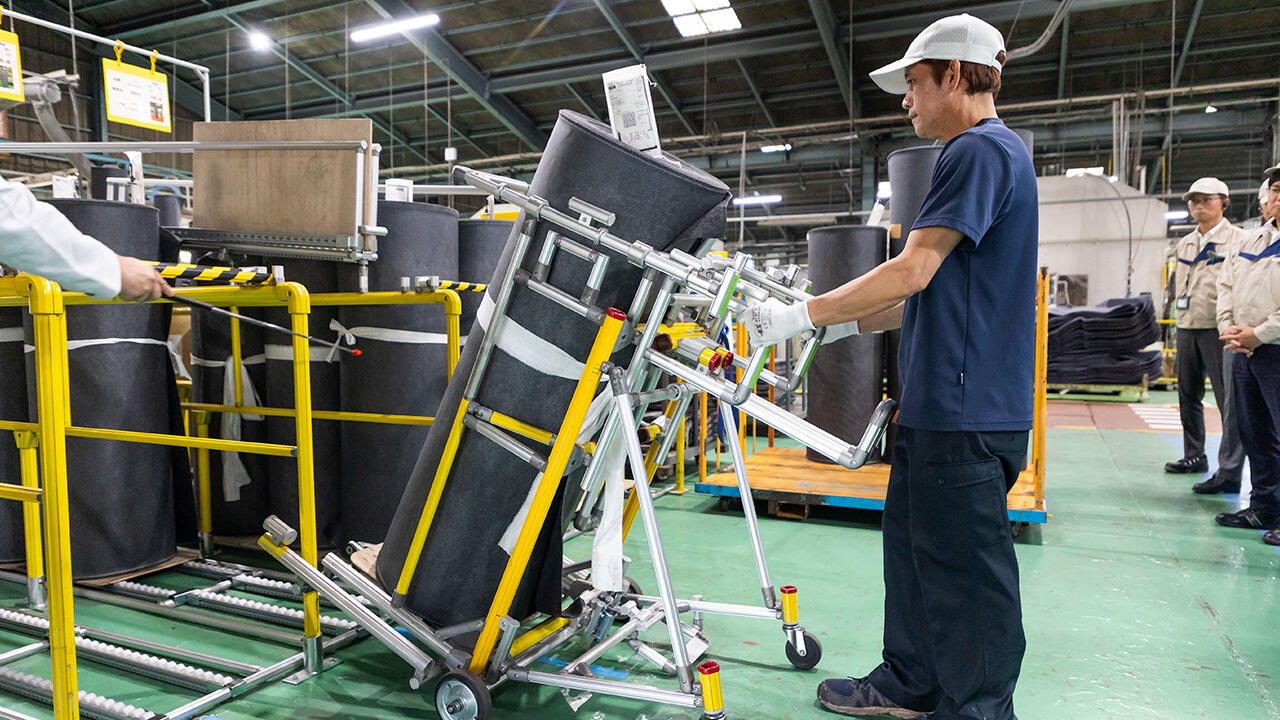
"Toyota is coming..." Initially uneasy about incorporating the Toyota Production System, this supplier gradually changed their outlook as the companies worked together to make improvements.
