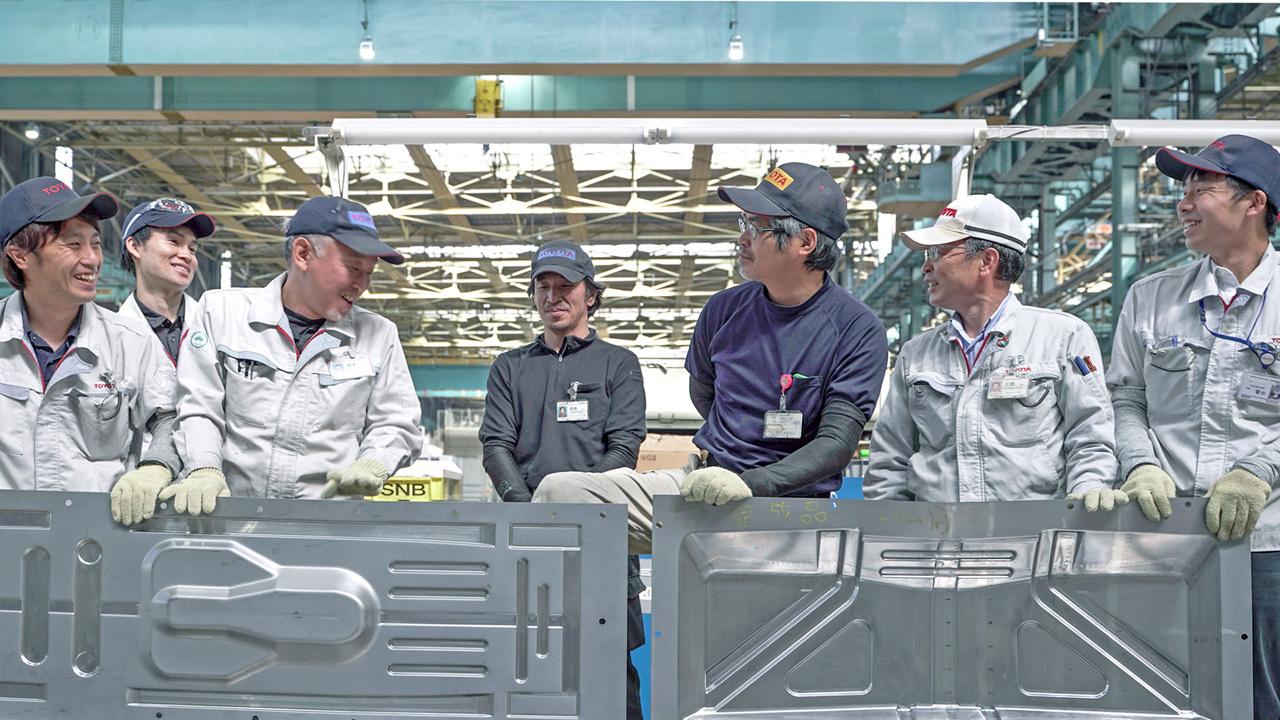
This series explores the project to restore a first-generation Crown, a car that embodies Toyota's origins. Part 6 reports on a groundbreaking process for rapidly reproducing corroded body panels at minimal cost.
