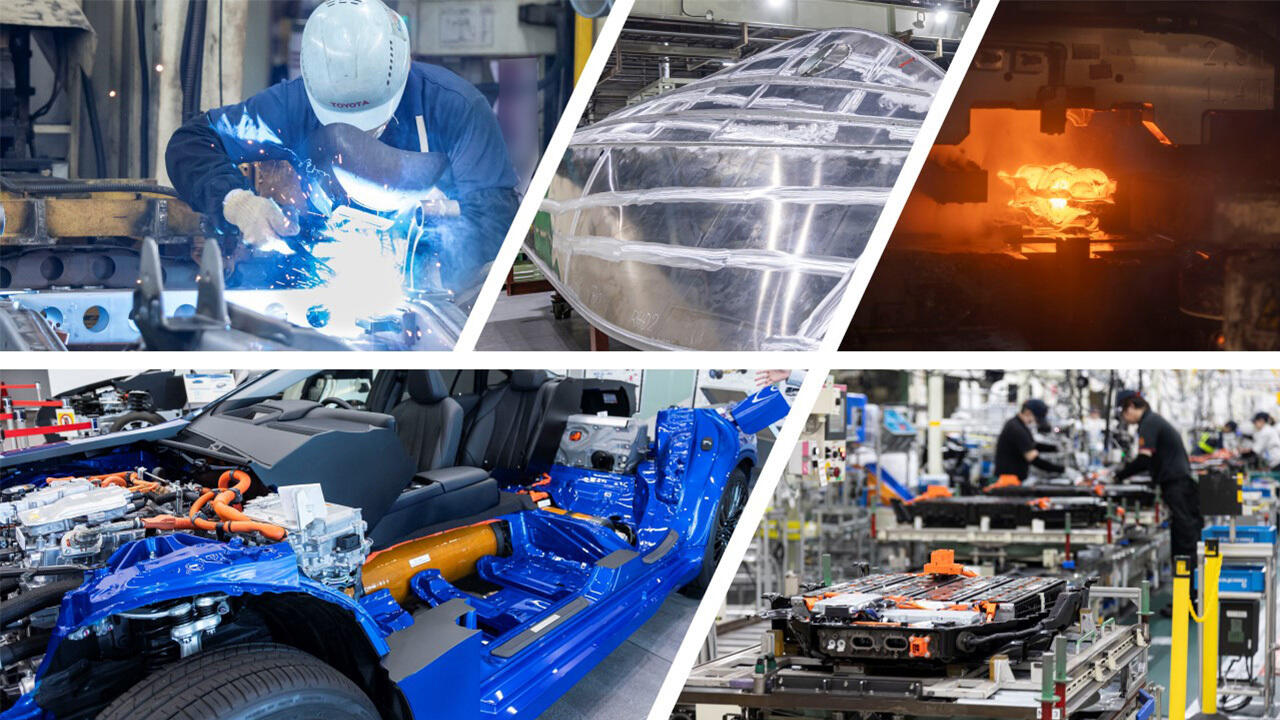
Toyota's Plants: Inheritance & Evolution is a series introducing the history and future vision of individual production facilities. This article focuses on the Honsha Plant's current situation and the challenges it is undertaking for the future.
[Fuel Cell Manufacturing Division ] The never-ending battle against impurities
“No impurities, even down to 100 micrometers.” Such is the standard at the Honsha Plant’s latest addition, the Fuel Cell Manufacturing Division. Established in 2017, the FC team has dramatically improved the contamination defect rate through diligent analysis, awareness raising among members, and working as one team with suppliers.
The division mainly produces FC stacks for the second-generation Mirai.
