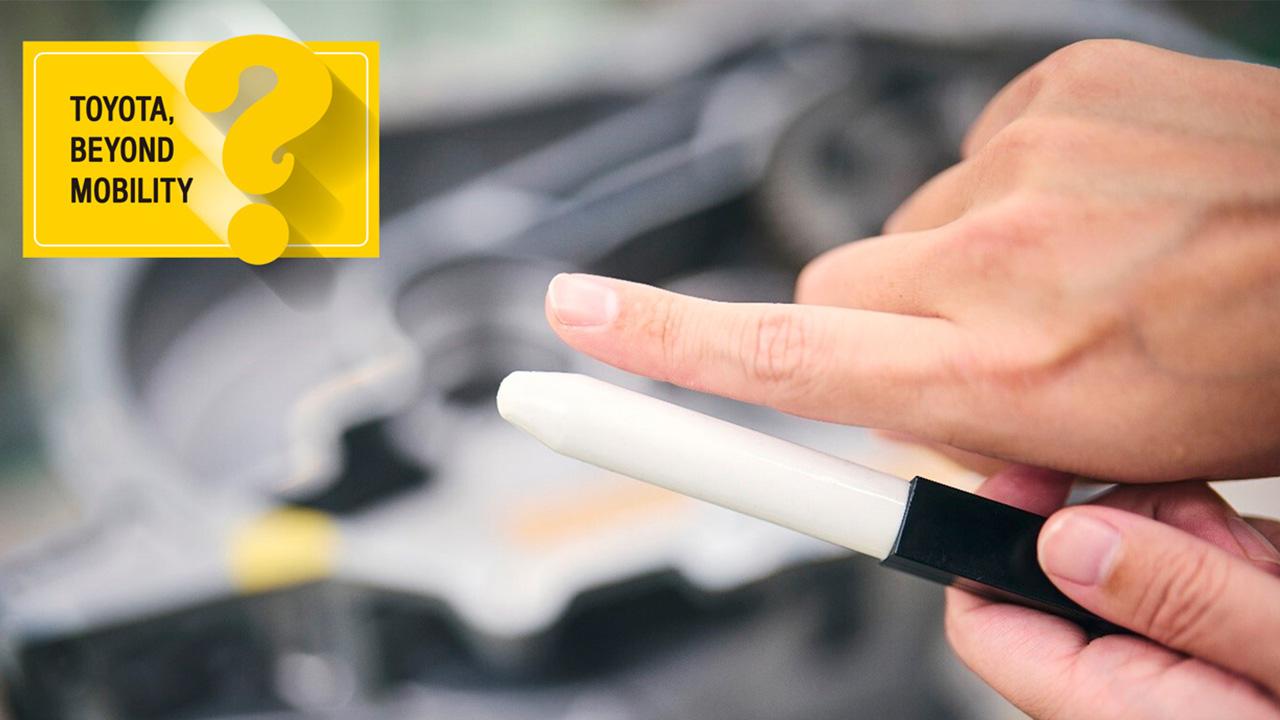
This is a series showcasing Toyota's research in non-automotive fields. This time, we delve into the world of... finger-making?!
