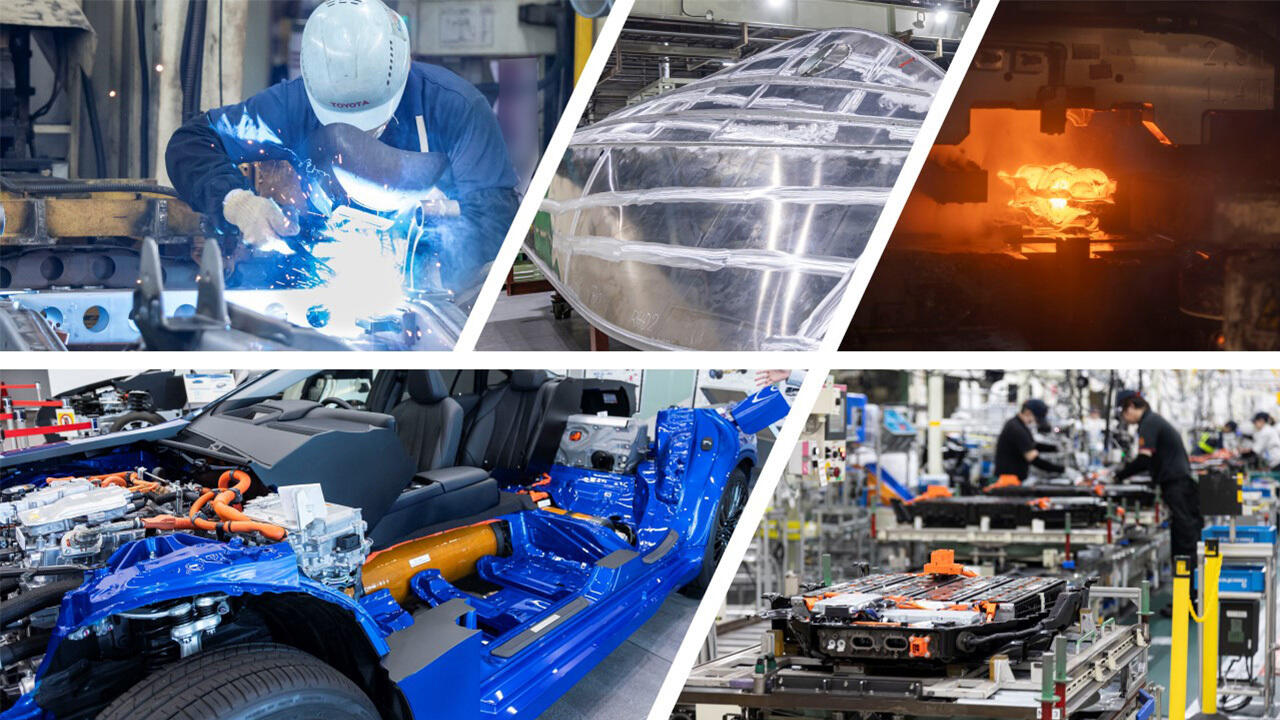
Toyota's Plants: Inheritance & Evolution is a series introducing the history and future vision of individual production facilities. This article focuses on the Honsha Plant's current situation and the challenges it is undertaking for the future.
[Chassis Manufacturing Division ] Indispensable human senses
In November 2023, Toyota’s first overseas production facility, the Sao Bernardo Plant in Brazil, closed the curtain on its 60-year history. When the