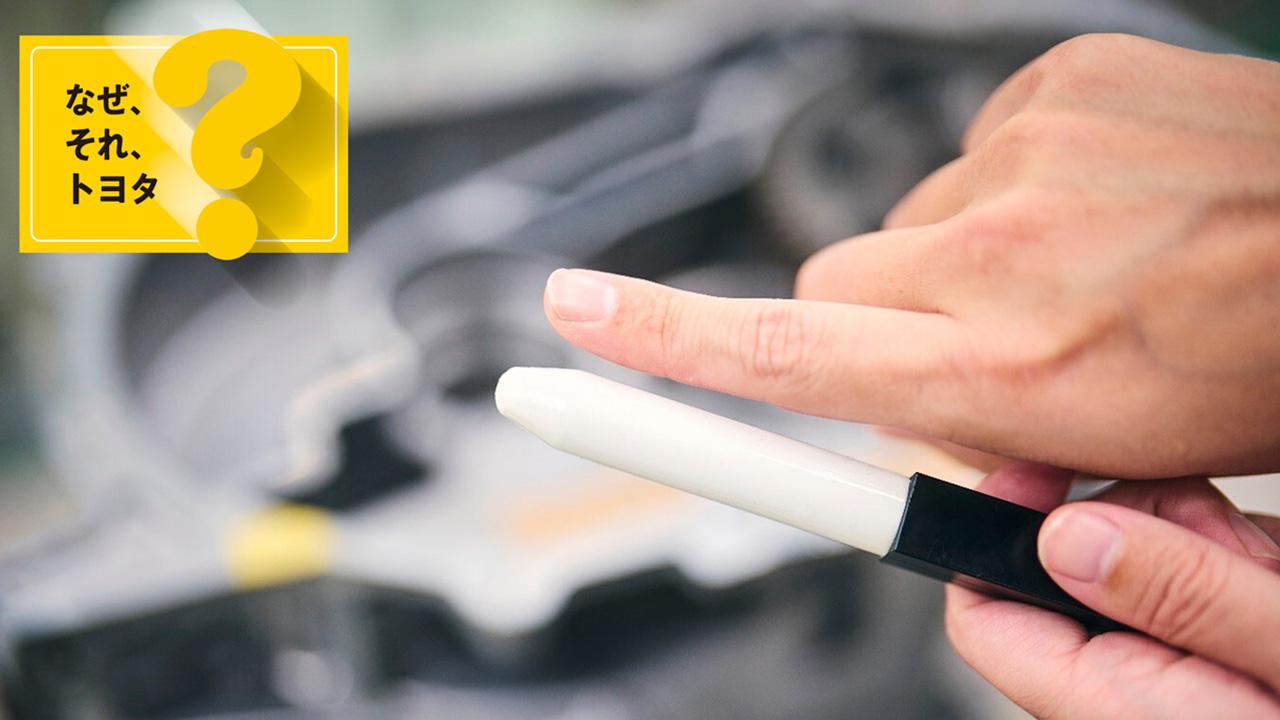
本業とは関係ないように見える取り組みを紹介する「なぜ、それ、トヨタ」。今回は指づくり。一体何のために...?
