
自動車業界を匠の技で支える「職人」特集。第4回はWRCマシンのボデーも手掛けた「板金加工の匠」に話を聞く

3DプリンターやAIをはじめとするテクノロジーの進化に注目が集まる時代だが、クルマづくりの現場では今もなお数多の「手仕事」が生かされている。
トヨタイムズでは、自動車業界を匠の技能で支える「職人」にスポットライトを当て、日本の「モノづくり」の真髄に迫る特集「日本のクルマづくりを支える職人たち」をスタート。
今回は、「板金と溶接の匠」 吉野栄祐(よしの えいすけ)を取材した。
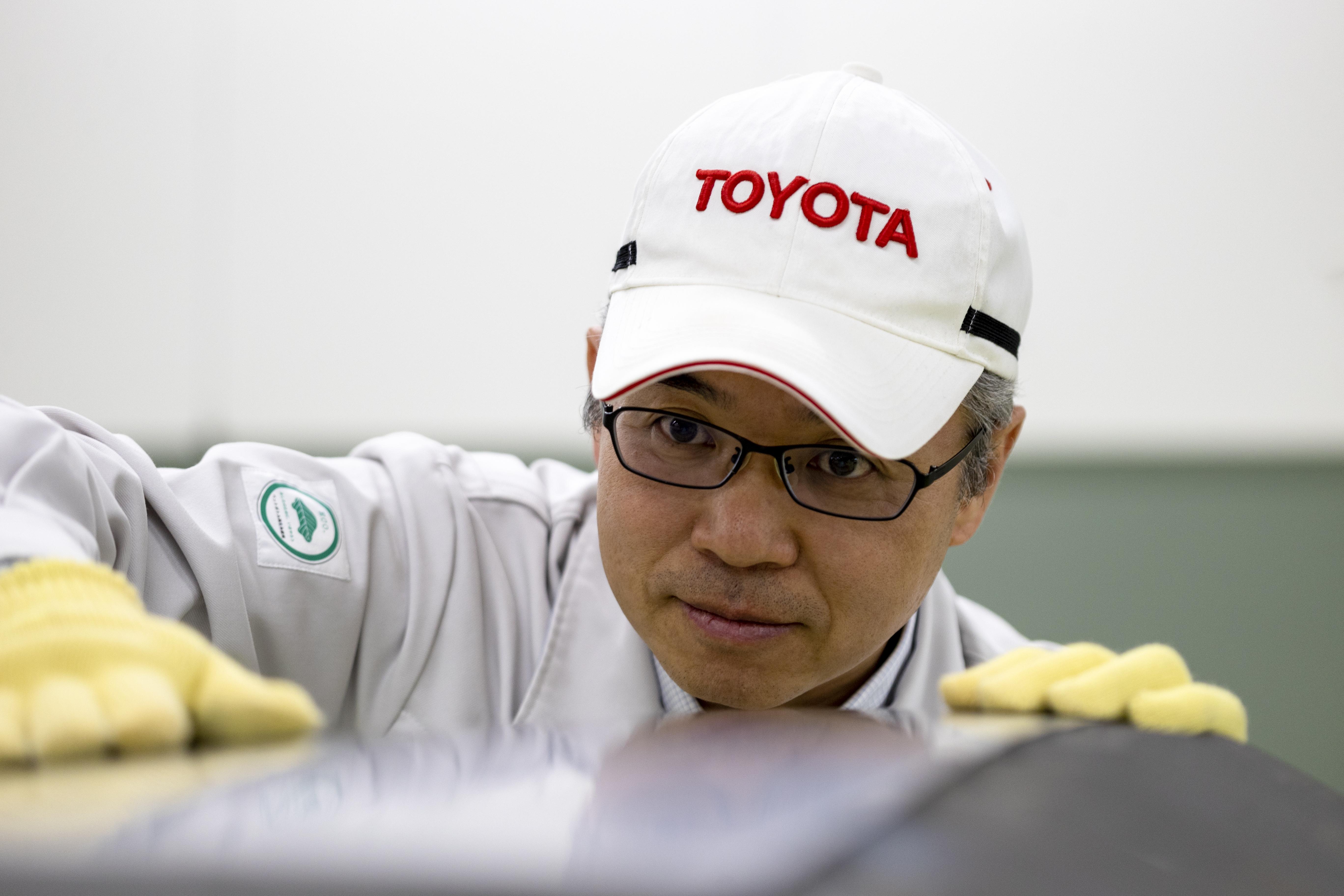
第4回 鋼鉄の板から手作業でボデーをつくる「板金と溶接の匠」 吉野栄祐
トヨタ自動車 モノづくり開発センター 開発試作部 ボデー試作課 吉野工長
ハンマーと溶接で試作車のボデーを手づくりする
クルマのボデーがどのようにつくられるのかご存じだろうか?ボデーづくりの最初の一歩は、まずデザイナーがクルマのデザインスケッチを描くことから始まる。そしてこのデザインをベースに、設計部門が最先端の3D設計ソフトでクルマ全体の、さらにクルマを構成するさまざまな部品の設計図を制作していく。こうしたなかの一部としてボデーの設計図がつくられる。
最近ではこの3D設計ソフトのデータで工作機械を制御し、いきなり部品をつくってしまう手法も使われる。ただ、普通の部品と違いサイズの大きなボデーのパーツをつくる場合は、こうした手法を用いることはできない。
一般的に生産車のボデーは、大型のプレス機を使って、プレス加工で大きな鋼板を一気にボデーの形状に仕上げる方法でつくられている。この際にも、3D設計ソフトのデータが活用されている。だが、こうしたプレス加工による大掛かりなボデーづくりには、大型の金型が必要だ。
