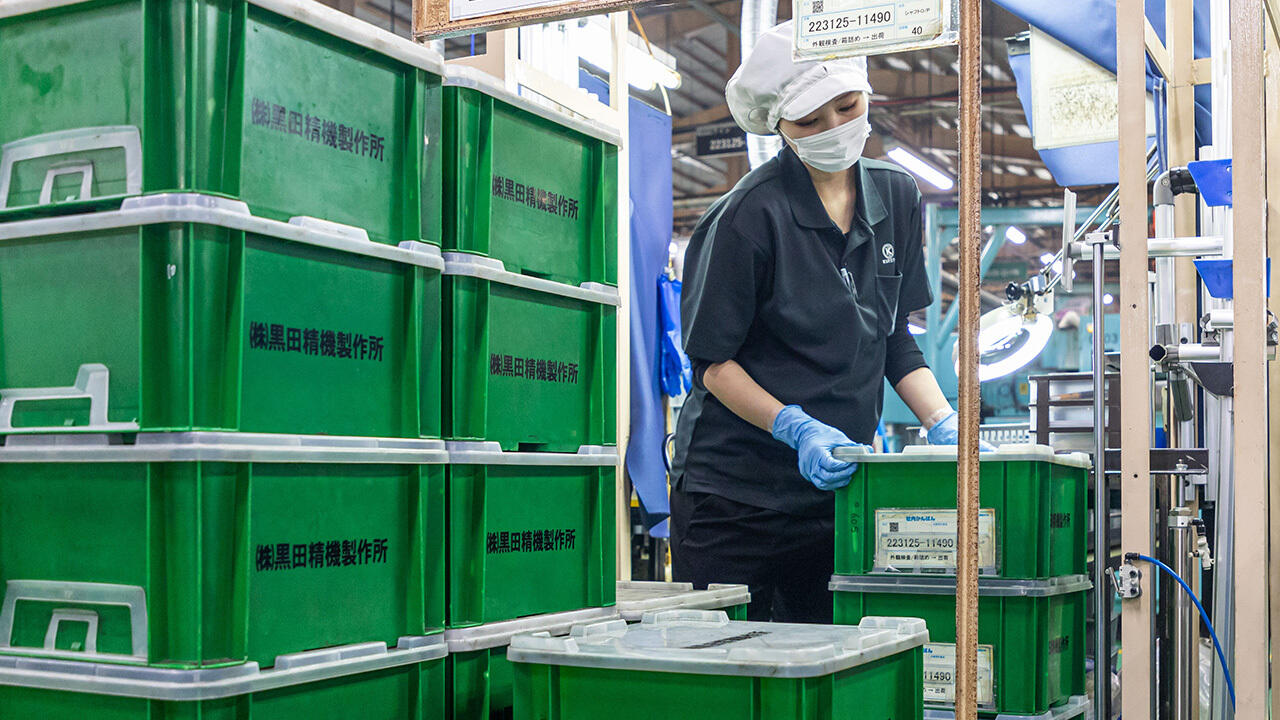
"We were aware of the problems; we just didn't know how to tackle them." How Toyota helped a supplier tackle some long-overlooked issues.
