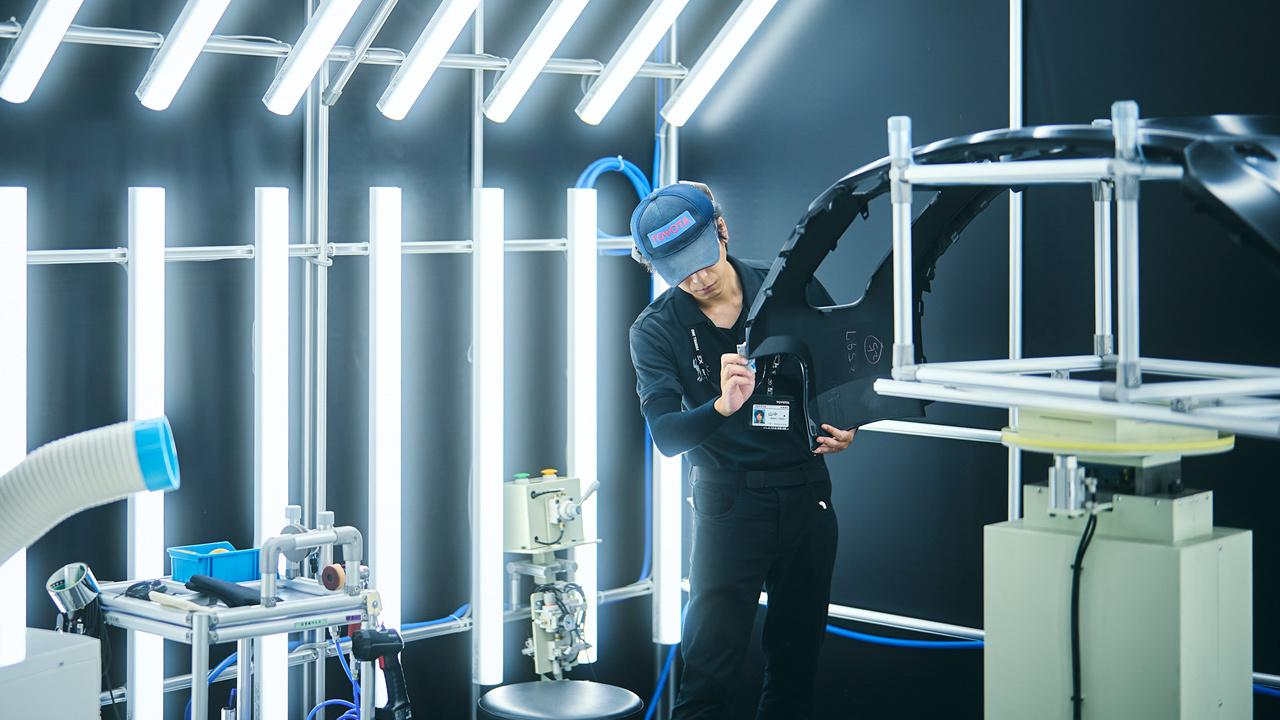
The process of molding plastic car parts inevitably leaves behind some faint work lines. To achieve the stunning finish of a Century bumper, one master plastics polisher smooths these markings down to thousandths of a millimeter.
Turning 0.02 mm into 0.002 mm
As mentioned earlier, injection molded plastic parts generally move on to the painting process, with parting lines left untouched. Therefore, Yamanaka’s first task was to develop the methods for polishing PLs to make them as smooth as possible.
In fact, certain models, such as the RC and RC F, already employ a polishing process for parting lines factored into the design. With the techniques used on those models serving as a benchmark, Yamanaka trialed various ways of achieving the clarity standards set for the new Century.