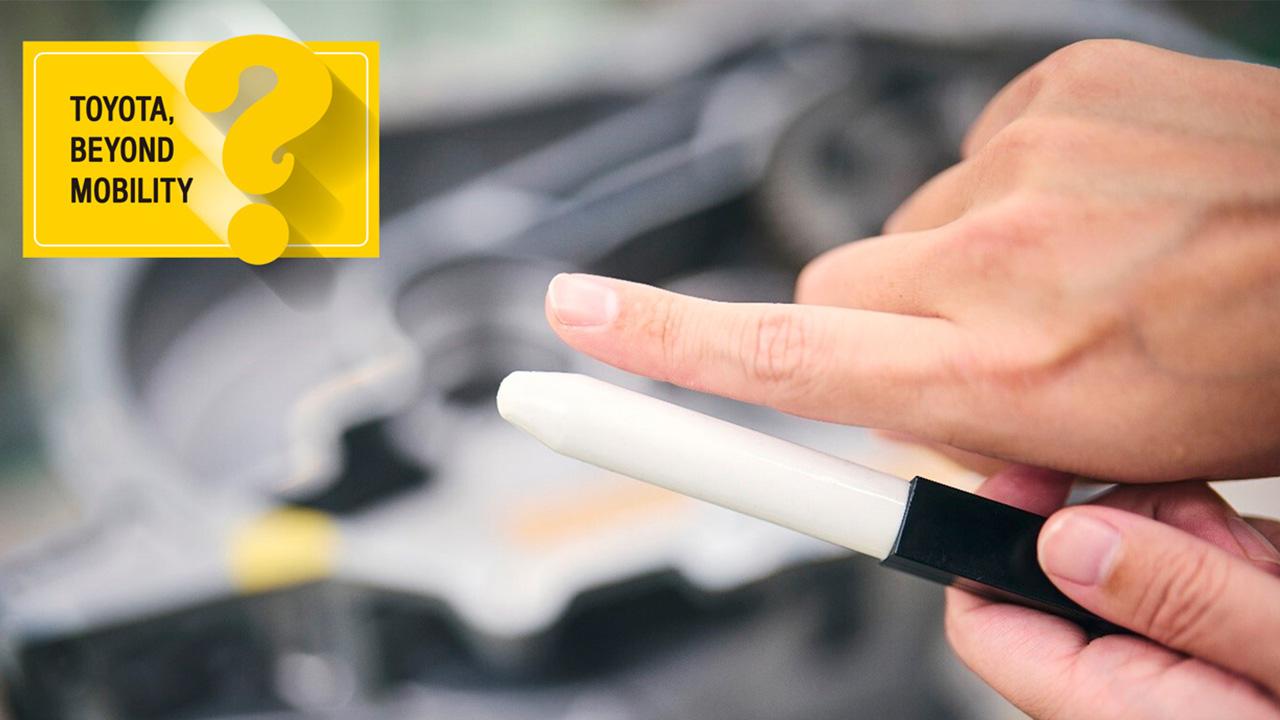
Something out of the ordinary is brewing at Toyota. To find out more, we visited the Honsha Plant in Toyota City.
Believe it or not, one of the plant’s engineers is developing not cars or vehicle parts but—of all things—artificial fingers. What exactly is going on?
Down to the bone
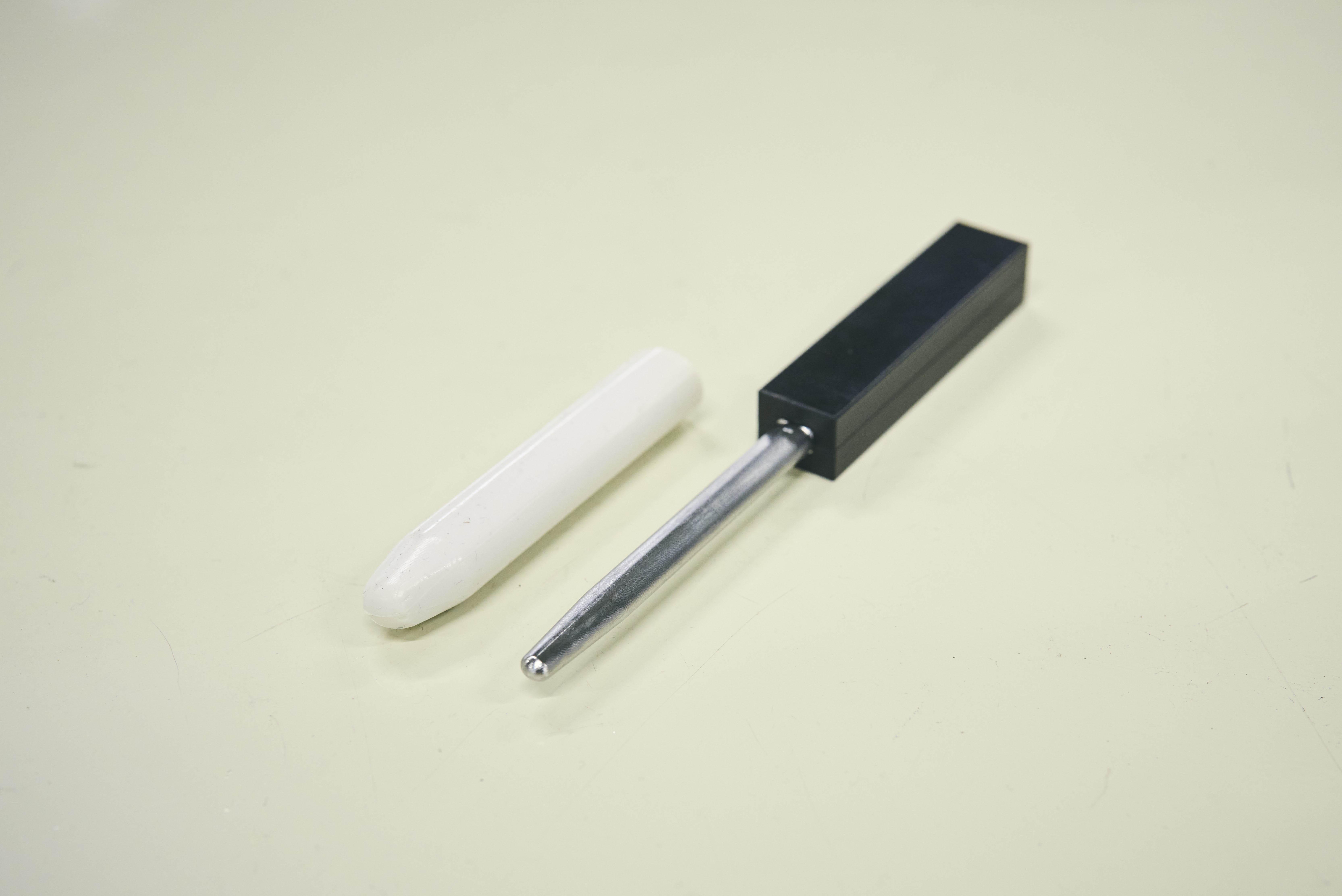
Let’s dive right in: here is the digit in question. Despite being just an imitation of the real thing, it even comes with a metal “bone” at its core.
We asked the project leader why something like this was being developed.
Tatsuro Mori, Project Manager, Elemental Technology Development Dept., Production Engineering Div.
