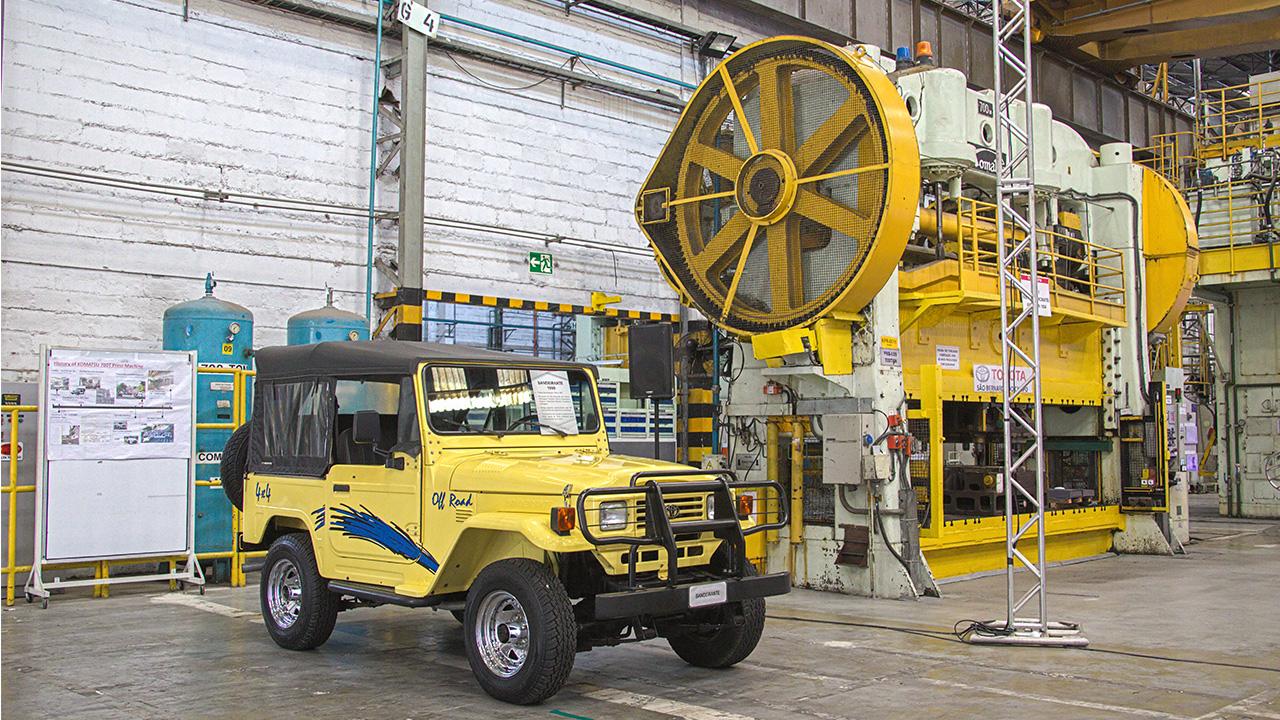
"Have you ever considered why we are manufacturing in South America?" This was the question Akio Toyoda, then-President of Toyota, posed to the Toyota Latin America Chief Executive Officer, who had come to discuss the plant's closure.