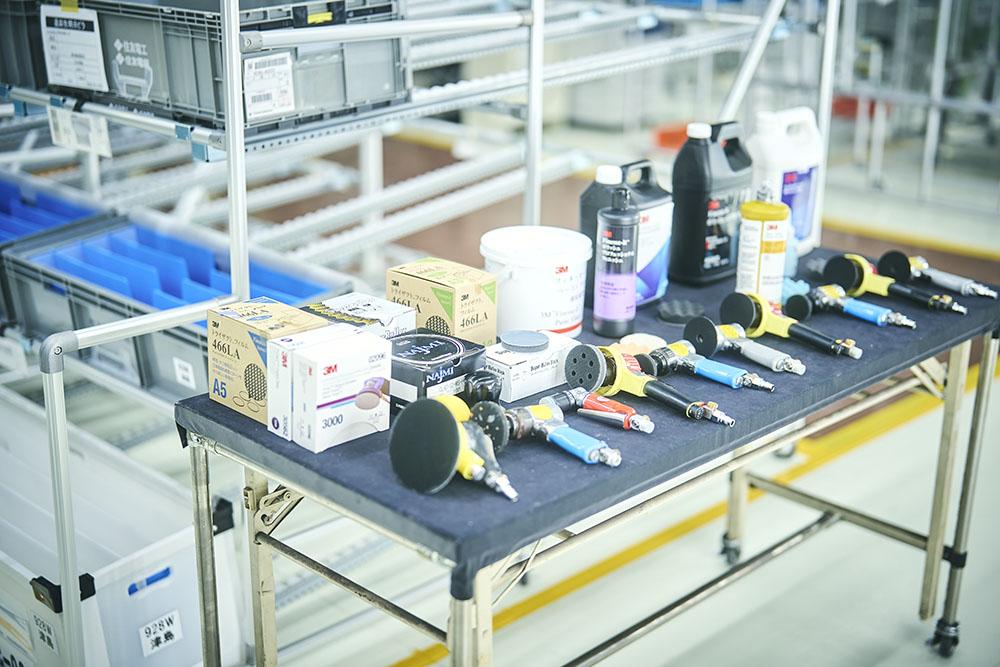
Yamanaka
In the beginning, I tried everything I could think of, from heating the PLs with a gas burner to using the tools with which dentists grind cavities. Eventually, I settled on a method that breaks it down into three separate steps, using both grinders and hand polishing.
The sandpaper used for polishing is numbered according to coarseness, with smaller digits indicating coarser grit.
To find the optimal method, Yamanaka trialed dozens of combinations, using both hand tools and electric grinders with various sandpaper grits. The technique he finally arrived at divides the polishing work into three stages.
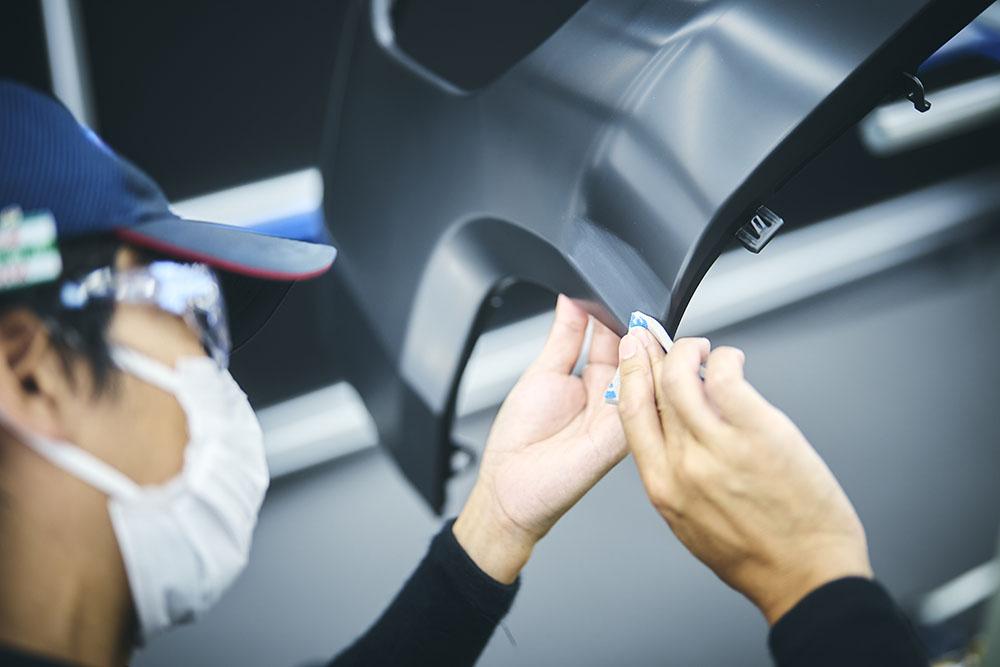
In the first stage, Yamanaka uses 600-grit sandpaper to remove 80-85% of the PL’s height. Stage two grinds away a further 10-15% with 1000 grit. By this step, the 0.02 mm parting line is down to a ridge of just 0.007 mm.
