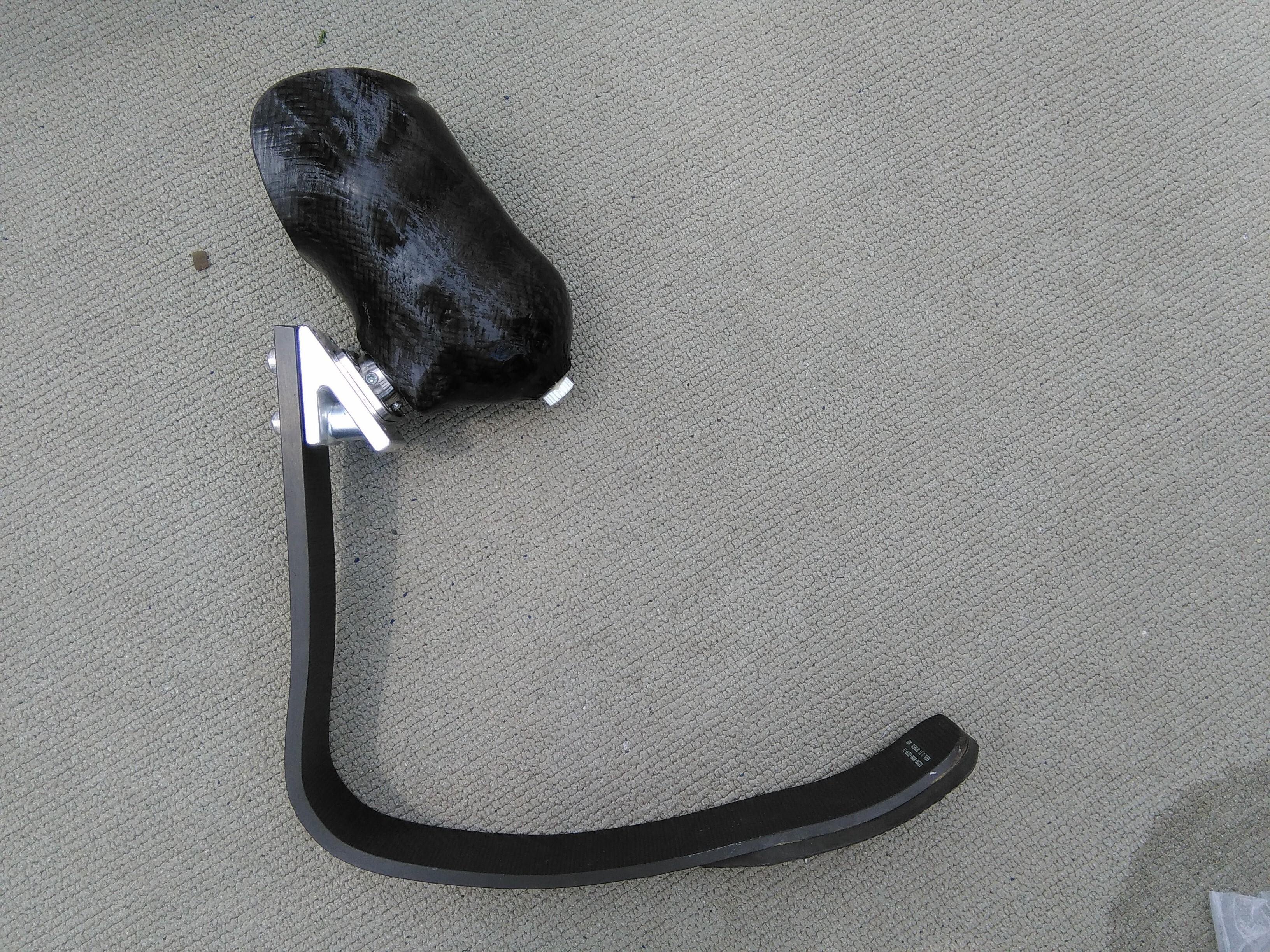
「佐藤選手からは『走りやすい』との評価を頂きましたし、100mのタイムは0.21秒向上したそうです。また、このトヨタ流のモノづくりに義肢装具士さんが感動して、トヨタ車を購入してくださったと聞いています」
この義足の開発で、岡田は設計、機械加工、木型、樹脂成型、カーボン成型、空力解析など、日常の業務では関わることのないさまざまな分野の「匠」と仕事をした。この経験は貴重で、自身の価値観や思考が変わるきっかけになったという。
「東京2020パラリンピックの仕事でのいちばんの財産はアスリート、つまりエンドユーザーの意見を直接聞きながら仕事を進める経験ができた、ということでしょうか。