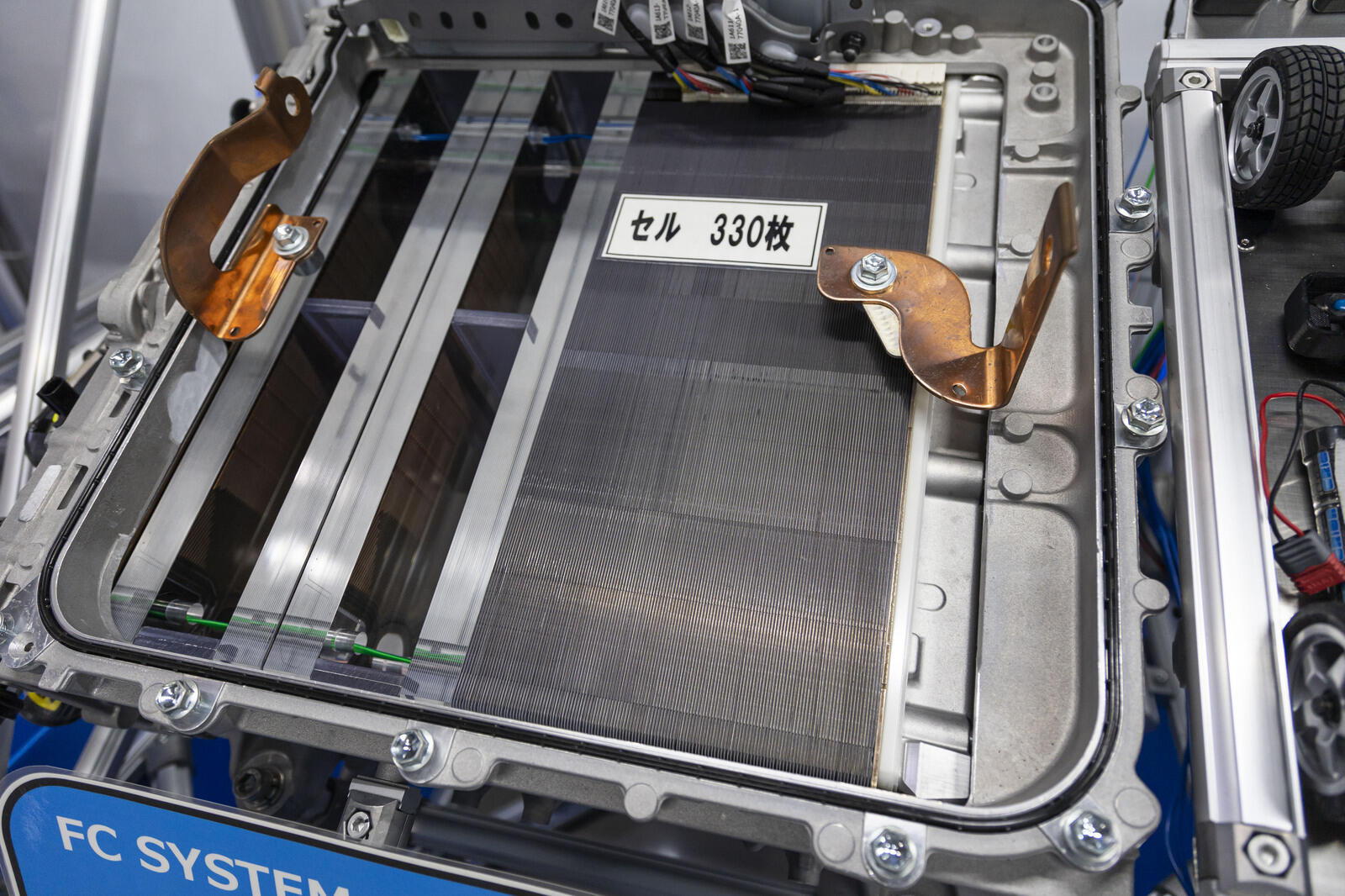
These stacks contain 330 cells, each around 1 mm thick, and deliver significantly better performance than the first generation. On the flip side, even a single fleck of steel as small as 100 micrometers (about 1/50th the size of a rice grain) can degrade a stack’s quality if it gets inside a cell.