As it happens, these first two stages ended up exactly the same as the method used for the Lexus RC F.
These alone, however, proved insufficient for meeting the Century’s quality requirements, leading to a third stage: a final finish with ultra-fine 2000 grit paper. The process hones the line to a height of just 0.002 mm.
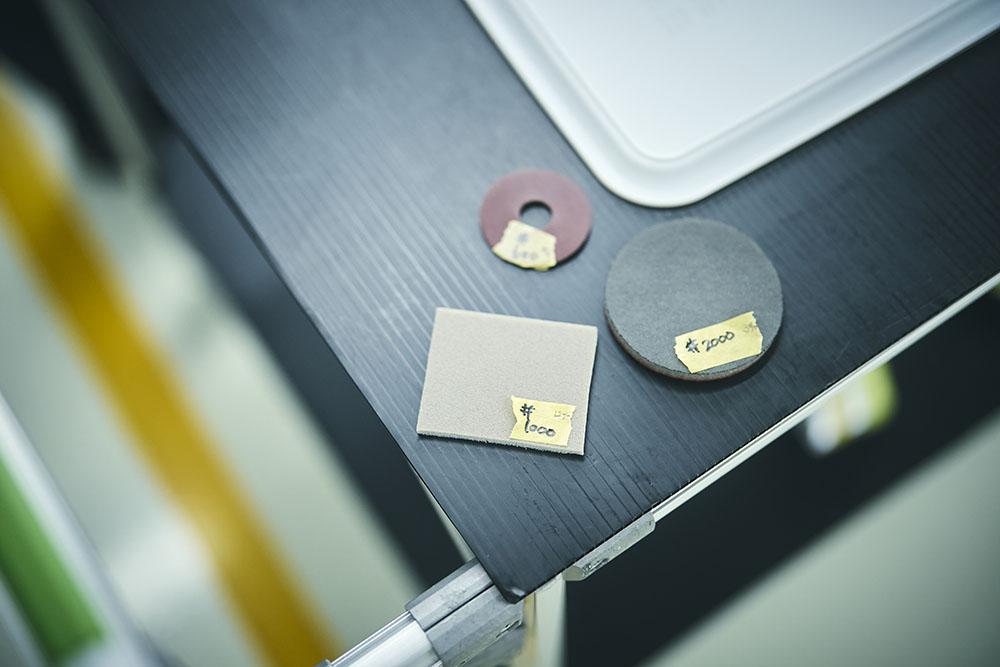
Yamanaka
For the first stage, I use an electric grinder to even out the surface, but in the second step, I switch to working by hand, adjusting the degree of polishing from section to section to ensure a smooth final finish.
The key lies in seeing with your eyes and sensing with your fingertips as you go, which is why I insist on doing the task by hand.
Checking the finished surface, the parting line seems to have vanished entirely to the untrained eye, with even the fingers failing to pick up any trace.