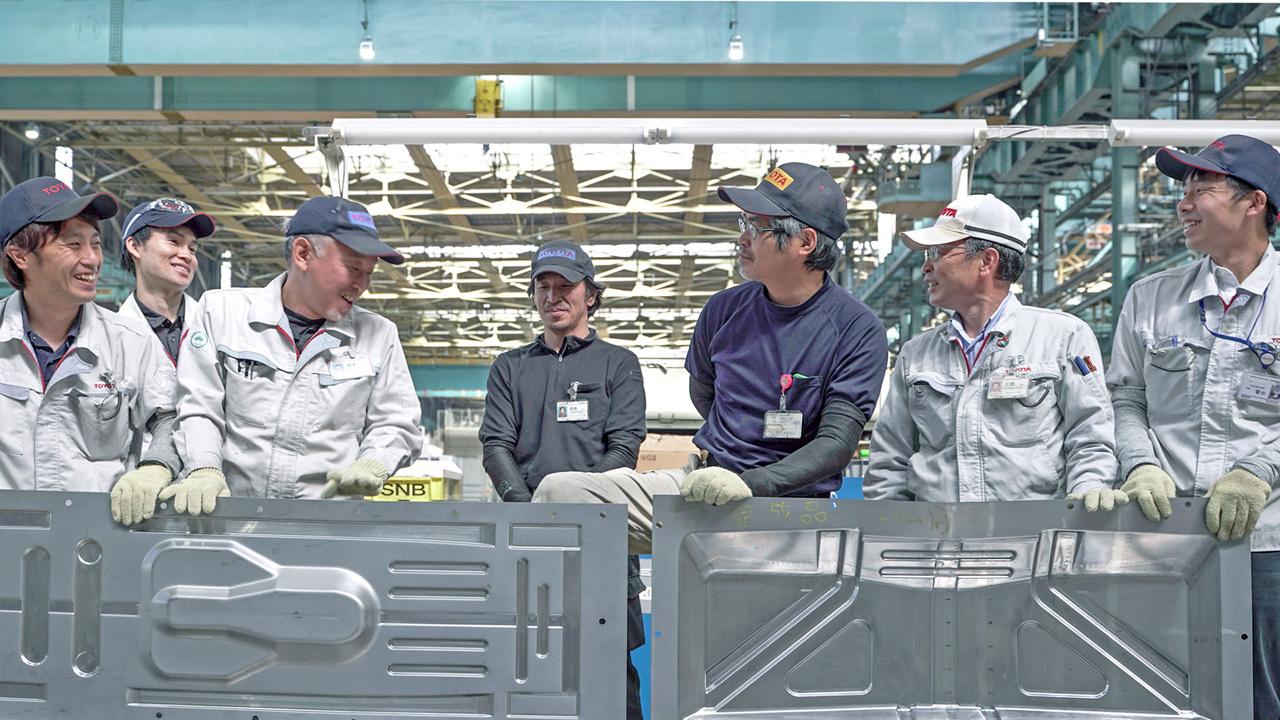
A project to restore a first-generation Crown started in the spring of 2022 at the Motomachi Plant, bringing together a diverse group of skilled members.
This series closes in on their restoration efforts.
In this sixth article, we delve into “incremental forming,” the metalworking technique introduced in Part 4 and used in restoring the car’s body.
A groundbreaking technology for building body parts from scratch
As introduced in Part 4, the task of restoring the first-generation Crown’s body was taken up by an elite group of nine members from across the company, including the Tsutsumi, Tahara, Takaoka, and Motomachi plants, as well as the Technical Development & Prototype Division.
Unfortunately, the body and related parts turned out to be in a poor state, with severe rusting. This was particularly true for the underbody, which is not visible from outside, and areas such as the bottom of doors and wheelhouses, where rainwater inevitably pools. Corrosion on the floor and rocker panels proved far worse than expected, leaving the team with no choice but to cut out the rusted sections and rebuild them from scratch.
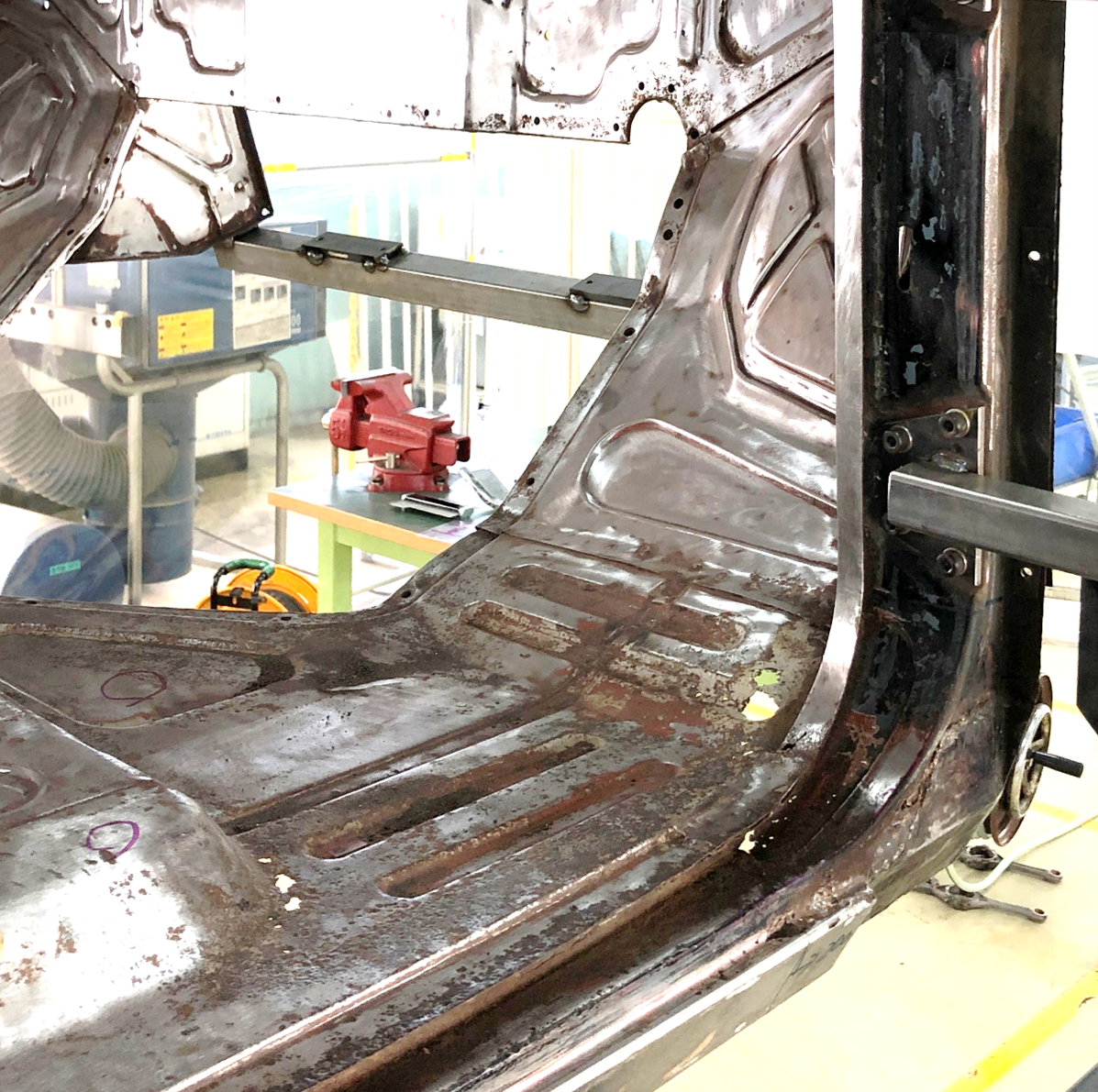
For the team, this was an obvious choice, given the project’s commitment to restoring the first-generation Crown to its original condition by replicating the monozukuri (manufacturing) processes of its day.
However, the biggest barrier to creating body panels from scratch is manufacturing costs. Stamping them out in the same way as mass-produced vehicles would require an enormous outlay of time and money.
A huge set of body panel stamping molds, like those featured in the fifth article of our series on Toyota’s carmaking masters, costs upwards of ten million yen and takes a long time to fabricate and fine-tune. This makes stamping feasible only for high-volume models with production runs in the tens of thousands.
Body panels can also be made using the time-honored method of hammering sheet metal by hand. The presence of skilled sheet metal craftspeople among Toyota’s production personnel made this option possible but time-consuming.