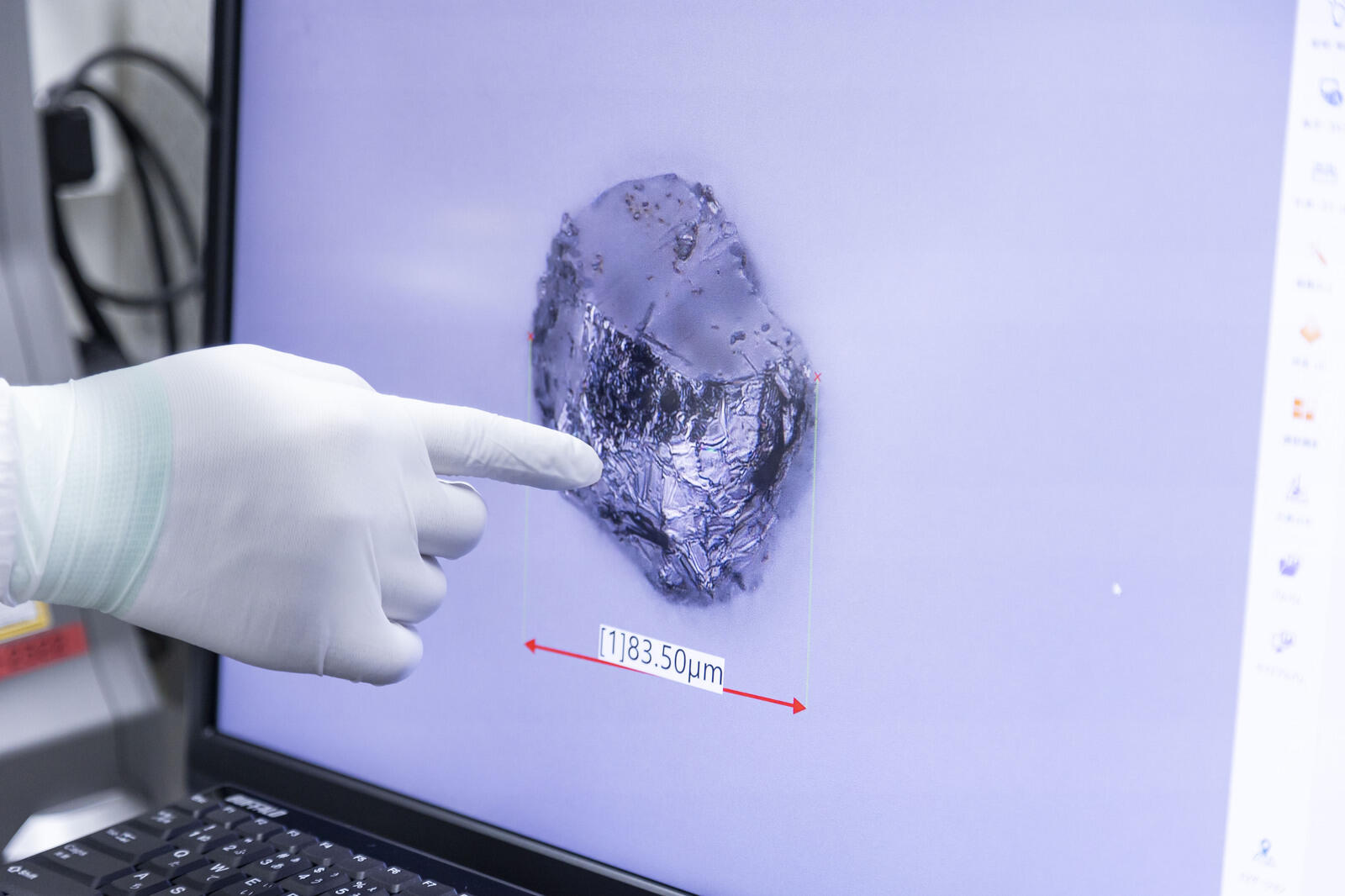
The genba producing these second-generation FC stacks must do so in a monozukuri environment cleaner than any that has come before.
Daisuke Sugisaki, General Manager, Production & Development Dept., Fuel Cell Manufacturing Div.