Sitting down face-to-face
President Umemura, Umemura Industry
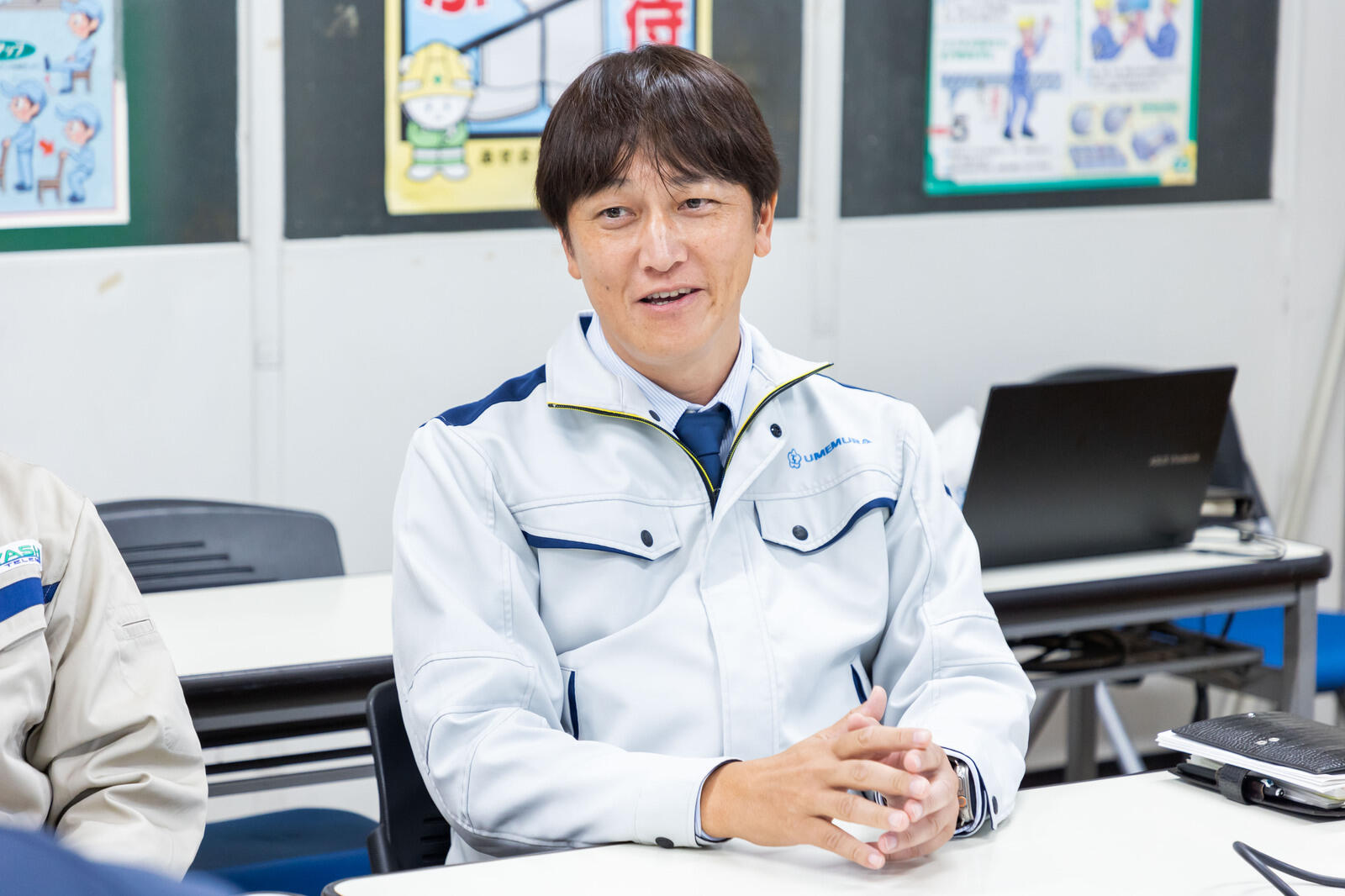
Toyota and the Tier 1 manufacturers made time for us every week, but to be honest, I expected the collaboration to be something superficial at first—they might come in and say, “This is wrong, fix it,” then on the next visit they’d check what we did and tell us it still needs fixing.
In reality, they sat down with us face-to-face, and we were able to work with Toyota and Hayashi Telempu through each problem, one by one.
As the collaborative activities progressed and the genba began to enjoy some breathing room, more Umemura members got involved.
Hirotaka Ishikawa, general manager of Hayashi Telempu’s Interior Value Chain Division, was then serving in the company’s Interior System Planning Division. He recalls how the genba gradually found its spark.