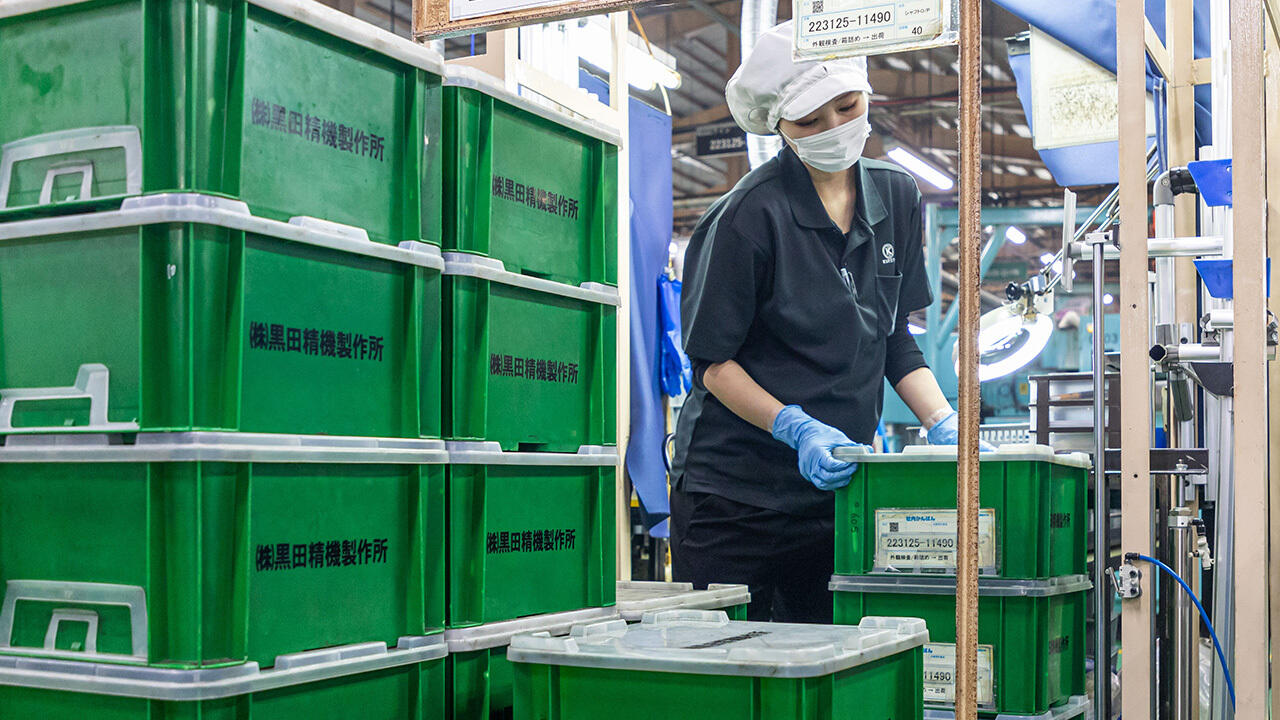
“The staff from Toyota and Aisin worked with our employees to make improvements,” says a smiling Toshihiro Kuroda, president of Nagoya-based Kurota Seiki-Seisakusho Co., Ltd. “Times have changed.”
This series explores the relationship between Toyota and its suppliers. In our second article, we introduced the Group Collaborative Activities, through which Toyota works with its primary suppliers (Tier 1) to solve issues faced by secondary suppliers (Tier 2). We shared the case of two companies that participated in these efforts, Hayashi Telempu (Tier 1) and Umemura Industry (Tier 2), both engaged in making car interior parts.
For this third article, we look at another Group Collaboration example that shows how Toyota, Tier 1, and Tier 2 companies tackle known problems that have been neglected for many years.
Taking logistics improvements off the back burner
Kurota Seiki-Seisakusho is a Tier 1 supplier for Aisin, producing mainly engine and brake parts. The company has six facilities in Japan and abroad; among them, the Yoro Factory (Gifu Prefecture) took part in Group Collaborative Activities from March to November 2023.
One of the site’s issues was its logistics operations within the factory.
