
Why is Toyota involved in expressway construction, and how exactly does "virtual Genchi Genbutsu" improve conditions for workers?

GEN-VIR, a construction simulator, is playing a key role in visualizing the process, along with talk of a strange new concept, “virtual Genchi Genbutsu.” What has Toyota been up to on the construction site?
Crawling into work
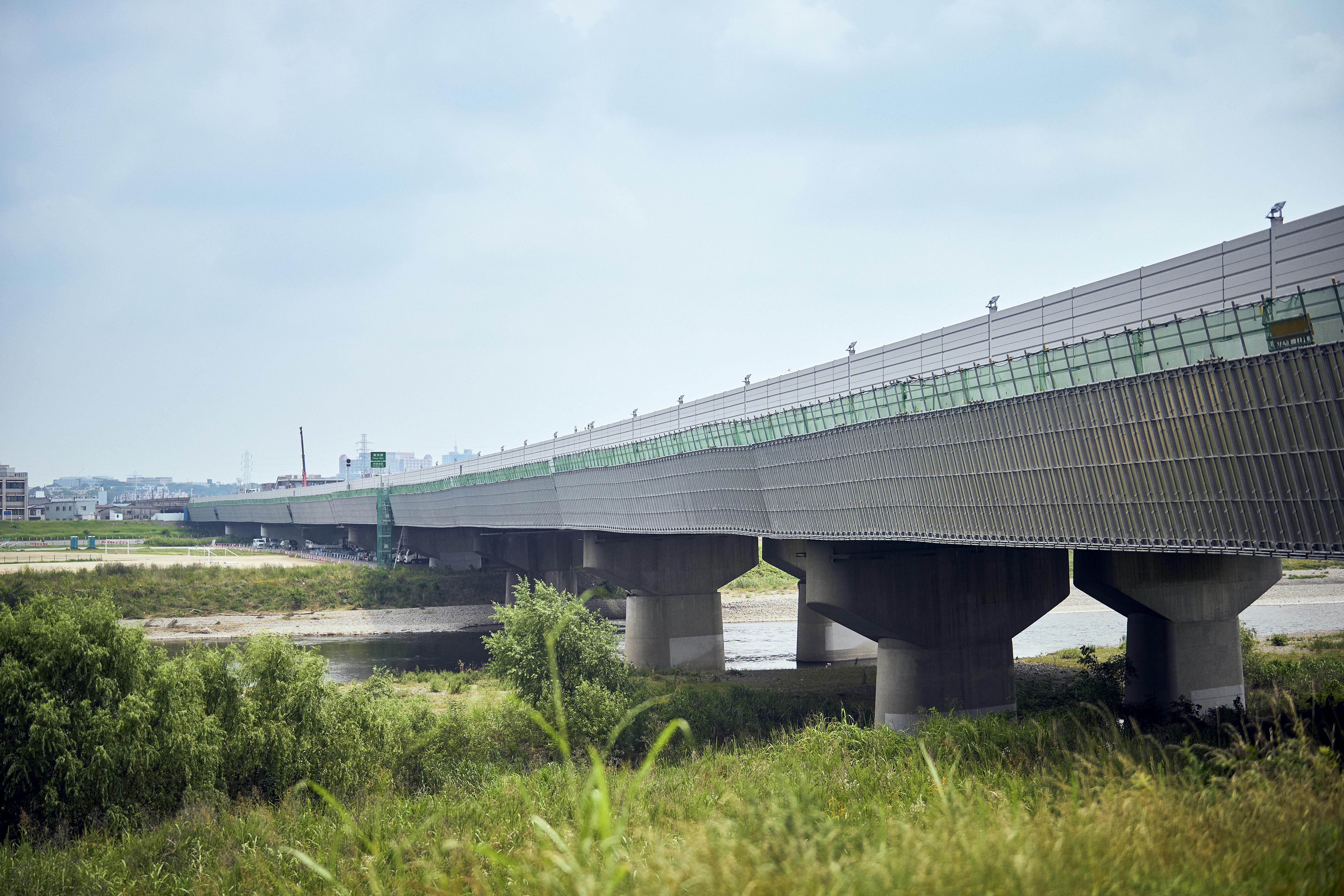
When Toyota Times visited the banks of the Tama River, we found a Toyota employee venturing into a mysterious location. Ascending a steep staircase inside a restricted access area, this is what we saw:
