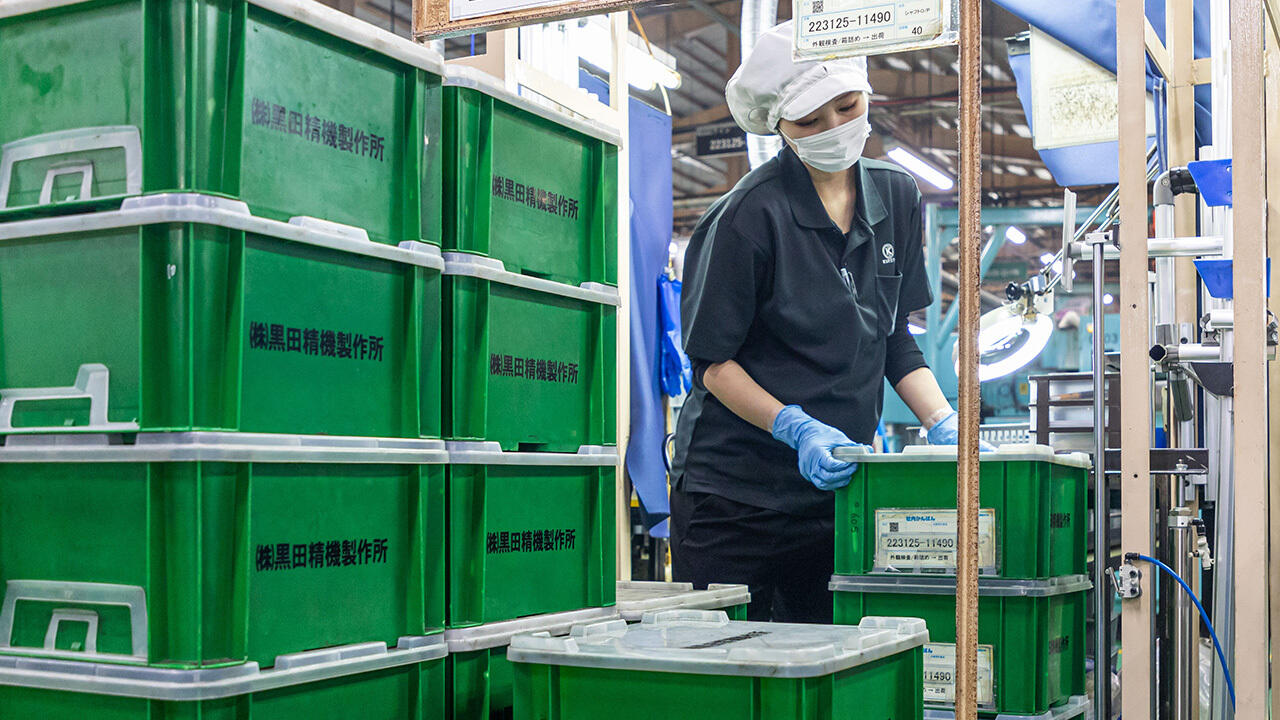
"We were aware of the problems; we just didn't know how to tackle them." How Toyota helped a supplier tackle some long-overlooked issues.
From “What to do?” to “We can do this!”
President Kuroda had previously taken part in TPS training, an experience that left him initially uneasy about the Group Collaborative Activities.