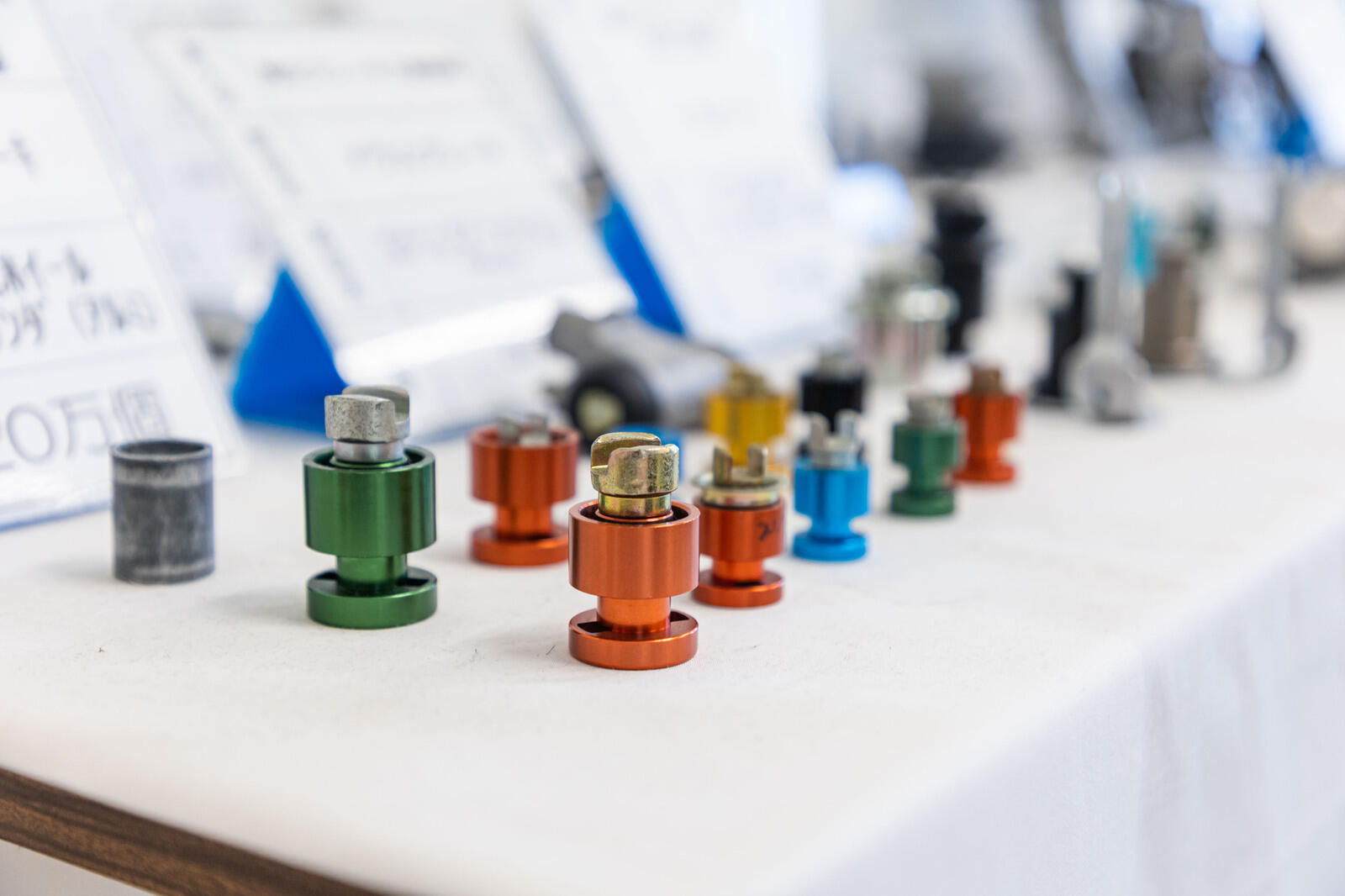
Since first opening its doors some 40 years ago, the Yoro Factory has continued to increase production, with three plants now in operation.
Each plant has its own yard, yet the focus on production meant that logistics arrangements—including the planning of flow lines for supplying parts and shipping finished products—had not been updated.
Part of Toyota’s kaizen efforts is the 4S approach: Sort, Set in Order, Shine, and Standardize. The second of these, set in order, can be further broken down into the “five sets” that make it easier to implement. Among them is creating “set paths,” a task that the Yoro Factory continued to put off.