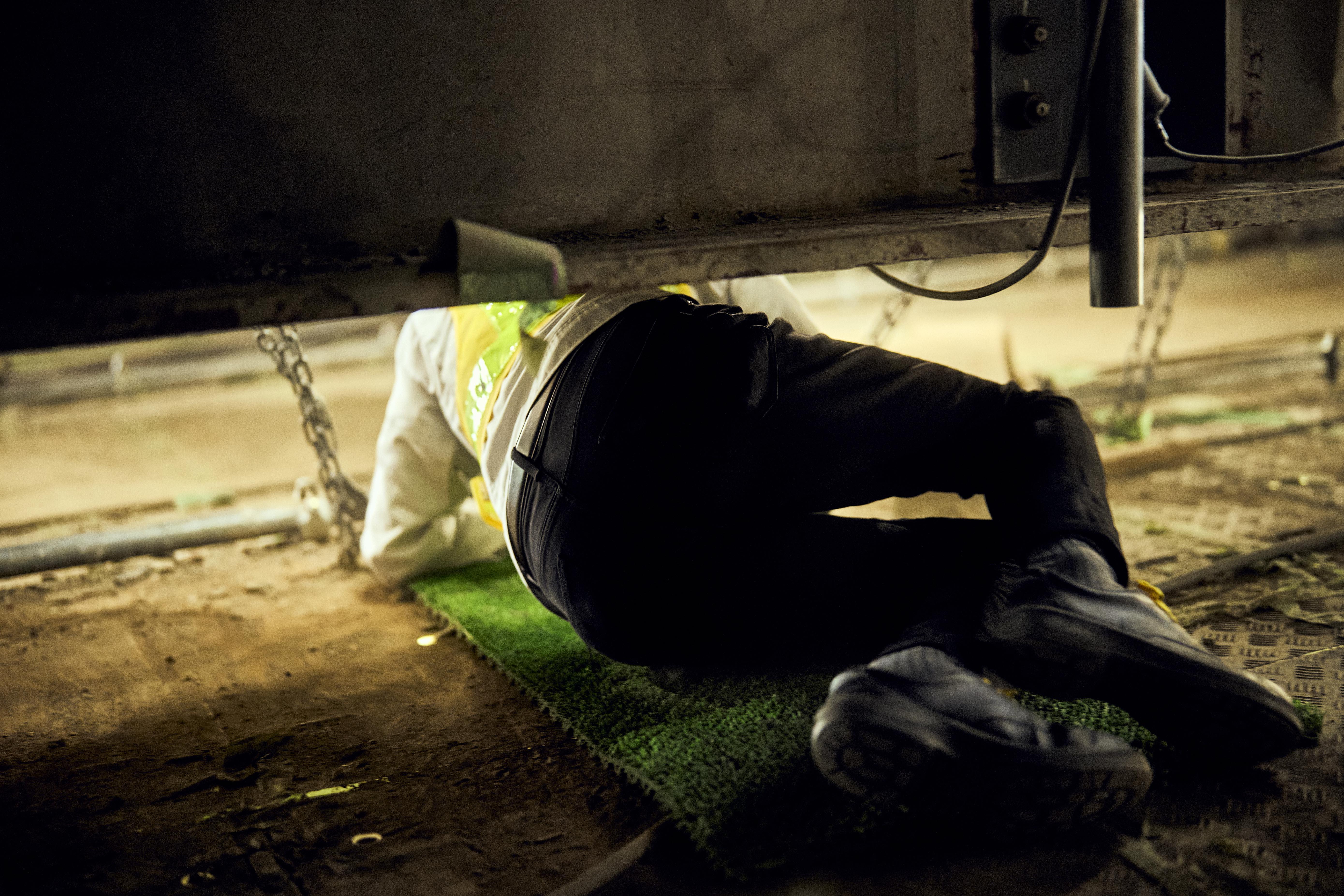
The inside of an expressway bridge girder, crisscrossed by steel beams.
The Toyota employee seemed right at home. Without hesitation, he suddenly got down on the floor and began crawling through a gap of no more than 50 cm.
Clad in a helmet and goggles and working within the safety guidelines of site staff, he pushed on further, looking to confirm certain results firsthand in the genchi genbutsu tradition.
