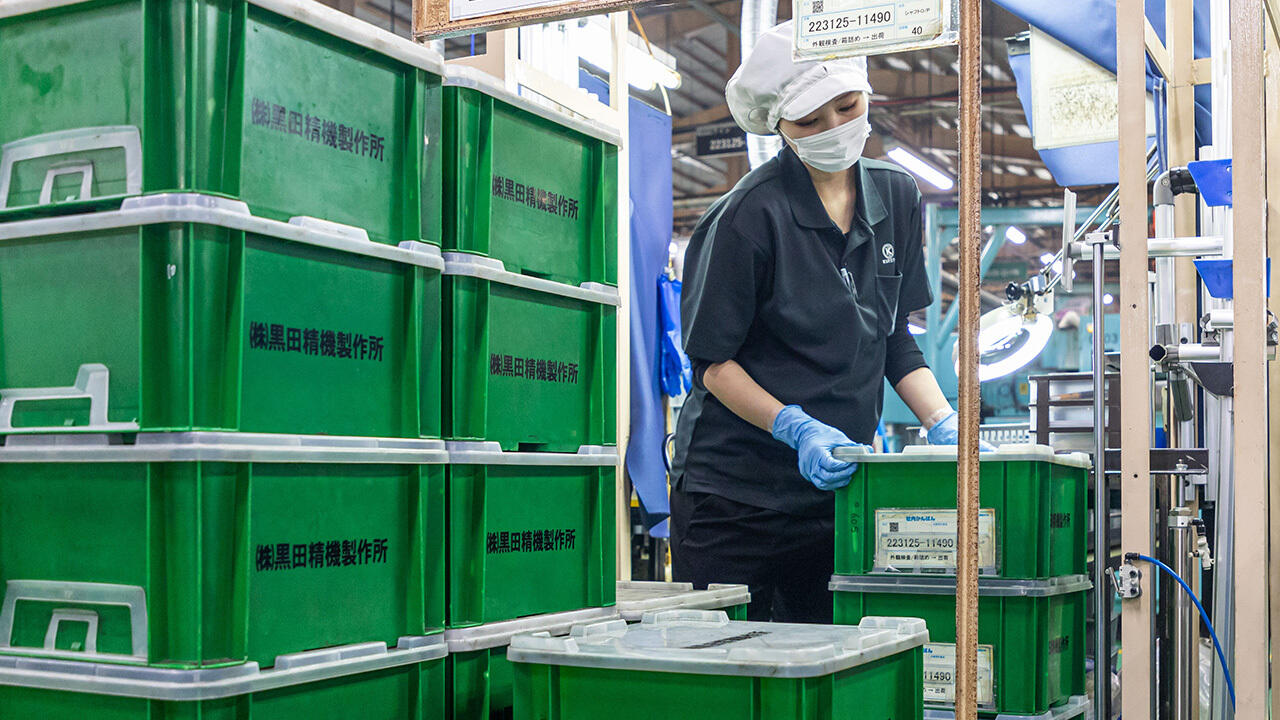
"We were aware of the problems; we just didn't know how to tackle them." How Toyota helped a supplier tackle some long-overlooked issues.
A better work environment for all
Beyond logistics, karakuri were used to make improvements in the inspection genba, as shown in the video below:
Containers filled with inspected products, like those in the video, weigh around 11 kilograms. Kurota’s inspection team includes people with various levels of physical strength, especially among women, and carrying these containers was an onerous task.
The improvements added a pulley-based karakuri* that allows workers to inspect parts in a set position, saving them from the job of hauling heavy containers.
*Tools and mechanisms that use gravity, levers, and other mechanical solutions to boost efficiency or make tasks easier without needing electricity or high-powered motors. Familiar examples include pedal-operated bin lids and self-opening umbrellas. In addition to curbing costs, karakuri also saves energy.
This karakuri was created by Kurota and Toyota’s Global Production Center (GPC). When the collaboration began, however, none of Kurota’s staff had any experience making karakuri.
To learn about such devices, Kurota members visited the Karakuri Ideas Gallery at Toyota’s Motomachi Plant (Toyota City, Aichi). They also participated in a “training camp” with GPC, learning basics such as welding and assembly while developing their solution.
