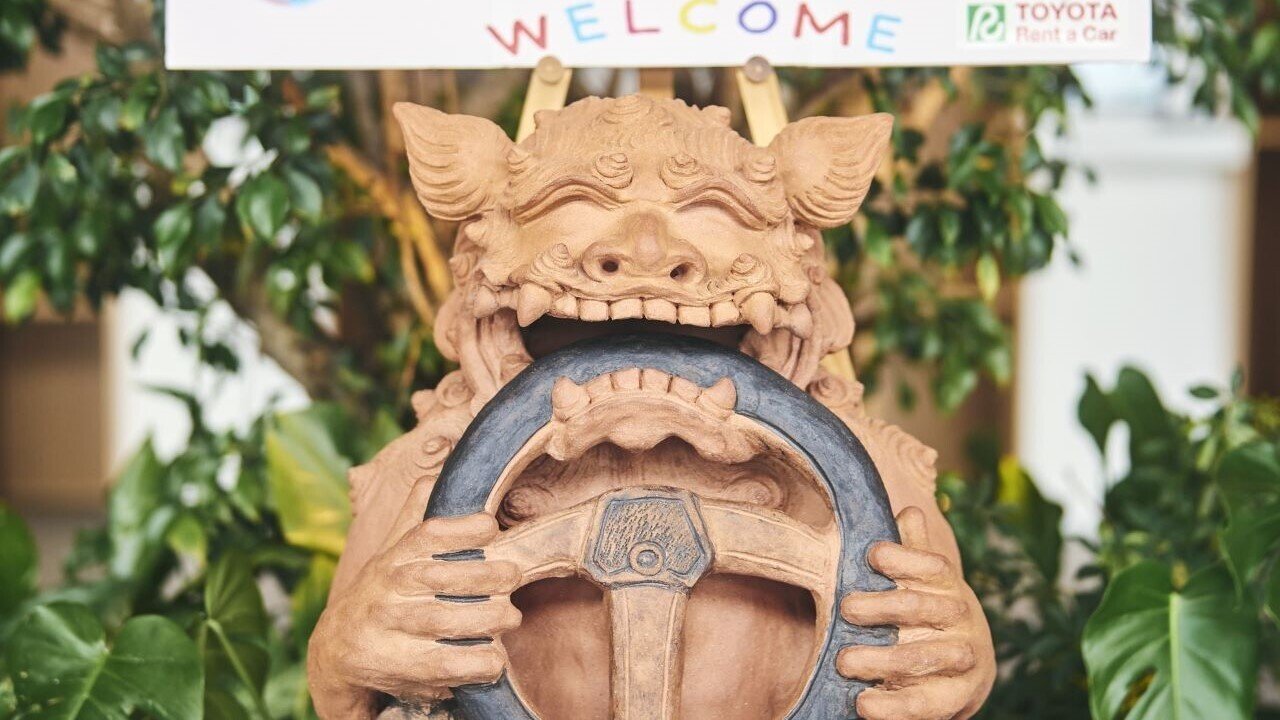
The long, snaking lines are no more! Recent efforts have dramatically shortened Okinawa's dreaded rental waiting times. We uncover the fascinating details of how it was accomplished.
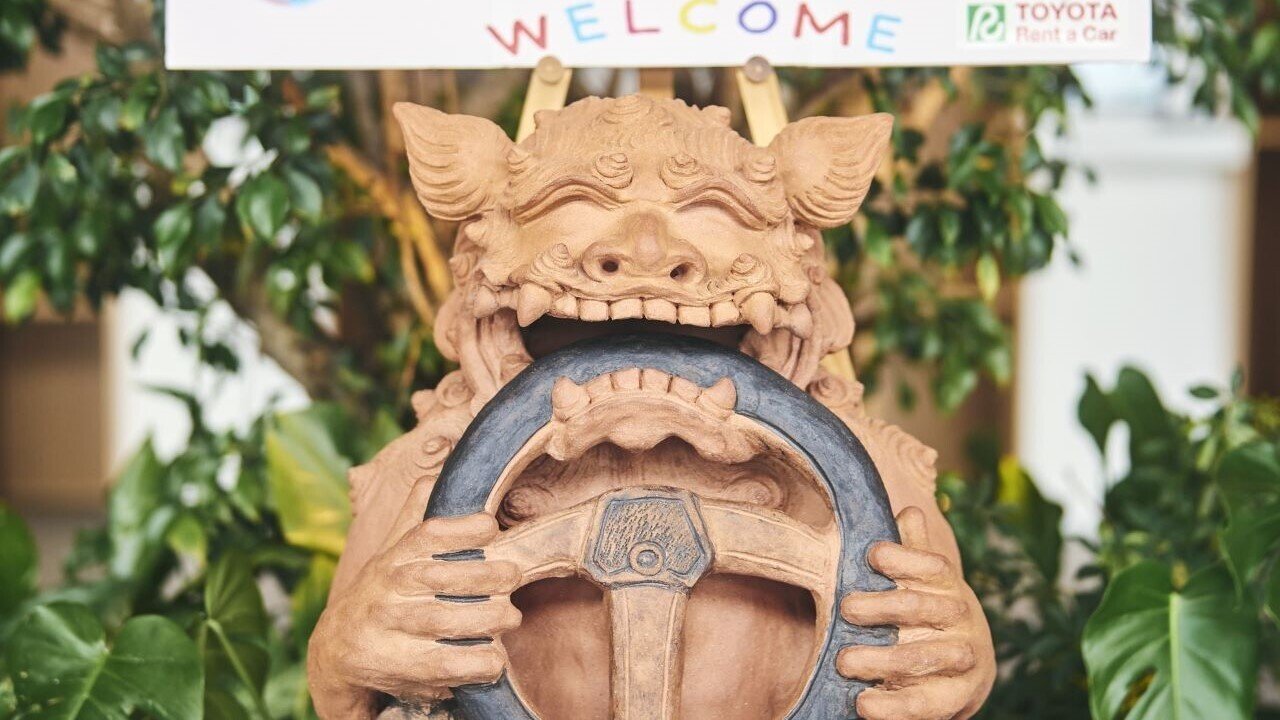
Take a look at these two photographs.