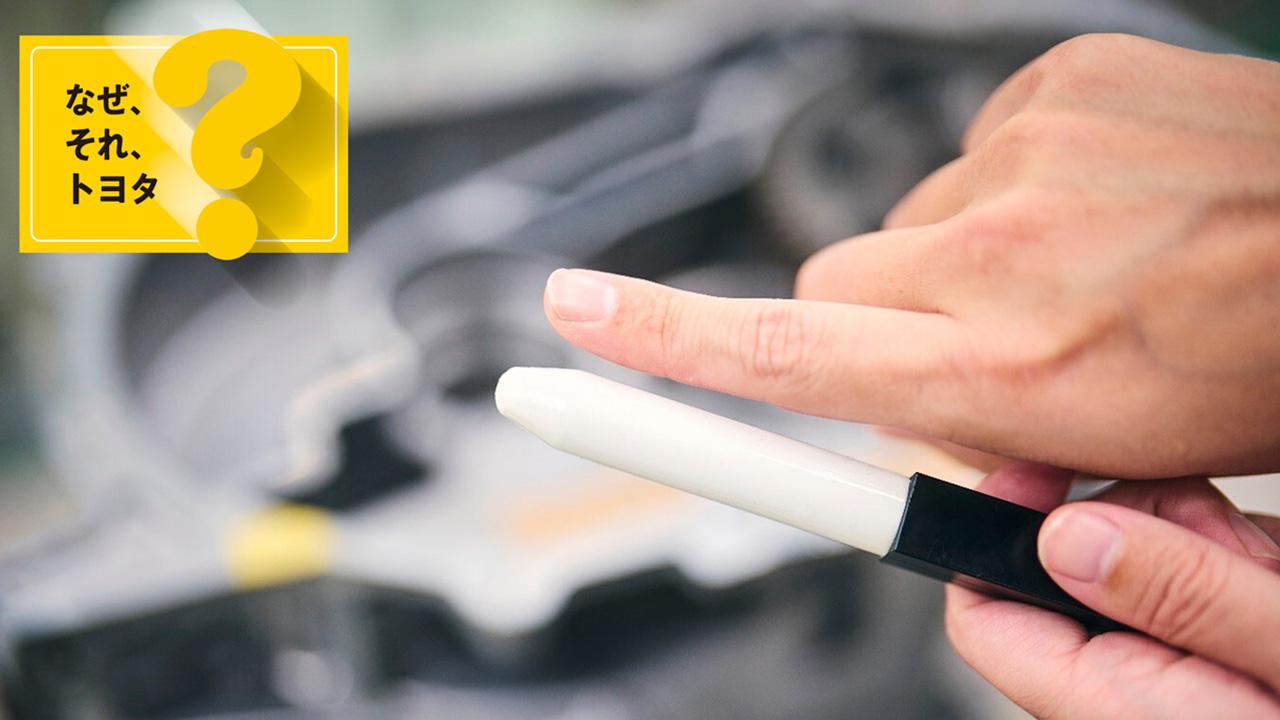
とんでもないものがトヨタの工場で開発されている!そんな情報を聞き、豊田市の本社工場を訪れた。
信じがたい話だが、なんとここでは「指」が開発されているのだ。クルマや車両パーツではなく、まさかの指づくり…!一体どういうことなのか?
なんと骨まであった!
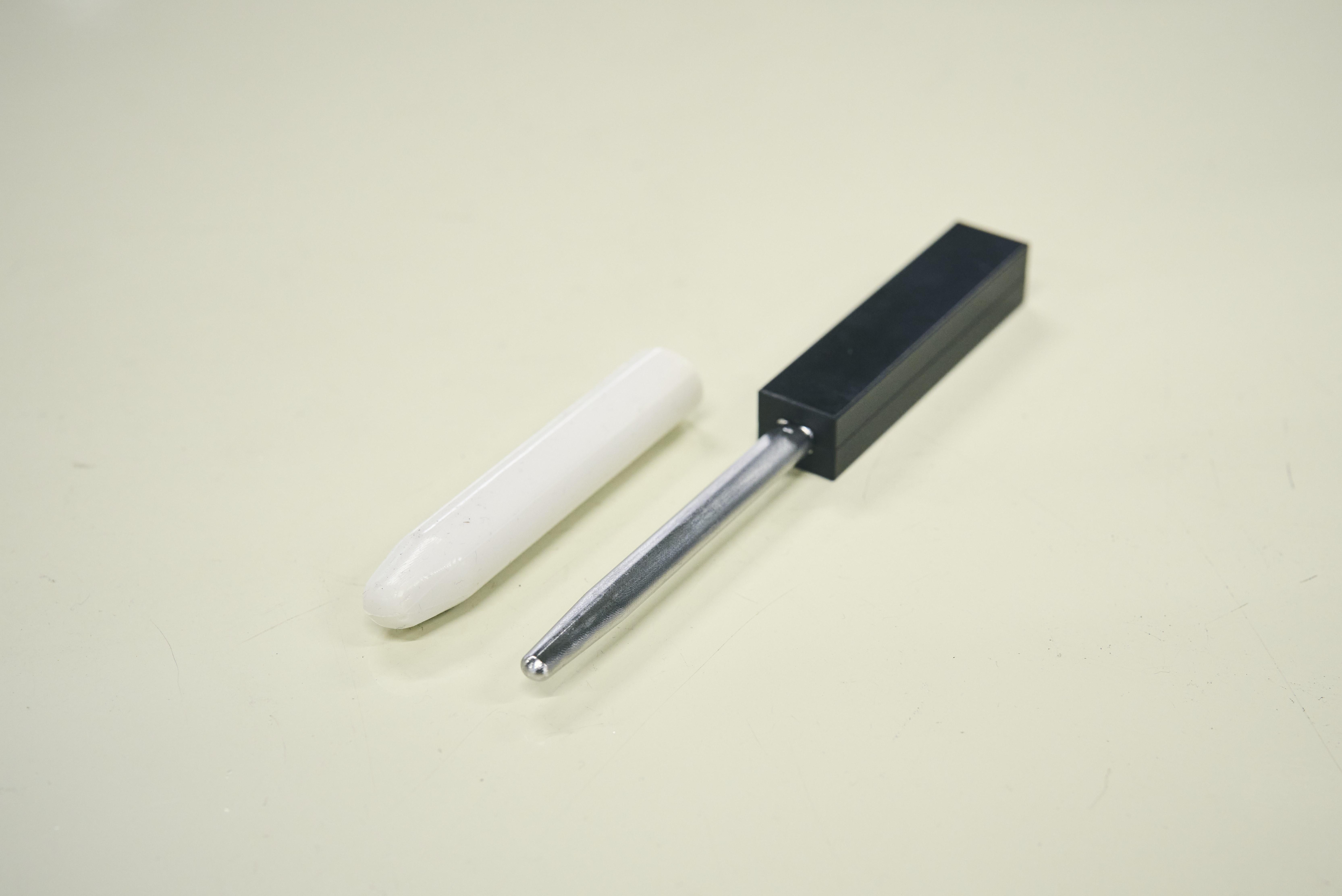
さっそく見ていただきたい。これがその指だ。もちろんダミーだが、中には骨を模した金属まで。
なぜこんなものをつくっているのか、開発担当者に聞いてみた。
モノづくりエンジニアリング部 要素技術開発室 森建郎 主幹