President Kuroda, Kurota Seiki-Seisakusho
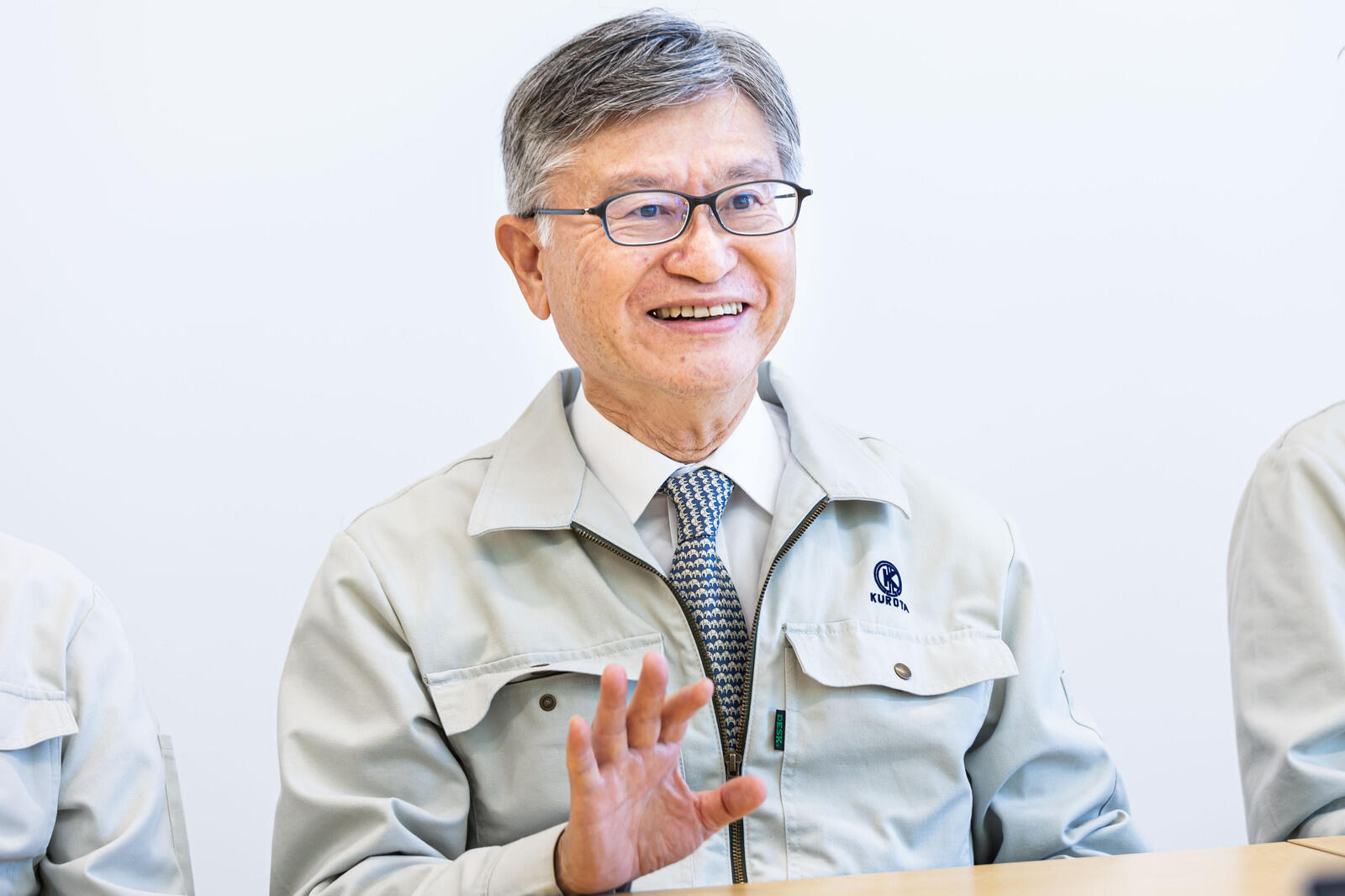
Back in the day, Toyota Production System workshops were—how can I put this—rather onerous… The improvements bring amazing benefits, but we got a glimpse of what it takes to get there…
When I heard that Toyota would be instructing us on TPS, I couldn’t help but think, “What are we going to do?”
This time around, however, that wasn’t the case at all. The staff from Toyota and Aisin really worked with our employees to make improvements. Times have changed.
Unfortunately, in the past, we weren’t able to keep things going by ourselves after the Aisin staff left. It was short-lived.
This time was different. Both Toyota and Aisin came down to our level to understand our situation and worked together with us to figure out how we could boost productivity.
Yunosuke Kariya, who heads the Supplier Structure Improvement Support Department within Aisin’s Group Procurement Division, also senses that things have changed. “It feels like the distances between us, including Toyota, have disappeared.”