For the record, the other five sets are as follows:
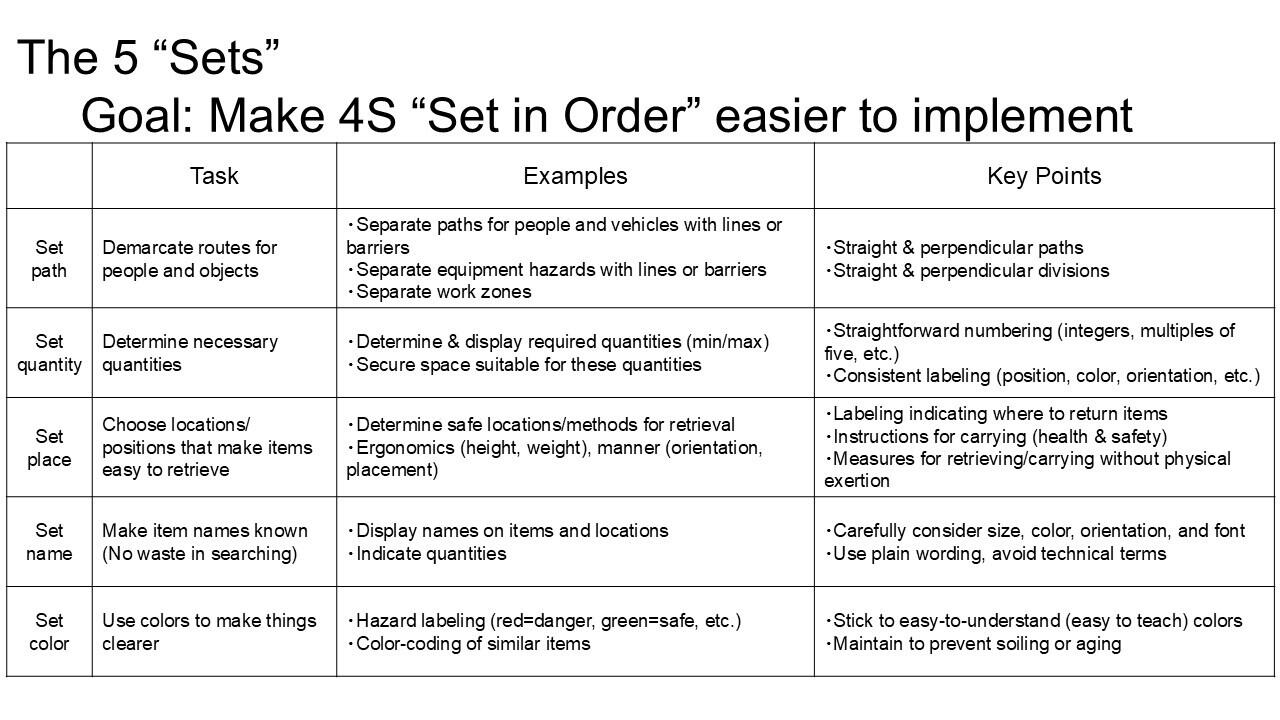
At the Yoro Factory, logistics operations had not been standardized to ensure safety and eliminate waste. In the yards, where inbound and outbound shipping functions were undifferentiated, task conflicts occurred and walking paths overlapped with forklift lanes.
Workers were aware of such problems, but the situation had persisted for so long that “we didn’t know how to go about making improvements.”
The Group Collaborative Activities focused on one particular trouble spot, the shared yard for inbound and outbound shipments, turning it into a dedicated dispatch zone. Just as in Toyota’s plants, lines were drawn on the floor to ensure safety by clearly separating work areas for people and forklifts.
Creating safe and secure work environments is a top priority at Toyota, which likewise advised Kurota to put safety first.
The receiving functions were consolidated in a separate inbound shipment yard. As a result, goods now flow in one direction—materials are received and supplied to the plant, then finished products are collected and shipped out—eliminating clashes.