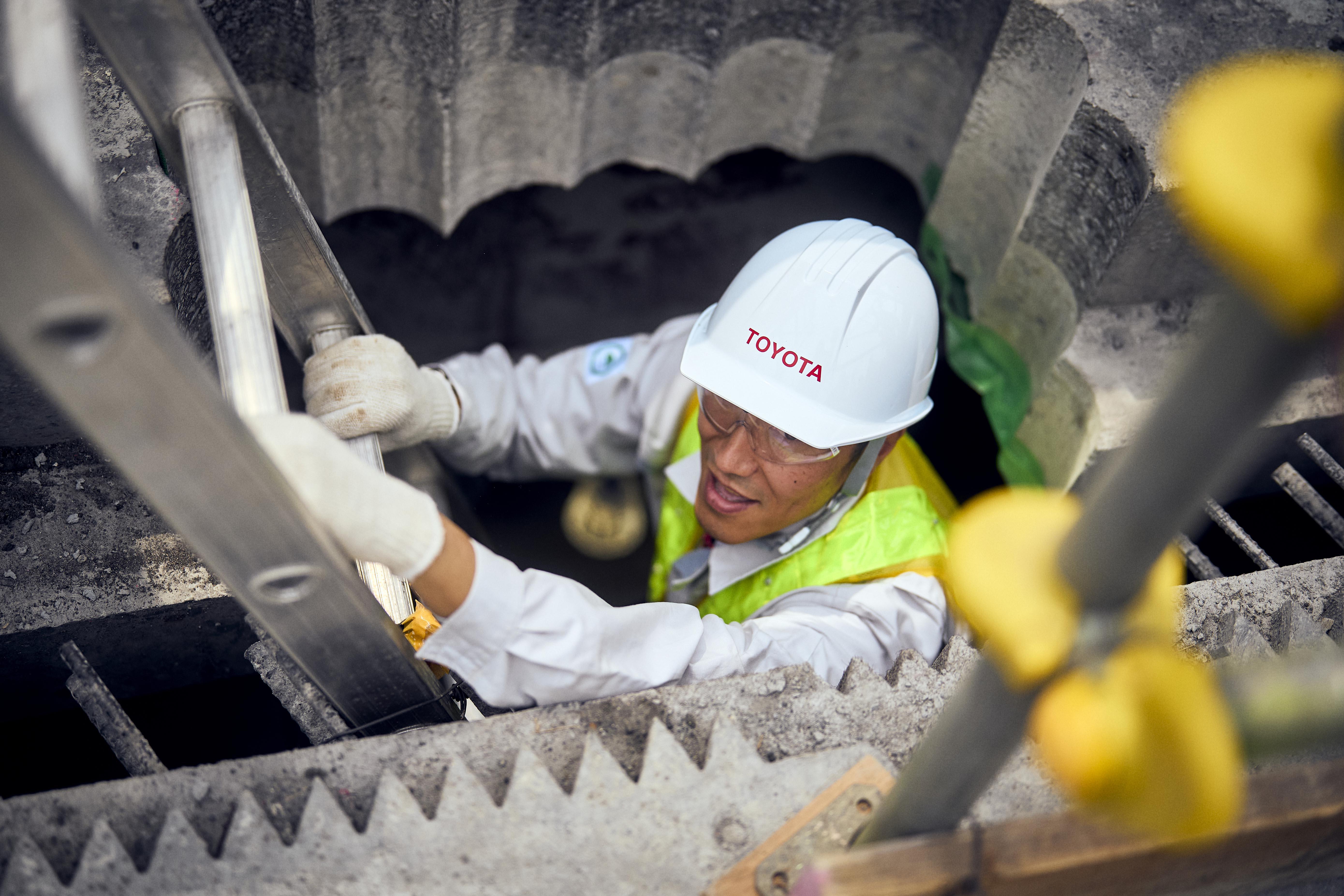
Climbing a ladder, we arrived atop the Tomei Express Tamagawa Bridge that links Tokyo and Kanagawa Prefecture. Traversed by around 100,000 vehicles daily, this is Japan’s third busiest stretch of expressway.
The cars whizzed past, one after another. Why was a Toyota employee coming to work in such a place?
“Virtual Genchi Genbutsu” explained
Toyota has developed the construction simulator GEN-VIR to improve conditions for on-site workers. This particular site is a proving ground for testing whether Toyota’s kaizen (continuous improvement) can be incorporated into a vast construction project that involves 10,000 tonnes of concrete.