plant’s Komatsu 700-ton press machine came home to Japan, it ended up at the Chassis Manufacturing Division.
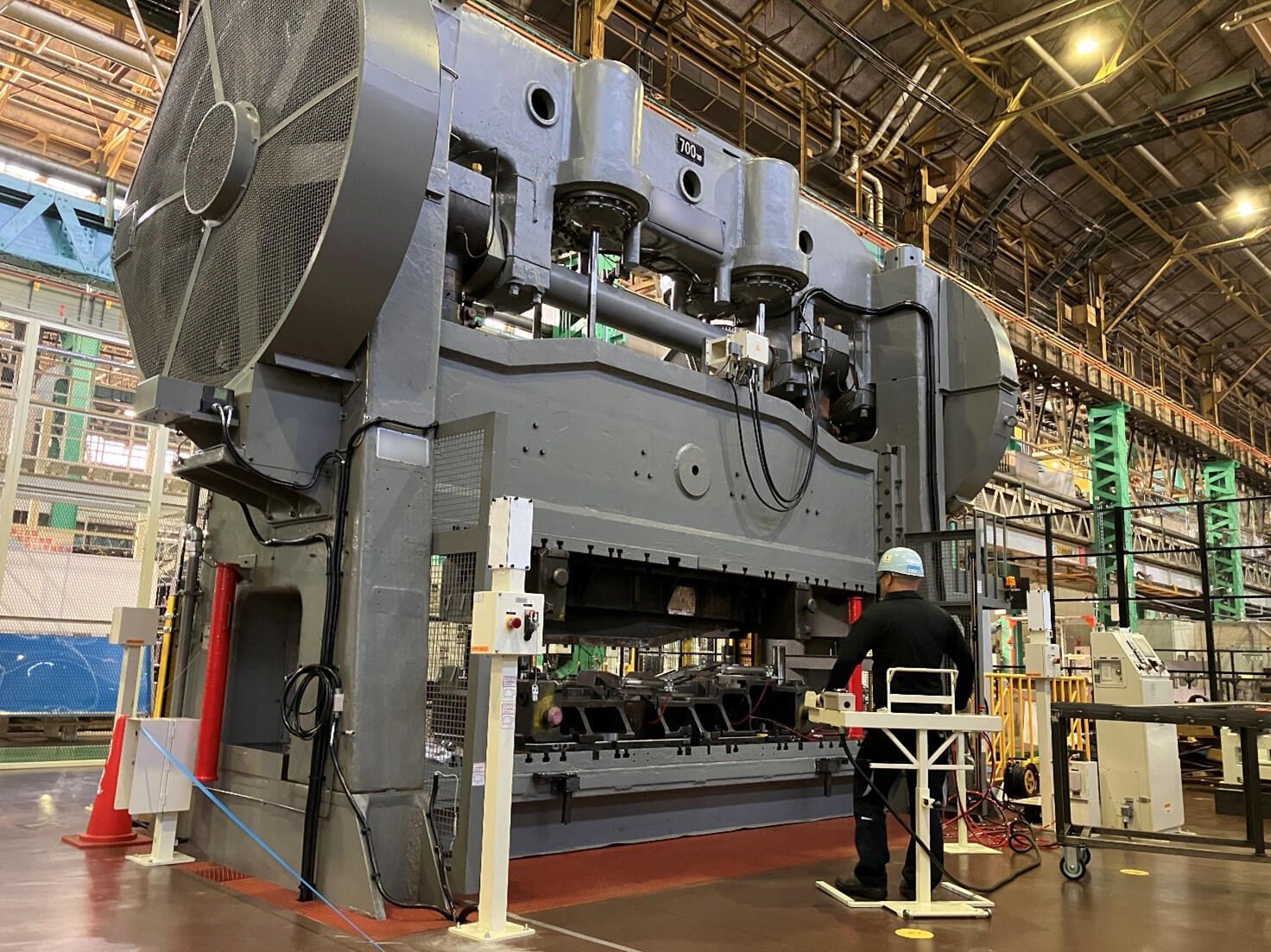
The division mainly welds frames and stamps the steel plates that make up chassis and suspension components. It is here that frames for the Land Cruiser 300 and other vehicles take shape.
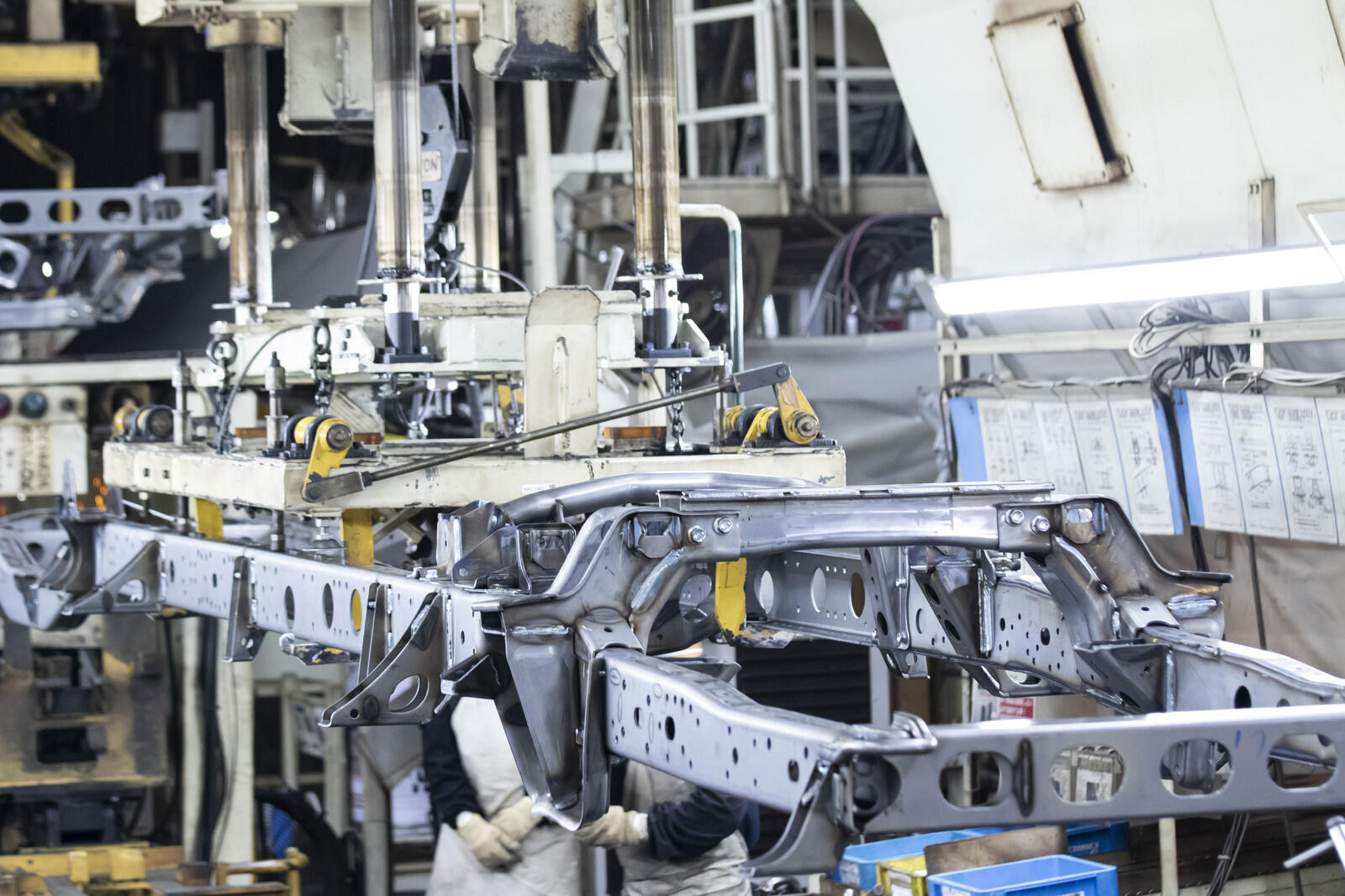
This process involves cutting and bending steel plates, and human touch is essential for ensuring consistent quality