General Manager Ishikawa, Hayashi Telempu
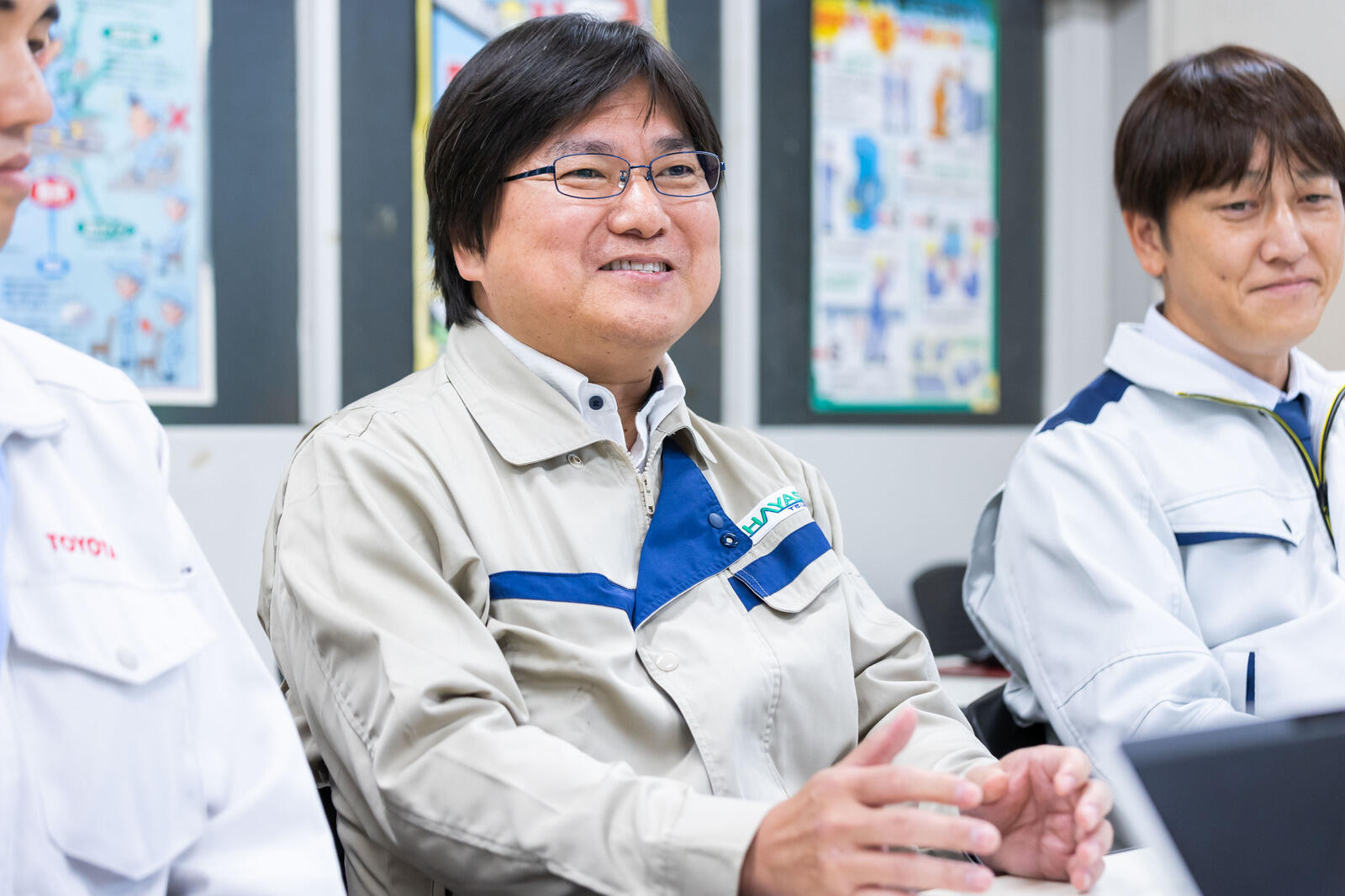
At first, we were told they (Umemura Industry) could only contribute about three people to these efforts, but before we knew it, they outnumbered those of us from Hayashi Telempu as they gradually got more and more into it.
I think they came to see that when three companies work together, these improvement activities can really bear fruit.
What made me happiest of all was hearing that the employees had gained greater motivation.
Even so, challenges remain. “Although Umemura Industry was a success story, other companies aren’t exactly lining up to be next… There’s still some reluctance.”
