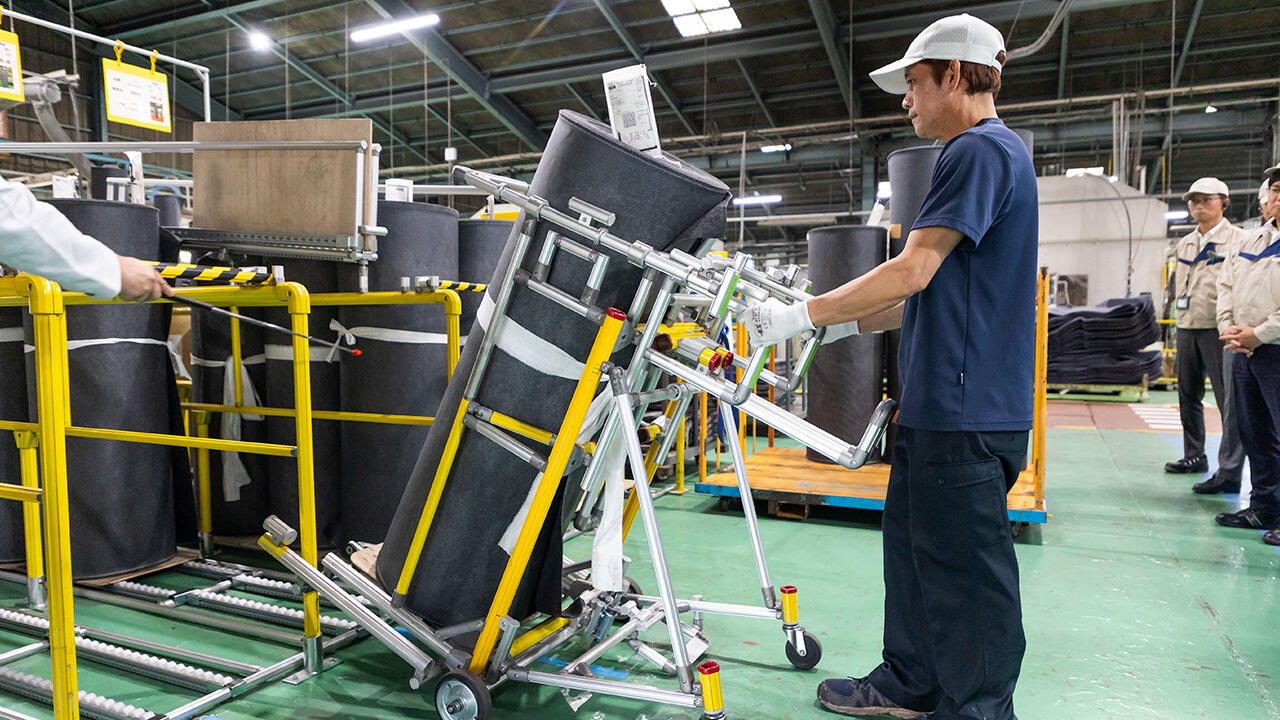
"Toyota is coming..." Initially uneasy about incorporating the Toyota Production System, this supplier gradually changed their outlook as the companies worked together to make improvements.
Achieving the unthinkable
Molding and cutting the carpets involves equipment such as heaters, presses, and water jet cutters. This stage also creates wasted downtime when the equipment is stopped for changeover, the process of switching over machinery and settings to accommodate different products or requirements.
