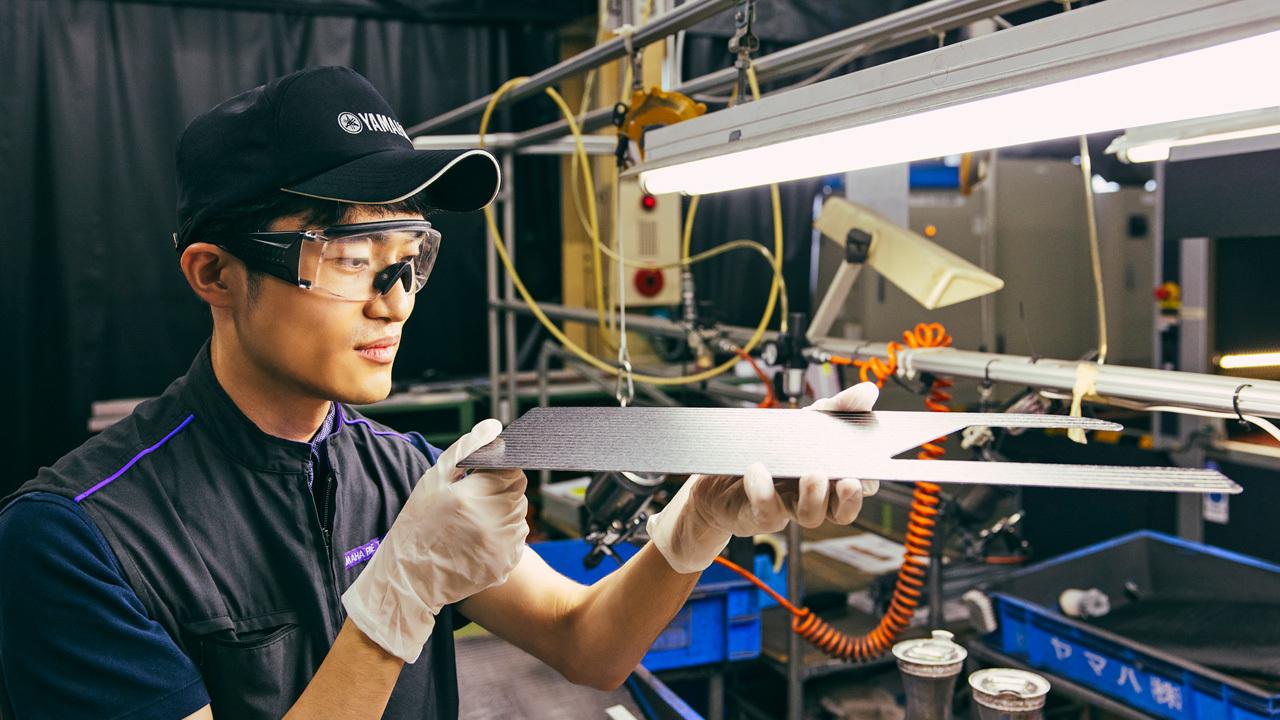
This is an ongoing series looking at the master artisans supporting the automotive industry. Here, in Part 2 of the 17th installment, we hear from the master decorative engineer behind the new Century's beautiful wooden panels.
A first-time laser-cutting challenge
And how about the aesthetic issues? Ubukata explains the effort that went into the decorative panel pinstriping, a key element in conveying luxurious simplicity.
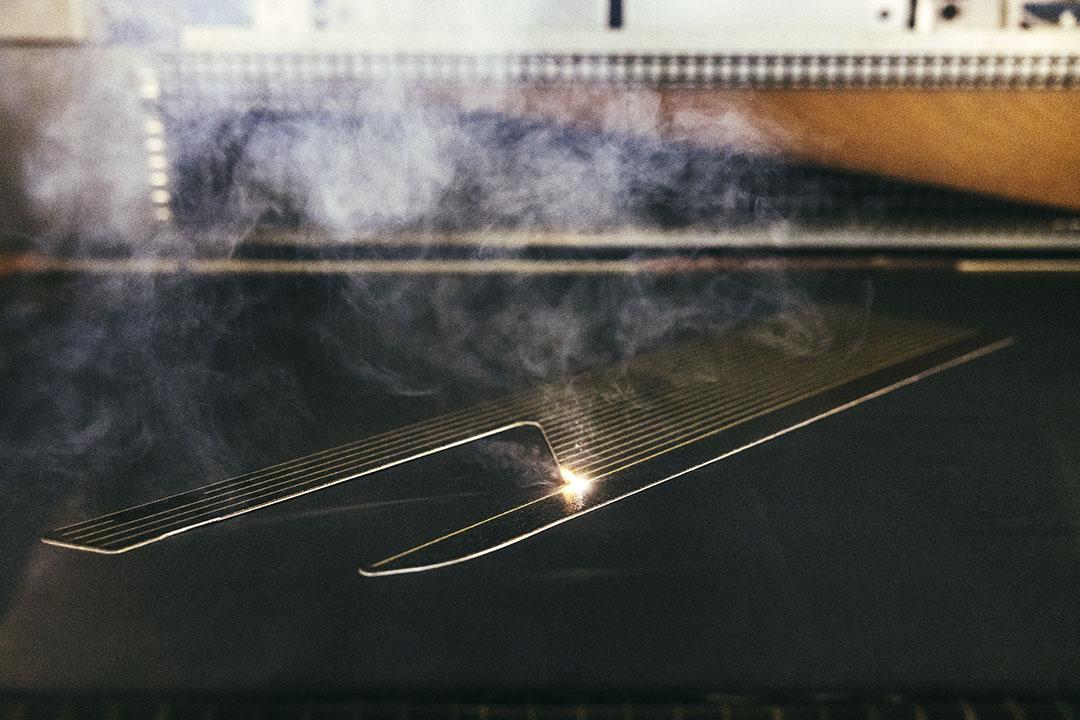
Ubukata
We initially proposed several different ways of arranging the lines, before ultimately settling on the thin, sharp pinstriping.