With its fixation on eliminating waste, inconsistencies, and unreasonable requirements, the TPS approach may seem to some like endless work.
Among Toyota’s participants was Group Manager Junichi Iwata of the Monozukuri Innovation Department (Purchasing Engineering & Project Promotion Division), who also senses high hurdles to getting these activities off the ground.
Group Manager Iwata, Toyota
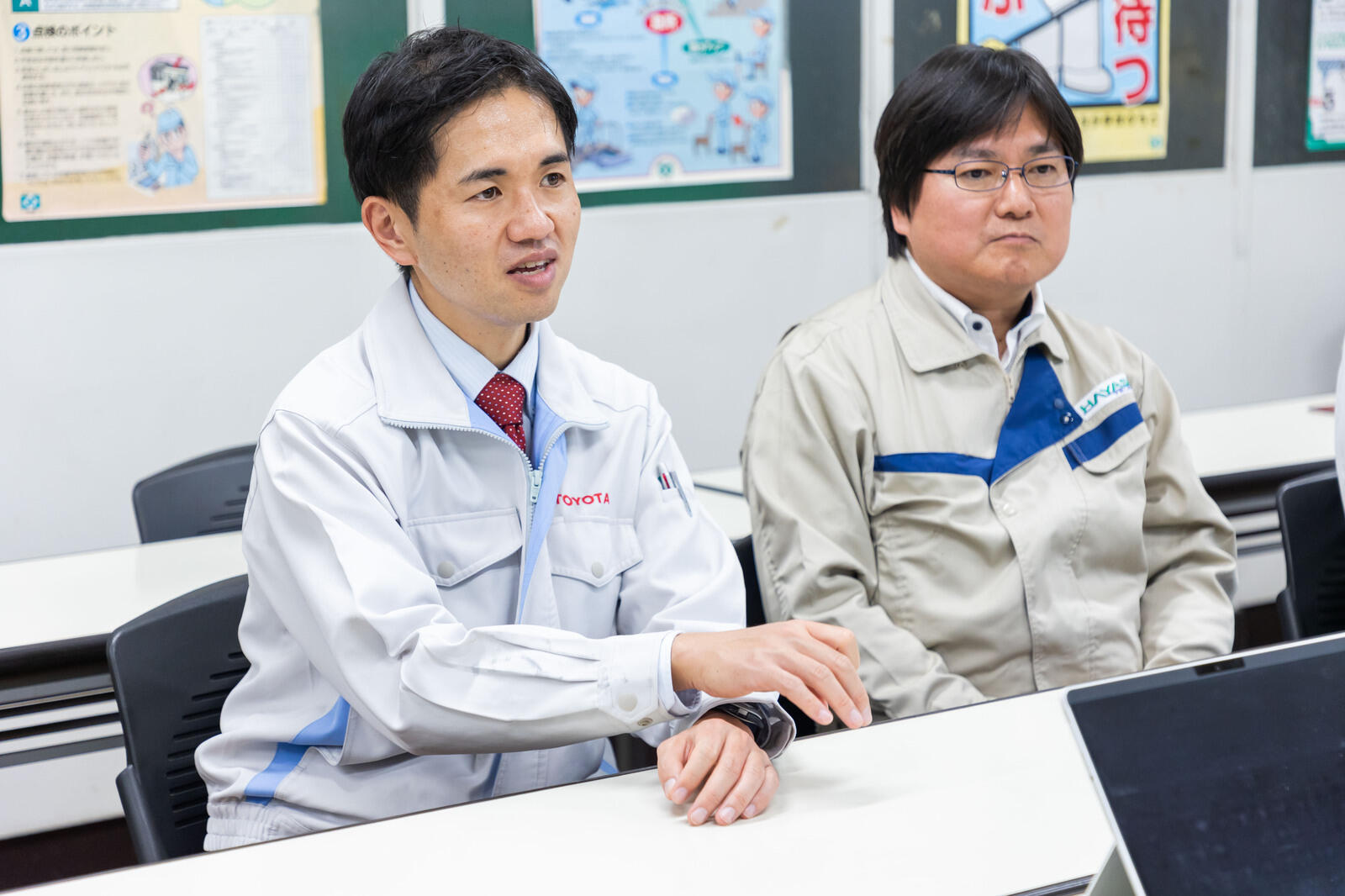
When you try TPS, you understand the benefits. But we can’t shake the image that it is just an added difficulty… that’s the problem.