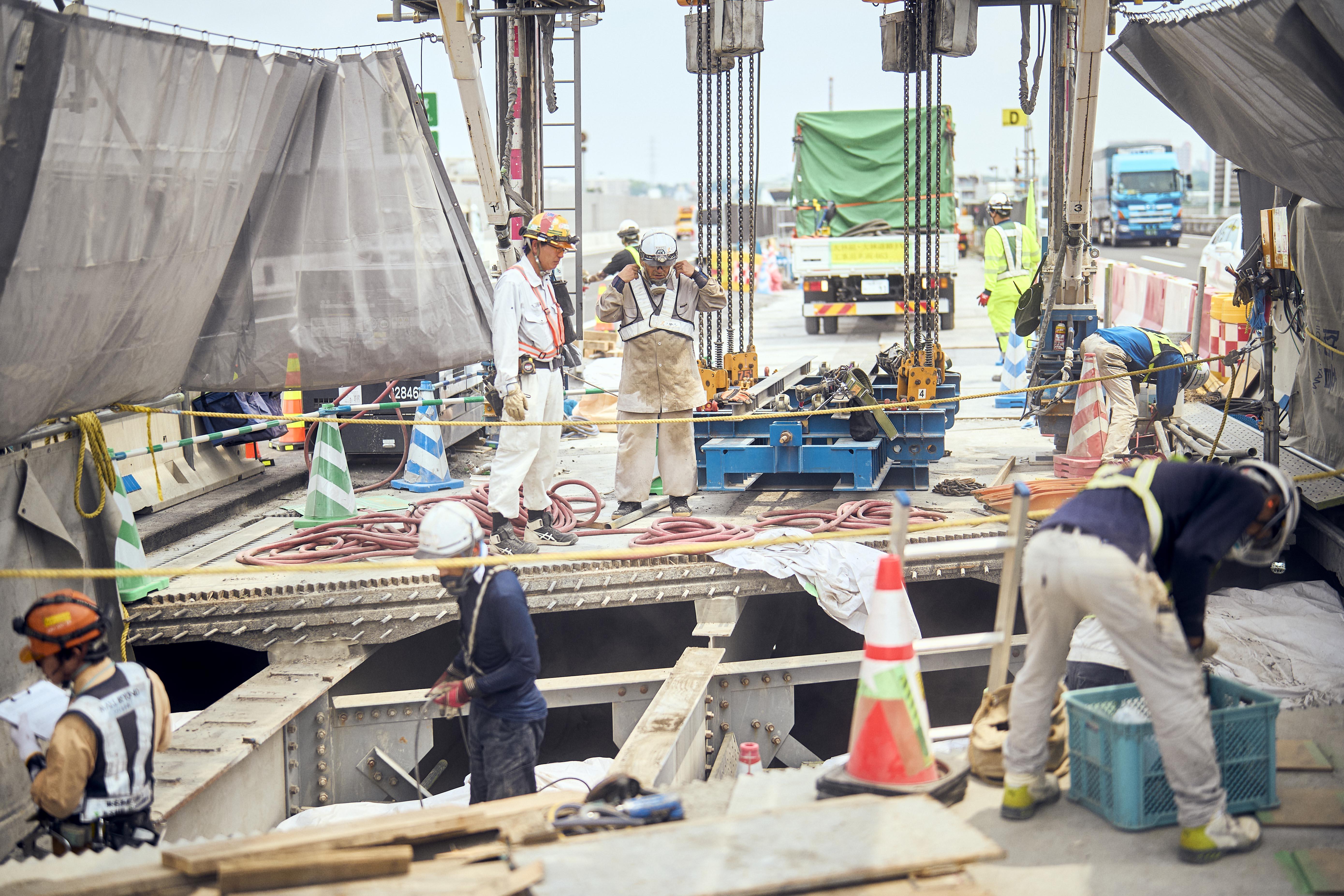
Let’s start with a simulation video to see what the construction work entails.
This simulation trial is a joint research project with Obayashi Corporation. The work involves replacing the deck slabs that make up the road surface of the Tomei Express Tamagawa Bridge, a span of expressway that has deteriorated over the roughly fifty years since its construction.
As many roads that were built during Japan’s period of rapid growth near the end of their lifespans, the construction sector is seeing a surge of renovation projects. With more large-scale works on the horizon, the industry is facing severe labor shortages.
Part of the solution is to ease the burden on workers as much as possible.
Closing off an expressway in the Tokyo metropolitan area is a challenging task. To get around that, the work must be broken up into stages, requiring significantly more people and time. Making things more difficult, factors such as the weather and personnel can change from moment to moment.
This creates the need for virtual Genchi Genbutsu, a simulation of the physical site. But could kaizen be applied to a complex project entirely different from carmaking?