普段の業務はエンドユーザーと直接話す機会はありませんから。このプロジェクトで初めて『お客様目線とは何か』を体感することができました」
第一線に立ちつつ、後継者を育てる
そんな岡田が今、最も力を入れて取り組んでいるのが後継者の育成、そして自身のスキルアップだ。
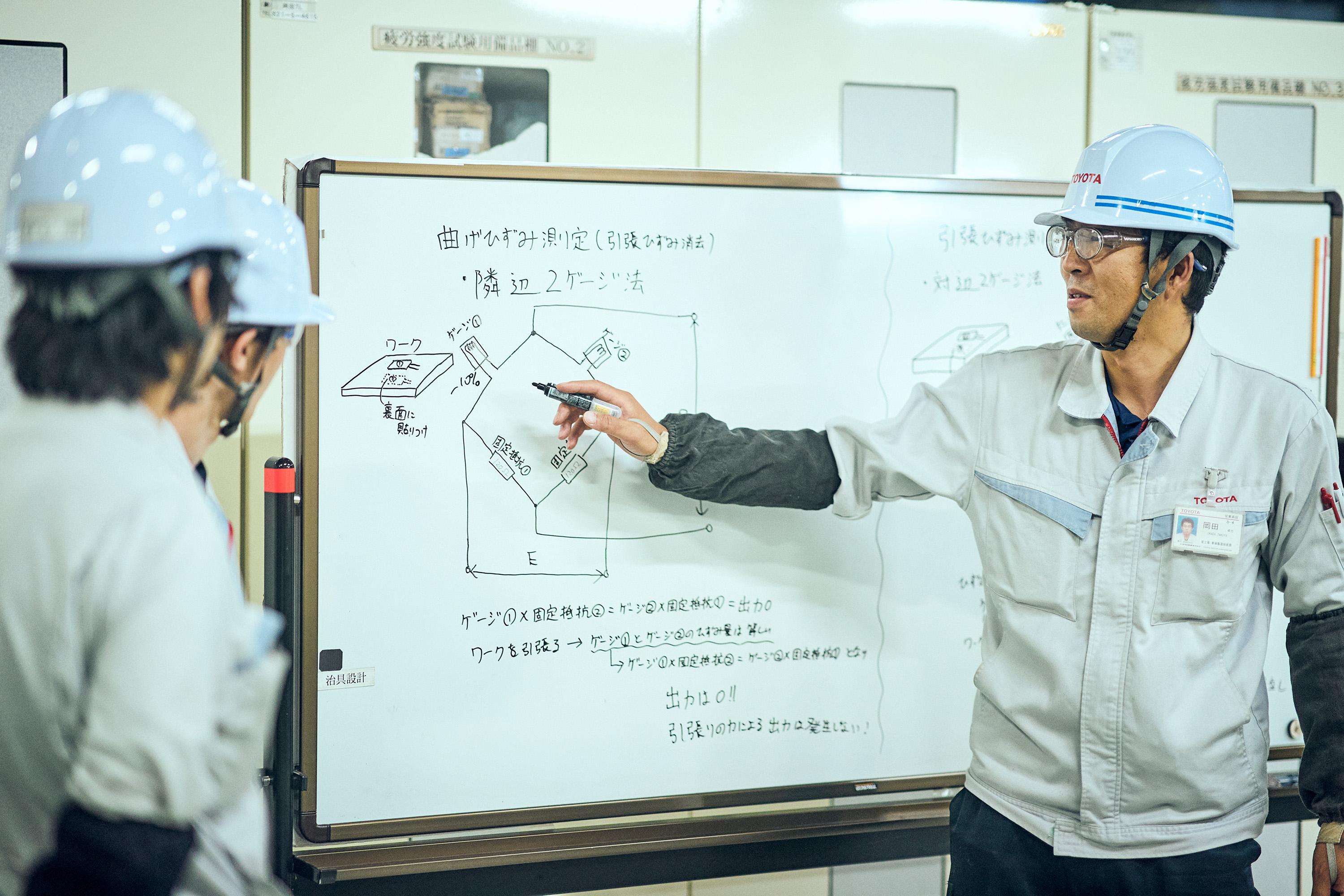
「今ふたりの後輩がいるのですが、いずれも20代の若手。毎日、正しい測定のやり方を講義していますが、教えるときにいちばん大切にしているのは、測定の原理や原則を理解してもらうこと。測定作業の手順を教えるのは、その後。彼らの成長は目覚ましく、新しい機器でも、どう使えばいいのか、自ら考えて工夫できるようになっています」