しかし、ボデーをつくるための大型の金型は、それを製作するだけでも巨額のコストと時間がかかる。生産車のボデー製造では問題ないが、新型車の試作段階ではこの方法は使えない。
新たに開発されたクルマは、まず試作車としてこの世に誕生する。この試作車を使って、機能、安全性、耐久性や品質などに問題はないか、さまざまテストを実施し、徹底的な検証が行われる。何十台もの試作車がつくられては壊され、そこで明らかになった問題点を解決することで、クルマはようやく商品として完成し、生産・販売できるものになる。
この試作車のボデーづくりの主役になるのが、今から90年近くも前の1935年にトヨタが初の試作自動車「トヨダA1型」を製造した時にも活躍した板金職人だ。平らな鋼板を、ハンマーでたたいて曲げて絞って、必要なら溶接で鋼板を付け足して、さらにたたいて曲げて絞るという、極めてアナログな方法である。
トヨタでこの仕事を担当するのが、モノづくり開発センター 開発試作部 ボデー試作課であり、その現場を率いるのが工長の吉野栄祐だ。吉野はこの「図面なし板金部品加工、造型技能」の分野で2020年、トヨタ全社でもわずか十数名しかいない「S級」技術者に認定されている。

吉野はボデー試作課のリーダーであると同時に、トヨダA1型に始まるトヨタの板金職人の源流技能を継承し、未来に伝える使命を担う。トヨタ社内でも最高峰の技能を持つ「板金と溶接の匠」である。
3Dデータを見て、ゼロから、どうつくるかを考える