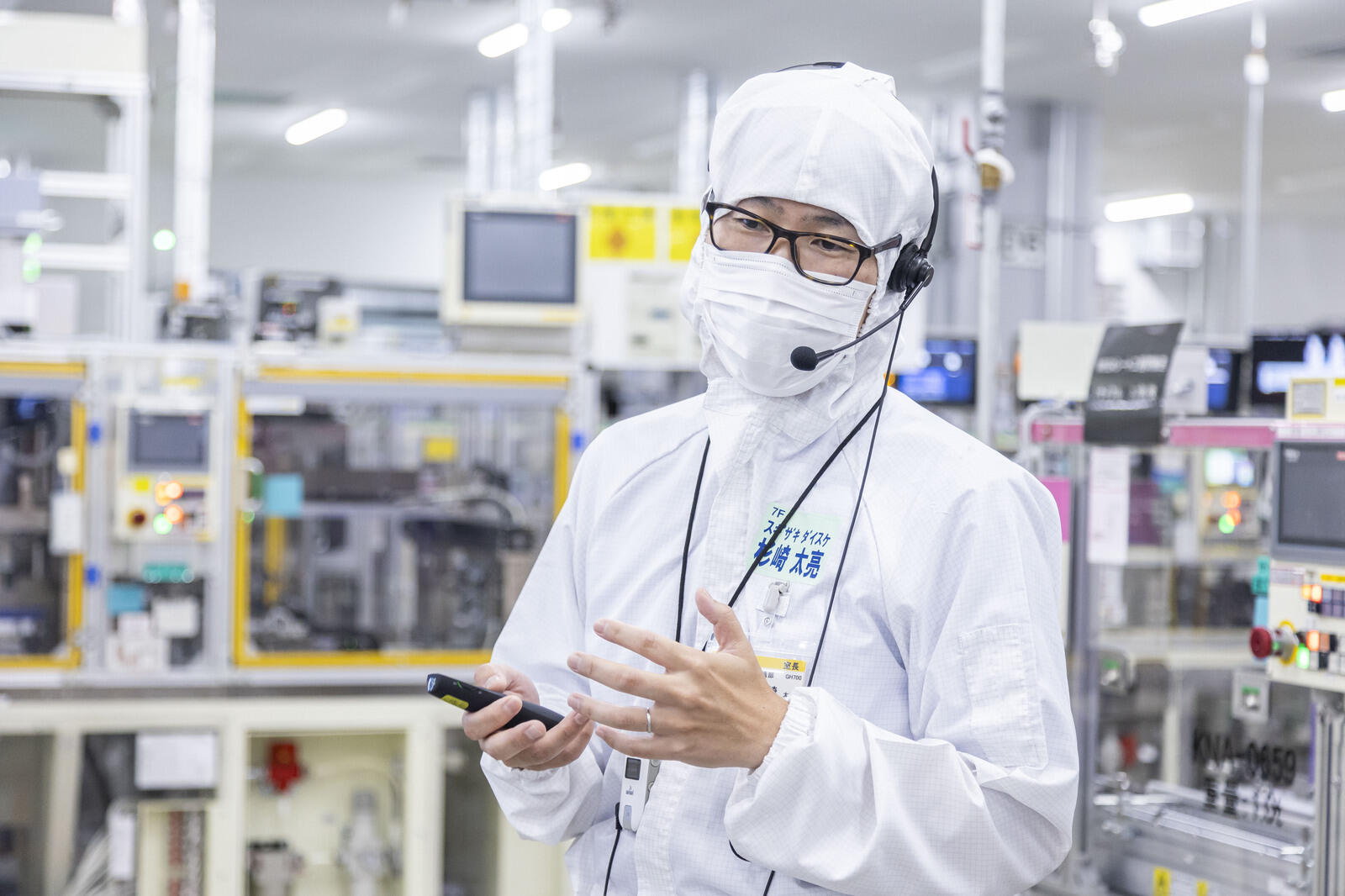
When you talk about clean production facilities, semiconductor fabrication comes to mind, but that requires massive investments in equipment and an environment for purifying air.
Instead, we began by visualizing the “enemy’s” behavior, mapping how 100-micrometer steel contaminants move. By doing so, we found that unlike semiconductor impurities that constantly float around in the air, the steel essentially drops and settles on the floor.
At first, we were worried about all the different measures we would have to take, but in that moment, we realized, “We can deal with this!” and began moving forward.
From there, each of us looked for ways to prevent steel impurities. We adopted three principles regarding contaminants: don’t bring in, don’t create, and eliminate any that arise. Based on these, we were able to get everyone—from design and production engineering to manufacturing, quality control, and our suppliers—moving towards a single goal. At the time, our motto became “Just in Clean.”