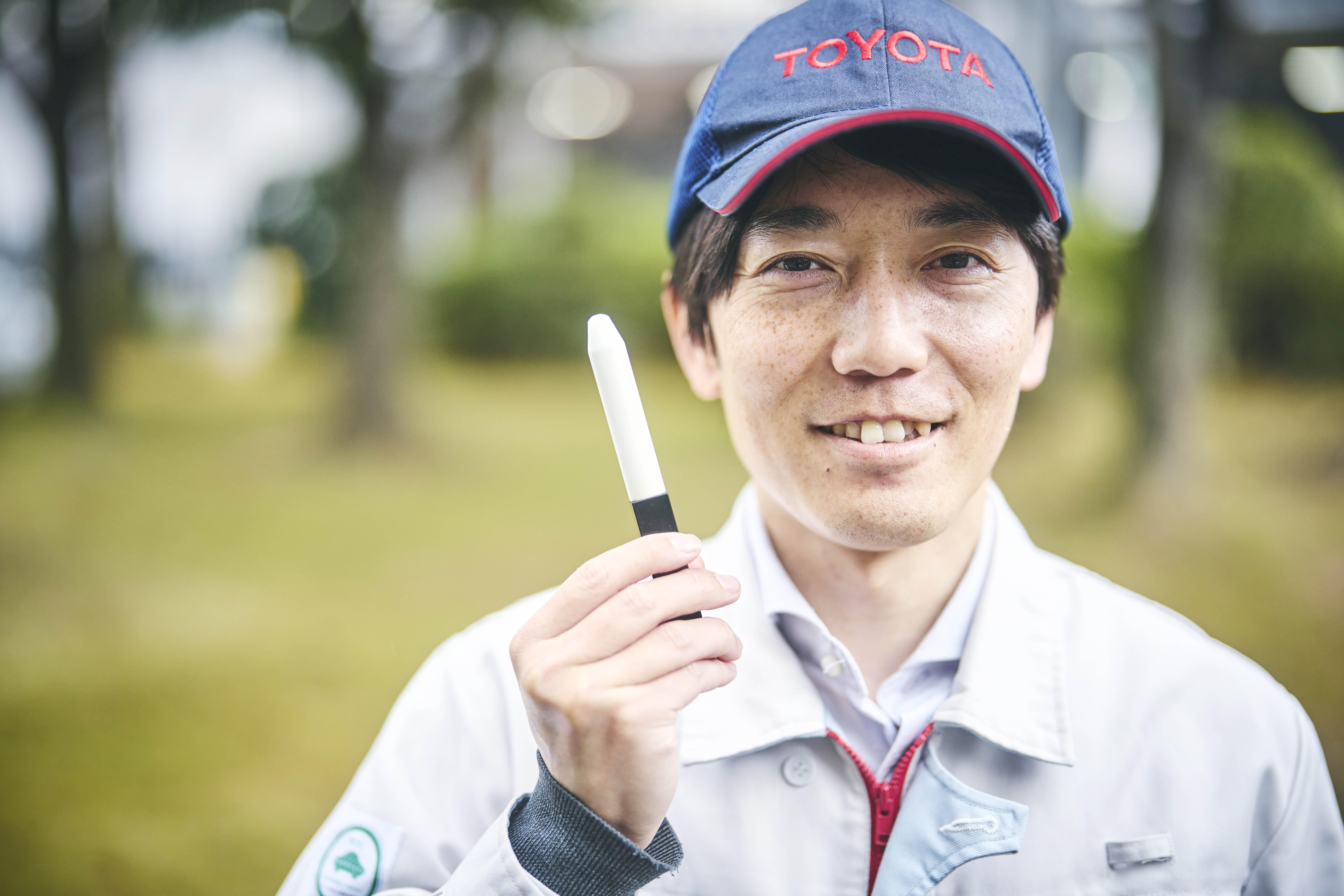
To keep frontline workers safe.
As is true across the manufacturing industry, falling birthrates and an aging population mean our workforce will keep shrinking. More and more, we are likely to find ourselves working alongside robots.
With people and robots coming closer, there are concerns about the safety risks to workers’ hands.
Many injuries in the manufacturing sector involve hands and fingers, which may become caught in machinery.
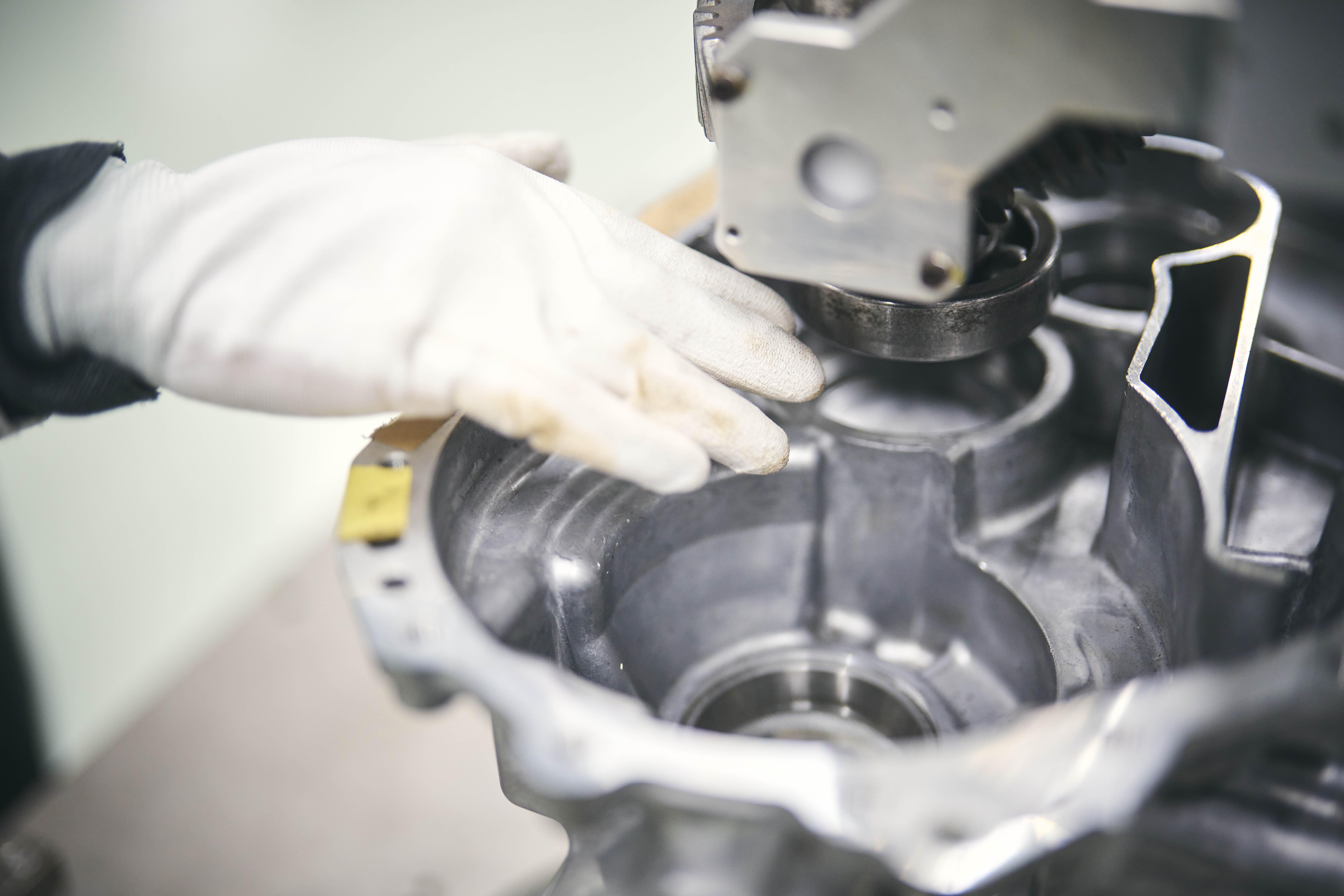
Mori
We teamed up with Panasonic’s Product Analysis Center to develop a dummy finger for assessing safety.