Resolving these issues was crucial to achieving one of the project’s goals: a low-cost, high-quality restoration made possible by the superior skills of a carmaker.
Building upon the Publica restoration
The members who proposed the first-generation Crown restoration recognized this challenge from the outset and had been researching potential solutions within Toyota and beyond before the project even kicked off.
In the process, they came across incremental forming, a technique already adopted by Toyota’s Mobility Tooling Division that had first caught their eye when restoring the Publica.
The Crown restoration project got underway in April 2022. In June, as the car was being stripped down to the last screw, particularly severe rust and corrosion were found on the floor and rocker panels, as mentioned earlier.
These two panels, at least, would somehow have to be completely rebuilt. The team decided to consult the Mobility Tooling Division’s SX Masanori Sato and EX Masashi Takahashi, along with technician Kohei Takayama, about making the floor panels with incremental forming.
Sato had been a specialist in stamping mold correction (welding, precision repairs, quality adjustments). While also involved in training others, he continued to push himself and was selected for the incremental forming personnel due to his wide range of skills. He is now a twelfth-year veteran in the technique.
In this job, Sato prides himself on “never turning down a request—even if a design seems unworkable, we figure it out together.”
Takahashi has also acquired a wide array of skills from previous roles, including prototype parts fabrication (sheet metal working, welding, laser machining), mold correction, and panel surface inspection. Among the highlights of his stellar career is a gold medal in sheet metal work at the 35th National Skills Competition.
On the job, Takahashi strives for efficiency, keeping reworking to a minimum by not skimping on advance planning.
