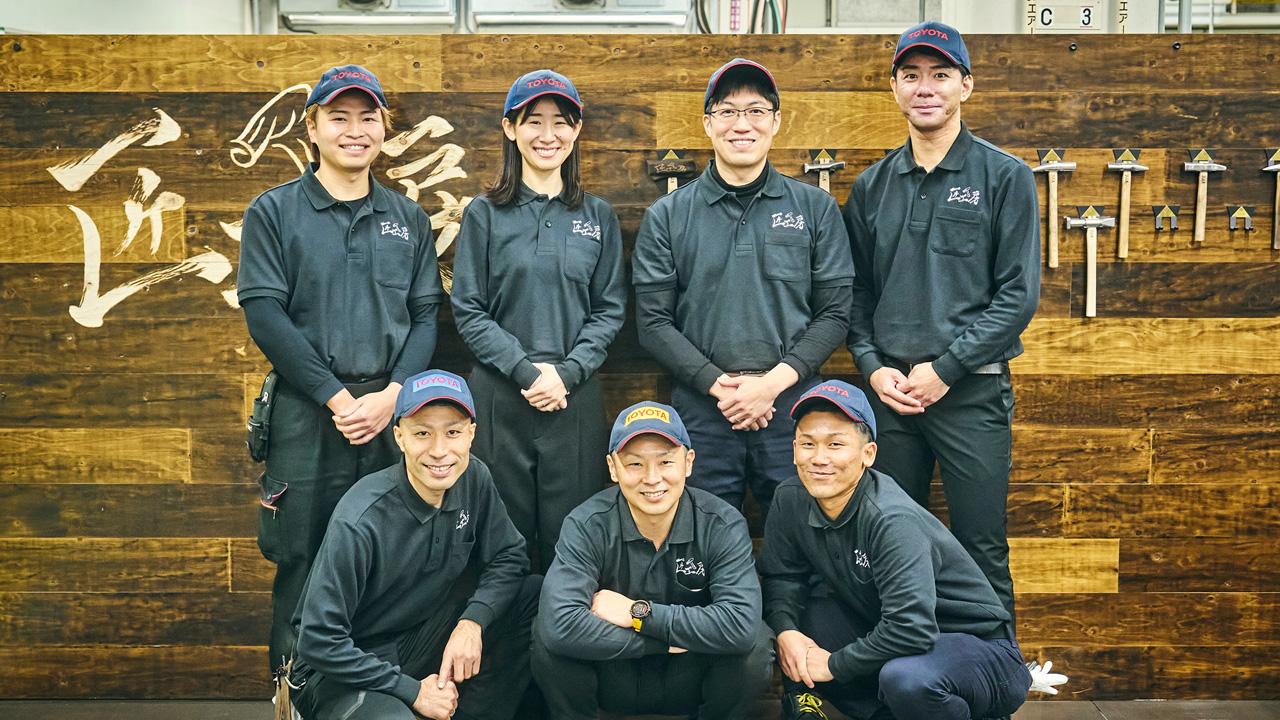
This is part two of a report on the Takumi Kobo, which harnesses the sheet metal craftsmanship and monozukuri spirit passed down since Toyota's founding.
Here, we take a closer look at the team's aspirations and the monozukuri genba, the place where things are made.
The value of one-of-a-kind creations
Besides developing the design, the Takumi Kobo members had another hurdle to clear: controlling deformation. Tsuchiya explains.
Tsuchiya
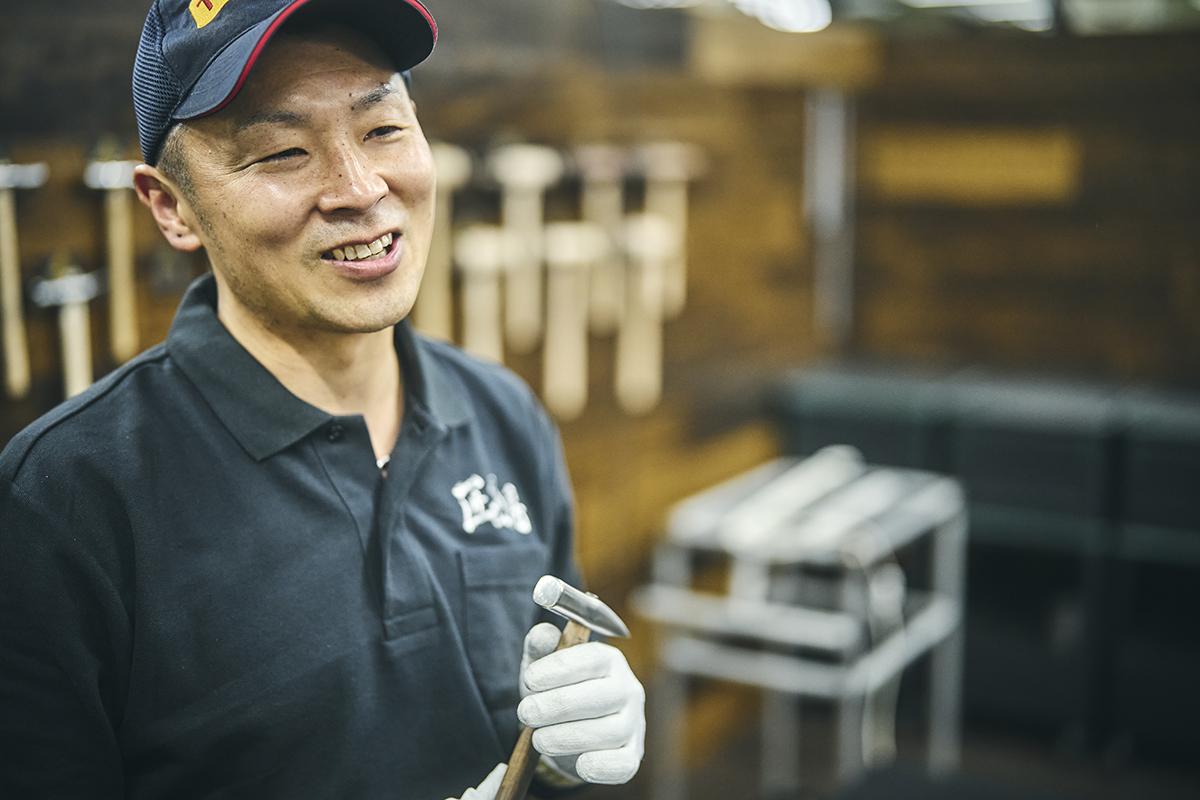
Sheet metal work involves beating steel plates or similar materials with hammers and mallets to create three-dimensional forms.
Normally, hammer marks are hidden on the reverse side of body panels, but in this case our challenge was to create something valuable by using these very markings as ornamentation.
At the same time, materials elongate and distort when struck, but scuff plates must be finished as a level surface. Deformation doesn’t look good.