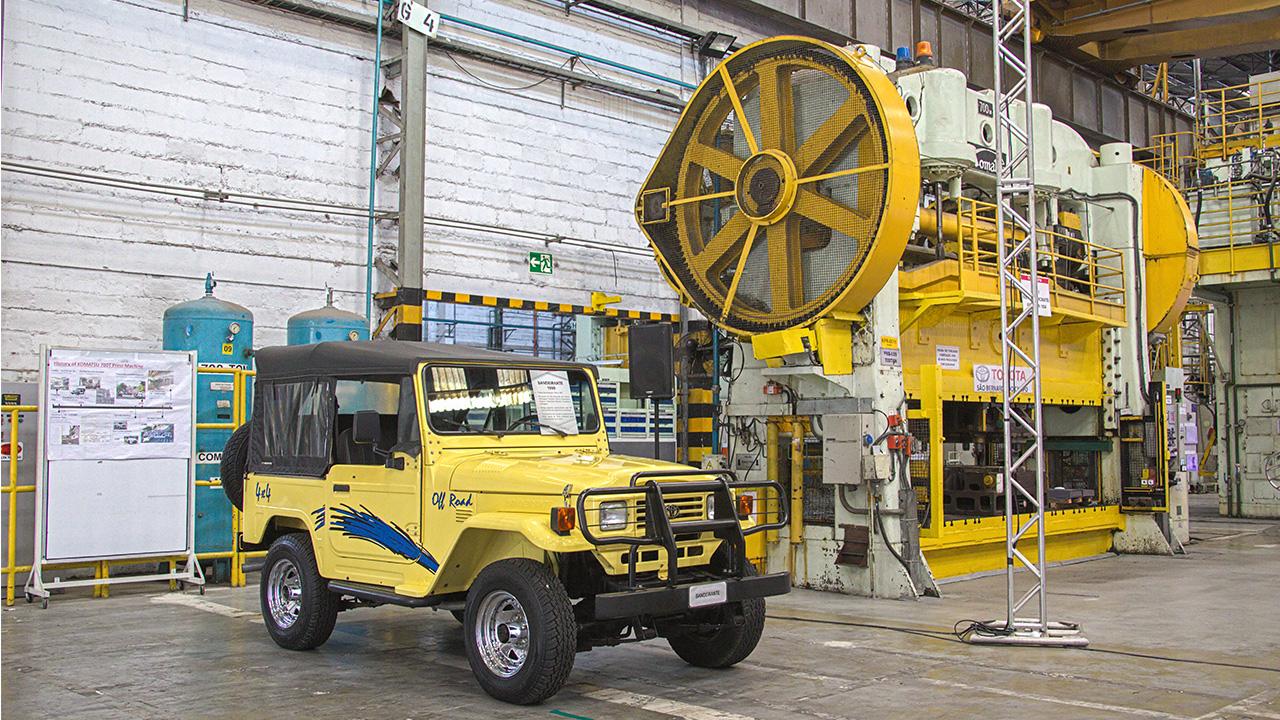
The Sao Bernardo Plant, Toyota’s first overseas plant, concluded its production on November 11, 2023, ending its 60-year history in Sao Paulo, Brazil.
Starting operations in 1962, the plant produced over 100,000 Bandeirantes* by 2001. Recently, it had been manufacturing parts for models like the Corolla and Hilux.
*Brazilian version of the Land Cruiser, whose name means “pioneer” in Portuguese.

Its production has been consolidated into three other plants in Sao Paulo to enhance competitiveness.
At the closing ceremony, Masahiro Inoue, Chief Executive Officer of Latin America & Caribbean Region, expressed his determination: “While the history of production at the Sao Bernardo Plant may be coming to a close, it allows us to take flight into the future. Together with the employees and their families who have relocated (due to the production transfer), Toyota will produce ever-better cars and expand exports to Latin America. We are committed to contributing to the further development of Brazil’s automotive industry.”