Kariya, Aisin
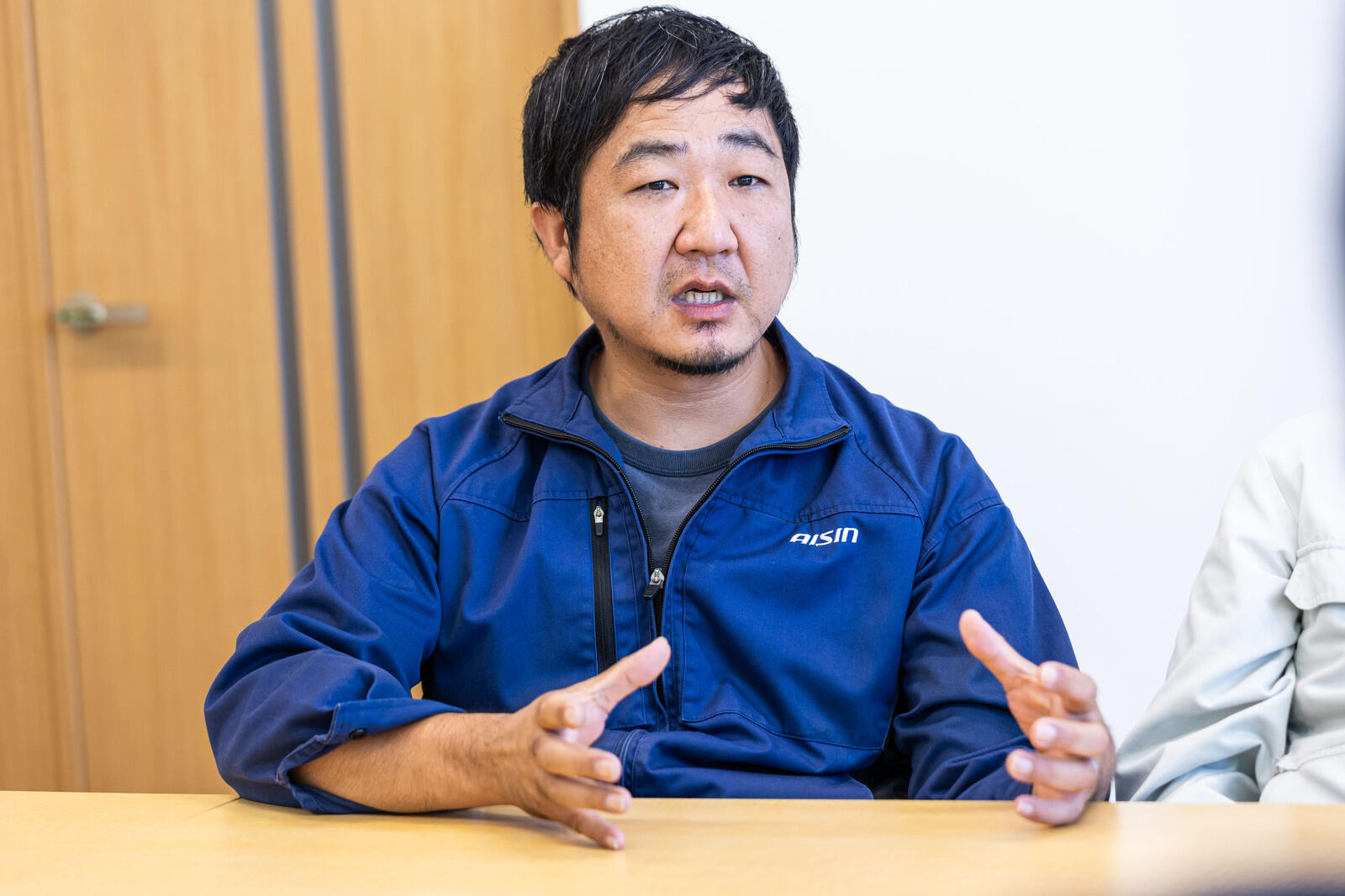
In the past, we were just taking stationary observations, telling them, “Please do this” or “Please get us that data.”
We came to realize that we needed to do things differently, and it was only when we changed our approach by bridging the gap and getting more involved that our suppliers began reaching out to us.
They began to thank us and say, “It was tough, but we’re glad we did it.” In the process, I feel that we have changed as well.
According to Operating Officer Takahiro Kuroda, these activities have given genba employees greater confidence.