One of the challenges for us was figuring out how to work the metal without it looking as though it had gone under the hammer.
Since thicker material expands less, the craftspeople start with 1 mm stainless steel sheets. When these proved too thick to turn into scuff plates, they switched to 0.5 mm sheets.
Although this made controlling deformation more difficult, the takumi were able to draw on their accumulated skills and experience to achieve consistent quality.
Tsuchiya
What’s important is the sound of your hammer striking the metal. An uneven sound indicates that you aren’t hitting the sheet evenly. This means you will have uneven elongation and more deformation. That’s why you need to keep an ear on the sound as you go.
Nitahara
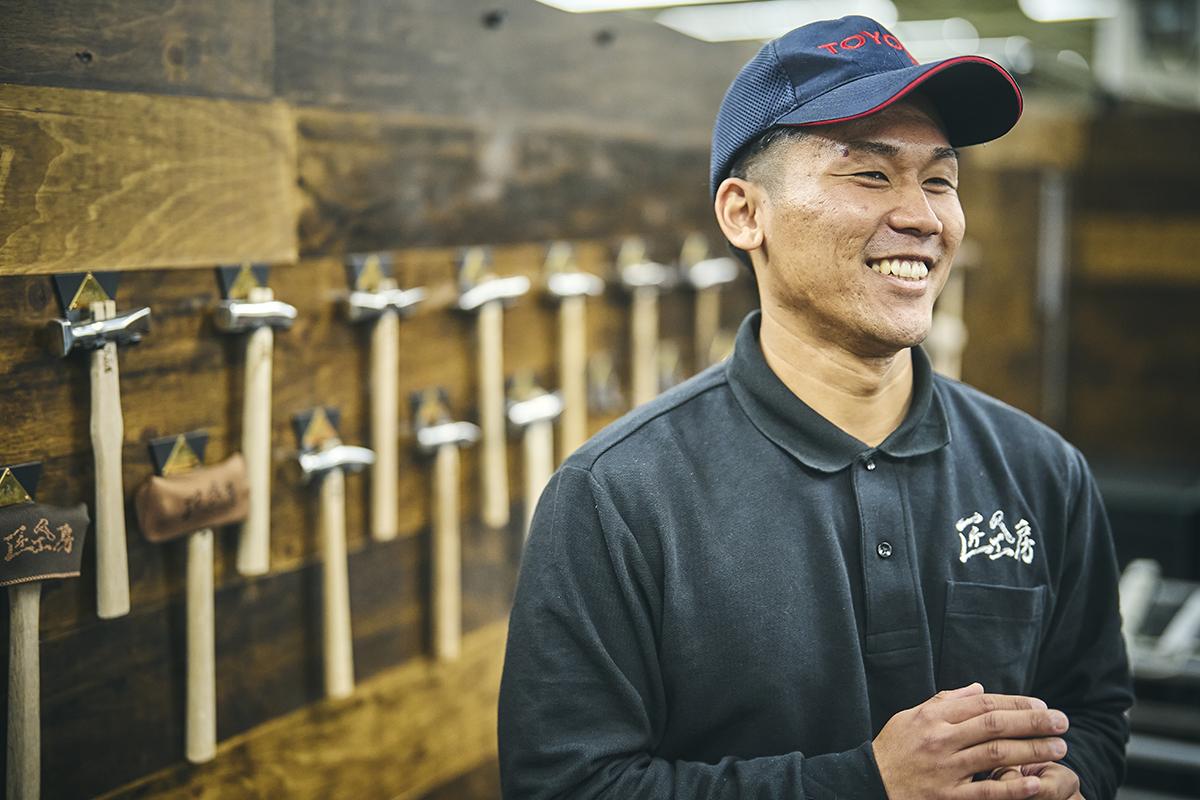
Another key aspect is how you make the indents on stainless steel. For instance, if you start at the edge and work in a single direction, the distortion will be concentrated in that area, and the surface will suddenly lose shape.