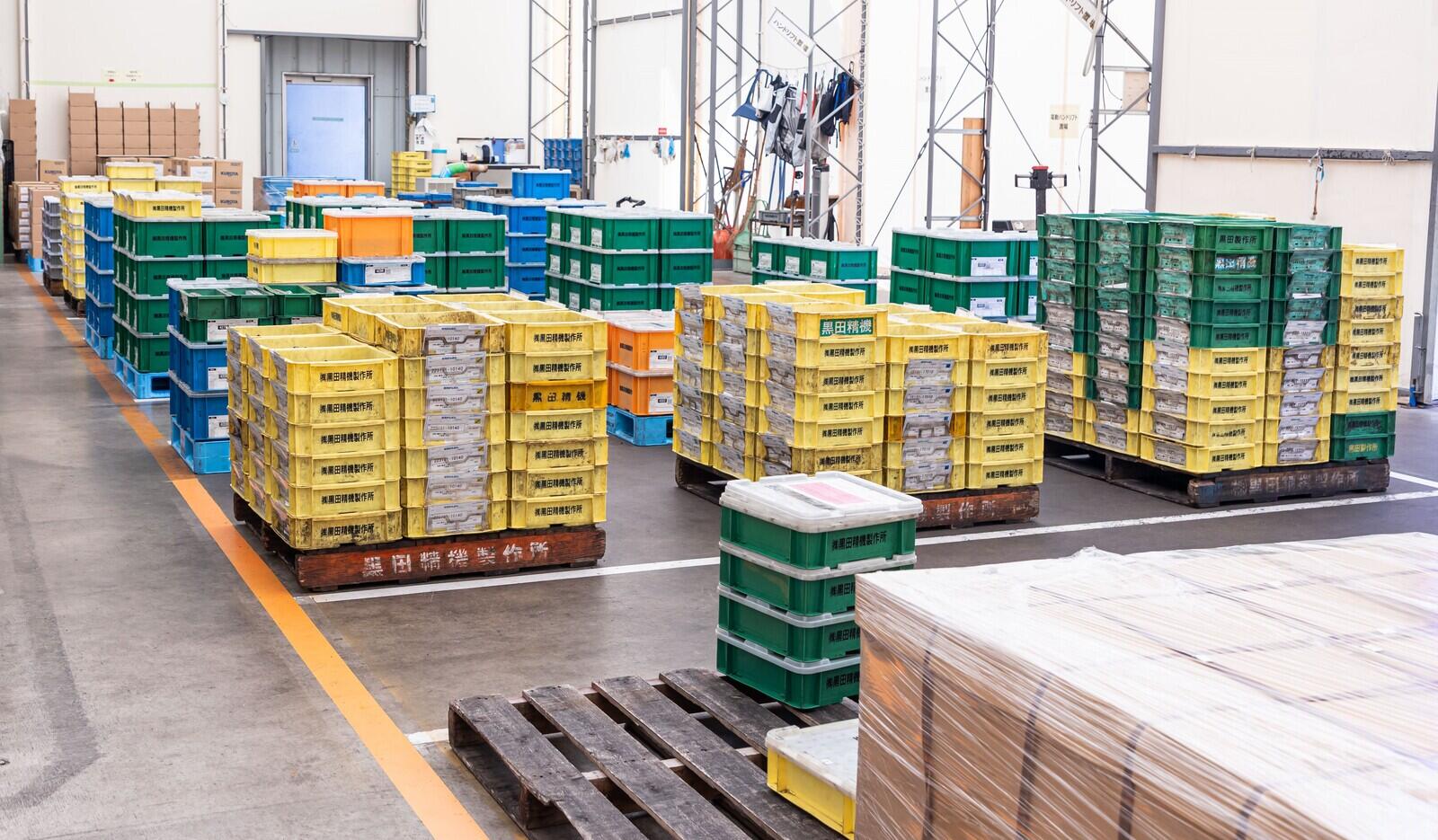
Moving the receiving function elsewhere also freed up space for the forklifts to maneuver more easily. Outbound items are divided into lanes for each shipment, earning praise from downstream logistics drivers for “making our work easier.”
Progress management made easy with kanban card boxes
To help establish efficient on-site logistics, the team selected Plant 1, which has the largest shipment volumes and longest travel distances of the three Yoro plants, to serve as a model.
To set up the shortest pickup routes, the team gathered basic information on shipped volumes and appropriate placements for finished products and kayoibako*. Staff from Toyota and Aisin were involved in identifying elemental tasks, such as loading kayoibako onto carts or transferring finished parts onto shipping pallets, measuring the time required to move to and complete each one.
*Plastic containers for safely and efficiently transporting parts and products between stations. Inserts can be changed according to the needs of various production genba and items being carried.