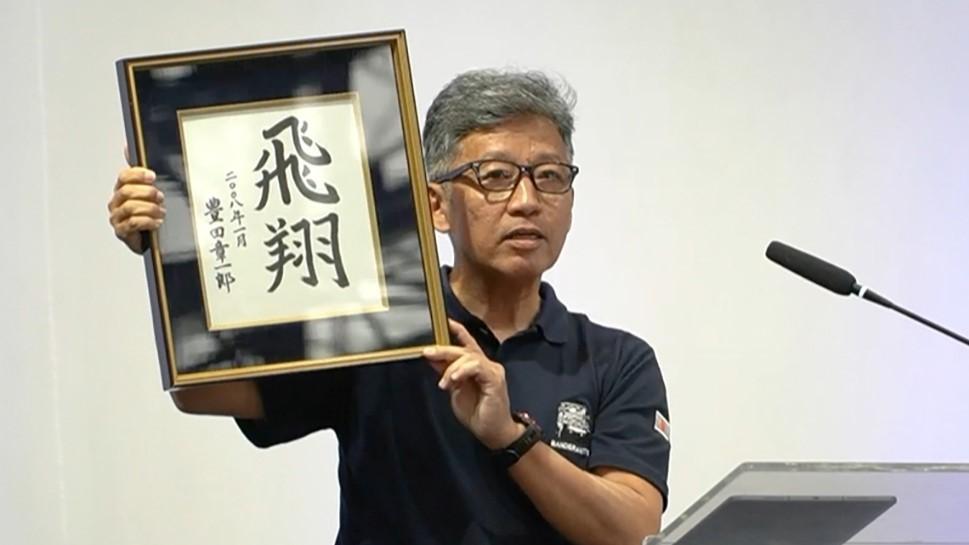
The decision to close Toyota’s most historic overseas plant was significant. Three years ago, Inoue nervously approached then-President Akio Toyoda for consultation and was asked, “Have you ever considered why we are manufacturing in South America?”
What did this question imply? And what significance did this plant hold for Toyota? We delve into these questions through the testimonies of the people involved.
Toyota’s first overseas plant
The Sao Bernardo Plant began operation in 1962 when Toyota only had two plants in Japan—its headquarters and the Motomachi Plant (opened in 1938 and 1959, respectively, both in Toyota City, Aichi Prefecture).
At that time, Toyota’s production volume was 230,000 vehicles. Compared to the group’s global production of 10.61 million units in 2022, this represented a modest beginning at merely 2% of that scale.
In the 1950s, Toyota considered expanding its operations overseas, and Latin America was a potential region. Brazil, with its vast territory and the largest population in the region, was seen as a promising market.
Furthermore, the existence of the world's largest Japanese immigrant community is also cited as one of the reasons for the choice.