Our decorative panels combine the veneer, aluminum plate, and backing material into a three-ply sheet, and we created these fine lines by laser-cutting the veneer to expose the aluminum layer beneath.
Laser cutting wood is a common way to engrave wind instruments, for example, so this is a technique that we honed through musical instruments.
Laser-cut lines can be very fine, measuring as little as 0.2 mm wide. Ubukata and his colleagues worked with the Century’s design team to prototype many different line widths before settling on 0.6 mm from an aesthetic standpoint.
What, then, made these laser-cut lines so challenging?
Ubukata
Straight lines of 0.6 mm make for an extremely simple design. As I already mentioned, for this project we use neat, straight grained sapele veneers, with an open pore coating that brings out the vessels on the wood’s surface.
Combining a simple-patterned veneer with simple lines means that even the slightest irregularity will stand out—whether it's the positioning of the wood pores or uneven thickness—and the lines won’t look nice.
It therefore requires a stricter eye in the sumikake (wood selection) process, taking into account how well the veneer’s grain and vessels will fit with the fine striping. We managed to clear this hurdle thanks to Kaneko and the other sumikake members.
After laser cutting, we also use a press to mold the flat three-ply sheets and bond them to the underlying plastic structures. The machine's pressure can squash the wooden surface, eliminating the grain texture or the lines’ clarity and sharpness.
We addressed this by modifying aspects such as the three-ply sheets' physical structure (layer thickness) and the press’s shaping parameters.
What’s more, since the painting process entailed coating two different materials (wood and aluminum), selecting the right paints and adjusting hues also involved some trial and error.
Ubukata
As part of that trial and error, we informed Toyota’s design team that, since we were working with genuine wood, there was bound to be some variability in the lines and colors.
The response was: “Clean, straight lines are crucial to creating something that is simple yet luxurious—please do your best to make it happen.” These words expressed a strong commitment and spurred us to meet their expectations, which we somehow managed to do.
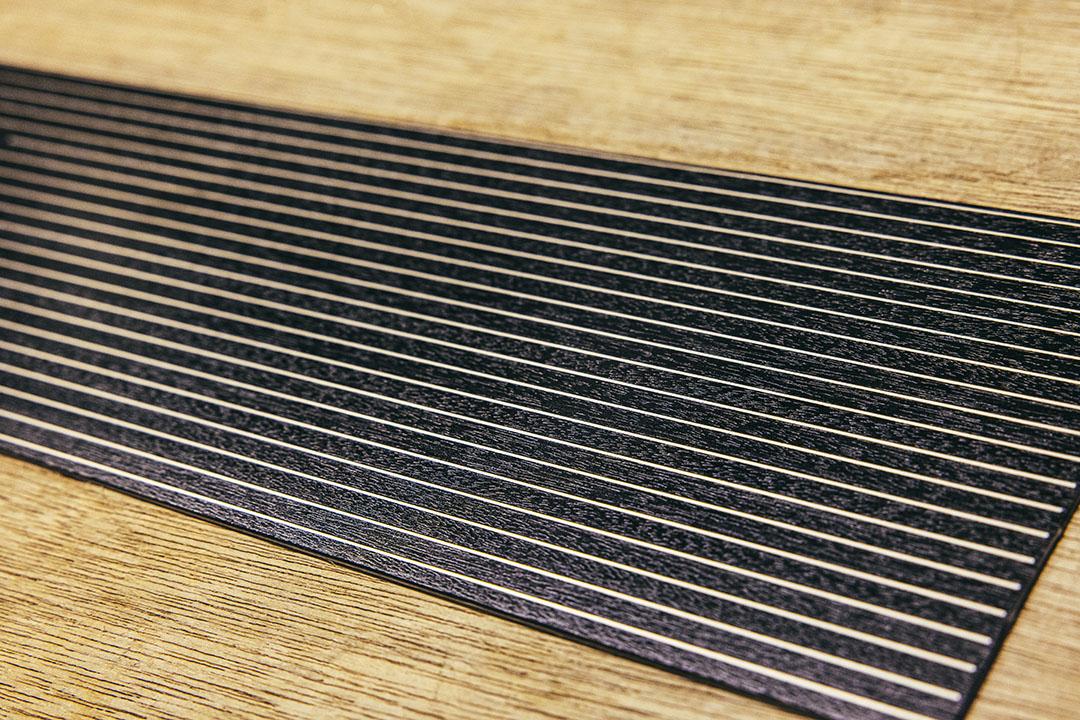