Yuji Ito, Group Manager, Infrastructure System Group No.2, Frontier Research Center
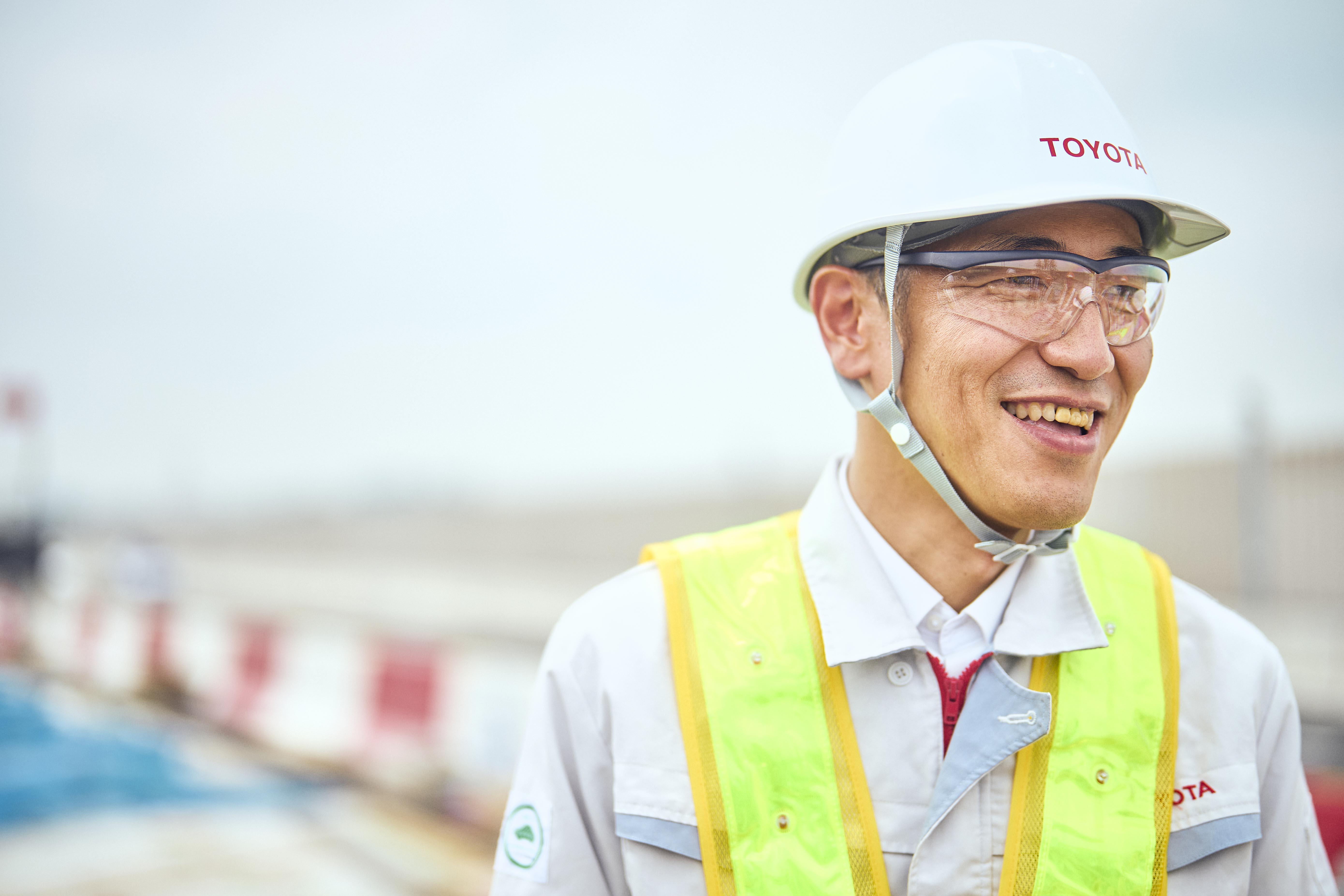
We strived to streamline tasks and processes so that the work could be carried out with minimal downtime.
To use driving as an analogy, when traffic is designed to flow well, with little congestion or red lights, you can keep moving at a constant speed and reach your destination sooner. You also get better fuel efficiency.
In other words, improving flow reduces wasted time, making the job easier for workers. It also shortens the construction schedule, leading to happier users as well.
However, continuous work inevitably causes fatigue, which is why Toyota also set out to simulate processes that are less physically demanding and provide time for recovery.
The result was a 20% reduction in working time while cutting personnel requirements by 20%. Though only a simulation, both Toyota and Obayashi sensed great promise.
Improving conditions for construction workers
“In situations involving repetitive tasks, Toyota’s kaizen produces tangible benefits,” says Takahiro Kanemaru, a project director for the Obayashi Corporation/Obayashi Road Corporation joint venture (Obayashi JV).
