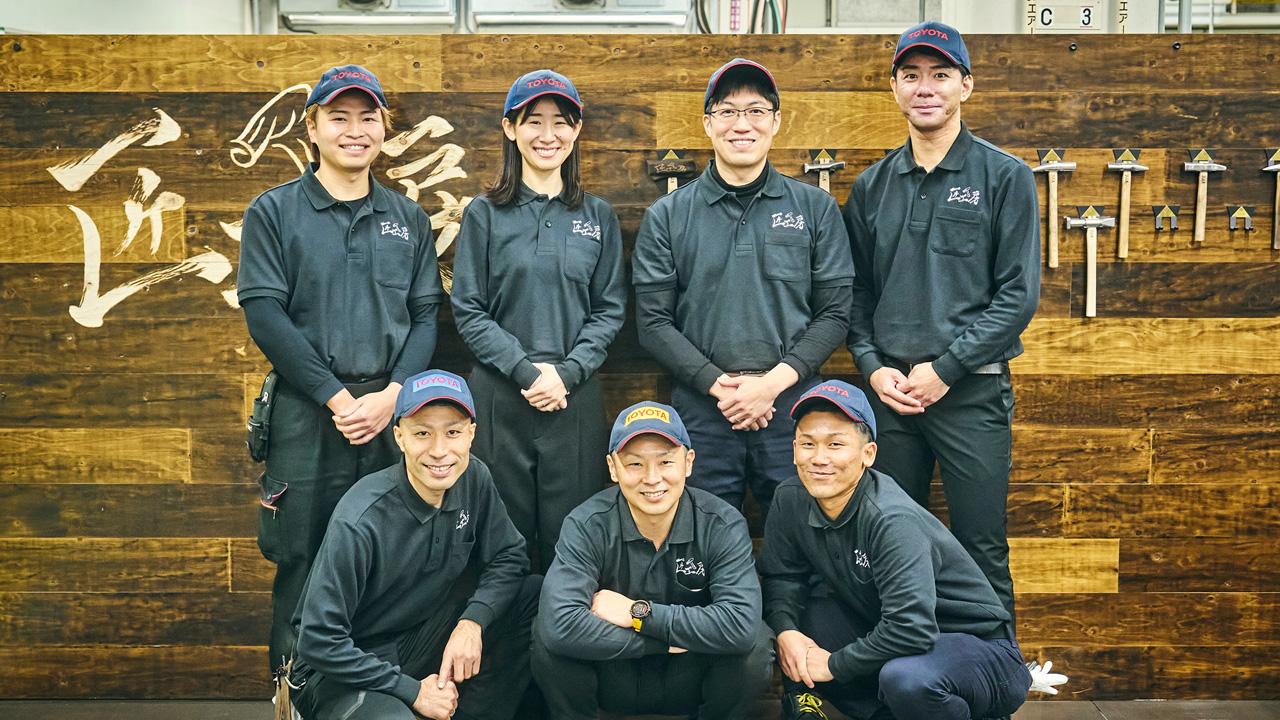
This is part two of a report on the Takumi Kobo, which harnesses the sheet metal craftsmanship and monozukuri spirit passed down since Toyota's founding.
Here, we take a closer look at the team's aspirations and the monozukuri genba, the place where things are made.
How the Takumi Kobo came to create Century scuff plates
The Takumi Kobo started with the ambition of preserving and promoting the valued skills of Toyota’s takumi to boost the value of the brand and the products offered to customers. Yuto Tanaka explains why the team decided to tackle the Century for its first project.