「試作車のボデーづくりはまず3D設計ソフトのビジュアルデータをディスプレイで見ることから始まります。画像をパッと見て、どのくらいの大きさなのか、これだったらどこからつくっていこうか。使う素材の厚さや材質も考慮し、まず鋼板のどこをどのように曲げて、次にどこをどう曲げるのか。どんな順序でどのように作業を進めていくのか。どうすれば早く安くいいものにつくれるかを、板金職人が過去の経験をもとに、ゼロから考えて製作します。使用する治具も自分で作ります」
吉野は3Dの設計データを見た瞬間に「どうつくるか」、つくり方のイメージが頭に浮かぶという。板金職人としてこのレベルに到達しないと、この仕事はできない。到達するまでには、最低でも5年から10年ほどかかるという。
「つくり方は一つではありません。同じものでもつくり手によって、またその試作車をどんな用途に使うかでも、変わります。つくり方の“正解”はたくさんある。だから、現場で指導する際は『自分なりのやり方を自分で考える』ように促します」
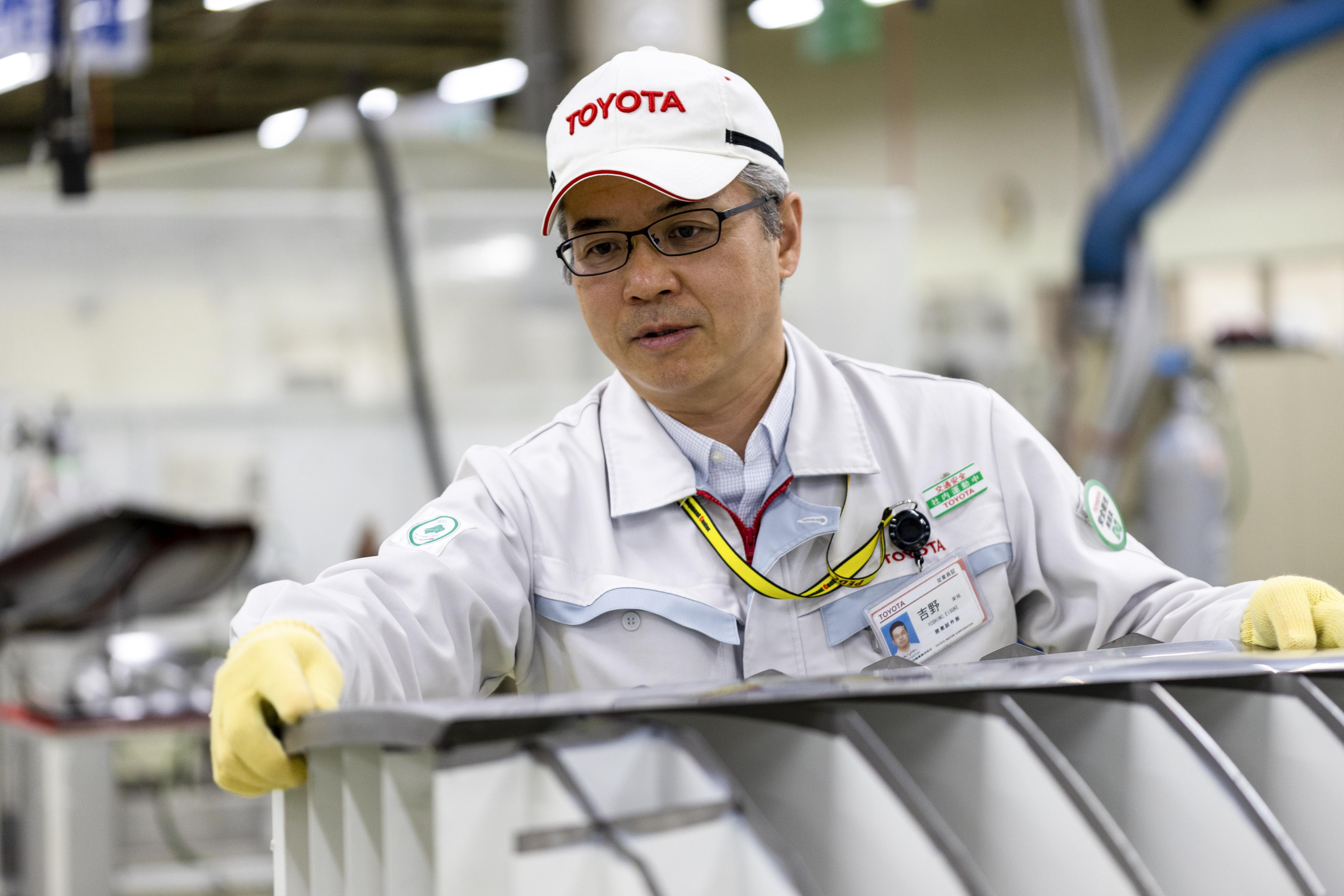
どのつくり方を選択するかは、担当者が自分の技能と、試作するボデーの用途を考慮して決定する。衝突安全試験に使うのか。それとも耐久試験に使うのか、見栄えをチェックするためだけに使うのか。それによってつくり方も変わる。
「試作するボデーの用途を確認し、その要求に合ったものを、もっとも早くもっとも安く、もっとも質が高くつくることができるのはどの方法なのか。それを考えてつくり方を決めます。他部署に切削やレーザー加工、プレスなどの作業をお願いすることもあります。自分たちの手作業と組み合わせ、ベストな方法でボデーを製作します」
