
An ongoing series looking at the master artisans supporting the automotive industry. For the 15th installment, we speak with a master craftsperson who assembles parts with no deviation from design values.
The care of a Century craftsperson
A key factor in the high-precision assembly required of Tanaka and his team is the ability to tighten nuts and bolts with the strength specified in the design. This tightening strength (i.e., torque) is expressed in Newton-meters (Nm).
On vehicle assembly lines, inspection standards typically allow for up to 20% deviation from design values. For example, if a part is to be tightened at 100 Nm, anywhere from 80 to 120 Nm is deemed acceptable.
For the Century, however, the tolerance in assembly is set at 5%. Even with high-precision parts, a single tightening anomaly can affect the vehicle’s finely tuned quality. This is particularly true for the suspension components that Tanaka oversees, where assembly accuracy directly impacts ride comfort.
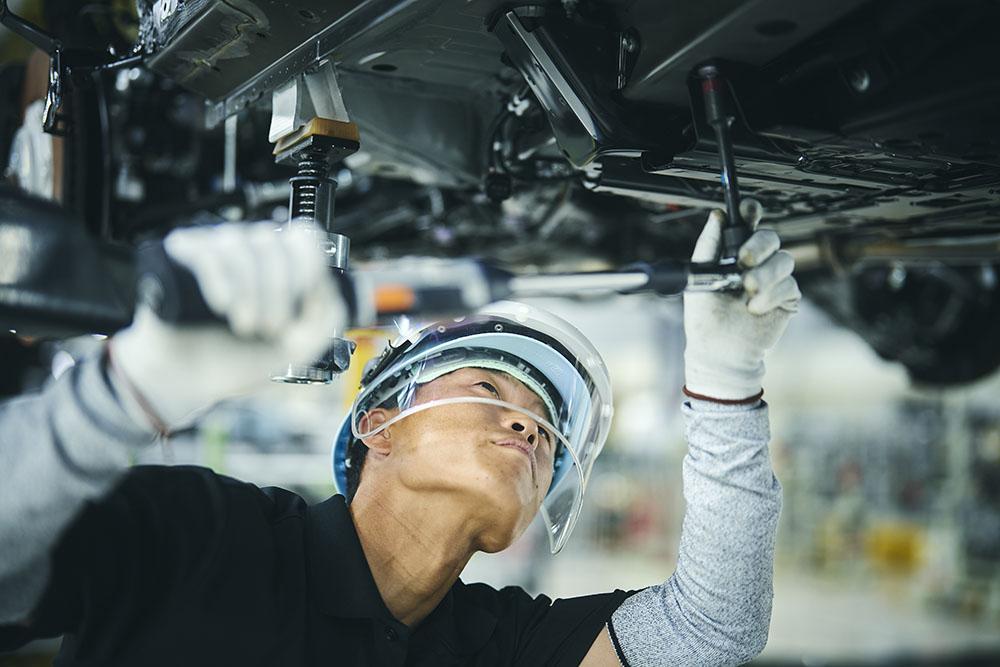
Tanaka
On any assembly line other than the Century, each nut or bolt is tightened in a single pass with a fastening tool. The tool is pre-set with the target torque value, so with a 20% allowance, we can end up within the specified range after tightening just once.
On the Century assembly line, however, the stringent precision requirements mean that we first use a jig to tighten by hand, then tighten again with a fastening tool to get closer to the target torque. Lastly, we use a digital torque wrench, whose torque values are uploaded to the computers, working by hand to obtain the final value.
Although the tolerance for Century assembly is within 5% of the design value, I always aim for 0% in my daily work.
All data sent from the digital torque wrench is recorded, ensuring that the tightening precision for every nut and bolt is tracked.