It would be nice if people could clearly understand the value in advance, but the hard part is you have to try it for yourself.
On working with Umemura Industry, Iwata recalls, “We spoke about the purpose of TPS in making work easier for those in the genba and tried to convey the outcomes they can expect, both verbally and visually, including visits to Toyota sites. I think we were able to get the message across, and that got things moving.”
In our previous article, Chief Officer Kumakura explained that “our suppliers receive the profits” of cost reductions achieved through SSA, and this mindset extends to Toyota’s Group Collaborative Activities. Any benefits gained become assets for the supplier.
“As we grapple with business challenges such as energy and personnel expenses, being able to reduce our costs was a great result for the company,” says President Umemura.
Although the final activity report was presented in May 2024, Umemura is working to apply the lessons learned to other production lines and plants.
The kaizen cycle has been set in motion.
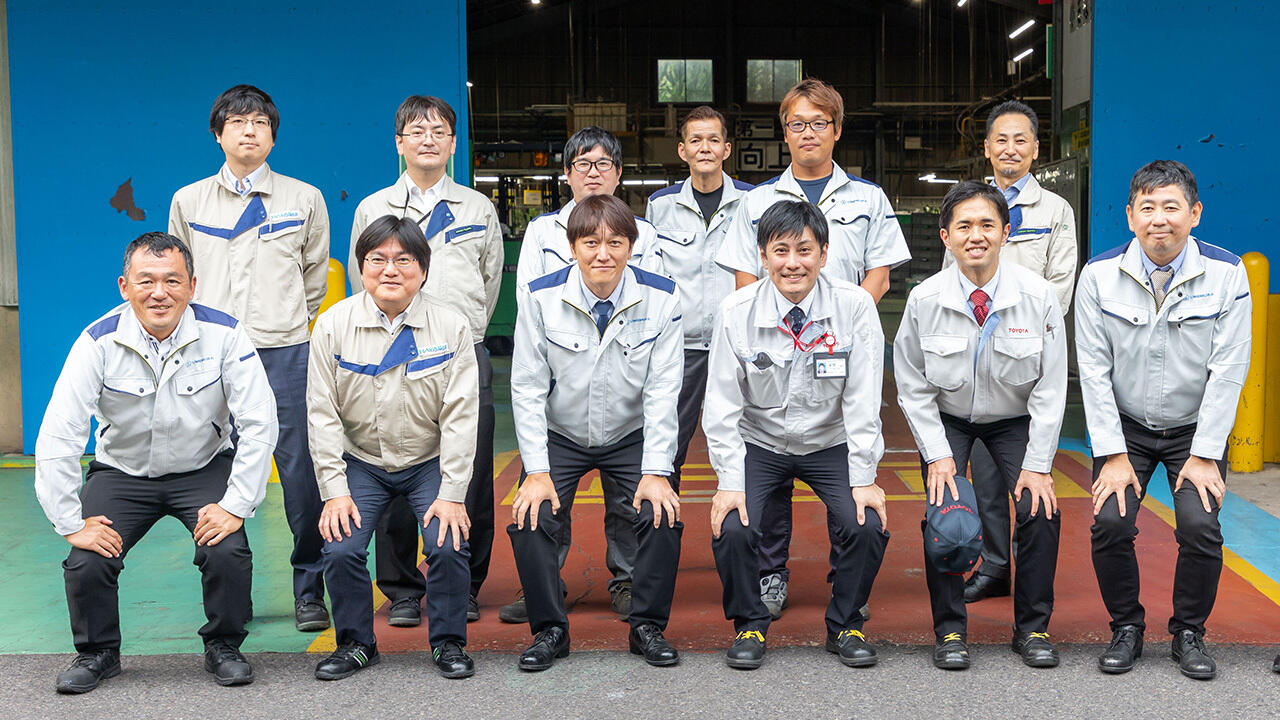