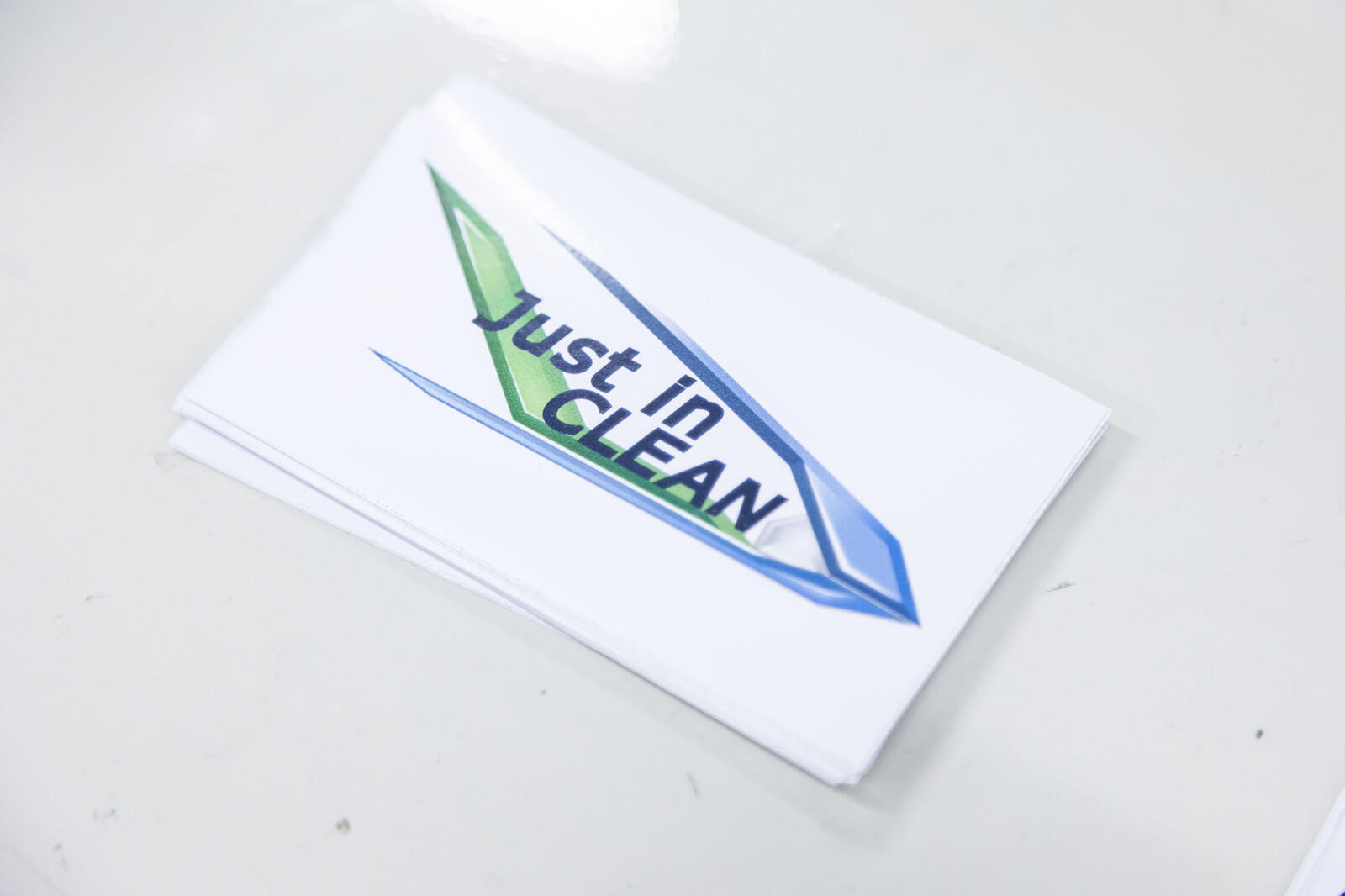
“Apply only the measures needed, where they are needed, and at the level needed.” It’s about using brains, not money.