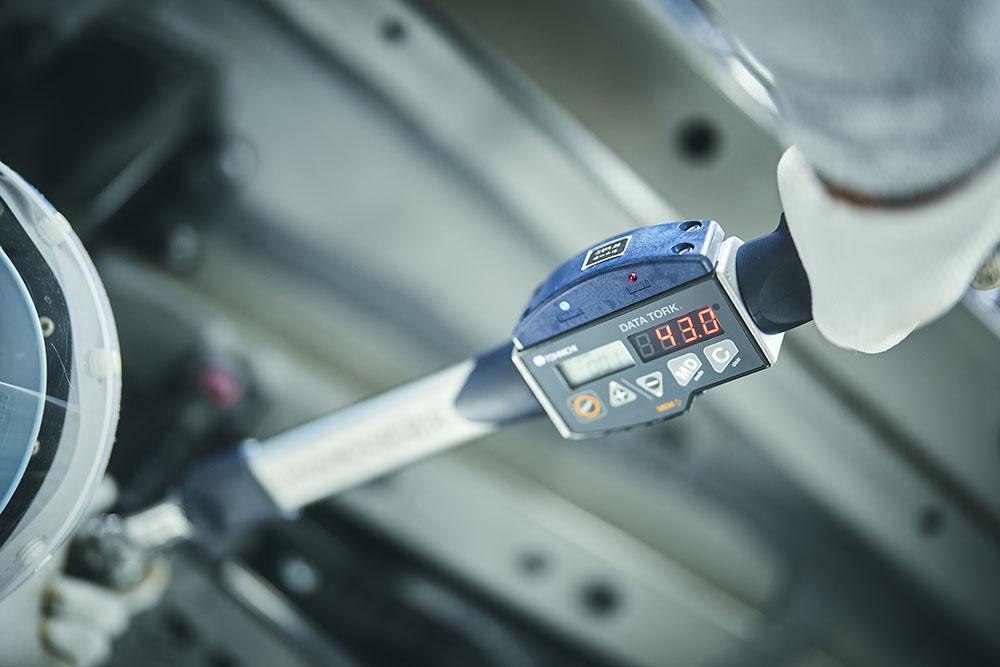
For tightening small parts like battery terminals or wiring harnesses, design values are around 10 Nm, about the same as fastening an ordinary screw with a screwdriver. On the other hand, for something like a drive shaft, which is large and must be firmly secured, the specified tightening values reach 300 Nm.
When working on such bulky parts, tightening takes Tanaka about one minute. For comparison, the figure is around five seconds on a regular vehicle, where the task requires only a fastening tool. This means that he spends more than ten times as long, carefully tightening each nut and bolt.
Tanaka explains that the job becomes increasingly difficult as torque values rise.
Tanaka
For instance, with fairly low design values up to about 50 Nm, controlling the torque is relatively easy because you can feel it by hand. However, for torques of 150 Nm or more, you’re working with large wrenches and using your whole body, which makes it quite hard to deliver torque accurately.
This is truly a world of feeling and intuition. I’ve improved my accuracy by tightening all kinds of nuts and bolts, working each day to figure out how I can get that deviation from the design values closer to zero.
As a Century craftsperson, Tanaka says the most important thing for him is the sense of camaraderie.
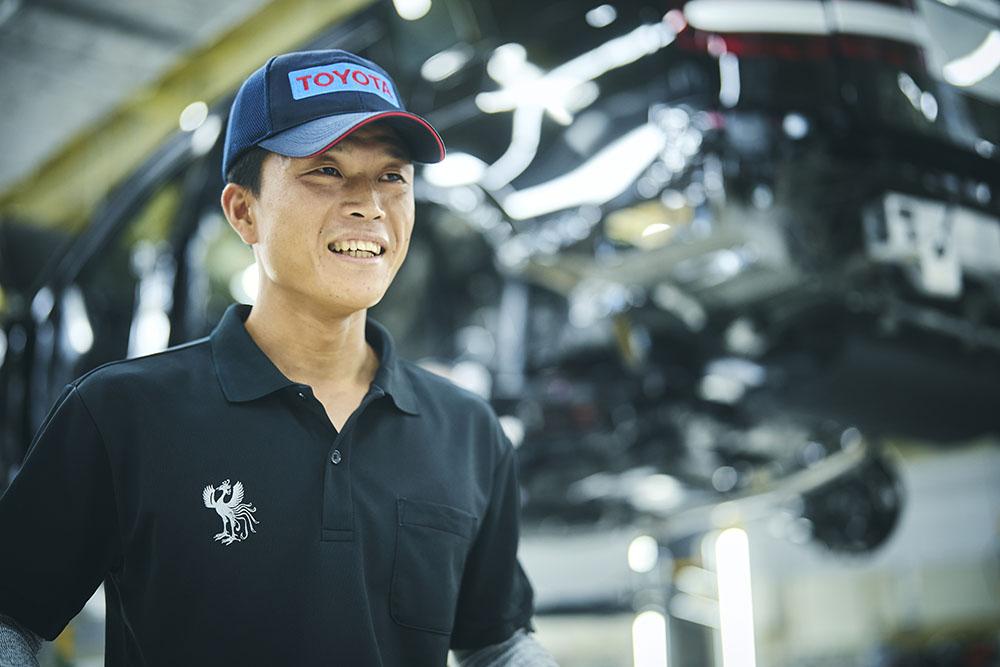
Tanaka
Needless to say, carmaking is certainly not something you can do alone. Learning from each other, we want to work as a team to create cars that customers will appreciate. Everyone on the Century production floor feels the same.
In a few years, when I move onto another role, I hope to use the many things that I’ve learned through the Century project to train the next generation.
Alongside the advanced skills, deep knowledge, and mindset required of Century craftspeople, the team has developed a camaraderie that will no doubt continue driving Toyota’s efforts to make ever-better cars.