3Dの設計ソフト上では、設計者は自由に形状を描くことができる。だが実際のボデーづくりはそうはいかない。サイズが大きなボデー部品は、どこかで切り継ぎしてつくる。つまり設計図には描かれていないが、どこかで分割して溶接で継いでつくる、いわゆる「切り継ぎ」をしなければならない。だが、切り継ぎをした部分は強度が落ちる。切り継ぎするなら、目的や用途に応じて強度の問題がない部分で行わなければならない。設計データに描かれた部品を、どこでどう切り継いでつくるか。この判断も長年の経験が物を言う。
開発中の新型車。その試作車のボデーを素材である鋼板から、治具も自分で手づくりしながら、設計データに沿って0.1mm単位まで正確に、しかも目的、用途に応じて限られた時間で、何十台も手作業で製作しなければならない。クルマは常に時代の最先端をいく工業製品だが、そのボデーづくりは吉野たち職人の手作業なしに製作することはできない。
プラモデル好き、モノづくり好きの少年
吉野は三重県の出身。1987年3月の入社以来33年間、この手作業によるボデーづくりをほぼひと筋に歩んできた。板金加工に初めて取り組んだのは、トヨタ工業高等学園(現トヨタ工業学園)のとき。学園2年生のときには「打出し板金職種技能五輪訓練生」に選ばれ、入社2年目にはこの職種で全国大会に出場。3年目には日本の全国大会で1位に、さらにこの年、技能五輪国際大会にも出場し2位に入賞。社内で特別表彰を受け、さらに労働大臣賞も受賞している。
「学園に進んだのは自分の希望です。自分で探して『こんな学校があるから行きたい』と両親に言いました。何か、クルマに関わる仕事がしたかった。もっとも、入学した当時、なりたかったのはテストドライバーでしたが。子どもの頃は、よくプラモデルをつくっていました。中学生の頃にはスーパーカブをバラして組み直したことも。学園に入学して板金をやってみたら、意外にスムーズに課題ができた。もともと、モノづくりが好きなので、この仕事に就いてよかったと思っています」
