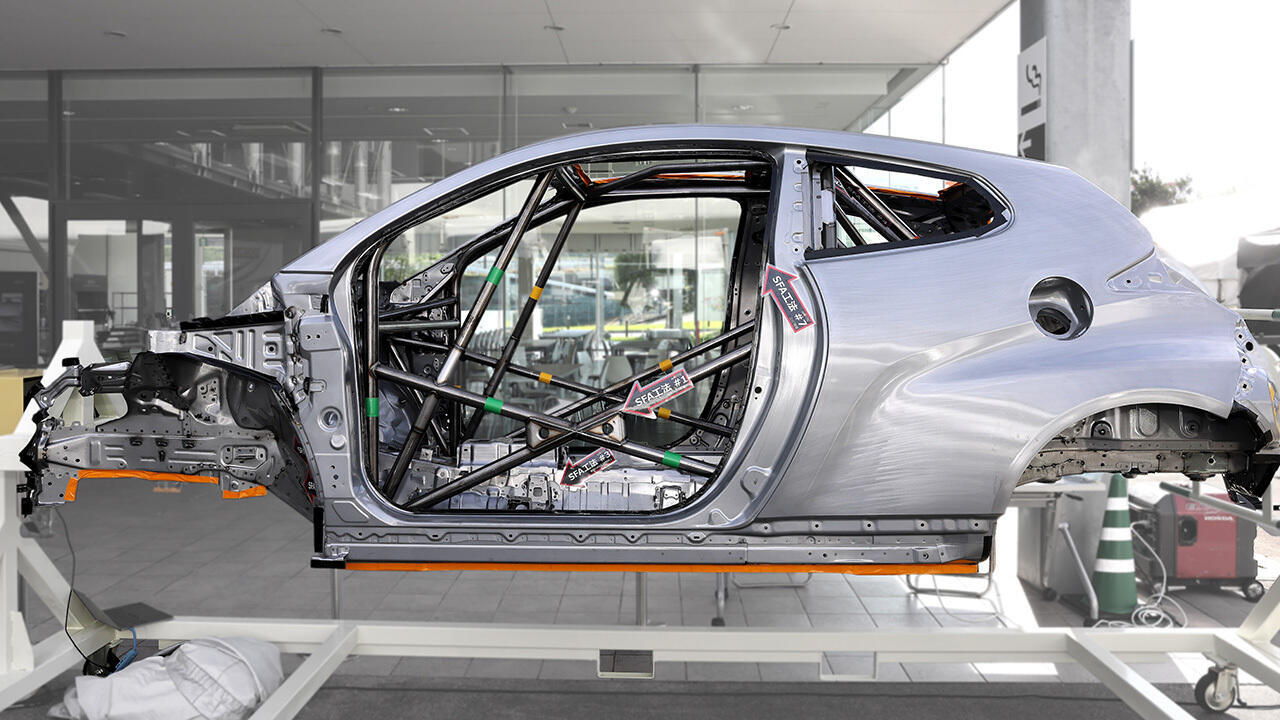
Toyota is tackling the challenges faced by motorsports and working to expand their reach. At a recent Super Taikyu event, the company unveiled a world-first welding technology.
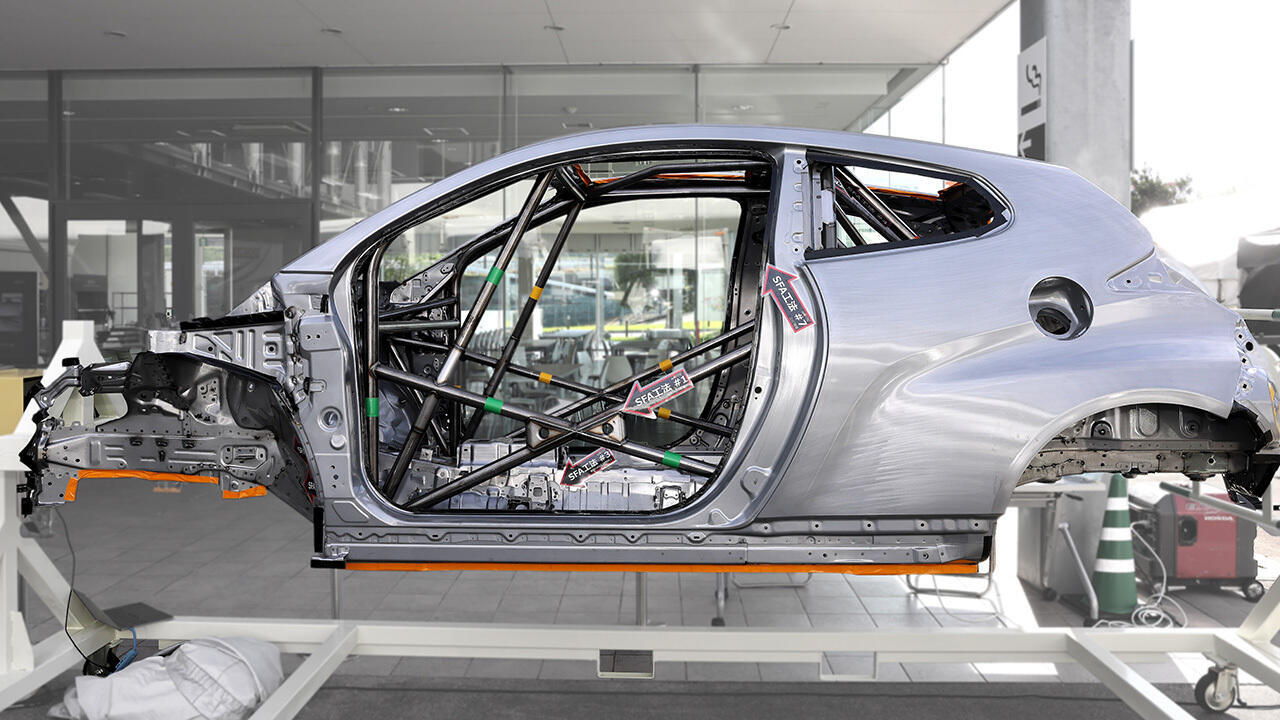
Hydrogen-powered engines, carbon-neutral fuel vehicles, direct automatic transmissions (DAT)—Toyota has used the racetrack to hone various new technologies that contribute to making ever-better cars.
These innovations also expand the options for production vehicles and help broaden motorsports' reach.
Now, Toyota has debuted another world-first technology, Sequence Freezing Arc-welding (SFA), which could make motorsports more sustainable.
SFA was unveiled at Round 5 of the 2024 ENEOS Super Taikyu Series Empowered by BRIDGESTONE, held at Suzuka Circuit (Mie Prefecture) on September 28 and 29. The technology was used for ROOKIE Racing’s #32 GR Yaris, competing in the ST-Q class.
Also on display at the venue was a roll cage assembled using that same SFA method.
Toyota Times investigated this new welding technology, which harnesses robotics to drastically reduce lead times.
A race against time
SFA’s development can be traced back to August 2023, when Chairman Akio Toyoda, aka Morizo, toured the TOYOTA GAZOO Racing World Rally Team (TGR-WRT) manufacturing genba in Finland. At the time, TGR-WRT was struggling with roll cage assembly on the body in white (the production stage when a car body frame and panels are put together prior to painting).
As the name suggests, roll cages are cage-like frames built into the bodies of racing vehicles to protect occupants in the event of a crash. The fitting of roll cages is strictly stipulated by competition rules.
Assembling the 50-odd pipes that make up a roll cage requires advanced welding skills. Typically, each piece is mounted onto the body by the hands of expert welders. This process takes between two to three weeks for a single vehicle, making it the most time-consuming part of putting together a racing car.
Such lead times mean that if a rally car was totaled during a crash, a replacement could not be made ready in time for the next race. Drawing on the capabilities of the Toyota Production System (TPS), the challenge was to assemble a body as quickly as possible.
The development process took around a year, led by GR Vehicle Development Division Project General Manager Atsushi Kawakita and Shota Shibata of the Robot Technology Dept. Robotics Div. at Yaskawa Electric, which manufactures industrial robots.
Project General Manager Kawakita, GR Vehicle Development Div.