The division was able to bring everyone together to tackle contamination from the equipment and surroundings, yet even more important was the mindset of those working in the genba. For products like FC stacks that generate electricity via chemical reactions, impurities directly affect quality, and the genba serves as the final line of defense. To foster a cleanliness culture, the division set up the Contaminants Lab.
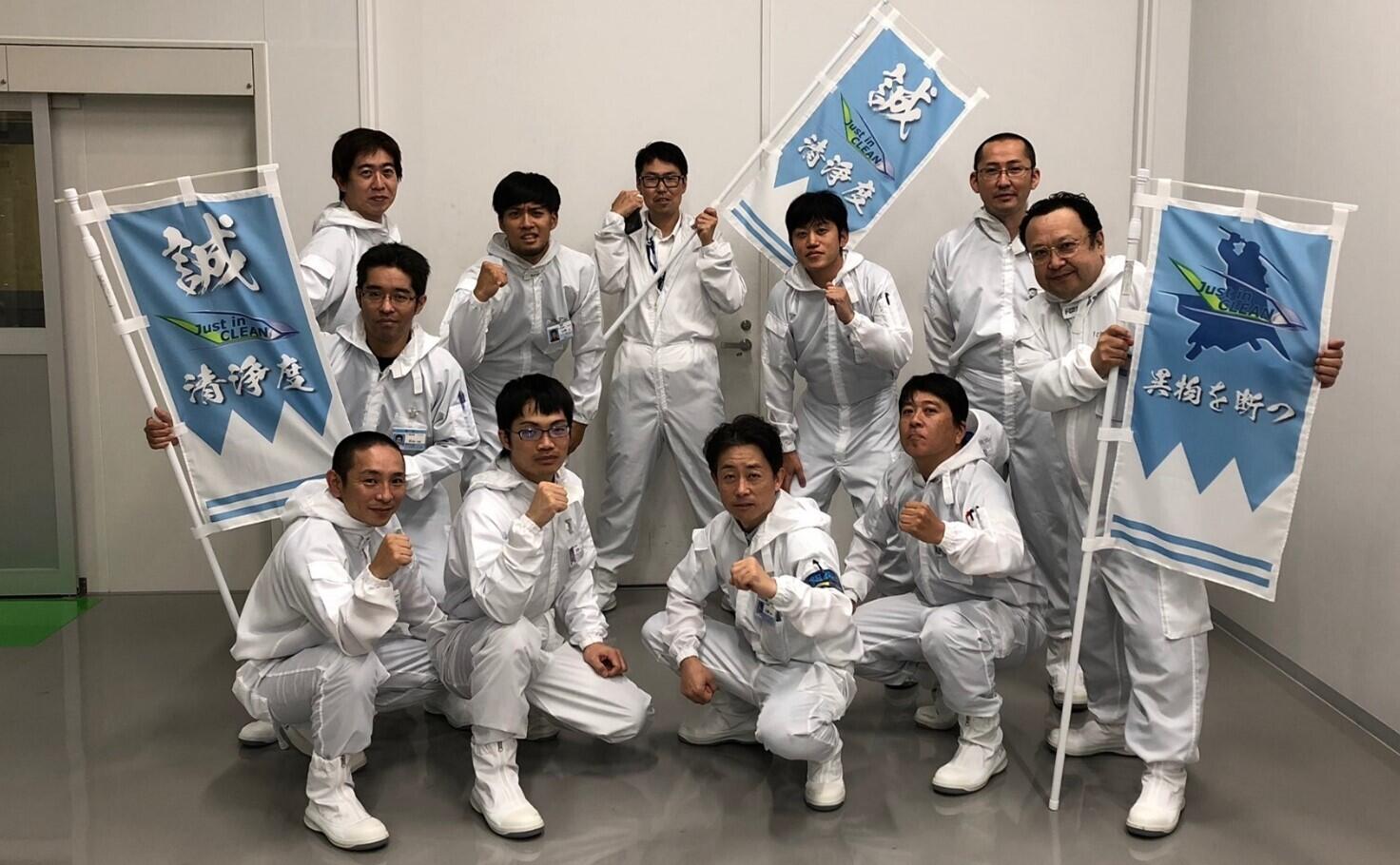
Comprising genba members, the team uses cutting-edge electron microscopes and X-ray analyzers to swiftly examine foreign matter found on products or equipment. Within hours, the production floor receives feedback and sets about making improvements.