Tanaka
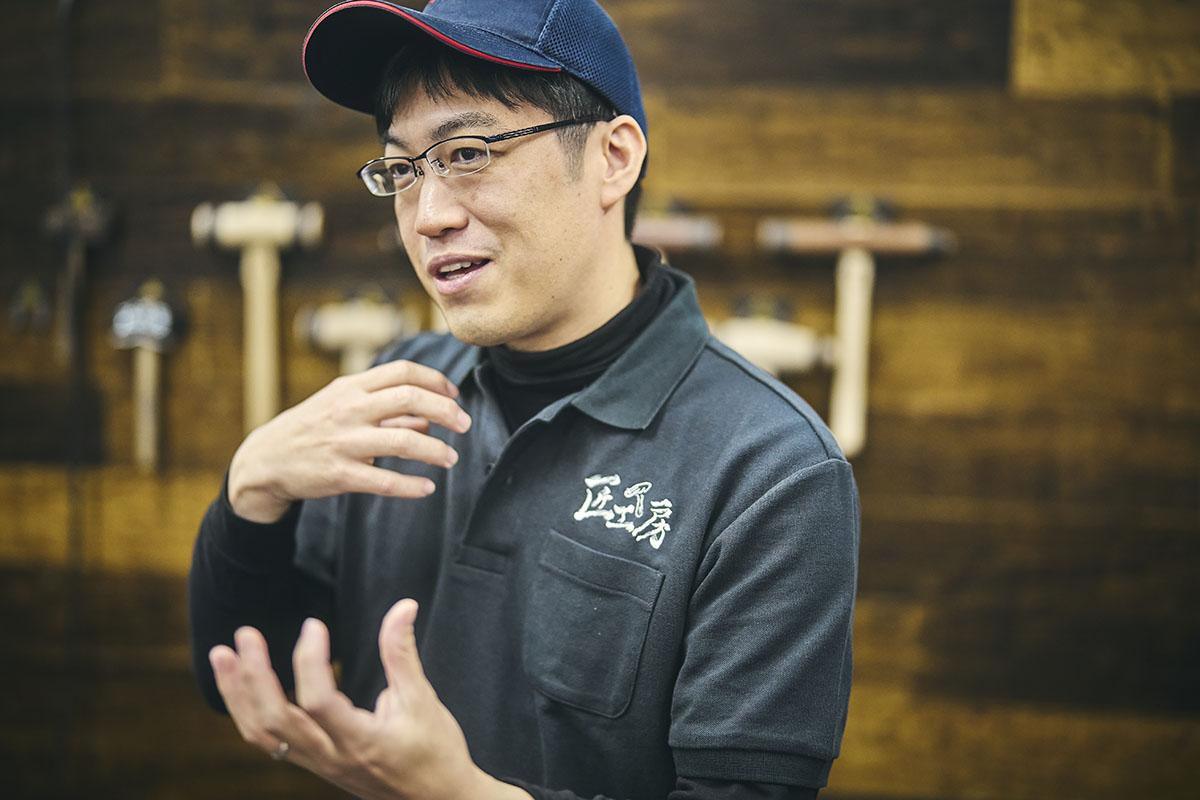
I learned about the “inheritance and evolution” philosophy passed down among the teams of Century developers. At Takumi Kobo, we are also committed to passing on takumi skills and ensuring they evolve into a new phase. This shared mentality made us keen to take on the Century project.
We also found out that the Century is built on a concept of providing customers with the ultimate in hospitality, catering to their every need like a tailor-made vehicle. We felt that the scuff plates could be one item that embodies this concept.
As it happened, concept discussions for the new Century took place in April 2021, exactly a year before the Takumi Kobo launched. This created the opportunity for an initial pitch to Chief Engineer Yoshikazu Tanaka and his development team.
Instead of the scuff plate, the craftspeople presented a prototype decorative panel for the tower console, a Century tradition. Unfortunately, they struggled to make it fit the model’s overall design and worldview.
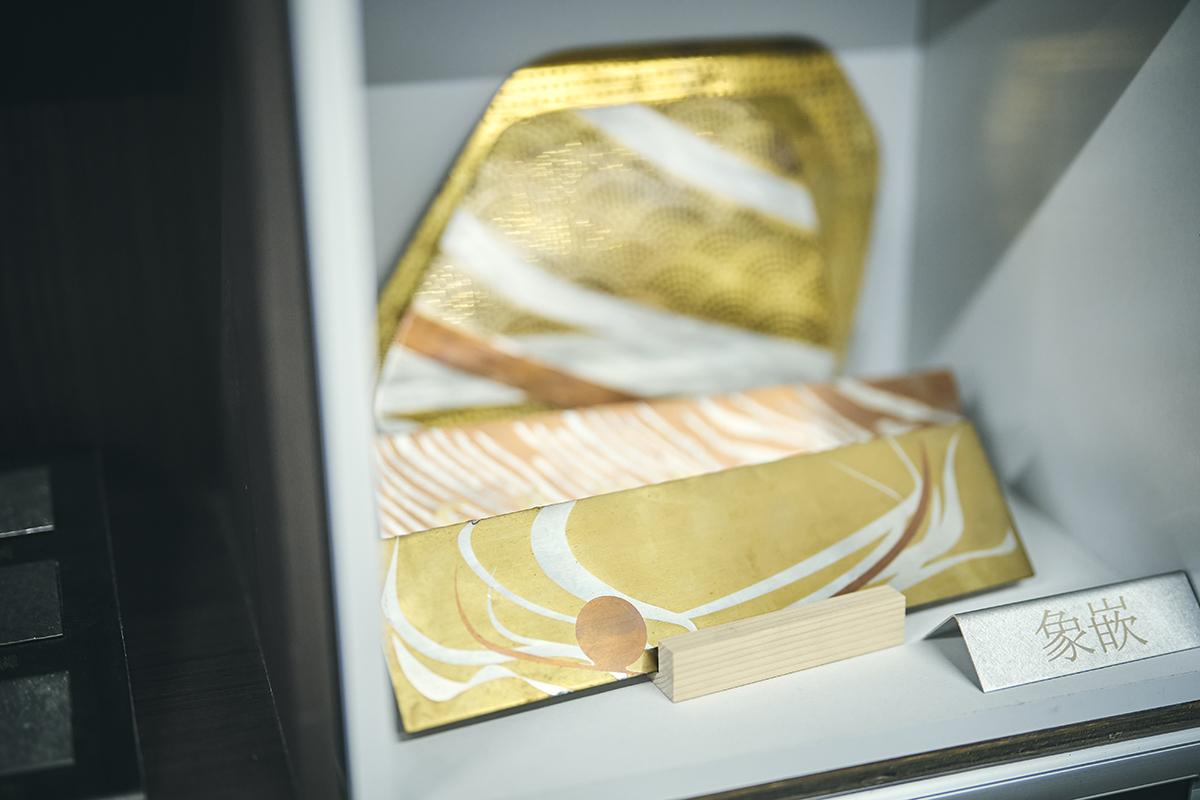
Horikawa