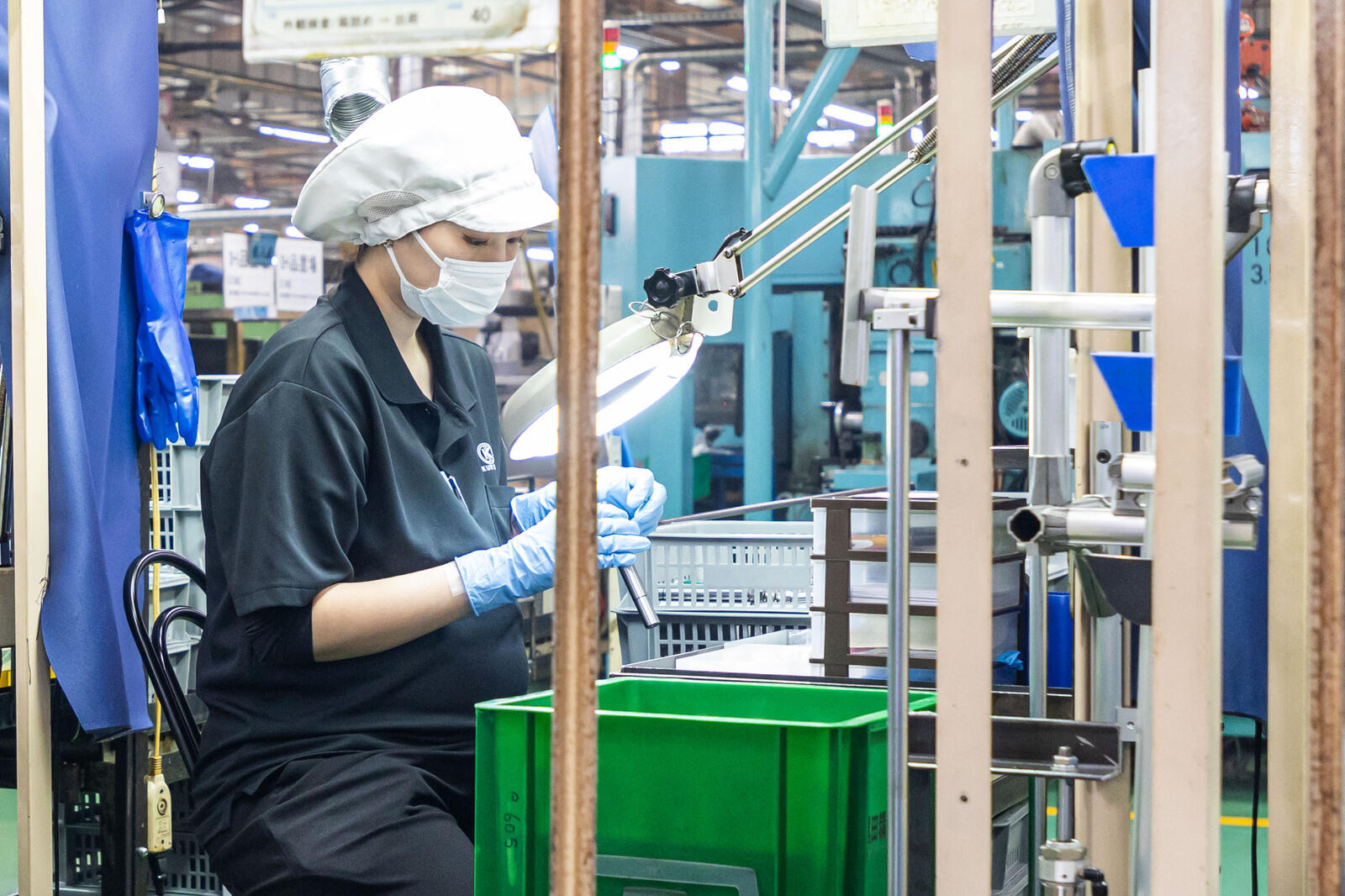
Thanks to the karakuri, the woman pictured above can continue to work comfortably even while pregnant. “With the way things were before, she may well have said, ‘I can’t keep working while pregnant,’ or asked to be moved to another role or company,” says President Kuroda with a smile. “It makes me really happy that people can choose to continue working right up until they give birth.”
A completely novel idea
In some cases, collaborative efforts were even able to fix broken equipment.
One such machine was the centrifugal separator, which removes metal shavings (created when processing metals) from the cutting oil so that it can be recycled.