as the metal expands and contracts. The degree to which it distorts depends on temperature changes and heat input during processing, requiring meticulous calculations.
In the arc welding step, heat is applied to melt and connect the steel plates. With joint temperatures reaching as high as 1,300 degrees, the task is handled by machines in place of people.
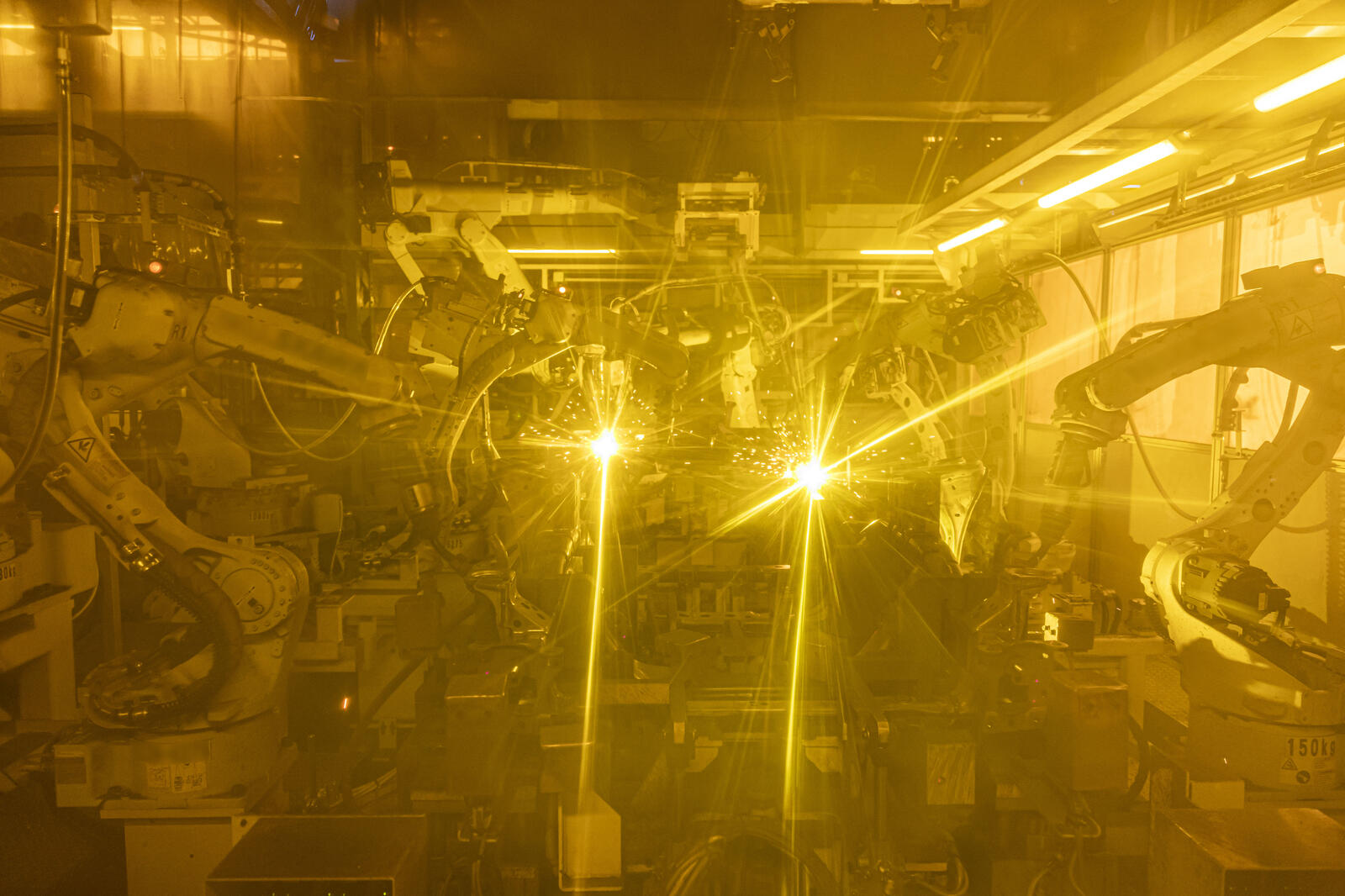
On the other hand, the division also deliberately retains welding tasks for training personnel.