Incremental forming attracts manufacturing genba attention
Takayama

Incremental forming is a technique for shaping thin metal sheets by pushing a tipped tool across surface sections. The shape is formed not by removing material but by applying force to gradually deform it.
More specifically, we set a flat metal sheet in the processing machine and shaped it with the tipped tool by applying force through computer numerical control.
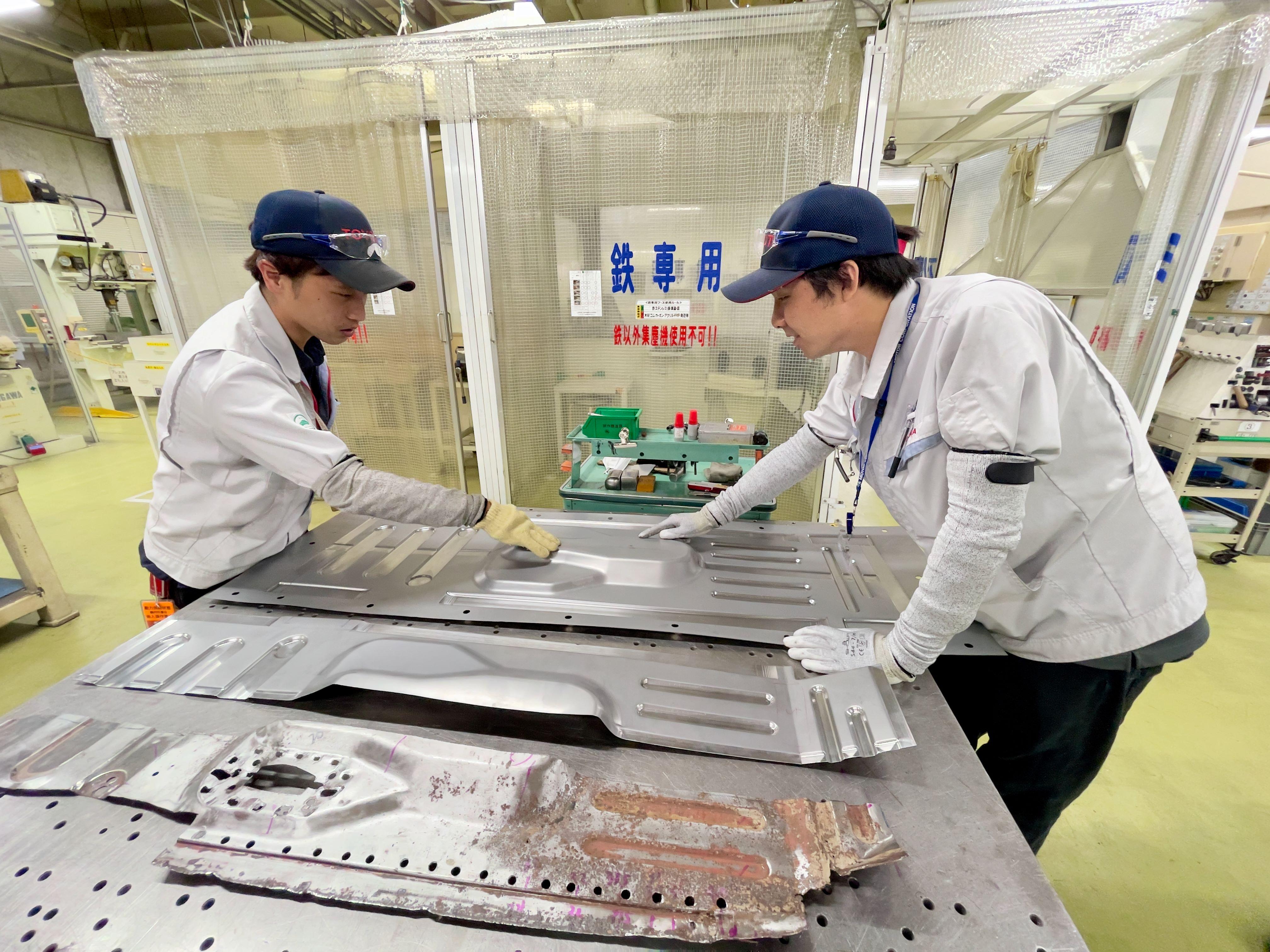
The Mobility Tooling Division, where Takayama works, first employed this technology back in 2012 to create embossed lettering on the door of the iQ GRMN SuperCharger.