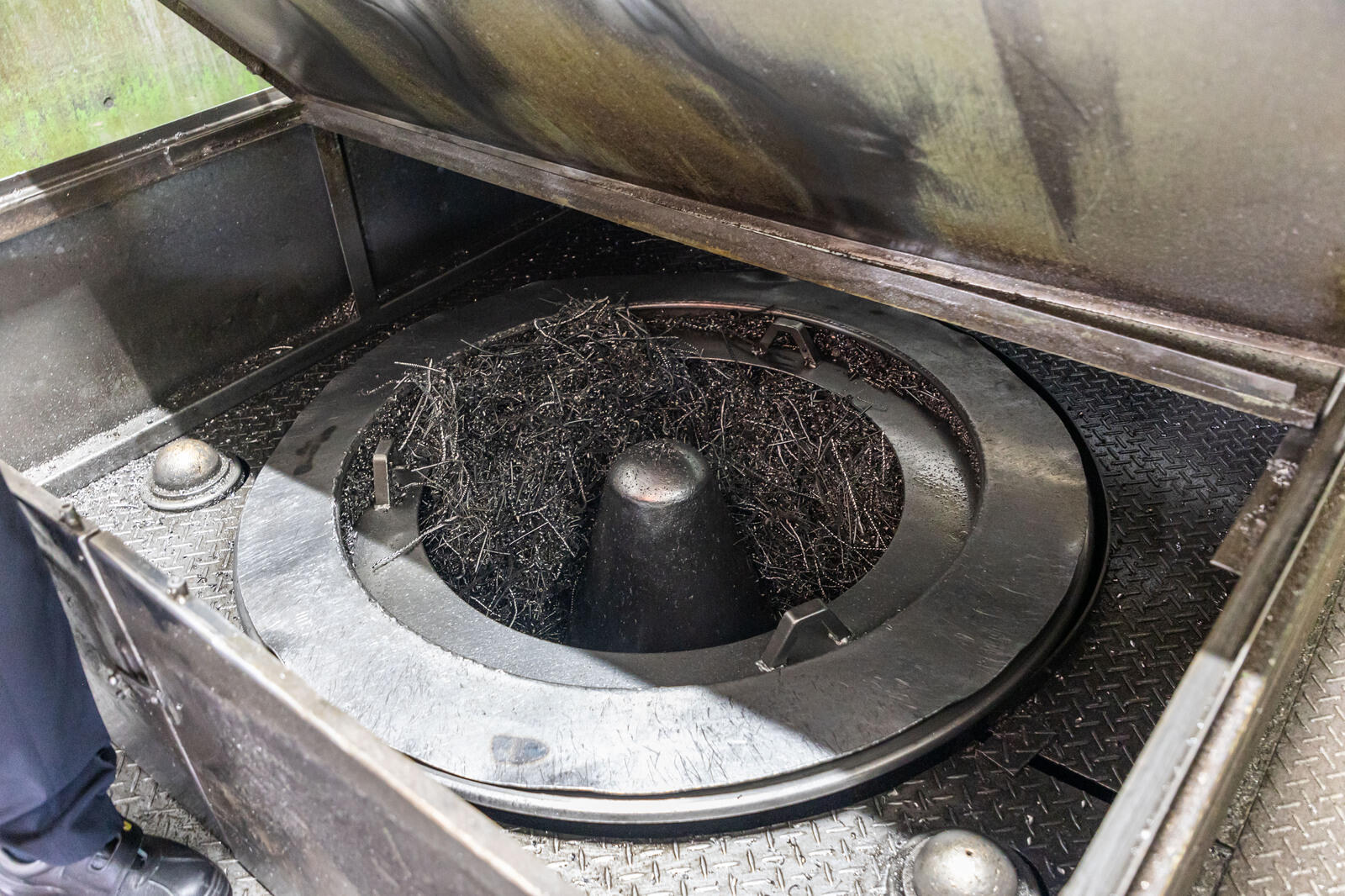
The machine’s brake was faulty, but the original manufacturer had closed down, and Kurota lacked the knowledge to fix it. Employing an outside repairer would cost 2 million yen, a considerable sum.
Instead, Kurota’s staff approached GPC. An investigation of the causes revealed that the brake pads which stopped the machine’s rotation were damaged and worn.
Since dismantling the machine for repairs would be incredibly labor-intensive, GPC came up with the idea of installing modified car brake pads. For the staff at Kurota, this was a completely novel approach.
After considering size and other factors, the team settled on RAV4 pads. With Kurota members helping to fabricate jigs and parts, the separator was brought back to life with minimal cost and time spent.
Kurota’s team has followed up with its own efforts to prevent repeat issues, requiring pads to be replaced every six months and even preparing a manual.
The logistics improvements and karakuri we have showcased are just a sample of what the Group Collaborative Activities achieved at Kurota. Operating Officer Norio Kawase, who helped oversee the efforts, says that a key element was working together with Toyota rather than receiving a one-way knowledge transfer.