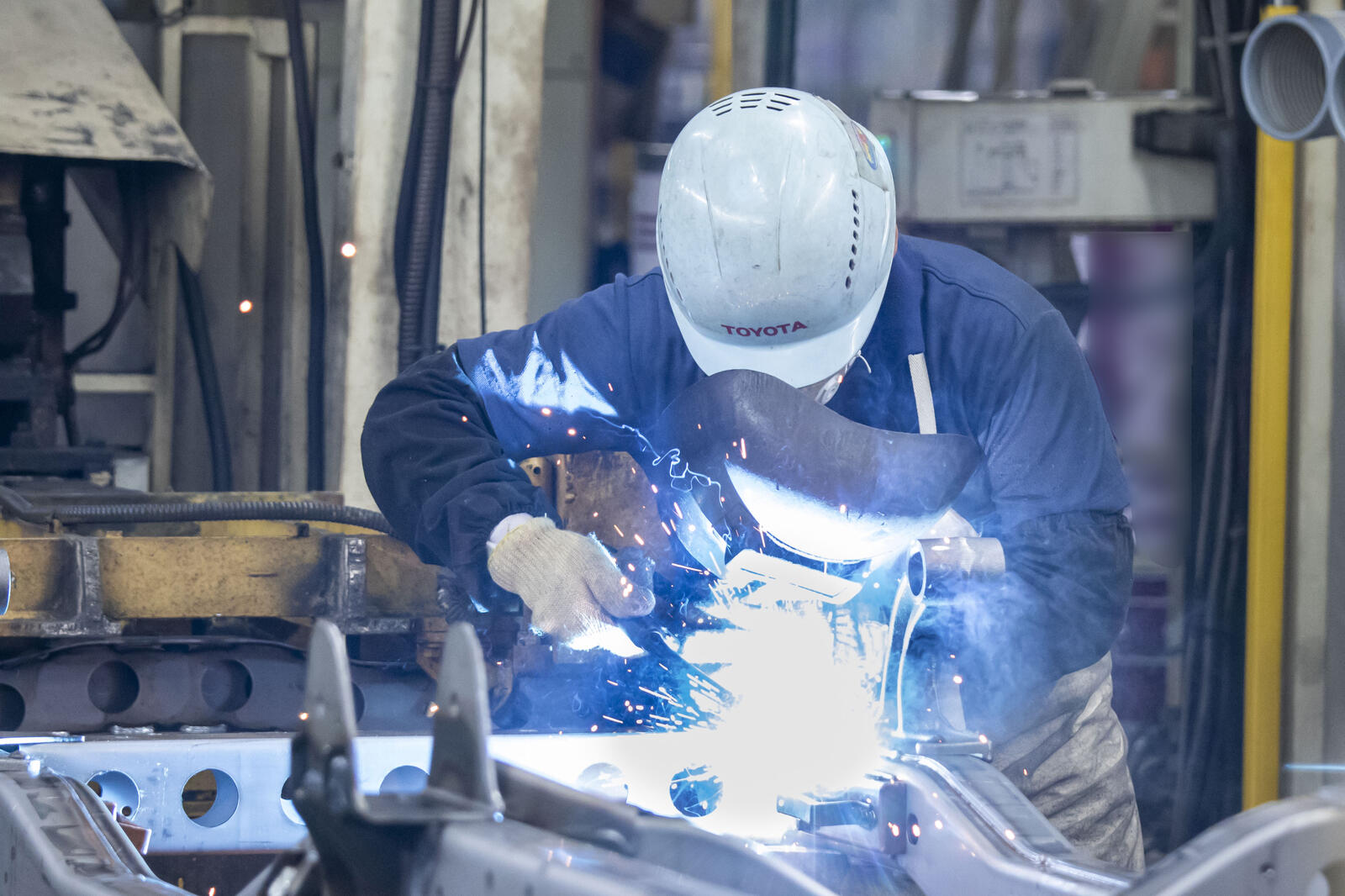
Chihiro Tabata, general manager of the division’s Engineering Service Department, outlines the reasons for preserving this hands-on work.
Chihiro Tabata, General Manager, Engineering Service Dept., Chassis Manufacturing Div.