学園の先生や会社の上司たちは、早くから吉野の類いまれなるセンスと技術の可能性を見抜いていたのだろう。吉野は入社当初からボデーの試作部門に配属され、技能五輪での活躍を経て、ボデーを改造する仕事に就く。そして現場でその才能を発揮することになる。
「技能五輪には決まった課題があるのですが、現場で仕事を始めてみると、決まった仕事はひとつもない。最初は戸惑いましたが、面白くなってきました。当時はちょうど『セリカGT-FOUR』がWRC(世界ラリー選手権)を席巻していた時期。セリカGTの外観はそのままに、ボデーパネルを薄い鋼板に代えて軽量化。さらに部品で補強してつくったホワイトボデー(エンジンなどを載せる前の状態)をヨーロッパのTTE(トヨタ・チーム・ヨーロッパ)に送る仕事もしていました。そのクルマが優勝すると、とても嬉しかったですね」
こうしたラリー車用に市販車のボデーを改造する仕事や、現行車をマイナーチェンジする際にそのボデーを改造して評価用の試作ボデーを製作する「ボデー改造」の仕事に続いて、吉野が手掛けてきたのが特殊板金。アルミやステンレス、銅やチタンや特殊合金など、加工が難しい素材を使った板金部品の試作や、図面や治具もなくデザインスケッチだけを頼りに、モーターショーやおもちゃショーなどに出展するイベント車を製作する仕事だ。
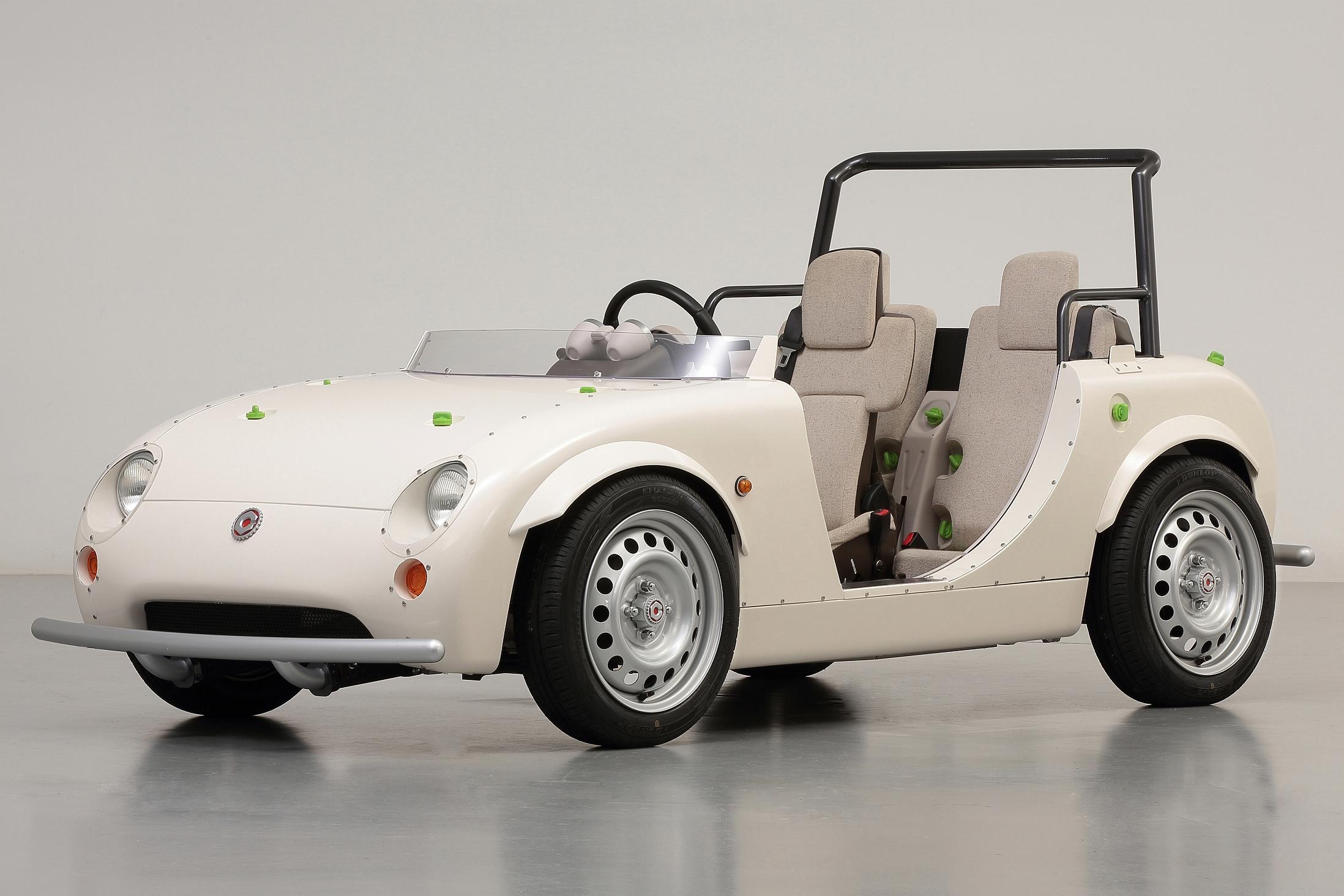
特に2012年から2017年にかけて東京おもちゃショーに出展したイベント車のボデー製作や、ショーでの板金によるモノづくりの実演は思い出深いと吉野は語る。治具なしで、パーツを分割して早く安くつくる方法を考案した結果、コストも作業時間も劇的に短縮することができたという。