自身だけが「匠」や「職人」と言われている状況ではまだまだ。後輩たちがそう呼ばれるまで、育成に力を入れたい。とはいえ、自分自身もまだ30代後半。この先も現場で第一線に立って、エンジニアとして挑戦を続けたいという。
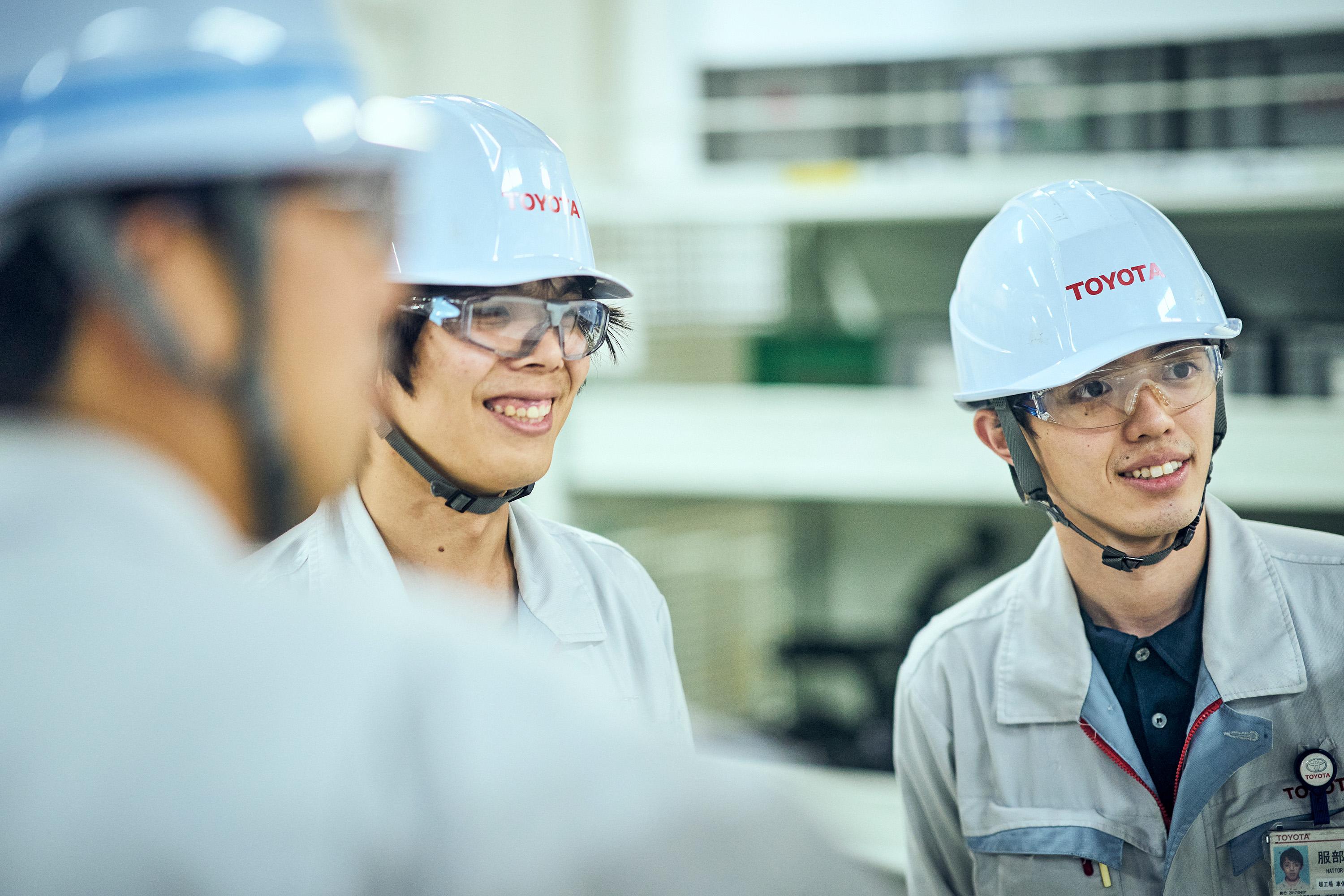
「計測の世界は日進月歩。ネットや文献で新しい計測機器や、計測の対象である新素材などについて勉強しています。自分自身、もっと進化したいと思っていますし、私の知見がたくさんの方々のお役に立つとうれしい。そう思っています」
若き「ひずみゲージの匠」岡田卓也。彼の「測る技術」を知り、社内のさまざまな部署から助けを求める声が高まっている。さらに塑性(そせい)加工学会など、社会からも岡田の仕事は注目されている。匠の活躍はまだ始まったばかりだ。