By eliminating the need for molds, incremental forming can drastically reduce both machining costs and development time. In recent years, it has attracted attention in the auto industry and beyond as a plastic processing technology that reduces the cost of high-mix, low-volume production. Carmakers are competing fiercely to develop the technology.
Making the same body parts by hand using a mold would take a skilled sheet metal craftsperson several days for each piece.
With incremental forming, however, the work is automated by numerically controlled machinery, requiring only processing data and the flick of a switch. This makes the technique ideal for situations such as fabricating additional spare parts.
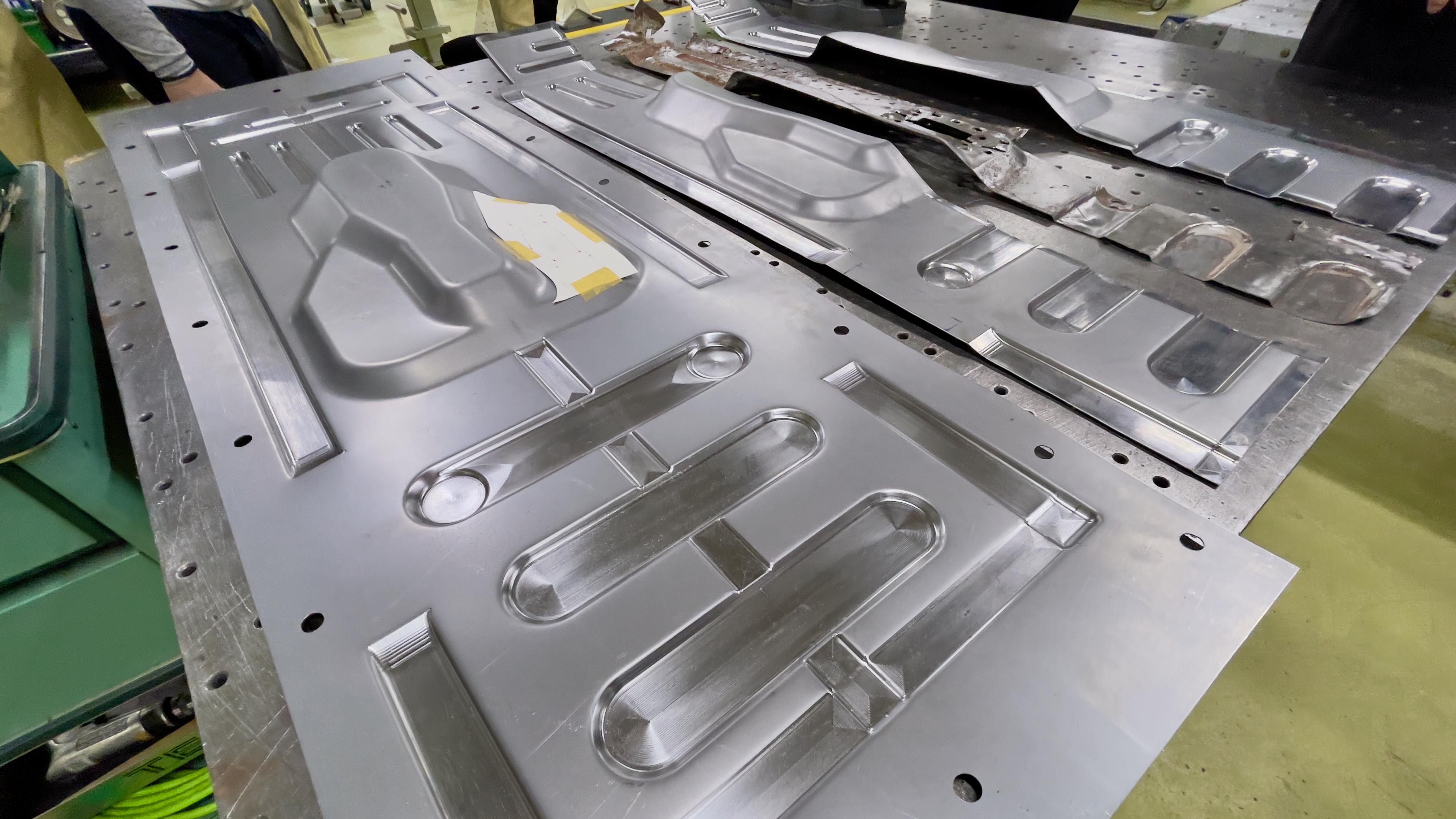