ISO (International Organization for Standardization) standards include safety evaluation guidelines. However, these don’t account for the possibility of fingers being caught in narrow spaces under 10 mm, and there are inevitable limits to detecting dangers with sensors.
Automotive parts are often hard or have sharp edges. They also involve much intricate work, so we needed a tool for assessing the degree to which fingers could become trapped within small surface areas.
Development kicked off in 2019 as a collaboration with Nagoya University and Panasonic, which was engaged in similar research.
Working with the Safety & Health Promotion Division that oversees safety at Toyota, Mori led the project as part of his role coordinating plant-wide robotics and automation. Among some 70,000 Toyota employees in Japan, he is the only one making fingers.
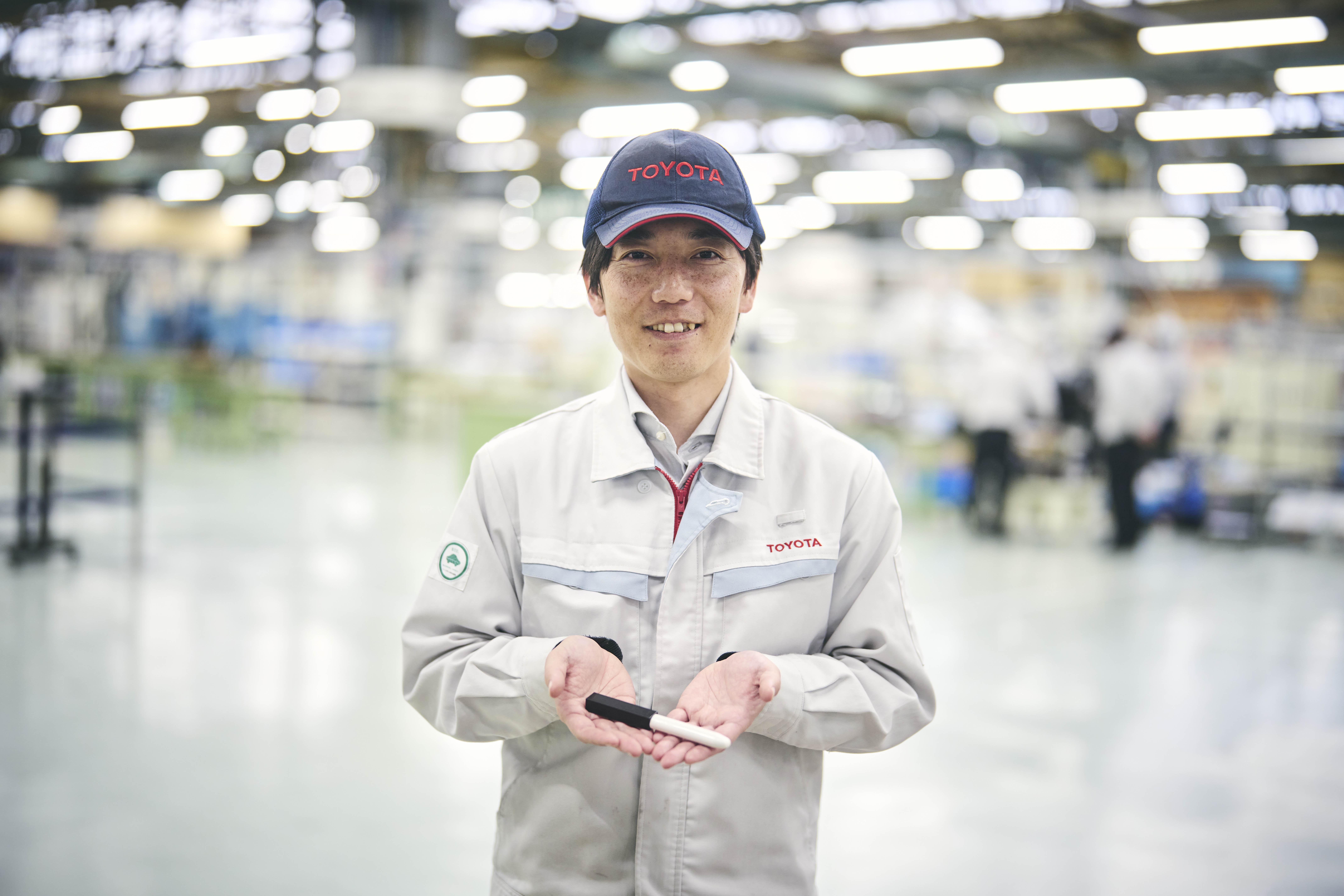
As for the implement itself, it seems strikingly analog for this day and age. Meaning no disrespect, we posed the question to Mori.
Mori
At the outset, Panasonic’s intention was to create something that would give us data to analyze.
Meanwhile at Toyota, we spoke with the manufacturing division and found that workers preferred something analog that anyone could easily use onsite without a computer. As such, we centered our ideas on being practical and functional.
Every plant is seeking to introduce more productive robots. But if safety assessments take too long, implementation is delayed. Our analog solution reduces the time and effort involved in evaluating safety.
Although an over-emphasis on safety may lead to excessive precautions, making safety the top priority can also help raise productivity. That’s the power of analog—amazingly, this approach eases the workloads of those who assess safety and, by introducing robots, those working on the front lines, while also boosting safety in the process.
The damage plain for all to see
With that, Mori started up some machines to demonstrate the kinds of dangers that lurk on the factory floor.