As we work, at each moment, we are assessing how the sheet is deforming and where to strike next to correct that distortion.
For the rear seat scuff plates, we strike each plate some 7,000 times, all the while considering how to ensure each one ends up flat after that 7,000th strike lands.
As the takumi explains, the Masame grain pattern is applied line by line, while paying careful attention to the sound and feel of the hammer on stainless steel, along with the material’s deformation. Each artisan is able to create just two plates a day.
What’s more, such hand processing means that strictly speaking, every scuff plate has a one-of-a-kind pattern.
In this way, Takumi Kobo members emphasize that they offer customers something distinct from items mass-produced by machines.
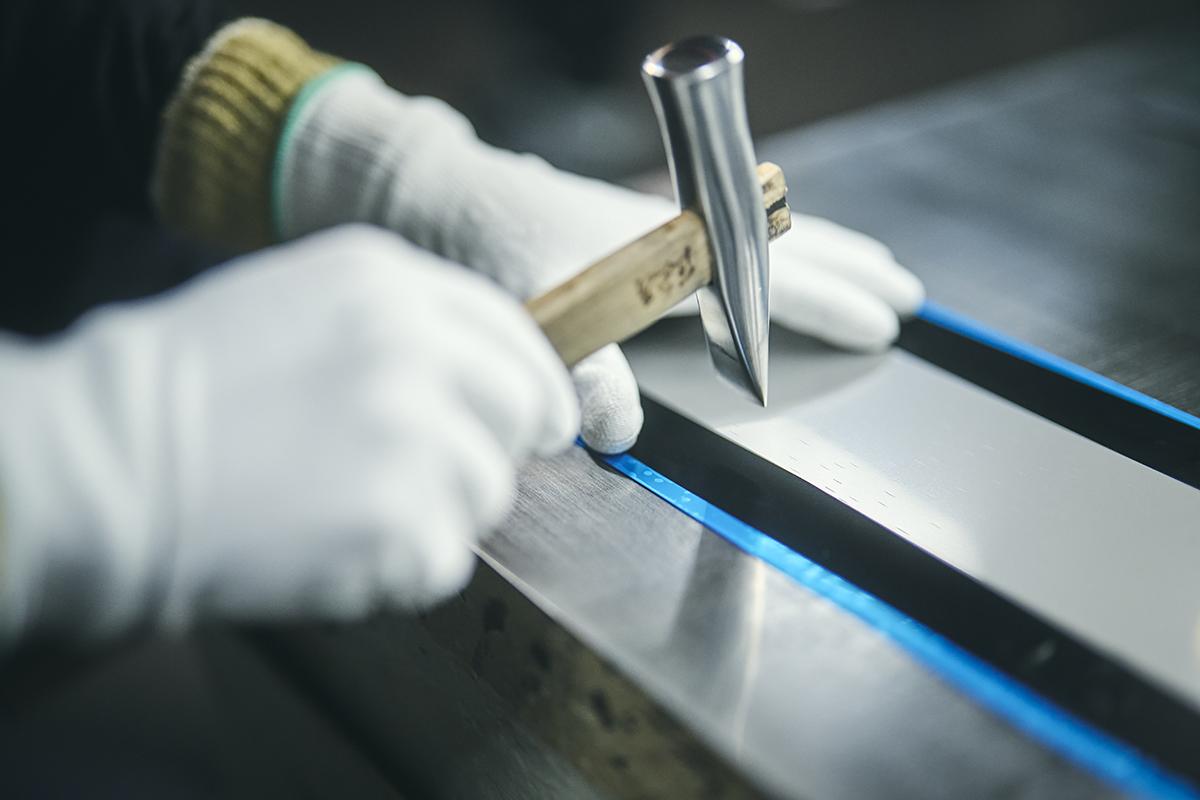