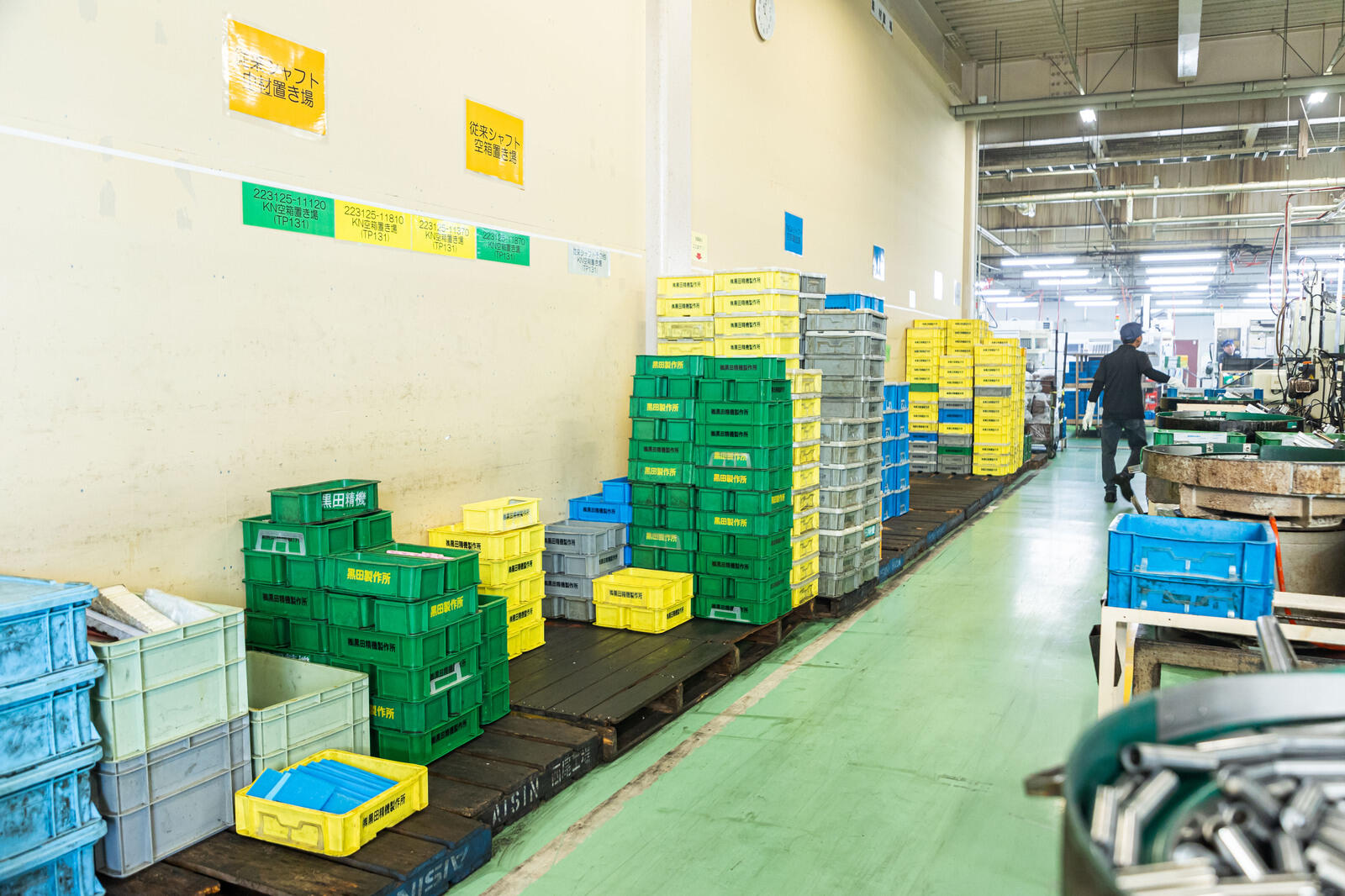
Goods are moved around using Toyota’s mikara (loaded-empty) system.
Here is how it works: a worker departs from the dispatch yard, picking up empty containers on their way to collect finished parts ready for shipping. At the collection point, they swap the empty containers for loaded ones containing parts, then return to the yard.
Before the collaborative improvements, finished parts collection was being handled by multiple people, at times causing doubling up and wasteful transport of only empty containers. These problems were resolved by having just one person doing the collection work.
In addition, kanban card boxes were installed in the outbound yard. The collection schedule can now be checked at a glance, making it easier for supervisors to manage progress. Previously, when the task relied on individual instinct and intuition, workers thought only about getting finished parts to the yard; the new approach also considers downstream processes, transporting “only what is needed, when it is needed, and in the amount needed.”