Whereas sending the job to an analysis provider would normally take a week, the lab can provide results and feedback in as little as an hour. This powerful analysis squad was placed right at the heart of the production genba.
What’s more, the team treats processes performed by materials suppliers as its own. By analyzing thousands of samples and sharing them with suppliers, they improved the defect rate from over 1% in February 2020 to around one-hundredth of that by December 2022.
Their slogan is “Cleanliness = Quality = Genba Strength.” In other words, Toyota’s frontline capabilities stem from improvements driven by a deep-rooted commitment to keeping a clean genba.
The Contaminants Lab has become an indispensable part of FC production.
Masahiro Kondo, Group Leader, Manufacturing Support Section, Fuel Cell Manufacturing Div.
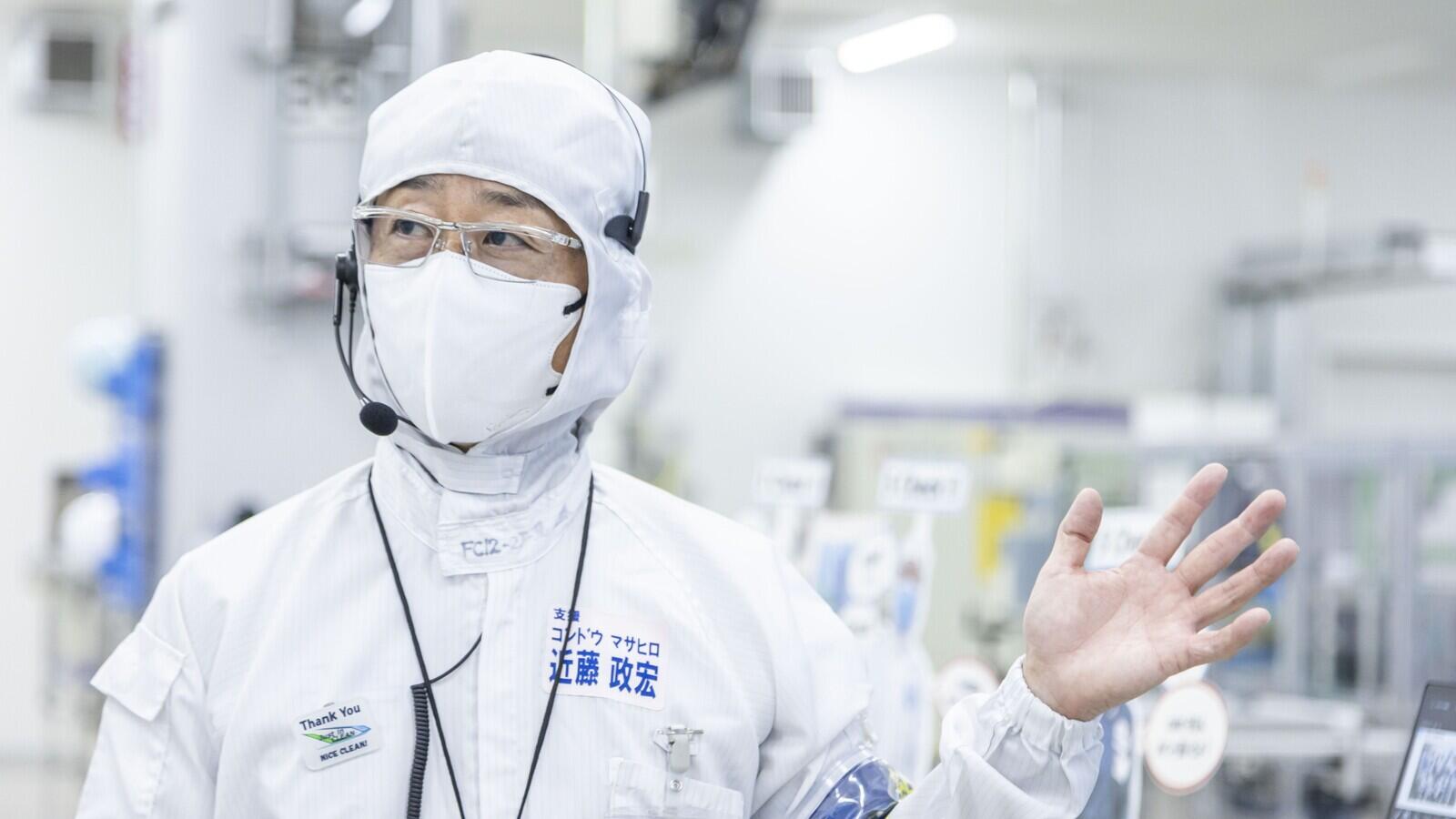
To prevent impurities, you can’t expect to motivate people by simply setting rules. The key to maintaining high quality is to change everyone’s mindset.