Mori
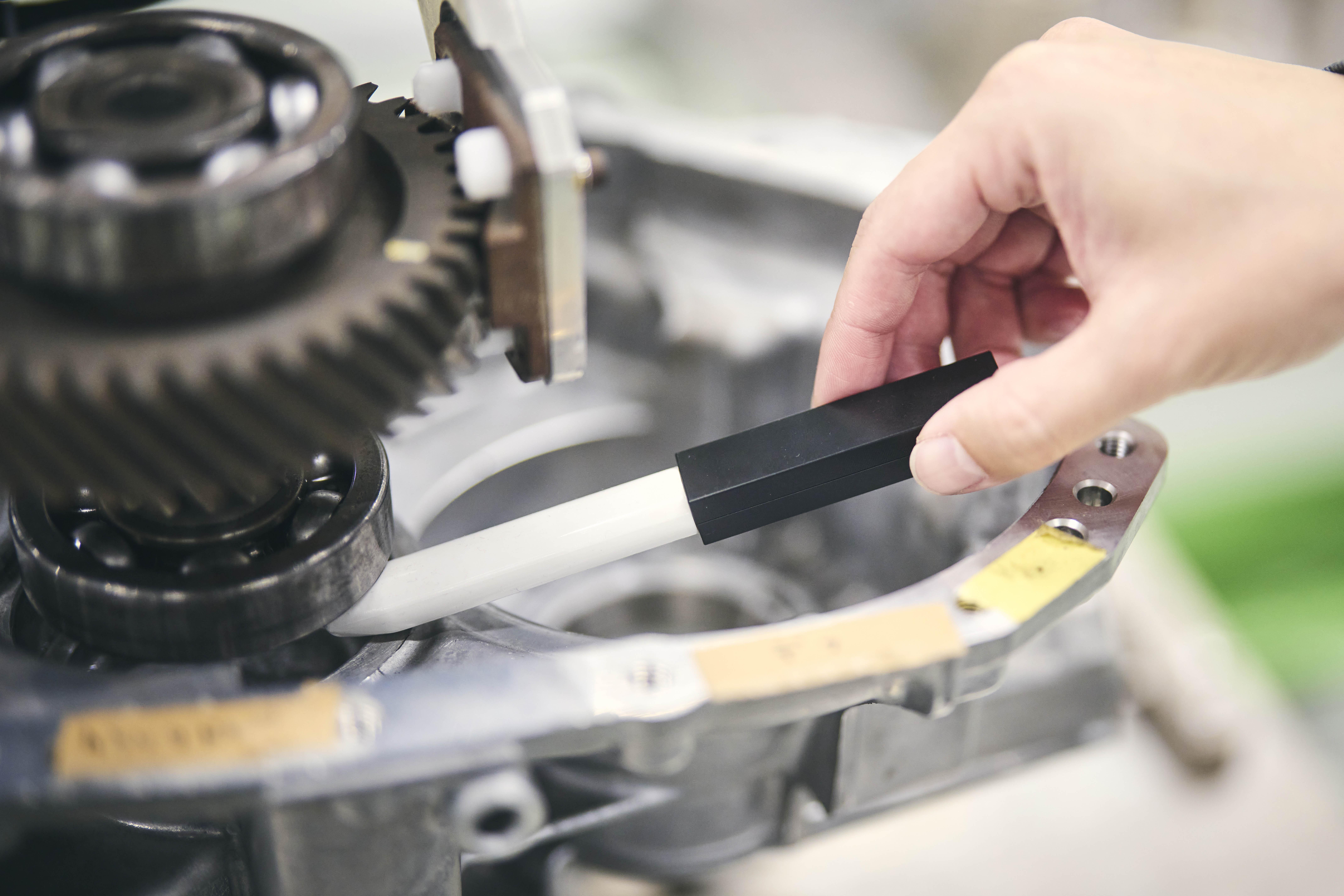
Fortunately, thanks to the meticulous safety measures put in place at each facility, we haven’t had any major accidents involving people working alongside robots so far.
However, it takes a lot of time to check whether these safety measures are adequate. By contrast, inspecting the damage on a dummy finger instantly shows you how much force would cause an injury if a worker’s hand was caught.
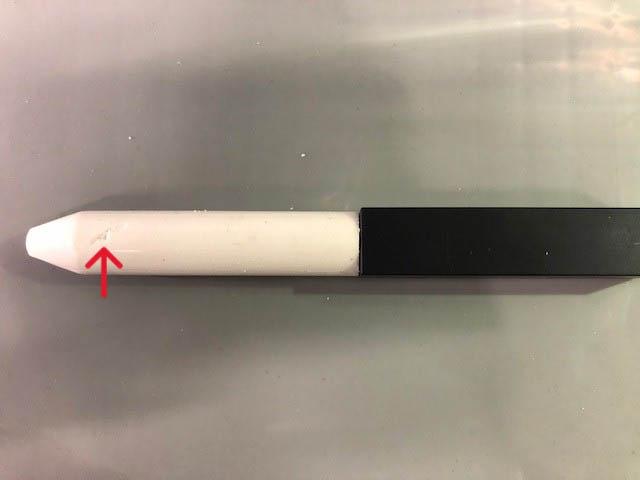
The dummy fingers allow us to visually adjust mechanical forces to safe levels.
At present, these artificial digits are increasingly being used at Toyota’s plants in Japan. Mori also revealed the development backstory, including how a particular animal skin helped him achieve the squishy elasticity of a real finger.