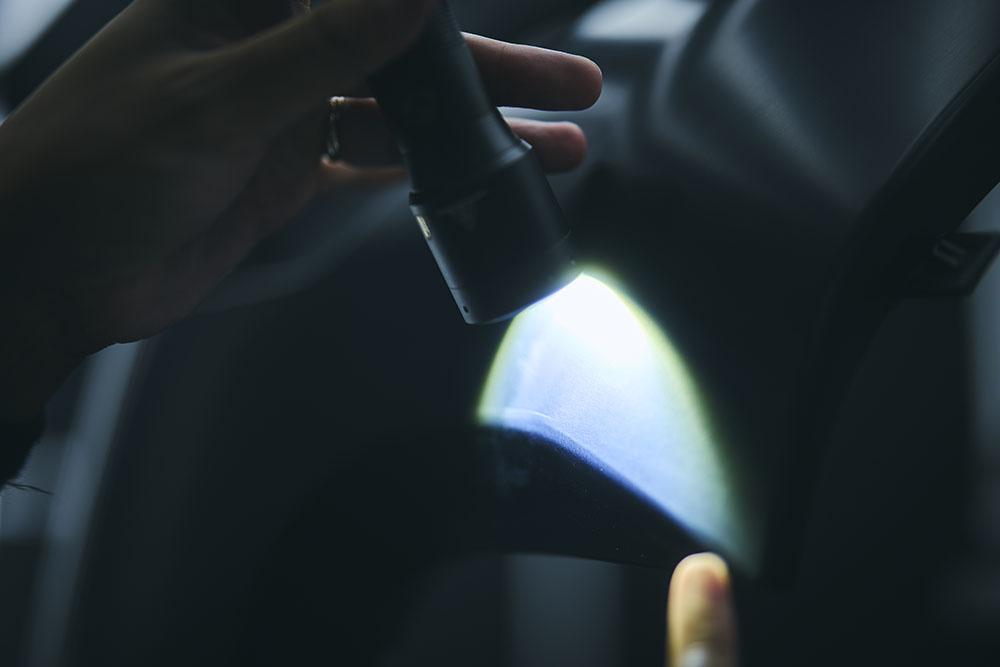
Yamanaka
To be honest, I was relieved once I settled on the process, knowing that I could prepare the surface to meet the Century’s quality standard. Starting from scratch, at first, I wasn’t sure whether I could pull it off.
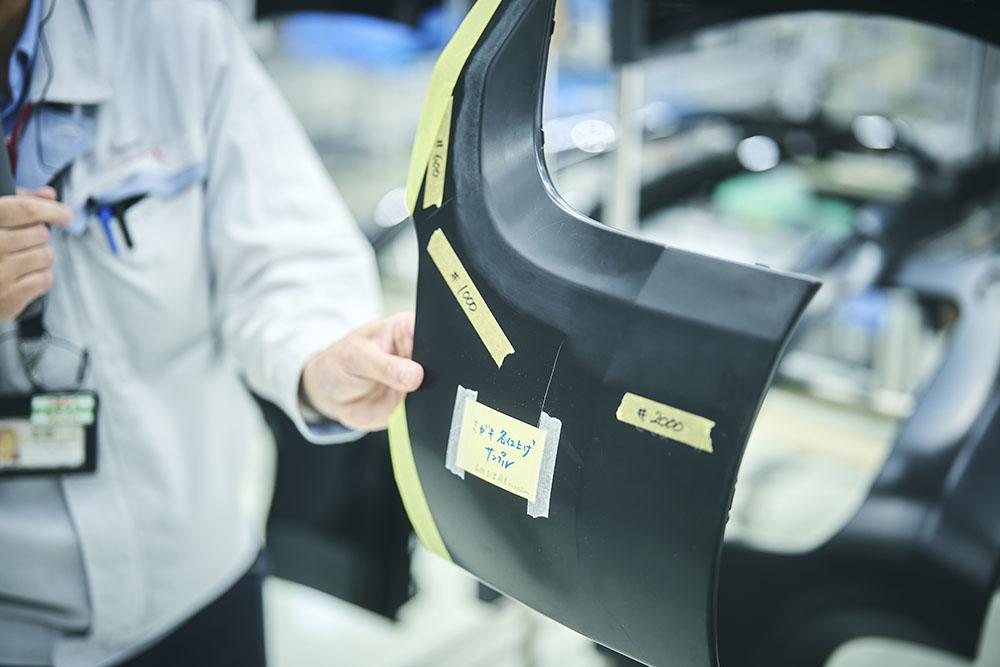