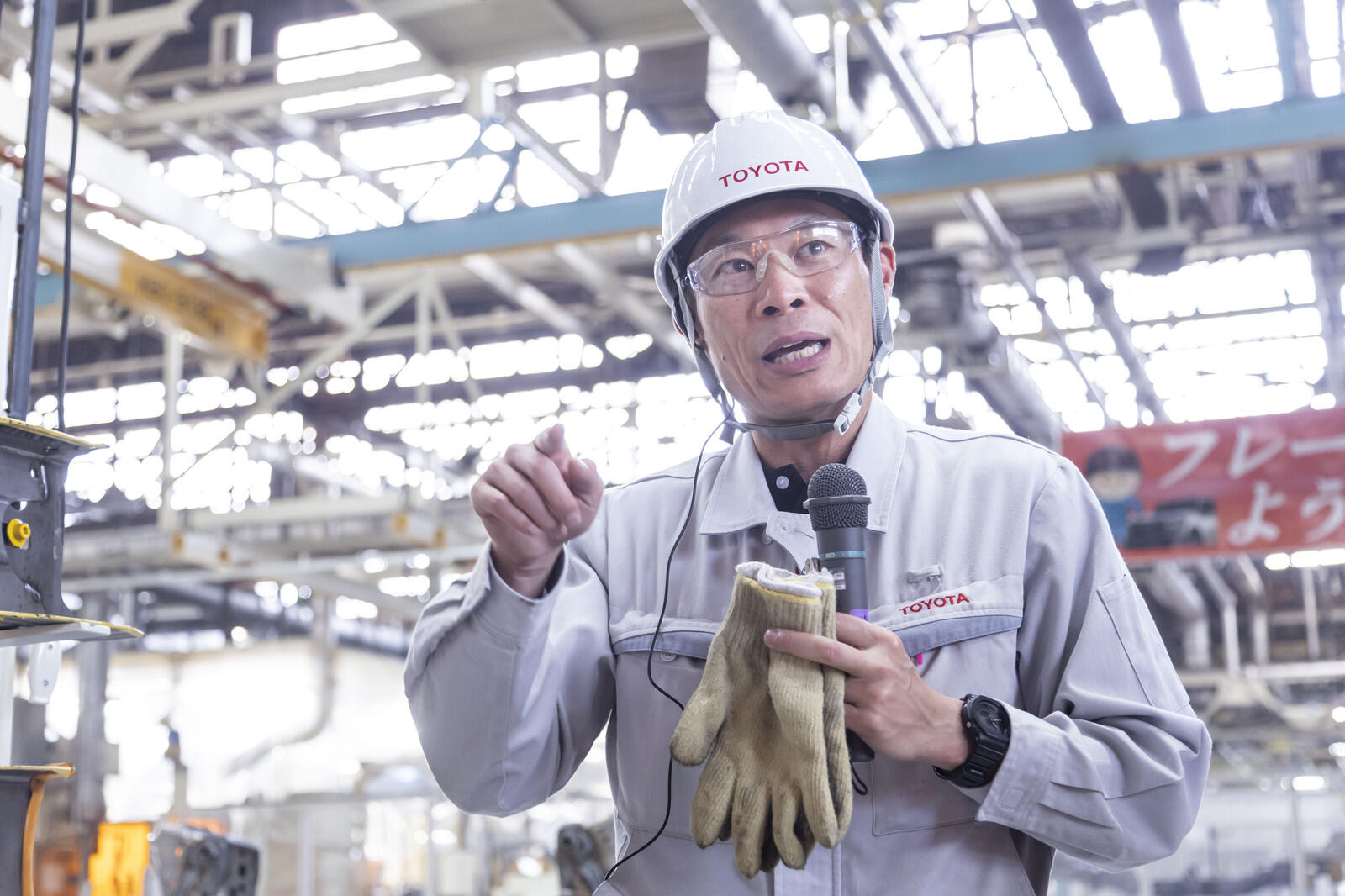
At one point, we pitted the latest welding machinery against skilled technicians, but the machines were no match for humans.
There are aspects of good welding that don’t show up in the numbers and can only be perceived by human senses. Conveying that to machines is a challenge, and that’s why we cannot allow hands-on human welding skills to die out.
In recent years, the division has also begun using laser welding to increase frame strength. Given its adoption of such technologies, since 2024, the Chassis Manufacturing Division has been dubbed the “Frame Center” and now also serves a role in researching and sharing frame-making expertise.
Working together to create the future
Kiichiro Toyoda established the Honsha Plant (originally the Koromo Plant) in order to develop an automobile industry in Japan. Plant General Manager Yoshinori Eri pledges to carry forth this vision by continuing to take on new challenges, calling this the Honko Tamashii (Honsha Plant Spirit).
Although each of the four divisions showcased in this article works in different domains, they all embody the Honko spirit in their dedication to future-focused personnel development and tireless pursuit of ever-better products.
Currently, the Honsha Plant is also focused on creating workplaces where every member can flourish.
For the past three years the plant has organized Honko Live, a simultaneous livestream connecting all departments, to encourage flat, open communication across organizational and functional boundaries. It is used to share each team’s improvements and digitalization efforts.