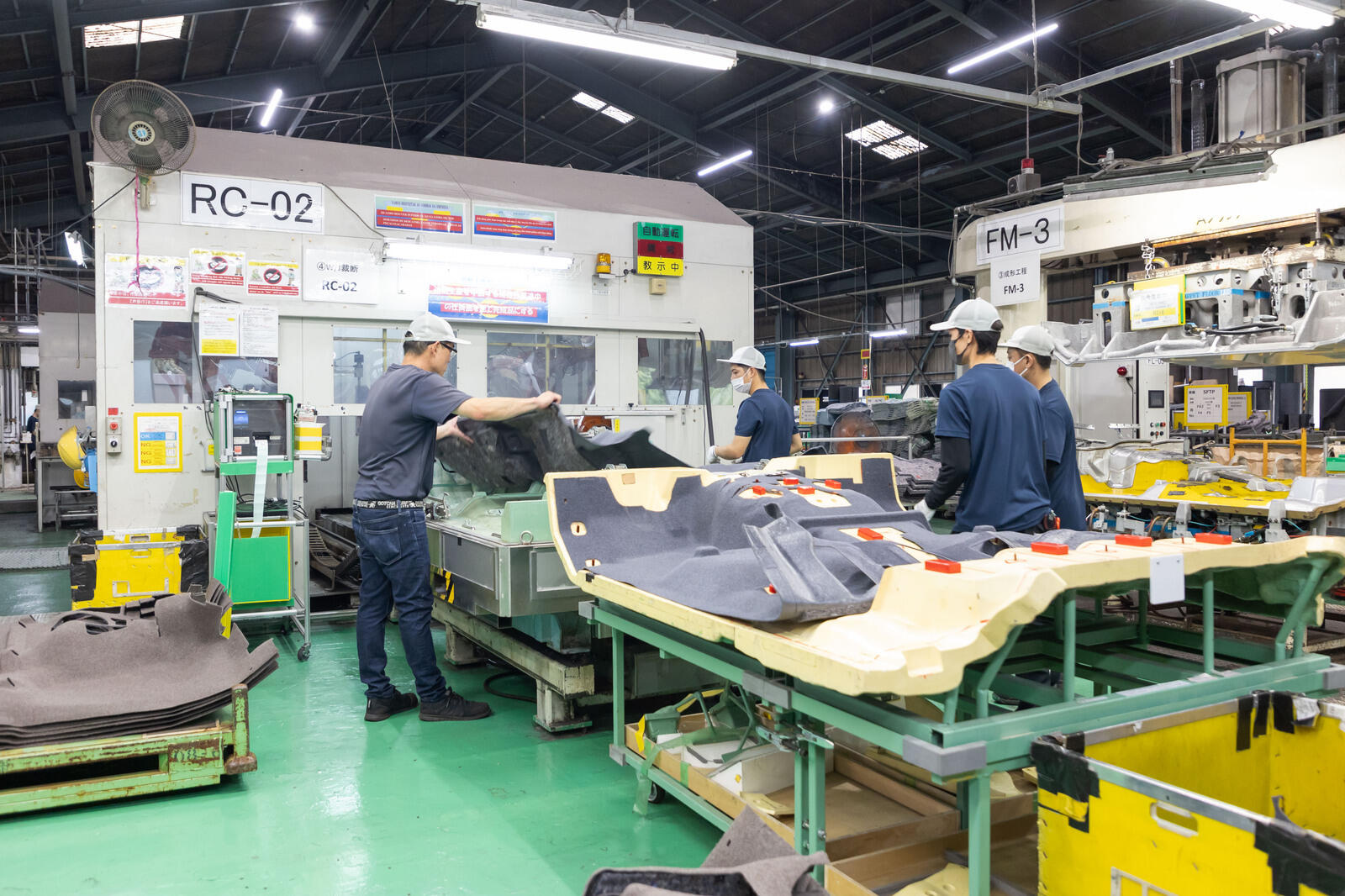
To make improvements, Umemura borrowed from Toyota’s playbook, including measuring the time taken for individual tasks and capturing video for analysis. Changeover times were shortened by revising mold and material placements to bring them closer to workers, raising the operational availability* of equipment from 67.9% to 82.6%.
*The proportion of time a machine actually operates compared to the time it should be in operation. Stoppages for changeovers or breakdowns reduce availability.
At the start of Group Collaborative Activities, the operational availability target was 74%. Given the high-mix, low-volume nature of this production process—with many changeovers creating longer downtimes—no one at Umemura Industry thought it could be done.
And yet, as with the karakuri, harnessing Toyota and Hayashi Telempu's experience saw the numbers tick up day by day. The initial concern soon turned into confidence, as staff pushed themselves to outdo the targets with each improvement.
These changes reduced monthly overtime from the typical 46 hours to zero.
Kanban replaces instinct and intuition
The collaborative improvements didn’t end there.
Umemura also incorporated Toyota’s Kanban system for scheduling production. Previously, a reliance on individual instinct and intuition sometimes led to inventory surpluses or shortages. In its place, the company instilled proper management practices by adopting the “fill-up” system for replenishing only what is used.
Through these efforts, Umemura succeeded in halving both product and materials inventories.