On that occasion, we created plates with flashy designs that brought our metalworking skills to the fore, trying to show what we were capable of producing.
However, this ended up being a self-serving idea that didn’t fit with the new Century’s direction.
Murata
At that point, I think we were still figuring out, through trial and error, exactly what kind of car the Century was.
Based on the feedback, we decided to start by considering what sort of products would fit the Century story and customer needs.
Working with a mockup of the Century’s interior, Murata and the team held numerous discussions with members from product planning, design, accessory planning, and domestic sales, trying to determine what parts could be turned into products and how to make them fit stylistically.
In terms of parts selection, they reached the conclusion that scuff plates would be an ideal item to express the Century’s unique hospitality, and this was endorsed by the development team.
Murata
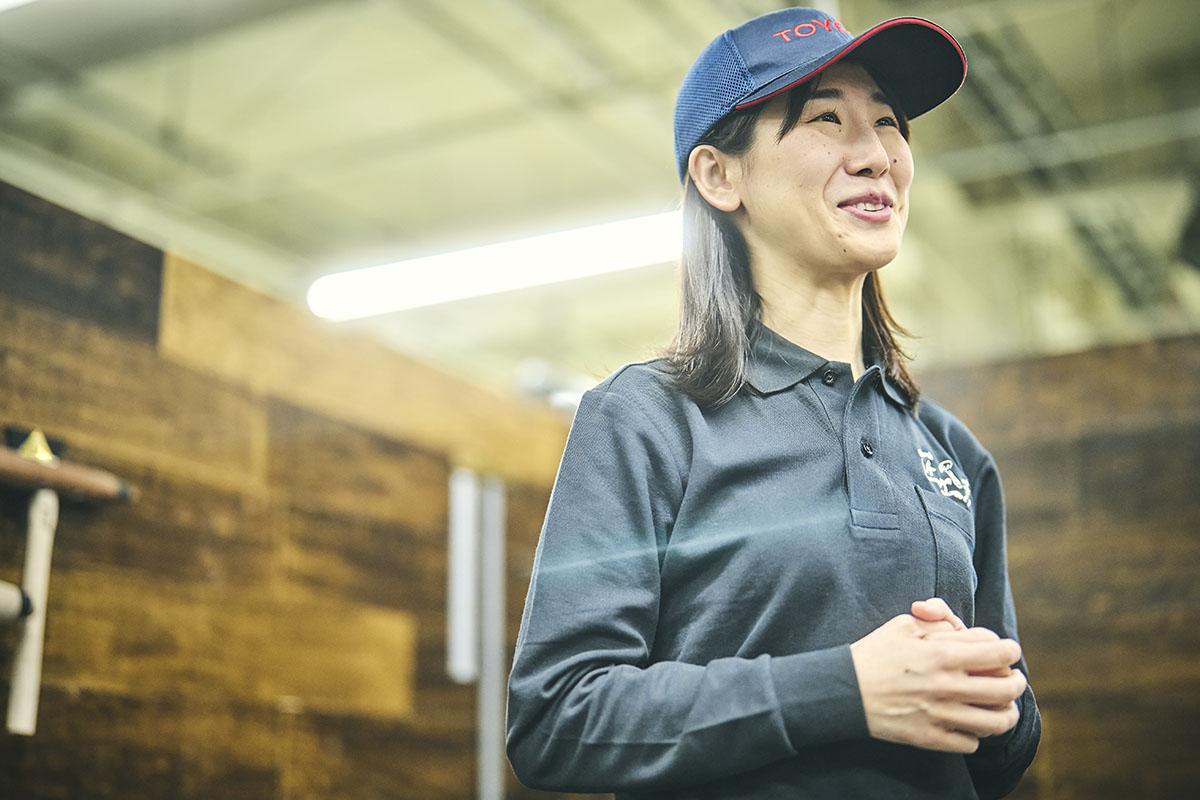
A Century is primarily about the rear seats, so we felt that scuff plates would instantly convey the car’s unique spirit of hospitality the moment a passenger opened the rear doors.