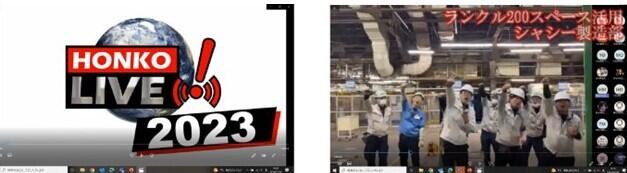
Honko Live has spurred many young employees to put up their hands and show what they can do, in many cases leading to new developments.
Plant General Manager Eri
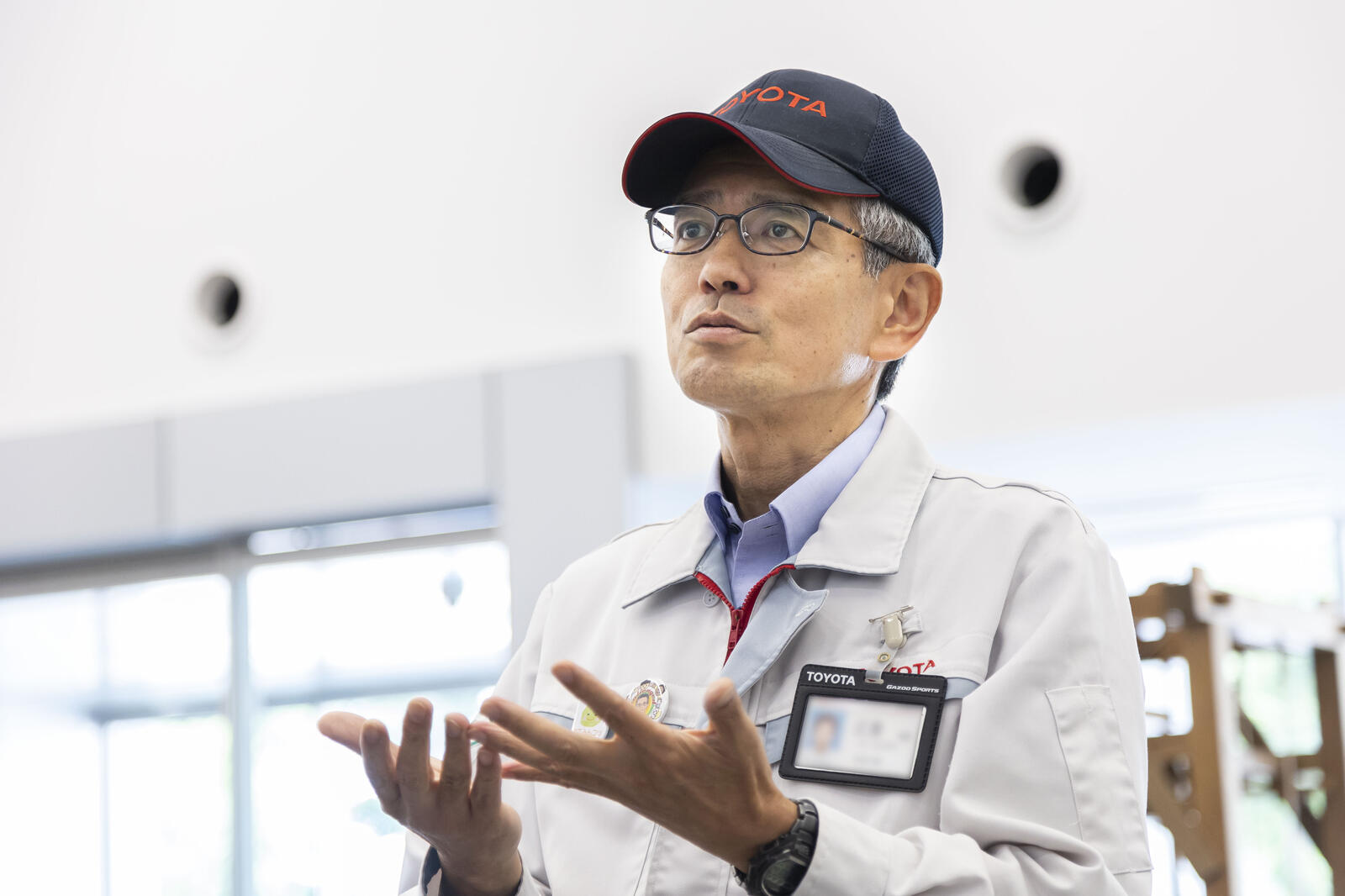
Many people look forward to Honko Live, which gives everyone from young technicians to managers a chance to mix and communicate. One moment that made me really happy was hearing someone say, “This is the most fun I’ve had in my 30 years at the company.”
The Honsha Plant can be seen as Toyota’s soil, where people have honed their monozukuri skills. When you sow the seeds of a new challenge, it is sure to sprout and grow, despite the hardships.
I’m happy to say that since the Honsha Plant has many such places across various domains, the areas we can tackle continue to expand, and I think that makes our staff happy as well.