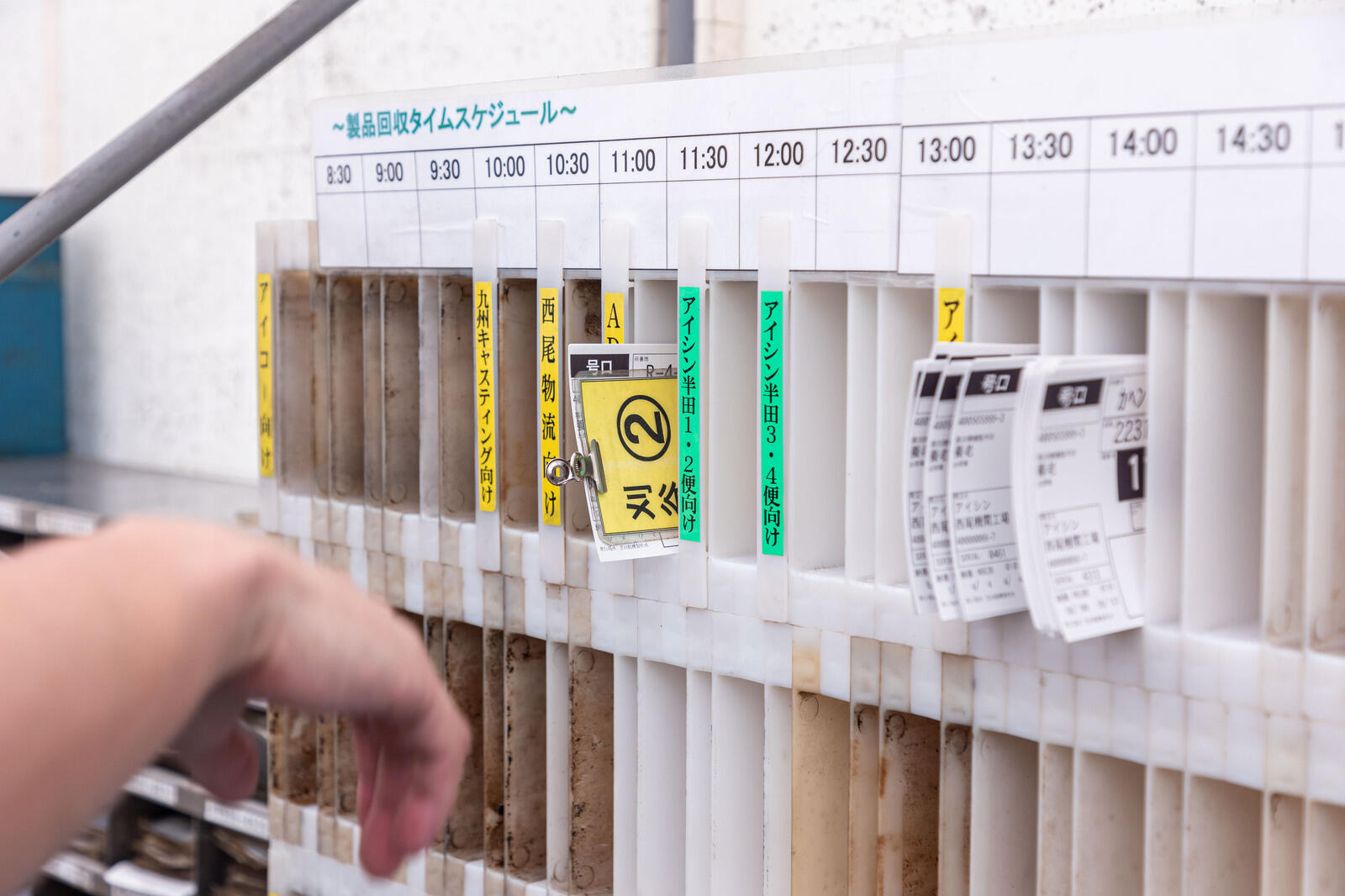
Such improvement efforts succeeded in freeing up two members from the Yoro Factory’s logistics team, helping boost productivity.
Workers are keen to keep the kaizen going. “We don’t want to waste everything we have learned over the past year.”