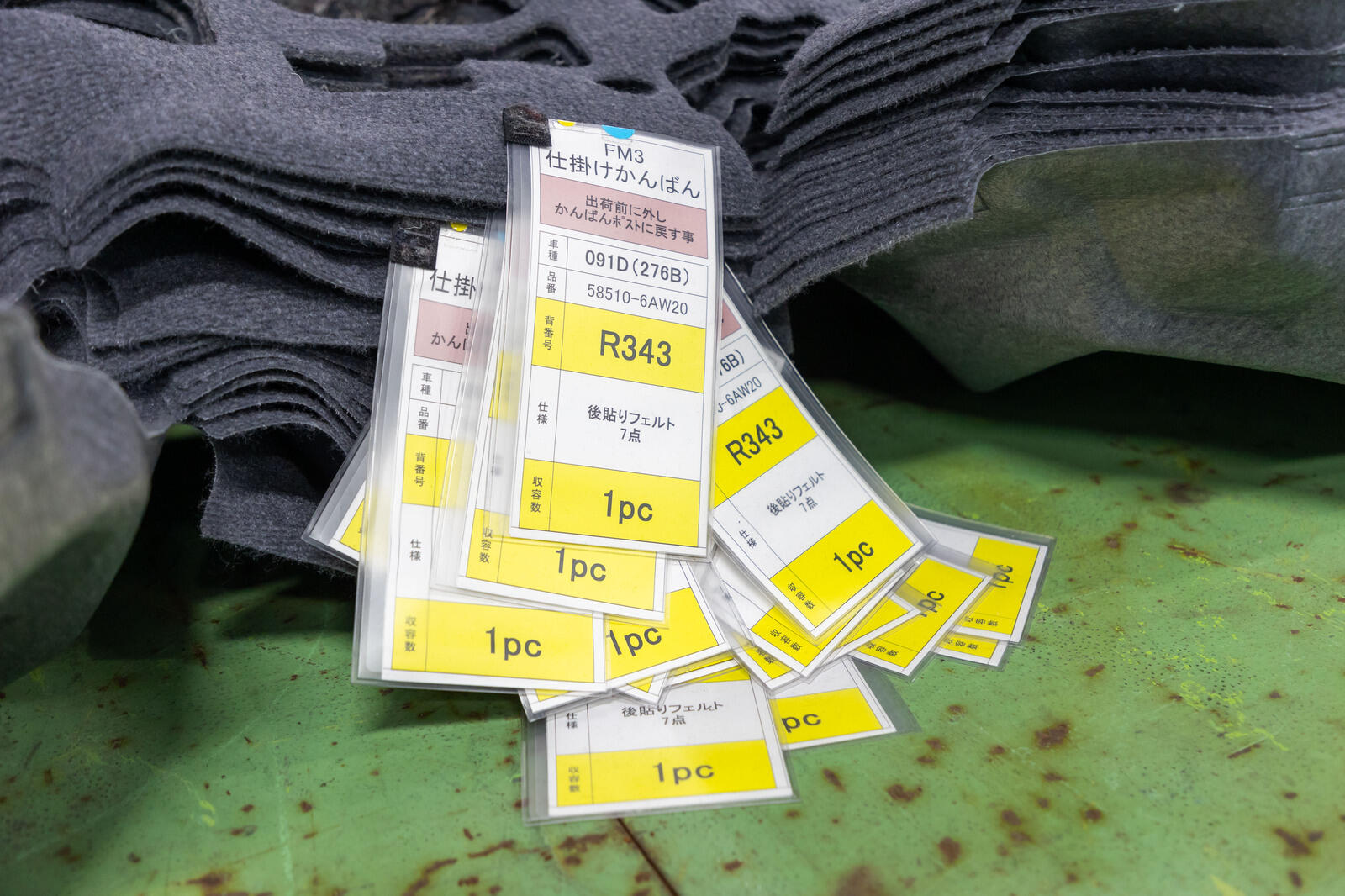
Introducing karakuri or Kanban and working to improve operational availability are part of the routine at Toyota. However, there was no guarantee that things would go similarly well at Umemura Industry. Would employees be able to squeeze in improvement efforts alongside their regular work? Manufacturing Division General Manager Katsuya Kawai, who oversaw the collaborative activities, recalled his initial feelings.