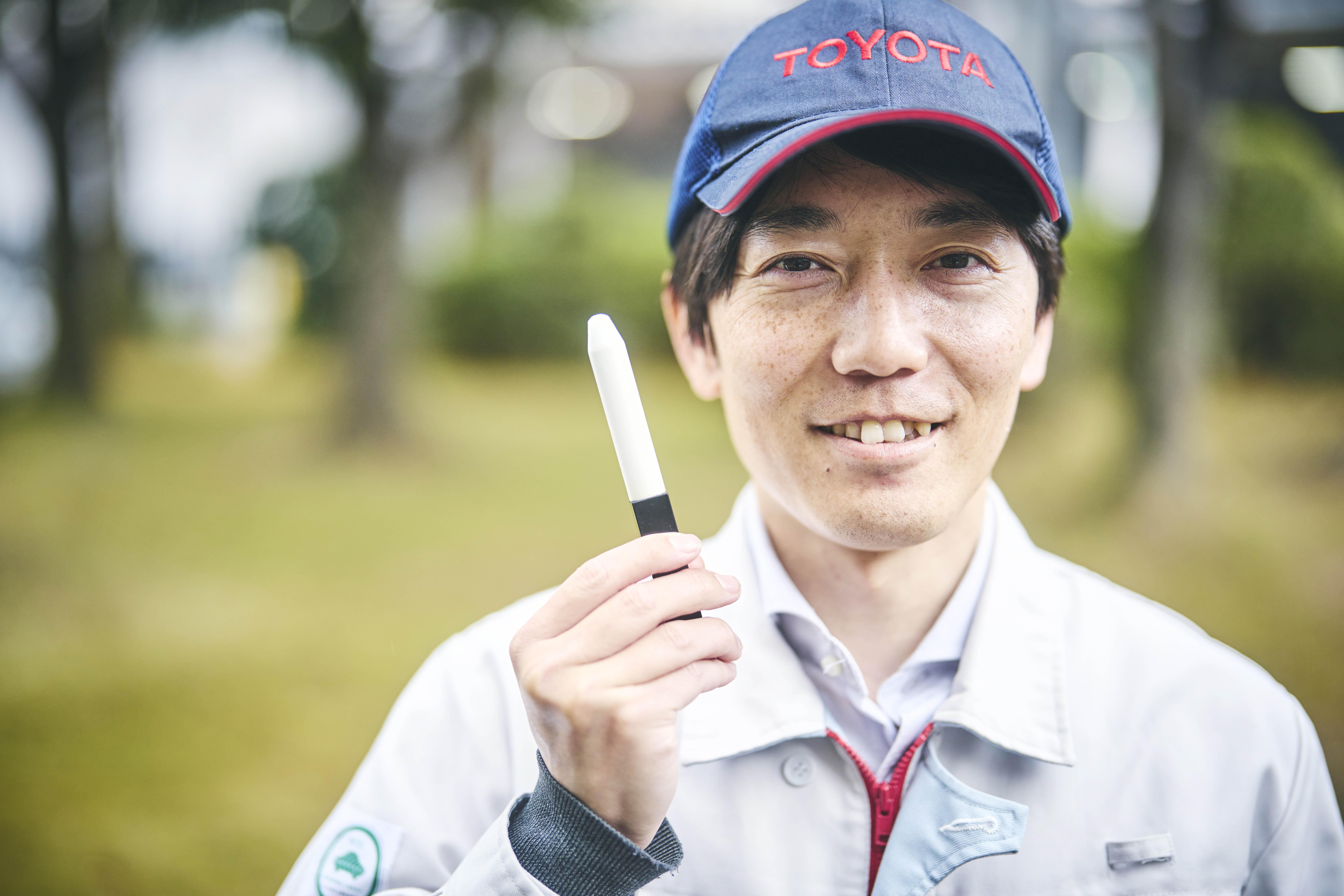
現場で働く皆さんの安全のためです。
製造業全般に言えることですが、少子高齢化にともない、労働人口が確実に減っていきます。これまで以上にロボットと一緒に働くことが増えるはずです。
人とロボットの距離が近くなることで、働く人の“手先の安全リスク”が懸念されるようになっています。
製造業でケガをされる方は、機械に挟まれるなど、手や指のケガが多いという。
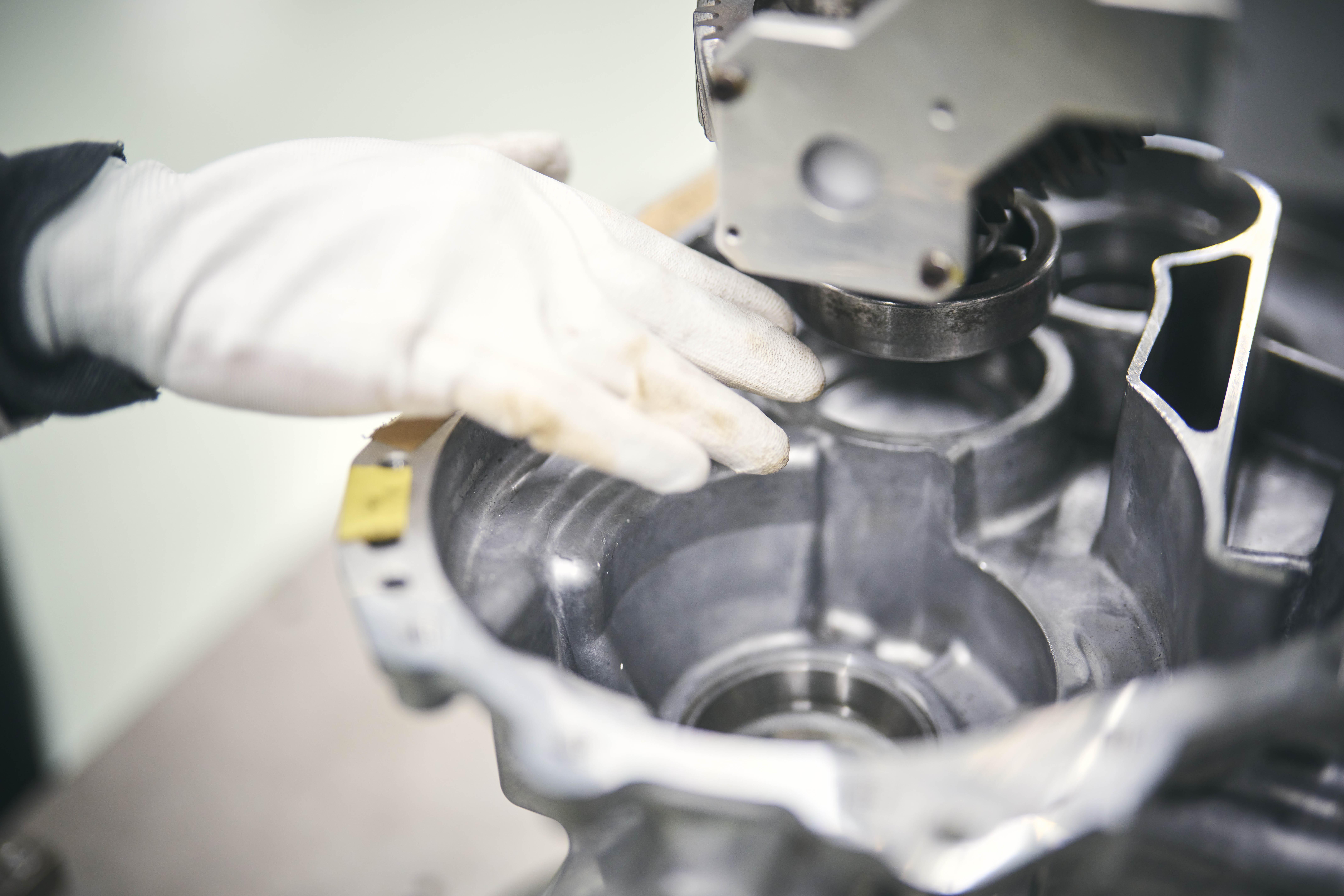
森 主幹