And since scuff plates are not always visible to customers but appear only when the door is opened, they add to the story of every detail being painstakingly designed.
As Murata tells, however, this spurred a cycle of further trial and error.
How could they express the new Century’s interior concept of “comfort and convenience through luxurious simplicity?” Tsuchiya and his two fellow takumi worked with Murata to explore possible solutions.
Horikawa
We spent our days researching on the internet about patterns used in traditional crafts, for example, or classic Japanese designs, and brainstorming ideas for what we wanted to depict.
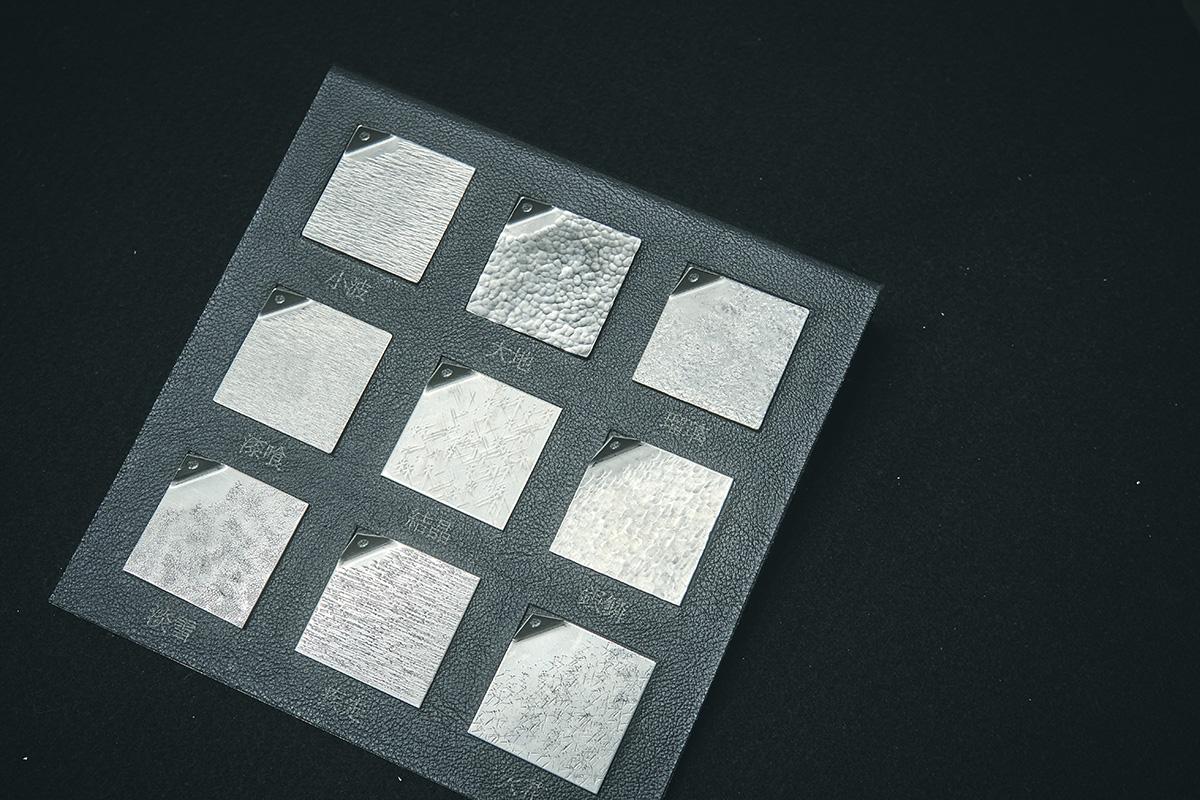
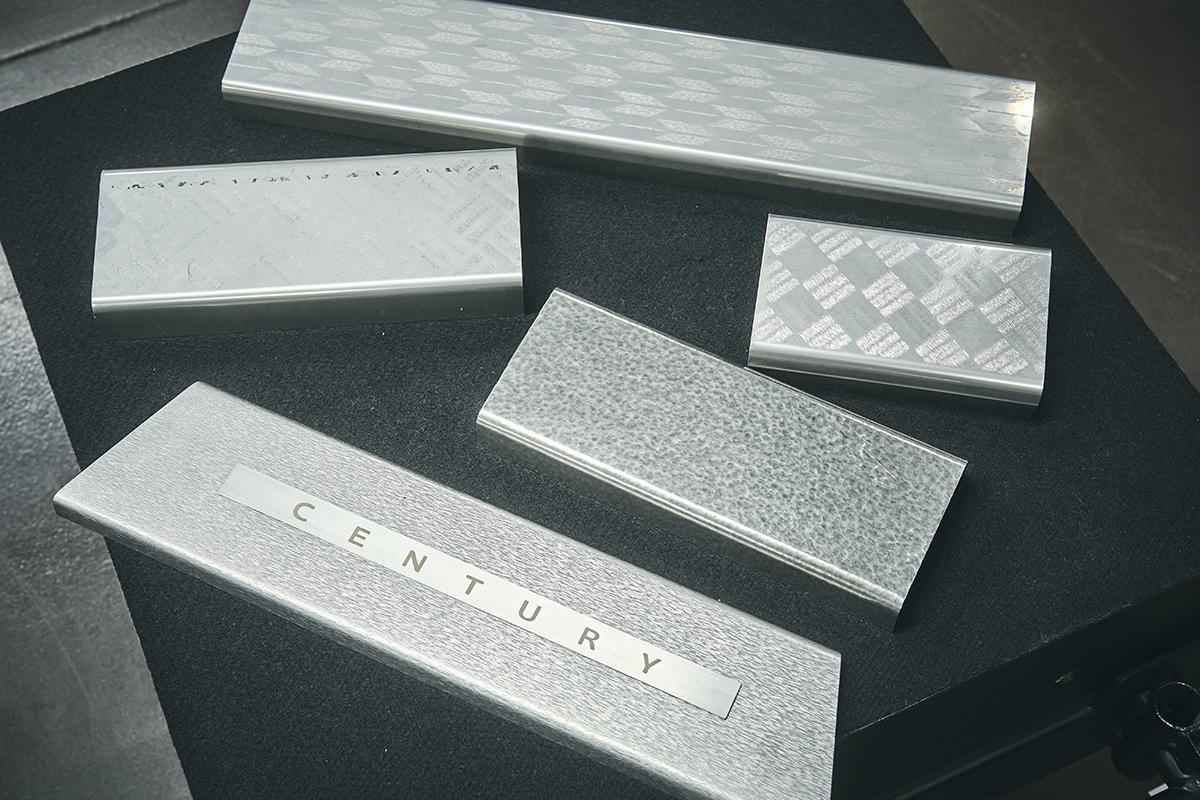
In this kind of development, technicians like Murata generally take part in the development team’s planning meetings and then share outcomes with the takumi who create the items. This time, however, there were also efforts to involve the artisans in meetings as much as possible. The idea was that hearing directly from engineers and designers would give them a sense of the fine nuances, enabling them to work toward the end product with greater certainty.
Through many twists and turns, this collective effort of planning sessions and prototype presentations arrived at the elegant Masame pattern, which perfectly encapsulates the concept of luxurious simplicity.
Murata
When our takumi produced the Masame prototype, it was truly beautiful, and I could instantly tell this design would delight customers.
Horikawa
Even after settling on the Masame pattern, we continued working with the designers to fine-tune aspects such as the density and depth of the indentations.
Eventually, Chief Engineer Tanaka and his development team gave us their seal of approval.