勘とコツ、感覚が頼りの板金作業
では吉野の「板金の匠」の技とは? モノづくり開発センターの現場で、ハンマーを使っての手作業を実演してもらった。
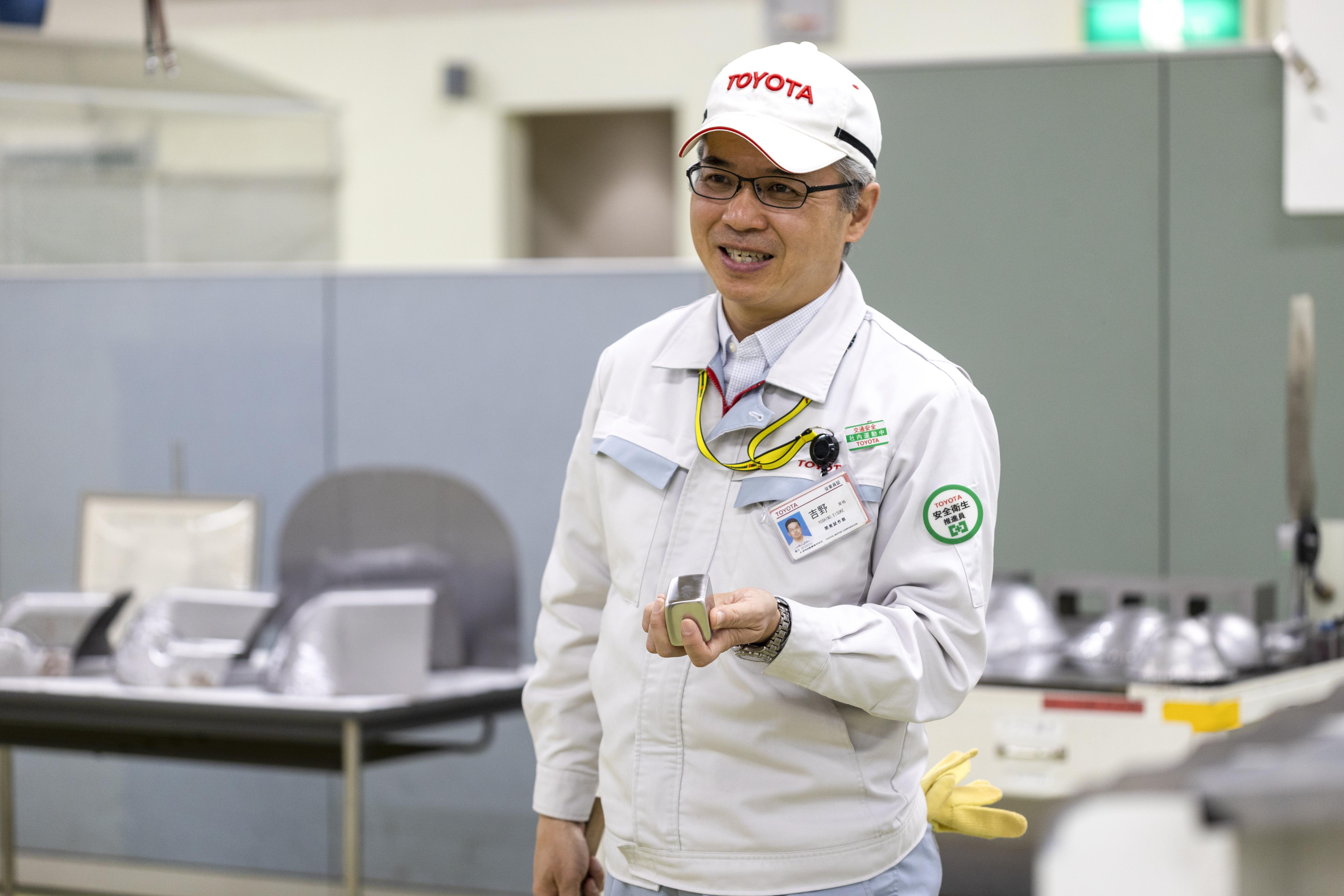
吉野が使う金属製のハンマーや木づち、当て板などの道具はすべて手づくり。使い込まれているが、どれもピカピカだ。特に金属製のハンマーの輝きには驚いた。どれも、自分で素材を選んで加工してもらい、最後は自身の手で仕上げるという。
この部署で働く板金職人はみな自分だけの道具を持っている。工具はたたくモノに合った素材のものでないとダメなのだが、何を素材に使うかも板金職人のノウハウの一つ。特に木づちには、職人それぞれにこだわりの素材があるという。吉野は木材に加えて、ベークライトという樹脂素材のものもつくって使っている。これは技能五輪の世界チャンピオンだった“板金の師”から受け継いだノウハウだ。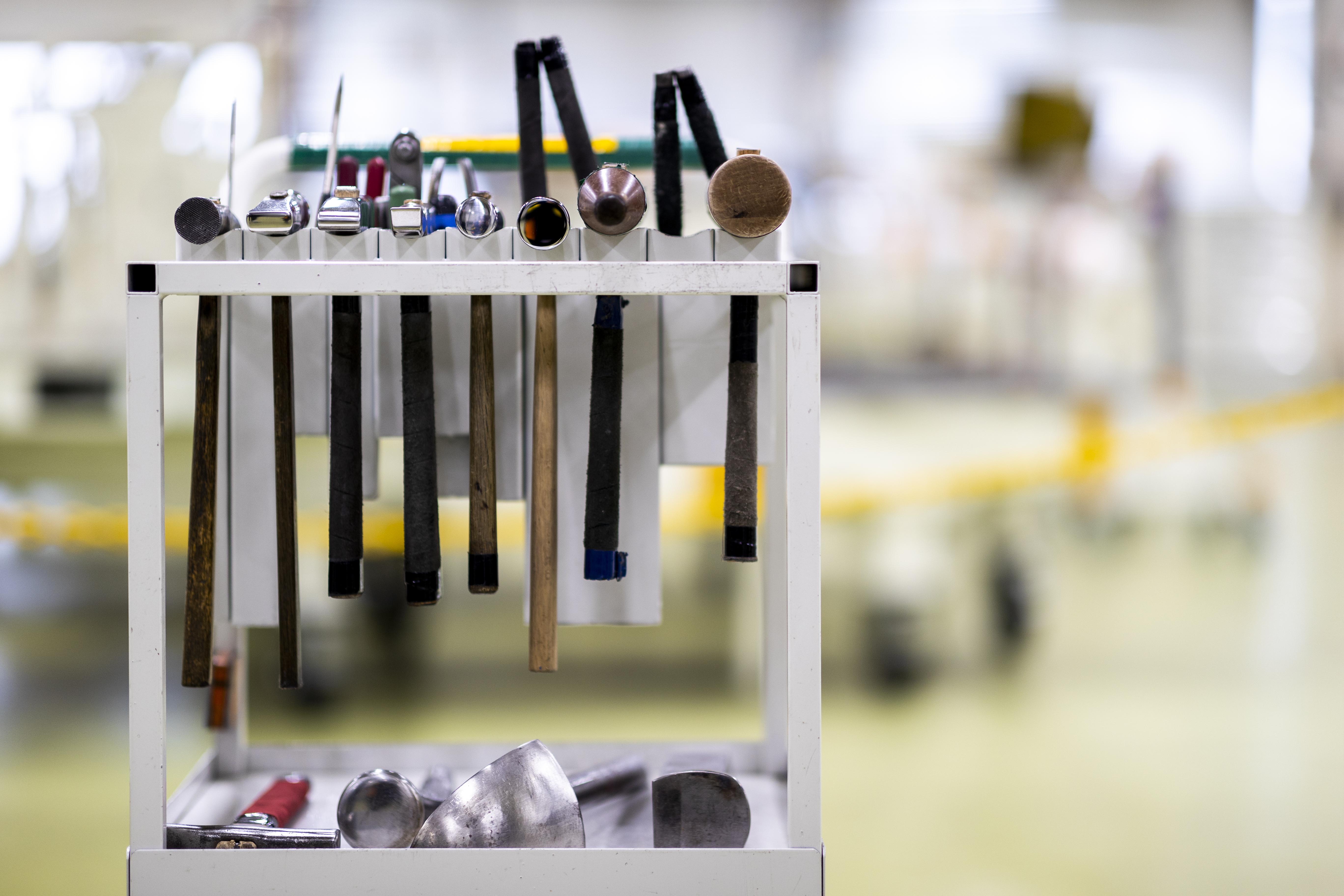
「道具を見れば、特に板金作業でいちばん大事な『ならしハンマー』を見れば、板金職人の技量はすぐに分かります。ちゃんと手入れしてある人は、間違いなくうまい人ですね」
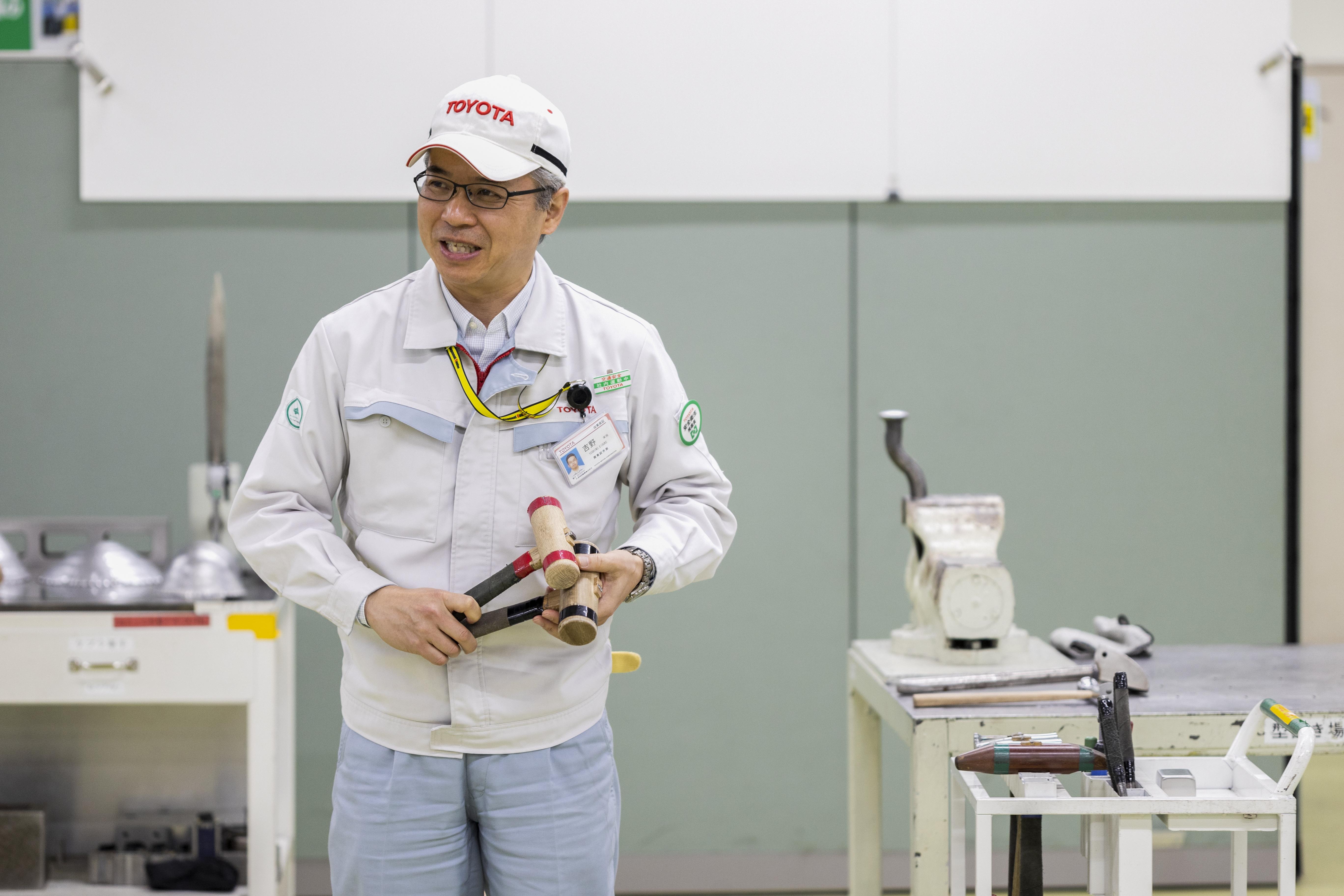
吉野が鋼板を金属製の定盤や木の台に載せてハンマーや木づちでたたくと、平らだったものが、立体へと次第に姿を変えていく。たたくリズムは一定で規則正しい。金属製のハンマーや木づちが奏でる音は、まるで仏教音楽のようだ。
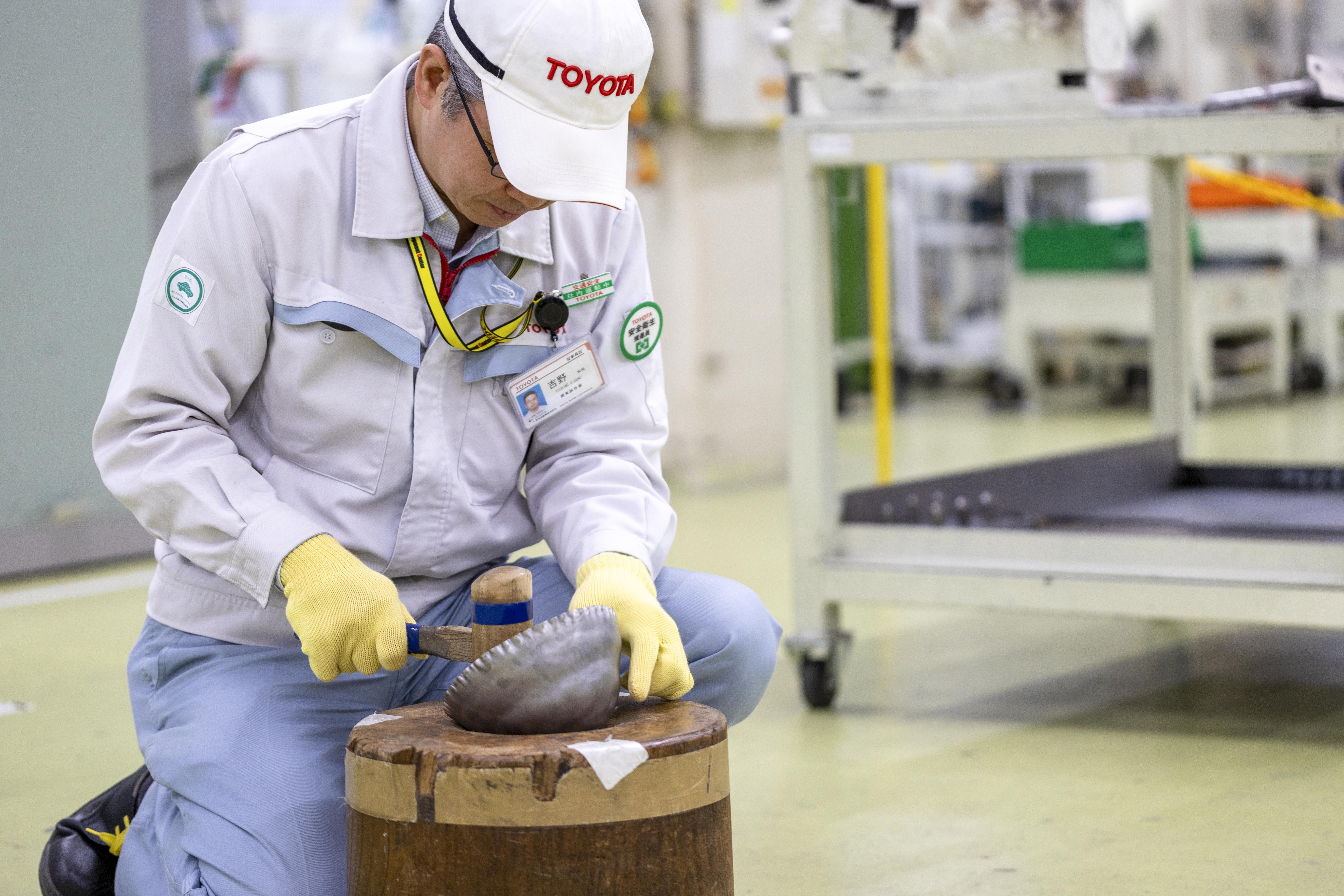