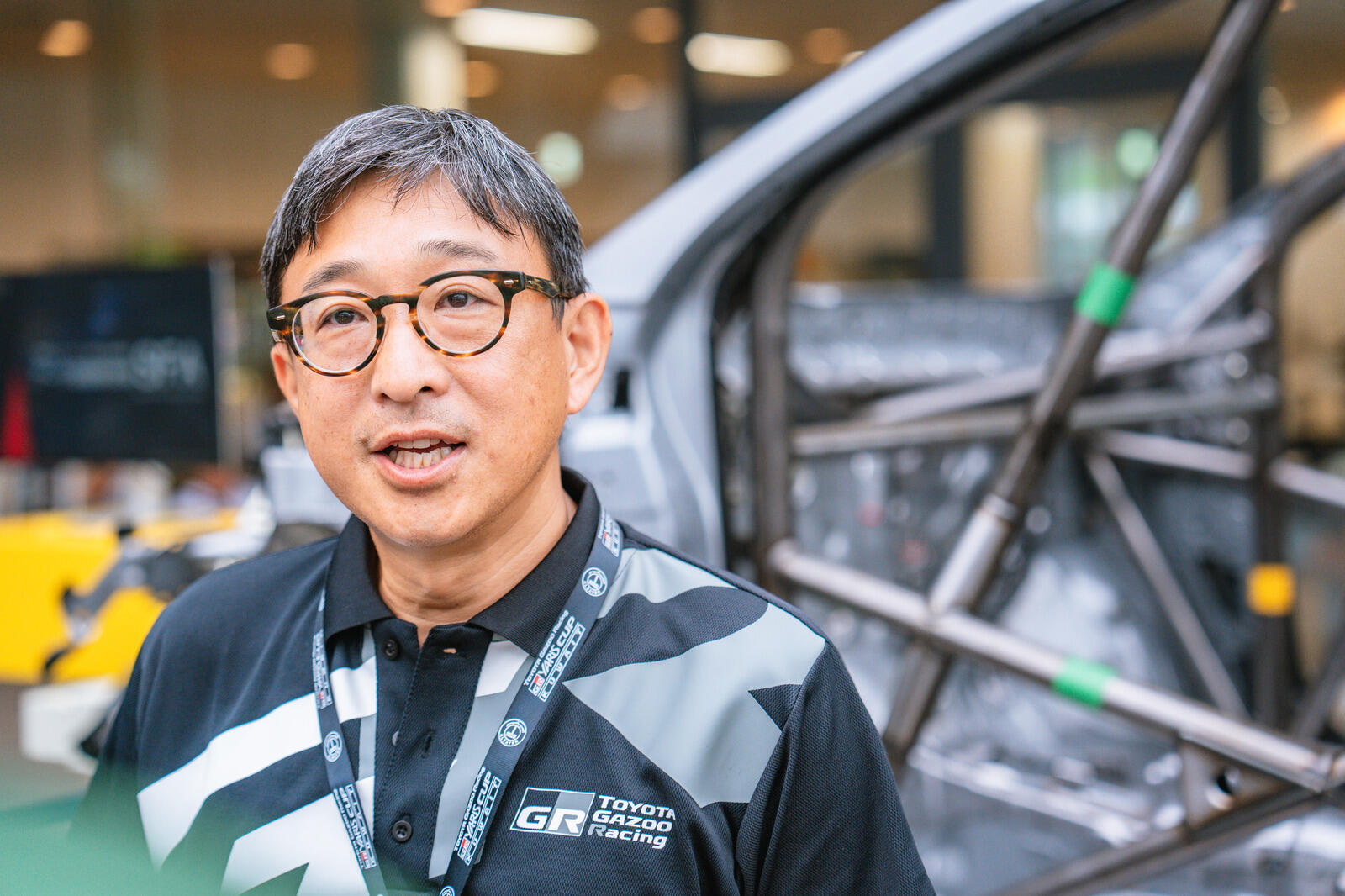
As a manufacturer, we wondered what we could do to make motorsports more sustainable and to create a more accessible environment for a wider range of participants. The challenge we started with was this: how fast can we supply a body in white with a roll cage?
Slowly and carefully
In SFA, the skills of seasoned welders are quantified, allowing robots to be trained on their expertise.
The reason why roll cages require such a skilled craft is because the heat generated during welding creates distortion. Whereas an experienced welder tracks these distortions in their mind and makes the necessary adjustments with their hands, these artisanal processes pose difficulties for robots.
After some three months of development, the team turned the problem on its head: if computing distortion during welding was too difficult, how about preventing the distortion from happening in the first place?
Conventional welding increases the likelihood of distortion by applying too much heat to the metal. SFA gets around this issue by welding more slowly than human technicians and spacing out individual welds to avoid heat buildup.
Compared to the takt time (time needed to make one product) on Toyota’s mass production lines, which create a car every 60 seconds, this type of welding is ten times slower. Still, it is more than fast enough for racing cars, where “we can throw out the takt time concept entirely,” said Project General Manager Kawakita.
The challenge for Yaskawa Electric was making efficiency-oriented robots work more slowly and carefully. Shota Shibata, a car enthusiast who participates in drifting competitions and even makes his own roll cages, explained the situation.