そこで、安全性を評価するためにパナソニックのプロダクト解析センターさんと共同で“指ダミー”を開発することに。
ISO規格(国際標準化機構)による安全評価のガイドラインがあります。
でも、10mm以下の狭い面積で指が挟まれることは想定されておらず、センサーで危険を察知するにしても、どうしても限界がありました。
自動車の部品は、固いものや尖ったものが多い。さらに細かい作業も多く、狭い表面積での指が挟まれる度合いを評価できるツールが必要でした。
開発がスタートしたのは2019年。名古屋大学や、同様の研究に取り組んでいたパナソニックと共同研究が始まった。
安全を総括する安全健康推進部と連携し、工場全体のロボット自働化を進める部署にいた森主幹が中心となってプロジェクトを進めている。
国内で約7万人いるトヨタ社員で唯一、指をつくっている人材だ。
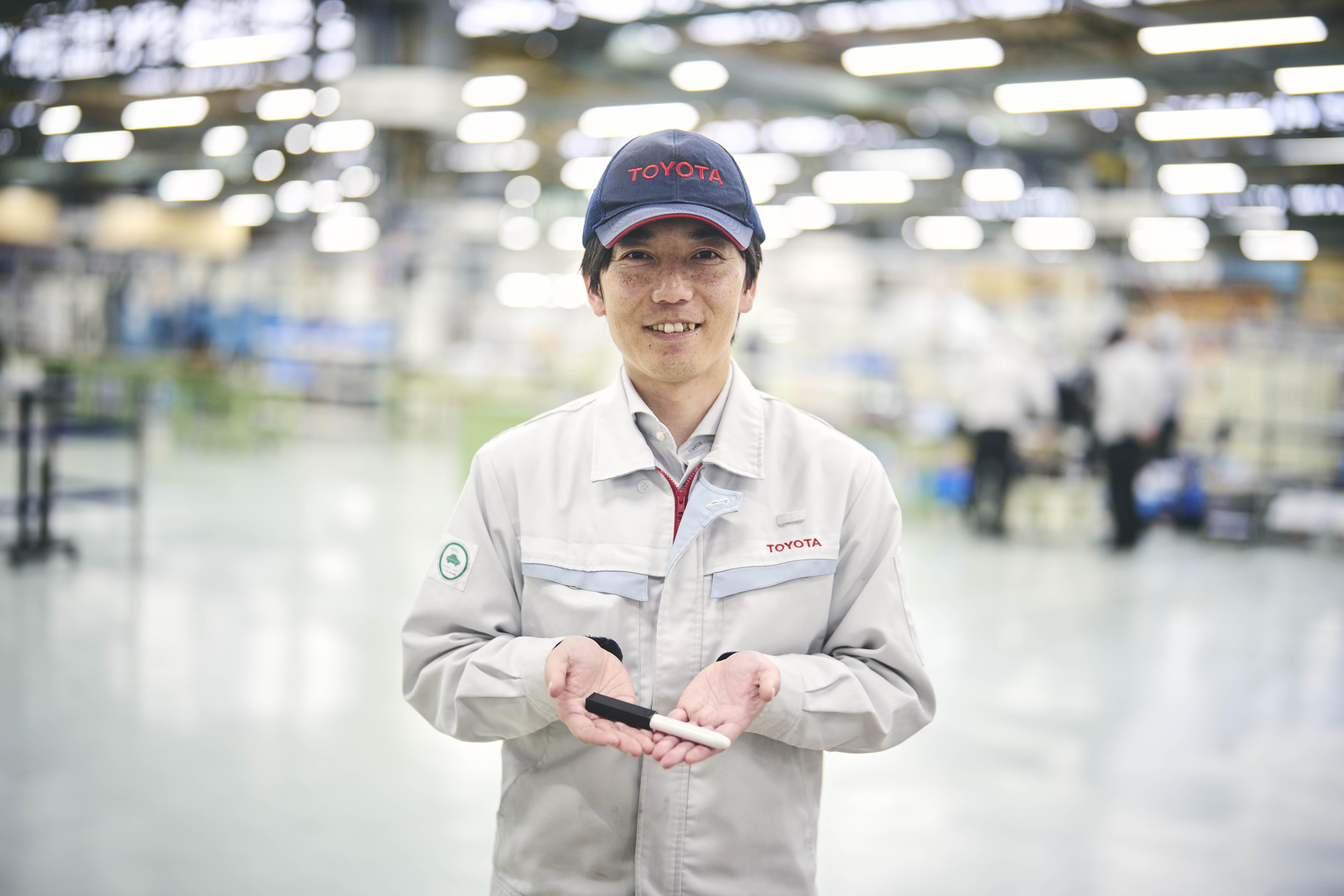
でも、この指。今の時代かなりアナログに見える。失礼を承知で聞いてみた。
森 主幹
開発当初、パナソニックさんの意向としてはデータ解析できるものが前提にありました。
一方トヨタでは、製造部にヒアリングすると、PCがなくても誰でも現場で使いやすいアナログなものがいいという要望がありました。そこで、実用的に使えることを軸に考えていきました。
各工場では、これまで以上に生産性の高いロボットの導入が求められています。