「やってみますか?」という言葉に甘えて、吉野のハンマーを手に定盤の上に平らな鋼板を載せてたたいてみた。形を作るわけではない。ハンマーで板をただたたいただけだ。ところが、同じ金属のハンマーで同じ鋼板をたたいているのに、吉野がたたいたときに出る「キーン、キーン、キーン」という高く澄んだ音とはまったく違う、低くて鈍い音がする。
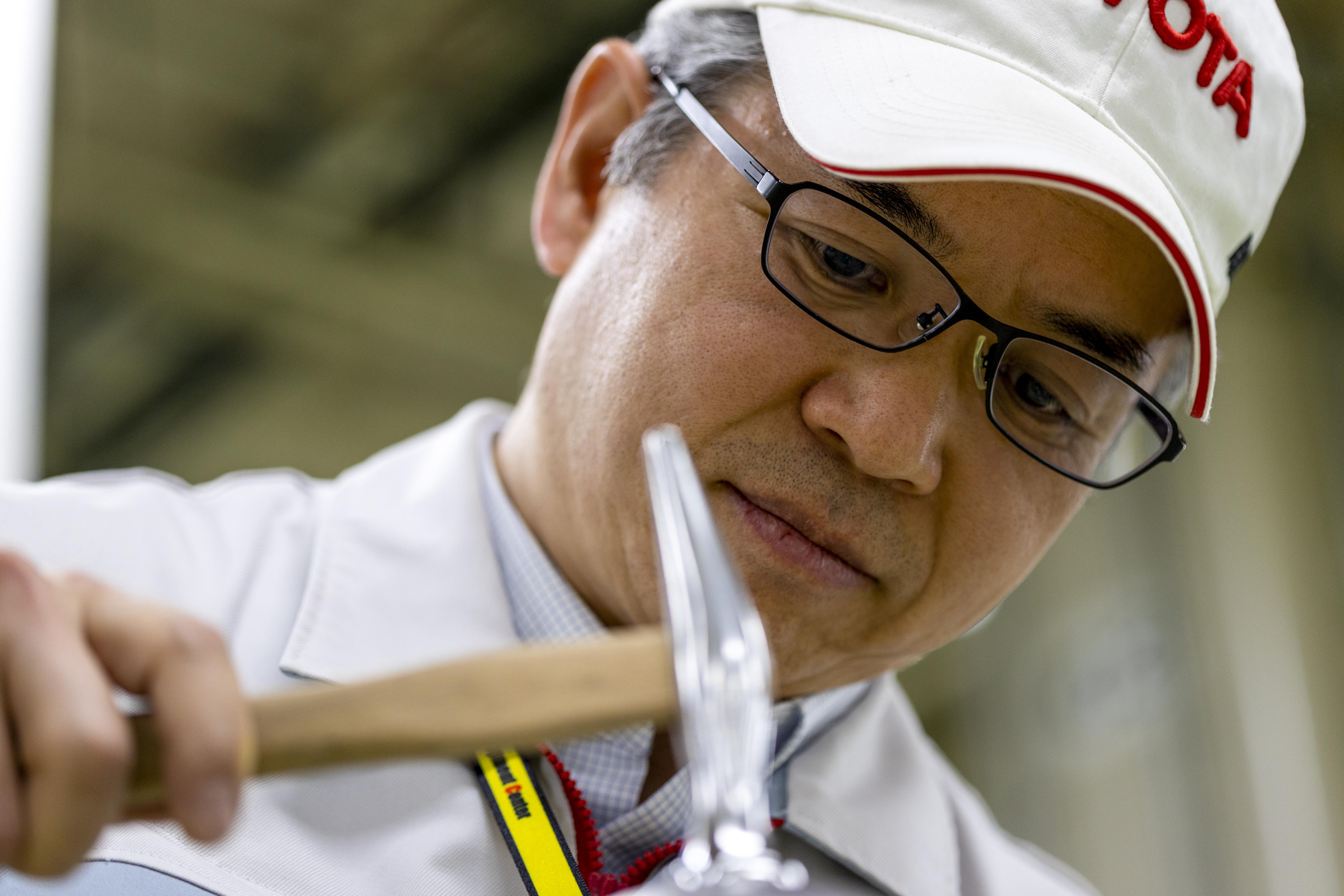
「鈍い音になるのは、定盤との間にすき間があって、ハンマーの力が鋼板にしっかり伝わっていないから。鋼板にひずみが出てしまいます。澄んだ音は鋼板が定盤に密着していて、ハンマーの力がしっかりと鋼板に伝わっている証拠。ハンマーの芯を捉え、その中心でしっかりたたくことができれば、ハンマーがブレずに正確に跳ね返ってきて、気持ち良く正確にたたき続けることができます」
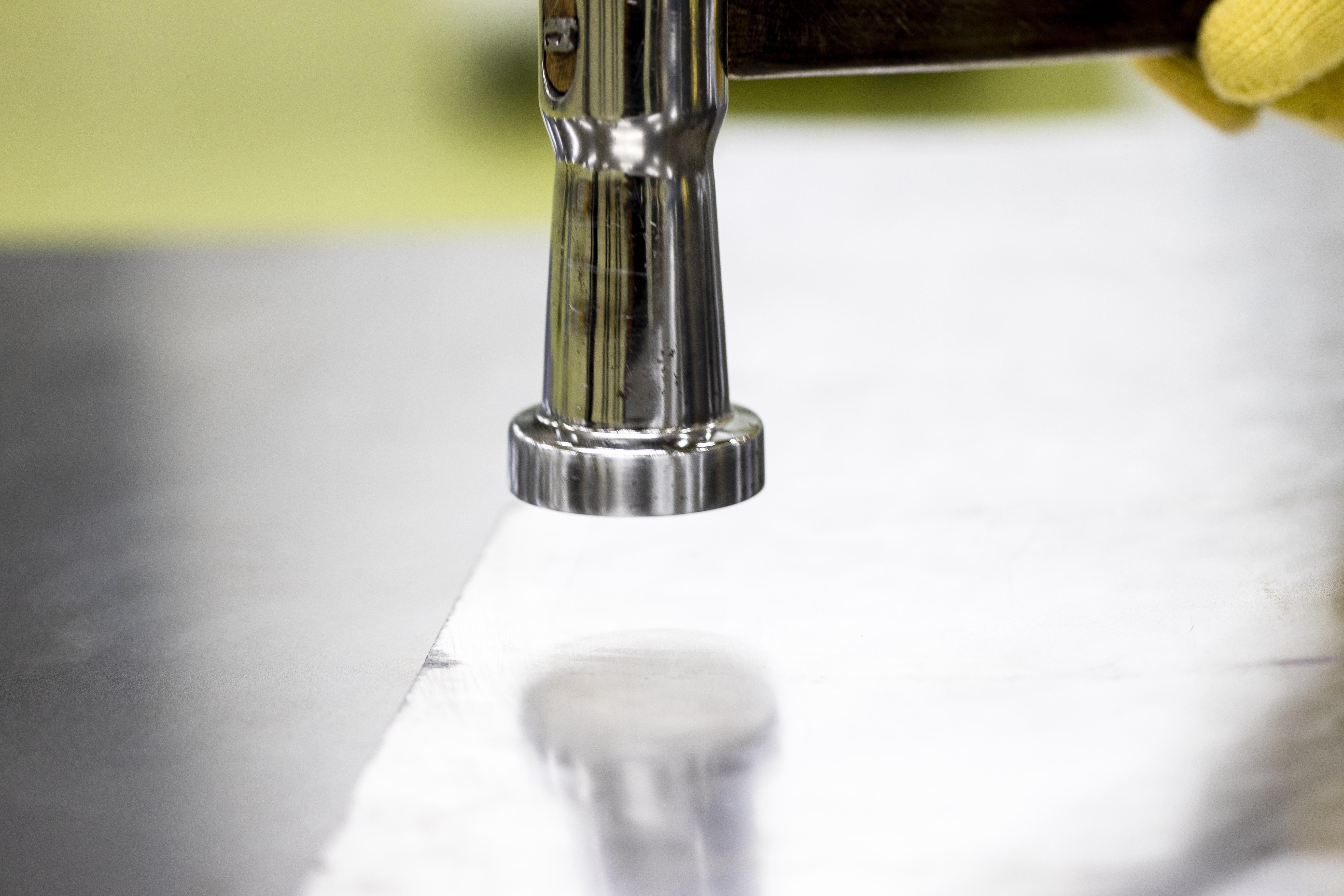

感覚を研ぎ澄まし、音を聞きながら連続して手を動かす。頭だけで考えても絶対にできない。まさに感覚が頼りの「勘とコツ」の世界だ。この感覚だけで、設計データから誤差わずか0.5mmという精度でボデーを仕上げるのだという。
「未来に伝承するためにも、この板金加工の技能を数値化できないか。以前からずっと言われているのですが、正直なところ現状では『数値化は不可能ではないか』と思います。今は後輩を指導する場合も、とにかくやらせてみて、感覚で身に付けてもらうしかない技術ですが、デジタル化やAI技術が進めばいずれは可能になると思います」
板金加工の源流技術を未来へ
伝統的なモノづくりでもそうだが、感覚がモノを言う源流技能の伝承は、とにかく難しい。だが、クルマづくりも、こうした源流技能の継承なしには不可能だ。