Takahiro Kuroda, Operating Officer, Kurota Seiki-Seisakusho
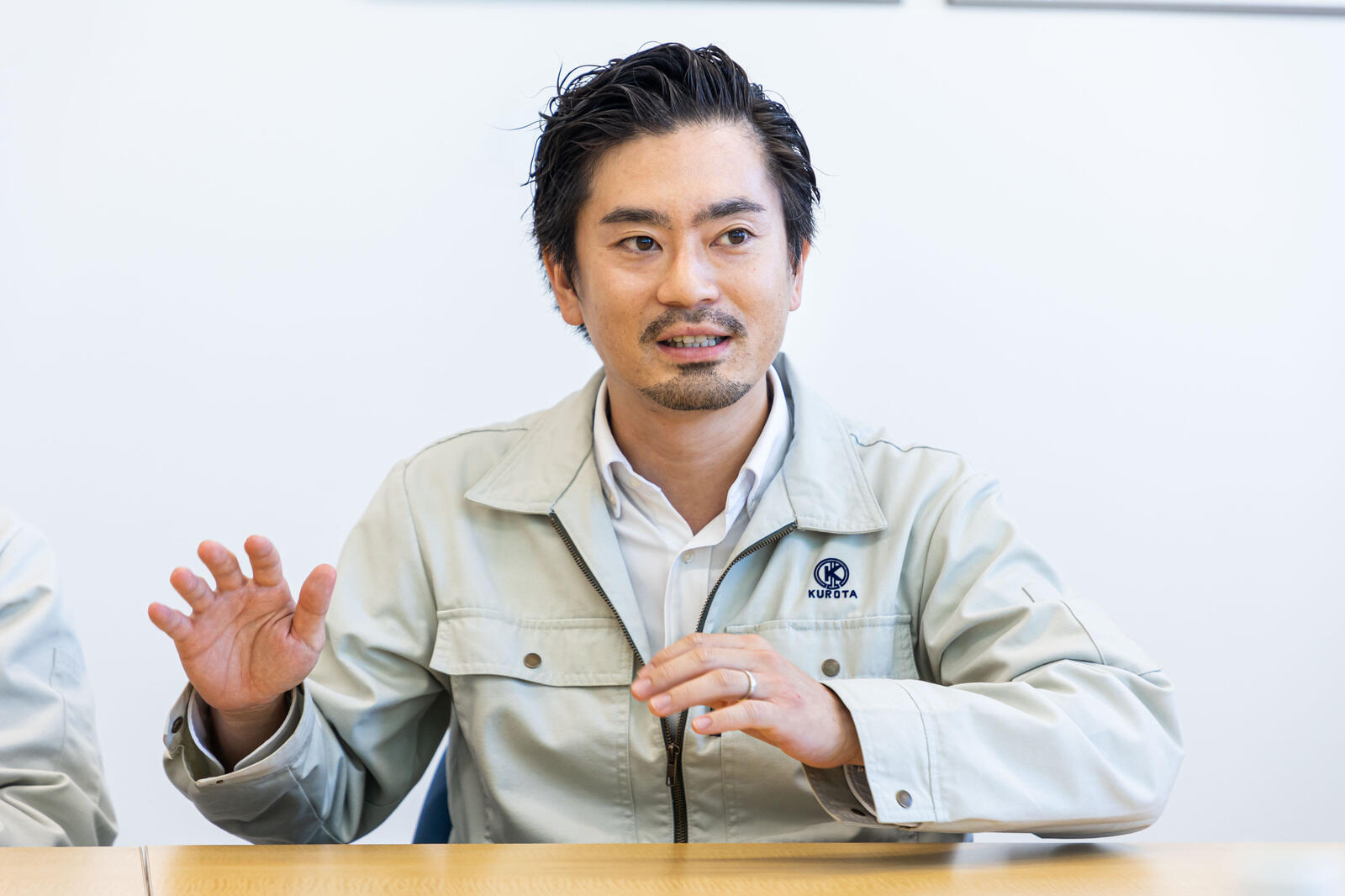
Whenever you set out to do something big, it takes a lot of effort to get the ball rolling.