The turning point came in 1956 when the Brazilian government passed an act to promote a domestic automotive industry that effectively banned the import of finished vehicles. This prompted European and American manufacturers to consider expanding their operations locally.
Toyota established Toyota do Brazil in 1958, rented land in Sao Paulo, and in May of the following year, the Bandeirante, Toyota’s first overseas production vehicle, was born.
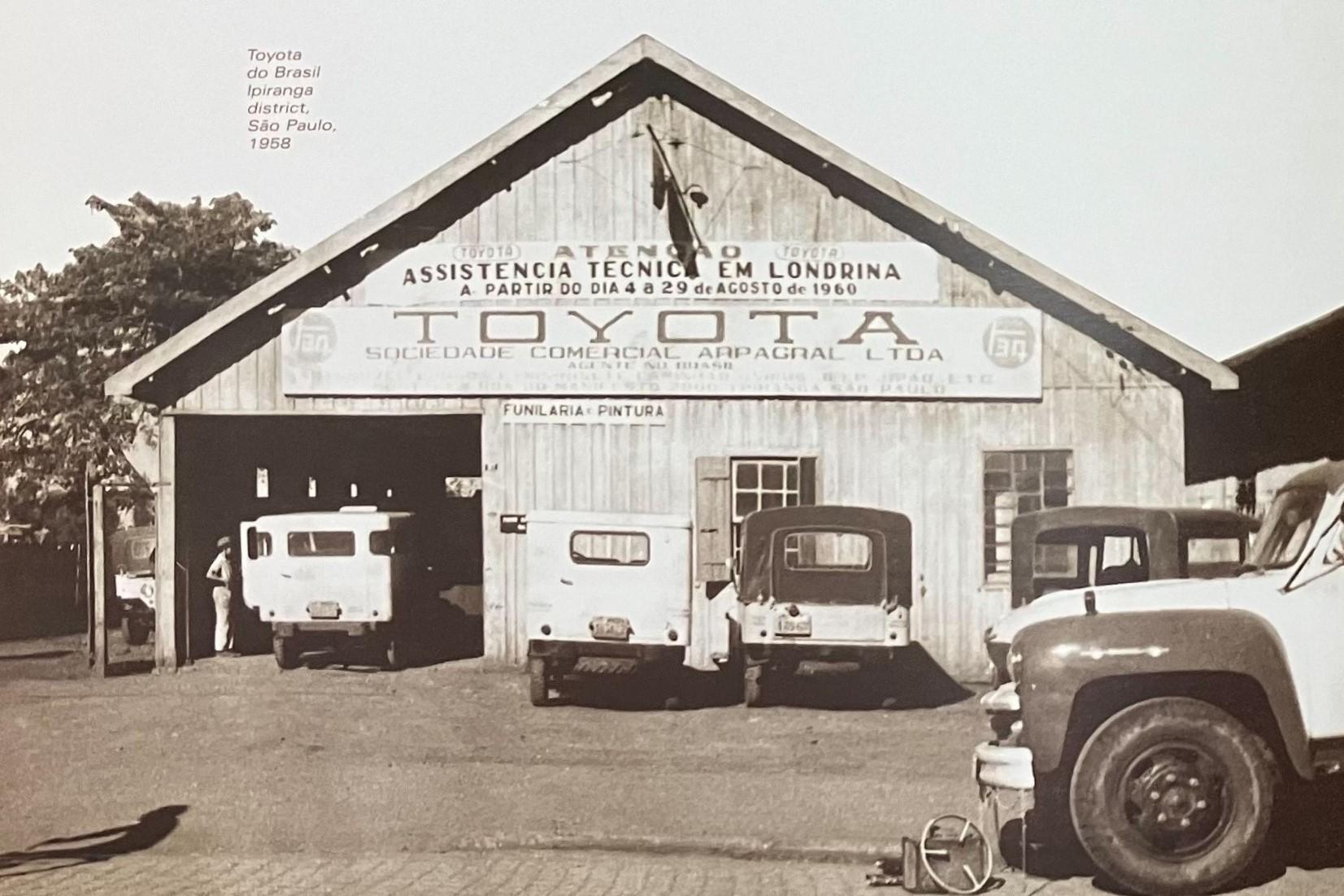
This vehicle contained approximately 60% Brazilian-made parts, but the government’s domestic production demands increased yearly. The Sao Bernardo Plant was established as a full-fledged vehicle plant to comply.
The engines were locally sourced from other companies. In 1968, Toyota achieved 100% domestic production of previously imported drive components, like transmissions and differentials.
At the time, Brazil had a high demand for robust vehicles, primarily for agriculture and livestock. In response, Toyota launched the Bandeirante, originally developed for the National Police Reserve (now the Self-Defense Forces) in Japan, where it was highly regarded.
The Bandeirante, renowned for its ability to effortlessly conquer challenging terrain like mud, dust, and watersides without breaking down, significantly reinforced Toyota’s brand image as being synonymous with “reliability” and “durability.”