吉野は今さまざまなかたちで、現場で自身が身に付けた、最高峰の板金加工技術の伝承に取り組んでいる。職場で後進の指導に当たるのはもちろん、社外でも、職業能力開発大学校で鋼板のひずみ取りの原理や方法を、豊田工業大学校で溶接の指導を行なっている。また、愛知県内の小中学校を対象に「板金加工の匠」としての技を披露し、モノづくりの楽しさ、面白さを伝えている。
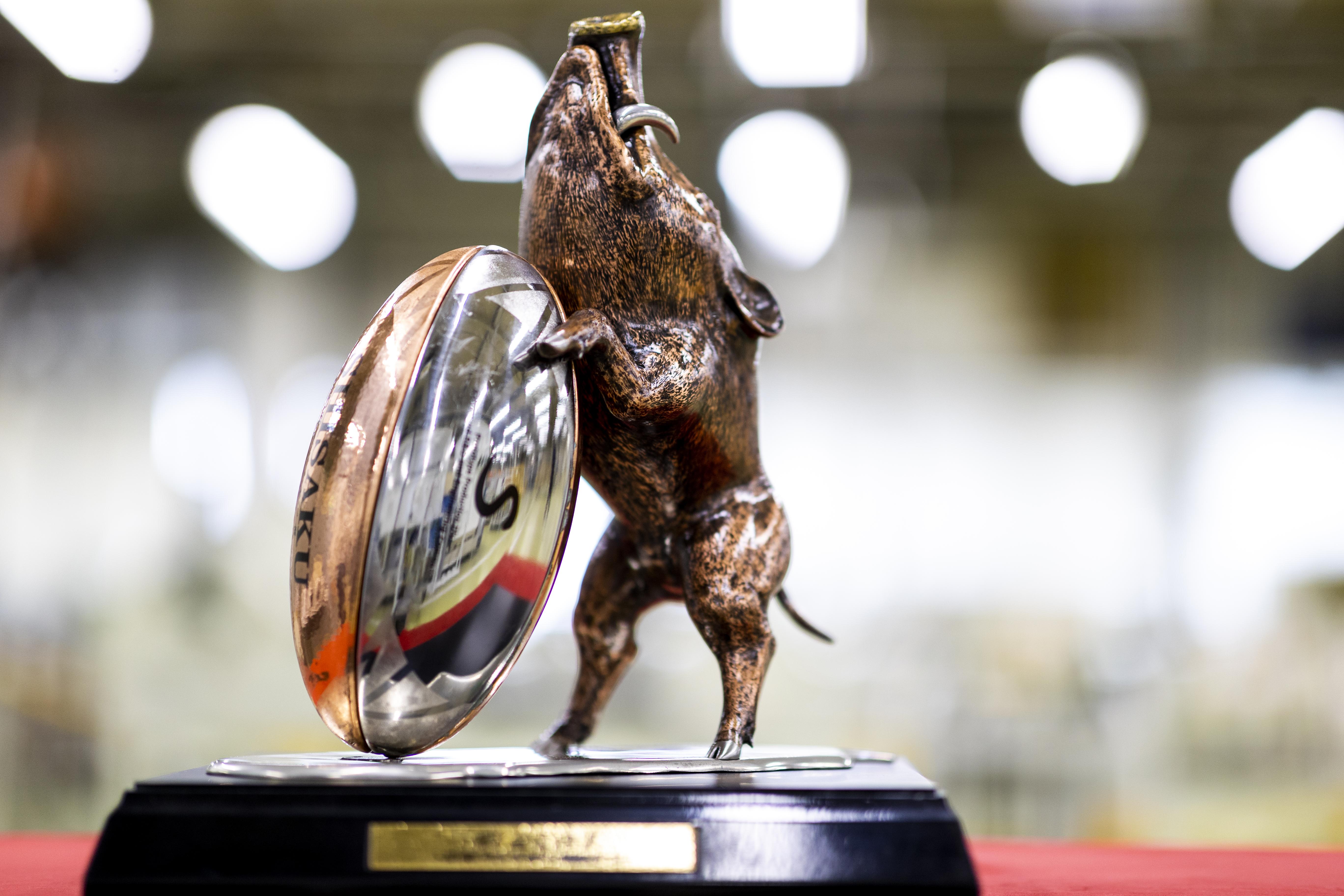
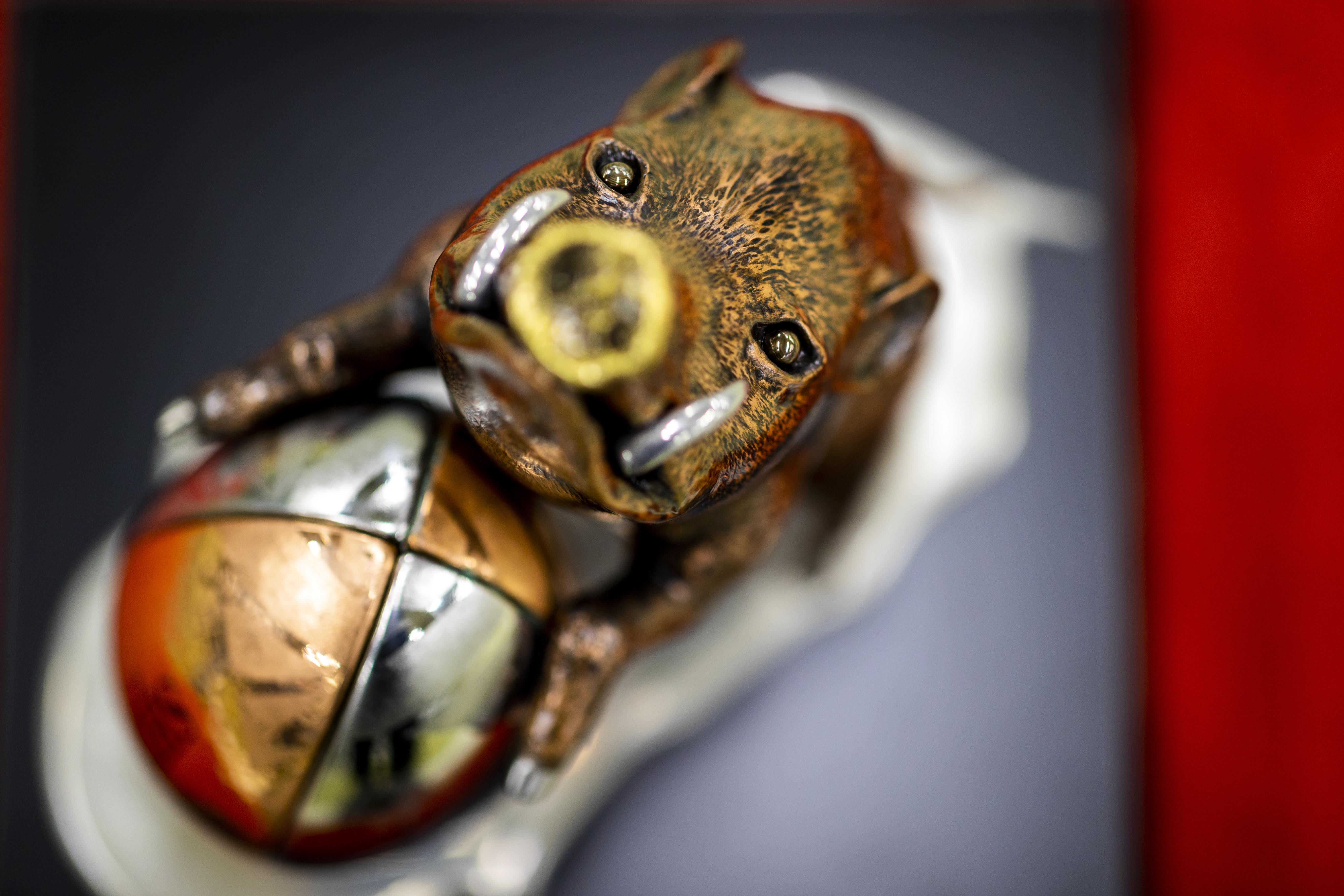
「自分の手で、たたいているうちに形になる。それが板金という仕事の面白さです」と語る吉野は、後進に対する技術指導、技能の伝承に加えて、自身の進化にも余念がない。デザイナーとともにスケッチから金属でイメージを立体で形にしてみたり、チタンなど扱いが難しい素材の溶接に取り組んでみたり、常に新しいことに挑戦し、未来に向けて研鑽を重ねている。

「最近はハイテン(ハイテンション)鋼など、板金の手加工が難しい、手加工ができない素材も増えています。また、プレス金型や治具の製作でも、3Dソフトの設計データを活用することで、紙図面が不要になるなど、昔よりもモノづくりが早くできるようになっています。それでも、昔からの板金の手加工の技能・技術は今後のクルマづくりでも絶対に欠かせない、伝承しなければならない技能です。ただ技能の習得には10年という長い時間がかかります。どうすればもっと効率良く、早く技能を習得させることができるのか。その方法を考えてこの源流技能の伝承を行なっていきたいですね」
無から有を作り出す「板金と溶接の匠」吉野栄祐。その挑戦はさらに続く。
(文・渋谷 康人、写真・前田 晃)