でも設備の安全評価に時間がかかりすぎると導入が遅れる。アナログな方が、安全性評価の時間や労力を減らせるのです。
安全面を考慮すればするほど対策が過剰になりがちだが、安全を最優先にしながら生産性を上げることにも貢献できる。
アナログ、恐るべし…。
安全性を評価する人の負担を減らしつつ、ロボットの導入によって現場で働く人の負担も軽減。かつ安全性を高められるとは驚きだ。
裂傷度合いが一目瞭然
では、実際に現場ではどのような危険があるのか、機械を動かしながら説明してくれた。
森 主幹
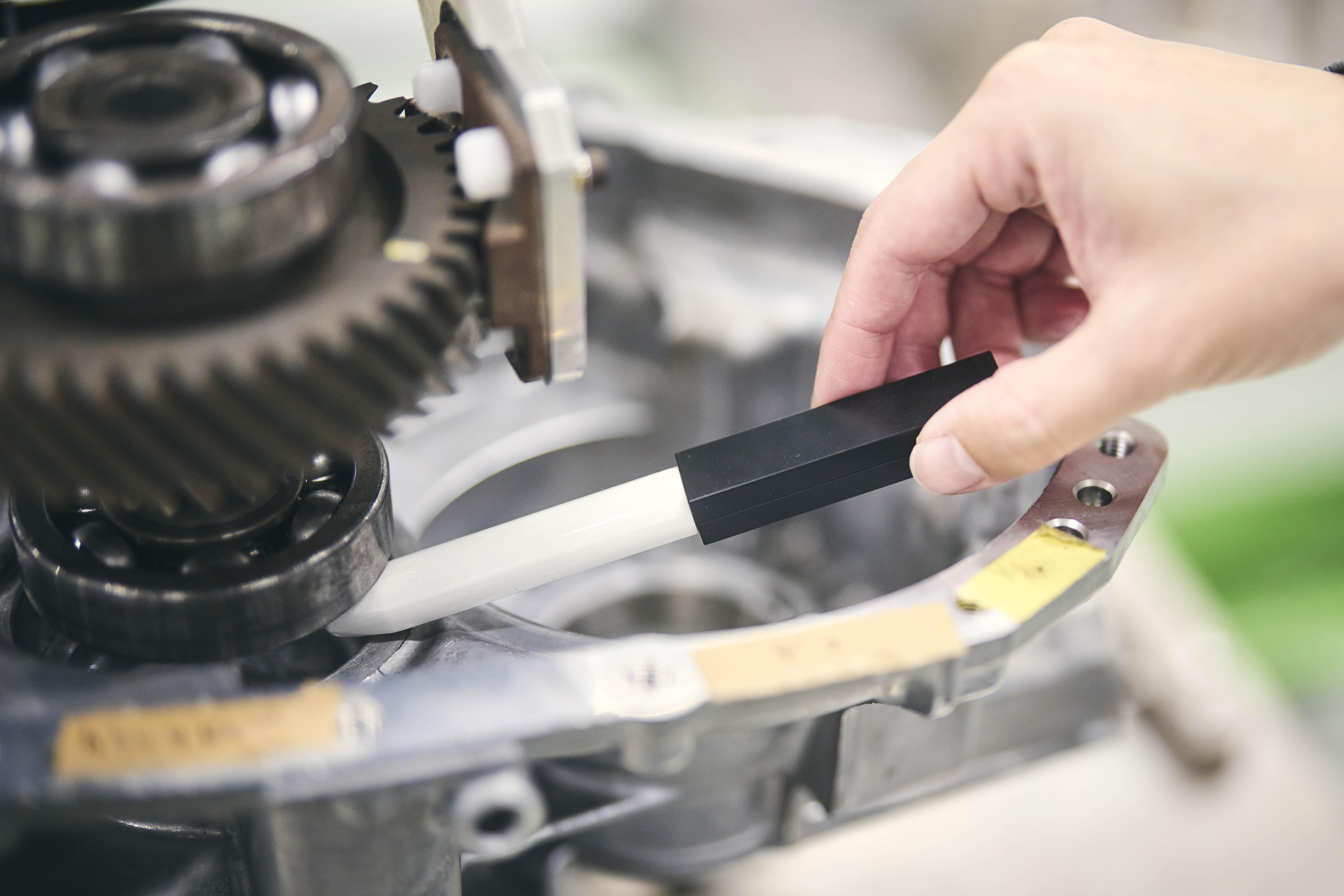