In this case, receiving that firm push from Toyota made us feel like, “It’s happening! We can do this!”
Expertise gained through the collaborative activities is also being shared via the Yoro Factory’s training area for new employees, apprentices, and trainees from overseas plants, including Thailand and Mexico.
“The mentality of ‘we can change things,’ with each person thinking of ways to make things better—I believe that’s what drives kaizen,” emphasized Operating Officer Kuroda.
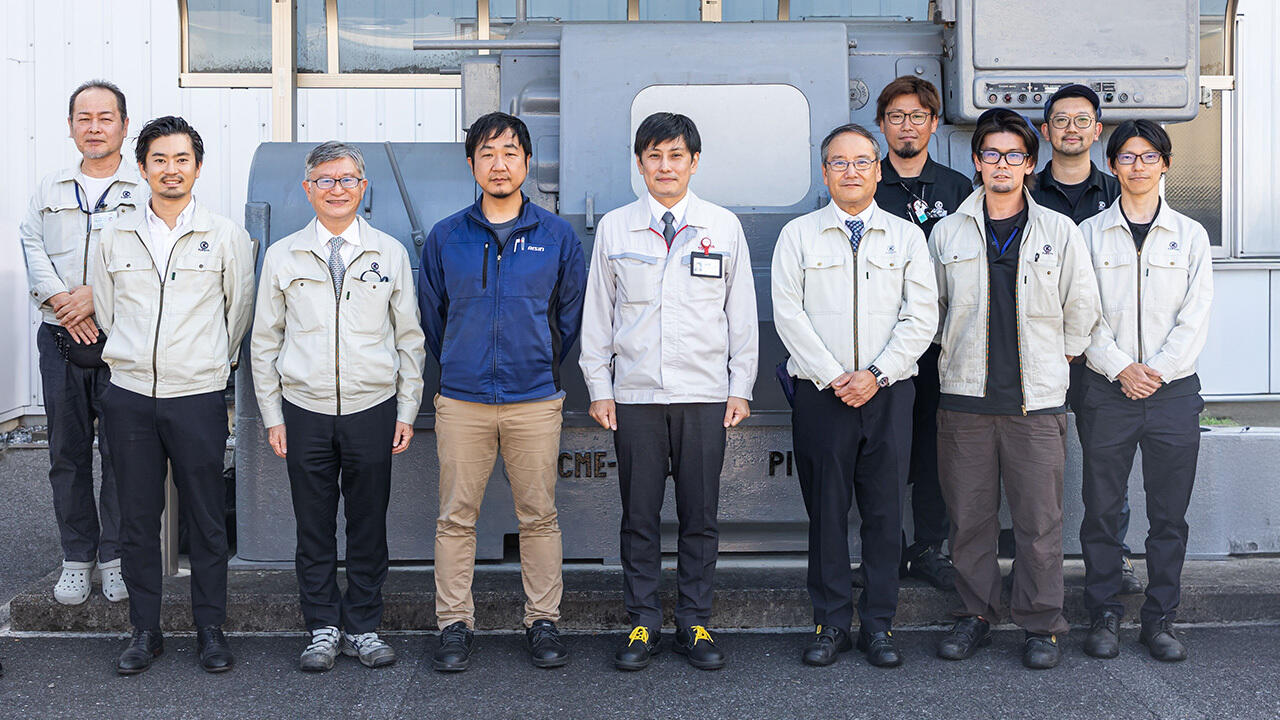
Seeing eye to eye
Over the past two articles, we have shared just a few examples of how Toyota pursues improvement by working together with Tier 1 (Hayashi Telempu and Aisin) and Tier 2 suppliers (Umemura Industry and Kurota Seiki-Seisakusho).
In both cases, the companies started out uncertain about embarking on improvement efforts with Toyota.
However, as Toyota’s staff engaged them “face-to-face” (President Koji Umemura, Umemura Industry), on “our level” (President Kuroda), these anxieties were soon dispelled. Indeed, as results manifested, concerns were replaced by confidence.
In the words of Chairman Akio Toyoda, the companies that participated in Group Collaborative Activities did so “from an equal standpoint,” leading to relationships focused on working together to tackle the challenges before them.