Takahiro Kanemaru, Project Director, Project Office, Obayashi JV
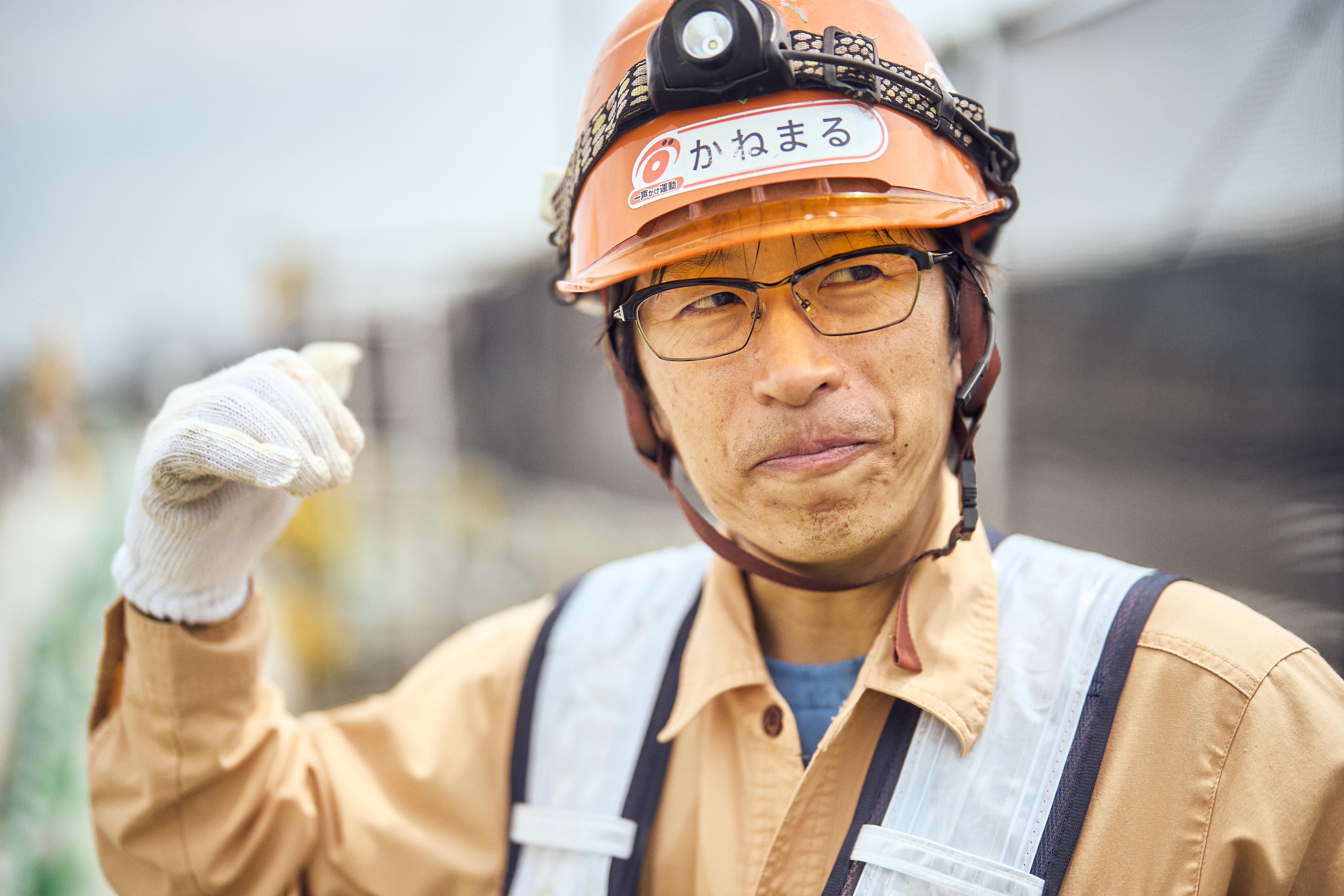
At Obayashi, our ultimate goal is to make someone else's job easier, as Chairman Toyoda says. That’s why we strive to improve efficiency.
A renewal is more technically challenging and time-consuming than a new build. It also demands more from workers.
With the number of projects set to grow, we fear that the construction industry’s future is in peril if we do not increase productivity while also easing workloads.
Translating simulation results into real-world practices helps to improve conditions for many workers. However, the venture’s efforts also went beyond simulation.