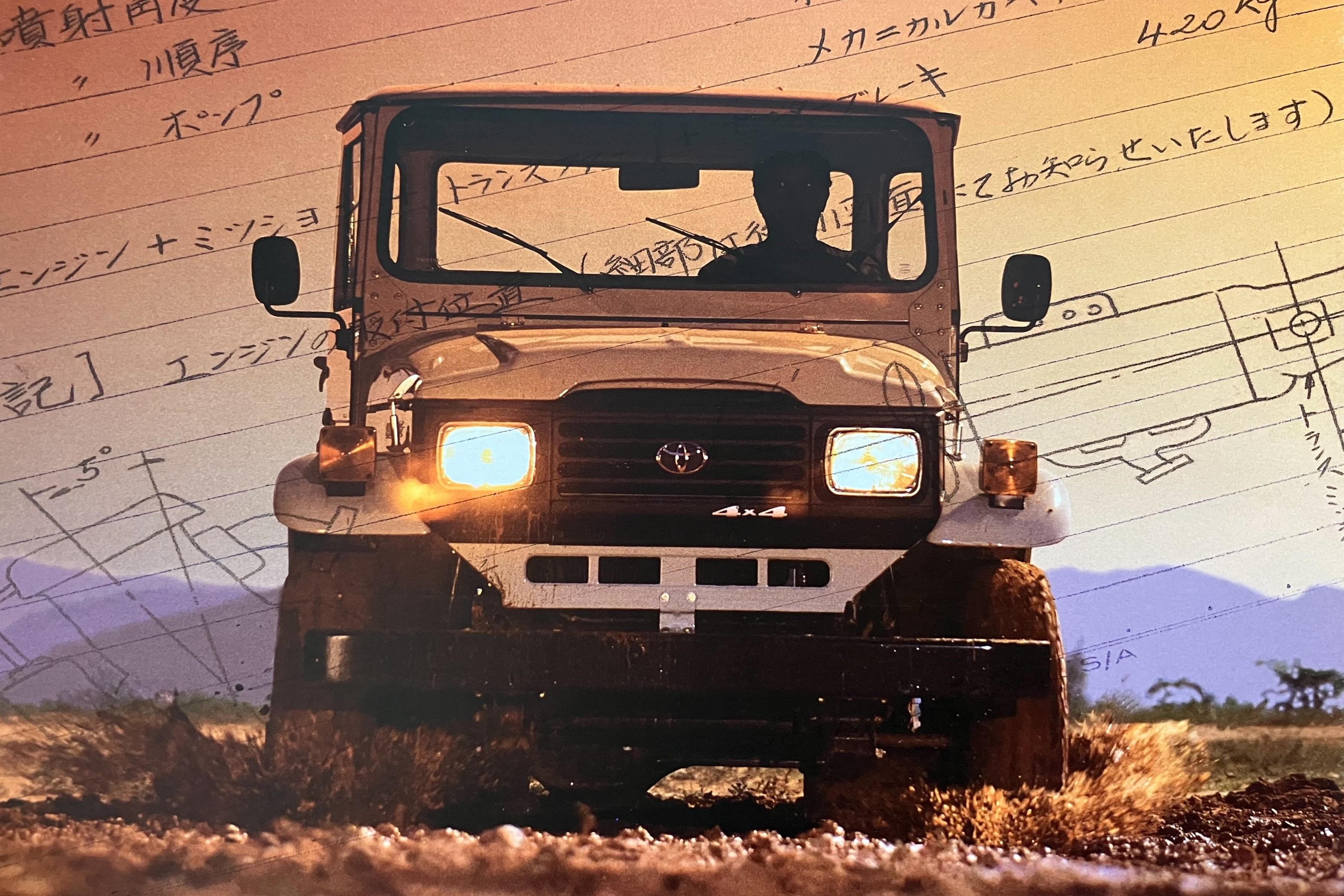
A plant preserving the footprints of Toyota’s founding
The Sao Bernardo Plant is distinguished by its numerous stories from Toyota’s founding period.
With the plant’s closure, its press machine will come home to Japan after 60 years of service. It was originally acquired in 1934, predating the establishment of Toyota Motor Corporation, by the Toyoda Automatic Loom Works Automobile Department based in Kariya, Aichi Prefecture.