Shibata, Yaskawa Electric
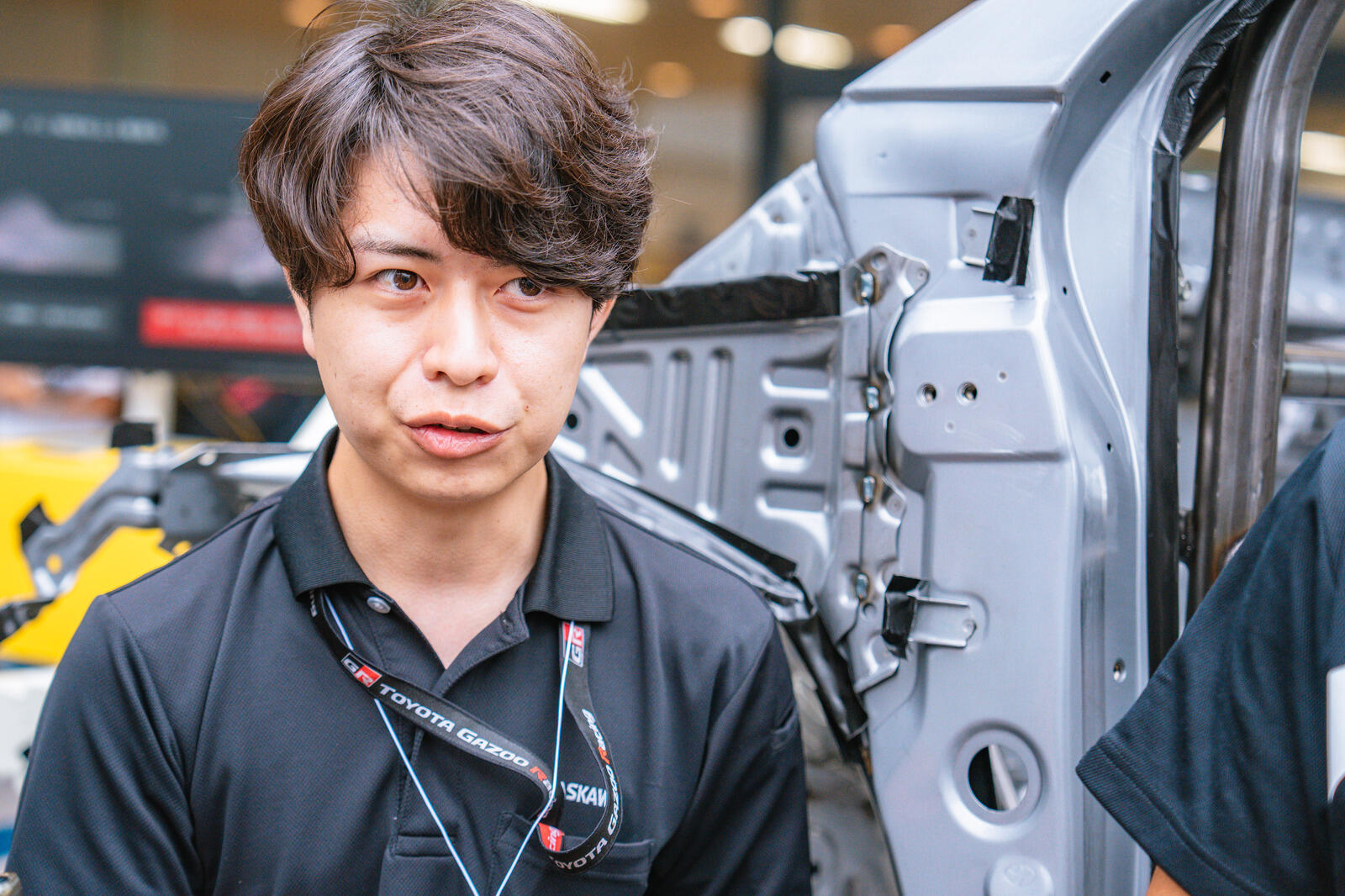
As a robot manufacturer, we were focused on delivering robots that can build cars more quickly and efficiently.
We had never ventured into the area of taking more time and care than humans. In tackling that challenge, we could not rely on existing technologies for rapid production, so we spent a year building up the capabilities for working more slowly and carefully.
Using SFA results in a weld joint—or bead—that is thinner and wider, reducing its weight by roughly 25%. The weld also sinks deeper into the base metal, making the joint 10 to 25% stronger.
What’s more, since each weld is allowed to solidify during the process, the molten metal does not droop under its own weight, enabling joints to be made on the undersides of parts or sloping angles that were previously difficult.
As an added feature, SFA is also capable of arc welding with results similar to spot welds * and welding while leaving gaps of 2 to 3 mm.
*A method in which overlapping plates are clamped between two electrodes, applying electric current and pressure that melts the metal to form a single “spot” joint. In arc welding, a welding wire is melted together with the metal plates, creating a joint through alloying. It is used in places that do not allow for spot welding (cannot be clamped with electrodes).
Another SFA “by-product” is the ability to weld sections that were previously not possible, which can increase the rigidity of not just roll cages but also the vehicle body itself.