Toyota’s production facilities (genba) employs the Kanban system to make the sequence of operations clearly visible. At the Tama River site, work vest colors play the same role. Teams are given different colors to identify who is working on which task easily.
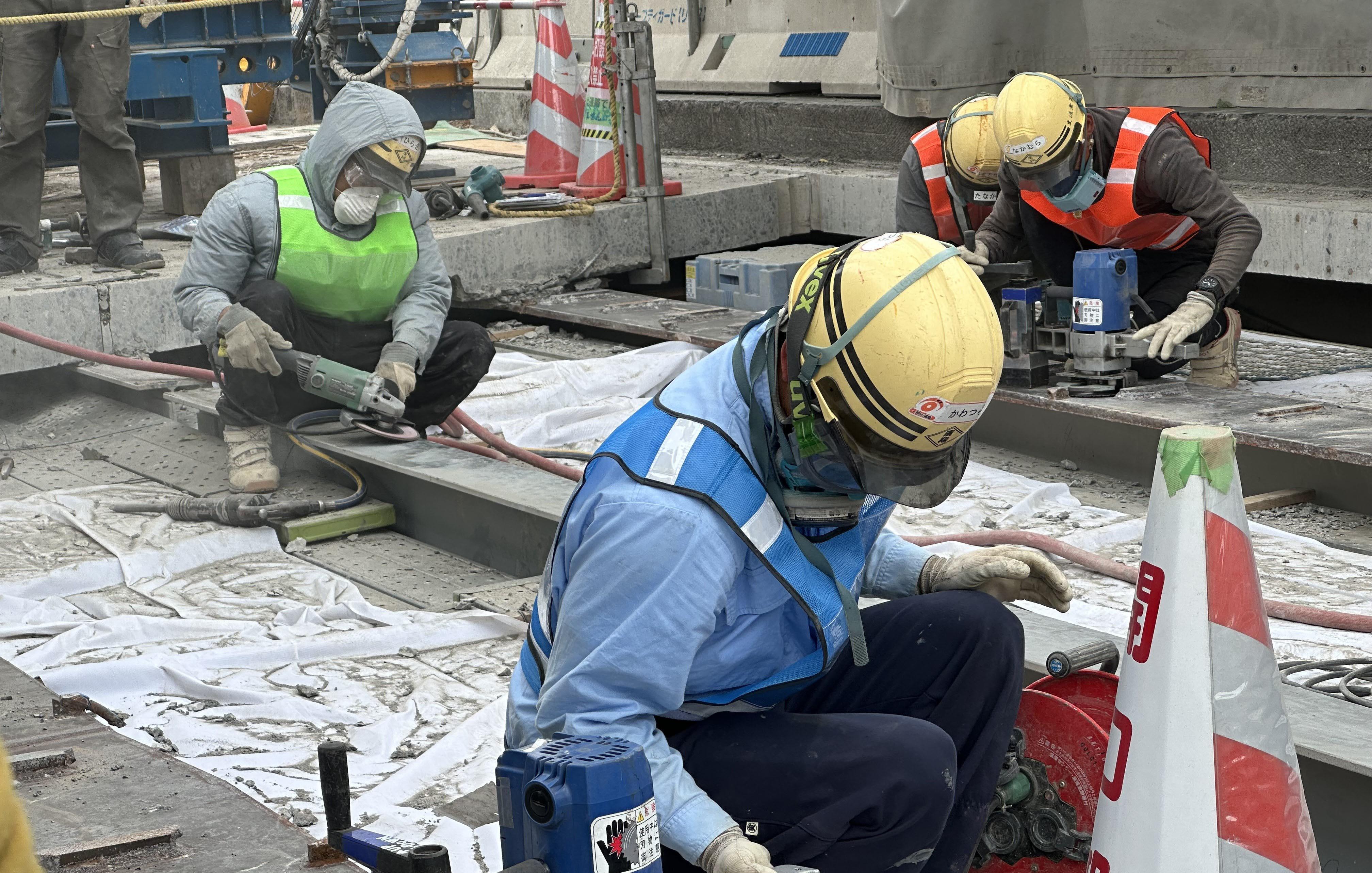
Takahiro Kanemaru, Project Director, Project Office, Obayashi JV
Previously, many well-meaning workers would move on to one task after another without taking lunch breaks, trying to finish the job before the expressway became congested. Working alongside each other, it was hard to tell who was doing what.
To make things more organized, we streamlined the process with a simple rule: only handle the tasks assigned to your vest color.