幸いなことに、それぞれの工場で細かく安全対策がとられているため、今のところ協働ロボットとの作業時に大きな事故はありません。
でも“その安全対策で十分なのか”を確認するのに多くの時間がかかっています。一方で挟まれた場合、どの程度の強さならケガをしないか。指ダミーの裂傷度合いを目視すればすぐにわかります。
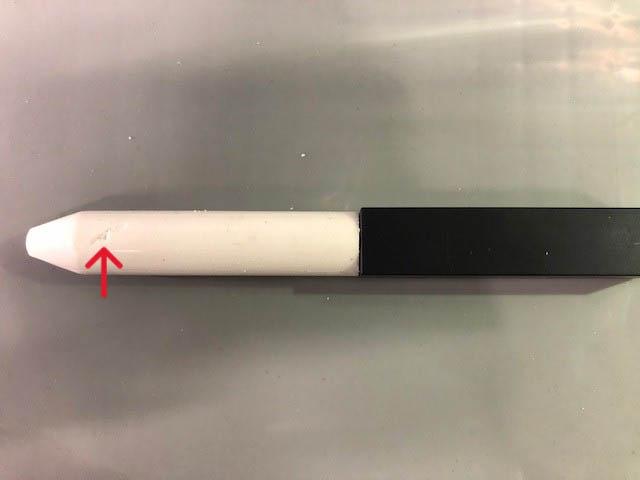
指ダミーがあれば、目視で、機械の力を安全が担保できるレベルに調整できるんです。
現在、国内のトヨタの工場で実用化が進んでいるこの指ダミー。
本物の指のようにプニプニした弾力があるのだが、開発途中では、ある動物の皮膚を使ったなど秘話も明かされた…