As individual members thrive, the Honsha Plant’s capabilities grow, and the more they grow, the greater our capacity to take on new challenges. That is why we want to ensure that everyone can flourish here.
Let’s work together to maintain and improve the soil that helps us grow. It’s not just about honing skills but also the human side, the Honko spirit. That’s the message I want to send.
Cultivate our skills and enhance our technologies. Never stop challenging and keep the Honko Tamashii alive.
Having an environment where we can challenge ourselves, a place where we can grow, is what allows us to plant seeds for the future. I want to create a workplace that invigorates and allows everyone to flourish.
Creating the future is about more than simply adopting the latest machinery. To hone manufacturing skills, you need fertile soil where everyone can flourish.
Fostering formidable skills
Over these two articles, we have covered the Honsha Plant’s history (Inheritance) and future (Evolution).
To wrap things up, we want to share the words of Oyaji Mitsuru Kawai, a veteran with more than 60 years of genba experience. We spoke to him ahead of the Monozukuri Workshop held in 2023.
Oyaji Kawai
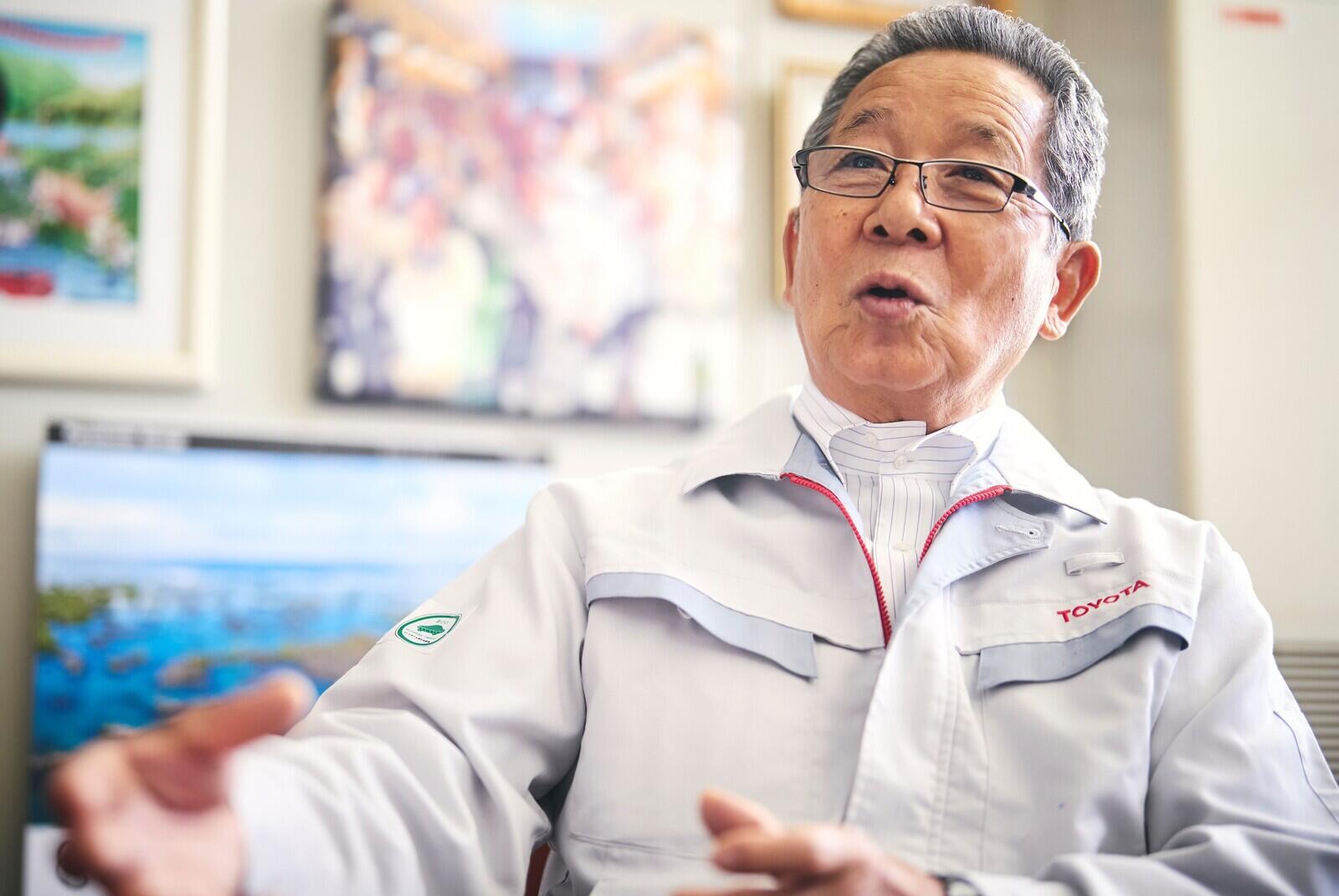
As I always say, skills are not something you develop because some car or other is being brought into the plant. If you constantly nurture and strengthen them, you can handle anything that comes your way.