Another innovation was the use of simulations to check worker fatigue.
Yuji Ito, Group Manager, Infrastructure System Group No.2
We have data on how long someone can work with arms raised, which we used to estimate the level of fatigue. Through joint research with Toyota Central R&D Labs.,Inc., we came up with a gauge that shows the percentage of a worker’s remaining stamina.
Picture something like the stamina bar in a fighting game.
Workers welcomed the various initiatives that were trialed, saying they appreciated being able to have lunch and the mental boost of seeing the steps to the finish line.
And yet, some site workers responded with skeptical expressions, as if to say, “How can we do that?”
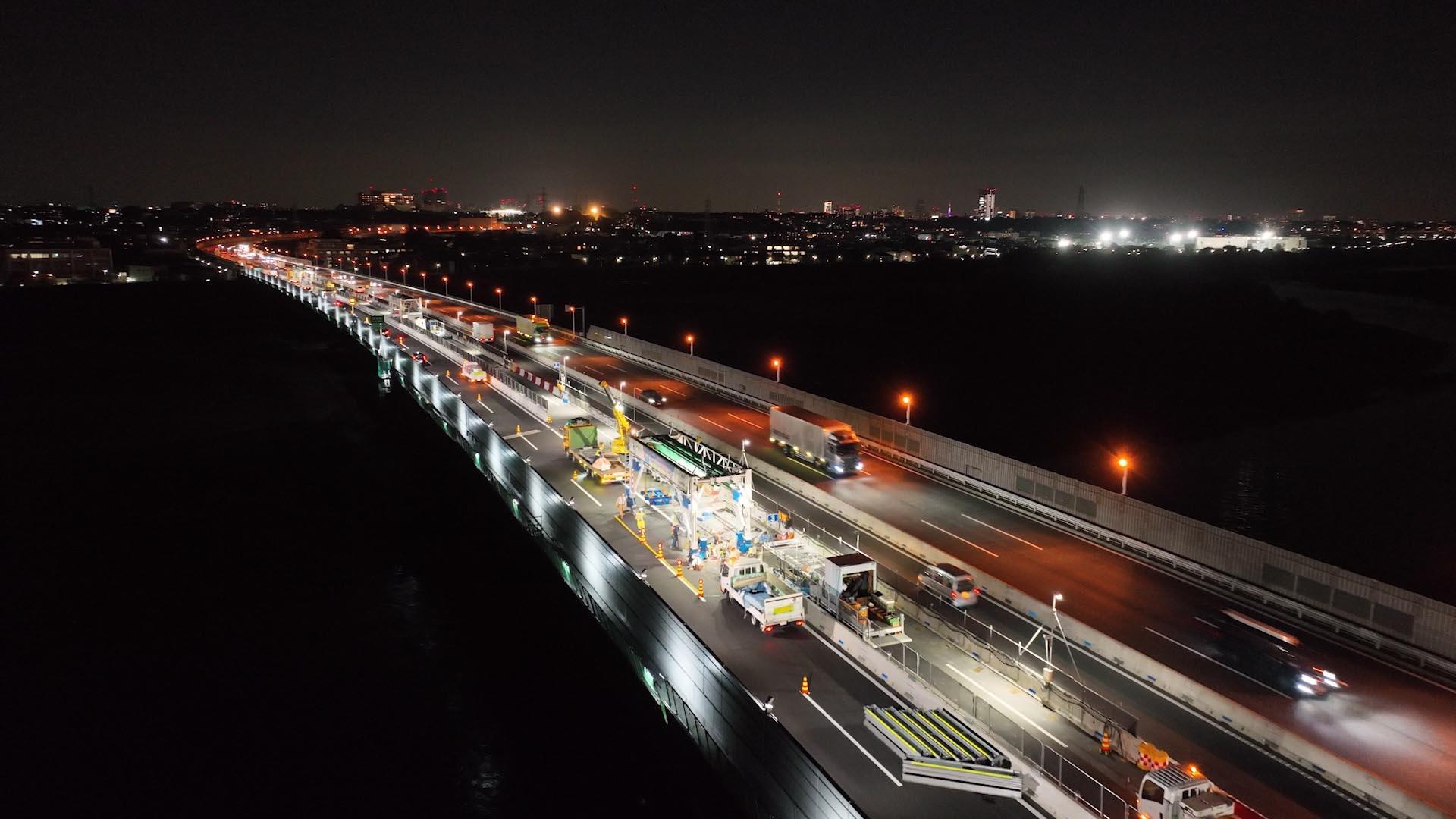