That’s why we set up the Contaminants Lab as a fun way to raise awareness and boost cleanliness.
Initially, the entire genba came together as one team, regardless of department or role, to perform a thorough cleaning. Since then, we’ve continued to share ideas on how to make the site cleaner and prevent impurities, creating a workplace where everyone is united around a shared purpose.
As people grow, so does the genba. Today, we have a rising number of people who can handle analysis equipment like police forensics experts, and everyone is enjoying working together to make constant improvements.
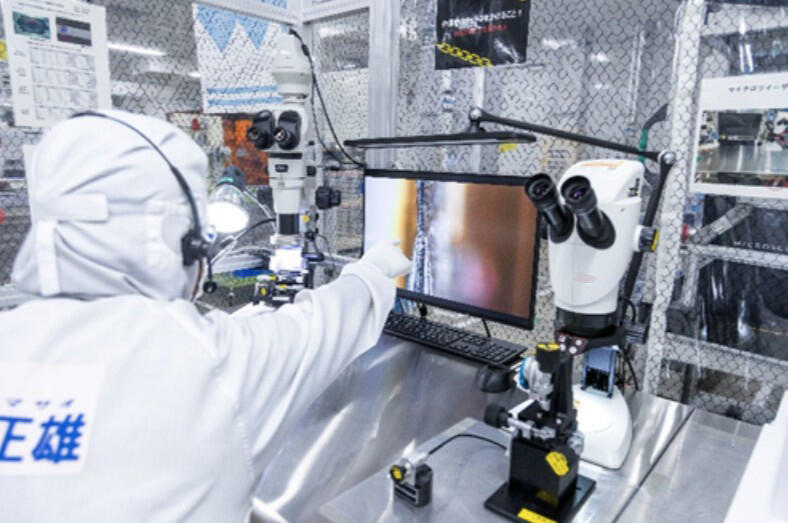
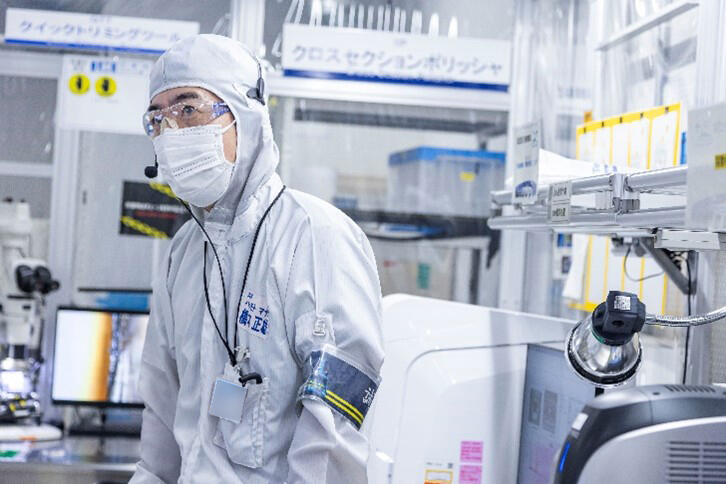
Formerly a welder, Manufacturing Support Section Team Leader Masao Hashimoto is now a master of impurities analysis with the skills to eliminate 100-micrometer contaminants from products.
The FC stacks and various other technologies developed for the Mirai are now used in applications ranging from trains and ships to power generators, as people and products alike continue to evolve.