During the peak summer vacation season, visitors hoping to rent a car near Naha Airport have to line up for the rental office shuttle bus, only to join another long queue at the office itself…
Recently, however, these wait times have been significantly shortened. What happened?
From 150 minutes to 10
Let’s jump back to 2018. At the time, Toyota Rent a Car’s Naha Airport Shop had teams of some 30 to 60 staff working to rent out as many as 1,000 vehicles per day.
Wait times climbed to a staggering two and a half hours!
The complaints also piled up, with customers asking how long they were going to be kept waiting, and saying their vacations had been ruined. In terms of customer satisfaction, the shop scored lowest in the Kyushu-Okinawa region. With staff worn out, employee satisfaction was also dropping, and turnover was high.
Today, however, the process from the reception counter to driving away takes no more than 10 minutes.
That’s right—10 minutes! The improvement almost seems too good to be true, yet there were several reasons behind the change. To begin, in March 2022, the company opened its Naha Airport Seaside Shop, among the largest in Japan, and adjusted overall volumes by turning customers away when capacity was exceeded.

Let us give you a sense of how smoothly things now run by walking through the customer experience. First, when the airport shuttle bus drops you off at the shop, staff guide you straight to the reception area.

The shop largely shifted to an automated check-in system, RaCCU, which handles the paperwork—including driver's license scanning, optional insurance, and credit card payment—in around three minutes.

After picking up your keys at the nearby counter…

…a 30-second walk takes you to the vast pick-up area. If you signed up for insurance, you don’t even need to check the car’s condition with the staff. You can just drive away! The entire process to this point has taken just seven minutes.

While we were at the shop, a bus arrived with a large group of tourists, yet the stream of people to the pick-up area remained almost comically smooth. Setting up a large new shop and adjusting the number of rented vehicles had the desired effect: the excessively long queues were gone.
And here’s the part where Toyota’s true character shines through. To further raise customer and employee satisfaction, the company undertook “TSL improvements.” So, what is TSL?

Building on one employee’s efforts, 30 years on
The Toyota Production System (TPS) is central to the company’s operations, focusing on making work easier for employees, thoroughly eliminating waste, and delivering quality products to customers in a timely and affordable way.
Although TPS began in the production genba, about 30 years ago, a certain employee incorporated its ideas into Toyota’s sales force.
Kaizen efforts were aimed at improving the flow of products. The result was the Toyota Sales Logistics (TSL) system, intended to create happiness for staff and customers.
As it happens, the employee behind this was none other than Akio Toyoda, then a sub-section manager who established a Team for CS Creation to improve sales operations.
At first, he received a great deal of opposition from dealers who felt that “making products and selling products are two different things.” However, with many Toyota employees stationed at dealerships and continuing to make improvements, work gradually became easier, and more people embraced what Akio was trying to do.
Even today, many dealerships are engaged in autonomous and ongoing improvement efforts, with Toyota Rent a Car Okinawa being just one example.

What kind of improvements did they make? The staff shared some fascinating stories.
The team began by working with members from Toyota Motor Corporation’s TSL Promotion Division to create a flow chart of goods and information so they could better understand the movement of customers and cars. Doing so revealed many issues in areas that had been regarded as routine.

Daisuke Takanohashi, Deputy General Manager, OJT System Improvement Department, Toyota Rent a Car Okinawa

In the past, individual staff members relied on their instincts and intuition when it came to the timing for preparing cars for customers. The job had no clear rules despite the wide range of employees, from veterans to newcomers and part-time staff, doing it.
There was a lot of waste, inconsistencies, and unreasonable tasks, such as prioritizing vehicles that would not be rented out until the following day or washing cars a second time because of rain. During peak season, moving vehicles took so much time that they weren’t cleaned properly, sometimes leading to complaints.
What proved useful was a familiar feature of Toyota’s production plants, and something that our readers might also recognize.