Ten years ago, I set out to train highly skilled technicians because I was deeply concerned that, amid the rapid progress of automation, more and more people would take it for granted that you can make things by simply pushing a button, with no need for human skills.
As the number of defects and equipment stoppages decreased, we were losing opportunities for developing the skills to improve quality or solve malfunctions.
To continue advancing automation, we need to nurture people that can teach the robots, with skills that outshine them. Unless we train people who can weld better than robots, quality won’t improve, and we won't get better.
Ever since joining Toyota, Oyaji Kawai’s workplace has been the Honsha Plant’s Forging Division. As the longest-serving mass-production facility in Toyota history, the Honsha Plant carries on the Honko spirit in every genba, always remaining at the forefront of the company’s challenges.
Toyota Honsha Plant
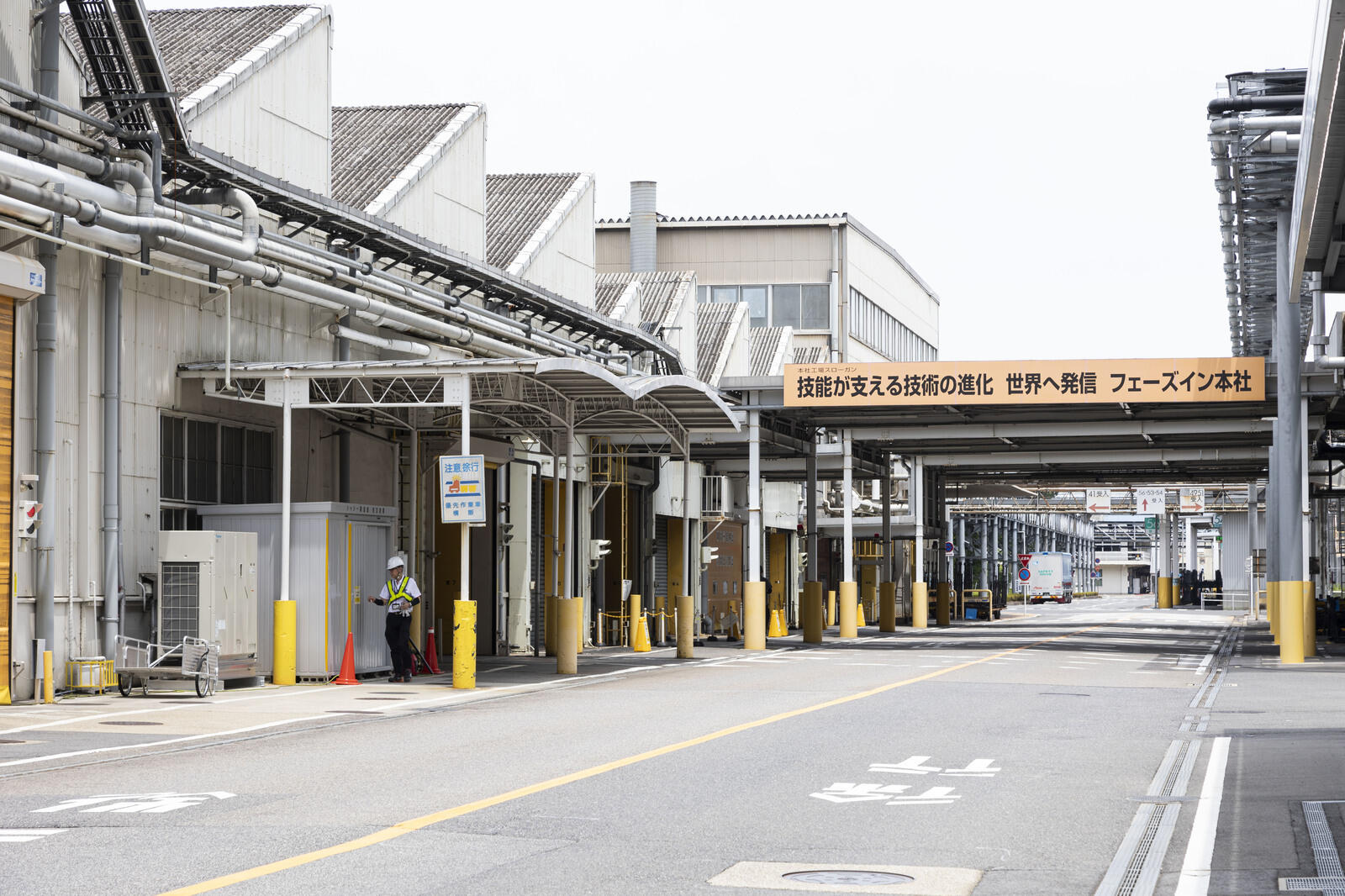
Location: 1 Toyota-cho, Toyota City, Aichi 471-8571
Start of production: November 3, 1938
Site area: 599,000 m 2
Employees: 1,940 (as of March 2024)
Main products: Engine and transmission parts, Mirai fuel cell stacks, Prius hybrid units, Land Cruiser frames, etc.