Norio Kawase, Operating Officer, Kurota Seiki-Seisakusho
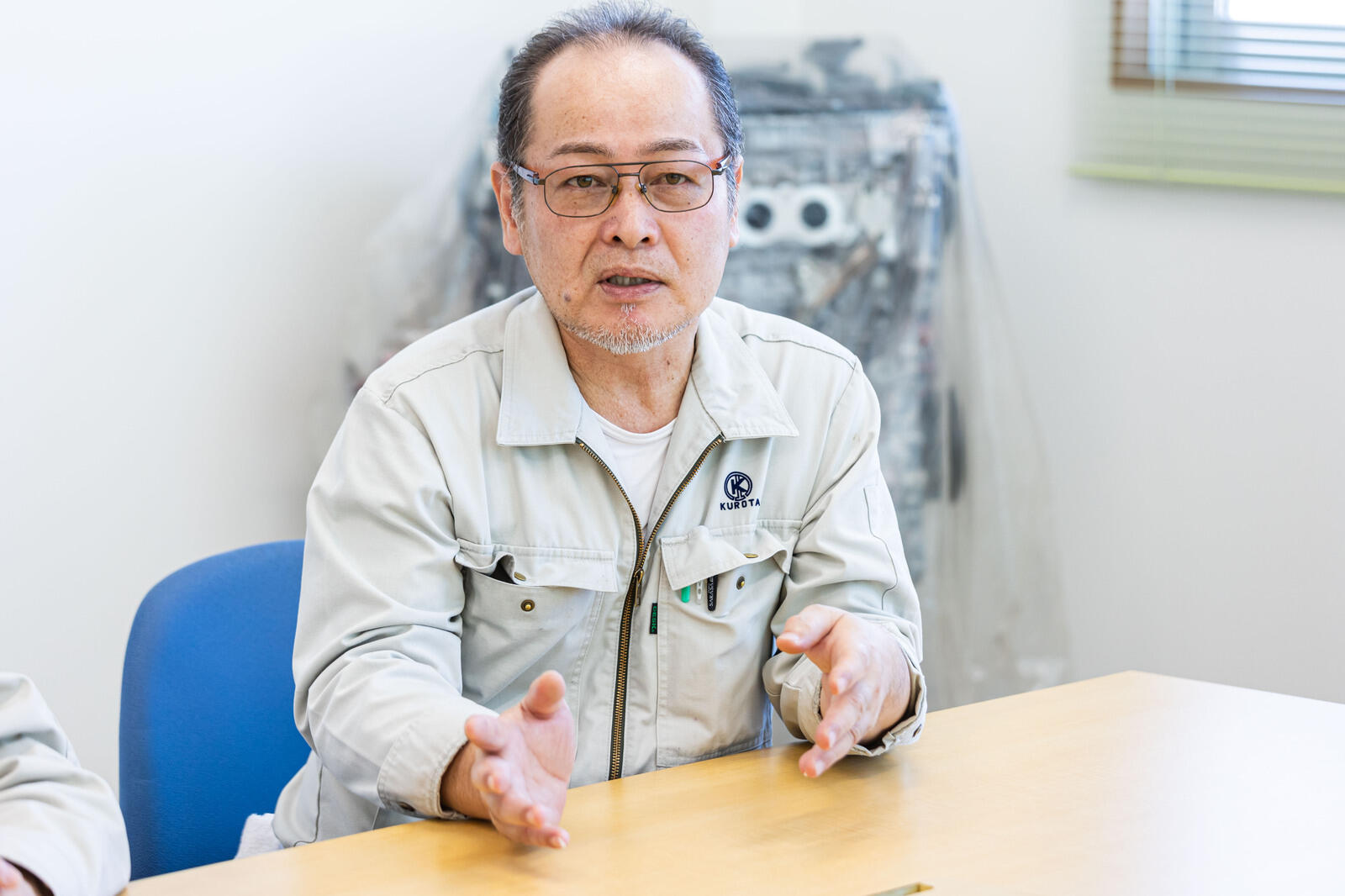
When undertaking improvements, the biggest annoyance for those on the ground is being told, “Do this,” like being given homework.
I don’t think that’s a great way to get things done. Instead, we actually received guidance in a very friendly way, and they taught us whatever we didn’t know.
The best part for me was that we became very close and really enjoyed tackling these challenges together.
We also developed a closer relationship with GPC, so now we can bring them our concerns and receive ideas for how to proceed.
The more we learned, the more our karakuri team enjoyed themselves, and things took shape. I think that’s how we were able to achieve what we did.