Katsuya Kawai, General Manager, Manufacturing Division, Umemura Industry
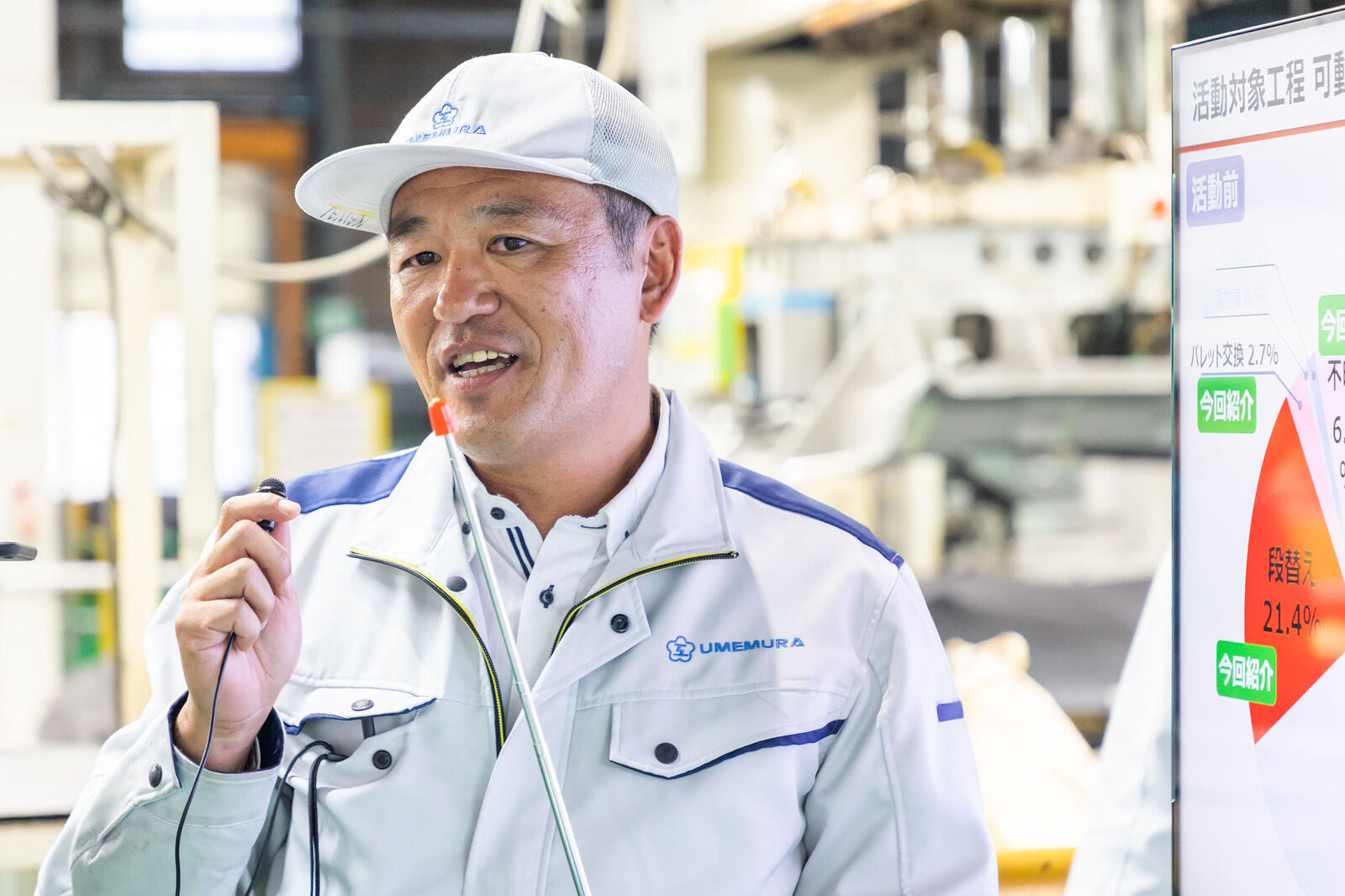
Initially, we were bracing ourselves for Toyota’s approach. We had no idea what we could manage to achieve, and to put it bluntly, we wondered how much they would try to push their views. As it turned out, they respected our opinions above all else, which made working together far easier than expected.
Umemura Industry undertook these efforts from June 2023 to May 2024. Despite other Tier 2 success stories, President Koji Umemura started out somewhat skeptical.