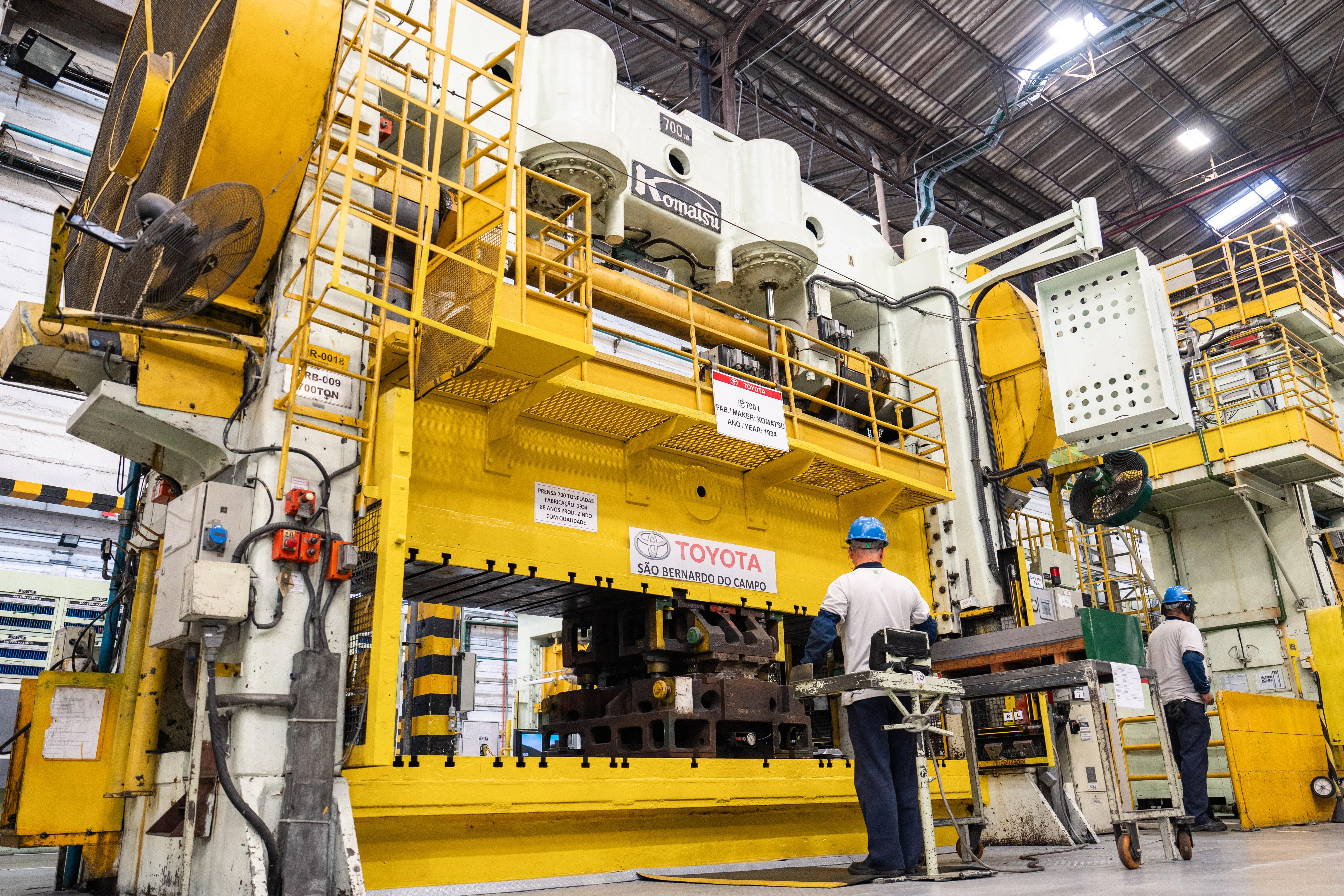
When the Koromo Plant (later the Honsha Plant) was established in 1938, this press machine was also relocated there, supporting the nascent Toyota in car manufacturing.

In 1962, aligning with the inauguration of the Sao Bernardo Plant, the press machine was relocated to the other side of the globe. It has been in active use for an impressive 89 years, producing parts consistently.
Inoue says, “It’s unbelievable that a Japanese company made and purchased such a large item before the war. It must have been incredibly expensive. I speculate that it was largely funded by the money earned from selling Toyoda Automatic Loom Works patents to a British company, which also funded the establishment of Toyota Motor Corporation. I believe it must have been expensive.”
After consultation with Chairman Akio Toyoda, the company decided to preserve this historically valuable press machine through “functional conservation” (maintained in a production-capable state).
The machine will be reinstalled in the same location within the Honsha Plant where it stood 60 years ago, continuing its role in producing spare parts. Additionally, it is slated to be used in training workers in die maintenance and other related tasks.